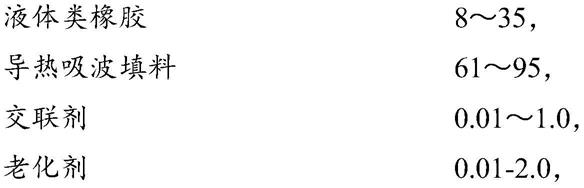
2000cs。
10.优选的,所述液体类橡胶的粘度为52cs-900cs。
11.优选的,所述导热吸波填料为石墨烯包覆铁氧体、石墨烯包覆钡铁氧体、钴铁氧体-铁钴合金共包覆空心玻璃微珠、钴铁氧体-铁钴合金共包覆碳微球、羰基铁粉、氧化铝、氮化铝、钴铁氧体-铁钴合金、二氧化硅中的一种,所述导热吸波填料的结构为球形、类球形或角型,所述导热吸波填料的粉体粒径为1~200μm。
12.优选的,所述石墨烯包覆铁氧体或石墨烯包覆钡铁氧体的石墨烯包覆层厚度为0.5~2μm。
13.优选的,所述钴铁氧体-铁钴合金共包覆空心玻璃微珠或钴铁氧体-铁钴合金共包覆碳微球的钴铁氧体-铁钴合金包覆层厚度在0.1~2μm。
14.优选的,所述交联剂为含有过氧化双(2,4-二氯苯甲酰)、二异氰酸酯、过氧化二苯甲酰、二(亚肉桂基-1,6-己二胺)硫化物或1,3,5-三巯基-2,4,6-均三嗪基团的化合物中的一种。
15.优选的,所述老化剂为胺类防老剂、酮胺类防老剂、醛胺类防老剂、气相二氧化硅防老剂或酚类防老剂中的一种。
16.第二方面,本发明还提供一种上述的导热吸波片材的制备方法,包括:
17.将所述液体类橡胶、导热吸波填料和防老剂进行搅拌,搅拌均匀后,再加入所述交联剂进行搅拌,控制温度在-5~10℃,得到所述导热复合材料混合物;
18.将所述基材浸泡于所述导热复合材料混合物中,抽真空一段时间后,逐步升温到80~120℃,保持一段时间,使所述导热复合材料混合物填充于所述基材的孔洞中,得到导热吸波片材。
19.本发明通过对导热吸波填料的种类、粒径和形貌选择,以及,基体的选择和处理可保证保证导热吸波特性的同时还可以使导热吸波片材具有良好的回弹性和可压缩性,得到的复合材料高于常规导热吸波片材,且具有较低的硬度。此外,本导热吸波片材可有效解决自动驾驶雷达密集型、体积小的场合对导热吸波片材的需求,以满足产品的散热和信号稳定的要求,还具有弹性、低残余应力、使用方便、易返修的特点。
具体实施方式
20.下面将结合本发明实施例,对本发明实施例中的技术方案进行清楚、完整地描述,显然,所描述的实施例是本发明一部分实施例,而不是全部的实施例。基于本发明中的实施例,本领域普通技术人员在没有做出创造性劳动前提下所获得的所有其他实施例,都属于本发明保护的范围。
21.应当理解,当在本说明书和所附权利要求书中使用时,术语“包括”和“包含”指示所描述特征、整体、步骤、操作、元素和/或组件的存在,但并不排除一个或多个其它特征、整体、步骤、操作、元素、组件和/或其集合的存在或添加。
22.还应当理解,在此本发明说明书中所使用的术语仅仅是出于描述特定实施例的目的而并不意在限制本发明。如在本发明说明书和所附权利要求书中所使用的那样,除非上下文清楚地指明其它情况,否则单数形式的“一”、“一个”及“该”意在包括复数形式。
23.还应当进一步理解,在本发明说明书和所附权利要求书中使用的术语“和/或”是
指相关联列出的项中的一个或多个的任何组合以及所有可能组合,并且包括这些组合。
24.本发明实施例公开一种导热吸波复合片材,包括基材和导热复合材料混合物,基材为多孔弹性泡棉,导热复合材料混合物填充于基材的孔洞中,导热复合材料混合物按重量百分比计,由以下组分组成:
[0025][0026][0027]
上述各组分的重量百分比之和为100%。
[0028]
进一步的,导热吸波片材的制备方法如下:
[0029]
(1)将液体类橡胶、导热吸波填料和防老剂进行搅拌,搅拌均匀后,再加入交联剂进行搅拌,控制温度在-5~10℃,得到导热复合材料混合物。具体可以是:将所述液体类橡胶、导热吸波填料和防老剂置于转速为30~70r/min、真空度为-0.08以下的搅拌器内搅拌15~60分钟,使各组分混合均匀,搅拌均匀后,再加入交联剂并置于动力混合机中进行搅拌,控制温度在-5~10℃,得到导热复合材料混合物;
