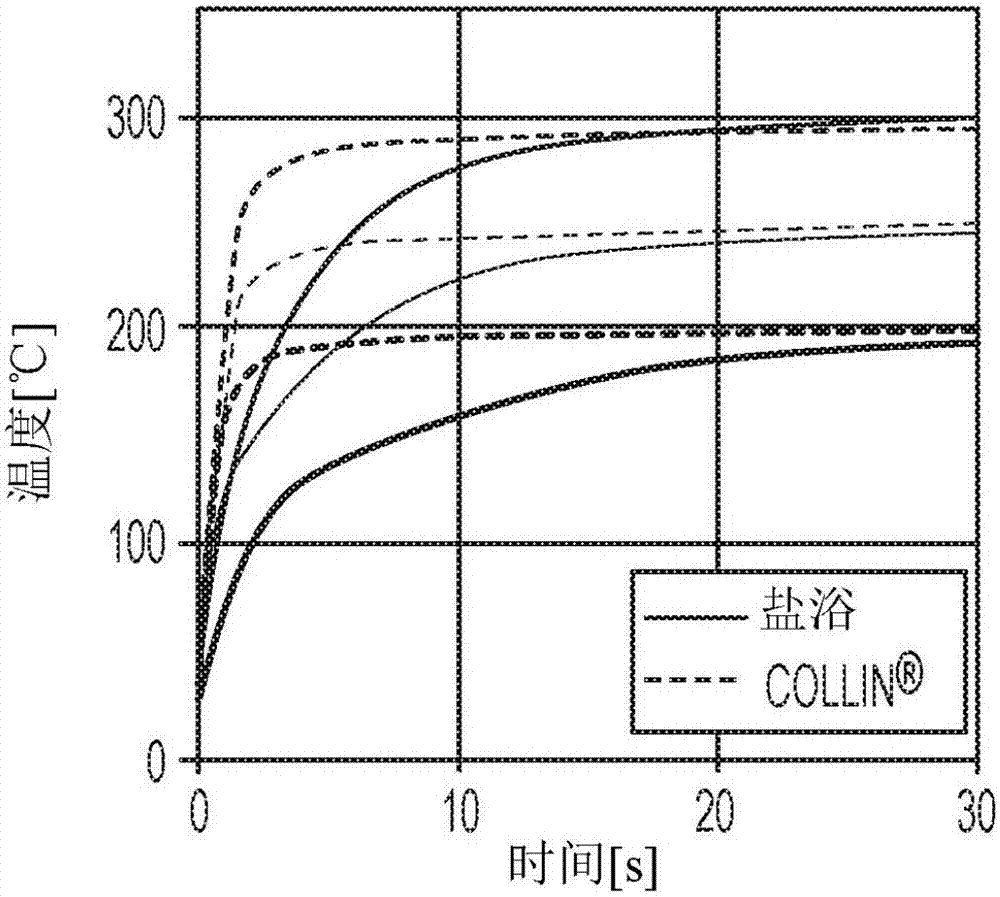
相关申请的交叉引用本申请要求2015年5月8日提交的美国临时专利申请第62/158,727号的权益,所述美国临时专利申请通过引用以其整体并入本文。本发明涉及材料科学、材料化学、冶金、铝合金、铝制造、运输业、机动车工业、汽车工业,机动车制造及相关领域。
背景技术:
:将可热处理的、可时效硬化的铝合金,如2xxx、6xxx和7xxx铝合金,用于生产车辆如汽车中的面板。这些合金通常以处于延性t4状态(或回火)的铝片材的形式提供给汽车制造商,以使制造商能够通过冲压或压制来生产汽车面板。为了生产满足所需强度规格的功能性汽车面板,制造商必须对由处于t4回火的铝合金生产的汽车面板进行热处理,以增加其强度并将铝合金转化为t6回火。在汽车制造中,在组装的机动车车身的烤漆工艺中,经常对外部汽车面板进行热处理。对于内部汽车零件,通常需要单独的热处理,称为后成型热处理(“pfht”)。在机动车工业中用于对压制的铝汽车面板进行热处理以增加其强度的当前工艺具有显着的缺点。在组装的机动车车身的烤漆循环期间的热处理需要具有足够热功率的涂漆线以达到所需的温度,特别是在汽车的厚的和内部结构元件中。烤漆热处理是困难的,特别是对于内部汽车面板,因为外部面板用作隔热罩,导致机动车车身的不同零件的不均匀硬化。例如,在通常的烤漆循环期间,可将外部面板暴露于170℃至185℃的温度约20分钟,这导致其“烘烤”硬化。然而,在类似的烤漆循环中,将组装的汽车车身中的地板面板暴露于仅130℃至160℃的温度下10分钟至15分钟,这不会导致明显的硬化。虽然有效,但pfht效率低下。例如,可能需要在约225℃下进行约30分钟的热处理以通过pfht在面板中获得完全t6回火。pfht导致高能量成本且耗时,并且需要对生产线进行昂贵的修改。换言之,pfht显著地增加了成本并延长了机动车生产周期。技术实现要素:本发明提供了铝合金制品以及相关产品和工艺,其可在运输工业或其它工业中用于生产铝合金零件如汽车面板。更通常地,本发明的产品和工艺可用于制造用在多种机械和机构中的铝零件。本发明所涵盖的实施例由权利要求书限定,而不是本
发明内容。本
发明内容是对本发明的多个方面的高度概述,并且介绍了在下面的详细描述部分中进一步描述的一些概念。本
发明内容并不旨在确定所要求保护的主题的关键或本质特征,也不旨在单独地使用以确定所要求保护的主题的范围。应通过参考整个说明书的适当部分、任何或所有附图和每个权利要求来理解所述主题。如本文中所使用的,术语“发明”、“本发明(theinvention)”、“此发明(thisinvention)”和“当前发明(thepresentinvention)”旨在广泛地指代本专利申请和以下权利要求的所有主题。包含这些术语的声明并不限制本文所描述的主题或限制以下专利权利要求的含义或范围。公开了用于由可热处理的、可时效硬化的铝合金如2xxx、6xxx和7xxx铝合金生产的铝合金制品的改进的热处理工艺。本文所公开的热处理工艺,例如,通过增加其强度改善了所处理的铝合金制品的机械特性。与目前在汽车工业中用于热处理铝面板的工艺(如pfht)相比,改进的热处理工艺显著地更短时并且使用非常快的加热速率。改进的热处理工艺可以在预老化或非预老化的合金上进行。可以将所公开的热处理工艺有效地合并到机动车零件(如汽车铝合金面板)的生产工艺中,并且可有利地在汽车生产周期中替代pfht。同时,通过改进的热处理工艺处理的铝合金制品能够达到与通过使用pfht所达到的强度特性相当的强度特性。可以将所公开的热处理工艺(可称为“冲击热处理”)容易地合并到用于制造压制的铝面板的现有汽车生产线中。例如,可以将冲击热处理站合并到汽车面板生产线的冲压生产线(pressline)中,以产生处于t6或t61回火的热处理的铝汽车面板。术语“t61回火”用于表示t4与t6之间的中间回火,具有比t4回火中的材料更高的屈服强度但更低的伸长率,并且具有比t6回火中更低的屈服强度但更高的伸长率。术语“t4回火”是指在没有中间分批退火和预老化的情况下生产的铝合金。此外,汽车面板可以处于t8回火。术语“t8回火”用于表示已进行固溶热处理、冷加工然后人工老化的合金。在本文所述的方法中使用的合金可以是预老化的或非预老化的。尽管其能很好地适用于汽车铝合金面板在生产过程中的热处理,但是改进的热处理工艺更适用于多种铝合金制品(如冲压或压制的铝合金制品)的热处理,以调节其机械特性,例如,增加其强度。所公开的工艺可以将冲击热处理合并到用于生产铝合金制品(如冲压的铝制品)的现有工艺和生产线中,从而以简化和经济的方式改进所述工艺和所得制品。在一些实例中,通过使用适当形状的加热工具的接触加热来加热预成型的铝制品从而实现改进的热处理工艺。在一些实例中,使预成型的铝制品经受多个冲击热处理步骤,其可以在不同的温度下进行。这样的冲击热处理步骤的组合在比常规热处理工艺更短的时间内实现了铝制品的期望的机械性能(例如,强度)。在一个实例中,在冲压步骤之后,可以使冲压的铝合金制品在两个不同的温度下经受两个或更多个不同的接触加热步骤。在另一个实例中,在冲压步骤之后,可以使冲压的铝合金制品的不同部分经受局部接触冲击加热步骤,以在铝合金制品的不同部分中获得不同的强度特性。还公开了通过改进的热处理工艺生产的铝合金制品,如机动车铝合金面板。用于制造机动车车身的所得汽车铝合金面板的使用也包括在本发明的范围内。一些示例性实施例如下。