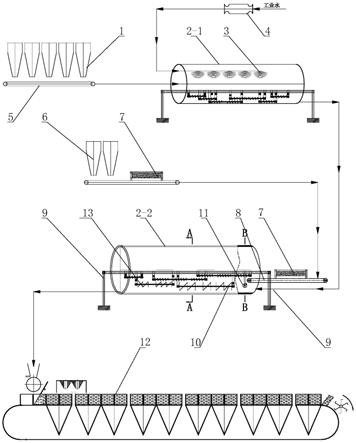
1.本发明属于冶金节能环保领域,涉及到烧结原料配料混合造粒单元的生产系统,具体的说是一种基于差动螺旋协同混合及粘料自清理的烧结混合料磁化水造粒系统。
背景技术:2.烧结过程开始于烧结混合料料层的表面点火,自上而下进行混合料层的烧结。由于烧结料层具有蓄热功能,最理想的布料应使混合料沿料层高度产生垂直偏析,即粒度由上往下逐渐变粗,含碳量由上往下逐渐变少。可是,现有的烧结原料的混合造粒难以满足如此理想的燃料偏析要求。
3.现有的烧结混合造粒工艺中,烧结混合料(包括固体燃料)在一次混合、二次混合,甚至三次混合设备内,经过加水、混匀、制粒造球等过程,到达烧结机时,固体燃料基本上以三种方式存在:一是成为小球的核心,被铁矿粉或熔剂包裹;二是比较牢固地粘结在小球或大颗粒混合料的表面;三是以自由状态存在,并混在相应粒级的混合料中。
4.如此燃料分布的烧结混合料料球进入烧结机布料时,在现有的工艺设备、布料方式及重力作用下,较大粒径的混合料球总是有更多的机会分布到台车底部,较小粒径的混合料球分布烧结混合料层上部,最终效果是大量燃料在布料时明显往下层偏析,形成与理论烧结过程所要求的燃料偏析相反的燃料分布,即下层热量过剩,上层热量不足,造成整个烧结过程热量梯度分布不合理,导致烧结过程存在如下弊端:
5.①
在台车运行过程中,离开点火器的初始阶段,因烧结料层上部燃烧带中的燃料含量少,燃烧带温度低,也使此处高温区对气流通过时产生的阻力增加不大,因而料层的透气性很好,气流流速大,使料层快速冷却,甚至将燃烧带的烧结混合料冷却到燃料的着火温度以下。
6.②
随着台车运行,燃烧带也逐渐下移到中、下层。因中、下层的燃料含量逐渐增多,料层的自动蓄热作用加强,燃烧带温度也随之升高,使气体阻力有所加大,透气性明显下降,燃烧带产生的热量因透气性下降向外传导的速率下降,料层还原性气氛增强,不利于磁铁矿的氧化,甚至使赤铁矿还原,出现焙烧过熔而形成大孔薄壁结构、feo含量高等一系列问题,致使产品质量不符合高炉冶炼要求。
7.③
因混合料料层的燃料分布与理论烧结过程所要求的燃料偏析相反,将造成烧结过程的其它方面如气流分布、过湿层变化等一系列的极端不均匀。
8.为了分析现有混合造粒工艺形成的燃料偏析对烧结矿质量的影响,代汝昌等【代汝昌,袁培燕,孙艳红,等.烧结生产节能潜力解析.山东冶金,2012,34(4):51-53】对烧结后的料层截面进行的分析研究,在600mm厚的料层中,上部(及表面)大约150mm厚的料层非常疏松,即使表面看上去结块状态较好,而且具有明显的液相粘结,但其强度仍很低,不足以形成符合高炉要求的成品烧结矿;而在下层(靠近篦条)大约100mm厚的料层中,冷却后颜色为深黑色,颗粒之间具有较多的像“雾凇”一样的液相生成,欲滴未滴,但彼此之间并未形成
块状矿,而只是象没有煮好的“夹生”米饭一样,矿粉颗粒清晰可见。此区域也有终点提前形成密实块状烧结矿的时候,但都呈致密而少孔状态。只有大约350mm的中间层,形成外观良好的烧结矿,具有明显的金属光泽与微孔,破碎后解理面清晰,使颗粒之间形成一体化(完整而带有一定孔隙度)的块矿。也就是说现有的烧结混合料造粒工艺生产的烧结矿成品率低,返矿量大,烧结过程的无效能耗高。
9.另外,烧结混合料在圆筒混合机内混合造粒过程中,在圆筒内壁会产生大量的粘结料,随粘结层厚度的增加,筒体有效容积减小,筒内环境恶化,直接影响混匀制粒效果和设备使用寿命,严重时不仅发生停机事故,甚至在清理时造成人员伤亡。
