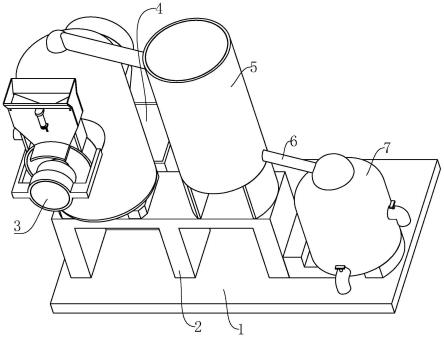
1.本发明涉及化妆品原料加工领域,特别涉及一种化妆品原料蒸馏提取分离机。
背景技术:2.化妆品是指以涂抹、喷洒或者其他类似方法,散布于人体表面的任何部位,如皮肤、毛发、指趾甲、唇齿等,以达到清洁、保养、美容、修饰和改变外观,或者修正人体气味,保持良好状态为目的的化学工业品或精细化工产品,而化妆品中通常又含有植物精油的成分。
3.植物精油又称挥发油或香精油,是带有芳香味的油状液体。植物精油源自草本植物的花、苞、叶、枝、根、树皮、果实、种子和树脂等,通过蒸馏、压榨、溶剂萃取等方式提炼出来。植物精油在化妆品中的功效应用具体包括抗氧化、抑菌等方面。而现有技术采用蒸馏的方式从植物中提取精油的过程,会影响到植物的出油率、对植物进行蒸馏的效率、以及植物精油的使用效果。
4.所以相关技术人员也在对植物进行蒸馏以提取植物精油的过程进行大量的优化,为了进行更准确的对比,例如公开号为cn208151327u的中国专利公开了一种玫瑰花精油蒸馏提取装置;其在使用时:当筒体底端的加热线圈使筒体温度内部升高时,带动搅拌棒旋转能够对玫瑰花瓣进行搅拌,玫瑰花精油蒸发后进入冷却机构的内部;当蒸馏结束后,转动螺杆带动第二挡板进行移动,使第二挡板与出料漏斗分开,再将第一水管接通水源,水从喷头中从上到下的清洗筒体的内部,将筒体内部的玫瑰花瓣运输到出料漏斗的上方,从而使玫瑰花瓣从出料漏斗中排出。
5.然而,在采用上述现有技术对植物进行蒸馏以提取植物精油的过程中:由于加热线圈位于筒体外侧,导致加热线圈的热传导效率不高,从而降低了对植物进行加热蒸馏的效果;当筒体内部的植物经过蒸馏后,需要停止对植物的加热和搅拌,然后采用加水的方式才能够将经过蒸馏的植物向外排出,而加水以排出植物的过程较为繁琐,从而降低了排出植物的效率;进一步的,由于上述现有技术在排出植物的过程中,无法对植物进行蒸馏作业,从而降低了对植物进行蒸馏加工的效率。因此,在上述陈述的观点之下,现有技术对植物进行蒸馏以提取植物精油的过程还有可提高的空间。
技术实现要素:6.为了解决上述问题,本发明提供了一种化妆品原料蒸馏提取分离机,包括底座和设置在底座上端的m形架,所述的m形架上端设置有用于对植物进行蒸馏加工的蒸馏机构,底座上位于蒸馏机构的一侧设置有用于接料的接料箱,蒸馏机构一侧设置有用于对蒸汽进行冷却的冷却机构,冷却机构一侧设置有排液管,排液管与油水分离机构相接通。
7.通过采用上述技术方案,首先将原料放置在蒸馏机构内,然后通过蒸馏机构能够对原料进行蒸馏,且蒸馏机构还能够在蒸馏过程中对原料进行搅拌,从而增加原料被蒸馏的效果;蒸馏机构还能够在进行自动的加料以及排料,完成蒸馏后的原料则能掉落至接料
箱内,从植物中被蒸馏出的精油则成为水蒸气并进入冷却机构内;然后通过冷却机构能够对水蒸气进行冷却,使水蒸气形成液体并流至油水分离机构内,之后油水分离机构则能够将其内部的液体分离成水和植物精油并区分排出,从而完成对植物的蒸馏加工。
8.所述的蒸馏机构包括安装在m形架上端并呈对称设置的支撑块,支撑块上端安装有内部中空的蒸馏筒,蒸馏筒下端设置有用于加热的加热单元,蒸馏筒的一侧接通有用于往其内部注水的进水龙头,蒸馏筒上开设有安装通槽,安装通槽内转动设置有转动筒,转动筒上位于蒸馏筒内的部分均匀开设有蒸馏通孔,转动筒上侧设置有进排料单元,蒸馏筒上端倾斜设置有用于往冷却机构内输送蒸汽的输气管。
9.通过采用上述技术方案,将进水龙头与外部排水设备相接通,然后通过外部排水设备往蒸馏筒注入清水,当蒸馏筒内具有适量清水后关闭进水龙头;再往进排料单元内放置适量的原料,之后通过加热机构对蒸馏筒内的清水进行加热,同时通过进排料单元带动转动筒和原料进行转动;当清水被加热至变成水蒸气后将会向上穿过原料、输气管并进入冷却机构内,当水蒸气经过原料时则能够将原料中的精油提取出来。
10.所述的加热单元包括设置在蒸馏筒下端并位于蒸馏筒内部的球形罩,所述m形架上端设置有位于球形罩内部的加热器,且加热器位于支撑块之间,。
