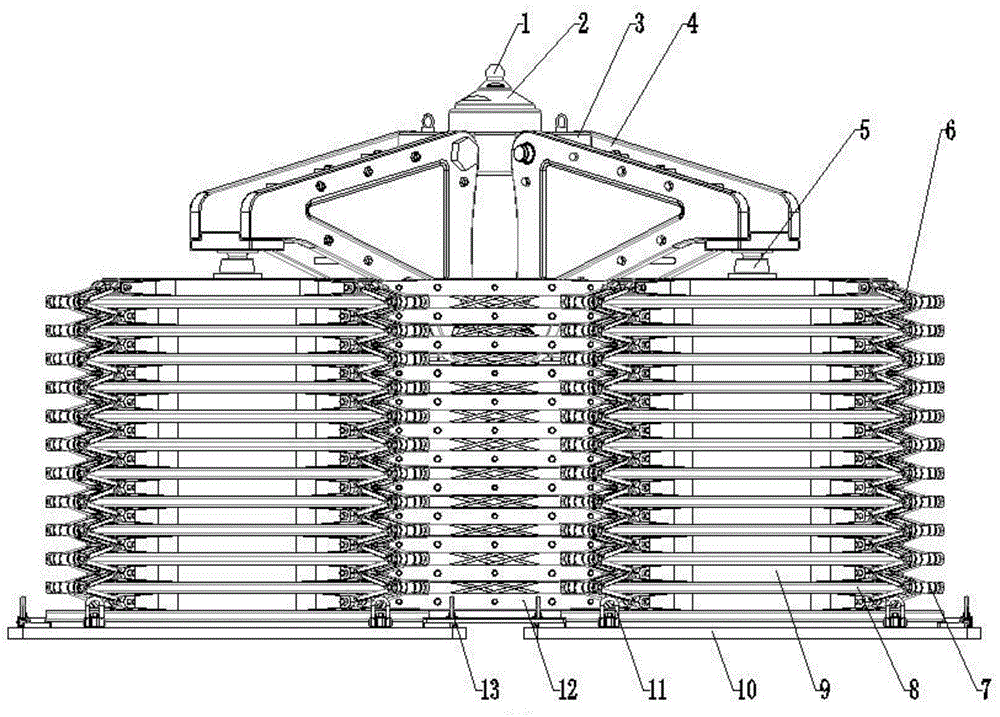
本发明属于航空器救援领域,涉及一种航空器用顶升设备,尤其是一种航空器用顶升系统及顶升方法。
背景技术:
:千斤顶是一种采用刚性顶举件为基础的顶升装置,其采用被广泛应用于各个领域当中。以其在航空器救援领域的实施方式为例,可应用于飞机维修,养护以及设备更换等多个工作过程中。目前航空器用的顶升设备多采用传统的柱式液压千斤顶,其结构主要包括油缸和与机型适配的适配器。该类千斤顶体积小,荷载大可广泛应用在大部分的机型当中。在实际使用过程中,由于千斤顶的可调节行程有限因此一般需配置相应的底座来增大其顶升行程。其实际使用方式如专利号为“201201945103”,“2017204340641”以及专利号为“2015105243625”的多篇专利所示。上述公开文件所示的底座多采用三脚架或类三脚架的结构,将传统的柱式液压缸固定在底座的上端位置,在使用过程中,先采用底座作为大范围的调整基准,待柱式液压缸移动至航空器下方的调节行程内后,再通过柱式液压缸进行顶升。但上述结构的顶升装置均存在一定的问题。其一,在竖直方向上的高度调整不够灵活,由于各个底座的高度均是有限的,因此,各个底座在展开状态下的最大高度即限制了顶升装置的顶升高度极限。由于各航空器的型号不同,其顶升位置与地面之间的间距是不固定的,而上述专利公开的底座的高度极限均是固定的,不可进行大范围的调整,当航空器与地面之间的间距过高或过低时,该类顶升装置均无法正常使用。其二,以上顶升装置的结构对于顶升位置的地面都有很高要求,即需要底座底部的三角形结构基本处于水平状态才可以正常使用。如地面为泥土,草地等软质基面,就会导致以上顶升装置的底部固定不够稳固,存在很大的倾倒风险。其三,以上结构的顶升装置的液压缸的顶升角度无法调整,只能在竖直方向上进行位移。由于顶升装置是布置在航空器顶升位置的下方的,其在低位位置时无法保证液压缸的水平位置恰好处于顶升位置的正投影位置下方。当顶升装置展开至高位位置时,则很可能出现液压缸和航空器顶升位置存在偏差的情况,此时,只能再将顶升装置下放至低位位置,然后整体将其整体平移再次顶升。该过程操作要求高,难度大,可能需重复调整进行几次。技术实现要素:本发明的目的在于克服现有技术的不足,提供一种结构灵活,适应性广,顶升稳固,顶升角度可调的航空器用顶升系统。本发明采取的技术方案是:一种航空器用顶升系统,包括一个油缸,所述油缸的升降端安装有一适配器,该油缸可控制适配器发生上下位移,其特征在于:所述油缸的下方安装有顶升装置,该顶升装置用于将油缸和适配器同步上、下移动并在水平方向内调整适配器的轴线角度。进一步的,所述油缸的下端部安装在一个安装座内,该安装座外部均匀间隔安装有多个耳板,所述耳板远离安装座的端部和顶升装置的安装固定。进一步的,所述顶升装置包括高度调节组件和角度调节组件,其中高度调节组件用于调整油缸的水平高度,角度调节组件用于调整适配器水平方向内的角度。进一步的,所述高度调节组件和角度调节组件均采用气囊,多个气囊沿纵向叠放,位于底层的为角度调节组件,位于底层之上的多个气囊为高度调节组件。进一步的,所述的气囊成组设置,每组内包括多个气囊,同组内的多个气囊沿水平方向均匀间隔布置形成气囊层。进一步的,所述高度调节组件还包括多个连接法兰,每个气囊的下端部和上端部均安装有一连接法兰,每个所述的连接法兰均沿水平方向设置,各连接法兰相互平行。进一步的,竖直方向内相邻的连接法兰之间采用多个连杆铰装连接,所述的连杆均匀间隔安装在连接法兰的外沿位置。进一步的,水平方向内相邻的连接法兰之间采用横梁一体连接。