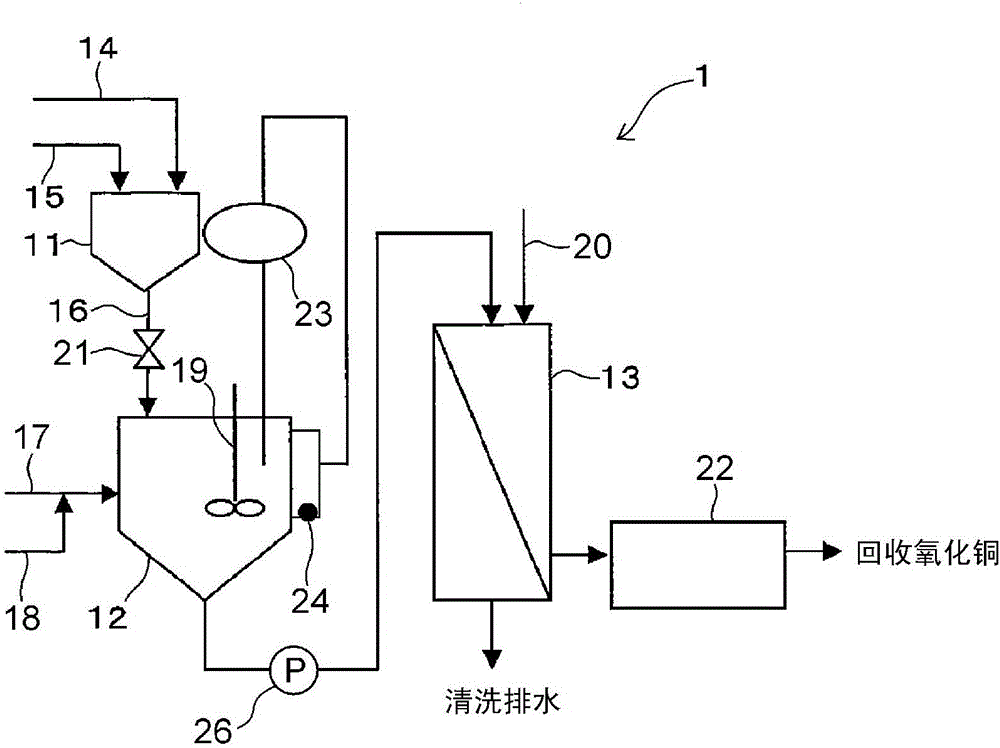
本发明涉及含铜酸性废液的处理方法,更详细地说,涉及例如对用氯化铜蚀刻液蚀刻铜印制电路板时产生的蚀刻废液、电解铜箔制造中的镀液的更新废液、在生产多层印制电路板时的层叠工序中的基板表面的粗化处理中产生的蚀刻废液等含有高浓度铜离子的含铜酸性废液进行中和处理,从含铜酸性废液中将铜以氧化铜的形式除去并回收的方法及其所用的装置。此外,本发明涉及通过对含铜酸性废液进行处理来生产氧化铜的氧化铜生产方法。
背景技术:
:作为以高浓度含有铜离子的酸性废液(以下称为“含铜酸性废液”),为人所知的有用氯化铜蚀刻液蚀刻铜印制电路板时产生的蚀刻废液及电解铜箔制造中的镀液的更新废液、在生产多层印制电路板时的层叠工序中的基板表面的粗化处理中产生的蚀刻废液等。这些废液一方面铜离子浓度高达5~20质量%(以下仅用“%”表示)的范围,另一方面共存的氯化物离子及硫酸根离子的浓度通常也高达5~30%。作为以含铜酸性废液为对象的铜的回收处理,有一部分利用离子化倾向之差,例如通过使其与铁废料反应来析出金属铜而进行回收的方法。但是,在该方法中,有废液中的铜回收率低的问题。此外,由于含有因与铜离子反应而溶出的铁离子和残留的铜离子的废液残留下来,所以该废液需要另行处理,难说是有效率的处理方法。此外,作为含铜酸性废液的通常的处理方法,为人所知的有通过添加氢氧化钠等碱性物质,以氢氧化物沉淀除去重金属类的处理方法,但该方法由于生成的淤泥的体积大,而且含水率高,因此难处理,不适合铜离子浓度高的含铜酸性废液的处理。另外,关于蚀刻废水,例如如日本特开2004-50096号公报(专利文献1)中公开的那样,尝试了通过添加碱使铜离子以铜氢氧化物的形式不溶化,进而通过添加氧化剂形成氧化铜进行回收的处理方法。但是,在作为氧化剂使用次氯酸盐及漂白粉等含有氯化物离子的氧化剂的情况下,有因添加后的液体中的氯化物离子浓度进一步提高而担心生成氯化铜和氧化铜的复盐或盐分混入淤泥中等问题,此外,在以高浓度废液为处理对象的情况下,回收的氧化铜中的杂质含量增多等要改进的地方比较多。在以含铜酸性废液为对象的铜回收处理方法中,开发了例如如日本专利4323668号公报(专利文献2)中所示的那样,从含铜酸性废液中回收碱性碳酸盐,不使含铜酸性废液中大量含有的硫酸根离子及氯化物离子等阴离子类混入回收的碱性碳酸铜中的技术。由于在再利用回收的铜化合物时,杂质浓度低的铜化合物的再利用的用途广,所以回收高纯度的碱性碳酸铜。本发明人先前发现了在按照日本专利4199821号公报(专利文献3)将含铜酸性废液和氧化剂混合后,添加到碱性溶液中,能够高效率地回收氧化铜的方法。根据该方法,通过将含铜酸性废液和氧化剂的混合液滴在碱性溶液中,可得到以氧化铜为主成分的固体物质。这样,通过将含铜酸性废液与氧化剂一同每次少量地混合在碱剂中,可一面得到适当的稀释效果,一面对含铜酸性废液进行中和,使含在含铜酸性废液中的铜离子氧化,形成氧化铜。可是,根据发明者的试验,用该方法回收的氧化铜中的氯含有率有时达到200mg/kg左右,根据回收氧化铜的用途的不同,有时要求进一步降低氯含有率。现有技术文献专利文献专利文献1:日本特开2004-50096号公报专利文献2:日本专利4323668号公报专利文献3:日本专利4199821号公报技术实现要素:发明所要解决的课题本发明是为解决上述课题而完成的,其目的在于提供一种通过对含铜酸性废液进行处理能够高效率地回收氧化铜,同时能够使回收的氧化铜中的阴离子含有率降低的含铜酸性废液的处理方法、从含铜酸性废液中回收氧化铜的方法及装置。