11.通过采用上述技术方案,当位于球形罩内的加热器向四周加热时,球形罩能够尽可能的提高其受热的面积,从而提高了加热器的导热效果,并提高了对清水进行加热的效率以及效果。
12.所述的进排料单元包括设置在转动筒上远离接料箱一端的进料半环,进料半环下端安装有与蒸馏筒相固定的支撑连板,进料半环上端对称安装有支撑侧板,支撑侧板之间设置有进料器,进料半环内侧滑动安装有挤料环板,转动筒上位于接料箱上方的一端设置有排料器,排料器与进料器之间设置有用于带动原料进行转动的转动挤料器。
13.通过采用上述技术方案,进料器能够在添加原料前对原料进行承托,当进料器内的原料掉落至挤料环板上后,转动挤料器则能够将原料挤至转动筒内部,同时转动挤料器还能够带动转动筒一同转动,原料随转动筒进行转动时受热更均匀,从而增加对原料进行蒸馏的效果,经过蒸馏后的原料将会从排料器处向外掉落至接料箱内。
14.优选的,所述的进料器包括进料斗、销轴杆、托料斜板、伸缩气缸、升降板、连接挡板和条形板,进料斗安装在支撑连板之间,进料斗内部通过销轴杆以转动配合的方式对称设置有托料斜板,进料斗的一侧通过气缸座设置有伸缩端朝下的伸缩气缸,伸缩气缸下端安装有升降板,进料斗上开设有与升降板位置相对应的滑动通槽,升降板上靠近滑动通槽的的一侧设置有位于滑动通槽内的连接挡板,连接挡板上位于进料斗内的一侧安装有用于承托托料斜板的条形板,滑动通槽的上下侧壁上开设有与连接挡板相对应的容纳槽,连接挡板的上下两端分别位于上下两侧的容纳槽内。
15.通过采用上述技术方案,首先将原料放置在进料斗内的托料斜板上端,当需要加料时,通过伸缩气缸带动升降板、连接挡板和条形板一同向下移动,此时托料斜板将在重力的作用下向下翻转,位于托料斜板之间的原料则能够向下掉落至进料半环上端;当完成加料后,通过伸缩气缸再间接带动条形板向上移动复位,此时托料斜板能够在条形板的带动下向上翻转复位,复位后相贴合的两个条形板能够避免水蒸气中条形板之间向上散出;在连接挡板上下移动的过程中,能一直将滑动通槽堵住,从而能够避免水蒸气从滑动通槽内
向外散出。
16.优选的,所述的转动挤料器包括驱动转杆、驱动电机、螺旋条板、挡缝板、弧形螺纹、弧形凸起和挡料弧板,驱动转杆设置在挤料环板内侧,驱动转杆靠近挤料环板的一端安装有驱动电机,驱动电机通过电机座与进料半环相固定,驱动转杆与转动筒之间设置有环形分布的多个螺旋条板,螺旋条板上均匀开设有透气通孔,相邻的两个螺旋条板为一组,相邻的两组螺旋条板之间位于其前后两侧均设置有的挡缝板,驱动转杆外侧面上且位于前侧的挡缝板前端开设有相对的两条弧形螺纹,两条弧形螺纹相交且弧形螺纹两侧的端头处相接通,挤料环板内侧设置有位于弧形螺纹内的弧形凸起,挤料环板上端设置有与进料器滑动配合的挡料弧板。
17.通过采用上述技术方案,能够将原料挤压至螺旋条板之间;当进料器内的原料掉落至进料半环内时,开启驱动电机,驱动电机输出轴旋转能够带动驱动转杆进行转动,驱动转杆转动时将通过弧形凸起带动挤料环板沿弧形螺纹进行移动,当挤料环板向靠近蒸馏筒的一侧移动时则能够对原料进行挤压,使原料进入螺旋条板之间;当挤料环板内侧的弧形凸起移动至贴合挡缝板时,弧形凸起将进入另一个弧形螺纹内,此时弧形凸起将带动挤料环板向远离蒸馏筒的一侧移动复位。
18.优选的,所述的排料器包括排料半环、支撑折板、挡料圆板、复位拉簧杆、连接圆板、支撑圆杆和堵料板,排料半环转动设置在转动筒上位于接料箱上方的一端,排料半环下侧开口的两侧对称设置有与蒸馏筒相固定的支撑折板,排料半环内侧设置有挡料圆板,驱动转杆上靠近挡料圆板的一侧设置有复位拉簧杆,复位拉簧杆的伸缩端安装有连接圆板,连接圆板上均匀设置有与螺旋条板位置相对应的支撑圆杆,支撑圆杆靠近螺旋条板的一侧设置有位于一组所述螺旋条板之间的堵料板。
19.通过采用上述技术方案,便于对经过蒸馏后的原料进行排料;当驱动转杆进行转动时,复位拉簧杆、连接圆杆、支撑圆杆和堵料板能够随之进行转动,当挤料环板将原料挤压至螺旋条板之间时,位于螺旋条板之间且经过蒸馏的原料则会顶起堵料板,使得经过蒸馏后的原料能够从堵料板与螺旋条板之间向外排出,而排出后的原料则会向下掉落至接料箱内。