基于所述顶升系统的顶升方法:其顶升和降低包括如下步骤,步骤1:固定安装好的顶升系统,高度距离航空器顶升支点高度大于800mm时,同步充气顶层的气囊至0.4mpa,使顶层气囊升高至连杆具有张力的状态;步骤2:把底层的气囊层中的四个气囊充气至高度约300mm,此时没有外部负载,只考虑自重的情况下,实际充气压力不到0.1mpa,如果初试高度小于800mm可跳过第一步,直接操作第二步即可;步骤3:升高或者降低底层的气囊层中的四个气囊,此时气囊层可以发生转动,同时升高油缸使球面与航空器的球窝吻合,继续升高油缸直至安全阀自动打开,安全阀打开后油缸将保持静止,即停止上升;步骤4:底层的4个气囊应兼具单独充放气及互通功能,继步骤3后,打开第一层之间的互通功能,升高底层气囊层,使其压力达到1mpa,航空器开始被顶升;以此类推陆续升高第各个层气囊层至1mpa,直至达到救援高度要求;步骤5:下降过程中,保持底层气囊互通功能打开状态,油缸安全阀打开状态,先放气次底层的气囊层,逐层放气直至顶层,关闭油缸安全阀,回落油缸,最后放气底层气囊,完成收起。本发明的优点和积极效果是:1、本发明中,保留现有装置中的油缸配合适配器作为顶升力输出的终端,其采用顶升装置取代原有的三脚架机构,在确保油缸和适配可同步升降的基础上配置有一定范围的轴线角度调整能力,解决现有技术中顶升角度不可调整的问题。2、本发明中,将油缸固定在安装座内,固定方式采用球面接触,航空器的顶升过程近似与定点转动,球面接触保证油缸在顶升过中不受径向力;并在其外部安装多个多个耳板进行固定,即分散油缸顶升的反作用力。通过最下层没有连杆结构组合的气囊层,利用气压平衡原理使航空器顶升过程中(定点转动)随重心变化自动调整角度。3、本发明中,所述顶升装置包括高度调节组件和角度调节组件,高度调节组件用于调整油缸的水平高度的位置极限,角度调节组件用于调整油缸和适配器的轴线角度。4、本发明中,采用多个气囊沿纵向叠放作为高度调节组件和角度调节组件,在对每个气囊充气时,其发生膨胀进而实现高度的调整,除此之外,可通过设置不同数量的气囊,以及不同的充气量来实现高度极限的变化,进而适配不同型号的航空器。5、本发明中,由于气囊为柔性顶举件,其底部的受力面积是可根据充气量进行调整的,进而保证其底面和地面之间的接触面积。为提升顶升过程的稳定性,每层采用多个气囊均匀间隔布置形成气囊层,在和软质基面配合时由于其受力面积足够大,软质基面所受压强小,因此不会如现有顶升装置一样造成软质基面发生凹陷,有效防止顶升系统发生倾倒。6、本发明中,由于气囊为柔性顶举件,因此需配合其他高度调节组件连提升各气囊之间的刚性,防止其在顶升过程中发生坍塌。其中所用的连接法兰配合外沿制出的多个连杆铰装连接,可保证每个连接法兰相互平行,连接法兰形成骨架,连杆形成关节,气囊充气时,确保由次底层至顶层的气囊始终处于一个直线内。而底层的气囊之所以不安装连接法兰是将其作为转轴,通过对于底层的不同气囊充气量的变化来实现轴线角度的变化,使得顶层的气囊相对于竖直方向的基准线在一定范围内进行摆转。7、本发明中,竖直方向内的相邻气囊采用连杆铰装,水平方向内的气囊采用横梁一体连接,确保高度调节组件中的气囊膨胀只能实现高度位置的调整,水平位置和摆转角度均受到有效限制。8、本发明中,基于所述的顶升系统衍生出相应的顶升方法,该方法相较于传统的顶升装置,其操作更为简便,定位更加准确,顶升更为稳定快速。附图说明图1为本发明的结构示意图;图2为图1的俯视图;图3为顶升状态的结构示意图。具体实施方式下面结合实施例,对本发明进一步说明,下述实施例是说明性的,不是限定性的,不能以下述实施例来限定本发明的保护范围。