10.唐钢烧结厂圆筒混合机因筒体粘料多次发生筒体托辊轴承烧坏、断轴等事故。筒体粘料过多,增加了传动与支承部位的负荷。当筒体内粘料厚度达100mm时,混合机的负荷将增加26.7%;当粘料厚度达250mm时,混合机的负荷将增加64%。长期的筒体粘料给混合机的传动系统及支承托辊带来了额外的负担【栾景林.减轻混合机筒体粘料的探讨.烧结球团,1997,22(1):61-63】。
11.为了解决筒体粘料问题,各钢铁厂和科研机构均进行了大量的研究,并提出了一系列的防治处理办法,包括优化加水方式、优化配料结构及圆筒混合机工艺参数、优化衬板及圆筒内部结构、改变落料高度、增加刮料吹扫装置和加设清料装置等。莱钢在混合机筒体内设置刮料吹扫装置实施强行刮料。为了保证刮料吹扫装置不被与转动的筒体产生的较大作用力而损毁,对刮料吹扫装置实施混合机筒体外强化固定。该改造尽管发挥了刮料的效果,但刮料装置磨损快、噪声大【张惠,熊伟,王珂,等.烧结生产混合机粘料的原因分析与改进措施.设备管理与维修,2010,(3):41-42】。
12.济钢为了解决一次圆筒混合机的粘料问题将圆筒混合机内的尼龙衬板更换为柔性陶瓷衬板,缓解了混合机粘料量、设备运行稳定,制粒效果得以保证【阳习端,石玥,潘建,等.涟钢四烧圆筒混合机衬板性能研究,烧结球团.2019,44(05):29-31+56】。
13.河北钢铁集团烧结厂采用了一种形似狼牙棒的φ0.4m
×
3m转动辊筒,在辊筒表面呈螺旋线焊接4排长0.2m的棒针,选择特定的位置和与筒壁的距离,利用专用吊挂装置悬于圆筒混合机中,利用料层产生的阻力作为旋转动力进行清料,具有一定的清理效果【李鹏.抑制圆筒混合机粘料的措施.河北冶金,2015,(1):55-57】。
14.长治钢铁(集团)烧结厂通过降低出料端挡料环高度、变更混合机加水位置等措施减轻筒体粘料现象【史郑斌,赵建芳,梁栋.解决二次混合机衬板粘料问题.山西冶金,2003.(4):54】。龙钢公司烧结厂通过降低落料高度、采用较低吸水率的高分子尼龙衬板替换含油尼龙衬板等方案较大改善了混合机的粘料情况【彭元飞,王亮.减少混合机粘料的探索与实践.2015年第三届炼铁对标、节能降本及相关技术研讨会论文集河北省冶金学会会议论文集】。
15.如上所述的减缓粘料,或强制刮料等方案并不能完全解决圆筒混合机内壁粘料引起的混合机不能长期稳定运行的问题,特别是安装的强制刮料装置,由于刮料的反作用力,必然会引起混合机转动的平稳性,产生振动。同时刮料装置磨损快,寿命短,甚至装置脱落,进入其他设备系统,影响其他设备的运行安全。
16.水是烧结混合料在圆筒混合机内造粒成球过程必不可少的原料之一。烧结混合料只有在达到一定的含水量时,才能生成生产所需的成球率,满足烧结料层的透气性要求。但
是水分对烧结过程也会产生一些不利的影响【陈铁军主编.现代烧结造块理论与工艺.2018:42】,如形成过湿层,冷凝水充塞粒子间间隙,增大料层阻力。水分过量,加之燃料上层少、下层多的不合偏析,会引起过湿层在短时间内迅速下移,会在焙烧的开始阶段集中释放,带来诸如糊箅条、破坏混合料中的小球等一系列坏的作用。更不利的是烧结混合料中,水分的增加会增加额外的烧结工序能耗。炉料游离水的蒸发热总吸热达2595.96kj/kg-水【炼铁学,梁中渝,冶金工业出版社,2019,p215】,还不包括烧结后烟气温度超100℃以上部分的吸热。
17.在加水方式方面,若局部加水过量,烧结原料中小于0.5~1mm的矿粉易泥化,影响造粒效果,粘结混合机内壁。陕钢通过优化混合料加水方式,在混合料中采用分段加水方式,混合机加水占总水量的70%,制粒机加水占总水量的30%【韦胜利.陕钢汉钢超厚料层均质烧结技术工业实践.山西冶金,2020,(3):116-118,+125】。
18.总之,现有的烧结原料混合造粒单元生成的混合料球进入烧结机布料烧结时存在以下的不足:
