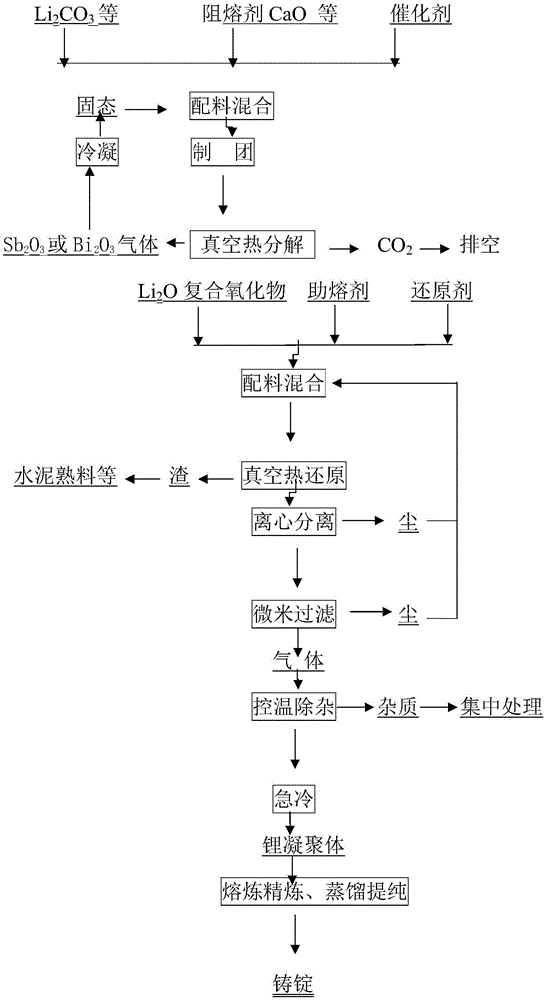
本发明属于轻金属制备
技术领域:
,涉及高纯金属锂的提取和提纯方法,具体为一种用真空热还原法制备高纯度金属锂的方法。
背景技术:
:金属锂原子序数为3,原子核由三个质子和四个中子组成,核的周围有三个电子,在k电子层上有2个电子,电子层结构为1s22s1,锂的化学性质非常活泼,能与许多元素形成重要的化合物和固溶体,形成的合金如镁锂合金,为密排六方晶格或体心立方晶格,具有可加工性,金属锂与空气中的h2o、o2、n2、co2等均可反应,造成得到纯的锂比较困难。金属锂的熔点为180.54℃,沸点为1327±10℃,在800℃时,纯金属锂的蒸汽压为390.6pa,使保持还原得到的锂以金属锂蒸汽的状态存在,采用在高真空过滤时成为可能,可以除掉携带的尘。li、k、na、ca、mg等金属的饱和蒸汽压,与金属锂的饱和蒸汽压有差别,可经过控制冷凝温度、冷却温度速度梯度,可以把k、na、ca、mg进行部分分离,li纯度达到国标。目前工业上生产锂的唯一方法是高温电解氯化锂-氯化钾熔融盐法,这种方法固定资产投资巨大,锂的密度仅为0.53g/cm3,金属易暴露表面,电解、熔炼、精炼时易造成挥发损失,收率偏低,氯盐电解环保投资巨大,有氯气产生,环保不易解决,制造成本高,电解锂含k、na、mg高,分离比较困难。另外,锂的碳酸盐、硝酸盐等锂盐熔点低,在热分解时呈液态,分解率低,且在工业上不易控制,过去的资料报道金属还原中得到的金属锂纯度不高,还原率不高,氧化物具有强腐蚀性,设备材质易损,为工业化生产增加了难度。金属锂具有许多优异的性质,并无可替代性,在原子能工业、热核反应、洲际导弹、人造卫星等诸多领域都有应用,一个核聚变反应堆中金属锂用量就达到500-1000吨;锂的合金应用领域更加广泛,镁锂合金是目前世界上最轻的结构材料,锂是理想的电池材料,广泛被应用,在高科技领域、国防、航天航空等诸多领域都有不可替代的作用;因此,降低锂的生产成本,扩大生产就变得很有必要。技术实现要素:本发明根据以上技术问题,提供一种用真空热还原法制备高纯度金属锂的新方法。该方法所采用的原料来源广泛,价格低,得到的还原物气相便于提纯。用真空热还原法制备高纯度金属锂,固定资产投资少、收率高、制造成本低,可连续化自动化生产出高纯度的金属锂。为了实现以上发明目的,本发明的具体技术方案如下:一种用真空热还原法制备高纯度金属锂的方法,其包括以下步骤:1)将含锂的原料、阻熔剂和催化剂按比例混合后压力制团;制团后的混合物放置在工业管式炉内进行热分解,催化剂升华冷凝后再利用,氧化锂与阻熔剂生成不饱和的复合氧化物。作为优选,所述的工业管式炉为带有气相沉积氮碳化合物坩埚的工业管式炉。所述含锂的原料的为碳酸盐、硝酸盐、硫酸盐、硅酸盐或含锂的硫化物;所述的阻熔剂为cao、al2o3、或cao与al2o3的混合物,al2o3为工业氧化铝;所述的催化剂为sb2o3或bi2o3。cao杂质含量(k+na)≤0.05%,si≤1%,mg≤0.5%的caco3烧制而成,亦可用化学沉淀法制得cao。催化剂中锑、铋氧化物不参与化学反应,加入的三氧化二锑、氧化铋仅仅是起到吸附液态碳酸锂的作用,使之不能或使液珠变大,有利于碳酸锂的热分解,也就是使碳酸锂的热分解表面积增加,当分解完成后,三氧化二锑和氧化铋又会汽化升华离开生成物,减少了氧化钙加入量,增加单位生产能力。