用于解决课题的装置为达到上述目的,本发明涉及一种含铜酸性废液的处理方法,其特征在于:在将含铜酸性废液和氧化剂混合后,一边将该混合液添加到碱剂中,一边进行管理使混合液加入后的碱剂溶液的pH即使暂时也不会降低至7以下,从而回收以生成的氧化铜作为主成分的固体物质,其中,在预先稀释碱剂而调节了浓度后,将所述混合液添加到碱剂中,或在预先稀释碱剂而调节了浓度、并将稀释了的碱剂加温后,将所述混合液添加到碱剂中。这里,所谓预先稀释碱剂,意味着只要是在将混合液添加到碱剂中之前,无论何时、何地稀释何种形态的碱剂(液体状或固体状的碱剂)都可以。也就是说,既可以在购入碱剂时稀释,也可以在固体状碱剂的溶解时稀释,还可以获得稀释到规定浓度的碱剂来使用。根据本发明的一方案,其特征在于:作为碱剂使用氢氧化钠溶液。根据本发明的一方案,其特征在于:作为碱剂使用含有氢氧化钠和碳酸钠的溶液。根据本发明的一方案,其特征在于:作为碱剂使用碳酸钠溶液。根据本发明的一方案,其特征在于:将氢氧化钠溶液的浓度设定为6质量%以下。根据本发明的一方案,其特征在于:将氢氧化钠溶液的浓度设定为0.2质量%以下且将碳酸钠的浓度设定为1.1质量%以下。根据本发明的一方案,其特征在于:将碱剂的温度设定为70℃以上。本发明涉及一种从含铜酸性废液中回收铜的装置,其特征在于,所述从含铜酸性废液中回收铜的装置具备:混合槽,用于混合含铜酸性废液和氧化剂;加入机构,用于从混合槽将混合液加入到反应槽中,使混合液加入后的碱剂溶液的pH即使暂时也不会降低至7以下;反应槽,用于使混合液和碱剂溶液反应而生成以氧化铜为主成分的固体物质;碱剂供给机构,用于向反应槽供给碱剂;以及固液分离装置,用于对反应槽中生成的固体物质进行分离回收;所述反应槽和所述固液分离装置以可输送含有固体物质的液体的方式连通,其中,通过设置稀释液供给机构稀释碱剂而调节浓度;在所述反应槽或所述碱剂供给机构中设置碱剂加温机构,对稀释了的碱剂进行加温。本发明涉及一种从含铜酸性废液生产氧化铜的方法,其特征在于:将含铜酸性废液和氧化剂混合,一边将含铜酸性废液和氧化剂的混合液添加到碱剂中,一边进行管理使混合液加入后的碱剂溶液的pH即使暂时也不会降低至7以下,从而回收以生成的氧化铜为主成分的固体物质,其中,在预先稀释碱剂而调节了浓度后,将所述混合液添加到稀释后的碱剂中,或在预先稀释碱剂而调节了浓度、并将其加温后,将所述混合液添加到稀释并加温后的碱剂中。发明的效果根据本发明,能够不稀释地直接对因生成复盐或氢氧化铜而难处理的、铜离子的含有浓度为5~20%的高浓度含铜酸性废液进行处理。此外,来自含铜酸性废液的回收物由于以氧化铜为主成分,所以与复盐及氢氧化铜不同,其脱水性好,能够降低含在回收的氧化铜中的杂质的浓度。另外,因回收物的氯含有率低,因而能够得到容易再利用这种形态的氧化铜。附图说明图1是表示本发明的铜回收装置的一个样式的图示。图2是表示本发明的铜回收装置的另一样式的图示。图3是表示本发明的铜回收装置的又一样式的图示。具体实施方式本发明的处理工艺在最初是稀释碱剂。接着,混合含铜酸性废液和氧化剂,将得到的混合液加入稀释了的碱剂中,从而生成固体物质。本发明中成为处理对象的含铜酸性废液能够以10000mg/L以上的浓度含有离子状的铜,并且呈酸性。即使铜离子浓度低于10000mg/L,也可进行本发明的处理,但在铜离子浓度低的情况下,得到的氧化铜的量减小。因此,考虑到得到的回收物的量,优选应用于经济上相称的废液。