[0030]
(2)将基材浸泡于所述导热复合材料混合物中,抽真空一段时间后,逐步升温到80~120℃,保持一段时间,使导热复合材料混合物填充于基材的孔洞中,得到导热吸波片材。具体可以是:将基材浸泡于导热复合材料混合物中,保持真空度为-0.1以下,抽真空20~40分钟后,逐步升温到80~120℃,保持3~5个小时,使导热复合材料混合物填充于基材的孔洞中,得到导热吸波片材。
[0031]
其中,多孔弹性泡棉为石墨烯类、镍碳类、镀石墨烯聚氨酯类、氮化硼纤维类,结构为通孔或粗孔,其中孔的直径为5μm-300μm;液体类橡胶为液体丙烯酸酯橡胶、液体羟基封端丁二烯橡胶、液体酸酐封端丁二烯橡胶、带有乙烯基基团的硅橡胶中的一种,液体类橡胶的粘度为30cs-2000cs,优选粘度为52~900cs的液体类橡胶。
[0032]
进一步的,导热吸波填料为石墨烯包覆铁氧体、石墨烯包覆钡铁氧体、钴铁氧体-铁钴合金共包覆空心玻璃微珠、钴铁氧体-铁钴合金共包覆碳微球、羰基铁粉、氧化铝、氮化铝、钴铁氧体-铁钴合金、二氧化硅中的一种,导热吸波填料的结构为球形、类球形或角型,其中导热吸波填料的粉体粒径为1~200μm最佳。优选同一中导热吸波填料的不同粒径复配,例如选取氧化铝1~5微米和10~15微米、25~30微米和100~120微米的粒径复配。其中,石墨烯包覆铁氧体或石墨烯包覆钡铁氧体的石墨烯包覆层厚度为0.5~2μm,其中石墨烯主要为氧化石墨烯,需要将材料在石墨烯包覆后,在氩气气氛中煅烧后得到的,石墨烯包覆物;钴铁氧体-铁钴合金共包覆空心玻璃微珠或钴铁氧体-铁钴合金共包覆碳微球的钴铁氧体-铁钴合金包覆层厚度在0.1~2μm。
[0033]
进一步的,交联剂为含有过氧化双(2,4-二氯苯甲酰)、二异氰酸酯、过氧化二苯甲酰、二(亚肉桂基-1,6-己二胺)硫化物或1,3,5-三巯基-2,4,6-均三嗪基团的化合物中的一种。老化剂为胺类防老剂、酮胺类防老剂、醛胺类防老剂、气相二氧化硅防老剂或酚类防老剂中的一种。
[0034]
其中,交联剂主要是使基体和液体类橡胶在高温下发生化学反应,提高导热吸波
片材的强度和弹性、伸长率。老化剂主要是延长导热吸波片材的应用时间,提高材料的寿命。此外,由于交联剂在高温下发生化学反应,且为了让液体类橡胶和导热吸波填料充分混合,保证导热吸波填料在导热复合材料混合物中的均匀性,因此在加入交联剂之前,让液体类橡胶、导热吸波填料和防老剂进行搅拌,这样既能保证粉体混合均匀,又能保证材料在搅拌过程中化学反应的可控性。
[0035]
将制得的导热吸波片材进行导热、硬度、残余应力、吸收率等测试,其中,导热系数测试采用satm d5470的测试标准;介电常数测试采用asm d1461,采用sbjd厘斯-a型设备,gb/t1409-2006;吸收率采用拱形反射法,gjb2038a-2011;残余应力采用万能拉力机,25mm*25mm,下降速度25mm/min,稳定10min数据。
[0036]
实施例1的导热吸波片材制备:
[0037]
首先将20.7%粘度为800cs的聚丙烯酸酯橡胶、13%粒径为2微米的石墨烯包覆铁氧体、40%粒径为28微米的羰基铁粉、26%的粒径100微米的氧化铝、0.2%的防老剂n-苯基二胺置于转速为30转/min、真空度为-0.08以下的搅拌器内搅拌50min,使各组分混合均匀后,加入0.1%二异氰酸酯交联剂,转速为30转/min、真空度为-0.08以下的搅拌器内搅拌30min,物料温度为3℃,使各组分混合均匀,得到导热复合材料混合物。最后将多孔弹性石墨烯泡棉(孔径120微米)浸泡在导热复合材料混合物中,保持真空度为-0.1以下,抽真空30分钟后,逐步升温到120℃,保持4小时,得到导热吸波片材。
[0038]
实施例2的导热吸波片材制备:
[0039]