反应温度可降低,主要作用由于反应界面面积增加,可提高反应速度,对产品质量没有影响,相同条件下可提高分解率12-15%。作为优选,含锂的原料、阻熔剂和催化剂的质量比为32-40∶58-67∶1-3。热分解高温钢的真空反应炉内的真空度为10-20pa,温度600-1300℃。步骤1)中含锂的原料、阻熔剂和催化剂在混合前需在球磨机中进行磨细至40-100um;制团要求为杏核形,25-35g/个重,压力制团的条件为35-45mpa,热分解温度为600-1300℃,分解率达到99%以上。2)将步骤1)中生成的不饱和的复合氧化物与还原剂、助熔剂分别粉碎球磨后制团。其球磨后的粒度为40-100um,制团的条件为:在30-45mpa压制成25-35g/个,杏核形。3)将步骤2)中的球团装入高温钢的真空反应炉内真空还原,此时还原产物为锂的蒸汽,蒸汽中会夹带有一些还原物料的尘及少量也可被还原出来的金属杂质。所述的还原剂为高硅的硅铁,al含量≥99wt%的铝粉,活性大于70wt%且粒度小于8um的铝粉,铝硅合量大于等于98%的铝硅粉或碳粉,助熔剂为caf2,其纯度为97.5%。作为优选,不饱和复合氧化物,还原剂与助熔剂质量比为79-85:12-20∶1-3。热还原工业耐热钢管式炉的真空度为1-15pa,温度800-1300℃,热还原时间为8~12小时。4)将步骤3)中携带有固体物料的锂的蒸汽通过除尘室中的离心过滤器,然后进入第一冷凝室,用气流速度为1.2-1.8m/sec的气体,控制离心分离器与第一冷凝室温度在700-800℃;携带大于20um的98%的固体颗粒气体通过第一冷凝室时被除去,通过0.5um的微米陶瓷过滤器时>99.95的携带尘被净化,出口温度控制在650-700℃;5)被净化后纯的锂的蒸汽通过急冷装置的第二冷凝室,第二冷凝室内的冷凝器外层用小于-100℃的冷却液体与金属气体进行热交换,气体温度急剧冷却到50-80℃,使金属气体冷凝为凝聚态的金属锂。所述急冷控温装置包括反应区、除尘室、第一冷凝室、第二冷凝室、除尘室排渣孔和真空管,其反应区与除尘室连通;除尘室内设离心分离器,在除尘室的下端设置漏斗;在漏斗的一侧下端设置加热区进口一,漏斗的底部为除尘室排渣孔;在除尘室一侧的上端设置加热区出口一,在除尘室的顶部设置第一冷凝室,在第一冷凝室与除尘室连接的位置上端设置加热区出口二,在第一冷凝室内设置陶瓷微米过滤器;第一冷凝室与第二冷凝室连通;在第一冷凝室内与第二冷凝室连接的位置设置加热区进口二;在第二冷凝室内与第一冷凝室连接处设置真空管,在第二冷凝室两侧分别设置冷却液进口和冷却风进口、冷却液出口和冷却风出口。所述的第一冷凝室和第二冷凝室均为双层套管式冷却器,第二冷凝室内冷却器中心的气体流速为1.5-4m/sec,冷却面积与凝象的金属比为0.4-0.7dm3/kg。携带一定的固体物料粉尘中含有被还原出来的其他金属杂质,通过离心沉淀,微米级陶瓷复合材料装置滤掉尘,用控制气流速度、冷却速度、冷却温度和冷凝温度梯度把其他金属杂质与凝聚锂分离,得到高纯的锂的蒸汽,采用急剧降温冷却的方式得到凝聚态的金属锂,锂的收率大于98.5%,渣中锂含量<0.04%。6)将凝聚态的金属锂在井式炉内,并在ar气保护下进行熔剂熔炼,蒸馏,得到高纯度锂。