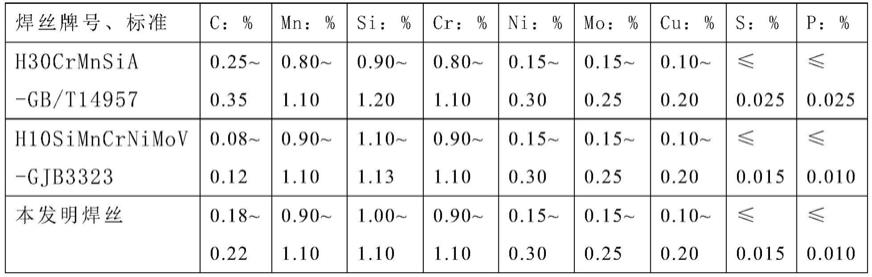
1.本发明涉及大厚度壳体的加工技术领域,具体涉及一种大厚度 航弹壳体焊接与热处理方法。
背景技术:2.传统的小型航弹直径约200mm,长度500mm左右,一般采用 棒料加热挤压成坯料后进行切削加工。现代大型的航弹一般直径大 于400mm,长度大于1500mm,厚度15~50mm,采用传统的热挤压 成形坯料,由于热挤压设备能力不足和热挤压成形内部质量难于保 证,而难于实现。
3.现有的大型航弹壳体成形与加工,采用锻棒坯料,粗加工内外 型面后进行淬火+回火热处理,再精加工内外型面。这种加工方法 的缺点是:材料利用率低,只有30~40%,切削加工周期长,一般 要半个月左右,导至制造成本高。
4.为了解决材料利用率低、加工周期长的问题,将航弹壳体设计 成壳体主段和壳体尾段焊接结构,壳体主段采用35crmnsia超高 强度钢厚壁无缝钢管旋压成形后数控加工成形,壳体尾段采用 35crmnsia超高强度钢自由锻件数控加工成形。产品试验件采用 h30crmnsia焊丝焊接、热处理后进行产品试验,壳体在穿过多层 混凝土板后壳体尾段断裂,不满足试验要求。为此,产品设计对材 料性能提出了更加严格的要求:基体材料抗拉强度不小于1850mpa、 延伸率不小于6%、冲击功不小于40焦耳,焊缝材料抗拉强度不小 于1100mpa不大于1300mpa、延伸率不小于10%、冲击功不小于 40焦耳。现有的大厚度航弹壳体的焊接与热处理方法,不能满足产 品的性能要求。
技术实现要素:5.本发明的目的就是针对现有评估方法的缺陷,提供一种基体材 料抗拉强度不小于1950mpa、延伸率不小于7%、冲击功不小于50 焦耳且焊缝材料抗拉强度不小于1100mpa并且不大于1300mpa、 延伸率不小于10.5%、冲击功不小于54焦耳的大厚度航弹壳体焊接 与热处理方法。
6.为实现上述目的,本发明所设计的大厚度航弹壳体焊接与热处 理方法,包括如下步骤:
7.1)壳体主段加工
8.采用热轧无缝厚钢管加工成壳体主段;
9.2)壳体尾段加工
10.将壳体尾段锻造坯料加工为壳体尾段;
11.3)焊接试样环形件加工
12.采用与壳体主段材料成分相同、等效壁厚相等的厚壁钢管加工 主段焊接试样环形件;
13.采用与壳体尾段材料成分相同、等效壁厚相等的厚壁钢管加工 尾段焊接试样环
形件;
14.4)壳体主段与壳体尾段焊接成壳体,主段焊接试样环形件与 尾段焊接试样环形件对焊成试样
15.5)壳体、试样焊缝射线探伤
16.6)壳体、试样淬火、回火热处理
17.壳体及试样淬火加热温度880~900℃保温1.5~2h,机械油冷却 1~0.5h;壳体及试样回火加热温度260~300℃保温2~2.5h,水冷却 1~0.5h;
18.7)试样加工及检测
19.在试样上加工焊接接头横向拉伸试样、焊接接头纵向拉伸试样、 焊接接头冲击试样、基体纵向拉伸试样、基体冲击试样并检测。
20.进一步地,所述步骤1)中,壳体主段的尾部焊接坡口采用y 型坡口,y型坡口角度α为33
°
~38
°
。
21.进一步地,所述步骤1)中,壳体主段的尾部焊接定位凸台的 厚度为1~2mm、宽度为1~2mm。
22.进一步地,所述步骤2)中,壳体尾段的焊接坡口采用y型坡 口,y型坡口角度α为33
°
~38
°
,与壳体主段坡口相同。
23.进一步地,所述步骤2)中,壳体尾段的焊接定位凹台的厚度 为1~2mm、宽度为1~2mm,与壳体主段焊接定位凸台相同。
24.进一步地,所述步骤4)中,采用氩弧焊将壳体主段与壳体尾 段焊接、主段焊接试样环形件与尾段焊接试样环形件对焊,焊前采 用感应器加热母材,预热温度300~360℃,焊后及时进行650~700℃ 保温1.5~2h消除焊接应力和除氢处理。
