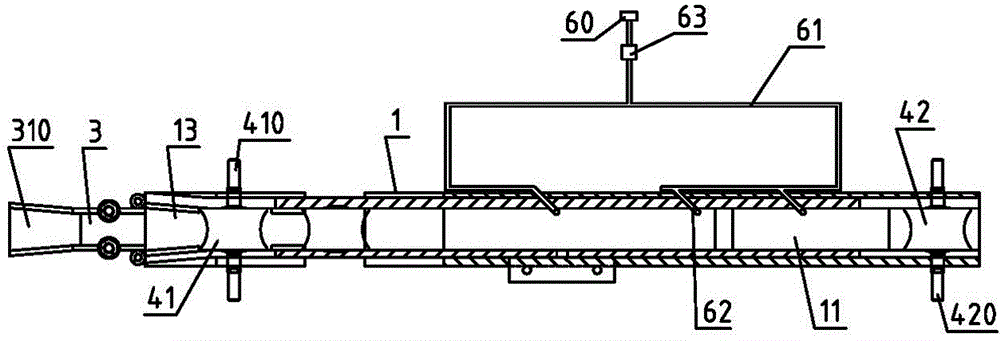
本实用新型涉及到冶金轧钢机械领域,尤其涉及一种用于连轧机组中的立式活套。
背景技术:在热轧棒材生产线中,为保证成品棒材的尺寸公差精度,提高产品的成材率和合格率,一般在中精轧机组中采用微张力或无张力控制轧制。在连轧生产中,张力来源于相邻二个轧机之间的秒流量差,当下游轧机的秒流量大于上游轧机的秒流量时,二个轧机之间的棒材就存在张力,张力过大就会导致拉钢轧制,使棒材的尺寸精度无法保证;当下游轧机的秒流量小于上游轧机的秒流量时,就会出现堆钢事故,因此必须将二个轧机之间的棒材张力控制在一个极小范围之内。微张力控制实质上是通过对相邻二个轧机中的上游轧机的电机转距进行检测,加以记忆存储,形成表示棒材张力大小的实际值,与设定的张力给定值的偏差通过比例、积分控制校正上游轧机的速度,协调二个轧机的轧制速度,实现微张力控制。其控制关键是准确测量各轧机的轧制力矩,系统通过检测对应轧机的电枢转距间接得到该值。当上游轧机咬钢而棒材尚未进入下游轧机时,系统计算出的力矩值便是上游轧机的轧制力距值。当下游轧机也咬钢时,重新计算得到新的力矩,两力矩之差是棒材上的张力力矩。若偏差值为正,表示二个轧机之间堆钢;若偏差值为负,表示二个轧机之间拉钢。系统就是根据该偏差值的正负和大小,相应修正二个轧机的速度,保证二个轧机之间的棒材张力被限制在一定范围内,实现微张力控制。由于张力由二个相邻轧机的轧辊速度差造成,并且张力形成受环境条件和建模误差的影响,因而微张力控制存在不确定性,为使连轧机组始终保持棒材在恒定的微张力下轧制或无张力控制,一般还会在二个相邻轧机之间设置活套,通过活套来调节二个轧机之间的棒材张力,传统的活套在使用过程中,容易出现棒材在活套中跑偏、碰撞、磨损现象,大大降低了活套的使用寿命,导致活套更换频率高。另外活套在使用过程中需要间歇对活套内部进行水冷却处理,水冷却处理后的冷却水会有部分残留于活套中而无法排出,棒材进入活套中后其头部会与残留的冷却水接触,这会加快棒材头部冷却、导致棒材头部发黑,使后续轧制过程中棒材头部轧制困难。
技术实现要素:本实用新型所需解决的技术问题是:提供一种能控制棒材走向且棒材通道中不会积水的立式活套。为解决上述问题,本实用新型采用的技术方案是:所述的一种立式活套,包括活套本体,在活套本体中设置有前后贯通的、供棒材通过的棒材通道,在活套本体前侧设置有进口导卫,进口导卫能引导棒材进入活套本体的棒材通道中;在棒材通道的前端设置有第一支承轴,第一支承轴通过第一轴承座支承设置于棒材通道前端顶部,在第一支承轴上设置有第一孔型轮,第一孔型轮能在第一支承轴上转动;在棒材通道的后端设置有第二支承轴,第二支承轴通过第二轴承座支承设置于棒材通道后端顶部,在第二支承轴上设置有第二孔型轮,第二孔型轮能在第二支承轴上转动;在棒材通道中设置有调节棒材张力的张力调节机构,张力调节机构位于第一孔型轮和第二孔型轮之间的棒材通道中;在活套本体中还设置有将棒材通道中的水分清除的水分清除机构。进一步地,前述的一种立式活套,其中,所述的第一孔型轮和第二孔型轮的截面轮廓线均为由两端逐渐向中部倾斜下降的弧状光滑曲线。进一步地,前述的一种立式活套,其中,在棒材通道前端设置有由前至后、开口逐渐减小的喇叭口通道,进口导卫后端连接于喇叭口通道前侧,且进口导卫后端与喇叭口通道之间留有间隙,棒材通道中的部分水分能通过该间隙向外流出。