精炼后得到高纯度金属锂,铸锭,得到的锂纯度为99.0-99.99%wt。本发明的积极效果体现在:(一)采用真空热还原法生产锂,原料来源广泛,价格低,得到的还原物气相便于提纯;固定资产投资少,制造成本低,易于实现工业化。(二)解决了热分解时出现液相不易分解的难题,分解率高,热还原率高。(三)热分解和热还原反应炉抗高温、腐蚀、耐磨、寿命长,充分利用还原反应时的热量进行了气固分离除杂,金属锂得到提纯,产品纯度高,回收率高,节能环保,固定投资少,制造成本低,具有很好的经济效益,可以规模化生产。附图说明:图1为本发明所述利用真空热还原法制备高纯金属锂的工艺流程示意图。图2为本发明所述急冷装置的结构示意图。其中,1——反应区、2——除尘室、3——第一冷凝室、4——第二冷凝室、5——除尘室排渣孔、6——真空管、7——加热区进口一、8——加热区出口一、9——加热区进口二、10——加热区出口二、11——冷却液出口、12——冷却液进口、13——冷却风进口、14——冷却风出口、15——陶瓷微米过滤器。具体实施方式为了使本发明的目的、技术方案及优点更加清楚明白,下面结合具体实施方式对本发明作进一步的详细描述,但不应将此理解为本发明上述主题的范围仅限于下述实施例。以下实施例中所采用的急冷装置包括反应区、除尘室、第一冷凝室、第二冷凝室、除尘室排渣孔和真空管,其反应区与除尘室连通;除尘室内设离心分离器,在除尘室的下端设置漏斗;在漏斗的一侧下端设置加热区进口一,漏斗的底部为除尘室排渣孔;在除尘室一侧的上端设置加热区出口一,在除尘室的顶部设置第一冷凝室,在第一冷凝室与除尘室连接的位置上端设置加热区出口二,在第一冷凝室内设置陶瓷微米过滤器;第一冷凝室与第二冷凝室连通;在第一冷凝室内与第二冷凝室连接的位置设置加热区进口二;在第二冷凝室内与第一冷凝室连接处设置真空管,在第二冷凝室两侧分别设置冷却液进口和冷却风进口、冷却液出口和冷却风出口。所述的第一冷凝室和第二冷凝室均为双层套管式冷却器,第二冷凝室内冷却器中心的气体流速为1.5-4m/sec,冷却面积与凝象的金属比为0.4-0.7dm3/kg。以下实施例中所记载的%,如无特殊说明,均表示其wt%。实施例1:1)按比例称取原料,其中碳酸锂的粒度为89um,氧化钙的粒度为74um,将碳酸锂、阻熔剂cao和催化剂sb2o3按摩尔比1:1.6:0.4的比例混合,并在35mpa的压力条件下制团;团块28克/个,团形状为杏核状。将制作好的球团放在φ330mm*3300mm,且带有气相沉积氮碳化合物坩埚的工业管式炉中进行热分解,催化剂升华冷凝后可再利用,氧化锂与阻熔剂生成不饱和的复合氧化物。工业管式炉的真空度为10pa,温度860℃。高温分解时间5小时,碳酸锂分解成氧化锂的分解率99.2%,锂收率达到99.5%。2)分别将步骤1)中得到的氧化锂和阻熔剂形成的不饱和复合氧化物与硅铁、caf2分别粉碎球磨至粒度60um,按照质量比81:17:2配料混合,在30mpa压制成28g/个的球团。3)将步骤2)中的球团装入φ330mm*3300mm的工业耐热钢管式炉内进行真空还原,炉内真空度3pa,温度1200℃;此时还原产物为气态,并携带有固体物料;锂的还原率为99%。4)将携带有固体物料的气体通过控温装置内除尘室中的离心分离器,接着通过第一冷凝室,第一冷凝室带有夹层,用气流速度为1.5m/sec的气体,控制离心分离器与第一冷凝室温度为750℃。