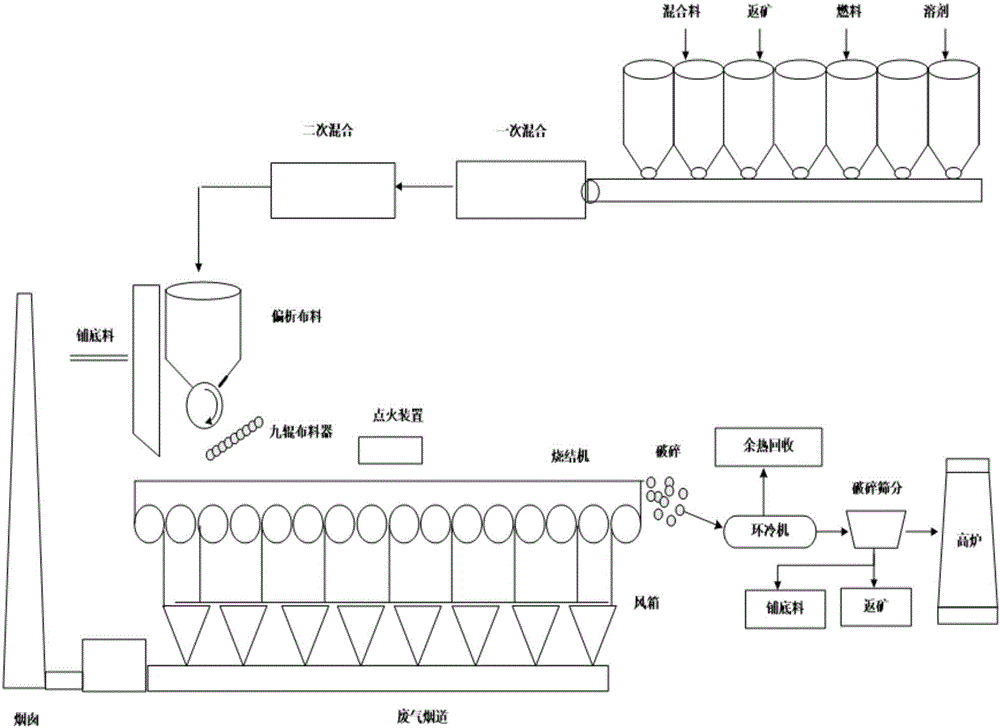
本发明涉及钢铁烧结过程生产节能降耗领域,尤其涉及一种基于风箱废气温度的烧结矿成品率预测方法。
背景技术:
:钢铁工业是国民经济支柱产业之一,钢铁工业的发展也将决定我国国民经济的发展。钢铁已广泛用于国防、交通、建筑、机械制造、汽车等工业,在国民经济发展中具有十分重要的战略地位。铁矿粉烧结是钢铁生产过程中的重要环节之一,是保证高炉获得优质烧结矿的关键所在,其向含铁的矿石原料中添加一定量的燃料和溶剂,经过混合制粒后平铺在烧结机上进行烧结点火,使混合料在高温条件下发生一系列的物理和化学反应,产生的优质含铁烧结矿是高炉生产的主要原料。在钢铁生产中,烧结矿的质量和产量影响钢铁的质量和产量,制约着企业经济生产效益的增长。烧结矿成品率的预测方法有利于提前预测烧结矿的产量,从而实现提前调整原料参数、设备参数和烧结操作参数,对于提高烧结矿的质量和产量具有重要的作用。钢铁生产工序多、工艺流程长,烧结工艺主要包括:烧结配料、混合制粒、偏析布料、点火燃烧、热矿破碎、冷却筛分等工艺环节。目前,烧结过程中所使用的烧结机一般都是带式抽风烧结机,由布料机构、主机、点火器、大烟道、水封拉链机等组成。烧结过程的工艺流程见附图1。烧结生产过程中,混合料中燃料燃烧提供的高温环境(热状态)是影响烧结矿质量和产量的最重要的过程参数,对其准确识别是预测烧结矿的质量和产量关键。烧结过程中混合料所处环境温度的高低、高温环境保持时间的长短和混合料完成烧结过程所处的位置,都会影响烧结矿的成品率和质量。烧结料层的分层现象见附图2。目前,烧结生产过程中工人主要是通过烧结终点温度和位置进行预测烧结矿成品率,根据检测结果来调整燃料配入量和烧结机速度,但是这种检测方式往往是在混合料烧结完成后才能进行,具有一定的滞后性,同时仅仅根据烧结终点时刻的温度信息,不能够全面地反应混合料在整个烧结过程中的热状态;而且这种预测主要是通过控制烧结终点温度和位置处在一定的范围内,从而判断烧结矿的质量和产量的情况,并没有直接对烧结矿成品率进行预测。因此,通过烧结过程热状态来直接预测烧结矿的成品率对高炉炼铁具有重要的意义。技术实现要素:有鉴于此,本发明的实施例提供了一种能对烧结过程烧结矿的成品率进行准确预测的基于风箱废气温度的烧结矿成品率预测方法。本发明的实施例提供一种基于风箱废气温度的烧结矿成品率预测方法,包括以下步骤:(1)根据烧结矿的烧结过程确定影响烧结矿的成品率的热状态参数;(2)对影响烧结过程的烧结参数的历史生产数据进行零相位滤波和时序配准处理,并对所述历史生产数据进行采样处理,建立历史生产数据样本数据库;(3)利用所述历史生产数据样本数据库计算已烧结矿的成品率;(4)采用多项式拟合法对所述历史生产数据样本数据库中的风箱废气温度数据进行曲线拟合得到一个拟合函数,通过对所述拟合函数进行微分求极值,得到热状态参数的数值;(5)以步骤(4)得到的热状态参数的数值作为输入变量,以步骤(3)得到的已烧结矿的成品率作为输出变量进行重复计算和验证,建立烧结矿成品率预测模型;(6)采用多项式拟合法对待预测矿的风箱废气温度数据进行曲线拟合并通过微分求极值法得到待预测矿的热状态参数的数值;(7)将步骤(6)得到的待预测矿的热状态参数的数值作为输入变量输入烧结矿成品率预测模型,所述烧结矿成品率预测模型的输出变量即为待预测矿的成品率。进一步地,所述步骤(1)中,热状态参数通过分析烧结过程的机理得到,分析确定影响烧结矿的成品率的热状态参数包括风箱高温温度、高温保持时间、烧结终点温度和烧结终点位置。进一步地,所述烧结参数包括风箱废气温度、台车速度、小成矿、返矿和大成矿。