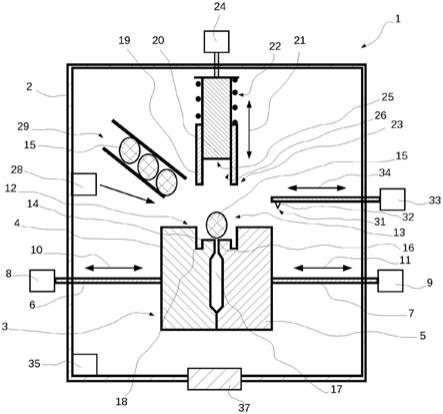
[0001]
本发明涉及一种用于制造由非晶态或部分非晶态金属形成的铸件的设备,其包括:铸件模具,该铸件模具具有用于引入形成铸件的铸造材料的至少一个浇注口;以及用于熔融铸造材料的装置。本发明还涉及一种用于制造铸件的方法以及一种由非晶态或部分非晶态金属制成的铸件。
背景技术:[0002]
非晶态金属为无结晶凝聚的金属材料。它们又称为金属玻璃,并因其非晶态或部分非晶态结构而具有卓越的机械特性。
[0003]
现有技术中已知用于制造由非晶态金属制成的铸件的设备和方法。为此,在坩埚中感应加热铸造材料,并在压铸法中借助铸压柱塞将铸造材料通过浇注口压入到永久铸模中。
[0004]
其缺陷在于,因使用熔融坩埚,可能将杂质引入熔体,从而在凝聚期间引起结晶。这意味着丧失有利的机械特性。另外,在所谓的冷坩埚法中,因感应加热铸造材料,只能达到比铸造材料的熔融温度高出约50℃至60℃的轻微过热。为了确保非晶态凝聚,必须将铸造材料优选地加热到远高于其熔融温度的温度,尤其是高出75℃至1300℃。
技术实现要素:[0005]
本发明的目的是提供一种用于制造由非晶态或部分非晶态金属制成的铸件的设备,该设备能够实现铸件的极高过热,并且能够简化加工。
[0006]
本发明用以达成上述目的的解决方案为熔融装置具有至少一个设置用于熔融铸造材料的区域。
[0007]
在所述设备的熔融区域内,铸造材料可以熔融并过热高达1300℃。可以将为此所需的能量极有针对性地引入到铸造材料中,该铸造材料例如可以呈现丸粒形式。
[0008]
所述设备的周围区域或相邻部件有利地不受热应力。此外,铸造材料仅在引入到铸件模具的前才熔融。在熔体温度能够急剧下降时不必从熔炉中进行输送。根据本发明的设备可以提高过热,还会确保待制造的铸件可以非晶态或部分非晶态凝聚,尤其是主要非晶态凝聚。
[0009]
适宜地,熔融装置具有用于在至少一个熔融区域中形成至少一个电弧的机构,该机构尤其是包括至少两个彼此间隔布置的电极,在该至少两个电极之间能够形成至少一个电弧。电弧可以从电极向铸造材料延伸,尤其是呈现为丸粒并待熔融的铸造材料,和/或电弧可以被引导经过铸造材料的表面的上方。有利地,将熔融所需的能量输入有针对性地引入丸粒,而周围区域不受热应力。如果设置多个其中应熔融铸造材料的区域,则可以设置多个电极,发自这些电极的各自至少一个电弧向待熔融的铸造材料延伸。也可设想,形成多个电弧,以熔融单一的优选呈丸粒形式的铸造材料。铸造材料可以极高过热且更快熔融。
[0010]
还可设想,通过激光和/或电子束熔融铸造材料。
[0011]
在本发明一实施方案中,至少两个电极之一至少部分地由铸造材料制成。有利地,铸造材料无需单独的电接触。由此简化制造过程中的操作。
[0012]
在本发明另一实施方案中,至少一个熔融区域被引入到铸件模具中。为此,熔融区域优选地与铸件模具的浇注口流体连通。通过优选使用电弧、激光束和/或电子束来熔融铸造材料,将能量输入局部限定于铸造材料。不会对铸件模具造成热损伤。有利地,铸造材料可以熔融并立即通过浇注口引入到模具中。不再需要从远距离熔融区域到铸件模具的传输路径。
[0013]
如果设置多个熔融区域,则可以例如使用单个铸件模具同时制造多个铸件。
[0014]
也可设想,设置多个熔融区域,以通过多个浇注口浇灌单个模具型腔。可以有利地制造更大型的铸件。
[0015]