携带大于20um的98%的固体颗粒气体通过第一冷凝室时被除去,通过0.5um的微米陶瓷过滤器时>99.95的携带尘被净化,出口温度控制在680℃。5)被净化后纯的金属气体通过急冷装置的第二冷凝室,在第二冷凝室的双层套管式冷却器内,内层温度控制在60℃,外层用-110℃的低温冷却液体与金属气体进行热交换,冷却器中心通过3m/sec的气体带走传热到内壁的热量,冷却面积为0.65dm3/kg,可迅速使金属气体冷凝为金属凝聚相。6)将凝聚相的金属锂在井式炉内,在ar气保护下并搅拌进行熔剂熔炼、精炼,得到纯度为99%的锂金属粗锭。7)将粗锂金属进行蒸馏分离,控制蒸馏器下部温度为550℃,中部温度控制在450℃,上部温度控制在70℃,下部除去高熔点杂质fe、ni、co、si、ca等;上部除去低熔点金属杂质k、na等,中部排出为li金属铸锭。将经蒸馏后铸锭得到的商品进行化学成分检测(icp测试),所得到锂锭的化学成分检测结果(wt%)见下表。liknacafesial99.9910.00040.00090.00050.00050.00050.0005nicumgcl-npb0.00040.00050.00050.00080.0030.0005由实施例1可知,通过该方法,本发明可制备得到纯度为99.99%的纯锂,适用于较多纯锂需求领域。实施例2:1)按比例称取原料,其中碳酸锂的粒度为80um,氧化钙的粒度为65um,将碳酸锂、阻熔剂cao和催化剂sb2o3按摩尔比1:1.6:0.4的比例混合,并在40mpa的压力条件下制团;团块28克/个,团形状为杏核状。将制作好的球团放在φ330mm*3300mm,且带有气相沉积氮碳化合物坩埚的工业管式炉中进行热分解,催化剂升华冷凝后可再利用,氧化锂与阻熔剂生成不饱和的复合氧化物。工业管式炉的真空度为10pa,温度880℃。高温分解时间5小时,碳酸锂分解成氧化锂的分解率99.3%,锂收率达到99.4%。2)分别将步骤1)中得到的氧化锂和阻熔剂形成的不饱和复合氧化物与硅铁、caf2分别粉碎球磨至粒度60um,按照质量比83:15:2配料混合,在35mpa压制成28g/个的球团。3)将步骤2)中的球团装入φ330mm*3300mm的工业耐热钢管式炉内,控制炉内真空度3pa,温度1200℃,此时还原产物为气态,并携带有固体物料,锂的还原率99.1%。4)将携带有固体物料的气体通过控温装置除尘室中的离心分离器,接着通过第一冷凝室,第一冷凝室带有夹层,用气流速度为1.5m/sec的气体,控制离心分离器与第一冷凝室温度在780℃。携带大于20um的98%的固体颗粒气体通过第一冷凝室时被除去,通过0.5um的微米陶瓷过滤器时>99.95的携带尘被净化,出口温度控制在690℃。5)被净化后纯的金属气体通过急冷装置的第二冷凝室,在第二冷凝室的双层套管式冷却器内,内层温度控制在70℃,外层用-110℃的低温冷却液体与金属气体进行热交换,冷却器中心通过2.9m/sec的气体带走传热到内壁的热量,冷却面积为0.60dm3/kg,可迅速使金属气体冷凝为金属凝聚相。6)将凝聚相的金属锂在井式炉内,在ar气保护下并进行搅拌,使熔剂熔炼精炼,得到纯度为99%的锂金属粗锭。