20.优选的,所述的冷却机构包括撑筒板、冷却筒、制冷环、安装圆筒、制冷块、螺旋冷却管和刮壁单元,撑筒板对称安装在m形架上端,撑筒板上端之间设置有冷却筒,冷却筒内均匀设置有多个上下分布的制冷环,冷却筒中部设置有安装圆筒,安装圆筒内部均匀设置有多个上下分布的制冷块,制冷块、制冷环的温度为从上往下递减设置,冷却筒的上下侧壁之间还设置有螺旋冷却管,且螺旋冷却管位于制冷环和制冷块之间,输气管穿过冷却筒和制冷环与螺旋冷却管相接通,螺旋冷却管的下端与排液管相接通,螺旋冷却管与安装圆筒之间设置有刮壁单元。
21.通过采用上述技术方案,能够对蒸馏产生的水蒸气进行冷却;当水蒸气进入螺旋冷却管内后,通过制冷环和制冷块能够对螺旋冷却管内的水蒸气进行冷却,在此过程中,由于位于不同高度的制冷环、制冷块的温度不同,从而能够避免因螺旋冷却管内的水蒸气温度过高,制冷块、制冷环的温度过低,而降低螺旋冷却管使用寿命的问题。
22.优选的,所述的刮壁单元包括电动滑杆、电动滑块、电磁铁环和磁石刮环,电动滑杆安装在冷却筒的上下侧壁之间,电动滑杆外侧面上滑动设置有电动滑块,电动滑块的一
侧安装有电磁铁环,电磁铁环滑动套设在安装圆筒外侧面上,螺旋冷却管内滑动设置有与电磁铁环相吸附的磁石刮环。
23.通过采用上述技术方案,能够对螺旋冷却管的内壁进行刮动;通过电动滑块能够带动电磁铁环进行上下移动,电磁铁环上下移动时则能带动磁石刮环在螺旋冷却管内进行螺旋移动,而磁石刮环的移动则能够对螺旋冷却管的内壁进行清理。
24.优选的,所述的油水分离机构包括安装底块、分离筒、排油龙头、排水龙头和升降单元,安装底块设置在底座上端并与m形架相连接,安装底块上端设置有与排液管相接通的分离筒,分离筒壁上至少开设有上下分布的两个出液孔,上侧的出液孔内设置有排油龙头,下侧的出液孔内设置有排水龙头,分离筒内还设置有用于带动液体进行升降调节的升降单元。
25.通过采用上述技术方案,能够通过油水不融的原理将植物精油与蒸馏水区分开;当植物精油和蒸馏水在冷却机构内完成冷却后,将从排液管内流动至分离筒内;位于分离筒内下侧的则为蒸馏水,位于蒸馏水上端的是植物精油,然后通过位于上侧的排油龙头将植物精油向外排出,再通过位于下侧的排水龙头将蒸馏水向外排出,从而达到油水分离的目的。
26.优选的,所述的升降单元包括升降气缸、托液板、橡胶密封圈、支撑杆和刮油环,安装底块中部以及底座上端开设有气缸槽,气缸槽内设置有升降气缸,分离筒下端开设有与升降气缸伸缩端相对应的圆形通孔,升降气缸的伸缩端向上穿过圆形通孔并设置有托液板,托液板的外侧面上设置有与分离筒相贴合的橡胶密封圈,托液板上端环形设置有多个支撑杆,支撑杆上端之间设置有与分离筒内壁相贴合的刮油环。
27.通过采用上述技术方案,能够对分离筒内液体的高度进行调节;当经过冷却机构的流动液体流动至分离筒内后,托液板能够对液体进行承托,此时橡胶密封圈能够避免液体从托液板和分离筒之间流出;然后通过升降气缸能够带动托液板进行上下调节,从而避免因植物油的高度过低而从排水龙头中流出;当托液板上下调节时能够通过支撑杆带动刮油环对分离筒内壁的植物精油进行刮除。
28.综上所述,本技术包括以下至少一种有益技术效果:
29.一、本发明加热单元的位置能够被清水所包覆,从而起到从内向外加热的效果,并尽可能的提高了导热效果,从而提高了热传导率和对清水进行加热的速度,并提高了对原料进行蒸馏的效率。
30.二、本发明通过蒸馏机构能够将完成蒸馏后的原料自动排出,较于现有技术需要加水才能排出蒸馏后的原料而言,提高了排料操作的自动化程度以及排料的效率;进一步的,由于本发明能够在排料的同时对原料进行蒸馏,较于现有技术在不进行蒸馏时才能排料而言,提高了本发明对原料进行蒸馏的效率。
附图说明
31.下面结合附图和实施例对本发明进一步说明。
32.图1是本发明的结构示意图。
33.图2是本发明底座、m形架、蒸馏机构和接料箱之间的结构示意图。
34.图3是本发明转动筒、进排料单元、进料器和转动挤料器之间的结构示意图。
