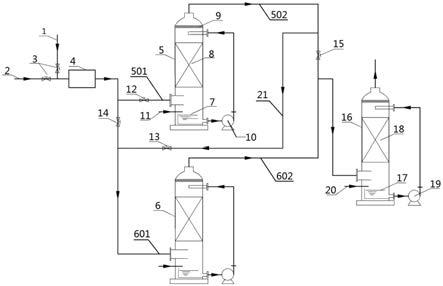
1.本实用新型属于玻璃生产尾气处理技术领域,尤其涉及一种脱除日用玻璃生产尾气中氮氧化物的装置。
背景技术:2.日用玻璃行业主要包括玻璃仪器制造业、日用玻璃制品及玻璃包装容器制造业、玻璃保温容器制造业。日用玻璃制造包括配合料制备、熔制、成型、退火、表面处理、检验和包装等工序。玻璃行业主要大气污染物为二氧化硫、氮氧化物和颗粒物。据测算,2018年,玻璃行业二氧化硫排放量9.83万吨,氮氧化物排放量14.4万吨,颗粒物排放量2.23万吨。由此可以看出氮氧化物在玻璃生产过程中占比较大。
3.日用玻璃行业现参考执行《工业炉窑大气污染物排放标准》(gb 9078-1996)和《大气污染物综合排放标准》(gb 16297-1996),现行标准部分污染物排放限值宽松,不利于促进行业技术进步和污染防治。《工业炉窑大气污染综合治理方案》(环大气(2019)56号)提出:日用玻璃、玻璃纤维等行业,应参照相关行业已出台的标准,全面加大污染治理力度;重点区域原则上按照颗粒物、so2、no
x
排放限值分别不高于30mg/m3、200mg/m3、300mg/m3实施改造,其中,日用玻璃no
x
排放限值不高于300mg/m3;己制定更严格地方排放标准的地区,执行地方排放标准。更严格的地方排放标准包括山东省出台的建材工业大气污染物排放标准(db 37-2373-2018),其中提出自2020年1月1日起,所有玻璃熔窑按照颗粒物、so2、no
x
排放限值分别不高于20mg/m3、100mg/m3、200mg/m3实施改造,重点区域按照不高于10mg/m3、50mg/m3、100mg/m3实施改造。此标准实施的情况下,日用玻璃行业由于生产过程中氮氧化物浓度波动较大,烟气温度较低,存在换火等排放特点,因此氮氧化物脱除技术亟需提升。
技术实现要素:4.有鉴于此,本实用新型提供一种脱除日用玻璃生产尾气中氮氧化物的装置,以解决目前玻璃生产尾气处理脱硝效率低,导致治理工艺与生产不匹配的技术问题。为了对披露的实施例的一些方面有一个基本的理解,下面给出了简单的概括。该概括部分不是泛泛评述,也不是要确定关键/重要组成元素或描绘这些实施例的保护范围。其唯一目的是用简单的形式呈现一些概念,以此作为后面的详细说明的序言。
5.本实用新型采用如下技术方案:
6.在一些可选的实施例中,提供一种脱除日用玻璃生产尾气中氮氧化物的装置,包括:原始组分调节器,用于调节生产工艺后烟气与初步脱硝后烟气的比例,并将调节后的混合尾气输送至氧化反应塔组;氧化反应塔组,与所述原始组分调节器的出气侧连接,用于使调节后的混合尾气与氧化剂接触,并将进行氧化反应后的尾气输送至吸收反应塔;吸收反应塔,与所述氧化反应塔组的出气侧连接,用于使进行氧化反应后的尾气与吸收剂接触,并将进行吸收反应后的尾气排出。
7.进一步的,所述氧化反应塔组包括:第一氧化反应塔;所述第一氧化反应塔通过第
一氧化进气管与所述原始组分调节器的出气侧连接,所述第一氧化反应塔通过第一氧化出气管与所述吸收反应塔的进气侧连接。
8.进一步的,所述氧化反应塔组还包括:第二氧化反应塔;所述第二氧化反应塔与所述第一氧化反应塔串联,或者,与所述第一氧化反应塔并联。