此外,即使含有高浓度的离子状的铜,但在液性为中性或碱性的情况下,有时以不使铜离子沉淀的方式含有螯合剂。含有这样的螯合剂的废液因认为螯合剂阻碍铜的氧化而不适合本发明。作为含铜酸性废液,具体地说,可列举出印制电路板的蚀刻处理工序中产生的氯化铜蚀刻废液、或电镀铜处理工序中产生的硫酸铜镀液废液。这些废液以10~150g/L的范围含有离子状的铜,因pH为1以下而适合本发明。此外,因废液中的铜离子浓度高而使可回收的氧化铜的量提高。作为本发明中使用的氧化剂,只要能将二价的铜离子形成氧化铜,就没有特别的限定,但作为对回收后的氧化铜的性状不产生不良影响的氧化剂,过氧化氢是合适的。作为本发明中使用的碱剂,只要可以对含铜酸性废液进行中和,就没有特别的限定,但考虑到如果反应后残留的阴离子形成不溶性的盐,则可能导致回收的氧化铜的纯度下降,所以优选使用碱金属的氢氧化物作为碱剂。具体可列举出容易廉价地得到的氢氧化钠的水溶液。此外,也可将碱金属的氢氧化物与碱金属的碳酸盐混合作为碱剂使用。此外,也可以代替碱金属的氢氧化物而使用碱金属的碳酸盐作为碱剂。由于对降低回收物的杂质浓度有效,还可使用例如碳酸钠的水溶液。在本发明中,由于对高浓度的含铜酸性废液不稀释地进行处理,所以按上述步骤使其反应是重要的。因此,以下以作为氧化剂溶液使用双氧水、作为碱剂使用氢氧化钠时为例,对本发明中的处理的步骤、混合及反应顺序的重要性进行说明。首先,在以往的一般的处理方法即在含铜酸性废液中加入碱剂的方式中,在对以高浓度含有铜离子的含铜酸性废液进行处理时,在含铜酸性废液中加入碱剂。可是,在高浓度的含铜酸性废液中加入碱剂的顺序中,生成复盐CuCl2·3Cu(OH)2或氢氧化铜。其中,复盐由于含水率高且脱水困难,并含有氯,因而使含有复盐的氧化铜在回收后难以照原样进行再利用。此外,氢氧化铜在高浓度生成时,含水率也高,处理困难,不适合再利用。此外,在将以高浓度含有铜离子的含铜酸性废液加入碱剂中后添加双氧水时,最初,含水率高的污泥状的复盐或氢氧化铜在碱剂中析出并蓄积。如果然后在其中加入双氧水,则液中析出的复盐或氢氧化铜难于以污泥状的固体进行分散,因此尽管复盐或氢氧化铜的表面被过氧化氢所氧化,但复盐或氢氧化铜内部的氧化延迟,或者没有均匀地氧化到复盐或氢氧化铜内部,所以使利用过氧化氢进行的氧化反应的效率降低。此外,氯化铜蚀刻废液在蚀刻处理的过程中,蚀刻液内的二价的铜离子被还原成一价,有时含有亚铜离子。在直接将这样的蚀刻废液加入碱剂中时,除了氢氧化铜以外,溶解性低的氯化亚铜(CuCl)也析出。在此种状态下,即使加入双氧水,由于该氯化亚铜(CuCl)作为过氧化氢的分解催化剂起作用,因此在对氧化铜的生成的贡献并不充分的状况下消费掉过氧化氢,从而使利用过氧化氢进行的氧化反应的效率进一步降低。为了避免以上那样的问题,在本发明的处理工艺中,在与碱剂溶液(稀释的碱剂溶液)混合、反应之前,使含铜酸性废液和双氧水混合是重要的。由此,含在废液中的二价铜离子向氧化铜的氧化反应在将含铜酸性废液和双氧水的混合液加入碱剂中时迅速地进行。此外,在废液中含有亚铜离子的情况下,通过在与碱剂接触前和过氧化氢混合,从而在过氧化氢的氧化作用下,亚铜离子被氧化成二价铜离子,因此能够回避溶解性低的氯化亚铜(CuCl)等亚铜盐的析出。在本发明中,混合含铜废液和双氧水所需要的时间也取决于要混合的两者的浓度,但在两者为高浓度时,亚铜离子即使在5秒左右的短时间内也以相当的比例被氧化,在20秒左右时充分地进行氧化反应。另一方面,如果混合含铜酸性废液和双氧水,则以铜离子作为催化剂进行过氧化氢的分解反应。