进一步地,前述的一种立式活套,其中,所述的进口导卫的结构包括:导向套筒,导向套筒的后侧与活套本体前侧相连接,且导向套筒的内通道与棒材通道相互连通;导向套筒由顶板、底板和二块侧板拼接而成,底板和二块侧板的前端均向外倾斜弯折,向外倾斜弯折部分的底板和二块侧板以及顶板前部构成前端大、后端小的喇叭口,喇叭口能引导棒材进入导向套筒的内通道中。进一步地,前述的一种立式活套,其中,在导向套筒的二块侧板上分别竖向设置有一根导向轴,在二根导向轴上分别设置有导向轮,二个导向轮均能在各自的导向轴上转动。进一步地,前述的一种立式活套,其中,所述的张力调节机构的结构包括:连接板,连接板的后端铰接于棒材通道底部,第三支承轴通过第三轴承座支承设置于连接板前端,在第三支承轴上设置有第三孔型轮,第三孔型轮能在第三支承轴上转动;在活套本体中设置有驱动连接板绕铰接点上下摆动的驱动装置。进一步地,前述的一种立式活套,其中,所述的驱动装置的结构为:在活套本体中铰接有气缸,气缸的伸出杆顶部铰连接于连接杆中部,气缸的伸出杆向外伸出时能推动连接板绕铰接点向下摆动,气缸的伸出杆向内缩回时能拉动连接板绕铰接点向上摆动。进一步地,前述的一种立式活套,其中,在活套本体两侧壁上分别设有限制连接板上下摆动幅度的限位槽,第三支承轴两端分别伸入二个限位槽中。进一步地,前述的一种立式活套,其中,所述的第三孔型轮的截面轮廓线均为由两端逐渐向中部倾斜下降的弧状光滑曲线。进一步地,前述的一种立式活套,其中,所述的水分清除机构的结构为:在活套本体中设置有气体管道,气体管道的进气口与气源相连接,在气体管道上由前至后间隔设置有若干与气体管道相连通的出气口,在各出气口处分别设置有一个冲气管,各冲气管管口伸入棒材通道中,且各冲气管均相对棒材通道向后倾斜设置,使冲气管关口朝向棒材通道的出料口;在气体管道上还设置有使气体管道畅通或关闭的电磁阀。本实用新型的有益效果是:能很好地调整棒材张力,在调节过程中通过进口导卫、第一孔型轮、第二孔型轮和第三孔型轮保证棒材从棒材通道的中部通过而不会左右晃动,使轧制过程更加稳定,有效提高了产品的成材率和合格率,避免出现因棒材跑偏而碰撞到进口导卫或棒材通道侧壁现象,大大提高了立式活套的寿命。除此之外,水分清除机构的设置能够将棒材通道中残留的水分去除,保证后续棒材轧制的顺利进行。附图说明图1是本实用新型所述的一种立式活套的结构示意图。图2是图1俯视方向立式活套的结构示意图。图3是图1中张力调节机构的结构示意图。图4是图3中连接板向上摆动后的结构示意图。图5是图1中水分清除机构的结构示意图。图6是图1中进口导卫的结构示意图。图7是图6中俯视方向进口导卫的结构示意图。图8是图1中A-A剖视方向第一孔型轮的内部结构示意图。具体实施方式下面结合附图及优选实施例对本实用新型所述的技术方案作进一步详细的说明。如图1和图2所示,本实施例所述的一种立式活套,包括活套本体1,在活套本体1中设置有前后贯通的、供棒材通过的棒材通道11。在活套本体1的前侧设置有进口导卫3,进口导卫3能引导棒材进入活套本体1的棒材通道11中;在棒材通道11的前端设置有由前至后、开口逐渐减小的喇叭口通道13,进口导卫3的后端连接于喇叭口通道13的前侧,在实际使用过程中,进口导卫3可采用铰链连接方式安装于喇叭口通道13的前侧,进口导卫3后端与喇叭口通道13之间留有间隙,棒材通道11中的部分水分能通过该间隙向外流出。