35.图4是本发明进料器的结构示意图。
36.图5是本发明蒸馏机构的部分结构示意图。
37.图6是本发明蒸馏筒和排料器之间的结构示意图。
38.图7是本发明底座、m形架、冷却机构和排液管之间的结构示意图。
39.图8是本发明安装圆筒、螺旋冷却管和刮壁单元的结构示意图。
40.图9是本发明底座、排液管和油水分离机构之间的结构示意图。
41.图中,1、底座;2、m形架;3、蒸馏机构;4、接料箱;5、冷却机构;6、排液管;7、油水分离机构;30、支撑块;31、蒸馏筒;32、加热单元;33、进水龙头;34、转动筒;35、进排料单元;36、输气管;37、进料器;38、排料器;39、转动挤料器;50、撑筒板;51、冷却筒;52、制冷环;53、安装圆筒;54、制冷块;55、螺旋冷却管;56、刮壁单元;70、安装底块;71、分离筒;72、排油龙头;73、排水龙头;74、升降单元;75、升降气缸;76、托液板;77、橡胶密封圈;78、支撑杆;79、刮油环;320、球形罩;321、加热器;350、进料半环;351、支撑连板;352、支撑侧板;353、挤料环板;370、进料斗;371、销轴杆;372、托料斜板;373、伸缩气缸;374、升降板;375、连接挡板;376、条形板;380、排料半环;381、支撑折板;382、挡料圆板;383、复位拉簧杆;384、连接圆板;385、支撑圆杆;386、堵料板;390、驱动转杆;391、驱动电机;392、螺旋条板;393、挡缝板;394、弧形螺纹;395、弧形凸起;396、挡料弧板;560、电动滑杆;561、电动滑块;562、电磁铁环;563、磁石刮环。
具体实施方式
42.以下结合附图1-9对本发明的实施例进行详细说明,但是本发明可以由权利要求限定和覆盖的多种不同方式实施。
43.本技术实施例公开了一种化妆品原料蒸馏提取分离机,说明的有,本化妆品原料蒸馏提取分离机主要是应用在对植物进行蒸馏以提取植物精油的过程中,在技术效果上能够在对植物原料进行蒸馏的过程中进行原料添加,同时还能够将经过适当蒸馏后的植物原料向外排出,特别是在对植物原料进行蒸馏的过程中,能够带动植物原料进行转动,使其能够位于不同位置,从而增加其受热的均匀性,提高了对植物进行蒸馏的效果。
44.实施例一:
45.参照图1所示,化妆品原料蒸馏提取分离机,包括底座1和设置在底座1上端的m形架2,m形架2上端设置有用于对植物进行蒸馏加工的蒸馏机构3,首先将原料放置在蒸馏机构3内,然后通过蒸馏机构3能够对原料进行蒸馏;底座1上位于蒸馏机构3的一侧设置有用于接料的接料箱4,完成蒸馏后的原料则能掉落至接料箱4内;
46.蒸馏机构3一侧设置有用于对蒸汽进行冷却的冷却机构5,冷却机构5下端安装在m形架2上端,从植物中被蒸馏出的精油则成为水蒸气并进入冷却机构5内,然后通过冷却机构5能够对水蒸气进行冷却;冷却机构5一侧设置有排液管6,排液管6与油水分离机构7相接通,冷却后的水蒸气将变成液体并从排液管6内流至油水分离机构7内,之后油水分离机构7则能够将其内部的液体分离成水和植物精油并区分排出,从而完成对植物的蒸馏加工。
47.参照图2所示,即本技术中的蒸馏机构3;具体的,蒸馏机构3包括安装在m形架2上端并呈对称设置的支撑块30,支撑块30上端安装有内部中空的蒸馏筒31,使得原料能够在蒸馏筒31内被进行蒸馏加工;蒸馏筒31下端设置有用于加热的加热单元32,蒸馏筒31的一
侧接通有用于往其内部注水的进水龙头33;将进水龙头33与外部排水设备相接通,然后通过外部排水设备往蒸馏筒31注入清水,当蒸馏筒31内具有适量清水后关闭进水龙头33;之后通过加热机构对蒸馏筒31内的清水进行加热,能够使被加热至一定程度的清水逐渐变成水蒸气;当蒸馏筒31内的清水较少时还可以再次通过加水龙头往蒸馏筒31内注水。