进一步地,所述步骤(2)中,选定采样周期对历史生产数据进行采样处理,所述采样周期为大成矿的波动周期,所述大成矿的波动周期为45min。进一步地,烧结矿的成品率是指烧结过程结束后,成品烧结矿占烧结饼的比重,所述烧结矿的成品率的计算公式如下:式中:ρ表示烧结矿的成品率(%),QD表示烧结的大成矿产量(Kg/h),QX表示烧结的小成矿产量(Kg/h),QF表示烧结的返矿量(Kg/h);所述大成矿产量、小成矿产量和返矿量的数据从历史生产数据样本数据库中获得。进一步地,所述得到热状态参数的数值包括以下步骤:(4.1)从所述历史生产数据样本数据库中选取风箱废气温度数据样本,设风箱数目为M,用(Xi,T(Xi))表示一个样本数据,i=1,2…M,Xi表示第i个风箱离点火处的距离,T(Xi)表示离点火处距离为Xi的风箱废气温度值;(4.2)采用多项式拟合法,对风箱废气温度数据样本中的一组样本数据(Xi,T(Xi))进行多项式拟合,得到拟合函数为T(Xi)=a8Xi8+a7Xi7+a6Xi6+a5Xi5+a4Xi4+a3Xi3+a2Xi2+a1Xi1+a0,a8、a7、a6、a5、a4、a3、a2、a1和a0分别为拟合得到的系数;(4.3)将步骤(4.2)中的拟合函数进行一次求导得到拟合函数的一次导数多项式,并求解出Xi的值,将求解出的Xi值代入拟合函数中即可求出拟合函数的最大值Tmax,Tmax为风箱废气温度曲线的最高值,即为烧结终点温度,Xi为烧结终点位置;如果拟合曲线的烧结终点温度大于300℃,且取得的烧结终点温度对应的烧结终点位置位于倒数第二个风箱和倒数第三个风箱之间,则拟合函数合理,从而确定拟合函数具有合理性;(4.4)将步骤(4.3)中拟合函数的一次导数多项式进行求导,得到拟合函数的二次导数多项式,并求解出Xi值;将求解出的Xi值代入拟合函数中即可求出风箱高温温度值Tp,将T(X)=Tp代入拟合函数中求出X1和X2,其中X2>X1;(4.5)根据烧结机理,利用步骤(4.4)中求解出的X1和X2的值,采用公式△X=X2-X1,得到其差值△X,利用△X可以得到高温保持时间,所述高温保持时间的计算公式如下:式中:t表示高温保持时间,表示烧结台车平均速度,所述烧结台车平均速度为已知值。进一步地,所述步骤(5)中,根据支持向量回归算法建立烧结矿成品率预测模型。进一步地,所述支持向量回归算法建立烧结矿成品率预测模型包括以下步骤:(5.1)设热状态参数和烧结矿的成品率组成的样本数据集为{(xi,yi),i=1,2…n},xi为输入参数,yi为对应的目标输出,即烧结矿的成品率;(5.2)利用非线性映射将输入参数映射到高维空间,在高维空间对输入参数进行线性回归,并求解线性回归问题的最优化问题:式中,ε是损失函数参数,C是惩罚因子,K(xi·xj)是高斯核函数,αi是权系数;(5.3)对(5.2)中的最优化问题进行求解,得到烧结矿成品率预测模型为:式中:K(xi,x)=exp(-||xi-x||2/2σ2),σ是核函数宽度,b是偏置量,b值的计算公式为:进一步地,所述建立烧结矿成品率预测模型的具体过程为:随机选取多组已烧结矿的成品率数据和热状态参数数据,将多组成品率数据和热状态参数数据中的一部分成品率数据和热状态参数数据作为训练数据,以所述一部分热状态参数数据为输入变量,以所述一部分成品率数据为输出变量进行重复计算,建立烧结矿成品率预测模型;将多组成品率数据和热状态参数数据中的剩余部分成品率数据和热状态参数数据作为测试数据,以所述剩余部分热状态参数数据为输入变量,输入烧结矿成品率预测模型,所述烧结矿成品率预测模型的输出变量为成品率的预测值,将所述剩余部分成品率数据与成品率的预测值进行验证。