一个非限制性实例是用于增加由可时效硬化的、可热处理的铝合金生产的成形的铝合金制品的强度的工艺,其包括将由可时效硬化的、可热处理的铝合金生产的成形的铝合金制品的至少一部分以10℃/秒至220℃/秒的加热速率加热一次或多次至250℃至300℃的热处理温度,并将热处理温度保持60秒或更短。另一个实例是用于由可时效硬化的、可热处理的铝合金的铝合金片材生产成形的铝合金制品的工艺,所述工艺包括使铝合金片材成形以形成成形的铝合金制品,将成形的铝合金制品的至少一部分以10℃/秒至220℃/秒的加热速率加热一次或多次至250℃至300℃的热处理温度,并将热处理温度保持60秒或更短。在成形步骤中,成形可以通过冲压、压制或压制成形铝合金片材而成形。在上述实例中,可以将热处理温度保持5秒至30秒或10秒至15秒。可时效硬化的、可热处理的铝合金可以是2xxx、6xxx或7xxx系列铝合金。可时效硬化的、可热处理的铝合金可以在加热步骤之前处于t4回火和/或在加热步骤之后处于t6或t61回火。在加热步骤之后,可时效硬化的、可热处理的铝合金的屈服强度可增加至少30mpa至50mpa。加热可以是传导加热。可以通过应用一个或多个互补形状的加热模具来加热成形的铝合金制品的至少一部分。成形的铝合金制品可以作为整体或部分进行加热。例如,成形的铝合金制品的一个或多个部分可以在相同或不同的温度下进行加热。示例性工艺可以包括在两个不同温度下和/或保持不同时间段的至少两个加热步骤。例如,所述工艺可以包括在两个不同温度下的至少两个加热步骤。第二加热步骤的温度可以低于第一加热步骤的温度。在上述工艺中,成形的铝合金制品可以是机动车面板,尽管其并不是必需的。另一个实例是通过所公开的工艺(如上所讨论的示例性工艺)生产的成形的铝合金形式。成形的铝合金形式可以是机动车面板,如汽车面板或任何其它合适的产品。另一个非限制性实例是使用汽车面板来制造机动车车身。附图说明图1是铝片材的冲压和热处理的工艺的示意图。图2是经受通过盐浴浸渍(实线)或热压机(虚线)的热处理的合金aa6451样品之作为时间函数的温度的曲线图。图3是经受通过盐浴浸渍和在压力机中的热处理的合金aa6451样品之作为时间函数的rp0.2的曲线图。图4a至图4b是经受通过盐浴浸渍(温度高于300℃)或在压力机中的(温度为300℃以下)热处理的合金aa6451样品之作为时间函数的rp0.2的曲线图。图5a至图5b是经受在多个温度下并且保持多个时间段的在压力机中的热处理的实验性合金样品之作为时间函数的rp0.2的曲线图。图6是在合金aa6451样品上进行的说明性两步热处理工艺,所述工艺包括在压力机中进行热处理以及随后的盐浴浸渍热处理。图7a至图7b是经受多个热处理工艺的合金aa6451(图a)和实验性合金(图b)的样品之作为时间函数的rp0.2的曲线图。图8a至图8d是在水平碰撞测试之后通过冲击热处理处理的合金(图a和图b)和处于t4回火的合金(图c和图d)的碰撞管的图示。图9a至图9b是水平碰撞测试中合金的作为位移函数的变形能量和载荷的曲线图。图10a至图10d是在垂直碰撞测试后通过冲击热处理处理的合金(图a和图b)和用常规热处理处理的合金(图c和图d)的碰撞管的图示。图11是在垂直碰撞测试中合金的作为位移函数的载荷和能量的曲线图。图12是弯曲性能测试的示意图。图13是在压力机中在不同温度下或通过热空气在不同温度下处理的合金之作为时间函数的rp0.2的曲线图。图14a至图14b是处于t4回火和具有2%预应变的t4的预老化和非预老化的合金在不同温度下之作为时间函数的rp0.2的曲线图。图15是表示在冲压生产线中的冲击热处理的整合的示意图。具体实施方式公开了用于提高可热处理的、可时效硬化的铝合金(如通常用于生产汽车面板的2xxx、6xxx和7xxx铝合金)的强度的工艺。用于提高可热处理的、可时效硬化的铝合金的强度的工艺包括称为“冲击热处理”的热处理步骤,所述热处理步骤包括以快速加热速率(例如,10℃/秒至220℃/秒)在200℃至350℃下进行热处理短的时间段(例如,60秒或更短,5秒至30秒或5秒至15秒)。与通常在汽车工业中使用的常规热处理工艺(如pfht)相比,本文所公开的冲击热处理工艺通过使用更短的加热时间和更快的加热速率来提高可热处理的铝合金的强度。在一些实例中,冲击热处理通过在加热的压力机模具之间接触加热铝合金制品来实现,尽管可以使用其它加热工艺,如进一步详细讨论的。由于使用的加热时间短,根据一些实例的冲击热处理可以有利地合并到用于制造铝制汽车零件如汽车车身面板的汽车工业中所使用的生产线和工艺中。所公开的冲击热处理工艺不限于汽车工业,或更一般地机动车工业,并且可用于涉及铝制品制造的其它工业中。在一个实例中,成形的铝合金制品(或其部分)由可时效硬化的、可热处理的铝合金如2xxx、6xxx或7xxx系列铝合金来生产,随后将其加热一次或多次至250℃至350℃的温度,保持60秒或更短。在另一个实例中,工艺包括例如通过冲压、压制或压制成形铝合金片材由可时效硬化的、可热处理的铝合金的铝合金板片材来使所述制品成形,随后将所述制品加热一次或多次至250℃至350℃,保持60秒或更短。下面更详细地讨论冲击热处理。冲击热处理根据实例的工艺涉及对铝合金制品施加一个或多个冲击热处理步骤。根据本文所公开的实例的冲击热处理是根据可用于描述一个冲击热处理步骤或多个冲击热处理步骤的特征参数(如温度、持续时间或加热速率)进行的热处理。特征参数之一是铝合金制品在升高的温度下保持的时间长度(即,保温时间),其可以是,但不限于,2秒至10分钟、60秒或更短、2秒至120秒、2秒至60秒、2秒至30秒、2秒至20秒、2秒至15秒、2秒至10秒、2秒至5秒、5秒至120秒、5秒至60秒、5秒至30秒、5秒至20秒、5秒至30秒、5秒至15秒、5秒至10秒、10秒至120秒、10秒至60秒、10秒至30秒、10秒至20秒或10秒至15秒。