适宜地,至少一个熔融区域包括用于容纳铸造材料的尤其是凹腔状的凹部和/或底座状的凸部,并优选至少部分地围绕至少一个浇注口布置。铸造材料可以放置在底座上或引入到凹部中并且熔融。也可设想,设置具有容纳底座的凹部。
[0016]
浇注口与底座和/或凹部流体连通,因此熔融的铸造材料可以直接通过该浇注口引入到铸件模具的模具型腔中。
[0017]
铸造材料可以例如作为丸粒放置到浇注口上,以便覆盖该浇注口。由于非晶态或部分非晶态凝聚的熔融金属合金的高粘性和/或高表面张力,丸粒在熔融状态下保持其形状并覆盖浇注口,直至借助铸压柱塞将其压入。
[0018]
在本发明一实施方案中,至少一个熔融区域由设置用于将熔融的铸造材料引入到铸件模具的模具型腔中的尤其是圆柱形的铸压柱塞的端面以及用于导引安置铸压柱塞的导引机构的内壁界定,其中,导引机构优选地包括圆柱形的套筒。内壁和铸压柱塞的端面形成坩埚,在该坩埚中可以将铸造材料在引入到铸件模具的前一刻熔融。可以有利地逆向于重力作用方向(“自下方”)浇灌铸件模具。如果控制铸压柱塞的移动,则可以设定模具浇灌速度或速度分布曲线。为此,可以设置控制装置,该控制装置尤其是设置用于使铸压柱塞和套筒向铸件模具的浇注口的方向同时移动。
[0019]
熔融的铸造材料在引入到铸件模具之前仅极为短暂地停留在所形成的坩埚中,这样有利地排除了污染。
[0020]
在本发明另一实施方案中,至少一个设置用于将熔融的铸造材料引入到模具型腔中的尤其是圆柱形的铸压柱塞能够相对于用于导引安置铸压柱塞的导引机构移动,尤其是逆向于复位机构的复位力的作用方向移动。复位机构可以例如包括弹簧。导引机构的壁部例如构造为套筒,并突出超过铸压柱塞与熔融的铸造材料相接触的底面。由此,当将套筒对接至铸件模具时,可以形成由套筒的内壁、铸压柱塞的端面和包含浇注口的铸件模具部段界定的空间。通过铸压柱塞相对于导引机构的相对移动,空间减小,并且布置在该空间中的熔融的铸造材料被压入到模具中。一旦完成引入铸造材料,则铸压柱塞与套筒共同离开铸件模具而导引到起始位置。在此情形下,复位力促使铸压柱塞移动到其起始位置,在该起始位置中,该空间具有最大体积,并且可以执行新的铸造过程。
[0021]
在本发明一实施方案中,至少一个熔融区域设置成用于接纳导引机构,并尤其是具有优选地呈环形的凹槽。环形凹槽尤其是置于铸件模具中。由此,用于形成在将铸造材料
引入到铸件模具之前接纳铸造材料的空间的导引机构可以与包含浇注口的铸件模具部段密封地连接。由此,铸造材料当压入时只会引入到铸件模具中。
[0022]
适宜地,铸件模具的温度可变。优选地,可通过调控装置调节温度。铸件模具可以例如采用风冷、水冷和/或油冷。另外,可以通过连续的过程管理使铸件模具的温度保持恒定。由此提高过程稳定性。
[0023]
在本发明另一实施方案中,所述设备包括用于将熔融的铸造材料排气和/或抽吸到铸件模具中的装置,优选地当将铸造材料引入到模具时,该装置可激活。由此,除铸压柱塞的压力之外,还可以施加吸力,该吸力将熔融的铸造材料抽吸到铸件模具中。这一点特别有利于铸造熔融的高粘性合金。另外,通过排气,即抽吸模具气体,该气体例如可以是诸如氩气等吹扫气体,不会在铸件中形成任何气体夹杂物。有利地,可以获得极佳的铸造质量。
[0024]
适宜地,铸件模具由至少两个部分形成,并优选地由特别导热的材料制成,优选地由铜或铜合金制成。为了防止非晶态或部分非晶态凝聚的金属合金发生非期望的结晶,需要高速冷却。特别适用的是由铜或铜合金制成的铸件。如果铸件模具由至少两个部分构成,则可以打开和闭合模具,尤其是可以多次使用该模具作为永久铸模。
[0025]