19.(1)烧结料层下层热量过剩,上层热量不足,造成整个烧结过程热量梯度分布不合理。在烧结混合料布料时,较小粒径的混合料球分布烧结混合料层上部,较大粒径的混合料球更多的分布到台车底部,最终效果是大量燃料在布料时明显往下层偏析,形成与理论烧结过程所要求的燃料偏析相反的燃料分布。
20.(2)圆筒混合机内壁粘料导致圆筒混合机的生产能力下降,混合造粒工艺系统运行的稳定性差。圆筒混合机进行烧结原料的混合造粒时,由于受烧结原料性质的制约,无法杜绝圆筒混合机内壁的粘料,筒体内壁粘料在运行过程中无法实时清理,造成设备使用寿命降低,还直接影响烧结混合料的混匀制粒效果。
21.(3)烧结原料混合造粒的用水量过高。烧结原料混合造粒过程中加水的目的是润湿物料,使物料颗粒表面被吸附水和薄膜水所覆盖,同时在颗粒与颗粒之间形成u型环,在水的表面张力作用下,使物料颗粒集结成团粒。烧结混合料中最适宜的水分含量是使混合料达到最高成球率。而物料的润湿与否不仅与加入的水量有关,还与物料的与水之间的润湿角有关,当物料一定时,则与水的性质有关,表面张力大的水难润湿物料。由于现有烧结原料混合造粒单元中加入的常规工业水,未对其进行相关处理降低其表面张力,导致用水量过高。
技术实现要素:22.本发明的目的是为了解决上述技术问题,提供一种系统简单、节能降耗、易于改造、运行成本低、烧结过程热量梯度分布合理、燃尽度高、设备使用寿命长、对环境友好的基于差动螺旋协同混合及粘料自清理的烧结混合料磁化水造粒系统。
23.本发明一种基于差动螺旋协同混合及粘料自清理的烧结混合料磁化水造粒系统,包括经原料输送皮带机依次连接的烧结原料仓、一次混合机、二次混合和烧结机,其中所述一次混合机内的喷头经管道与工业水磁化器连接;
24.还包括固体燃料仓,所述固体燃料仓经燃料输送皮带机与二次混合机连接。
25.在一次混合机进料口筒体长度10-20%区域及出料口筒体长度10-20%区域不设喷水段;在落料点下游距落料点距离为筒体长度10-20%位置开始依次设置至少3个喷水
段。
26.在落料点下游距落料点距离为筒体长度10-20%位置开始依次设置3个喷水段,从进料端到出料端,各喷水段的喷水量占总喷水量的比例依次为40-50%,30-40%,20-30%,合计100%。
27.所述固体燃料仓经燃料输送皮带机与二次混合机的进料端连接,所述燃料输送皮带机上设有电子发生器;所述二次混合机的进料端设有布料器,所述布料器位于所述燃料输送皮带机出料端的下方。
28.所述一次混合机和二次混合机中均设有差动螺旋机构。
29.所述差动螺旋机构由安装在支架上的多组螺旋组件组成,所述螺旋组件包含螺旋心轴和设置在螺旋心轴上的非连续的螺旋叶片;所述螺旋心轴的轴线与筒体轴线平行,螺旋心轴的两端通过轴承、轴承座及固定架安装在所述支架上。
30.多组所述螺旋组件成扇骨状沿筒体径向分布在筒体下部0.75-0.8π弧度范围内,并沿所述筒体轴线方向错开布置。
31.所述固定架上设有调距器。
32.在所述筒体落料点位置的圆筒段且远离筒体径向垂直方向中心轴位置至少设有一组螺旋组件;所述落料点下游的筒体径向垂直方向中心轴位置上设有至少两组螺旋组件,且落料点位置的圆筒段的螺旋组件与落料点下游的筒体径向垂直方向中心轴位置第一组螺旋组件的螺旋叶片旋向相同,且保证螺旋叶片被物料带动自转,推动物料向出料端方向运动;所述落料点下游筒体径向垂直方向中心轴位置的第一组螺旋组件与其它组螺旋组件旋向相反。所述布料器由连接传动机构的传动轴、套装在所述传动轴上的纺锤型的布料绝缘辊、位于布料绝缘辊两侧的绝缘挡煤板组成。
33.针对背景技术中存在的问题,发明人进行了如下改进:
