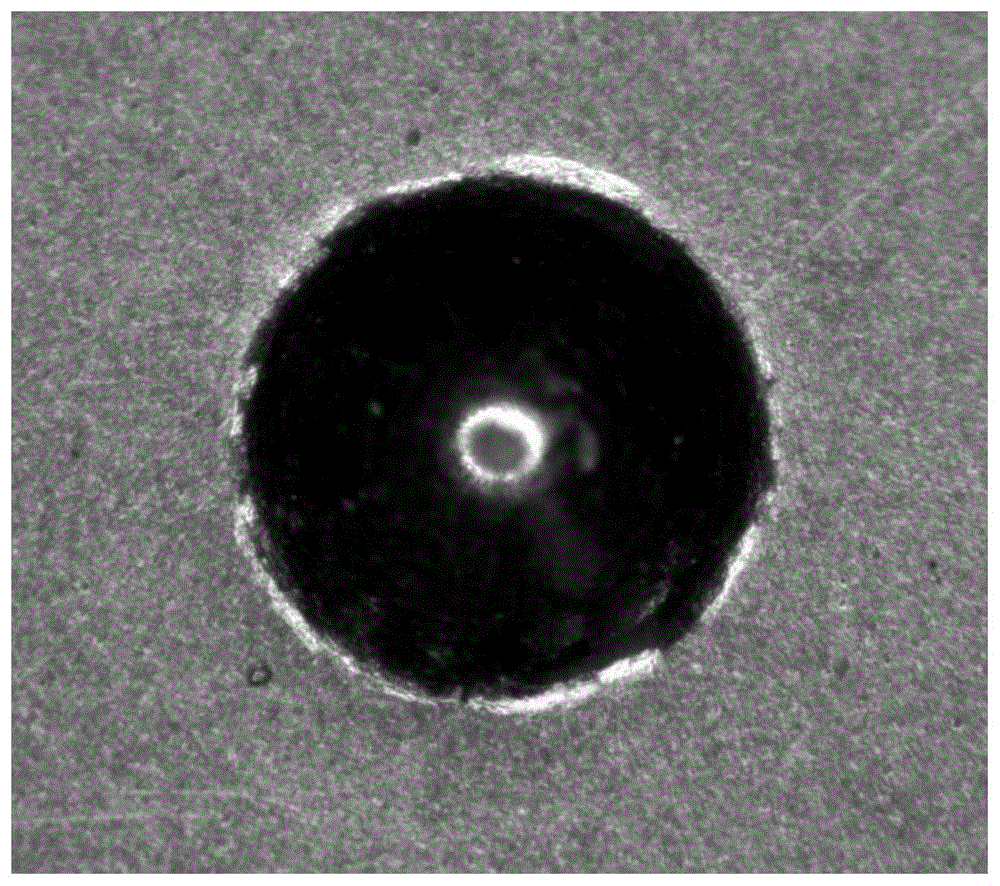
本发明涉及金属材料表面防护
技术领域:
,更具体地,涉及一种用于钛合金基体表面的防护涂层及其制备方法。
背景技术:
:工业应用机械零件的使用失效多发生在表面或从表面开始。据统计,表面损伤失效占全部失效的80%以上;我国每年仅因磨损造成的损失就高达数千亿元。以钛合金为例,钛合金具有密度小、比强度高、可焊性好等优点,主要应用于航空航天和军事工业上,同时在化工、石油、轻工、冶金、发电、体育、医疗等许多工业部门也有着广泛的应用。但是,钛合金耐磨性差,摩擦系数大,易发生粘着磨损,且钛合金很容易在振动构件的交接处发生微动磨损和微动疲劳,界面处的摩擦热和摩擦力将加剧疲劳失效,产生剥落损伤,600℃以上的高温抗氧化性能差,在具有还原性或者络合作用的介质中的不稳定造成腐蚀,这些问题使钛及其合金的应用受到限制,因此也成为材料研究领域的热点之一。目前,钛合金常用的表面硬化处理技术有热喷涂、电镀与化学镀、等离子渗氮、激光熔覆、气相沉积、微弧氧化以及复合型表面处理技术等,例如,周丹丹等人(tc4合金激光熔覆耐磨自润滑涂层的组织与性能研究[d].天津工业大学,2017.)选用h-bn、ti3sic2作为润滑剂通过激光熔覆在钛合金(tc4)表面制备ni基自润滑耐磨减摩涂层,虽然在一定程度上提高了耐磨耐腐蚀性能,但陶瓷类熔覆涂层裂纹及剥落问题严重,韧性和结合力不足。采用阳极氧化工艺在钛合金表面制备纳米tio2,虽然可以有效提高耐磨性能,但是阳极氧化膜结构疏松多孔,限制了对耐蚀性能的提高。因此,需要开发出同时具有良好的韧性、高结合力、高耐磨性和高耐腐蚀性的用于钛合金基体表面的防护涂层。技术实现要素:本发明为克服上述现有技术所述的韧性、结合力、耐磨耐腐蚀不足的缺陷,提供一种用于钛合金基体表面的防护涂层,提供的防护涂层具有良好的韧性、高硬度、高耐磨性和高耐腐蚀性,与基体结合力高,极大地扩展了基体钛合金在严苛环境下的应用范围并延长使用寿命。本发明的另一目的在于提供上述防护涂层的制备方法,提供的制备方法采用电弧离子镀制备防护涂层,工作性能稳定,重复率高,操作方便,工艺简单,制备周期短,成本低,绿色环保,便于大规模工业化生产。为解决上述技术问题,本发明采用的技术方案是:一种用于钛合金基体表面的防护涂层,包括依次层叠设置在基体表面上的cr界面打底层、crn过渡层、crn/zrn纳米多层涂层和crn缓冲层;所述crn/zrn纳米多层涂层由crn纳米涂层和zrn纳米涂层交替层叠构成。所述钛合金可以为tc4。发明人在基体表面上依次沉积cr界面打底层、crn过渡层、crn/zrn纳米多层涂层和crn缓冲层,成功得到用于钛合金基体表面的防护涂层。防护涂层中,cr界面打底层和crn过渡层主要用于改善涂层与钛合金tc4基体的结合力;调制crn/zrn纳米多层涂层的工作层能够降低其内应力,提高其致密度、韧性、硬度以及耐磨耐腐蚀性能;表面crn过渡层能够减缓crn/zrn纳米多层涂层受到外界环境的摩擦磨损及腐蚀介质的侵蚀等造成的破坏。综上,本发明提供的防护涂层具有良好的韧性、高硬度、高耐磨性和高耐腐蚀性,与基体结合力高,极大地扩展了基体钛合金在严苛环境下的应用范围并延长使用寿命,如机械零部件、刀模具、海上作业等产品表面的防护。优选地,所述crn/zrn纳米多层涂层的调制周期为1~500nm,所述crn/zrn纳米多层涂层的厚度为1~500μm。更优选地,所述crn/zrn纳米多层涂层的调制周期为20~150nm。