该分解反应从将两者混合后在大约经过60秒的时刻开始明显化,在经过7分钟~10分钟后,一边伴有显著的发泡一边激烈地进行。虽取决于要混合的两者的浓度,但在例如相对于铜离子按摩尔浓度混合2倍量的过氧化氢时,伴随着过氧化氢分解的发泡在经过20分钟后减少,在经过25分钟后达到微量,在此时刻加入碱剂中的情况下,与氧化铜相比生成含有较多氢氧化铜的沉淀物。因此,在加入碱剂中之前,作为含铜酸性废液和双氧水的混合、反应时间,可选择5秒钟~20分钟左右的时间,优选选择20秒钟~7分钟左右的时间。此外,如果相对于用于反应的含铜酸性废液的总量一次添加必要量的双氧水的总量,则有时两者的液量增多,过氧化氢急剧地分解,混合液激烈地发泡,同时液温急剧地上升。在此种情况下,可发生起因于过氧化氢的激烈的分解反应的事故,因此含铜酸性废液和双氧水只混合1次加入操作所使用的量,在发泡达到激烈之前必须结束加入操作。作为上述的含铜废液和双氧水的混合方法,例如可采用在混合槽内加入两种液体而进行搅拌的方法及使含铜废液和双氧水合流而进行混合的方法等。其中,在向混合用的槽内注入两种液体而进行搅拌的方法中,注入量的确认和调整是容易的。此外,如果在槽内设置溢流管,则具有的优点是:即使在混合时发泡,也由于为开放体系,因而能够防止槽爆炸等装置上的问题。此外,在使含铜废液和双氧水合流而进行混合的方法中,可使用通过Y字形管等连接两溶液的管道而使其合流的方法、向某一管道内注入另一方的液体而进行混合的方法等。另外,通过在合流后经过静态混合器也能够对两种液体进行搅拌混合。在该方法中,为了对发泡进行处置需要装置的耐压性、或能够排出发生的气体的机构,但具有能够均匀地维持从将两种液体混合后到供给的时间、且能够连续地供给的优点。接着,虽是含铜废液和双氧水的混合液(以下简称为“混合液”)与碱剂的反应,但为了避免生成复盐,在铜离子的浓度稀薄的条件下使其反应是必要的。此外,为了快速地进行铜离子的氧化反应,优选在过氧化氢的反应性高的强碱性条件下使其反应。为了实现这些条件,在本发明的技术中,使用操作性好的溶液状的碱剂,在搅拌该碱剂溶液时以适当的速度加入所述混合液是必要的。在加入后的碱剂溶液中,以其pH即使暂时也不下降到7以下的方式一边管理该加入速度,一边加入、混合,逐渐使反应进展及完结是必要的。对本发明中使用的碱剂进行预先稀释是重要的。在作为碱剂使用氢氧化钠时,氢氧化钠溶液通常以浓度在25质量%以上的高浓度出售。本发明中不直接使用碱剂,而是在将其稀释后用于反应。通过将稀释的碱剂用于反应,能够降低以回收的氧化铜为主成分的固体物质(以下简称为回收氧化铜)中的氯含有率。例如,在使用浓度为25质量%的氢氧化钠溶液时,则通过按容积比稀释至5倍,使浓度大约为6质量%,回收氧化铜的氯含有率大约降低4成左右。关于碱剂的稀释,既可以通过向反应槽供给碱剂、然后从稀释水供给管向盛有碱剂的反应槽中供给水来进行稀释,也可以在与反应槽不同的贮槽中稀释碱剂,还可以在调整市售的碱剂时调整浓度以达到规定的稀释度。稀释中所用的水必须为氯浓度低的水,可使用自来水、离子交换处理水。此外,也可以再利用对以回收的氧化铜为主成分的固体物质进行清洗的工序中发生的氯浓度低的清洗排水。在通过离子交换处理或反渗透膜处理将清洗排水脱盐(desalination)后,也可以用作稀释水。在再利用清洗排水时,为了防止杂质向以氧化铜为主成分的固体物质中的混入等再污染,可使用将有机物或氯、金属类等杂质除去后的再生水作为稀释水。此外,如果作为碱剂使用浓度为25质量%的氢氧化钠溶液和浓度为15质量%的碳酸钠溶液的混合液,则与单独使用氢氧化钠溶液时相比,以回收的氧化铜为主成分的固体物质中的氯含有率进一步降低。