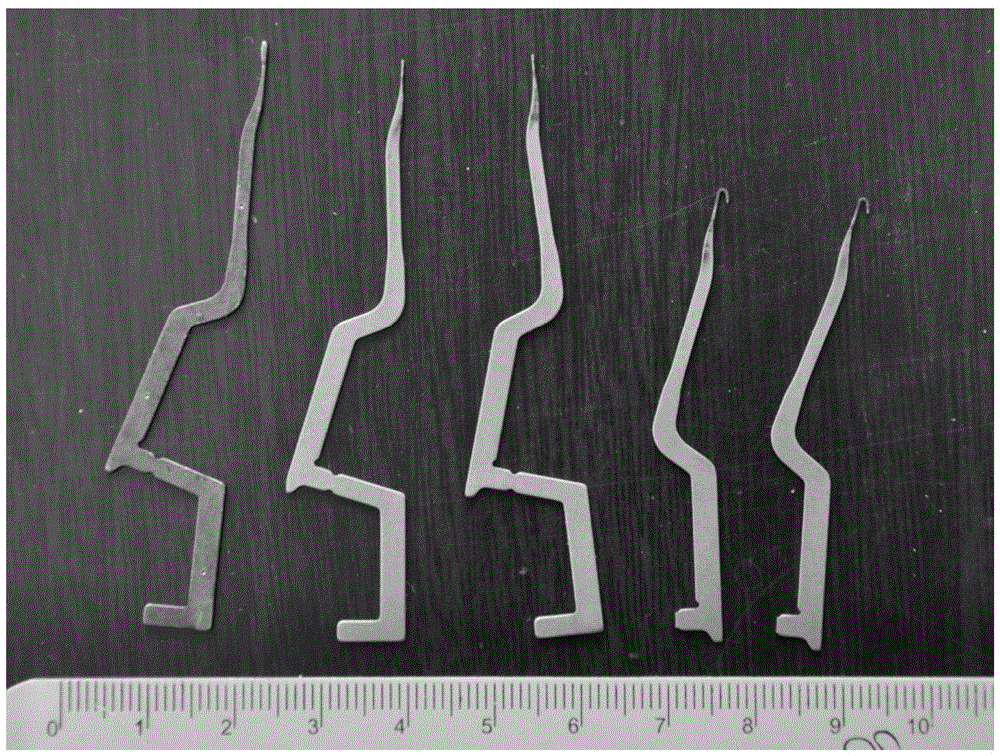
本发明属于合金钢领域,具体提供一种超高强高韧马氏体时效钢及其制备方法和应用。
背景技术:
:对于纺织钩针、撞针等高强度结构件的制备,高强度低合金钢凭借材料成本的优势,始终成为企业的首选。与高强度低合金钢相比,马氏体时效钢具有明显的强韧性优势,但一直无法得到企业的认可而实现产业化应用。在马氏体时效钢的发展过程中,强韧性匹配与使用成本是影响马氏体时效钢应用前景的两个核心问题,一方面,在保证韧性的前提下实现马氏体时效钢强度的提高,迎合产品的轻量化、节能减排以及安全环保等设计宗旨,是决定马氏体时效钢应用前景的关键因素;另一方面,与普通的高强度低合金钢相比,马氏体时效钢的强韧性优势明显,但由于其高含量的合金元素,马氏体时效钢的材料成本同样很高,如何充分利用马氏体时效钢的性能优势,降低结构材料使用成本,是影响马氏体时效钢应用前景的关键。技术实现要素:为解决上述技术问题,本发明提供一种超高强高韧的马氏体时效钢及其制备方法和应用,本发明的整体技术方案为:本发明在现有的高强度马氏体时效钢基础上,适量提高合金元素的含 量并优化合金元素配比,开发出抗拉强度达到3000MPa的新型超高强度马氏体时效钢,同时通过优化冶炼工艺,将钢中杂质元素含量降到较高级别,保证马氏体时效钢具有高强度的同时兼顾良好的韧性。根据上述设计思想,本发明的具体技术方案为:超高强高韧马氏体时效钢的化学成分为(wt.%):C:≤0.008%,Ni:18.0-20.0%,Co:15.0-18.0%,Mo:7.0-8.0%,Ti:1.5-2.5%,O≤0.01%,N≤0.01%,P≤0.01%,S≤0.01%,Fe:余量。优选为:C:≤0.005%,Ni:18.5-19.5%,Co:15.5-16.5%,Mo:7.0-7.5%,Ti:1.5-1.8%,O+N≤0.004%,P≤0.005%,S≤0.005%,Fe:余量。本发明所述马氏体时效钢的制备工艺,其特征在于,包括以下步骤:真空熔炼—真空自耗—均匀化处理—锻造—热处理,其中:真空熔炼:合金元素均以高纯度纯金属的形式加入,将配料置于真空感应炉中进行真空熔炼、Ca处理和真空脱气,严格控制钢中杂质元素含量,之后浇铸成铸锭。真空自耗:将真空熔炼并浇铸成的钢锭加工成自耗电极,之后将自耗电极置于真空自耗电弧炉中完成真空自耗结晶重熔工艺过程。均匀化处理:将自耗重熔以后浇铸成的钢锭置于热处理炉中,将热处理炉升温至1000-1200℃,保温15-25h。锻造处理:均匀化处理后的钢锭进行锻造加工,锻造初始温度为1000-1250℃,终锻温度为700-900℃。热处理:固溶处理830-870℃保温1-2h,空冷到室温;深冷处理:液氮 中保温5h以上;时效处理:480-520℃保温1-6h,空冷。本发明所述马氏体时效钢的制备工艺,其特征在于:所述超纯金属原材料中的杂质元素总含量(Si+Mn+P+S+O+N)%<0.1wt%。真空感应炉和真空自耗电弧炉的真空度均小于10-4Pa。所述锻造过程中的锻造比>10。本发明还提供了一种适用于所述马氏体时效钢的最优化的热处理工艺,其特征在于:850℃保温1.5h,空冷到室温,液氮中保温6h,500℃保温2h,空冷。本发明所述马氏体时效钢可以用于制备纺织钩针,包括以下步骤:真空熔炼—真空自耗—均匀化处理—锻造—热轧—冷轧—深冷处理—粗加工成型—时效处理—精加工成型。采用上述方法制得的纺织钩针,不仅具有优异的强韧性匹配,而且具有优异的耐摩擦磨损性能,可以很好的满足纺织工业的需求。