一些示例性冲击热处理保温时间为约5秒、10秒、15秒、20秒、25秒、30秒、35秒、40秒、45秒、50秒、55秒、1分钟(60秒)或2分钟(120秒)。在冲击热处理工艺中可以使用多于一个的冲击热处理步骤。例如,在一些情况下,可以进行2个至5个冲击热处理步骤,每个进行5秒,导致累积冲击热处理时间为10秒至25秒。可以将多个热处理步骤中的每一个进行上述指定持续时间中的一个;不同的步骤可以使用不同的持续时间。在一些情况下,多个冲击热处理步骤的累积或组合长度可比上述指定的最大保温时间长。在相对短的时间段(如5秒至30秒)内进行热处理步骤允许将热处理步骤有效地合并到某些制造工艺和生产线中,如汽车面板制造线,而不会对这样的生产线和工艺造成主要中断。如本文所公开的冲击热处理可以改善铝合金的机械特性,其至少与通过使用更长的保温时间的其它热处理工艺所达到的改善相当。可以通过选择冲击热处理的温度来实现冲击热处理的较短保温时间,以便在相对较短的时间段内调节可时效硬化的铝合金的机械特性的期望变化。根据本文所公开的方法通过使用冲击热处理实现的铝合金的机械性能可以通过改变温度、时间或冲击热处理两者来调节。如本文所述的冲击热处理使用200℃至350℃、200℃至325℃、200℃至320℃、200℃至310℃、200℃至270℃、250℃至350℃、250℃至325℃、250℃至320℃、250℃至310℃或250℃至270℃的示例性温度。例如,冲击热处理可以在250℃、255℃、260℃、265℃、270℃、275℃、280℃、285℃、290℃、295℃、300℃、305℃、310℃、315℃、320℃或325℃下进行。通过改变冲击热处理的温度,可以调节所得铝合金或铝合金制品的机械特性如屈服强度和/或调节实现这些机械特性的速率。例如,在合适范围内提高冲击热处理的温度可导致铝合金的更快硬化,其特征在于更快速率的屈服强度增加。因此,可以在更短的时间内实现铝合金的屈服强度的有益增加。可以使用更高的保温温度来实现冲击热处理期间屈服强度增加的更有利的动力学。同时,冲击热处理的温度提高可导致较低的峰值屈服强度,这在选择冲击热处理温度时应予以考虑。如下面更详细地讨论的,使用在不同的冲击热处理温度下进行的两个或更多个热处理步骤的组合,是实现铝合金或由铝合金制成的制品的合适机械特性的一种途径。对于一个或多个冲击热处理步骤的一个温度或多个温度的选择还取决于铝合金的性质,例如,其在冲击热处理之前的组成和处理(其可以通过回火来表征)。根据一个实例的冲击热处理采用10℃/秒至200℃/秒的加热速率,例如,10℃/秒至100℃/秒、10℃/秒至50℃/秒、10℃/秒至20℃/秒。可以通过选择适当的加热工艺或系统来达到加热速率以加热铝合金制品。通常,在冲击热处理中使用的加热工艺或系统应当传递足够的能量以达到上文指定的加热速率。例如,可以使用用于热传导加热的装置和工艺来达到适于所公开的冲击热处理的快速加热速率。这样的工艺的一个实例是通过互补形状的加热工具来接触加热铝合金。例如,对于冲击热处理,如图1所示,可通过向铝合金制品施加具有互补形状的一个或多个压力机的加热模具来处理铝合金制品。图1是铝片材的冲压和热处理的工艺的示意图。图1示出了冲压机100,其具有两个顶模110和两个底模120以及通过在顶模110与底模120之间压缩形成的成形制品130。图1还示出了置于具有加热的顶模210和加热的底模220的热压机200中的由冲压机100形成的成形制品130。使加热的顶模210和底模220成形为使得其接触成形制品130的表面,而模具210、220不改变成形制品130的形状。更通常地,接触加热可以通过与加热的物体、物质或主体的任何接触来实现。加热工具的应用就是一个实例。接触加热工艺的另一个实例是浸没加热,其可包括将铝合金制品浸入加热的液体(“加热浴”)中。冲击热处理也可以通过非接触加热工艺来实现,例如,通过辐射加热。可以使用的加热工艺的一些非限制性实例是热空气加热、接触加热、通过感应加热、电阻加热、红外辐射加热和通过气体燃烧器加热。例如,可以将合适尺寸和形状的接触加热工具或多个工具施加到铝合金制品的一个部分或多个部分上,以便实现制品的一个部分或多个部分的局部加热。在另一些实例中,可以将接触加热工具如热压机的模具施加到整个制品上,或者可以使用加热浴来实现整个制品的加热。在另一个实例中,冲击热处理可以仅在之前冲压的铝制品的成型部分上进行,而不对其凸缘区域进行,以保持凸缘的弯曲/卷边能力。因此,对于定制的冲击热处理,可以使用加热系统和方案的设计和优化来管理热流和/或实现经处理制品的期望特性。铝合金制品的冲击热处理影响铝合金的一个或多个机械性能。通过所公开的冲击热处理改善的铝合金的机械特性可以是一个或多个强度特性,如屈服强度、最大拉伸强度和/或伸长率。在一些实例中,通过一个或多个冲击热处理步骤来增加可时效硬化的、可热处理的铝合金的强度。例如,测量为0.2%条件屈服强度(rp0.2)的铝合金样品的屈服强度可以增加至少30mpa至50mpa,例如,30mpa至150mpa或30mpa至85mpa。铝合金的不同机械性能可受到不同方式的影响。例如,在特定条件下的冲击热处理可以实现与通过长时间段进行的热处理工艺所实现的那些相当的铝合金的rp0.2的改善,但是在这些条件下实现的最大拉伸强度(rm)和/或伸长率可能低于通过较长的热处理工艺所实现的最大拉伸强度(rm)和/或伸长率。在另一个实例中,如果在冲压后对铝制品进行冲击热处理,那么可以实现应变和烘烤硬化的组合效果。