例如,所述crn/zrn纳米多层涂层的调制周期可以为20.6、56或144nm。更优选地,所述crn/zrn纳米多层涂层的厚度为1~50μm。优选地,所述cr界面打底层的厚度为1~5000nm。更优选地,所述cr界面打底层的厚度为500nm。优选地,所述crn过渡层的厚度为1~9000nm。更优选地,所述crn过渡层的厚度为2μm。优选地,所述crn缓冲层的厚度为1~9000nm。更优选地,所述crn缓冲层的厚度为2μm。优选地,所述防护涂层的厚度为1~20nm。本发明还保护上述防护涂层的制备方法,所述制备方法包括如下步骤:s1.将基体清洗刻蚀后,在基体表面沉积cr界面打底层;s2.在cr界面打底层上沉积crn过渡层;s3.在crn过渡层上沉积crn/zrn纳米多层涂层;s4.在crn/zrn纳米多层涂层上沉积crn缓冲层。优选地,所述制备方法还包括如下步骤:s5.在crn缓冲层上沉积第二crn/zrn纳米多层涂层;s6.在第二crn/zrn纳米多层涂层上沉积第二crn缓冲层。优选地,所述沉积通过电弧离子镀进行。优选地,沉积时基体固定在支架上,所述支架自转1.5~15rpm/min,公转0.5~5rpm/min。本发明提供的制备方法采用电弧离子镀制备防护涂层,工作性能稳定,重复率高,操作方便,工艺简单,制备周期短,成本低,绿色环保,便于大规模工业化生产。具体地,步骤s1.如下:a1)清洗基体:将经抛光处理后的基体送入超声波清洗机,依次用丙酮、无水乙醇以15khz~30khz分别进行超声清洗10min~20min,然后用去离子水清洗,再用纯度≥99.5%的氮气吹干;a2)抽真空和离子束刻蚀清洗镀膜腔体:将超声清洗后的基体置于真空室的工件支架上,将沉积腔室工作温度加热至300℃~500℃,基体加热至300℃~500℃,并抽取沉积腔室内气体;抽至真空度5.0×10-3pa以下;a3)离子束脉冲刻蚀清洗:当腔室真空度为3.0×10-3pa~5.0×10-3pa后,通入气体流量为200sccm~450sccm的ar气,调节沉积腔室内环境压力为0.6pa~1.2pa,维持炉温400℃~500℃,工作时间为5~30min;a4)电弧cr离子刻蚀:开启电弧cr靶电源,通入气体流量为200sccm~450sccm的ar气,调节沉积腔室内环境压力为0.6pa~1.2pa,维持炉温400℃~500℃,工作时间为20~60min;a5)沉积cr界面打底层:打开电弧cr靶电源,弧源电流为80a~250a,通入氩气500sccm~1000sccm,控制真空室气压0.6pa~1.2pa,维持炉温400℃~500℃,沉积时间为0~1h。优选地,步骤a2)中使用的加热功率3kw~5kw。优选地,步骤a3)中使用的基体加负偏压-900v~-800v,占空比为50%~70%,加热功率3kw~5kw。优选地,步骤a4)中使用的基体加负偏压-900v~-800v,占空比为50%~70%,加热功率3kw~5kw。优选地,步骤a5)中使用的基体加负偏压-200v~-100v,占空比为60%~80%,加热功率1kw~5kw。具体地,步骤s2.如下:a6)沉积crn过渡层:继续开启电弧cr靶电源,弧源电流为80a~250a,通入氮气500sccm~950sccm,控制真空室气压1.5pa~4pa,维持炉温400℃~500℃,沉积时间为0.5~2h。优选地,步骤a6)中使用的基体加负偏压-200v~-100v,占空比为60%~80%,加热功率3kw~5kw。具体地,步骤s3.