34.(1)在二次混合(混合次数高于二次时,则在最后一次混合)时才加入全部固体烧结燃料,并且这部分燃料在混入混合料前经电子发生器负载负电荷,再通过布料绝缘辊转动冲击分散到混合料中。这是考虑煤粉或焦粉是优良的导电体,皮带相当于绝缘的容器,皮带上的煤粉或焦粉与外界电绝缘。
35.在皮带上方设置电子发生器,产生的电子喷射到煤粉或焦粉上,使煤粉或焦粉负载上一定电量的负电荷。负载上一定电量的负电荷的煤粉或焦粉从皮带抛撒到悬空状态时,带电的煤粉或焦粉颗粒会因排斥力相互分开。
36.带电的煤粉或焦粉颗粒落到煤粉布料器的布料绝缘辊,在布料绝缘辊的转动冲击下,颗粒进一步分开成较小粒径的颗粒。由于这些较小粒径的颗粒同样带有负电,颗粒之间也会因排斥力相互分开。
37.带电的煤粉或焦粉颗粒最终以较高的分散度落到混合机内的混合料上,并在混合机提供的机械力作用下,粘附到混合料球的表面。
38.由于是在最后一次混合造粒单元加入固体燃料,燃料被分散抛撒到混合机内料球表面,在混合机的转动下,引起料球的滚动和搓动,大部分的固体燃料将粘附到料球表面,小部分的固体燃料将与混合料中的细颗粒混在一起,进一步生成较大粒径的料球。如此混合,固体燃料只有极少部分被烧结混合料包裹在料球里面,由此形成烧结混合料料球表层固体燃料包裹的燃料偏析布局。则混合料中,料球粒径越小,单位体积物料占有燃料量越
多。
39.如此固体燃料分布的混合料在烧结机上进行常规的偏析布料时,布到下层的(较大粒径的料球)固体燃料量明显减少,而布到中、上层的固体燃料量则相应增加,在满足相同烧结所需热量的条件下,不但可以大量减少固体燃料配比,而且可以更好地与烧结过程理论上要求的燃料偏析接近,使烧结过程中,烧结料层的热量分布更趋合理。
40.烧结混合料点火烧结后,由于上层物料单位体积物料的燃料量较大,同时大部分燃料裸露在料球外表,燃烧过程的氧气进入燃烧面的扩散阻力小,燃烧速率快;另一方面,由于烧结料层中料球堆积,燃料较集中在料球接触界面,所以燃烧过程燃料充分,燃烧温度高,不易被抽入的助燃空气冷却到燃料着火点温度以下,也就是不易熄火,燃料燃尽度高。更重要的是,由于燃烧温度高,烟气体积流量大,烟气穿过料层时的阻力大,减少了抽风量,从而减慢了上层混合料中的热量向下层传递的速度,延长了上层混合料的保温时间,提高了烧结矿的品质。
41.(2)引入工业磁化水对烧结混合料进行润湿造料,同时在加水方式、加水区域方面进行分批分区域喷水。
42.引入磁化水具有如下技术效果:
43.①
降低了混合料颗粒间浆体的zeta电位,提高了颗粒间的凝结或凝聚效果,有利于成球。zeta电位的大小反映了浆体分散系的稳定性,分散粒子越小,zeta电位绝对值越高,体系越稳定。反之,zeta电位绝对值越低,越倾向于凝结或凝聚,即吸引力超过了排斥,分散体系被破坏,进而发生凝结或凝聚。
44.烧结混合料在初步喷水润湿混合后,润湿的颗粒与颗粒之间形成u型环,并在水的表面张力作用下,使物料颗粒集结成团粒,此时颗粒之间大部分空隙还是充满空气。在混合机的回转产生的机械力作用下,颗粒与颗粒之间的接触越来越靠近,空气被挤出。由于磁化水降低了混合料颗粒间浆体的zeta电位,更有利于颗粒的凝聚。
45.②
减少用水量,降低烧结工序能耗。物料在混合机内加水润湿后,物料颗粒表面被吸附水和薄膜水所覆盖。由于磁化的表面张力小,单位表面积的薄膜水量会减少,也就是说,在分级、分区域喷水的前提下,同样的水量将覆盖更大的混合料颗粒表面,从而减少烧结原料混合的用水量,有利于降低烧结工序能耗。
46.③