在本发明另一实施方案中,所述设备具有尤其是气密的壳体,至少铸件模具以及至少一个熔融区域被引入到该壳体中。有利地,壳体可以被抽空和/或填充有保护气体,例如氩气或其他惰性气体,使得壳体内部不再存在任何氧气。由此,在熔融期间或将材料引入到铸件模具期间,铸造材料都不可能发生氧化。有利地,可以制造出最高质量的铸件。
[0026]
在本发明一实施方案中,设置供料装置,该供料装置被配置成将固体铸造材料引入到至少一个熔融区域中。它可以例如是丸粒仓,在每次铸造过程之后,将新的丸粒仓引入到熔融区域中。有利地,根据本发明的制造方法可以实现自动化。
[0027]
适宜地,设置用于确定铸造材料、熔融的铸造材料和/或铸件模具的温度的机构,优选为高温计。有利地,可以在任何时刻监测温度,尤其是过热温度,该过热温度比铸造材料的熔融温度高出75℃至1300℃,优选地至多800℃。
附图说明
[0028]
下面结合实施例和实施例的相关附图详细说明本发明。图中:
[0029]
图1a至图1e示出根据本发明的设备的示意图;
[0030]
图2示出根据本发明的设备的又一实施方式的示意图;
[0031]
图3示出根据本发明的设备的细节图;
[0032]
图4示出根据本发明的设备的又一实施方式的示意图;
[0033]
图5示出根据本发明的设备的特殊实施方式的示意图;
[0034]
图6示出根据本发明的设备的另一特殊实施方式的细节图。
具体实施方式
[0035]
图1a至图1e示意性示出设备1的横向剖视图,该设备包括壳体2,由铜制成的两件式水冷铸件模具3嵌入到该壳体中。铸件模具3的两个部分4、5中的每一个均借助连杆6、7连接到各自用于使连杆6、7移动的电动机8、9,该电动机附接至壳体外部。通过使连杆6、7移动,可以打开铸件模具3以沿双箭头10、11的方向拾取铸件,并可以闭合铸件模具3以制造另
外的铸件。
[0036]
在铸件模具3的上侧12引入熔融区域13,该熔融区域具有由铸件模具3的两个部分4、5形成的底座14,并且铸造材料丸粒15放置到该熔融区域上。丸粒15完全覆盖浇注口16,通过该浇注口可以用铸造材料浇灌模具型腔17。围绕底座14布置有凹槽18,该凹槽设置成用于接纳圆柱形的套筒19。套筒19被配置成导引圆柱形的铸压柱塞20并包围该铸压柱塞。通过电动机24可以使铸压柱塞20和套筒19共同沿双箭头21的方向移动,并且铸压柱塞20布置成能顺向或逆向弹簧22的复位力在轴向方向上相对于套筒19移动。为了引入可加热到高达1300℃、优选地高达800℃的熔融的铸造材料15,使铸压柱塞20和套筒19共同向铸件模具3方向移动,直至套筒19的下段23接合到凹槽18中。铸造柱塞20向铸件模具3方向的进一步移动克服弹簧22的复位力。由此减小图1c所示由铸造柱塞20的端面25以及套筒的内壁26和铸件模具3的上侧12形成的空间27,使得熔融的铸造材料15沿垂直方向压入到模具型腔17中。
[0037]
另外,该设备包括在熔融期间检测丸粒15的温度的高温计28以及构造为丸粒仓的供料装置29。由此,在每次铸造之后,可以将新的丸粒15自动放置到熔融区域13的底座14上。
[0038]
通过图1b所示在设有尖端31的钨电极32与丸粒15之间形成的电弧30,对铸造材料丸粒15进行加热。壳体2以及铸件模具3和丸粒15为此以导电方式彼此连接,并形成钨电极32的对电极。钨电极32以能移动的方式布置在壳体2中,并可以借助电动机33沿双箭头34的方向朝向熔融区域13移动且在熔融之后移动离开熔融区域13。
[0039]