本发明所述马氏体时效钢还可以用于制备撞针,包括以下步骤:真空熔炼—真空自耗—均匀化处理—锻造—热轧—深冷处理—粗加工—时效处理—精加工成型。采用上述方法制得的撞针,具有优异的抗疲劳性能和耐高温软化性能,可以很好的满足撞针服役条件对材料的性能要求。本发明所述马氏体时效钢具有高的强韧性匹配,其σb≥3000MPa,σ0.2≥2600MPa,δ≥9%,ψ≥30%,适用于对结构材料的强韧性要求苛刻的环境。本发明所述马氏体时效钢已成功应用于纺织钩针的制备中,制得的纺织钩针具有优异的使用性能,与传统材料制备的钩针相比,具有更低的使用成本。采用本发明所述马氏体时效钢制备的撞针其使用寿命是传统材料 撞针的10倍,具有优异的使用性能,具备广阔的应用前景。附图说明图1为实施例8制备得到的高性能钩针示意图。图2为实施例9制备得到的高性能撞针示意图。具体实施方式实施例1按下述名义成分(wt.%):C:0.008%,Ni:21.5%,Co:17.0%,Mo:7.5%,Ti:1.7%,O:0.01%,N:0.01%,P:0.01%,S:0.01%,Fe:余量,配料和混料后在真空感应熔炼炉中熔炼,浇铸成铸锭以后进行真空自耗以及均匀化处理,并按下述工艺进行热加工和热处理:(1)在奥氏体单相区锻造,锻造初始温度为1150℃,终锻温度为850℃,锻造比为12,锻造之后空冷到室温;(2)热处理制度按如下步骤进行,固溶处理(850℃保温1.5h,空冷到室温),深冷处理(液氮中保温6h),时效处理(500℃保温2h,空冷)。显微组织观察以及XRD分析表明,该合金成分的马氏体时效钢,经过热处理后的残余奥氏体含量较多。对其热处理态的材料进行力学性能检测,其力学性能为抗拉强度2755MPa,屈服强度为2532MPa,延伸率为9%,断面收缩率为35%。该合金成分的马氏体时效钢中的Ni含量高于权利要求1中Ni含量的上限值(20.0%),造成了钢中残余奥氏体含量过高,进而导致强度较低。实施例2按下述名义成分(wt.%):C:0.008%,Ni:19.0%,Co:14.0%,Mo:7.5%,Ti:1.7%,O:0.01%,N:0.01%,P:0.01%,S:0.01%,Fe:余量,配料和混料后在真空感应熔炼炉中熔炼,浇铸成铸锭以后进行真空自耗以及均匀化处理,并按实施例1所述的工艺进行热加工和热处理。对其热处理态的材料进行力学性能检测,其力学性能为抗拉强度2975MPa,屈服强度为2814MPa,延伸率为8%,断面收缩率为33%。材料的断裂韧性为K1C=23MPa.m1/2。该合金成分的马氏体时效钢的Co含量低于权利要求1中的钴含量的下限值15.0%,导致钢中的析出强化作用减弱,最终导致其强度降低。实施例3按下述名义成分(wt.%):C:0.008%,Ni:19.0%,Co:17.0%,Mo:7.5%,Ti:1.4%,O:0.01%,N:0.01%,P:0.01%,S:0.01%,Fe:余量,配料和混料后在真空感应熔炼炉中熔炼,浇铸成铸锭以后进行真空自耗以及均匀化处理,并按实施例1所述的工艺进行热加工和热处理。对其热处理态的材料进行力学性能检测,其力学性能为抗拉强度2915MPa,屈服强度为2794MPa,延伸率为9%,断面收缩率为35%。材料的断裂韧性为K1C=20MPa.m1/2。该合金成分的马氏体时效钢的Ti含量低于权利要求1中的钛含量的下限值1.5%,Ti是马氏体时效钢最主要的强化元素,其含量的降低会导致钢的强度降低。实施例4在实施例1-3的基础上,调整了Cr当量与Ni当量的比值,重新优化了合金成分。按下述名义成分(wt.