节省混合时间,提高混合效果和混合料产量。烧结原料的混合造粒过程就是要得到一定强度和一定粒度的混合料,也就是要使喷水初期形成的小颗粒物料团聚长大成需要粒径的小球。球粒的形成与物料的亲水性、水在物料表面的迁移速度、物料的粒度组成以及机械力作用的大小等因素有关。采用磁化水,水中的大分子团被打散成更多的水分子或小水分子团,水分子的增多使得颗粒被更均匀的分散,表面张力小,增加了对颗粒的润湿性能,使得初期混合料水化更加充分,强化了混合料中的物料水化过程,缩短了水化时间,初期水化形成的小颗粒之间间隙小,在混合机提供的机械力作用下,小颗粒更容易团聚逐渐长成具有一定强度和一定粒度组成的混合料。实验研究表明,磁化水对sio2、fe2o3的接触角大小都有所改善,改善效果在7~28%之间,对fe2o3润湿性的改善效果最明显。
47.混合料造粒成球所需的所有水量全部在一次混合机中加入,并采用分级、分区域喷水。如此注水方式具有如下技术效果:
48.①
有利于以初期润湿的物料为母球,提高造球效果。烧结物料混合成球的关键是
加水润湿形成母球。当物料润湿到最大分子结合水后,成球过程才明显开始。当物料润湿到毛细阶段时,成球过程才得到应有的发展。当已润湿的物料在制粒机中受到滚动和搓动后,借毛细力的作用,颗粒被拉到水滴的中心形成母球。母球就是毛细水含量较高的集合体。母球长大的条件是:母球表面水分含量接近于适宜的毛细水含量;
49.②
有利于物料的均匀混合。磁化水的表面张力小,与物料的接触角小,易于润湿物料,一次性加水时,会导致局部物料含水率高,不利于物料的分散。母球在制粒机内继续滚动,被进一步压紧,引起毛细管状和尺寸的改变,从而使过剩的毛细水被挤压到母球表面上来。过湿的母球表面在运动中很容易粘附上润湿程度较低的颗粒。此过程多次重复,一直到母球中间颗粒间的摩擦力比滚动成型的机械压密作用力大时为止。当局部物料含水率高时,由于磁化水的润湿性好,会形成较大粒径、含水量较高的生球,物料分散均匀性降低,同时还降低了母球的生成量;
50.③
分级、分区域喷水来控制加水速度,可有效提高生球的质量。在混合机产生的滚动和搓动机械力作用下,生球内的颗粒发生选择性的接触面积最大排列,生球内颗粒进一步压紧,各颗粒的薄膜水层将相互接触,形成一个若干颗粒所共有的薄膜水层。其中,各颗粒靠着分子黏结力、毛细黏结力和内摩擦阻力的作用相互结合起来。生球内毛细水含量排除越彻底,生球的质量越高。由于磁化水的润湿性能好,当局部物料含水量较高时,物料会被完全润湿。在后期混合机提供的滚动和搓动机械力作用下,颗粒内部挤压出的水分不仅仅是毛细水,还包含有物料润湿过量的自由水。通过分级、分区域喷水,避免局部物料过湿,提高了生球内水分的排出;
51.④
有效控制局部物料含水率高形成浆液,缓解混合料在混合机内壁上的粘结。
52.(3)在一次混合机和二次混合机中均设置差动螺旋机构,具有以下技术效果:
53.①
强化混合料的混合效果,实现料球粒径分布的智能控制。改变了混合料的运行轨迹,通过螺旋作用使混合料的运行轨迹复杂多变,增加了混合效果;通过设置在固定架上的调距器和压力及扭转力矩传感器,根据扭转力矩值周期性的调整位于筒体径向垂直方向中心轴位置的多根螺旋与混合机筒体内壁之间形成不同的间距值,螺旋叶片在圆筒混合机转动时,受到圆筒内的积料或内壁粘料的推动作用,形成不同的自转速度,控制差动螺旋机构对物料的扰动效果,使圆筒混合机出料达到需求的物料料球粒径分布。
54.②
提高了混合料中大球比例。螺旋转动对混合料的推进与同时在混合机转动带动混合料总体流动,且通过对不同螺旋组件中螺旋叶片旋向的控制,使物料落入落料区后总体朝向出料端推进,但同时利用靠近出料端的螺旋组件对延长物料的推进速度,提高物料在筒体内的停留时间,从而有利于较大粒径混合料的滚动,同进对小粒径混合料具有拦截、滞留效果,延长了小粒径混合料在混合机内的停留时间,有利于小粒径混合料的长大。
55.③