25.进一步地,所述步骤4)中,焊丝成分按质量百分比包括:c: 0.18~0.22,mn:0.5~0.7,si:0.25~0.35,cr:0.9~1.1,ni: 0.15~0.3,mo:0.15~0.25,cu:0.1~0.2,s:≤0.02,p:≤0.025。
26.与现有技术相比,本发明具有以下优点:本发明大厚度航弹壳 体焊接与热处理方法通过优化焊丝成分和焊接、热处理参数,消除 了回火脆性,保证了母材和焊缝的特殊力学性能要求:基体材料抗 拉强度≥1950mpa、延伸率≥7%、冲击功≥50j,焊缝材料抗拉强 度≥1100mpa、≤1300mpa、延伸率≥10.5%、冲击功≥54j。
具体实施方式
27.下面结合具体实施例对本发明作进一步的详细说明,便于更 清楚地了解本发明,但它们不对本发明构成限定。
28.大厚度航弹壳体焊接与热处理方法,包括如下步骤:
29.1)壳体主段加工
30.采用热轧无缝厚钢管,通过热旋压、强力旋压和数控切削加工, 将圆管原材料加工成壳体主段;
31.壳体主段的成形与加工流程为:厚壁热轧无缝厚钢管下料
→
壳 体主段头部热旋压成形
→
壳体主段头部内型面及直筒段内孔数控加 工
→
壳体主段直筒段外形正向强力旋压成形
→
壳体主段尾部热旋压 成形
→
壳体主段外形及尾部内型面、尾部焊接坡口、尾部焊
接定位 凸台加工;
32.壳体主段尾部焊接坡口采用y型坡口,y型坡口角度α为 33
°
~38
°
;
33.壳体主段尾部焊接定位凸台的厚度为1~2mm、宽度为1~2mm;
34.2)壳体尾段加工
35.将壳体尾段锻造坯料加工为壳体尾段;
36.壳体尾段的成形与加工流程为:圆钢下料
→
壳体尾段坯料锻造 成形
→
壳体尾段坯料正火、回火
→
壳体尾段外形、内型面、焊接坡 口、焊接定位凹台加工;
37.壳体尾段焊接坡口采用y型坡口,y型坡口角度α为33
°
~38
°
, 与壳体主段坡口相同;
38.壳体尾段焊接定位凹台的厚度为1~2mm、宽度为1~2mm,与 壳体主段焊接定位凸台相同;
39.3)焊接试样环形件加工
40.采用与壳体主段材料成分相同、等效壁厚相等的厚壁钢管加工 主段焊接试样环形件;
41.采用与壳体尾段材料成分相同、等效壁厚相等的厚壁钢管加工 尾段焊接试样环形件;
42.4)壳体主段与壳体尾段焊接成壳体,主段焊接试样环形件与 尾段焊接试样环形件对焊成试样
43.对于厚度15~50mm的35crmnsia超高强度钢,焊缝材料抗拉 强度不小于1100mpa并且不大于1300mpa、延伸率不小于10%、 冲击功不小于40焦耳的大厚度航弹壳体的焊接,采用常规的 h30crmnsia高强度钢焊丝和焊接方法,焊缝韧性差,无法保证力 学性能要求。综合考虑大厚度焊缝母材熔合到焊缝中的体积比例小 即焊缝融合比小、超高强度钢的焊接特性等,通过多种焊丝成分对 比焊接、热处理、无损检测和力学性能测试等工艺试验,获得优化 的焊丝成分和焊接及性能检测方法,保证特殊的焊缝性能要求。
44.采用氩弧焊将壳体主段与壳体尾段焊接、两个焊接试样环形件;
45.焊接流程为:装配
→
预热
→
定位焊
→
加丝焊
→
盖面焊
→
背面手 工重熔焊
→
消除焊接应力、除氢处理;
46.通过多种焊丝成分对比焊接、热处理、无损检测和力学性能测 试等工艺试验,通过降低焊丝碳、硫、磷含量,降低成分离散度, 从而满足焊缝性能的要求。焊丝成分按质量百分比包括:c: 0.18~0.22,mn:0.5~0.7,si:0.25~0.35,cr:0.9~1.1,ni: 0.15~0.3,mo:0.15~0.25,cu:0.1~0.2,s:≤0.02,p:≤0.025。
47.焊前采用感应器加热母材,预热温度300~360℃,焊后及时进 行650~700℃保温1.5~2h消除焊接应力和除氢处理;
48.三种焊丝牌号、标准、成分见表1,焊丝成分、回火温度对比 试验性能测试结果见表2。
49.表1对比试验焊丝成分表
[0050][0051]