在需要低氯含有率的氧化铜的情况下为有效的手法。即使在采用氢氧化钠和碳酸钠的混合液时,通过稀释碱剂也能使回收氧化铜的氯含有率降低。因此,优选根据回收的氧化铜所要求的品质来确定稀释倍率。在本发明中,通过对碱剂进行预先加温而使以回收的氧化铜为主成分的固体物质中的氯含有率降低。已知一般来讲氢氧化铜在60℃以上通过自氧化而变化成氧化铜。因此,废液中的铜离子在处理反应过程中即使形成氢氧化铜的形态,只要碱剂的温度为60℃以上,也容易自氧化成氧化铜,可以认为这是因为难引入存在于反应液中的氯化物离子。此外,从实验结果得知,通过对碱剂进行加热,可使回收的氧化铜的氯含有率降低,该效果在碱剂的温度为70℃以上时可以明显看到,因此在本发明中优选将碱剂加热至70℃以上。为了对碱剂进行加温,既可以在盛有碱剂的反应槽中设置加热器,也可以作为碱剂的加温槽与反应槽分开设置,准备用于反应槽内的反应中接着的反应的碱剂并进行加热,也可以在碱剂的供给管道中设置加热器。作为含铜酸性废液和氧化剂的混合液向碱剂中加入的方法,例如可采用向盛有碱剂的反应槽中滴加混合液的方法、及通过管道将混合液注入碱剂液中的方法等。在向反应槽中滴加含铜酸性废液和氧化剂的混合液的方法中,具有能够用肉眼确认供给状况,在供给状况不稳定时容易采取对策的优点。另一方面,在通过管道向液体中供给的方法中,与从液体表面供给时相比,具有能够向可良好地进行混合的位置供给的优点。在混合含铜酸性废液和氧化剂的混合槽与反应槽相比充分小的情况下,通过与每1次相对应地分批注入混合槽,可用简易的设备进行。再者,在通过管道向液中注入的方法中,可以优选采用连续地添加由含铜废液和过氧化氢溶液合流而成的混合液的方法。另外,作为以碱剂溶液内pH即使暂时也不会降低至7以下的方式一边管理一边加入、混合混合液的方法,例如可列举出向处于搅拌混合状态的碱剂溶液中,间隔地断续加入少量混合液的方法及每次少量地连续加入混合液的方法。此时,混合液相对于碱剂溶液的加入量只要最终的反应结束时的pH为7以上,就可在后述的一定的范围内任意地调节。可是,如果在碱剂中加入含铜酸性废液,使pH降低到接近pH7,则以回收的氧化铜为主成分的固体物质中的氯含有率有时增高,优选与要求的氧化铜的质量相适应地调整成为反应终点的pH。在本发明中,处理中所用的双氧水的浓度没有特别的限定,例如可直接使用浓度为30%的双氧水。根据以上说明的本发明技术,含铜酸性废液在处理后得到的固体物质以氧化铜为主成分,呈现出固液分离比较容易、且脱水性也比较好的性状。但是,在为含有高浓度铜离子的含铜酸性废液的情况下,由于将浓酸与碱混合进行处理,所以反应结束时的固体物质中还共存由中和反应而产生的高浓度的盐类。于是,在以再利用为目的回收固体物质时,通过多次重复水洗对这些盐类进行冲洗,作为提高回收物的纯度的措施是有效的。作为此时的固液分离方法,例如可采用过滤分离、离心分离、沉降分离等。此外,作为用于对盐类进行冲洗的清洗水,可以使用盐类含量低的清澈的水,例如自来水或工业用水等,但取而代之,再利用通过对处理过的液体进行固液分离而得到的分离液、通过水洗对固体物质进行冲洗所得到的清洗排水、和/或对通过固液分离而得到的分离液等进行脱盐处理而得到的处理水也是有效的。再者,作为此时的脱盐处理方法,例如可以适用膜过滤法及减压蒸馏法、电渗析法等。接着,参照附图对用于实施本发明方法所使用的回收装置进行说明。图1是表示实施本发明时的铜回收装置的一个样式的系统图。