选择冲击热处理条件如所使用的一个温度或多个温度的选择和冲击热处理步骤的数量,使得其产生适合于特定应用的铝合金的机械性能。例如,选择在汽车面板制造中使用的冲击热处理条件,使得所得汽车面板具有合适的碰撞性能。在一些实例中,使用多于一个的冲击热处理步骤。可以使用在两个或更多个不同温度下、保持不同时间段和/或以不同加热速率的进行的两个或更多个冲击热处理步骤以获得期望的铝合金强度特性。例如,可以使用在两个或更多个不同温度下、保持不同时间段和/或以不同加热速率进行的两个、三个、四个或五个冲击热处理步骤。冲击热处理条件如温度、加热速率和/或持续时间的选择可影响经受冲击热处理的铝合金或由这样的合金制成的制品的性能,如屈服强度。例如,根据铝合金的性质,组合在250℃至350℃下在铝合金零件上进行2个至5个冲击热处理步骤(不同的冲击热处理步骤可以在不同的温度下进行),每个保持5秒,产生10秒至25秒的累积冲击热处理时间并实现30mpa至150mpa的屈服强度增加。如本文其它地方所讨论的,更高的冲击热处理温度导致更快的屈服强度增加,从而允许更短的冲击热处理时间,但也可能导致经受冲击热处理的铝合金的更低的最大屈服强度。因此,可以通过操纵冲击热处理条件和/或组合冲击热处理步骤来实现铝合金性能的期望组合。例如,与使用仅在一个温度下的冲击热处理的工艺相比,组合在较高温度下进行的一个或多个冲击热处理步骤与在较低温度下进行的一个或多个热处理步骤的工艺可导致合金在更短的时间内获得更高的屈服强度。在一些实例中,第一冲击热处理步骤在比第二冲击热处理步骤高的温度下进行。例如,第一步骤可以在300℃下进行,而第二热处理步骤可以在250℃下进行。在另一个实例中,可以使冲压的铝合金制品的不同部分经受不同的局部冲击热处理条件,例如,使用不同温度的接触加热工具,以在铝合金制品的不同部分中获得不同的强度性能。此外,如下面更详细地讨论的,可以使用更短持续时间的多个冲击热处理步骤的组合而不是一个更长的冲击热处理步骤,从而将冲击热处理工艺更有效地整合到铝合金制品的生产线和生产工艺中。不同的冲击热处理步骤可以通过相同或不同的加热方法,在相同或不同的加热温度下和/或保持相同或不同的持续时间来进行。例如,可以使用通过加热工具的接触加热与加热浴处理的组合。在使用两个或更多个热处理步骤的情况下,可以同时(例如,当使用制品的不同部分的局部冲击热处理时)、依次使用这些步骤或可以及时重叠这些步骤。铝合金和铝合金制品本文公开的冲击热处理可以用任何沉淀硬化铝合金(例如,含有al、mg、si和任选地cu并且能够表现时效硬化响应的铝合金)来进行。可以经受所公开的冲击热处理的铝合金包括可时效硬化的铝合金,如2xxx、6xxx和7xxx系列合金。可以经受冲击热处理的示例性铝合金除了铝之外还可以包括以下成分:si:0.4重量%至1.5重量%,mg:0.3重量%至1.5重量%,cu:0重量%至1.5重量%,mn:0重量%至0.40重量%,cr:0重量%至0.30重量%,以及至多0.15重量%的杂质。合金可以包含替代或附加成分,只要合金是沉淀硬化合金即可。铝合金的组成可影响其对冲击热处理的响应。例如,热处理后的屈服强度的增加可受到合金中存在的mg或cu-si-mg沉淀物的量的影响。用于本文所公开的冲击热处理的合适的铝合金可以在非热处理状态(例如,t4回火)下提供,或者可以在部分热处理的状态(例如,t61回火)下提供,并且可根据所公开的工艺进一步进行热处理以增加其强度。所述合金可以是预老化的或非预老化的。在一些实例中,经受冲击热处理的可热处理的、可时效硬化的铝合金是以处于延性t4状态的铝片材或由这样的片材形成的制品形式提供。称为t4的状态或回火是指在没有中间分批退火和预老化的情况下生产的铝合金。经受如本文所公开的冲击热处理步骤的铝合金不需要在t4回火下提供。例如,如果铝合金是在冲压之后作为人工老化的材料来提供,那么其处于t8回火。如果铝合金是在冲压之前作为人工老化的材料来提供,那么其处于t9回火。可以使这样的铝合金材料经受根据本文所公开的工艺的冲击热处理。在冲击热处理之后,铝合金片材或由这样的片材制造的制品处于t6回火或部分t6回火(t61回火),并且表现出与这样的回火相关的强度特性的改善。如上所述,名称“t6回火”意指已经经过固溶热处理和人工老化达到峰值强度的铝合金。在另一些实例中,经受冲击热处理的制品最初以部分热处理状态(t61回火)提供,并且在冲击热处理之后处于t61或t6回火。即使在冲击热处理之后铝合金制品的回火名称没有改变,如同在制品在冲击热处理之前和之后处于t61回火的情况下一样,冲击热处理仍改变了铝合金的特性,例如增加了其屈服强度。适用于根据本文公开的方法的冲击热处理的铝合金制品包括由铝合金片材成型或成形的铝合金制品。铝合金片材可以是由铝合金锭或条带生产的轧制铝片材。由其生产铝合金制品的铝合金片材以合适的回火(如t4或t61回火)提供。成型或成形的铝合金制品包括二维和三维形状的铝合金制品。成型或成形的铝合金制品的一个实例是从铝合金片材切割而没有进一步成形的扁平制品。成型或成形的铝合金制品的另一个实例是通过包括一个或多个三维成形步骤(如弯曲、冲压、压制、压制成型或拉伸)的工艺生产的非平面铝合金制品。这样的非平面铝合金制品可以称为“冲压的”、“压制的”、“压制成形的”、“拉伸的”、“三维成形的”或其它类似术语。铝合金制品可以通过“冷成型”工艺来形成,这意味着在成型之前或成型期间不会对制品施加另外的热量,或者通过“热成型”工艺来形成,这意味着在成型之前或成型期间加热制品或在升高的温度下进行成型。