7)将粗锂金属进行蒸馏分离,控制蒸馏器下部温度为580℃,中部温度控制在480℃,上部温度控制在80℃,下部除去高熔点杂质fe、ni、co、si、ca等;上部除去低熔点金属杂质k、na等,中部排出为li金属铸锭。将经蒸馏后铸锭得到的商品进行化学成分检测(icp测试),所得到锂锭的化学成分检测结果见下表。liknacafesial99.9910.00050.00080.00050.00050.00040.0004nicumgcl-npb0.00040.00050.00050.00090.00310.0005实施例3:1)按比例称取原料,其中碳酸锂的粒度为76um,氧化钙的粒度为66um,将碳酸锂、cao和催化剂sb2o3按摩尔比1:1.6:0.4的比例混合,并在40mpa的压力条件下制团;团块28克/个,团形状为杏核状。将制作好的球团放在φ330mm*3300mm带有气相沉积氮碳化合物坩埚的工业管式炉中进行热分解,催化剂升华冷凝后可再利用,氧化锂与阻熔剂生成不饱和的复合氧化物。工业管式炉的真空度为10pa,温度880℃。高温分解时间5小时,碳酸锂分解成氧化锂的分解率99.3%,锂收率达到99.3%。2)分别将步骤1)中得到的氧化锂和阻熔剂形成的不饱和复合氧化物与硅铁、caf2分别粉碎球磨至粒度60um,按照质量比82:16:2配料混合,在42mpa压制成32g/个的球团。3)将步骤2)中的球团装入φ330mm*3300mm的工业耐热钢管式炉内进行真空还原;控制炉内真空度3pa,温度1200℃,此时还原产物为气态,并携带有固体物料,锂的还原率为99.1%。4)将携带有固体物料的气体通过控温装置中除尘室内的离心过滤器,接着通过第一冷凝室,第一冷凝室带有夹层,用气流速度为1.5m/sec的气体,控制离心分离器与第一冷凝室温度在760℃。携带大于20um的98%的固体颗粒气体通过第一冷凝室时被除去,通过0.5um的微米陶瓷过滤器时>99.95的携带尘被净化,出口温度控制在680℃。5)被净化后纯的金属气体通过急冷装置的第二冷凝室,在第二冷凝室的双层套管式冷却器内层温度控制在65℃,外层用-105℃的低温冷却液体与金属气体进行热交换,冷却器中心通过2.9m/sec的气体带走传热到内壁的热量,冷却面积为0.60dm3/kg,可迅速使金属气体冷凝为金属凝聚相。6)将凝聚相的金属锂在井式炉内,并在ar气保护和搅拌的条件下进行熔剂熔炼-精炼,得到纯度为99%的锂金属粗锭。7)将粗锂金属进行蒸馏分离,控制蒸馏器下部温度为560℃,中部温度控制在460℃,上部温度控制在70℃,下部除尘高熔点杂质fe、ni、co、si、ca等;上部除去低熔点金属杂质k、na等,中部排出为li金属铸锭。将经蒸馏后铸锭得到的商品进行化学成分检测(icp测试),所得到锂锭的化学成分检测结果见下表。liknacafesial99.9550.00050.0090.0080.0020.0040.0005nicumgcl-npb0.00090.00050.00490.00480.0090.0009实施例4:物料碳酸锂的粒度为89um,氧化钙的粒度为74um,将碳酸锂、氧化钙与三氧化二锑按摩尔比为1∶1.6∶0.4的比例混合后制团;制团压力为35mpa,团块28克/个,团形状为椭圆形。