%):C:0.008%,Ni:19.0%,Co:16.0%,Mo:7.2%,Ti:1.7%,O+N:0.004%,P:0.005%,S:0.005%,Fe:余量,配料和混料后在真空感应熔炼炉中熔炼,浇铸成铸锭以后加工成自耗电极并进行自耗重熔工艺以及均匀化处理,之后按实施例1所述的工艺进行热加工和热处理,并测试了不同时效处理条件下的室温拉伸性能,拉伸力学性能测试结果如表1所示。表1实施例4拉伸力学性能测试结果时效工艺抗拉强度,MPa屈服强度,MPa延伸率,%面缩,%480℃2h293328559.535480℃4h297428969.435480℃6h299229109.432500℃1h299428329.636500℃2h301529119.234500℃4h295228969.037根据表1所示的力学性能结果,得出该合金的最优化热处理工艺为:850℃保温1.5h,空冷到室温,液氮处理6h,500℃保温2h,空冷。经过最优化热处理工艺得到的峰时效态样品的断裂韧性为K1C=80MPa.m1/2。实施例5以实施例4的合金成分为基础,但与实施例4不同的是,在真空感应熔炼过程中的真空度高于权利要求5中要求的10-4Pa,且不进行后续的自耗 重熔工艺,最终会导致钢中的杂质元素P、S、O、N的含量偏高。按下述名义成分(wt.%):C:0.008%,Ni:19.0%,Co:16.0%,Mo:7.2%,Ti:1.7%,O:0.02%,N:0.02%,P:0.015%,S:0.015%,Fe:余量,配料和混料后在真空感应熔炼炉中熔炼,浇铸成铸锭以后直接进行均匀化处理,并按实施例1所述的工艺进行热加工和热处理。该合金成分的马氏体时效钢的杂质元素含量超过了权利要求1中杂质元素含量的上限值。在实施例4所述的最优化热处理工艺条件下,其力学性能为抗拉强度3020MPa,屈服强度为2920MPa,延伸率为9%,断面收缩率为30%,材料的断裂韧性为K1C=8MPa.m1/2。其拉伸性能与实施例4的拉伸性能相当,而断裂韧性远低于实施例4的断裂韧性,说明杂质元素含量过高会大大恶化材料的韧性。实施例6按下述名义成分(wt.%):C:0.008%,Ni:18.0%,Co:16.0%,Mo:7.0%,Ti:1.5%,O+N:0.004%,P:0.005%,S:0.005%,Fe:余量,配料和混料后在真空感应熔炼炉中熔炼,浇铸成铸锭以后加工成自耗电极并进行自耗重熔工艺以及均匀化处理,之后按实施例1所述的工艺进行热加工和热处理。对其热处理态的材料进行力学性能检测,其力学性能为抗拉强度3010MPa,屈服强度为2895MPa,延伸率为9.5%,断面收缩率为36%,断裂韧性K1C=85MPa.m1/2实施例7按下述名义成分(wt.%):C:0.008%,Ni:20.0%,Co:17.0%,Mo:7.5%,Ti:2.5%,O+N:0.004%,P:0.005%,S:0.005%,Fe:余量,配料和混料后在真空感应熔炼炉中熔炼,浇铸成铸锭以后加工成自耗电极并进行自耗重熔工艺以及均匀化处理,之后按实施例1所述的工艺进行热加工和热处理。对其热处理态的材料进行力学性能检测,其力学性能为抗拉强度3025MPa,屈服强度为2905MPa,延伸率为8%,断面收缩率为34%,断裂韧性K1C=50MPa.m1/2实施例8按照实施例4设计的合金成分进行配料,之后按如下步骤制备马氏体时效钢材料的高性能纺织钩针。真空熔炼:合金元素均以高纯度纯金属的形式加入,将配料置于真空感应炉中进行真空熔炼、Ca处理和真空脱气,之后浇铸成铸锭,熔炼过程中的真空度≤10-4Pa。真空自耗:将真空熔炼并浇铸成的钢锭加工成自耗电极,之后将自耗电极置于真空自耗电弧炉中完成真空自耗结晶重熔工艺过程,真空自耗过程的真空度≤10-4Pa。