9.进一步的,所述第二氧化反应塔通过第二氧化进气管与所述原始组分调节器的出气侧连接,所述第二氧化反应塔通过第二氧化出气管与所述吸收反应塔的进气侧连接;所述第一氧化出气管通过串联管与所述第二氧化进气管连接,且所述串联管上设置串联阀门;所述第一氧化进气管上设置一塔进气阀门;所述第二氧化进气管上设置二塔进气阀门;所述第一氧化出气管上设置一塔出气阀门。
10.进一步的,所述原始组分调节器的进气侧分别与生产工艺后烟气输入管路及初步脱硝后烟气输入管路连接;所述生产工艺后烟气输入管路与所述初步脱硝后烟气输入管路上设置调节阀。
11.进一步的,所述第一氧化反应塔与所述第二氧化反应塔的配置相同,均包括:氧化剂循环储槽、氧化反应器、除雾器、氧化循环泵及补充氧化剂管路,所述氧化反应器通过管道分别与所述氧化循环泵和所述氧化剂循环储槽相连。
12.进一步的,所述第一氧化反应塔与所述第二氧化反应塔的烟气入口设置在所述氧化反应器的下方,烟气出口设置在所述除雾器的上方。
13.进一步的,所述吸收反应塔包括:吸收剂循环储槽、吸收反应器、吸收循环泵以及补充吸收剂管路,所述吸收反应器通过管道分别与所述吸收循环泵和所述吸收剂循环储槽相连。
14.进一步的,所述吸收剂循环储槽盛装的碱液为碳酸钠溶液或氢氧化钠溶液。
15.本实用新型所带来的有益效果:
16.1.利用多种不同氧化剂的氧化性调节尾气中的no和no2的比例,可根据实际情况调节氧化程度,达到氮氧化物高效脱除的目的;
17.2.本实用新型采用氧化吸收的方式,并配备原始组分调节器,可通过脱硝前后原始尾气调节进入装置的尾气氮氧化物浓度,并适用日用玻璃行业尾气波动变化幅度大的特点,稳定达标排放;
18.3.氮氧化物吸收采用碳酸钠或氢氧化钠溶液,反应产物为硝酸盐和亚硝酸盐,副产物具有一定的经济价值,实现尾气资源化处理,可以大大弥补系统运行成本,甚至可以产生盈利;
19.4.本实用新型具有90%以上的吸收效率,处理后的尾气可满足现行国家排放标准的要求。
附图说明
20.图1是本实用新型一种脱除日用玻璃生产尾气中氮氧化物的装置的结构示意图。
具体实施方式
21.以下描述和附图充分地展示出本发明的具体实施方案,以使本领域的技术人员能够实践它们。其他实施方案可以包括结构的、逻辑的、电气的、过程的以及其他的改变。实施
例仅代表可能的变化。除非明确要求,否则单独的部件和功能是可选的,并且操作的顺序可以变化。一些实施方案的部分和特征可以被包括在或替换其他实施方案的部分和特征。
22.如图1所示,在一些说明性的实施例中,本实用新型提供一种脱除日用玻璃生产尾气中氮氧化物的装置,包括:原始组分调节器4、氧化反应塔组、吸收反应塔16。
23.原始组分调节器4用于调节生产工艺后烟气与初步脱硝后烟气的比例,调节后的混合尾气输送至氧化反应塔组。日用玻璃生产过程中产生的尾气通过原始组分调节器4,在调节器内调整no
x
浓度高的原烟气和no
x
浓度低的初步处理后烟气至最合适浓度,而后进入氧化反应塔组。原始组分调节器4是一种调节不同组份比例并进行混合的设备,例如多组分比例调节器。