将制团后的物质放入φ330mm*3300mm带有气相沉积氮碳化合物坩埚的工业管式炉中进行热分解,热分解温度860℃,真空度10pa,高温分解时间5小时,热分解率99.2%。其余制备步骤同实施例1,经检测,经精炼后铸锭得到的商品中,锂纯度为99.99%。实施例5:物料碳酸锂粒度74um,氧化钙61um,将氧化锂、氧化钙和氧化铋按摩尔比=1∶1.8∶0.2混合,在制团压力为45mpa的条件下制备成椭圆形团块,团块35克/个。将制团后的物质放入φ330mm*3300mm带有气相沉积氮碳化合物坩埚的工业管式炉中进行热分解,热分解温度880℃,真空度10pa,高温分解时间5小时,热分解率99.5%。其余制备步骤同实施例1,经检测,经精炼后铸锭得到的商品中,锂纯度为99.991%。对比例1:1)将工业级硝酸锂,在无压团情况下焙烧,在温度在680℃,时间为7小时,形成稳定的li2o.2cao,硝酸锂分解成氧化锂分解率为98.1%,锂收率达到90.1%。2)分别将步骤1)中得到的氧化锂和阻熔剂形成的不饱和复合氧化物与硅铁、caf2分别粉碎球磨至粒度60um,按照质量比80:18:2配料混合,在35mpa压制成28g/个的球团。3)将步骤2)中的球团装入φ330mm*3300mm的工业耐热钢管式炉内进行真空还原,真空度3pa,温度1200℃,此时还原产物为气态,并携带有固体物料锂的还原率98.8%。4)将携带有固体物料的气体通过可控温装置除尘室中的离心过滤器,接着通过第一冷凝室,第一冷凝室带有夹层,用气流速度为1.5m/sec的气体,控制离心分离器与第一冷凝室温度在720℃。携带大于20um的98%的固体颗粒气体通过第一冷凝室时被除去,通过0.5um的微米陶瓷过滤器时>99.95的携带尘被净化,出口温度控制在660℃。5)被净化后纯的金属气体通过急冷装置的第二冷凝室,在第二冷凝室的双层套管式冷却器内层温度控制在550℃,外层用-105℃的低温冷却液体与金属气体进行热交换,冷却器中心通过3m/sec的气体带走传热到内壁的热量,冷却面积为0.68dm3/kg,可迅速使金属气体冷凝为金属凝聚相。6)将凝聚相的金属锂在井式炉内在ar气保护并搅拌下进行熔剂熔炼精炼,得到纯度为99%的锂金属粗锭。7)将粗锂金属进行蒸馏分离,控制蒸馏器下部温度为530℃,中部温度控制在430℃,上部温度控制在60℃,下部除去高熔点杂质fe、ni、co、si、ca等;上部除去低熔点金属杂质k、na等,中部排出为li金属铸锭。将经蒸馏后铸锭得到的商品进行化学成分检测(icp测试),所得到锂锭的化学成分检测结果见下表。由于硝酸锂在热分解时间比碳酸锂长,分解过程会产生氮氧化物气体,氮氧化物气体在环保过程中比较难处理,使整个工艺复杂化。直接进行的热分解造成锂收率偏低,能耗比较高。相比于碳酸锂金属锂产能低,使工艺复杂,收率低,造成生产成本增加。对比例2:1)将工业级硫酸锂,在无压团的情况下温度在920℃,时间为8小时,形成稳定的li2o.1.75cao硫酸锂分解成氧化锂分解率为94.8%,锂收率达到95.6%。2)分别将步骤1)中得到的氧化锂和阻熔剂形成的不饱和复合氧化物与硅铁、caf2分别粉碎球磨至粒度60um,按照质量比82:16:2配料混合,在40mpa压制成30g/个的球团。3)将步骤2)中的球团装入φ330mm*3300mm的工业耐热钢管式炉内,真空度3pa,温度1200℃,此时还原产物为气态,并携带有固体物料锂的还原率98.9%。