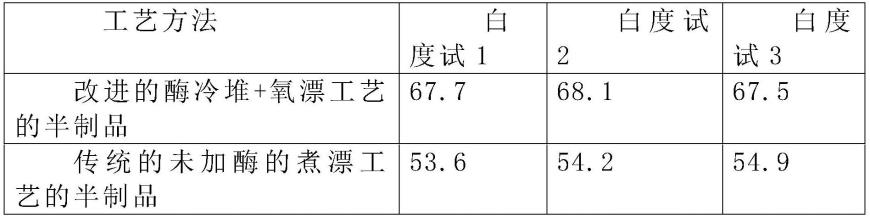
1.本发明属于麻面料加工技术领域,涉及一种柔软麻面料的加 工工艺。
背景技术:2.麻织物由于吸湿性号、无静电、抗腐耐热、抗拉力强,有独 特的凉爽感,出汗不沾身,有很好的的自然光泽,以圣洁、大方、 卫生、自然的风格,在人们印象中就形成了“麻就代表高档”的 概念。但麻纤维刚硬,手感粗糙,穿着有刺痒感,而且麻皮很难 处理。
3.一直以来印染行业对于麻皮的处理通常都是通过氯漂才能去 除,但氯的腐蚀性相当强,连不锈钢钢等金属很快就能被腐蚀烂 掉,所以氯漂设备的材质都是专门设计的,氯漂后的残液排到污 水处理池,会杀死污水处理最重要也是最有效的力量—菌群,从 而使污水处理的能力严重降低,而且过量的氯对人体造成伤害。
技术实现要素:4.本发明的目的是针对上述问题,提供一种柔软麻面料的加工 工艺。
5.为达到上述目的,本发明采用了下列技术方案:
6.一种柔软麻面料的加工工艺,其特征在于,包括以下步骤:
7.s1摆布:对麻面料进行摆布处理,麻面料通过输送带输送至 煮练容器中;
8.s2冷堆煮练:麻面料通过加有酶、稳定剂、双氧水以及烧碱 溶液中进行煮练,煮练之后进行冷堆静置;
9.s3汽蒸蒸漂:冷堆静置后的麻面料通过双氧水处理后,通过 汽蒸箱进行蒸漂处理;
10.s4捶打处理:对蒸漂处理后的麻面料进行物理捶打;
11.s5轧酶处理:捶打处理后的麻面料在带有酶的煮练剂中进行 煮练,煮练完成后进行冷堆静置;
12.s6去杂蒸洗:将轧酶处理后的麻面料输送至汽蒸箱内,并加 入去杂溶剂进行蒸洗;
13.s7轧染轧蒸:对去杂蒸洗后的麻面料进行染色处理;
14.s8皂洗软顺:对染色后的麻面料进行皂洗,然后在皂洗后对 麻面料加入软顺试剂并加热进行软顺处理;
15.s9舒松整理:采用拍打设备对软顺处理后的麻面料进行拍打 处理;
16.s10防缩处理:对拍打过的麻面料进行防缩处理。
17.在上述的柔软麻面料的加工工艺中,s2中的酶为精炼酶,稳 定剂的种类为精炼稳定剂,精炼酶的浓度为23-25g/l,精炼稳定 剂的浓度为8-12g/l,双氧水的浓度为10-11g/l,烧碱溶液中烧 碱的浓度为10-11g/l。
18.在上述的柔软麻面料的加工工艺中,s2中冷堆静置的时间为 20-24h,冷堆静置的风压为12bar。
19.在上述的柔软麻面料的加工工艺中,s3中麻面料在汽蒸箱内 的移动速度为100-120m/min,汽蒸蒸漂时间为30-60min,温度控 制为100-105℃。
20.在上述的柔软麻面料的加工工艺中,s4中麻面料物理捶打 时,麻面料的输送速度为:35m/min。
21.在上述的柔软麻面料的加工工艺中,煮练剂的浓度为8-12 g/l。
22.在上述的柔软麻面料的加工工艺中,s5中煮练剂包括烧碱与 表面活性剂。
23.在上述的柔软麻面料的加工工艺中,s5中的酶为退浆精炼 酶,酶的浓度可为8-12g/l。
24.在上述的柔软麻面料的加工工艺中,s5中冷堆静置的时间为 7-8h,冷堆静置的风压为35bar。
25.在上述的柔软麻面料的加工工艺中,s9中麻面料物理拍打 时,麻面料的输送速度为:30m/min。