从对比试验焊丝成分表1、焊丝成分、回火温度对比试验性能 检测表2可以看出,h30crmnsia
‑
gb/t14957焊丝碳含量较高、硫 磷含量较高,焊缝强度偏高、韧性较差。h10simncrnimov
‑ꢀ
gjb3323焊丝碳含量偏低由于基体厚度大,焊缝宽度大,基体碳元 素扩散到焊缝的体积比即融合比偏小,焊缝强度偏低。本发明焊丝 以h10simncrnimov
‑
gjb3323焊丝为基础进行了改进,增加碳含 量为c:0.18%
‑
0.22%,配合优化的热处理制度,各项力学性能都 满足设计指标要求。
[0052]
5)壳体、试样焊缝射线探伤
[0053]
对壳体和试样焊缝进行x射线探伤检测,按照jb/t4730
‑
2005 《承压设备无损检测第2部分射线检测》标准i级执行;
[0054]
6)壳体、试样淬火、回火热处理
[0055]
对壳体及试样进行淬火、回火热处理,保证基体及焊缝特殊的 力学性能要求;壳体及试样淬火加热温度880~900℃保温1.5~2h, 机械油冷却1~0.5h;壳体及试样回火加热温度260~300℃保温 2~2.5h,水冷却1~0.5h。
[0056]
35crmnsia超高强度钢具有第一类低温回火脆性和第二类高温 回火脆性的特性,通过工艺试验优化淬火、回火热处理参数,避免 回火脆性,保证基体材料抗拉强度不小于1950mpa、延伸率不小于 7%、冲击功不小于50焦耳,焊缝材料抗拉强度不小于1100mpa不 大于1300mpa、延伸率不小于10.5%、冲击功不小于54焦耳的力 学性能要求。
[0057]
7)试样加工及检测
[0058]
在试样上加工焊接接头横向拉伸试样2件、焊接接头纵向拉伸 试样2件、焊接接头冲击试样4件、基体纵向拉伸试样2件、基体 冲击试样4件,然后对试样进行检测。
[0059]
表2回火温度、焊丝成分对比试验性能检测表
[0060][0061][0062]
实施例1
[0063]
针对某型号35crmnsia超高强度钢大厚度航弹壳体,其外形直 径d0为400mm,壳体长度l0为1500mm,壁厚t0为16mm,大厚 度航弹壳体焊接与热处理方法具体如下:
[0064]
1)壳体主段加工
[0065]
采用热轧无缝厚钢管,通过热旋压、强力旋压和数控切削加工, 将圆管原材料加工成壳体主段;
[0066]
壳体主段的成形与加工流程为:厚壁热轧无缝厚钢管下料
→
壳 体主段头部热旋压成形
→
壳体主段头部内型面及直筒段内孔数控加 工
→
壳体主段直筒段外形正向强力旋压成形
→
壳体主段尾部热旋压 成形
→
壳体主段外形及尾部内型面、尾部焊接坡口、尾部焊接定位 凸台加工;
[0067]
壳体主段尾部焊接坡口采用y型坡口,y型坡口角度α为33
°
;
[0068]
壳体主段尾部焊接定位凸台的厚度为1mm、宽度为2mm;
[0069]
2)壳体尾段加工
[0070]
将壳体尾段锻造坯料加工为壳体尾段;
[0071]
壳体尾段的成形与加工流程为:圆钢下料
→
壳体尾段坯料锻造 成形
→
壳体尾段坯料正火、回火
→
壳体尾段外形、内型面、焊接坡 口、焊接定位凹台加工;
[0072]
壳体尾段焊接坡口采用y型坡口,y型坡口角度α为33
°
,与 壳体主段坡口相同;
[0073]
壳体尾段焊接定位凹台的厚度为1mm、宽度为2mm,与壳体 主段焊接定位凸台相同;
[0074]
3)焊接试样环形件加工
[0075]
采用与壳体主段材料成分相同、等效壁厚相等的厚壁钢管加工 主段焊接试样环形件;
[0076]
采用与壳体尾段材料成分相同、等效壁厚相等的厚壁钢管加工 尾段焊接试样环形件;
[0077]
4)壳体主段与壳体尾段焊接成壳体,主段焊接试样环形件与 尾段焊接试样环形件对焊成试样
[0078]
采用氩弧焊将壳体主段与壳体尾段焊接、两个焊接试样环形件;
[0079]
焊接流程为:装配
→
预热
→
定位焊
→
加丝焊
→