解决了圆筒混合机内壁粘料清理难题。圆筒混合机粘料现象普遍存在且较为严重,影响了混合制粒效果,造成混合料粒度较差,严重时由于呛料过多造成事故停机,大多数企业仍采用传统的定期停机人工清料的方式,不仅劳动强度大,粉尘浓度高,作业环境恶劣,还容易出现砸伤事故。为此,国内外企业曾尝试多种形式的清料装置和防止粘料措施,但由于圆筒内部环境恶劣,潮湿、粘结层硬、混合料易对清料装置造成磨损、筒壁上粘附的大块掉下后易砸坏清料装置等问题,故一直未能找到好的解决办法。混合机筒内安装差动螺旋机构后,利用调距装置调整间距,通过对间距的优化,筒内粘料越多,越有利于螺旋的
转动,清料效果越好。同时将多根螺旋沿混合机筒体中心轴线方向错开布置,覆盖混合机圆筒内壁中部区域及进料区域,实现筒内壁清料无死角。
56.④
降低圆筒混合机制造成本,内壁可不设置内衬。利用物料的粘结性能,在筒体内壁形成一层固定的粘结层,作为筒体的内衬,调整螺旋叶片与筒体内壁的间距,保持粘结料层的厚度,形成一层固定厚度的粘结层,保护筒体内壁,减少对筒体内壁磨损,还可有效节省投资和运行成本。
57.有益效果:
58.1)降低烧结混合料含水率。采用磁化水进行烧结原料的混合造粒,由于磁化水的表面张力小,形成浆液的zeta电位低,有利于原料的润湿及颗粒的凝聚,减少了烧结原料混合造粒所需的水量,节省水量5-8%。配合控制分级、分段喷水进一步提高生球质量、减少用水量、改善粘结。
59.2)通过改变固体燃料的添加时机,并利用电子发生器负载上负电荷,从而大大提高了混合料中固体燃料的均匀分散度,改善了烧结过程的燃烧效果,提高了燃料的燃尽度,可有效降低烧结烟气中的co浓度。
60.3)增加了混合料中大球比例,改善了烧结料层的透气性。采用差动螺旋机构迟滞了烧结原料的混合过程,特别是对小颗粒混合料的迟滞作用的选择性,增加了小颗粒混合料的成球时间,增加了较粒径混合料的比例,3-8mm粒径混合料比例达65%以上,提高了烧结料层的透气性;彻底解决了圆筒混合机内壁的物料粘结难题。通过调节差动螺旋机构中螺旋与混合机内壁的间隙,通过螺旋与混合机圆筒的差动,对内壁粘结物进行清理并强化物料的混合。
61.4)优化了烧结过程中的热量梯度利用。所有固体燃料在最后一步的混合机中加入,燃料只是与混合料颗粒进行简单地混匀,未参与烧结原料的造球制粒,燃料在混合料中的赋存形式主要有两种:一是细颗粒粘附在已经造好的小球表面;二是以自由状态按粒度大小与混合料中相应粒级的矿粉颗粒混在一起。布料过程中燃料在料层高度方向上分布到下层的燃料量明显减少,分布到中、上层的燃料量明显增加,这与烧结过程的机理(如自动蓄热作用等)更吻合,使上下料层的热量分布更符合工艺要求,优化了烧结过程中的热量梯度。
62.5)强化混合料的混合效果,实现料球粒径分布的智能控制。改变了混合料的运行轨迹,通过螺旋作用使混合料的运行轨迹复杂多变,增加了混合效果;通过设置在螺旋固定架上的调距器和压力及扭转力矩传感器,根据扭转力矩值周期性的调整位于筒体径向垂直方向中心轴位置的多根螺旋与混合机筒体内壁之间形成不同的间距值,螺旋叶片在圆筒混合机转动时,受到圆筒内的积料或内壁粘料的推动作用,形成不同的自转速度,控制差动螺旋机构对物料的扰动效果,使圆筒混合机出料达到需求的物料料球粒径分布。
63.6)降低了烧结工序能耗。采用磁化水、燃料最后配加、差动螺旋机构的强力混合等技术措施,降低了混合料中的含水量,增加了大球比例,从配料上保证了烧结料层上的燃料按烧结过程机理进行偏析,从而降低了整个烧结工序能耗,与传统的烧结原料混合造球工艺相比,节省能耗5-10kgce/t-烧结矿。
附图说明
64.图1为本发明系统图。
65.图2为螺旋差动机构的安装示意图;