24.原始组分调节器4的进气侧分别与生产工艺后烟气输入管路1及初步脱硝后烟气输入管路2连接,且生产工艺后烟气输入管路1与初步脱硝后烟气输入管路2上设置调节阀3。含有高浓度氮氧化物的烟气由生产工艺后烟气输入管路1进入,含有低浓度氮氧化物的烟气由初步脱硝后烟气输入管路2进入,通过调节阀3调节后进入原始组分调节器4,经过充分混合,进入氧化反应塔组,便于对原始烟气进行调节,且便于与玻璃生产线进行对接。
25.氧化反应塔组,与原始组分调节器4的出气侧连接,用于使调节后的混合尾气与氧化剂接触,并将进行氧化反应后的尾气输送至吸收反应塔16。
26.氧化反应塔组包括:第一氧化反应塔5及第二氧化反应塔6。
27.第一氧化反应塔5通过第一氧化进气管501与原始组分调节器4的出气侧连接,第一氧化反应塔5通过第一氧化出气管502与吸收反应塔16的进气侧连接。第二氧化反应塔6通过第二氧化进气管601与原始组分调节器4的出气侧连接,第二氧化反应塔6通过第二氧化出气管602与吸收反应塔16的进气侧连接。
28.第一氧化出气管502通过串联管21与第二氧化进气管601连接,且串联管21上设置串联阀门13;第一氧化进气管501上设置一塔进气阀门12;第二氧化进气管601上设置二塔进气阀门14;第一氧化出气管502上设置一塔出气阀门15。
29.第二氧化反应塔6与第一氧化反应塔5串联,或者,与第一氧化反应塔5并联。第一氧化反应塔5与第二氧化反应塔6布置一致,两座反应塔可通过阀门调节串联与并联形式。具体形式如下:
30.当单独使用第一氧化反应塔5进行氧化反应时,开启一塔进气阀门12和一塔出气阀门15,关闭串联阀门13和二塔进气阀门14;
31.当第一氧化反应塔5与第二氧化反应塔6串联使用时,开启一塔进气阀门12和串联阀门13,关闭二塔进气阀门14和一塔出气阀门15;
32.当第一氧化反应塔5与第二氧化反应塔6并联使用时,开启一塔进气阀门12、二塔进气阀门14和一塔出气阀门15,关闭串联阀门13。
33.吸收反应塔16,与氧化反应塔组的出气侧连接,用于使进行氧化反应后的尾气与吸收剂接触,并将进行吸收反应后的尾气排出。
34.在氧化反应塔组内尾气与高效氧化剂接触反应,2台氧化反应塔顺序布置,可视尾气氧化情况选择一次氧化或二次氧化,在氧化剂的作用下尾气中部分no被氧化成no2使尾气中的no2浓度增加。调整后的尾气进入到吸收反应塔16,在氮氧化物吸收反应器内尾气与碱性溶液接触反应,反应生成硝酸盐和亚硝酸盐,吸收液的碱度可根据不同的吸收效率适
当调整,经过吸收反应后尾气中的90%以上的no
x
被脱除。
35.根据尾气中氮氧化物的浓度,经过一级或多级氧化和吸收后,尾气中氮氧化物浓度可达到国家要求的排放标准。以浓度为41-50%硝酸溶液氧化溶液、氢氧化钠溶液吸收为例,该工艺的主要化学反应式如下:
36.no+2hno3=3no2+h2o;
37.no+no2+2naoh=2nano2+h2o;
38.3no2+2naoh=2nano3+no+h2o。
39.本实用新型工艺所采用的氧化剂可以为硝酸、亚氯酸钠、双氧水等,碱性吸收液可以为氢氧化钠、碳酸钠、氨等碱性物质的水溶液。
40.第一氧化反应塔5与第二氧化反应塔6的配置相同,均包括:氧化剂循环储槽7、氧化反应器8、除雾器9、氧化循环泵10及补充氧化剂管路11。第一氧化反应塔5与第二氧化反应塔6的烟气入口设置在氧化反应器8的下方,烟气出口设置在除雾器9的上方。调节后的尾气进入反应塔,自下向上移动,在氧化反应器8与氧化剂接触,进行氧化反应,随后尾气经除雾器9除去细小液体颗粒由顶部排出。