均匀化处理:将自耗重熔以后浇铸成的钢锭置于400℃的热处理炉中,将热处理炉升温至1200℃,保温20h。锻造处理:均匀化处理后的钢锭经锻造加工成60mm厚的热轧板坯, 锻造初始温度为1200℃,终锻温度为900℃。热轧步骤:将锻造后的热轧板坯加热到1150℃,首先在二辊轧机进行粗轧,经5道次轧制成7mm厚的中间坯;之后的精轧过程中,采用四辊轧机,将中间坯轧制成4mm厚钢板,终轧温度为800℃。冷轧步骤:将热轧得到的4mm厚热轧钢板在冷轧机上进行轧制,冷轧采用20辊冷轧机,经7道次轧制,终轧至1mm厚的钢带。深冷处理:将冷轧钢带在液氮(-196℃)中保温6h,然后将钢带从液氮中取出,恢复到室温。粗加工成型:以深冷处理后的钢带为原材料,根据产品的设计尺寸,保证足够的加工余量的前提下,将钢带粗加工成产品的坯料件。时效处理:将产品坯料件置于500℃的真空热处理炉中保温2h,取出恢复到室温。精加工成型:时效处理后的坯料件,按照产品尺寸精加工即可得到高性能马氏体时效钢纺织钩针。按上述工艺制备得到的马氏体时效钢纺织钩针具有优异的强韧性匹配,与传统材料T8制备的纺织钩针相比,服役寿命提高了5倍,其使用成本明显低于T8,已经成功替代传统材料并实现批量生产。实施例9按照实施例4设计的合金成分进行配料,之后按如下步骤制备马氏体时效钢材料的高性能撞针。真空熔炼:合金元素均以高纯度纯金属的形式加入,将配料置于真空 感应炉中进行真空熔炼、Ca处理和真空脱气,之后浇铸成铸锭,熔炼过程中的真空度≤10-4Pa。真空自耗:将真空熔炼并浇铸成的钢锭加工成自耗电极,之后将自耗电极置于真空自耗电弧炉中完成真空自耗结晶重熔工艺过程,真空自耗过程的真空度≤10-4Pa。均匀化处理:将自耗重熔以后浇铸成的钢锭置于400℃的热处理炉中,将热处理炉升温至1200℃,保温20h。锻造处理:均匀化处理后的钢锭经锻造加工成60mm厚的热轧板坯,锻造初始温度为1200℃,终锻温度为900℃,锻比为11。热轧步骤:将锻造后的热轧板坯加热到1150℃,首先在二辊轧机进行粗轧,经3道次轧制成20mm厚的中间坯;之后的精轧过程中,采用四辊轧机,将中间坯轧制成17mm厚钢板,终轧温度为800℃。深冷处理:将热轧钢板在液氮(-196℃)中保温6h,然后将热轧钢板从液氮中取出,恢复到室温。粗加工成型:以深冷处理后的热轧钢板为原材料,根据产品的设计尺寸,保证足够的加工余量的前提下,将热轧钢板粗加工成产品的坯料件。时效处理:将产品坯料件置于480-520℃的真空热处理炉中保温2h-4h,取出恢复到室温。精加工成型:时效处理后的坯料件,按照产品尺寸精加工即可得到高性能马氏体时效钢撞针。按上述工艺制备得到的马氏体时效钢材料撞针,经不同时效处理工艺后的性能差异较大,其实验测试结果如表2所示。表2实施例5撞针的测试结果时效处理工艺测试结果480℃2h60万次后失效,撞针弯曲480℃4h350万次后失效,撞针头部断裂500℃2h460万次后失效,撞针头部断裂500℃4h800万次后失效,撞针头部断裂520℃2h600万次后失效,撞针头部断裂520℃4h90万次后失效,撞针弯曲从表2可以看出,在时效处理工艺为500℃保温4h的条件下得到的撞针具有最优异的使用性能,其使用寿命是传统材料S7制备的撞针的10倍,具有很大的应用前景。上述实施例只为说明本发明的技术构思及特点,其目的在于让熟悉此项技术的人士能够了解本发明的内容并据以实施,并不能以此限制本发明的保护范围。凡根据本发明精神实质所作的等效变化或修饰,都应涵盖在本发明的保护范围之内。当前第1页1 2 3