还可设想,设置用于形成激光束和/或电子束的装置(图1未示出),该装置被配置成在熔融区域13中加热铸造材料丸粒15。
[0040]
此外,设置用于抽空壳体2的真空泵(未示出)以及用于引入诸如氩气等保护气体的机构(同样未示出)。附加地,壳体2内部存在所谓的吸气剂35,该吸气剂构造为钛板,并在铸造材料15熔融之前受到加热。由于钛对氧气的亲和力极高并且氧气在钛中的可溶性极高,因此从提供保护气体的壳体气体中去除氧气残留。这样就能额外地清洁气体。
[0041]
通过图1a至图1e示意性示出的闸门37可以拾取铸件36。由此,不必在每次铸造过程之前重新抽空整个壳体2。
[0042]
制造铸件36包括以下方法步骤,尤其是按下列顺序:
[0043]-将钨电极32从图1a所示的起始位置移动到图1b所示的终止位置至待熔融的铸造材料丸粒15的上方;
[0044]-抽空壳体2,并引入保护气体,优选地氩气;
[0045]-将优选地由钛制成的吸气剂35加热到高于600℃的温度;
[0046]-在钨电极32的尖端31与丸粒15之间形成电弧30,用于熔融丸粒15,并将该丸粒过热到比其熔融温度高出75℃至1300℃的温度;
[0047]-关断电弧,并将钨电极32移回到图1a所示的起始位置;
[0048]-将铸压柱塞20和套筒19向熔融区域13的方向移动,直至套筒19的下段23接合到凹槽18中,从而如图1c所示,在铸压柱塞20与浇注口16之间形成包围熔融丸粒15的空间27;
[0049]-将铸压柱塞20逆向弹簧22的弹力相对于套筒19相对移动,以减小空间27,由此将熔融的铸造材料15通过浇注口16压入到铸件模具3的模具型腔17中,以形成铸件36,这种移
动是铸压柱塞20从图1c所示的起始浇灌位置到图1d所示的终止位置的移动,在该终止位置中,模具型腔17浇灌有铸造材料15;
[0050]-将铸压柱塞20和套筒19移离到图1a所示熔融区域13上方的起始位置;
[0051]-将铸件模具3的两个部分4、5彼此相背地移动到图3所示的铸件拾取位置,并沿箭头38的方向通过闸门37拾取铸件36;
[0052]-闭合铸件模具3,并将新的丸粒15从丸粒仓29供送到熔融区域13中。
[0053]
可以设想附加的方法步骤,其中开始压入铸造材料时,抽吸装置(图1a至图1e未示出)可激活,该抽吸装置产生负压,通过该负压抽空铸件模具3,并将熔融的铸造材料15额外地抽吸到铸件模具3中。
[0054]
还可设想,通过激光束和/或电子束熔融铸造材料15。
[0055]
现参照图2,本图中与图1a至图1e中相同或作用相同的部分标有相同的附图标记,并且相关的附图标记均添加有字母a。
[0056]
图2所示的设备1a与图1a至图1e所示的设备的区别在于,设置两个电极32a、38,它们被配置为形成两个用于熔融铸造材料丸粒15a的电弧30a、39。有利地,可以更快地加热,实现更高的过热,并且加工大型铸造材料丸粒15a。
[0057]
现参照图3,本图中与图1a至图1e和图2中相同或作用相同的部分标有相同的附图标记,并且相关的附图标记均添加有字母b。
[0058]
图3的俯视图中所示的根据本发明的设备1b的铸件模具3b与图1和图2中所示的铸件模具3b的区别在于,设置两个具有底座的熔融区域13b、40,置于这两个熔融区域上的两个丸粒15b覆盖两个浇注口16b、41(如虚线所示)。不言而喻,为了在每个熔融区域13b、40中进行熔融,需要至少一个电弧和具有套筒的铸造柱塞(图3未示出)。两个丸粒15b尤其是被同步熔融,并且熔融的铸造材料丸粒15b通过优选地两个铸造柱塞和套筒的同步运动而被压入到铸件模具3b中。