26.与现有的技术相比,本发明的优点在于:对加工步骤中的冷 堆煮练以及轧酶工艺进行改进以此减少氯元素的使用,同时增加 了捶打处理以及舒松整理等步骤,通过特殊的加工工艺来提升面 料的柔软性。
27.本发明的其它优点、目标和特征将部分通过下面的说明体现, 部分还将通过对本发明的研究和实践而为本领域的技术人员所理 解。
具体实施方式
28.一种柔软麻面料的加工工艺,通过以下方式进一步阐述:
29.s1摆布:对麻面料进行摆布处理,麻面料通过输送带输送至 煮练容器中;在此过程中,面料通过输送机构来进入至煮练容器 中,本技术方案中涉及到的输送机构为现有技术,此输送机构仅 用于布料的输送,故不对此结构进行累述。
30.s2冷堆煮练:麻面料通过加有酶、稳定剂、双氧水以及烧碱 溶液中进行煮练,煮练之后进行冷堆静置;具体的,在此步骤中, 麻面料的传递速度是65m/min,酶为精炼酶cb-99,该精炼酶是生 物酶技术与化学品相结合的产品,为现有的酶制品,其作用用于 提升去除麻皮和麻皮屑的能力,因为氧漂对麻织物的白度提升率 很低,所以传统工艺主要靠氯漂提高麻织物的白度。我们在氧漂 时增加此类酶,可以大大提高氧漂白度,我们通过对比试验,证 明可以提高白度达20%以上。
31.对比试验数据
[0032][0033]
从三组实验数据可以看出,本技术方案采用的:在煮练过程 中加入精炼酶cb-99得到的麻织物半成体的白度在67-68之间, 传统的未加入酶的煮漂工艺得到的麻织物半成体的白度在53-55 度之间,可以看出在加入精炼酶cb-99之后,麻织物的白度得到 了明显
的提升。
[0034]
精炼稳定剂的种类为冷助灵cb-xd-4,为现有的添加剂种类, 精炼酶cb-99的浓度为23-25g/l,精炼稳定剂cb-xd-4的浓度 为8-12g/l,双氧水的浓度为10-11g/l,烧碱溶液中烧碱的浓 度为10-11g/l,酶的作用是用于去除麻面料的杂质和浆料,精 炼稳定剂的作用是用于提高毛效,双氧水用于除杂,烧碱起煮练 的作用,麻布料完成煮练之后对其进行冷
·
堆静置,本领域技术 人员应当理解,冷堆静置为现有的用于加工面料的工序,该工序 中会在堆置时间与风压上存在差异,具体到本方案中,冷堆静置 的时间为20-24h,冷堆静置的风压为12bar。
[0035]
s3汽蒸蒸漂:冷堆静置后的麻面料通过双氧水处理后,通过 汽蒸箱进行蒸漂处理;在此步骤中,麻面料在汽蒸箱内的移动速 度为100-120m/min,汽蒸蒸漂时间为30-60min,温度控制为 100-105℃,蒸漂的试剂中包括:烧碱、双氧水、高效精炼剂crn-f、 稳定剂hoc及裂解剂has,其中烧碱的浓度为:1.3g/l,双氧水 的浓度为:3.3g/l,高效精练剂crn-f的浓度:4g/l,稳定剂hoc 的浓度:7g/l,裂解剂has:4g/l,在本试剂中,双氧水起到漂 白的作用,裂解剂对提高白度的帮助很大。该工序为现有的用于 加工面料的工序,汽蒸箱为现有设备,高效精炼剂crn-f、稳定 剂hoc及裂解剂has为现有的添加剂。
[0036]