66.图3为图1的a-a剖视图。
67.图4为图1的b-b剖视图。
68.其中,1-烧结原料仓;2-1:一次混合机;2-2:二次混合机;3-喷头;4-工业水磁化器;5-原料输送皮带机;6-固体燃料仓;7-电子发生器;8-燃料输送皮带机;9-支架;10-差动螺旋机构;11-布料器;11-1:布料绝缘辊;11-2:传动轴;11-3:绝缘挡煤板;12-烧结机;13-螺旋组件;13-1:调距器;13-2:固定架;13-3:螺旋叶片;13-4:螺旋心轴、α-垂直方向中心轴、β-落料点。
具体实施方式
69.下面结合附图对本发明系统进行进一步解释说明:
70.参见图1,本发明基于差动螺旋协同混合及粘料自清理的烧结混合料磁化水造粒系统,包括经原料输送皮带机5依次连接的烧结原料仓1、一次混合机2-1、二次混合2-2和烧结机12,其中所述一次混合机2-1的喷头3经管道与工业水磁化器4连接;还包括固体燃料仓6,所述固体燃料仓6经燃料输送皮带机8与二次混合机2-2连接。
71.在一次混合机2-1进料口筒体长度10-20%区域及出料口筒体长度10-20%区域不设喷水段;在落料点β下游距落料点β距离为筒体长度10-20%位置开始依次设置至少3个喷水段,本实施例中设置3个喷水段,磁化水经各喷水段的喷头3喷出,从进料端到出料端,各喷水段的喷水量占总喷水量的比例依次为40-50%,30-40%,20-30%,合计100%(重量百分比)。
72.所述固体燃料仓6经燃料输送皮带机8与二次混合机2-2的进料端连接,所述燃料输送皮带机8上设有电子发生器7,所述电子发生器7的具体位置可根据需要进行选择;所述二次混合机2-2的进料端设有布料器11,所述布料器11位于所述燃料输送皮带机8出料端的下方。所述一次混合机2-1和二次混合机2-1中均设有差动螺旋机构。
73.参见图1及图2,所述差动螺旋机构10由安装在支架9上的多组螺旋组件13组成,所述螺旋组件13包含螺旋心轴13-4和设置在螺旋心轴13-4上的非连续的螺旋叶片13-3;所述螺旋心轴13-4的轴线与筒体轴线平行,螺旋心轴的13-4两端通过轴承、轴承座及固定架13-2安装在所述支架9上。
74.多组所述螺旋组件13成扇骨状沿筒体径向分布在筒体下部0.75-0.8π弧度范围内,并沿所述筒体轴线方向错开布置。
75.所述固定架13-2上设有调距器13-1,可通过调距器13-1调节螺旋固定架13-2的长度,以控制螺旋心轴13-4上的螺旋叶片13-3与筒体内壁的间距,在筒体下部0.75-0.8π弧度范围内,从筒体径向垂直方向中心轴位置到筒体径向左、右两侧,所述间距越来越小;
76.其中,保证位于筒体径向垂直方向中心轴α位置的螺旋组件13的螺旋心轴13-4下方螺旋叶片30-100%埋入混合料中,无积料时,最小保持10mm以上;
77.最远离筒体径向垂直方向中心轴位置α的螺旋组件的螺旋心轴13-4下方螺旋叶片13-3与筒体内壁的间距为10-20mm。
78.周期性的调整位于筒体径向垂直方向中心轴α位置的螺旋叶片13-3与筒体内壁之间的间距,螺旋叶片13-3在混合机转动时,随着间距周期性的变化,螺旋叶片13-3受到筒体内的积料或内壁粘料的推动力依此改变,形成不同的自转速度,强化对物料的扰动。