与现有技术相比,本发明具有以下有益效果:(1)本发明通过烧结过程的机理分析,确定影响烧结矿的成品率的热状态参数,并利用风箱废气温度数据,得到了热状态参数的数值,可实现直接预测烧结矿的成品率,为烧结过程实时调节工艺参数以提高烧结矿成品率和节能减耗提供重要依据;(2)本发明基于热状态参数,根据支持向量回归算法建立烧结矿成品率预测模型,能够直接预测烧结矿成品率,有效保证预测模型的精确与合理;(3)本发明基于烧结过程的历史生产数据,进行预测模型的仿真实验,能够在实际生产过程中广泛应用。附图说明图1是带式抽风烧结机的烧结过程工艺流程图。图2是带式抽风烧结机的烧结料层分层现象的示意图。图3是本发明一实施例的流程图。图4是本发明一实施例的风箱废气温度拟合曲线图。图5是本发明一实施例的风箱废气温度曲线上差值△X示意图。图6是本发明一实施例的成品率的预测值与实际的成品率数据的对比图。图7是本发明一实施例的成品率的预测值与实际的成品率数据的误差值。具体实施方式下面结合附图和实施例对本发明作进一步说明。利用本发明提供了一种基于风箱废气温度的烧结矿成品率预测方法,请参照图3,本实施例包括以下步骤:(1)通过分析烧结矿的烧结过程的机理确定影响烧结矿的成品率的热状态参数,烧结过程包括固相反应和液相反应,液相反应会生成铁酸钙液相,铁酸钙液相是烧结矿的成品率的主要影响因素,而铁酸钙液相的产生主要受到烧结料层热状态的影响,同时烧结料层热状态的变化可以由风箱废气温度曲线的变化反映,对于风箱废气温度曲线,主要的特征参数是风箱高温温度、高温保持时间、烧结终点温度和烧结终点位置,因此影响烧结矿的成品率的热状态参数包括风箱高温温度、高温保持时间、烧结终点温度和烧结终点位置。(2)对影响烧结过程的烧结参数的历史生产数据进行零相位滤波和时序配准处理,并选定大成矿的波动周期45min作为采样周期对历史生产数据进行采样处理,建立历史生产数据样本数据库;烧结参数包括风箱废气温度、台车速度、小成矿、返矿和大成矿;一实施例中,建立历史生产数据样本数据库的具体过程如下:收集烧结机一个月的历史生产数据,采集各个风箱废气温度、台车速度、大成矿、小成矿和返矿的历史生产数据,由于在历史生产数据采集过程中存在不确定因素,因此历史生产数据中存在较多的毛刺,从而需要对烧结过程中采集到的各个风箱温度、台车速度、大成矿、小成矿和返矿的历史生产数据进行零相位滤波处理;然后对各个风箱温度、台车速度、大成矿、小成矿和返矿的历史生产数据进行时序配准处理,以确保烧结过程参数数据在时序上保持一致;采用大成矿的波动周期45min作为采样周期,对经过零相位滤波处理和时序配准的历史生产数据进行采样处理,从而建立历史生产数据样本数据库。(3)利用历史生产数据样本数据库计算已烧结矿的成品率;烧结矿的成品率是指烧结过程结束后,成品烧结矿占烧结饼的比重,烧结矿的成品率的计算公式如下:式中:ρ表示烧结矿的成品率(%),QD表示烧结的大成矿产量(Kg/h),QX表示烧结的小成矿产量(Kg/h),QF表示烧结的返矿量(Kg/h);大成矿产量、小成矿产量和返矿量的数据从历史生产数据样本数据库中获得。