盖面焊
→
背面手 工重熔焊
→
消除焊接应力、除氢处理;
[0080]
35crmnsia超高强度钢产品焊接母材厚度为15mm;焊前采用 感应器加热母材,预热温度300℃,焊后及时进行650℃保温1.5h 消除焊接应力和除氢处理;
[0081]
5)壳体、试样焊缝射线探伤
[0082]
对壳体和试样焊缝进行x射线探伤检测,按照jb/t4730
‑
2005 《承压设备无损检测第2部分射线检测》标准i级执行;
[0083]
6)壳体、试样淬火、回火热处理
[0084]
壳体及试样淬火加热温度880℃保温1.5h,机械油冷却0.5h; 壳体及试样回火加热温度260℃保温2h,水冷却0.5h。
[0085]
通过工艺试验优化淬火、回火热处理参数,避免回火脆性,保 证基体材料抗拉强度不小于1850mpa、延伸率不小于7%、冲击功 不小于40焦耳,焊缝材料抗拉强度不小于1100mpa不大于 1300mpa、延伸率不小于10%、冲击功不小于40焦耳的力学性能 要求。
[0086]
7)试样加工及检测
[0087]
在试样上加工焊接接头横向拉伸试样2件、焊接接头纵向拉伸 试样2件、焊接接头冲击试样4件、基体纵向拉伸试样2件、基体 冲击试样4件,然后对试样进行检测。
[0088]
实施例2
[0089]
针对某型号35crmnsia超高强度钢大厚度航弹壳体,其外形直 径d0为500mm,壳体长度l0为2000mm,壁厚t0为20mm,大厚 度航弹壳体焊接与热处理方法具体如下:
[0090]
1)壳体主段加工
[0091]
采用热轧无缝厚钢管,通过热旋压、强力旋压和数控切削加工, 将圆管原材料加工成壳体主段;
[0092]
壳体主段的成形与加工流程为:厚壁热轧无缝厚钢管下料
→
壳 体主段头部热旋压成形
→
壳体主段头部内型面及直筒段内孔数控加 工
→
壳体主段直筒段外形正向强力旋压成形
→
壳体主段尾部热旋压 成形
→
壳体主段外形及尾部内型面、尾部焊接坡口、尾部焊接定位 凸台加工;
[0093]
壳体主段尾部焊接坡口采用y型坡口,y型坡口角度α为35
°
;
[0094]
壳体主段尾部焊接定位凸台的厚度为1.5mm、宽度为1.5mm;
[0095]
2)壳体尾段加工
[0096]
将壳体尾段锻造坯料加工为壳体尾段;
[0097]
壳体尾段的成形与加工流程为:圆钢下料
→
壳体尾段坯料锻造 成形
→
壳体尾段坯料正火、回火
→
壳体尾段外形、内型面、焊接坡 口、焊接定位凹台加工;
[0098]
壳体尾段焊接坡口采用y型坡口,y型坡口角度α为35
°
,与 壳体主段坡口相同;
[0099]
壳体尾段焊接定位凹台的厚度为1.5mm、宽度为1.5mm,与壳 体主段焊接定位凸台相同;
[0100]
3)焊接试样环形件加工
[0101]
采用与壳体主段材料成分相同、等效壁厚相等的厚壁钢管加工 主段焊接试样环形件;
[0102]
采用与壳体尾段材料成分相同、等效壁厚相等的厚壁钢管加工 尾段焊接试样环形件;
[0103]
4)壳体主段与壳体尾段焊接成壳体,主段焊接试样环形件与 尾段焊接试样环形件对焊成试样
[0104]
采用氩弧焊将壳体主段与壳体尾段焊接、两个焊接试样环形件;
[0105]
焊接流程为:装配
→
预热
→
定位焊
→
加丝焊
→
盖面焊
→
背面手 工重熔焊
→
消除焊接应力、除氢处理;
[0106]
35crmnsia超高强度钢产品焊接母材厚度为30mm;焊前采用 感应器加热母材,预热温度330℃,焊后及时进行675℃保温1.5h 消除焊接应力和除氢处理;
[0107]
5)壳体、试样焊缝射线探伤
[0108]
对壳体和试样焊缝进行x射线探伤检测,按照jb/t4730
‑
2005 《承压设备无损检测第2部分射线检测》标准i级执行;
[0109]
6)壳体、试样淬火、回火热处理
[0110]