一种航空器用顶升系统,包括一个油缸2,所述油缸的升降端安装有一适配器1,该油缸可控制适配器发生上下位移,本发明的创新在于,所述油缸的下方安装有顶升装置,该顶升装置用于将油缸和适配器同步上、下移动并在水平方向内调整适配器的轴线角度。本实施例中,所述油缸的下端部安装在一个安装座内,该安装座包括上下间隔设置的两个安装板3,所述的两个安装板平行间隔设置,两个安装板之间沿竖直方向安装有所述的油缸,所述油缸的活塞杆向上设置,其端部安装有所述的适配器,所述的两个安装板的外沿位置均匀间隔安装有多个耳板4,耳板上端和位于上方的安装板铰装,耳板下端和位于下方的安装板铰装,所述多个耳板均和两个安装板相互垂直,该两耳板远离安装板的端部通过安装组件5和顶升装置的安装固定。本实施例中,所述安装座和耳板采用活动安装的结构,两个安装板和耳板的连接位置均采用卸扣15销装配合。本实施例中,所述顶升装置包括高度调节组件和角度调节组件,其中高度调节组件用于调整油缸的水平高度,角度调节组件用于调整适配器水平方向内的角度。本实施例中,所述高度调节组件和角度调节组件均采用气囊8,多个气囊沿纵向叠放,位于底层的为角度调节组件,位于底层之上的多个气囊为高度调节组件。本实施例中,每个底层的气囊均安装在一个底板10内,所述底板的下端面平整制出。为方便顶升系统的移动和吊装,在底板内均匀间隔安装有多个吊耳11。相邻底板之间采用连接板13连接固定。本实施例中,所述的气囊成组设置,每组内包括多个气囊,同组内的多个气囊沿水平方向均匀间隔布置形成气囊层。本实施例中,所述高度调节组件还包括多个连接法兰9,每个气囊的下端部和上端部均安装有一连接法兰,每个所述的连接法兰均沿水平方向设置,各连接法兰相互平行。本实施例中,为提升气囊层拆装的便利性,竖直方向内相邻的连接法兰采用销轴6销装在制出的销孔内,可通过拆卸销轴去除或添加某一气囊层。本实施例中,竖直方向内相邻的连接法兰之间采用多个连杆7铰装连接,所述的连杆均匀间隔安装在连接法兰的外沿位置。本实施例中,水平方向内相邻的连接法兰之间采用横梁12一体连接。为提升横梁的强度,在竖直方向内相邻的两个横梁之间安装有一对拉带14,同一对拉带交叉设置分别由斜向对拉两个横梁的端部。实施例1:在实际应用中,所述的顶升系统采用2排,2列,12层共48个球形气囊的设计结构。竖向的12个球形气囊配置12个连接法兰,每个连接法兰均为方形,其四边中部一体制出所述的连杆,竖直方向内相邻的连杆采用销轴销装固定。底层的四个气囊两个一组,每组作为一个单元控制气压。次底层至顶层的11个气囊层,每个气囊层内的四个气囊为一组,每组作为一个单元控制气压,每个单元内出气囊外还需配置相应的管路,阀门,气泵,气压表等相关充气组件。该顶升系统的额定气压为1mpa,初始高度2m,最大顶升高度6.5m,最大允许轴线偏移角度7°额定载荷160t,占地面积3.4m×3.4m。本发明的使用过程是:本发明使用时包括如下步骤,(为方便描述对各气囊层进行标注,由底层至顶层分别采用1-12层进行划分。其中底层为第1层,顶层为第12层,之间的气囊层由2-11顺次递增。)步骤1:固定安装好的顶升球型气囊层高度距离航空器顶升支点高度大于800mm时,同步充气第12层至0.4mpa,使第12层气囊升高至连杆具有张力(预计高度450mm);步骤2:把第1层的四个气囊充气至高度约300mm,此时没有外部负载,只考虑自重的情况下,实际充气压力不到0.1mpa,如果初试高度小于800mm可跳过第一步,直接操作第二步即可;步骤3:升高或者降低第1层气囊层中的四个气囊(分别充气或者放气),此时气囊层可以发生转动,同时升高油缸使球面与球窝吻合,继续升高油缸直至