48.蒸馏筒31上开设有安装通槽,安装通槽内转动设置有转动筒34,转动筒34上位于蒸馏筒31内的部分均匀开设有蒸馏通孔,使得水蒸气能够穿过转动筒34;转动筒34上侧设置有进排料单元35,通过进排料单元35能够往转动筒34内部添加原料,水蒸气穿过蒸馏通孔能够对原料进行蒸馏,使得原料中的植物精油能够被水蒸气提取出来;蒸馏筒31上端倾斜设置有用于往冷却机构5内输送蒸汽的输气管36,水蒸气穿过原料后将从输气管36内流动至冷却机构5内。
49.继续参照图2所示,即用于在对蒸馏筒31内的清水进行加热时提高热传导率的加热单元32;具体的,加热单元32包括设置在蒸馏筒31下端并位于蒸馏筒31内部的球形罩320,当清水被注入至蒸馏筒31内部后会位于球形罩320外侧,此时清水形成了包覆住球形罩320的状态;m形架2上端设置有位于球形罩320内部的加热器321,加热器321进行加热时,能够达到从清水内部往外加热的效果,从而提高了对清水进行加热的效率以及加热器321的热传导率;加热器321位于支撑块30之间,从而使加热器321不会受到蒸馏筒31的压力。
50.参照图3所示,为了在对原料进行蒸馏的过程中往转动筒34内部进行加料,也为了便于在不影响对原料进行蒸馏的情况下及时的将经过蒸馏后的原料向外排出,便在转动筒34上设置了进排料单元35;具体的,进排料单元35包括设置在转动筒34上远离接料箱4一端的进料半环350,进料半环350下端安装有与蒸馏筒31相固定的支撑连板351,当转动筒34进行转动时,支撑连板351和进料半环350则不会转动;进料半环350上端对称安装有支撑侧板352,支撑侧板352之间设置有进料器37,支撑侧板352能够对进料器37进行支撑,往进料器37内添加原料,原料则能够在进料器37的驱动下被添加至进料半环350内侧。
51.进料半环350内侧滑动安装有挤料环板353,转动筒34上位于接料箱4上方的一端设置有排料器38,排料器38与进料器37之间设置有用于带动原料进行转动的转动挤料器39;当原料被添加至进料半环350内侧后,通过转动挤料器39能够带动挤料环板353进行移动,挤料圆板移动时则能够将进料半环350上端的原料挤压至转动挤料器39内,此时转动挤料器39则能够带动转动筒34和原料进行转动,在此过程中原料将被进行蒸馏处理,经过蒸馏后的原料将从排料器38出向外排出并掉落至接料箱4内。
52.参照图4所示,即本技术中的进料器37;具体的,进料器37包括进料斗370、销轴杆371、托料斜板372、伸缩气缸373、升降板374、连接挡板375和条形板376,进料斗370安装在支撑连板351之间,且进料都为上端外扩的结构,以便于对原料进行添加;进料斗370内部通过销轴杆371以转动配合的方式对称设置有托料斜板372,将原料放置在进料斗370内后托料斜板372将对原料进行承托;
53.进料斗370的一侧通过气缸座设置有伸缩端朝下的伸缩气缸373,伸缩气缸373下端安装有升降板374,伸缩气缸373能够带动升降板374进行上下移动;进料斗370上开设有与升降板374位置相对应的滑动通槽,升降板374上靠近滑动通槽的的一侧设置有位于滑动通槽内的连接挡板375,连接挡板375上位于进料斗370内的一侧安装有用于承托托料斜板372的条形板376,升降板374上下移动时能够带动连接挡板375和条形板376进行上下移动;
滑动通槽的上下侧壁上开设有与连接挡板375相对应的容纳槽,连接挡板375的上下两端分别位于上下两侧的容纳槽内。
54.当需要加料时,通过伸缩气缸373间接带动条形板376向下移动,此时托料斜板372将在重力的作用下向下翻转,位于托料斜板372上端的原料则能够从托料斜板372之间向下掉落至进料半环350上端;当完成加料后,通过伸缩气缸373再间接带动条形板376向上移动复位,此时托料斜板372能够在条形板376的带动下向上翻转复位,复位后相贴合的两个条形板376能够避免水蒸气中条形板376之间向上散出;在连接挡板375上下移动的过程中,连接挡板375能够在容纳槽内滑动并一直将滑动通槽堵住,从而能够避免水蒸气从滑动通槽内向外散出。