[0059]
在此情形下,可以浇灌单个模具型腔,也可以同时浇灌多个模具型腔。从而,利用根据本发明的设备,可以借助单个铸件模具同时制造超大型铸件或多个铸件。
[0060]
现参照图4,本图中与图1a至图1e、图2和图3中相同或作用相同的部分标有相同的附图标记,并且相关的附图标记均添加有字母c。
[0061]
图4中所示的设备1c与图1中所示的设备的区别在于,铸造柱塞20c和套筒19c被设置成从铸造模具3c的下侧42将铸造材料15c引入其中。能够有利地实现特别的分层浇灌。为了清楚起见,图4既未示出用于丸粒的供料装置,也未示出高温计。
[0062]
由铸造柱塞20c的端面25c和套筒19c的内壁26c形成坩埚状熔融区域13c,其中放置有丸粒15c。铸造柱塞20c和丸粒15c形成钨电极32c的对电极,钨极32c与丸粒15c之间可以形成有电弧(图4中未示出)以熔融丸粒15c。
[0063]
现参照图5,本图中与图1a至图1e、图2、图3和图4中相同或作用相同的部分标有相同的附图标记,并且相关的附图标记均添加有字母d。
[0064]
图5所示的设备1d与图1至图4所示的设备的区别在于,设置抽吸装置43,该抽吸装置通过抽吸通道44与铸件模具通道45流体连通。抽吸装置43可激活,并且当铸造柱塞20d移动时,通过该铸造柱塞20d将熔融的铸造材料15d抽吸到铸件模具3d中,优选地从背离该铸造柱塞20d的侧面将熔融的铸造材料15d额外地抽吸到铸件模具3d中。该额外的吸力能够有
利地实现更佳地浇灌铸件模具。
[0065]
不言而喻,抽吸装置43也可以布置在壳体2d的外部。还应理解,从抽吸通道44到铸件模具通道45的过渡区域被构造成还可以形成多件式铸件模具的开口。
[0066]
现参照图6,本图中与图1a至图1e、图2、图3、图4和图5中相同或作用相同的部分标有相同的附图标记,并且相关的附图标记均添加有字母e。
[0067]
图6所示的两件式铸件模具3e与图1至图5所示的铸件模具3、3a、3b、3c、3d的区别在于,可以水平地浇灌模具型腔17e。熔融区域13e在铸件模具3e的一部分5e中包括凹部14e,图6a所示的熔融的铸造材料丸粒15e位于其中。
[0068]
套筒19e在套筒下段23e中具有开口46,熔融的铸造材料15e可以通过该开口引入到铸件模具3e的模具型腔17e中。另外,铸造柱塞20e的端面25e呈倾斜构造。该端面的法线指向浇注口16e的方向。当铸造柱塞20e移动以浇灌模具型腔17e时,有利地确保将熔融的铸造材料丸粒15e通过浇注口16e供送到模具型腔17e中。为此,套筒19e的外侧和铸件模具3e的外侧以及套筒19e的端面和铸件模具3e的上侧进一步形成图6b所示的密封面。图6b所示的铸造柱塞位置对应于图1c所示的铸造柱塞位置。
[0069]
可以设想,在电极与单个尤其是丸粒状的铸造材料15、15a、15b、15c、15d、15e之间形成多个电弧30、30a、39。
[0070]
还可设想,铸件模具3、3a、3b、3c、3d、3e设置有多个不同尺寸的浇注口16、16a、16b、41、16c、16d、16e。为此有利的是,将铸造柱塞20、20a、20b、20c、20d、20e的尺寸减小到浇注口16、16a、16b、41、16c、16d、16e的尺寸和/或匹配于铸件丸粒15、15a、15b、15c、15d、16e的尺寸。为此,在设备1、1a、1b、1c、1d、1e中可以设置例如具有不同直径的不同尺寸的铸造柱塞20、20a、20b、20c、20d、20e。