安全阀自动打开(建议安全阀设置压力为1mpa),安全阀打开后油缸将保持静止,即停止上升;此过程油缸的油缸的上升速度是缓慢的,(上升速度3~10mm/s,操作方式:手动/电动);注意:此过程仅允许使用油缸上升动作使千斤顶球面与航空器球窝吻合,切勿使用气囊层上升操作此过程,气囊层上升速度太大,以免损坏航空器;步骤4:第1层4个气囊应兼具单独充放气及互通功能(四通的每条管线可以单独开合控制并可以互通)继步骤3后,打开第一层之间的互通功能,升高第12层气囊层,使其压力达到1mpa,航空器开始被顶升;以此类推陆续升高第109876.....2层气囊层至1mpa,直至达到救援高度要求;注意:此过程中第一层气囊层互通是一直保持开放状态;油缸安全阀门也一直是打开状态;步骤5:下降过程中,保持第1层气囊互通功能打开状态,油缸安全阀打开状态,先放气第2层,逐至34567.....12,关闭油缸安全阀,回落油缸,最后放气第1层气囊,完成收起。顶升高度对照表层数456789101112初试高度119012901390149015901690179018901990最大顶升高度311035604010446049104360581062606710顶升载荷对照表气压(mpa)0.20.30.40.50.60.70.80.91.0额定载荷天(t)3248648096112128144160本发明中,保留现有装置中的油缸配合适配器作为顶升力输出的终端,其采用顶升装置取代原有的三脚架机构,在确保油缸和适配可同步升降的基础上配置有一定范围的轴线角度调整能力,解决现有技术中顶升角度不可调整的问题。本发明中,将油缸固定在安装座内,固定方式采用球面接触,航空器的顶升过程近似与定点转动,球面接触保证油缸在顶升过中不受径向力;并在其外部安装多个多个耳板进行固定,即分散油缸顶升的反作用力。通过最下层没有连杆结构组合的气囊层,利用气压平衡原理使航空器顶升过程中(定点转动)随重心变化自动调整角度。本发明中,所述顶升装置包括高度调节组件和角度调节组件,高度调节组件用于调整油缸的水平高度的位置极限,角度调节组件用于调整油缸和适配器的轴线角度。本发明中,采用多个气囊沿纵向叠放作为高度调节组件和角度调节组件,在对每个气囊充气时,其发生膨胀进而实现高度的调整,除此之外,可通过设置不同数量的气囊,以及不同的充气量来实现高度极限的变化,进而适配不同型号的航空器。本发明中,由于气囊为柔性顶举件,其底部的受力面积是可根据充气量进行调整的,进而保证其底面和地面之间的接触面积。为提升顶升过程的稳定性,每层采用多个气囊均匀间隔布置形成气囊层,在和软质基面配合时由于其受力面积足够大,软质基面所受压强小,因此不会如现有顶升装置一样造成软质基面发生凹陷,有效防止顶升系统发生倾倒。本发明中,由于气囊为柔性顶举件,因此需配合其他高度调节组件连提升各气囊之间的刚性,防止其在顶升过程中发生坍塌。其中所用的连接法兰配合外沿制出的多个连杆铰装连接,可保证每个连接法兰相互平行,连接法兰形成骨架,连杆形成关节,气囊充气时,确保由次底层至顶层的气囊始终处于一个直线内。而底层的气囊之所以不安装连接法兰是将其作为转轴,通过对于底层的不同气囊充气量的变化来实现轴线角度的变化,使得顶层的气囊相对于竖直方向的基准线在一定范围内进行摆转。本发明中,竖直方向内的相邻气囊采用连杆铰装,水平方向内的气囊采用横梁一体连接,确保高度调节组件中的气囊膨胀只能实现高度位置的调整,水平位置和摆转角度均受到有效限制。本发明中,基于所述的顶升系统衍生出相应的顶升方法,该方法相较于传统的顶升装置,其操作更为简便,定位更加准确,顶升更为稳定快速。当前第1页12