55.参照图5所示,为了能够带动挤料环板353进行往复移动挤料,也为了带动原料和转动筒34一同进行转动,而设置的转动挤料器39;具体的,转动挤料器39包括驱动转杆390、驱动电机391、螺旋条板392、挡缝板393、弧形螺纹394、弧形凸起395和挡料弧板396,驱动转杆390设置在挤料环板353内侧,驱动转杆390靠近挤料环板353的一端安装有驱动电机391,驱动电机391通过电机座与进料半环350相固定,驱动电机391输出轴旋转时能够带动驱动转杆390进行转动;驱动转杆390与转动筒34之间设置有环形分布的多个螺旋条板392,驱动转杆390转动时能够通过螺旋条板392带动转动筒34进行转动。
56.螺旋条板392上均匀开设有透气通孔,从而便于水蒸气从透气通孔处穿过;相邻的两个螺旋条板392为一组,当挤料环板353带动原料向螺旋条板392一侧移动时,原料将进入同一组的两个螺旋条板392之间,而穿过透气通孔的水蒸气则能够对位于螺旋条板392之间的原料进行精油提取;相邻的两组螺旋条板392之间位于其前后两侧均设置有的挡缝板393,当挤料环板353将原料相螺旋条板392之间挤压时,挡缝板393则能够避免原料进入相邻两组的螺旋条板392之间,而前后两侧的挡缝板393之间的空隙则便于水蒸气穿过。
57.驱动转杆390外侧面上且位于前侧的挡缝板393前端开设有相对的两条弧形螺纹394,两条弧形螺纹394相交且弧形螺纹394两侧的端头处相接通,挤料环板353内侧设置有位于弧形螺纹394内的弧形凸起395;当驱动转杆390转动时能够通过弧形螺纹394带动弧形凸起395和挤料环板353沿弧形凸起395进行移动;当挤料环板353向靠近蒸馏筒31的一侧移动时则能够对原料进行挤压,使原料进入螺旋条板392之间;当挤料环板353内侧的弧形凸起395移动至贴合挡缝板393时,弧形凸起395将进入另一个弧形螺纹394内,此时弧形凸起395将带动挤料环板353向远离蒸馏筒31的一侧移动复位。
58.挤料环板353上端设置有与进料器37滑动配合的挡料弧板396,当挤料环板353向靠近蒸馏筒31的一侧移动时,挡料弧板396能够对进料半环350的上端开口进行阻挡,从而避免原料从挤料环板353和进料斗370之间向下掉落;当挤料环板353向远离蒸馏筒31的一侧移动时,掉落至挡料弧板396上端的原料将在进料斗370的挤压下掉落至进料半环350内。
59.参照图6所示,即用于与转动挤料器39配合而进行排料的排料器38;具体的,排料器38包括排料半环380、支撑折板381、挡料圆板382、复位拉簧杆383、连接圆板384、支撑圆杆385和堵料板386,排料半环380转动设置在转动筒34上位于接料箱4上方的一端,排料半环380下侧开口的两侧对称设置有与蒸馏筒31相固定的支撑折板381,当转动筒34转动时排料半环380将在支撑折板381的固定下不会转动,对称设置的支撑折板381则不会对排料的过程造成阻挡。
60.排料半环380内侧设置有挡料圆板382,驱动转杆390上靠近挡料圆板382的一侧设置有复位拉簧杆383,复位拉簧杆383的伸缩端安装有连接圆板384,复位拉簧杆383能够为连接圆板384提供始终向驱动转杆390一侧靠近的力;连接圆板384上均匀设置有与螺旋条板392位置相对应的支撑圆杆385,支撑圆杆385靠近螺旋条板392的一侧设置有位于一组所述螺旋条板392之间的堵料板386。
61.当驱动转杆390进行转动时,复位拉簧杆383、连接圆杆、支撑圆杆385和堵料板386能够随之进行转动,当挤料环板353将原料挤压至螺旋条板392之间时,位于螺旋条板392之间且经过蒸馏的原料则会顶起堵料板386,使得经过蒸馏后的原料能够从堵料板386与螺旋条板392之间向外排出,而排出后的原料则会向下掉落至接料箱4内;当挤料环板353向远离蒸馏筒31的一侧移动时,堵料板386又能够在复位拉簧杆383的拉力作用下,将同一组内的两个螺旋条板392之间的缝隙堵上,从而能够避免水蒸气从同一组内的两个螺旋条板392之间向外散出。
62.实施例二:
63.参照图7和图8所示,在实施例一的基础上,为了便于对水蒸气进行冷却,所以设置了与输气管36相接通的冷却机构5;具体的,冷却机构5包括撑筒板50、冷却筒51、制冷环52、安装圆筒53、制冷块54、螺旋冷却管55和刮壁单元56,撑筒板50对称安装在m形架2上端,撑筒板50上端之间设置有冷却筒51,冷却筒51能够被撑筒块进行支撑固定;冷却筒51内均匀设置有多个上下分布的制冷环52,冷却筒51中部设置有安装圆筒53,安装圆筒53内部均匀设置有多个上下分布的制冷块54,制冷块54和制冷环52能够进行制冷降温。
64.制冷块54、制冷环52的温度为从上往下递减设置,冷却筒51的上下侧壁之间还设置有螺旋冷却管55,且螺旋冷却管55位于制冷环52和制冷块54之间,输气管36穿过冷却筒51和制冷环52与螺旋冷却管55相接通;当水蒸气穿过输气管36后将会进入螺旋冷却管55内,此时位于螺旋冷却管55内外两侧的制冷块54则能够对螺旋冷却管55内的水蒸气进行降温,在此过程中,由于位于不同高度的制冷环52、制冷块54的温度不同,从而能够避免因螺旋冷却管55内的水蒸气温度过高,制冷块54、制冷环52的温度过低,而降低螺旋冷却管55使用寿命的问题了,而水蒸气在经过降温后能够变成液体并流动至螺旋冷却管55的下侧。
65.螺旋冷却管55的下端与排液管6相接通,流动至螺旋冷却管55下侧的液体则能够穿过排液管6并流动至油水分离机构7内;螺旋冷却管55与安装圆筒53之间设置有刮壁单元56,当螺旋冷却管55内的液体与螺旋冷却管55的内壁发生粘连时,通过刮壁单元56能够对螺纹冷却管的内壁进行刮动,从而使液体不再与螺旋冷却管55内壁相粘连,起到了对螺旋冷却管55内壁进行清理的作用,并且能够避免螺旋冷却管55内壁因粘附液体而影响液体通过效率的问题。
66.参照图8所示,即用于对螺旋冷却管55内壁进行清理的刮壁单元56;具体的,刮壁单元56包括电动滑杆560、电动滑块561、电磁铁环562和磁石刮环563,电动滑杆560安装在冷却筒51的上下侧壁之间,电动滑杆560外侧面上滑动设置有电动滑块561,电动滑块561能在电动滑杆560外侧上下移动;电动滑块561的一侧安装有电磁铁环562,电动滑块561移动时能够带动电磁铁环562一同移动;电磁铁环562滑动套设在安装圆筒53外侧面上,安装圆筒53能够对电磁铁环562的移动轨迹进行限位和导向;螺旋冷却管55内滑动设置有与电磁铁环562相吸附的磁石刮环563,当需要对螺旋冷却管55的内壁进行清理时,通过电动滑块
561能够带动电磁铁环562进行上下移动,电磁铁环562上下移动时则能带动磁石刮环563在螺旋冷却管55内进行螺旋移动,而磁石刮环563的移动则能够对螺旋冷却管55的内壁进行清理。
67.实施例三:
68.参照图9所示,在实施例二的基础上,为了对冷却后的油、水混合液体进行油、水分离,便通过油水不融的原理设置了与排液管6相接通的油水分离机构7;具体的,油水分离机构7包括安装底块70、分离筒71、排油龙头72、排水龙头73和升降单元74,安装底块70设置在底座1上端并与m形架2相连接,安装底块70上端设置有与排液管6相接通的分离筒71,当植物精油和蒸馏水在冷却机构5内完成冷却后,将从排液管6内流动至分离筒71内;位于分离筒71内下侧的则为蒸馏水,位于蒸馏水上端的是植物精油。
69.分离筒71壁上至少开设有上下分布的两个出液孔,上侧的出液孔内设置有排油龙头72,下侧的出液孔内设置有排水龙头73,然后通过位于上侧的排油龙头72将植物精油向外排出,再通过位于下侧的排水龙头73将蒸馏水向外排出,从而达到油水分离的目的;分离筒71内还设置有用于带动液体进行升降调节的升降单元74,通过对液体的位置进行调节,能够避免植物精油从排水龙头73中向外排出。
70.继续参照图9所示,即本技术中的升降单元74;具体的,升降单元74包括升降气缸75、托液板76、橡胶密封圈77、支撑杆78和刮油环79,安装底块70中部以及底座1上端开设有气缸槽,气缸槽内设置有升降气缸75,分离筒71下端开设有与升降气缸75伸缩端相对应的圆形通孔,升降气缸75的伸缩端向上穿过圆形通孔并设置有托液板76,当经过冷却机构5的流动液体流动至分离筒71内后,托液板76能对液体进行承托。