s4捶打处理:对蒸漂处理后的麻面料进行物理捶打;该工序 通过物理捶打的方法打掉麻皮屑,以便后续的工序中的酶能渗入 到麻织物的内部,捶打设备为现有技术,通过敲击来去除麻皮屑。 在此步骤中,麻面料的传递速度是35m/min,拍打频率为100次/ 分钟以上。
[0037]
s5轧酶处理:捶打处理后的麻面料在带有酶的煮练剂中进行 煮练,煮练完成后进行冷堆静置;在此过程中,麻面料的传递速 度是75m/min,煮练试剂可为烧碱溶液,煮练试剂的浓度为8-12 g/l。酶选用的种类为抛光酶8000a,该酶是一种纤维素酶,为现 有的酶品种,其用于提升去除麻织物表面的麻皮屑和粗硬的短麻 死皮效果,处理后的织物柔软度和光洁度明显提高。抛光酶8000a 的浓度可为8-12g/l,通过使用酶采用化学的方法来去除麻皮屑, 去除麻的死皮,消除刺痒感。
[0038]
s6去杂蒸洗:将轧酶处理后的麻面料输送至汽蒸箱内,汽蒸 箱为现有设备,并加入去杂溶剂进行蒸洗;在此步骤中,用于蒸 洗的试剂中包括:烧碱、双氧水、高效去杂剂、渗透剂以及螯合 分散剂,其中烧碱的浓度为:1g/l,双氧水的浓度为:5g/l,高 效去杂剂yxgx25的浓度:4g/l,渗透剂tf-107c的浓度:7g/l, 螯合分散剂tf-133ba:4g/l,渗透剂以及螯合分散剂均为现有的 添加剂,高效去杂剂包括亲水王cf和低泡高效精炼剂tf-125l, 主要通过亲水王cf和低泡高效精炼剂tf-125混合制成。该工序 使用的是现有的用于加工面料的常用设备,为现有技术。
[0039]
s7轧染轧蒸:对去杂蒸洗后的麻面料进行染色处理;在此步 骤中,麻面料的传递速度是40m/min,并采用多个上烘机径向烘 干处理,风机进行风干处理,通过固色液进行上色,通过轧车进 行压轧。轧染与轧蒸工序为现有的用于加工面料的常用工序,为 现有技术。
[0040]
s8皂洗软顺:对染色后的麻面料进行皂洗,然后在皂洗后对 麻面料加入软顺试剂并加热进行软顺处理;在此步骤中,麻面料 的传递速度是40m/min,此工序用于保证水洗的牢度,水洗之后 通过柔软剂、柔顺剂、防滑移剂对麻面料进行软顺处理,柔软剂 sf432ah的
含量为6%,柔顺剂sf-205的含量为0.5%,防滑移剂a 的含量为1%,柔顺剂采用柔顺剂sf-205,防滑移剂为防滑移剂a, 整个软顺处理过程中稳定恒定为130℃,软顺处理可以提升麻面 料的手感,减少刺痒感。皂洗与软顺工序为现有的用于加工面料 的常用工序,为现有技术,柔软剂sf432ah、柔顺剂sf-205以及 防滑移剂a均为现有的添加剂。
[0041]
s9舒松整理:采用拍打设备对软顺处理后的麻面料进行拍打 处理;在此步骤中,麻面料的传递速度是30m/min,利用拍打设 备拍打麻面料去除麻的粗硬感,用于拍打麻面料的设备为现有技 术。
[0042]
s10防缩处理:对拍打过的麻面料进行防缩处理。防缩处理 工艺为现有的用于加工面料的常用工序,为现有技术。
[0043]
本文中所描述的具体实施例仅仅是对本发明精神作举例说 明。本发明所属技术领域的技术人员可以对所描述的具体实施例 做各种各样的修改或补充或采用类似的方式替代,但并不会偏离 本发明的精神或者超越所附权利要求书所定义的范围。