例如,可以将热成型的铝合金制品在150℃至250℃、250℃至350℃或350℃至500℃下进行加热或成型。由本文所述的工艺提供或生产的铝合金制品包括在本发明的范围内。术语“铝合金制品”可以指在冲击热处理之前提供的制品、通过冲击热处理进行处理或经受冲击热处理的制品以及在冲击热处理之后的制品,包括涂漆或涂覆的制品。由于冲击热处理可以有利地用在包括汽车制造在内的机动车工业中,所以铝合金制品及其制造工艺包括机动车零件,例如汽车车身面板。落入本公开范围内的机动车零件的一些实例是地板、后壁、摇臂、电动机罩、挡泥板、车顶、门板、b-立柱、龙骨、车身侧面、摇臂或碰撞构件。术语“机动车”及相关术语不限于汽车,且包括但不限于多种车辆类型如汽车、小汽车、公共汽车、摩托车、非公路车辆、轻型卡车、卡车和货车。铝合金制品不限于机动车零件;设想和包括根据本文所述的工艺制造的其它类型的铝制品。例如,冲击热处理工艺可以有利地用于制造机械和其它装置或机器,包括飞机、船舶和其它水上交通工具、武器、工具,电子装置的主体等的多个零件。本文所公开的铝合金制品可包括多个零件或由多个零件组装。例如,包括由多于一个零件组装的机动车零件(如包括内面板和外面板的汽车罩,包括内面板和外面板的汽车门,或包括多个面板的至少部分组装的机动车车身)。此外,包括多个零件或由多个零件组装的这样的铝合金制品在其进行组装或部分组装之后可适用于根据本文所公开的方法的冲击热处理。此外,在一些情况下,铝合金制品可以包含非铝零件或部分,如包含其它金属或金属合金(例如,钢或钛合金)或由其它金属或金属合金(例如,钢或钛合金)制造的零件或部件。工艺和系统生产铝合金制品的工艺可以包括本文件中所讨论的一个或多个步骤。铝合金制品由铝合金片材制成。在一些情况下,铝合金片材可以例如通过将其切割成前体铝合金制品或称为“坯料”的形式,如“冲压坯料”,这意指用于冲压的前体,进行切面。因此,所公开的工艺可以包括生产铝合金制品的前体或坯料的一个步骤或多个步骤。然后通过合适的工艺使坯料成形为期望形状的铝制品。用于生产铝合金制品的成形工艺的非限制性实例包括切割、冲压、压制、压制成形、拉伸或可产生二维或三维形状的其它工艺。例如,工艺可以包括将铝片材切割成“冲压坯料”的步骤以在冲压机中进一步成形。工艺可以包括通过冲压使铝合金片材或坯料成形的步骤。一般而言,在冲压或压制加工步骤中,通过在两个互补形状的模具之间压制坯料来使其成形。本文公开的工艺包括冲击热处理的一个或多个步骤。所述工艺可以包括作为独立步骤或与其它步骤组合的冲击热处理。例如,所述工艺可以包括使铝合金制品成形的步骤和根据冲击热处理的特征参数(温度、加热时间和/或加热速率)对成形的铝合金制品进行热处理的一个或多个步骤。所述工艺可以将冲击热处理合并到用于生产铝合金制品(如冲压的铝制品(例如,冲压的铝合金汽车面板))的现有工艺和生产线中,从而以简化和经济的方式改进所述工艺和所得制品。用于进行本文件中描述的工艺和生产制品的设备和系统包括在本发明的范围内。实例是生产冲压的铝合金制品如机动车面板的工艺,其包括在冲压机序列(“冲压生产线”)上冲压制品的几个(两个或更多个,如两个、三个、四个、五个、六个或更多个)步骤。冲压步骤是所谓的“冷成型”步骤,意指不进行制品的另外加热。在第一冲压步骤之前提供冲压坯料。所述工艺包括在相对于一个或多个冲压步骤的不同工艺点进行的一个或多个冲击热处理步骤。可以在第一冲压步骤之前(即,在冲压生产线的入口处)在冲压坯料上进行冲击热处理步骤中的至少一个。在这种情况下,在上述冲击热处理步骤之后并且第一次压制步骤之前可以将坯料(其可以以t4回火提供)转化成t6或t61回火。可以在最后一个冲压步骤之后(即,在冲压生产线的末端)进行至少一次冲击热处理步骤。在这种情况下,可以通过在生产线末端的冲击热处理步骤将冲压的制品转化成完全t6回火。冲击热处理步骤还可以包括在一个或多个第一或中间压制步骤之后。例如,如果压制线包括五个冲压机和相应的冲压步骤,那么这样的中间冲击热处理步骤可以包括在第一、第二、第三和第四中间冲压步骤中的一个或多个之后。在包括中间冲击热处理步骤时的情况下,在中间冲击热处理步骤之前,制品可以处于t4或t61回火,在中间冲击热处理步骤之后可以处于t61或t6回火。冲击热处理步骤可以以多种组合包括在生产工艺中。例如,当使用一个或多个中间冲击热处理步骤时,冲击热处理步骤还可以包括在冲压生产线的开始和末端处,如上所讨论的。在生产工艺中决定冲击热处理步骤的具体组合和放置时,可以考虑多种考虑因素。例如,如果在一个冲压步骤或多个冲压步骤之前引入一个冲击热处理步骤或多个冲击热处理步骤,那么通过冲压成型可能变得更加困难,但与其它配置的生产线相比,所得制品可以保持更高的强度特性。基于多种考虑来决定冲击热处理步骤的持续时间和其它参数、冲击热处理步骤的数量和整合点以及包括在制造工艺或系统中的相应站。例如,如前所讨论的,可以通过操作冲击热处理条件来实现铝合金性能的期望组合。因此,可以至少部分地基于铝合金制品的期望性质来决定冲击热处理步骤的数量及其参数。例如,更长的冲击热处理时间可能更适于实现更好的碰撞性能,这对于机动车面板而言是期望的。另一个决策考虑是将冲击热处理步骤有效地整合到加工、制造或生产工艺中。例如,可以将相对短的持续时间,例如,5秒至20秒或10秒至20秒的冲击热处理步骤作为在压制步骤之间进行的中间步骤整合而不会产生生产线的主要中断。另一方面,可以将较长的(例如,30秒至60秒或更长)的冲击热处理步骤作为另外的步骤更有效地整合在冲压生产线的末端处。基于生产周期的要求,在一些情况下,可以作出决定支持较短持续时间的多个冲击热处理步骤以将其整合为中间步骤。