首先将15.7%粘度为800cs的聚丙烯酸酯橡胶、16%粒径为3微米的石墨烯包覆铁氧体、5%粒径为5微米的氮化铝、5%粒径为28微米的氧化铝、18%的粒径45微米的氧化铝、40%的粒径为80微米的羰基铁粉、0.2%的防老剂n-苯基二胺置于转速为30转/min、真空度为-0.08以下的搅拌器内搅拌50min,使各组分混合均匀后加入0.1%二异氰酸酯交联剂,转速为30转/min、真空度为-0.08以下的搅拌器内搅拌30min,物料温度为3℃,使各组分混合均匀,得到导热复合材料混合物。最后将多孔弹性石墨烯泡棉(孔径100微米)浸泡在导热复合材料混合物中,保持真空度为-0.1以下,抽真空30分钟后,逐步升温到120℃,保持4小时,得到导热吸波片材。
[0040]
实施例3的导热吸波片材制备:
[0041]
首先将15.5%粘度为800cs的乙烯基硅油橡胶、16%粒径为3微米的石墨烯包覆铁氧体、5%粒径为5微米的氮化铝、5%粒径为28微米的氧化铝、18%的粒径45微米的氧化铝、40%的粒径为80微米的羰基铁粉、0.2%的防老剂气相二氧化硅置于转速为30转/min、真空度为-0.08以下的搅拌器内搅拌50min,使各组分混合均匀后加入0.3%含氢硅油交联剂,转速为30转/min、真空度为-0.08以下的搅拌器内搅拌30min,物料温度为3℃,使各组分混合均匀,得到导热复合材料混合物。最后将多孔弹性石墨烯泡棉(孔径100微米)浸泡在导热复合材料混合物中,保持真空度为-0.1以下,抽真空30分钟后,逐步升温到80℃,保持4小时,得到导热吸波片材。
[0042]
实施例4的导热吸波片材制备:
[0043]
首先将15.7%粘度为800cs的乙烯基硅油橡胶、16%粒径为3微米的石墨烯包覆铁氧体、5%粒径为5微米的氮化铝、5%粒径为28微米的氧化铝、18%的粒径45微米的氧化铝、40%的粒径为80微米的羰基铁粉、0.2%的防老剂气相二氧化硅置于转速为30转/min、真空
度为-0.08以下的搅拌器内搅拌50min,使各组分混合均匀后加入0.1%含氢硅油交联剂,转速为30转/min、真空度为-0.08以下的搅拌器内搅拌30min,物料温度为3℃,使各组分混合均匀,得到导热复合材料混合物。最后将多孔弹性石墨烯泡棉(孔径100微米)浸泡在导热复合材料混合物中,保持真空度为-0.1以下,抽真空30分钟后,逐步升温到80℃,保持4小时,得到导热吸波片材。
[0044]
实施例5的导热吸波片材制备:
[0045]
首先将15.7%粘度为800cs的乙烯基硅油橡胶、16%粒径为3微米的石墨烯包覆铁氧体、5%粒径为5微米的氮化铝、5%粒径为28微米的氧化铝、18%的粒径45微米的氧化铝、40%的粒径为80微米的羰基铁粉、0.2%的防老剂气相二氧化硅置于转速为30转/min、真空度为-0.08以下的搅拌器内搅拌50min,使各组分混合均匀后加入0.1%含氢硅油交联剂,转速为30转/min、真空度为-0.08以下的搅拌器内搅拌30min,物料温度为3℃,使各组分混合均匀,得到导热复合材料混合物。最后将多孔弹性氮化硼纤维泡棉(孔径100微米)浸泡在导热复合材料混合物中,保持真空度为-0.1以下,抽真空60分钟后,逐步升温到80℃,保持4小时,得到导热吸波片材。
[0046]
实施例6的导热吸波片材制备:
[0047]
首先将15.7%粘度为800cs的乙烯基硅油橡胶、13%粒径为3微米的钴铁氧体-铁钴合金、31%粒径为28微米的羰基铁、40%的粒径为80微米的羰基铁粉、0.2%的防老剂气相二氧化硅置于转速为30转/min、真空度为-0.08以下的搅拌器内搅拌50min,使各组分混合均匀后加入0.1%含氢硅油交联剂,转速为40转/min、真空度为-0.08以下的搅拌器内搅拌40min,物料温度为3℃,使各组分混合均匀,得到导热复合材料混合物。最后将多孔弹性氮化硼纤维泡棉(孔径100微米)浸泡在导热复合材料混合物中,保持真空度为-0.1以下,抽真空60分钟后,逐步升温到80℃,保持4小时,得到导热吸波片材。