如下:a7)沉积crn/zrn纳米多层涂层:开启电弧cr靶电源,并开启一个电弧zr靶,通入氮气500sccm~950sccm,控制真空室气压1.5~4pa,维持炉温400℃~500℃,沉积时间为1~4h。优选地,步骤a6)中使用的基体加负偏压-200v~-100v,占空比为60%~80%,加热功率1kw~5kw。具体地,步骤s4.如下:a8)沉积crn缓冲层(重复a6):继续开启电弧cr靶电源,弧源电流为80a~250a,通入氮气500sccm~950sccm,控制真空室气压1.5pa~4pa,基体加负偏压-200v~-100v,占空比为50%~80%,加热功率3kw~5kw,维持炉温400℃~500℃,沉积时间为0.5~2h。具体地,步骤s5.如下:a9)沉积crn/zrn纳米多层涂层(重复a7):开启电弧cr靶电源,并开启一个电弧zr靶,通入氮气500sccm~950sccm,控制真空室气压1.5pa~4pa,基体加负偏压-200v~-100v,占空比为60%~80%,加热功率3kw~5kw,维持炉温400℃~500℃,沉积时间为1~4h。具体地,步骤s6.如下:a10)沉积crn缓冲层:继续开启电弧cr靶电源,弧源电流为80a~250a,通入氮气500sccm~950sccm,控制真空室气压1.5pa~4pa,基体加负偏压-200v~-100v,占空比为60%~80%,加热功率3kw~5kw,维持炉温400℃~500℃,沉积时间为0.5~2h;a11)沉积结束关闭电源,待真空室温度降至室温,打开真空室取出基体,在基体表面形成防护涂层。与现有技术相比,本发明的有益效果是:本发明基体表面上依次沉积cr界面打底层、crn过渡层、crn/zrn纳米多层涂层和crn缓冲层得到用于钛合金基体表面的防护涂层,制得的防护涂层具有良好的韧性、高硬度、高耐磨性和高耐腐蚀性,与基体结合力高,极大地扩展了基体钛合金在严苛环境下的应用范围并延长使用寿命,如机械零部件、刀模具、海上作业等产品表面的防护。另外,该防护涂层的制备方法采用电弧离子镀制备防护涂层,工作性能稳定,重复率高,操作方便,工艺简单,制备周期短,成本低,绿色环保,便于大规模工业化生产。附图说明图1为本发明实施例1的用于钛合金基体表面的防护涂层的结构示意图。图2为本发明实施例1的防护涂层中crn/zrn纳米多层涂层填补缺陷作用示意图。图3为本发明实施例1的防护涂层、对比例1的单层crn涂层和基体的xrd图。基体为tc4。图4为本发明实施例1的防护涂层的sem形貌图。其中,图4(a)为截面形貌图;图4(b)为放大1万倍下的表面形貌图。图5为本发明实施例1的防护涂层的洛氏压痕图。图6为本发明实施例1的防护涂层、对比例1的单层crn涂层和基体摩擦运行1万圈过程中的摩擦系数。相对湿度45%~60%,运行距离125.6m。图7为本发明实施例1的防护涂层、对比例1的单层crn涂层和基体摩擦运行2万圈过程中的摩擦系数。相对湿度75%~90%,运行距离351.8m。图8为本发明实施例1的防护涂层、对比例1的单层crn涂层和基体的3d磨痕形貌。其中,图8(a)为1万圈后磨损形貌;图8(b)为2万圈后磨损形貌。图9为本发明实施例1的防护涂层、对比例1的单层crn涂层和基体的磨损率柱状图。图10为本发明实施例1的防护涂层、对比例1的单层crn涂层和基体的腐蚀极化曲线图。具体实施方式下面结合具体实施方式对本发明作进一步的说明。