(4)采用多项式拟合法对历史生产数据样本数据库中的风箱废气温度数据进行曲线拟合得到一个拟合函数,通过对拟合函数进行微分求极值,得到热状态参数的数值;得到热状态参数的数值具体包括以下步骤:(4.1)从历史生产数据样本数据库中选取风箱废气温度数据样本,设风箱数目为M,用(Xi,T(Xi))表示一个样本数据,i=1,2…M,Xi表示第i个风箱离点火处的距离,T(Xi)表示离点火处距离为Xi的风箱废气温度值;(4.2)采用多项式拟合法,对风箱废气温度数据样本中的一组样本数据(Xi,T(Xi))进行多项式拟合,得到拟合函数为T(Xi)=a8Xi8+a7Xi7+a6Xi6+a5Xi5+a4Xi4+a3Xi3+a2Xi2+a1Xi1+a0,a8、a7、a6、a5、a4、a3、a2、a1和a0分别为拟合得到的系数;(4.3)将步骤(4.2)中的拟合函数进行一次求导得到拟合函数的一次导数多项式,并求解出Xi的值,将求解出的Xi值代入拟合函数中即可求出拟合函数的最大值Tmax,Tmax为风箱废气温度曲线的最高值,即为烧结终点温度,Xi为烧结终点位置;如果拟合曲线的烧结终点温度大于300℃,且取得的烧结终点温度对应的烧结终点位置位于倒数第二个风箱和倒数第三个风箱之间,则拟合函数合理,从而确定拟合函数具有合理性;(4.4)将步骤(4.3)中拟合函数的一次导数多项式进行求导,得到拟合函数的二次导数多项式,并求解出Xi值;将求解出的Xi值代入拟合函数中即可求出风箱高温温度值Tp,将T(X)=Tp代入拟合函数中求出X1和X2,其中X2>X1;(4.5)根据烧结机理,利用步骤(4.4)中求解出的X1和X2的值,采用公式△X=X2-X1,得到其差值△X,利用△X可以得到高温保持时间,高温保持时间的计算公式如下:式中:t表示高温保持时间,表示烧结台车平均速度,烧结台车平均速度为已知值。利用上述步骤,参照图2,一钢厂360m2烧结机,共有24个风箱,各个风箱之间的距离不同,根据此烧结机的实际情况,对于现场能够检测到的1#、2#、3#、5#、7#、9#、11#、13#、15#、17#、18#、19#、20#、21#、22#、23#、24#风箱的废气温度值,分别对应烧结台车上的离点火处的距离是1.5m、4.5m、7.5m、14m、22m、30m、38m、46m、54m、62m、66m、70m、74m、78m、82m、85.5m、88.5m;在检测到的风箱废气温度值中选取一组样本数据(Xi,T(Xi)),i=1,2…17,其具体值为(1.5,89.09154431),(4.5,58.20210398)…(88.5,294.3742171),共17组,采用多项式拟合法,选取多项式的次数为8次,可求解出拟合函数T(Xi)=a8Xi8+a7Xi7+a6Xi6+a5Xi5+a4Xi4+a3Xi3+a2Xi2+a1Xi1+a0的系数值a8、a7、a6、a5、a4、a3、a2、a1和a0,拟合函数的系数值经过四舍五入后的数值如下表所示,风箱废气温度拟合曲线图见图4。经过四舍五入后的拟合函数的系数值a8a7a6a5a4a3a2a1a0-2.69e-119.18e-9-1.28e-69.19e-5-0.0040.071-0.6913.18-181.6将求解出的拟合函数的系数值代入到拟合函数T(Xi)=a8Xi8+a7Xi7+a6Xi6+a5Xi5+a4Xi4+a3Xi3+a2Xi2+a1Xi1+a0中,对拟合函数进行一次求导得到拟合函数的一次导数多项式,求解以下方程可得到Xi的值;dT(Xi)/dXi=d(a8Xi8+a7Xi7+a6Xi6+a5Xi5+a4Xi4+a3Xi3+a2Xi2+a1Xi1+a0)/dXi=8a8Xi7+7a7Xi6+6a6Xi5+5a5Xi4+4a4Xi3+3a3Xi2+2a2Xi1+a1=0将求解出的Xi值代入到拟合函数T(Xi)=a8Xi8+a7Xi7+a6Xi6+a5Xi5+a4Xi4+a3Xi3+a2Xi2+a1Xi1+a0中,即求解出一组样本数据在Xi∈[0m,90m]内的Tmax,Tmax为风箱废气温度曲线的最高值。通过计算可得当Xi=83时,Tmax取最大值为356.6533。