如之前所讨论的,整合到所述工艺中的冲击加热步骤可以在相同或不同的温度下进行不同的持续时间。例如,可以将在不同温度下用于热处理的两个或三个冲击热处理步骤或站整合到机动车面板的生产线中。在一个实例中,将分别在275℃和300℃下进行冲击热处理各5秒钟的两个热处理站包括在机动车面板的生产线中。冲击热处理可以在独立的、专用装备(系统、站、机器或设备)上进行。还公开了用于生产或制造铝合金制品的系统,其包括用于冲击热处理的装备。一个示例性系统是用于生产冲压的铝合金制品如铝合金板面板的冲压生产线,其包括在生产线中的多个点处整合冲击热处理站或系统,如在上文所讨论的多个实例中。可对组装或部分组装的制品或零件进行冲击热处理。例如,在将其组装之后,可以对机动车零件(如机罩或门)进行冲击热处理。在另一个实例中,例如,可以通过将接触加热工具施加于车身的一个部分或多个部分,对完全或部分组装的机动车车身进行局部或部分冲击热处理。为了说明,可以使在烤漆循环期间未达到足够高温度的组装或部分组装的机动车车身的零件在烤漆循环之前或之后经受局部冲击热处理以增加其强度。在这种情况下,可以在机动车零件或车身的组装期间或之后的某个点处将冲击热处理步骤和相应的站整合到生产线中。可以通过多种考虑来决定在组装线上用于整合冲击热处理的点的选择。例如,可以在机动车车身组装之后进行冲击热处理,以在组装期间保持车身部零件的最佳铆接能力。在另一个实例中,冲击热处理步骤可以包括在机动车车身组装的任何阶段之间,包括在由这样的非限制性考虑所决定的点处,所述考虑出于在冲击热处理之前保持车身零件的铆接或接合能力。如本文所公开的生产或制造铝制品的工艺可以包括用合适的油漆或涂料对铝合金制品进行涂覆或涂漆的步骤。通常,随后对成形的和冲击热处理的铝合金制品进行涂漆。例如,当将铝合金制品用作汽车或其它机动车面板时,通常在组装之后对机动车的车身进行涂覆和/或涂漆以用于防腐和美观。油漆和/或涂料可以通过喷涂或浸渍来施加。在施加之后,通常以通常称为“烘烤”的工艺来处理油漆和/或涂料。本文公开的工艺可以包括油漆烘烤步骤,其可以称为“油漆烘烤(paintbaking)”,“烤漆(paintbake)”,“烤漆循环”或其它相关术语。烤漆通常涉及在160℃至200℃下进行热处理长达1小时的时间段,例如,20分钟至30分钟。铝合金制品即使未经涂漆或涂覆,也可经历烤漆循环或相当的热处理循环。例如,未经涂漆和/或未经涂覆的汽车面板可以作为组装的机动车车身的一部分经受烤漆循环。如本文件中其它地方所讨论的,烤漆循环可影响由其制造制品的铝合金的老化,从而影响其机械性能,如强度。因此,在本文所述的工艺中可以使用烤漆循环或类似的热处理步骤作为另外的热处理步骤,这意味着工艺可以包括除了冲击热处理步骤之外的烤漆或类似的热处理步骤。优点本文所述的工艺尤其适用于机动车铝合金面板的制造,并且可以在机动车生产周期中代替pfht。冲击热处理显著地比pfht更短时,并且可以容易地合并到现有的机动车生产工艺和生产线中。冲击热处理通常适用于多种铝合金制品(如冲压的或压制的铝合金制品)的热处理,以增加其强度。冲击热处理可以有利地代替在铝合金制品生产期间所使用的常规热处理步骤以增加其强度,或者可以在常规的热处理步骤之外使用。用本文所公开的冲击热处理工艺来代替常规热处理步骤(如pfht)的优点在于冲击热处理工艺可以是以下的一个或多个:由于较短的热处理时间而高效节能;耗时较短;和/或容易地合并到现有的生产工艺中,例如,以冲压生产线的生产速率合并到现有的冲压生产线中。这种整合的优点在于,冲压生产线接着可以产生处于t6或t61回火的冲压或压制的铝合金制品如机动车面板,其可以在冲压生产线之后进入下一个工艺步骤。本文所公开的冲击热处理工艺也是高度可定制的,从而提高生产工艺的灵活性。例如,可以将冲击热处理步骤容易且有效地整合到机动车生产周期中,以根据需要产生所生产的制品的期望特性。本文所述的方法增加了经受冲击热处理的铝合金制品的强度。反过来,增加的强度可以允许减少铝制品(如汽车面板)的厚度(向下测量),从而降低其重量和材料成本。此外,通过所公开的冲击热处理实现的铝合金的改善的强度特性可以扩大铝合金在多种行业中的使用,如机动车工业,特别是汽车工业。以下实例将用于进一步说明本发明,但同时并不构成其任何限制。相反,在不脱离本发明的精神的情况下,可以对其多种实施例、修改和等同物进行描述,在阅读本文的描述之后,可以向本领域技术人员提出建议。实例在以下的实例中,在t4回火和具有2%预应变的t4回火下,生产铝合金aa6451的片材和实验性合金组合物的片材(在本文件中称为“合金a”),以模仿后冲压条件。合金a的组成为0.95重量%至1.05重量%的si、0.14重量%至0.25重量%的fe、0.046重量%至0.1重量%的mn、0.95重量%至1.05重量%的mg、0.130重量%至0.170重量%的cr、0重量%至0.034重量%的ni、0重量%至0.1重量%的zn和0.012至0.028的ti、余量为al和杂质。样品通过盐浴程序和/或热压或板压程序进行热处理。对于盐浴程序,通过将样品在稳定的温度下浸入含有碱式硝酸盐的熔融盐混合物的盐浴炉中来加热样品。在以下实例中,对于热压程序,使用压力机。将压力机加热至稳定的温度,将样品放置在两个压板之间,并施加压力。压力确保样品的非常快速的加热。实例1热处理方法的比较为了比较一些以下实例中使用的盐浴和热压加热方法,通过盐浴程序和通过热压程序来加热aa6451的样品。收集盐浴和热压各自在200℃、250℃和300℃下的数据。两种热处理程序都能确保样品的快速加热,如图2所示。图2中的实线表示通过盐浴程序加热的样品的温度,虚线表示通过热压程序加热的样品的温度。