本发明实施例的附图中相同或相似的标号对应相同或相似的部件;在本发明的描述中,需要理解的是,若有术语“上”、“下”、“左”、“右”、“顶”、“底”、“内”、“外”等指示的方位或位置关系为基于附图所示的方位或位置关系,仅是为了便于描述本发明和简化描述,而不是指示或暗示所指的装置或元件必须具有特定的方位、以特定的方位构造和操作,因此附图中描述位置关系的用语仅用于示例性说明,不能理解为对本专利的限制。此外,若有“第一”、“第二”等术语仅用于描述目的,主要是用于区分不同的装置、元件或组成部分(具体的种类和构造可能相同也可能不同),并非用于表明或暗示所指示装置、元件或组成部分的相对重要性和数量,而不能理解为指示或者暗示相对重要性。实施例中的原料均可通过市售得到;除非特别说明,本发明采用的试剂、方法和设备为本
技术领域:
常规试剂、方法和设备。实施例1一种用于钛合金基体表面的防护涂层,如图1所示,包括依次层叠设置在基体表面上的cr界面打底层、crn过渡层、crn/zrn纳米多层涂层和crn缓冲层;crn/zrn纳米多层涂层由crn纳米涂层和zrn纳米涂层交替层叠构成,如图2所示。本实施中涂层总厚度为17.7um,调制周期为144nm,其制备方法如下:将经抛光处理后的钛合金(tc4)基体送入超声波清洗机,依次用丙酮、无水乙醇以30khz分别进行超声清洗10min,然后用去离子水清洗,再用纯度≥99.5%的氮气吹干。将超声清洗后的基体置于真空室的工件支架上,加热功率2kw,将沉积腔室工作温度加热至500℃,并抽取沉积腔室内气体至真空度5.0×10-3pa以下。通入气体流量为250sccm的ar气,调节沉积腔室内环境压力为0.9pa,基体加负偏压-950v,占空比为42%,加热功率2kw,维持炉温500℃,进行脉冲辉光清洗,持续时间为7min后,开启电弧cr靶电源,通入气体流量为200sccm的ar气,调节沉积腔室内环境压力为0.8pa,基体加负偏压-950v,占空比为42%,加热功率2kw,炉温保持500℃,进行cr离子刻蚀30min。继续打开电弧cr靶电源,弧源电流为180a,通入氩气200sccm,控制真空室气压0.8pa,基体加负偏压-80v,占空比为70%,加热功率2kw,维持炉温400℃,沉积金属cr层5min。随后通入氮气800sccm,控制真空室气压2pa,基体加负偏压-80v,占空比为70%,加热功率1kw,维持炉温400℃,沉积crn涂层1h。开启电弧cr靶电源的同时开启一个电弧zr靶,通入氮气800sccm,控制真空室气压3pa,基体加负偏压-80v,占空比为70%,加热功率1kw,维持炉温400℃,沉积crn/zrn纳米结构涂层1.5h。关闭电弧zr靶电源,继续开启电弧cr靶电源,弧源电流为180a,通入氩气200sccm,控制真空室气压0.8pa,基体加负偏压-950v,占空比为42%,加热功率2kw,维持炉温500℃,电弧铬离子刻蚀30min。随后继续沉积crn/zrn纳米结构涂层,开启电弧cr靶电源,并开启一个电弧zr靶,通入氮气800sccm,控制真空室气压3pa,基体加负偏压-80v,占空比为70%,加热功率1kw,维持炉温400℃,沉积时间为1.5h。随后再沉积一层crn层:关闭电弧zr靶电源,继续开启电弧cr靶电源,弧源电流为180a,通入氮气800sccm,控制真空室气压2pa,基体加负偏压-80v,占空比为70%,加热功率1kw,维持炉温400℃,沉积时间0.5h后沉积结束。镀膜过程中所述基体支架自转转速为2rpm/min,公转转速为1rpm/min。关闭电源,待真空室温度降至室温,打开真空室取出基体,在基体表面形成的防护涂层。