可知,烧结终点温度为356.6533℃,烧结终点位置为83m;此时烧结终点温度大于300℃且烧结终点位置位于倒数第二个风箱和倒数第三个风箱之间,说明该拟合函数是合理的;一般而言,风箱废气温度曲线的最高温度在300℃以上。将求解出的拟合函数的系数值代入拟合函数T(Xi)=a8Xi8+a7Xi7+a6Xi6+a5Xi5+a4Xi4+a3Xi3+a2Xi2+a1Xi1+a0中,对拟合函数的一次导数多项式进行求导,得到拟合函数的二次导数多项式,并求解出以下方程的Xi值;56a8Xi6+42a7Xi5+30a6Xi4+20a5Xi3+12a4Xi2+6a3Xi+2a2=0将求解出的Xi值代入拟合函数T(Xi)=a8Xi8+a7Xi7+a6Xi6+a5Xi5+a4Xi4+a3Xi3+a2Xi2+a1Xi1+a0中,可得风箱高温温度值Tp=259.4902,然后将T(X)=Tp=259.4902代入拟合函数T(Xi)=a8Xi8+a7Xi7+a6Xi6+a5Xi5+a4Xi4+a3Xi3+a2Xi2+a1Xi1+a0中求得X1和X2,可得X1=70.800,X2=89.8207,采用公式△X=X2-X1,得到其差值△X=89.8207-70.800=19.0207;风箱废气温度曲线上差值△X示意图见图5;由于高温保持时间等于差值△X除以烧结台车平均速度,所以根据上述求解出的△X和已知的烧结台车平均速度,可求出高温保持时间t,其表示为:(5)以步骤(4)得到的热状态参数的数值作为输入变量,以步骤(3)得到的已烧结矿的成品率作为输出变量进行重复计算和验证,根据支持向量回归算法建立烧结矿成品率预测模型;根据支持向量回归算法建立烧结矿成品率预测模型的具体步骤为:(5.1)设热状态参数和烧结矿的成品率组成的样本数据集为{(xi,yi),i=1,2…n},xi为输入参数,yi为对应的目标输出,即烧结矿的成品率;(5.2)利用非线性映射将输入参数映射到高维空间,在高维空间对输入参数进行线性回归,并求解线性回归问题的最优化问题:式中,ε是损失函数参数,C是惩罚因子,K(xi·xj)是高斯核函数,αi是权系数;(5.3)对(5.2)中的最优化问题进行求解,得到烧结矿成品率预测模型为:式中:K(xi,x)=exp(-||xi-x||2/2σ2),σ是核函数宽度,b是偏置量,b值的计算公式为:(6)采用多项式拟合法对待预测矿的风箱废气温度数据进行曲线拟合并通过微分求极值法得到待预测矿的热状态参数的数值;(7)将待预测矿的热状态参数的数值作为输入变量输入烧结矿成品率预测模型,烧结矿成品率预测模型的输出变量即为待预测矿的成品率。一实施例中,随机选取200组已烧结矿的成品率数据和热状态参数数据,以170组成品率数据和热状态参数数据作为训练数据,以热状态参数数据为输入变量,以成品率数据为输出变量进行重复计算,建立烧结矿成品率预测模型;以30组成品率数据和热状态参数数据作为测试数据,以热状态参数数据为输入变量,输入烧结矿成品率预测模型,烧结矿成品率预测模型的输出变量为成品率的预测值,将成品率数据与成品率的预测值进行验证,预测值与实际的成品率数据的对比图和误差值分别见图6和图7,由图7可知,烧结矿的成品率的预测结果的相对误差在[-0.06%,0.08%]之内,因此,建立的烧结矿成品率预测模型具有可行性。本方法可以实现直接预测烧结矿的成品率,预测准确率高,为烧结过程实时调节工艺参数以提高烧结矿成品率和节能减耗提供重要依据。在不冲突的情况下,本文中上述实施例及实施例中的特征可以相互结合。以上所述仅为本发明的较佳实施例,并不用以限制本发明,凡在本发明的精神和原则之内,所作的任何修改、等同替换、改进等,均应包含在本发明的保护范围之内。当前第1页1 2 3