图中,11表示混合槽,12表示反应槽,13表示固液分离装置,14表示含铜酸性废液管道,15表示氧化剂供给管道,16表示混合液供给管道,17表示碱剂供给管道,18表示稀释水供给管道,19表示搅拌机,20表示清洗水供给管道,21表示阀门,22表示脱水装置,23表示温度计,24表示加热器。在图2及图3中,对于同一构成要素标注同一符号,并将重复的说明予以省略。图1所示的铜回收装置1具备带有搅拌机19的反应槽12、与反应槽12连通的固液分离装置13。在反应槽12的上部设有混合槽11,通过混合液供给管道16与反应槽12连接,形成可将混合槽11内的含铜酸性废液和氧化剂的混合液加入到反应槽12中的结构。含铜酸性废液管道14和氧化剂供给管道15与混合槽11连接,形成可在混合槽11内混合含铜酸性废液和氧化剂的结构。在混合液供给管道16上设有阀门21,形成可任意地控制混合液的供给的结构。从碱剂供给管道17向反应槽12中供给碱剂。此外,从稀释水供给管道18供给用于稀释碱剂的水。反应槽12具备温度计23和加热器24,形成能对供给的碱剂的稀释液进行加温、并维持在规定温度的结构。为了将碱剂加温至70℃以上的任意温度,为了使温度保持恒定,优选加热器24具备温度调节功能。此外,为了防止液温下降,也可根据需要在反应槽12上缠绕隔热材料来形成保温结构。由于在反应槽12中向碱剂供给酸,因而一并进行中和反应。由于中和反应为发热反应,所以一般认为温度将过于上升。因此,反应槽12的加温装置中通过采用水套,也可以形成在温度过于上升时可供给冷却水的结构。再者,在由碱剂供给管道17向反应槽12供给预先稀释过的碱剂的情况下,可将稀释水供给管道18的设置省略。图2是表示实施本发明时的铜回收装置的另一样式的系统图。图2中,反应槽12的局部与图1所示的形态不同。为了对碱剂进行加温而在反应槽12中设置碱剂加温槽25,在向反应槽12供给碱剂之前,预先对碱剂进行加温。在碱剂加温槽25中一边对从碱剂供给管道17供给的碱剂和从稀释水供给管道18供给的稀释水进行混合一边加温至设定的温度。加温至设定的温度的碱剂向反应槽12供给。当如图2所示那样设置碱剂加温槽25时,则可在反应槽12内的反应中一并进行碱剂的加温。因此,在反应结束后,在从反应槽12输送生成的氧化铜泥浆后,可立即将新加温的碱剂供给至反应槽12,从而可提高处理设备的运转率。图3是表示实施本发明时的铜回收装置的又一样式的系统图。图3中,反应槽12的部分与图1、图2所示的形态不同。为了对碱剂进行加温,在将碱剂供给管道17和稀释水供给管道18连接成1根的管道中设置加热器24,形成能够对碱剂进行加温的结构。在图3所示的回收装置1中,没有设置碱剂加温槽25(参照图2)而能对碱剂进行加温,但加热器24需要具有与碱剂及稀释水的流量相应的能力。以该反应槽12中生成的氧化铜为主体的固体物质通过输送泵26被输送至固液分离装置13中,在固液分离装置13中分离成固体物质和上清水。然后,再用从清洗水供给管道20供给的清洗水进行清洗,然后进行再利用。在图1~图3所示的装置中,各自在混合槽11的上部设有含铜酸性废液管道14和氧化剂供给管道15,在该混合槽11内充分混合后,通过混合液管道16加入到反应槽12中。再者,在不设置混合槽11而使含铜酸性废液管道14和氧化剂供给管道15连结时,也能从连结的管道直接向反应槽12中供给混合液。上述混合槽11由于不能长时间地保持氧化剂的氧化力,因而不需要能一次收容应处理的含铜酸性废液和加入其中的氧化剂的容量,只要是能收容分割处理的含铜酸性废液和加入该废液中的对应数量的氧化剂的容量即可。