79.在所述筒体落料点β且远离筒体径向垂直方向中心轴α位置至少设有一组螺旋组件a(本实施例中为一组);所述落料点β下游的筒体径向垂直方向中心轴a上设有至少两组螺旋组件(本实施例中为两组),且落料点β处的螺旋组件a与落料点β下游的筒体径向垂直方向中心轴α方向上的第一组螺旋组件b的螺旋叶片13-4旋向相同(以保证螺旋叶片被物料带动转动时,推动物料向出料端方向运动),与其它组螺旋组件旋向相反(即其它组螺旋组件的螺旋叶片被物料带动转动时,会推动物料向进料端方向运动)。这样,物料由筒体的进料端进入在落料点β下落后,在筒体转动的带动下先作用于螺旋组件a,螺旋叶片13-3被物料带动转动,从而推动物料向出料端方向运动,当物料被推至第一组螺旋组件b处时,同理继续向出料端方向运动,当推至靠近出料端方向的其它螺旋组件的位置时,由于其它螺旋组件的旋向相反,因此会对物料有一个反方向(即进料端方向)的作用力,既有利于较大粒径混合料的滚动,,同进对小粒径混合料具有拦截、滞留效果,延长了小粒径混合料在混合机内的停留时间,有利于小粒径混合料的长大。
80.参见图4,所述布料器11由连接传动机构的传动轴11-2、套装在所述传动轴11-2上的纺锤型的布料绝缘辊11-1、位于布料绝缘辊11-1两侧的绝缘挡煤板11-3组成。所述绝缘挡煤板11-3为直径大于布料绝缘辊11-1的纺锤中心最大直径4-6%的圆盘。
81.在一次混合机2-1和二次混合机2-2中安装差动螺旋机构10,调整螺旋机构10中的螺旋叶片13-3或螺旋心轴13-4与混合机2-1(或2-2)的同轴度,保证同轴度偏差小于0.1%。烧结混合料通过运输皮带送入混合机2-1(或2-2)内,混合料在混合机中充分混合的同时被差动螺旋机构10协同作用,强化混合效果,颗粒的粒径进一步增大,同时也解决了混合机内壁粘料清理难题,一举多得。
82.当混合机停机检修时,通过调距器13-1调整筒体径向垂直方向中心轴α位置上的螺旋组件13的螺旋叶片13-3与混合机2内壁的间距,调大第一组螺旋组件b与混合机2内壁的间距,逐渐调小第一组螺旋组件b下游方向的其他螺旋组件13与混合机2内壁的间距,甚至可调整到10mm以下,并调整混合机2的转动方向,实现混合机2内壁粘料及混合机2筒体积料的快速清理,缩短检修时间。
83.工艺过程:
84.将除固体燃料(如焦粉或煤粉)外的全部烧结原料(如矿粉和熔剂粉)加入一次混合机2-1中进行混合造粒,同时工业水经工业水磁化器4处理后形成磁化水经管道送入一次混合机2-1中的的喷头3喷出以润湿烧结原料,采用分级、分区域向一次混合机2-1内喷入磁化水,具体为:
85.在一次混合机进料口筒体长度10-20%区域及出料口筒体长度10-20%区域不加水;在落料点下游距落料点距离为筒体长度10-20%位置开始喷水,依次设置3个喷水段(磁化水通过若干个喷头3喷出)。从进料端到出料端,各喷水段的喷水量占总喷水量的比例依次为40-50%,30-40%,20-30%,合计100%;
86.出一次混合机2-1的混合料经送入二次混合机2-2中与加入的固体燃料进一步混合;来自固体燃料仓6的固体燃料在燃料输送皮带机8上通过电子发生器7负载上负电荷后
由燃料输送皮带机8卸到布料器11的布料绝缘辊11-1上,在落下的固体燃料的冲击作用下,布料器11以及布料绝缘辊11-1产生转动,转动的作用加强对固体燃料的冲击,进一步提高固体燃料的分散性。调整燃料输送皮带机8与布料器11的相对位置(参见图1),保证燃料输送皮带机8卸下的固体燃料落在布料绝缘辊11-1靠近燃料输送皮带机8方向的一侧,提高燃料对布料绝缘辊11-1冲击力,进一步提高燃料的分散效果。
87.在布料绝缘辊11-1转动冲击下,固体燃料分散抛撒到二次混合机2-2内的混合料中,在二次混合机2-2的转动混合作用下,粘附到混合料颗粒表面;出二次混合机2-2的混合料送入烧结机12进行烧结。
88.采用本发明系统减少了烧结原料混合造粒所需的水量,节省水量5-8%,相应也降低了烧结工序能耗,节省能耗5-10kgce/t-烧结矿;增加了较粒径混合料的比例,3-8mm粒径混合料比例达65%以上,提高了烧结料层的透气性,优化了烧结过程中的热量梯度。