实施例2本实施例为本发明用于钛合金基体表面的防护涂层的第二实施例,与实施例1不同的是,支架自转4rpm/min,公转转速为2rpm/min,涂层厚度为16.3um,调制周期为56nm。实施例3本实施例为本发明用于钛合金基体表面的防护涂层的第二实施例,与实施例1不同的是,支架自转6rpm/min,公转转速为3rpm/min,涂层厚度为15.1um,调制周期为20.6nm。对比例1本对比例中,防护涂层为单层crn涂层;制备方法如下:清洗基体及对样品进行清洗过程同实施例1;开启电弧cr靶电源,弧源电流为180a,通入氮气800sccm,控制真空室气压2pa,基体加负偏压-80v,占空比为70%,加热功率1kw,维持炉400℃,沉积时间8h后沉积结束。关闭电源,待真空室温度降至室温,打开真空室取出基体,在基体表面形成的涂层即为crn单层涂层。结构与性能测试(1)形貌测试通过sem测试防护涂层的形貌,仪器为feinovananosem430,背散射模式,截面放大1万倍,表面放大2万倍。(2)xrd测试xrd采用brukerd8advance进行测试,cu靶、加速电压40kv、电流40ma)扫描步长为0.02°、停留时间0.1s、扫描范围为20~80°。(3)硬度及杨氏模量测试采用纳米压痕仪(antonpaarttx-nht2)测量涂层的硬度与弹性模量,测量载荷为5mn、加载速率为10mn/min,重复测量10次,压入深度不超过涂层厚度的1/10,取其平均值表征涂层硬度;另外,该过程可同时测量出杨氏模量。(4)结合力测试采用洛氏压痕仪测试涂层膜-基结合力,hr-150dt型电动洛氏硬度计,金刚石洛氏压头,压力为150kgf(1471n)。(5)耐磨性能测试采用摩擦磨损实验机研究涂层在不同磨擦圈数下的耐磨性能,仪器为csmtht-1000型球盘式高温摩擦磨损仪,磨球运行速度10mm/s,运行半径2mm,运行圈数10000,压力为5n;3d磨痕形貌使用仪器为ols4100型激光共聚焦。(6)耐腐蚀性能测试采用电化学工作站测试涂层及基体的耐腐蚀性能,仪器为1470e电化学工作站,动电位极化曲线,扫描范围-0.8~0.3v,在室温下3.5%nacl溶液中采用三电极体系(ag/agcl(饱和)作参比电极)测试样品的腐蚀极化曲线图。测试结果表1硬度及杨氏模量测试结果h(gpa)e(gpa)h/eh3/e2tc44.22139.570.030.004实施例121.58351.100.060.08由图3可知,实施例1的防护涂层主要由crn、zrn组成。如表1所示,该防护涂层能有效提高表面硬度5倍以上,并且根据h/e、h3/e2值的提高,显示出涂层良好的韧性,即具有更好的抗裂纹扩展能力。利用sem观察实施例1的防护涂层的形貌,如图4所示。由图5可知,防护涂层与基体具有优异的结合力。由图6~9可知,本发明实施例1提供的防护涂层具有摩擦系数低,耐磨性能优异的特点,即使摩擦距离的延长也对涂层的磨损没有造成明显变化。由图10可以看出,实施例1提供的防护涂层自腐蚀电流最小,具有最好的耐腐蚀性能,能够对基体进行有效的防护。显然,本发明的上述实施例仅仅是为清楚地说明本发明所作的举例,而并非是对本发明的实施方式的限定。对于所属领域的普通技术人员来说,在上述说明的基础上还可以做出其它不同形式的变化或变动。这里无需也无法对所有的实施方式予以穷举。凡在本发明的精神和原则之内所作的任何修改、等同替换和改进等,均应包含在本发明权利要求的保护范围之内。当前第1页12