如图6和图7所示,本实施例中所述的进口导卫3的结构包括:导向套筒31,导向套筒31的后侧与活套本体11的前侧的喇叭口通道13相连接,且导向套筒31的内通道与棒材通道11相互连通;导向套筒31由顶板311、底板313和二块侧板312拼接而成,底板313和二块侧板312的前端均向外倾斜弯折,向外倾斜弯折部分的底板313和二块侧板312以及顶板311前部构成前端大、后端小的喇叭口310,喇叭口310能引导棒材进入导向套筒31的内通道中。本实施例中在导向套筒31的二块侧板312上分别竖向设置有导向轴32,在二根导向轴32上分别设置有导向轮33,二个导向轮33均能在各自的导向轴32上转动。棒材经喇叭口310、导向套筒31进入棒材通道11的过程中,二个导向轮33能引导棒材从二个导向轮33之间通过,避免出现棒材碰撞二个侧板312的现象,大大延长了进口导卫3的使用寿命。如图1和图2所示,在棒材通道11的前端设置有第一支承轴410,第一支承轴410通过第一轴承座支承设置于棒材通道11的前端顶部,在第一支承轴410上设置有由碳化钨制成的第一孔型轮41,第一孔型轮41能在第一支承轴410上转动;在棒材通道11的后端设置有第二支承轴420,第二支承轴420通过第二轴承座支承设置于棒材通道11的后端顶部,在第二支承轴420上设置有由碳化钨制成的第二孔型轮42,第二孔型轮42能在第二支承轴420上转动。如图1、图2和图8所示,本实施例中所述的第一孔型轮41和第二孔型轮42的截面轮廓线均为由两端逐渐向中部倾斜下降的弧状光滑曲线。在实际使用过程中,为使第一孔型轮41和第二孔型轮42能更好地在第一支承轴410、第二支承轴420上转动,一般在第一孔型轮41和第一支承轴410之间以及第二孔型轮42和第二支承轴420之间分别设置轴承。如图1、图3和图4所示,在棒材通道11中设置有调节棒材张力的张力调节机构5,张力调节机构5位于第一孔型轮41和第二孔型轮42之间的棒材通道11中;本实施例中所述的张力调节机构5的结构包括:连接板51,连接板51的后端铰接于棒材通道11的底部,第三支承轴430通过第三轴承座支承设置于连接板51的前端,在第三支承轴430上设置有由碳化钨制成的第三孔型轮43,第三孔型轮43能在第三支承轴430上转动。本实施例中所述的第三孔型轮43的截面轮廓线为由两端逐渐向中部倾斜下降的弧状光滑曲线。在实际使用过程中,为使第三孔型轮43能更好地在第三支承轴430上转动,一般在第三孔型轮43和第三支承轴430之间设置轴承。在活套本体1中设置有驱动连接板51绕铰接点50上下摆动的驱动装置。所述的驱动装置的机构为:在棒材通道11上方的活套本体1中铰接有气缸52,气缸52的伸出杆53顶部铰连接于连接杆51的中部,气缸52的伸出杆53向外伸出时能推动连接板51绕铰接点50向下摆动,气缸52的伸出杆53向内缩回时能拉动连接板51绕铰接点50向上摆动。本实施例中在活套本体1的两侧壁上分别设有限制连接板51上下摆动幅度的限位槽12,第三支承轴430的两端分别伸入二个限位槽12中。如图1、图3和图5所示,在活套本体1中还设置有将棒材通道11中的水分清除的水分清除机构6。