71.托液板76的外侧面上设置有与分离筒71相贴合的橡胶密封圈77,橡胶密封圈77能够避免液体从托液板76和分离筒71之间流出;托液板76上端环形设置有多个支撑杆78,支撑杆78上端之间设置有与分离筒71内壁相贴合的刮油环79,当托液板76上下调节时能够通过支撑杆78带动刮油环79对分离筒71内壁的植物精油进行刮除;通过升降气缸75能够带动托液板76进行上下调节,从而避免因植物油的高度过低而从排水龙头73中流出。
72.工作时:第一步,将进水龙头33与外部排水设备相接通,然后通过外部排水设备往蒸馏筒31注入清水,当蒸馏筒31内具有适量清水后关闭进水龙头33;再通过加热器321对清水进行加热,在此过程中将适量原料放在进料斗370内的托料斜板372上。
73.第二步:当需要进行加料时,通过伸缩气缸373间接带动条形板376向下移动,此时托料斜板372将在重力的作用下向下翻转,位于托料斜板372上端的原料则能够从托料斜板372之间向下掉落至进料半环350上端;当完成加料后,通过伸缩气缸373再间接带动条形板376向上移动复位,此时托料斜板372能够在条形板376的带动下向上翻转复位。
74.第三步:之后开启驱动电机391,驱动电机391输出轴旋转时能够带动驱动转杆390、螺旋条板392和转动筒34一同转动;当驱动转杆390转动时能够通过弧形螺纹394带动弧形凸起395和挤料环板353沿弧形凸起395进行移动;当挤料环板353向靠近蒸馏筒31的一侧移动时则能够对原料进行挤压,使原料进入螺旋条板392之间;当挤料环板353内侧的弧形凸起395移动至贴合挡缝板393时,弧形凸起395将进入另一个弧形螺纹394内,此时弧形凸起395将带动挤料环板353向远离蒸馏筒31的一侧移动复位。
75.第四步:当原料进入同一组内的两个螺旋条板392之间后,将会在转动的过程中于
蒸馏筒31受到蒸馏加工;当驱动转杆390进行转动时,复位拉簧杆383、连接圆杆、支撑圆杆385和堵料板386能够随之进行转动,当挤料环板353将原料挤压至螺旋条板392之间时,位于螺旋条板392之间且经过蒸馏的原料则会顶起堵料板386,使得经过蒸馏后的原料能够从堵料板386与螺旋条板392之间向外排出,而排出后的原料则会向下掉落至接料箱4内。
76.第五步:而提取了植物精油的水蒸气则向上进入输气管36内,之后水蒸气将穿过输气管36后进入螺旋冷却管55内,此时位于螺旋冷却管55内外两侧的制冷块54则能够对螺旋冷却管55内的水蒸气进行降温;当螺旋冷却管55内的液体与螺旋冷却管55的内壁发生粘连时,通过电动滑块561能够带动电磁铁环562进行上下移动,电磁铁环562上下移动时则能带动磁石刮环563在螺旋冷却管55内进行螺旋移动,而磁石刮环563的移动则能够对螺旋冷却管55的内壁进行清理。
77.第六步:当植物精油和蒸馏水在冷却机构5内完成冷却后,将从排液管6内流动至分离筒71内;位于分离筒71内下侧的则为蒸馏水,位于蒸馏水上端的是植物精油;通过升降气缸75能够带动托液板76进行上下调节,从而避免因植物油的高度过低而从排水龙头73中流出;然后通过位于上侧的排油龙头72将植物精油向外排出,再通过位于下侧的排水龙头73将蒸馏水向外排出,从而达到油水分离的目的。
78.对于本领域技术人员而言,显然本发明不限于上述示范性实施例的细节,而且在不背离本发明的精神或基本特征的情况下,能够以其他的具体形式实现本发明。因此,无论从哪一点来看,均应将实施例看作是示范性的,而且是非限制性的,本发明的范围由所附权利要求而不是上述说明限定,因此旨在将落在权利要求的等同要件的含义和范围内的所有变化囊括在本发明内。不应将权利要求中的任何附图标记视为限制所涉及的权利要求。
79.此外,应当理解,虽然本说明书按照实施方式加以描述,但并非每个实施方式仅包含一个独立的技术方案,说明书的这种叙述方式仅仅是为清楚起见,本领域技术人员应当将说明书作为一个整体,各实施例中的技术方案也可以经适当组合,形成本领域技术人员可以理解的其他实施方式。