如图2所示,达到目标热处理温度所需的时间为盐浴程序约15秒,冲压程序约5秒。盐浴和热压程序提供了合金样品的相当的硬化。测量样品的0.2%条件屈服强度(rp0.2),以监测每个热处理工艺在250℃、275℃和300℃的温度下的硬化过程,如图3所示。x轴表示合金在指定温度下保持的时间。不包括到指定温度的加热时间,但是从图2所示的数据可以推断出所述加热时间为盐浴浸渍15秒,热压5秒。图3表明,预计使用盐浴和热压程序的合金硬化几乎相同。因此,在以下的实例中,虽然在各温度下仅使用一个程序,但结果是通常在该温度下加热的示例,而不管所使用的加热方法如何。实例2在多种温度下获得的屈服强度通过使aa6451样品和合金a样品经受在200℃至350℃的热处理温度范围内的多种温度下的热处理并测量2%条件屈服强度rp2.0,在多种温度下测定峰值屈服强度。图4和图5示出了,对于合金aa6451和合金a两者,当在较高的温度下较快达到峰值rp0.2时,热处理温度从200℃提高到350℃导致合金aa6451和合金a的峰值rp0.2降低。使合金样品经受通过高于300℃温度的盐浴浸渍的热处理,和在压力机中的不高于300℃温度的热处理。在不同温度下的加热程序的差异是可用装备的限制的结果,并且不应当影响结果,因为实例1证明通过两种加热方法实现了类似的硬化。在图4和图5中,x轴表示合金在指定温度下保持的时间,不包括加热时间。图4a示出了在多种温度下经受热处理的处于t4回火的合金aa6451的实验结果。图a中的水平虚线是表示处于t6回火的相同合金样品在180℃下热处理10小时之后所达到的rp0.2的参考线。图4b示出了在多种温度下经受热处理的处于具有2%预应变的t4回火的合金aa6451的实验结果。图b中的水平虚线是表示相同的预应变t4合金样品在185℃热处理20分钟以将合金置于t8x回火之后所达到的rp0.2的参考线。如图4b中所示,对于处于具有2%预应变的t4回火的aa6451样品,在275℃下热处理约1分钟(总压制时间)导致rp0.2为约240mpa,其接近通常在相同合金的模拟烘烤硬化工艺(在185℃下加热20分钟)中所达到的rp0.2。因此,使用冲击t6工艺,由该合金形成的不会经历标准烤漆的零件,如在烤漆期间被外部零件遮挡的内部零件,可以达到与来自该合金的烤漆零件相同的强度。图5a示出了在多种温度下经受热处理的处于t4回火的合金a的实验结果。图a中的水平虚线是表示处于t6回火的相同合金样品在180℃下热处理10小时之后所达到的rp0.2的参考线。图5b示出了在多种温度下经受热处理的处于具有2%预应变的t4回火的合金a的实验结果。图b中的水平虚线是表示相同的预应变t4合金样品在185℃热处理20分钟以将合金置于t8x回火之后所达到的rp0.2的参考线。如图5b中所示,对于处于具有2%预应变的t4回火的合金a样品,在300℃下热处理10秒至15秒(总压制时间)导致rp0.2为约300mpa,其对应于通常在相同合金的模拟烘烤硬化工艺(在185℃下加热20分钟)中所达到的rp0.2。因此,使用冲击t6工艺,由该合金形成的不会经历标准烤漆的零件,如在烤漆期间被外部零件遮挡的内部零件,可以达到与来自该合金的烤漆零件相同的强度。在表1中示出了在热处理条件的测试期间获得的一些rp0.2增加。表1.在热处理条件的测试期间获得的rp0.2增加实例3铝合金样品的组合热处理使aa6451和合金a的片材的样品经受两步热处理工艺,其包括压力机热处理程序(在300℃下10秒或30秒)和盐浴程序(在250℃下多个时间),随后通过空气进行冷却。图6中示出了示例性两步处理工艺,图6是加热aa6451样品的工艺的作为时间函数的合金片材温度曲线图,所述工艺包括通过压力机在300℃下热处理30秒,转移到盐浴中,并通过盐浴在250℃下热处理20秒。使aa6451样品和合金a样品经受多个一步或两步热处理。将合金样品在以下热处理中进行加热:在250℃下在盐浴中进行的一步热处理中;两步热处理,包括在300℃下进行压力机处理10秒,随后在250℃下进行盐浴处理;两步热处理,包括在300℃下进行压力机处理10秒或30秒,随后在250℃下进行盐浴处理;或者在300℃下在压力机中进行的一步热处理。x轴表示合金样品在每个温度下保持的时间,不包括加热时间。如图7所示,对于aa6451和合金a两者,通过两种两步工艺都达到了比在300℃下的一步工艺更高的rp0.2值。在两步工艺的初始加热步骤(在300℃下)过程中和在300℃下的一步工艺的rp0.2比在205℃下的一步工艺在相同时间段期间的rp0.2增加得更快。但是,两种两步工艺在转换到250℃下的第二加热步骤之后的过程中,rp0.2比在300℃的一步工艺过程中经过相同时间段的rp0.2增加得更快。实例4冲击热处理的合金的碰撞测试将通过本文所公开的方法处理的合金样品与相同合金的未经热处理的(即,t4回火)样品的碰撞性进行比较。该合金样品的组成为si1.0、fe0.2、cu1.0、mg1.0、mn0.08、cr0.14,全部以重量%计,多达0.15重量%的杂质,余量为铝,并且将所述合金样品在本文中称为“合金b”。将合金b的片材(2mm厚)在500℃下的烘箱中加热90秒(不包括将片材升高到500℃的时间),以将片材置于“冲击t6”回火。然后将片材折叠并螺接以形成碰撞管。由处于t4回火的合金b的片材(2mm厚)形成第二个碰撞管。在准静态3点弯曲设置(水平碰撞测试)中对管进行测试。图8示出了在水平碰撞测试之后碰撞测试管的图示。图8a和图8b示出了冲击t6合金b。图8c和图8d示出了t4合金b。