4)将携带有固体物料的气体通过除尘室中的离心过滤器与第一冷凝室,第一冷凝室带有夹层,用气流速度为1.5m/sec的气体,控制离心分离器与第一冷凝室温度在740℃。携带大于20um的98%的固体颗粒气体通过第一冷凝室时被除去,通过0.5um的微米陶瓷过滤器时>99.95的携带尘被净化,出口温度控制在670℃5)纯的金属气体通过急冷装置的第二冷凝室,在第二冷凝室的双层套管式冷却器内层温度控制在65℃,外层用-105℃的低温冷却液体与金属气体进行热交换,冷却器中心通过3m/sec的气体带走传热到内壁的热量,冷却面积为0.63dm3/kg,可迅速使金属气体冷凝为金属凝聚相。6)将凝聚相的金属锂在井式炉内在ar气保护并搅拌下进行熔剂熔炼精炼,得到纯度为99%的锂金属粗锭。7)将粗锂金属进行蒸馏分离,控制蒸馏器下部温度为560℃,中部温度控制在440℃,上部温度控制在75℃,下部除去高熔点杂质fe、ni、co、si、ca等;上部除去低熔点金属杂质k、na等,中部排出为li金属铸锭。将经蒸馏后铸锭得到的商品进行化学成分检测(icp测试),所得到锂锭的化学成分检测结果见下表。liknacafesial99.9910.00040.00090.00050.00050.00050.0005nicumgcl-npb0.00050.00050.00050.00090.00280.0005由于硫酸锂分解相比碳酸锂困难,不能完全被分解,直接进行的热分解造成锂收率偏低,能耗比较高时间长,还原率低,金属产能低,工艺复杂,收率低,生产成本增加。通过多次验证,采用本方法制备得到的锂金属中的杂质含量均优于gb/t4369-2015,li-1、li-2标准。实验1:采用实施例1相同的方法和步骤进行实验,测定控温装置第一冷凝室内温度、第一冷凝室出口和第二冷凝室内温度不同对最后制备得到凝聚态锂的形态的影响。具体结果如下:第一冷凝室(℃)第一冷凝室出口(℃)第二冷凝室(℃)形态试验效果85075090蓬松状凝聚态金属一般75068070凝聚态金属、易收集良65060040凝聚态金属、不好收集不好通过试验可知,当第一冷凝室温度在750℃,第二冷凝室温度在70℃时形成的镁锂合金的凝聚态金属最好、易收集。而第一冷凝室和第二冷凝室的温度越高会使形成的镁锂合金蓬松且形态一般。第一冷凝室和第二冷凝室的温度太低会使形成的凝聚态金属不好收集,形不成一个团块。实验2:采用实施例1相同的方法和步骤进行实验,测定不同的还原温度,不同的还原时间,不同的还原真空度对锂还原率的影响,如下表所示:还原温度(℃)还原时间(min)还原真空度(pa)li还原率(%)1000600361.11050600271.81100600481.61150600391.51200600299.3从表中可以看出,当温度在1200℃时,还原时间为10小时,锂的还原率较好。对所公开的实施例的上述说明,使本领域专业技术人员能够实现或使用本发明。对这些实施例的多种修改对本领域的专业技术人员来说将是显而易见的,本文中所定义的一般原理可以在不脱离本发明的精神或范围的情况下,在其它实施例中实现。因此,本发明将不会被限制于本文所示的这些实施例,而是要符合与本文所公开的原理和新颖特点相一致的最宽的范围。当前第1页12