所述的水分清除机构6的结构为:在活套本体1中设置有气体管道61,气体管道61的进气口与气源相连接,在气体管道61上由前至后间隔设置有若干与气体管道61相连通的出气口,在各出气口处分别设置有一个冲气管62,各冲气管62的管口620伸入棒材通道11中,且各冲气管62均相对棒材通道11向后倾斜设置,使各冲气管62的管口620朝向棒材通道11的出料口,通过高压气体将棒材通道11中的水分吹向棒材通道11的出料口,迫使水分从棒材通道11的出料口流出。本实施例中在气体管道61上还设置有使气体管道61畅通或关闭的电磁阀63。连轧机组工作时,通过对相邻二个轧机中的上游轧机的电机转距进行检测,加以记忆存储,形成表示棒材张力大小的实际值,与设定的张力给定值的偏差通过比例、积分控制校正上游轧机的速度,协调二个轧机的轧制速度,实现微张力控制。当上游轧机咬钢而棒材尚未进入下游轧机时,系统计算出的力矩值便是上游轧机的轧制力距值。当下游轧机也咬钢时,重新计算得到新的力矩,两力矩之差是棒材上的张力力矩。若偏差值为正,表示二个轧机之间堆钢;若偏差值为负,表示二个轧机之间拉钢。系统就是根据该偏差值的正负和大小,相应修正二个轧机的速度,保证二个轧机之间的棒材张力被限制在一定范围内,实现微张力控制,同时结合该立式活套进行张力微调,保证二个轧机之间的棒材张力被限制在要求范围内。从上游轧机中输出的棒材经进口导卫3、棒材通道11后进入下游轧机的进料口中,此时位于立式活套中的棒材的两侧由二个导向轮33引导,上部由第一孔型轮41和第二孔型轮42引导,棒材下部由第三孔型轮43引导,从而使棒材在棒材通道11的中部移动而不会碰撞到棒材通道壁上。使气缸52的伸出杆53向外伸出一定距离,气缸52的伸出杆53向外伸出的距离根据微调张力大小而定。假设气缸52的伸出杆53所处位置如图4所示,棒材在第一孔型轮41、第二孔型轮42和第三孔型轮43的引导下在棒材通道11中形成向上凸起的光滑曲线运动轨迹,当上游轧机的轧制速度低于下游轧机的轧制速度时,位于棒材通道11中的棒材张力逐渐增大,当棒材张力和重力的合成力能克服气缸52的气压力时,棒材压迫第三孔型轮43使连接板51向下摆动直至合成力与气压力相互平衡,此时气缸52的伸出杆53随连接板51向下摆动而向外伸出。反之当上游轧机的轧制速度高于下游轧机的轧制速度时,位于棒材通道11中的棒材张力逐渐减小,当棒材张力和重力的合成力小于气缸52的气压力时,气缸52的伸出杆53在气压力的作用下向内缩回,迫使连接板51向上摆动直至合成力与气压力相互平衡。当棒材从棒材通道11输出后,对立式活套进行水冷却,然后控制电磁阀使气体管道61畅通,高压气体通过气体管道61、各冲气管62将棒材通道11中的水分吹向棒材通道11的出料口,迫使水分从棒材通道11的出料口流出,一般1秒就能将棒材通道11中的水分清除掉,此时该立体活套又可以引导上游轧机中的棒材进入下游轧机中了。以上所述仅是本实用新型的较佳实施例,并非是对本实用新型作任何其他形式的限制,而依据本实用新型的技术实质所作的任何修改或等同变化,仍属于本实用新型要求保护的范围。本实用新型的优点是:能很好地调整棒材张力,在调节过程中通过进口导卫3、第一孔型轮41、第二孔型轮42和第三孔型轮43保证棒材从棒材通道11的中部通过而不会左右晃动,使轧制过程更加稳定,有效提高了产品的成材率和合格率,避免出现因棒材跑偏而碰撞到进口导卫3或棒材通道11侧壁现象,大大提高了立式活套的寿命。除此之外,水分清除机构的设置能够将棒材通道11中残留的水分去除,保证后续棒材轧制的顺利进行。