如图8所示,两根管都通过了测试。图9示出了水平碰撞测试的作为冲孔位移(mm)的函数之所施加的冲击力(kn)和变形能量(kj)。图9a是处于冲击t6回火的合金b的作为位移函数的力和变形能量的曲线图,图9b是处于t4回火的合金b的作为位移的函数的力和变形能量的曲线图。如图9所示,冲击t6回火合金比t4回火合金多吸收了26%的能量(2.4kj相比于1.9kj)。这些测试表明,通过本文所公开的方法处理的材料具有良好的碰撞性。通过本文所公开的方法处理的材料与t4材料相比在碰撞期间吸收了更多的能量,但不如标准t6材料那么多。还比较了通过本文所公开的方法处理的铝合金样品与通过标准热处理处理的相同合金样品的碰撞性。所述合金的组成为0.91si、0.21fe、0.08cu、0.14mn、0.68mg、0.04cr和0.030ti,全部以重量%计,多达0.15%重量的杂质,余量为铝,并且将所述合金在本文中称为“合金c”。将处于t4回火的合金c的片材(2.5mm厚)在275℃下的盐浴中通过冲击热处理加热1分钟(不包括将片材升高至275℃的25秒),以将片材置于“冲击t6”回火。然后将片材折叠并螺接以形成碰撞管。由处于t4回火的合金c的片材(2.5mm厚)形成第二个碰撞管。在形成之后,将管在180℃下加热25分钟,以将管置于按照iso2107所定义的t62回火。选择另外的加热条件以使t62管具有与冲击t6管相同的rp0.2,即约200mpa。在压力机中以恒定的准静态速度在垂直压缩中测试管(垂直碰撞测试)。图10示出了在垂直碰撞测试之后碰撞测试管的图示。图10a和图10c示出了测试之后碰撞管的侧视图,图10b和图10d示出了测试之后碰撞管的仰视图。图10a和图10b示出了测试之后的合金c冲击t6管。图10c和图10d示出了测试之后的合金ct62管。处于冲击t6的碰撞管在垂直碰撞测试中在破碎时成功地折叠而没有撕裂或裂纹,而参考碰撞管在图10c所示的区域410中显示出一些表面裂纹。将负载和能量测量为合金材料的位移函数。图11是冲击t6和t62材料的作为位移函数的负载和能量的曲线图,说明冲击t6管在碰撞测试期间吸收较少的能量。与常规热处理相比,冲击热处理产生了合金,所述合金具有更低的如通过iso6892-1所测量的极限拉伸强度,但是具有稍微更好的通过iso7438(一般弯曲标准)和类似rp0.2的vda238-100所测量的弯曲性能。图12是根据vda238-100进行的弯曲性能测试的示意图。表4总结了测试结果。表4冲击t6t62rp/rm[mpa]200/204198/281dc(α)[°]115107碰撞等级完美良好碰撞能量[kj]10.411.7实例5使用热空气的冲击热处理用热空气进行冲击热处理可以提供与用热压机进行的冲击热处理类似的硬化。使用加热至250℃、275℃或300℃的压力机或使用在350℃、400℃或500℃下的热空气来加热合金a的样品。图13是示出使用不同的加热方法加热的样品的作为时间函数的rp0.2增加的曲线图。使用热压法的rp0.2增加得更快,但使用热空气法在只有约120秒时达到类似的最大rp0.2。实例6在预老化相对于非预老化的材料上的冲击热处理在250℃和275℃下,在压力机中对处于t4回火的aa6451的预老化和非预老化样品进行冲击热处理。也在250℃和275℃下,在压力机中对处于具有2%预应变的t4回火的aa6451的预老化和非预老化样品进行加热。图14示出了样品的老化曲线。图14a示出了t4材料的作为时间函数的rp0.2(mpa),其中“px”表示预老化,图14b示出了t4+2%预应变材料的作为时间函数的rp0.2,再次以“px”表示预老化。在冲击热处理之后,在250℃和275℃两者下处理的预老化的t4aa6451提供了比类似的非预老化的样品更高的强度。同样,在冲击热处理之后,在250℃和275℃两者下处理的预老化的具有2%预应变的t4的aa6451提供了比类似的非预老化的样品更高的强度。实例7冲击热处理在汽车生产工艺中的整合可以将冲击热处理步骤整合到用于制造压制的汽车面板的生产线中。可以将冲击热处理步骤整合在任何点处,其中这样的处理可能是有利的。例如,可以将冲击热处理步骤整合在压制站之后、在一系列压制站中的压力机之间的一个或多个位置中和/或在系列中的最后一个压力机之后。在图15中图解地示出了生产线的一个实例。将压力机的顺序布置为五个压制站。图15中所示的生产线包括获得面板的最终形状所需的多达五个压制站(压力机)。在示例性工艺中,由于需要将面板转移到压制站,所以在压制站之前或之间存在等待时间段。在这些等待时间段期间可以实施一个或多个冲击热处理步骤,如图15中的箭头所示。时间长度配合冲压速度。在一种情况下,通过在最后一个压制站之后添加接触加热站来将冲击热处理步骤整合到生产周期中。在另一种情况下,通过在压制站4与压制站5之间添加接触加热站来将冲击热处理步骤整合到生产周期中。在又一种情况下,通过在每个压制站之后或在压制站之间添加接触加热站来将几个冲击热处理步骤整合到在生产周期中。在整合到压制站之间的接触站处将冲击热处理进行5秒至30秒。如果冲击热处理步骤需要多于30秒,例如,30秒至60秒,那么在最后一个压制站之后整合的接触加热站处加入这样的步骤。将冲击热处理整合到生产线中降低了生产成本。上文所引用的所有专利、专利申请、出版物和摘要通过引用以其整体并入本文。已经描述了本发明的多种实施例以实现本发明的多种目的。这些实施例仅仅是本发明的原理的说明。在不脱离如所附权利要求所限定的本发明的精神和范围的情况下,对本领域技术人员来说,其许多修改和改变将是显而易见的。当前第1页12