41.氧化反应器8通过管道分别与氧化循环泵10和氧化剂循环储槽7相连,氧化循环泵10不断将氧化剂循环储槽7内的氧化剂输送至氧化反应器8,与烟气进行接触,从而构成氧化反应循环。新鲜氧化剂通过补充氧化剂管路11进入氧化剂循环储槽7,实现氧化剂的补充。
42.吸收反应塔16包括:吸收剂循环储槽17、吸收反应器18、吸收循环泵19以及补充吸收剂管路20。经过氧化反应后的尾气进入吸收反应塔16,自下至上移动,在吸收反应器18内与吸收剂接触,进行吸收反应,随后尾气经除雾器除去细小液体颗粒由顶部烟囱排出。吸收反应器18通过管道分别与吸收循环泵19和吸收剂循环储槽17相连,构成吸收反应循环。新鲜吸收剂的补充通过补充吸收剂管路20完成。
43.日用玻璃生产尾气分两个管道进入脱硝装置,两个管道是指生产工艺后烟气输入管路1与初步脱硝后烟气输入管路2,生产工艺后烟气输入管路1输送来自生产工艺后含有高浓度氮氧化物的烟气,初步脱硝后烟气输入管路2输送经过初步脱硝后含有低浓度氮氧化物的烟气,两个管道通过调节阀3,进入原始组分调节器4,经过充分混合,对照后续氧化和吸收能力,调整至适合的处理前氮氧化物浓度。
44.原始组分调节器4调整后的尾气从第一氧化反应塔5的下部进入塔内进行氧化反应,将尾气中部分no氧化为no2。反应塔内布置有氧化剂循环储槽7、氧化反应器8和除雾器9,其中氧化反应器8采用板式或填料吸收的形式,烟气入口设在氧化反应区下端,烟气出口设置在除雾器9上方,氧化剂通过氧化循环泵10连接氧化剂循环储槽7和氧化反应器8进行反应循环,氧化剂循环储槽7配备有氧化剂浓度测定仪,可根据测定仪给出的数据,补充新鲜氧化剂进入氧化剂循环储槽7控制循环溶液浓度,保证氧化效率。
45.氧化反应区域顺序布置2台氧化反应塔,通过可调节阀门控制尾气走向,可视尾气氧化情况选择一次氧化或二次氧化:开启一塔进气阀门12,关闭二塔进气阀门14,使尾气进行一次氧化;开启串联阀门13,使尾气进行二次氧化,二次氧化后的尾气随后进行高效吸收反应。第二氧化反应塔6与第一氧化反应塔5可串联进行二次进一步氧化反应,也可并联容纳更多尾气进行氧化反应,亦可单独使用。
46.经过氧化反应的尾气从吸收反应塔16下部进入塔内进行吸收反应,将尾气中部分no和no2吸收去除。反应塔内布置有吸收剂循环储槽17、吸收反应器18和除雾器,其中吸收反应器18采用板式或填料吸收的形式,烟气入口设在吸收反应区下端,烟气出口设置在除雾器上方,吸收剂通过吸收循环泵19连接吸收剂循环储槽17和吸收反应器18进行反应循环,吸收剂循环储槽17配备有吸收剂浓度测定仪,可根据测定仪给出的数据,补充新鲜吸收剂进入吸收剂循环储槽17控制循环溶液浓度,保证吸收效率。吸收反应塔16的出口设置在顶部除雾器上方,配备烟囱,尾气脱硝达标后排放。
47.上述实施例为本实用新型较佳的实施方式,但本实用新型的实施方式并不受上述实施例的限制,其他任何未背离本实用新型的精神实质与原理下所做的改变,修饰,替代,组合,简化,均应为等效的置换方式,都应包含在本实用新型的保护范围内。