在利用图1~图3所示的装置时,相对于供给1次反应的含铜酸性废液量,需要采用适当量的氧化剂量和碱剂量。氧化剂量相对于含铜酸性废液中的铜量优选设定在按摩尔比为当量以上那样的量。此外,碱剂量由于需要使反应结束时刻的pH在7以上,所以优选预先通过小规模试验来确定对一定量的含铜酸性废液进行中和所需的碱剂量,以该量比为基础确定碱剂量。此外,根据本发明,在预先稀释碱剂而调节了浓度后,将碱剂用于反应。通过采用这样的步骤,能够使回收氧化铜的氯含有率降低,但如后述的实施例中所示的那样,回收氧化铜的氯含有率随着稀释程度的变化而变化。因此,优选预先采用小规模试验确定好满足所要求的氯含有率的碱剂的稀释倍率或碱剂浓度。如上所述,在本发明中,通过将含铜酸性废液和氧化剂的混合液每次少量地加入到稀释完毕的碱剂中,可一边得到稀释效果一边使铜氧化。因此,优选将混合液间歇地供给碱剂中。在此种情况下,例如将用于1次反应的含铜酸性废液量的1/8量和与此相称的氧化剂供给至混合槽11,在进行了混合后,打开阀门21,向反应槽12供给。在此种情况下,预先在反应前向反应槽12供给碱剂,在稀释至规定的稀释倍率后,加温至70℃以上,由此可向被稀释及加温的碱剂中供给混合液。重复含铜酸性废液和氧化剂的混合液的加入操作,在对规定量的含铜酸性废液全部进行了处理后结束反应。将反应槽12中生成的氧化铜供给至固液分离装置13,分离成氧化铜和含高浓度盐的液体。氧化铜照原样残留在固液分离装置13内,通过通入纯水进行清洗操作可提高氧化铜的纯度。将清洗后的氧化铜供给至脱水装置22进行脱水,从而以氧化铜的形式进行回收。在本发明的铜回收装置中,由于作为清洗水通常使用盐类含量低的清澈水,例如自来水及工业用水等,但也可以取而代之,或者作为它的一部分使用通过反应而得到的上清水、或清洗排水及通过用脱盐装置对来自脱水装置的脱水滤液进行处理而得到的脱盐处理水,所以在考虑到后续的废水处理的情况下是有效的。(实施例1)在实施例1中,对从印制电路板制造工序排出的氯化铜蚀刻废液进行了处理。该废液为铜离子浓度大约为140g/L的盐酸酸性性状。此外,作为碱剂使用浓度为25质量%的氢氧化钠溶液,作为氧化剂使用浓度为30质量%的双氧水。关于废液的添加量,在将对使用的碱剂1000mL进行中和所需的废液量规定为1当量时,使用达到0.9当量、0.8当量、0.5当量这样的量。表1中示出了以回收的氧化铜为主成分的固体物质中的氯含有率和生成的泥浆中的溶解性铜离子浓度。表1废液加入量0.9当量0.8当量0.5当量氯含有率(mg/kg)13011767生成泥浆中的溶解性铜浓度(mg/L)0.61.623.9可以确认有通过降低废液相对于碱剂量的加入量而使回收氧化铜的氯含有率降低的倾向。另一方面,生成泥浆中的溶解性铜离子浓度,在废液的加入量为0.5当量时大约残留24mg/L,从降低溶解于生成泥浆中残留的铜的浓度的观点出发,废液的加入量最好限于0.8当量。(实施例2)在实施例2中,对从印制电路板制造工厂排出的氯化铜蚀刻废液进行了处理。该废液是铜离子浓度大约为140g/L的酸性废液。此外,作为碱剂使用浓度为25质量%的氢氧化钠溶液,作为氧化剂使用浓度为30质量%的双氧水。关于废液的添加量,在将对使用的碱剂1000mL进行中和所需的废液量规定为1当量时,采用达到0.8当量的量,将反应开始温度设定在25℃、60℃、70℃、80℃。表2中示出了以回收的氧化铜为主成分的固体物质中的氯含有率。表2反应开始温度25℃60℃70℃80℃氯含有率(mg/kg)1801579893回收的氧化铜的氯含有率在60℃时为157mg/kg,但在70℃、80℃时降低至100mg/kg以下。