[0048]
实施例7的导热吸波片材制备:
[0049]
首先将8.7%粘度为800cs的乙烯基硅油橡胶、10%粒径为3微米的钴铁氧体-铁钴合金、10%粒径为5微米的氮化铝、15%粒径为28微米的羰基铁粉、20%粒径为45微米的氧化铝、20%的粒径为80微米的羰基铁粉、16%粒径为100微米的氧化铝、0.16%的防老剂气相二氧化硅置于转速为30转/min、真空度为-0.08以下的搅拌器内搅拌50min,使各组分混合均匀加入0.14%含氢硅油交联剂,转速为40转/min、真空度为-0.08以下的搅拌器内搅拌40min,物料温度为3℃,使各组分混合均匀,得到导热复合材料混合物。最后将多孔弹性氮化硼纤维泡棉(孔径120微米)浸泡在导热复合材料混合物中,保持真空度为-0.1以下,抽真空60分钟后,逐步升温到80℃,保持4小时,得到导热吸波片材。
[0050]
实施例8的导热吸波片材制备:
[0051]
首先将8.7%粘度为800cs的乙烯基硅油橡胶、10%粒径为3微米的钴铁氧体-铁钴合金、10%粒径为5微米的氮化铝、15%粒径为28微米的羰基铁粉、20%粒径为45微米的氧化铝、20%的粒径为80微米的羰基铁粉、16%粒径为100微米的氧化铝、0.16%的防老剂气相二氧化硅置于转速为30转/min、真空度为-0.08以下的搅拌器内搅拌50min,使各组分混合均匀后加入0.14%含氢硅油交联剂,转速为40转/min、真空度为-0.08以下的搅拌器内搅拌40min,物料温度为3℃,使各组分混合均匀,得到导热复合材料混合物。最后将多孔弹性石墨烯泡棉(100微米)浸泡在导热复合材料混合物中,保持真空度为-0.1以下,抽真空60分
钟后,逐步升温到80℃,保持4小时,得到导热吸波片材。
[0052]
实施例9的导热吸波片材制备:
[0053]
首先将8.7%粘度为800cs的乙烯基硅油橡胶、5%粒径为2微米的石墨烯包覆铁氧体,5%粒径为3微米的石墨烯包覆铁氧体、10%粒径为5微米的氮化铝、15%粒径为28微米的羰基铁粉、20%粒径为45微米的氧化铝、20%的粒径为80微米的羰基铁粉、16%粒径为100微米的氧化铝、0.16%的防老剂气相二氧化硅置于转速为30转/min、真空度为-0.08以下的搅拌器内搅拌50min,使各组分混合均匀后加入0.14%含氢硅油交联剂,转速为40转/min、真空度为-0.08以下的搅拌器内搅拌40min,物料温度为3℃,使各组分混合均匀,得到导热复合材料混合物。最后将多孔弹性氮化硼纤维泡棉(孔径120微米)浸泡在导热复合材料混合物中,保持真空度为-0.1以下,抽真空60分钟后,逐步升温到80℃,保持4小时,得到导热吸波片材。
[0054]
实施例10的导热吸波片材制备:
[0055]
首先将11.2%粘度为800cs的乙烯基硅油橡胶、9%粒径为2微米的石墨烯包覆铁氧体,2%粒径为3微米的钴铁氧体-铁钴合金、13%粒径为5微米的氮化铝、15%粒径为28微米的羰基铁粉、20%粒径为45微米的氧化铝、20%的粒径为80微米的羰基铁粉、13%粒径为100微米的氧化铝、0.4%的防老剂气相二氧化硅置于转速为30转/min、真空度为-0.08以下的搅拌器内搅拌50min,使各组分混合均匀后加入0.4%含氢硅油交联剂,转速为40转/min、真空度为-0.08以下的搅拌器内搅拌40min,物料温度为3℃,使各组分混合均匀,得到导热复合材料混合物。最后将多孔弹性氮化硼纤维泡棉(孔径120微米)浸泡在导热复合材料混合物中,保持真空度为-0.1以下,抽真空60分钟后,逐步升温到80℃,保持4小时,得到导热吸波片材。
[0056]
对比例1的导热吸波片材制备:
[0057]