壳体及试样淬火加热温度890℃保温1.8h,机械油冷却0.5h; 壳体及试样回火加热温度280℃保温2.3h,水冷却0.5h。
[0111]
通过工艺试验优化淬火、回火热处理参数,避免回火脆性,保 证基体材料抗拉强度不小于1850mpa、延伸率不小于7%、冲击功 不小于40焦耳,焊缝材料抗拉强度不小于1100mpa不大于 1300mpa、延伸率不小于10%、冲击功不小于40焦耳的力学性能 要求。
[0112]
7)试样加工及检测
[0113]
在试样上加工焊接接头横向拉伸试样2件、焊接接头纵向拉伸 试样2件、焊接接头冲击试样4件、基体纵向拉伸试样2件、基体 冲击试样4件,然后对试样进行检测。
[0114]
实施例3
[0115]
针对某型号35crmnsia超高强度钢大厚度航弹壳体,其外形直 径d0为600mm,壳体长度l0为2500mm,壁厚t0为24mm,大厚 度航弹壳体焊接与热处理方法具体如下:
[0116]
1)壳体主段加工
[0117]
采用热轧无缝厚钢管,通过热旋压、强力旋压和数控切削加工, 将圆管原材料加工成壳体主段;
[0118]
壳体主段的成形与加工流程为:厚壁热轧无缝厚钢管下料
→
壳 体主段头部热旋压成形
→
壳体主段头部内型面及直筒段内孔数控加 工
→
壳体主段直筒段外形正向强力旋压成形
→
壳体主段尾部热旋压 成形
→
壳体主段外形及尾部内型面、尾部焊接坡口、尾部焊接定位 凸台加工;
[0119]
壳体主段尾部焊接坡口采用y型坡口,y型坡口角度α为38
°
;
[0120]
壳体主段尾部焊接定位凸台的厚度为2mm、宽度为2mm;
[0121]
2)壳体尾段加工
[0122]
将壳体尾段锻造坯料加工为壳体尾段;
[0123]
壳体尾段的成形与加工流程为:圆钢下料
→
壳体尾段坯料锻造 成形
→
壳体尾段坯料正火、回火
→
壳体尾段外形、内型面、焊接坡 口、焊接定位凹台加工;
[0124]
壳体尾段焊接坡口采用y型坡口,y型坡口角度α为38
°
,与 壳体主段坡口相同;
[0125]
壳体尾段焊接定位凹台的厚度为2mm、宽度为2mm,与壳体 主段焊接定位凸台相同;
[0126]
3)焊接试样环形件加工
[0127]
采用与壳体主段材料成分相同、等效壁厚相等的厚壁钢管加工 主段焊接试样环形件;
[0128]
采用与壳体尾段材料成分相同、等效壁厚相等的厚壁钢管加工 尾段焊接试样环形件;
[0129]
4)壳体主段与壳体尾段焊接成壳体,主段焊接试样环形件与 尾段焊接试样环形件对焊成试样
[0130]
采用氩弧焊将壳体主段与壳体尾段焊接、两个焊接试样环形件;
[0131]
焊接流程为:装配
→
预热
→
定位焊
→
加丝焊
→
盖面焊
→
背面手 工重熔焊
→
消除焊接应力、除氢处理;
[0132]
35crmnsia超高强度钢产品焊接母材厚度为50mm;焊前采用 感应器加热母材,预热温度360℃,焊后及时进行700℃保温2h消 除焊接应力和除氢处理;
[0133]
5)壳体、试样焊缝射线探伤
[0134]
对壳体和试样焊缝进行x射线探伤检测,按照jb/t4730
‑
2005 《承压设备无损检测第2部分射线检测》标准i级执行;
[0135]
6)壳体、试样淬火、回火热处理
[0136]
壳体及试样淬火加热温度900℃保温2h,机械油冷却0.5h;壳 体及试样回火加热温度300℃保温2.5h,水冷却0.5h。
[0137]
通过工艺试验优化淬火、回火热处理参数,避免回火脆性,保 证基体材料抗拉强度不小于1850mpa、延伸率不小于7%、冲击功 不小于40焦耳,焊缝材料抗拉强度不小于1100mpa不大于 1300mpa、延伸率不小于10%、冲击功不小于40焦耳的力学性能 要求。
[0138]
7)试样加工及检测
[0139]
在试样上加工焊接接头横向拉伸试样2件、焊接接头纵向拉伸 试样2件、焊接接头冲击试样4件、基体纵向拉伸试样2件、基体 冲击试样4件,然后对试样进行检测。