确认通过如此提高反应开始温度可使氯含有率降低,反应开始温度在70℃以上是合适的。由表2的结果表明:氯含有率随着反应开始温度的上升而降低,但作为反应开始温度的上限,考虑到装置的限制及安全性,90℃是妥当的。(实施例3)在实施例3中,对与实施例1及实施例2不同的从印制电路板制造工序排出的氯化铜蚀刻废液进行了处理。该废液为铜离子浓度大约为126g/L的酸性废液。此外,作为碱剂使用浓度为25质量%的氢氧化钠溶液,作为氧化剂使用浓度为30质量%的双氧水。处理条件如表3所示。表3在实施例3中,对未稀释地使用480mL碱剂的对照体系和按容积比分别以达到2倍、5倍、10倍的方式稀释的稀释体系进行了处理。稀释体系中的氢氧化钠浓度分别相当于大约14、6、3质量%的浓度。此外,关于氯化铜蚀刻废液的供给量,在将对使用的480mL的碱剂进行中和所需的氯化铜蚀刻废液量规定为1当量时,将0.8当量的氯化铜蚀刻废液供于反应。将每次加入操作的氯化铜蚀刻废液的供给量设定在62.5mL,将氧化剂量设定在大约15mL。在将碱剂预先加温至80℃后开始反应。在将氯化铜蚀刻废液和氧化剂混合后用大约3分钟加入碱剂中,加入后搅拌3分钟。将该加入操作合计重复8次。表4中示出了对得到的黒色氧化铜泥浆进行分析所得的结果。生成泥浆SS表示泥浆中的固体物质浓度。关于回收氧化铜的氯含有率,对照体系为145mg/kg,与此相对照,在5倍稀释体系中降低到98mg/kg,在10倍稀释体系中降低到82mg/kg,由此可以确认如下的效果:通过稀释碱剂,将碱剂浓度调整至较低,能够降低回收氧化铜的氯含有率。表4本发明中,可以认为碱剂的稀释倍率越高即碱剂浓度越低,回收氧化铜的氯含有率越降低,即使稀释倍率超过10倍,也能期待回收氧化铜的氯含有率降低。可是,如果提高稀释倍率,则从装置尺寸的制约及招致排水量的增加的观点出发而确定稀释倍率的上限。(实施例4)在实施例4中,作为处理的废液使用与实施例1及实施例2中所使用的废液相同的氯化铜蚀刻废液(铜离子浓度大约为140g/L)。此外,作为碱剂使用按容积比为25∶75的比例混合浓度为25质量%的氢氧化钠溶液和浓度为15质量%的碳酸钠溶液而成的混合碱剂。处理条件如表5所示。处理步骤与实施例1同样地进行。表5表6中示出了在表5所示的处理条件下进行的结果。在实施例4中,与实施例3相比较,回收氧化铜的氯含有率整体都较低,由此确认氢氧化钠和碳酸钠的混合碱剂对于降低氯含有率是有效的。此外,确认回收氧化铜的氯含有率随着碱剂的稀释倍率的增加而下降,在使用混合碱剂时也具有碱剂的稀释效果。表6以上,对本发明的实施方式进行了说明,但本发明并不限定于上述的实施方式,当然能在其技术思想的范围内以各种不同的方式加以实施,当然可在不脱离发明主旨的范围内进行各种变更。产业上的可利用性本发明涉及含铜酸性废液的处理方法,更详细地说,能够在例如对用氯化铜蚀刻液蚀刻铜印制电路板时产生的蚀刻废液、电解铜箔制造中的镀液的更新废液、在生产多层印制电路板时的层叠工序中的基板表面的粗化处理中产生的蚀刻废液等含有高浓度铜离子的含铜酸性废液进行中和处理,从含铜酸性废液中将铜以氧化铜的形式除去并回收的方法及其所用的装置中加以应用。符号说明:1铜回收装置11混合槽12反应槽13固液分离装置14含铜酸性废液管道15氧化剂供给管道16混合液供给管道17碱剂供给管道18稀释水供给管道19搅拌机20清洗水供给管道21阀门22脱水装置23温度计24加热器25碱剂加温槽26输送泵当前第1页1 2 3