首先将15.7%粘度为800cs的乙烯基硅油橡胶、13%粒径为3微米的钴铁氧体-铁钴合金、31%粒径为28微米的羰基铁、40%的粒径为80微米的羰基铁粉、0.2%的防老剂气相二氧化硅置于转速为30转/min、真空度为-0.08以下的搅拌器内搅拌50min,使各组分混合均匀后加入0.1%含氢硅油交联剂,转速为40转/min、真空度为-0.08以下的搅拌器内搅拌40min,物料温度为3℃,使各组分混合均匀,得到导热复合材料混合物。最后将导热复合材料混合物直接压延成片逐步升温到80℃,保持4小时,得到导热吸波片材。
[0058]
对比例2的导热吸波片材制备:
[0059]
首先将15.5%粘度为800cs的乙烯基硅油橡胶、16%粒径为3微米的石墨烯包覆铁氧体、5%粒径为5微米的氮化铝、5%粒径为28微米的氧化铝、18%的粒径45微米的氧化铝、40%的粒径为80微米的羰基铁粉、0.2%防老剂气相二氧化硅置于转速为30转/min、真空度为-0.08以下的搅拌器内搅拌50min,使各组分混合均匀加入0.3%含氢硅油交联剂,转速为30转/min、真空度为-0.08以下的搅拌器内搅拌30min,物料温度为3℃,使各组分混合均匀,得到导热复合材料混合物。最后将导热复合材料混合物直接压延成片逐步升温到80℃,保持4小时,得到导热吸波片材。
[0060]
对比例3的导热吸波片材制备:
[0061]
首先将15.5%粘度为800cs的乙烯基硅油橡胶、16%粒径为3微米的石墨烯包覆铁氧体、5%粒径为5微米的氮化铝、5%粒径为28微米的氧化铝、18%的粒径45微米的氧化铝、
40%的粒径为80微米的羰基铁粉、0.2%防老剂气相二氧化硅置于转速为30转/min、真空度为-0.08以下的搅拌器内搅拌50min,使各组分混合均匀后加入0.3%含氢硅油交联剂,转速为30转/min、真空度为-0.08以下的搅拌器内搅拌30min,物料温度为3℃,使各组分混合均匀,得到导热复合材料混合物。最后将多孔弹性氮化硼纤维泡棉(孔径100微米)浸泡在导热复合材料混合物中,保持真空度为-0.1以下,抽真空60分钟后,逐步升温到80℃,保持4小时,得到导热吸波片材。
[0062]
对比例4的导热吸波片材制备:
[0063]
首先将8.7%粘度为800cs的乙烯基硅油橡胶、10%粒径为3微米的钴铁氧体-铁钴合金、10%粒径为5微米的氮化铝,15%粒径为28微米的羰基铁粉,20%粒径为45微米的氧化铝,20%的粒径为80微米的羰基铁粉,16%粒径为100微米的氧化铝,0.16%的防老剂气相二氧化硅置于转速为30转/min、真空度为-0.08以下的搅拌器内搅拌50min,使各组分混合均匀吼加入0.14%含氢硅油交联剂,转速为40转/min、真空度为-0.08以下的搅拌器内搅拌40min,物料温度为3℃,使各组分混合均匀,得到导热复合材料混合物。最后将多孔弹性聚氨酯泡棉(100微米)浸泡在上述搅拌均匀的物料中,保持真空度为-0.1以下,抽真空60分钟后,逐步升温到80℃,保持4小时,得到导热吸波片材。
[0064]
对各实施例及对比例中的导热吸波片材的性能检测进行导热、硬度、残余应力、吸收率测试。各测试结果如表1所示:
[0065][0066]
表1
[0067]
从实验结果中实施例及对比例来看,实施例明显在导热、硬度、残余应力、吸收率方面均优于对比例,通过将导热复合材料混合物填充到多孔弹性泡棉中,利用泡棉形成的导热网络具有良好的导热吸波特性,此外,由于多孔弹性泡棉骨架的存在,使导热吸波片材具有良好的回弹性,并且材料硬度适中,完全满足毫米波雷达中的应用。
[0068]
以上所述,仅为本发明的具体实施方式,但本发明的保护范围并不局限于此,任何熟悉本技术领域的技术人员在本发明揭露的技术范围内,可轻易想到各种等效的修改或替换,这些修改或替换都应涵盖在本发明的保护范围之内。因此,本发明的保护范围应以权利要求的保护范围为准。