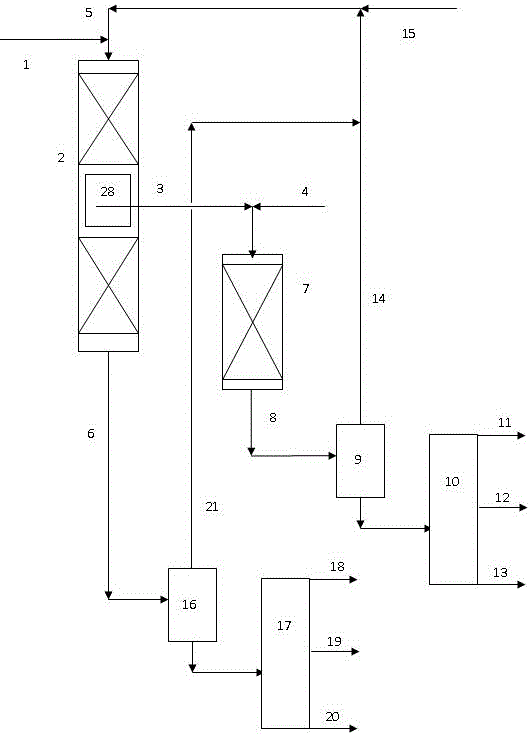
本发明属于石油炼制领域,具体涉及一种以渣油和lco为原料油灵活生产优质催化裂化原料的渣油加氢处理与加氢精制组合工艺。
背景技术:
:流化催化裂化(fcc)是重质油轻质化的重要手段之一,但是随着催化裂化加工原料的劣质化和重质化,其操作条件越来越苛刻,轻质产品收率和产品性质变差,而催化裂化原料加氢处理技术不仅可以除去硫、氮、金属等杂质的含量,还可改善进料的裂化性能,降低fcc操作苛刻度,改善产品分布,提高目的产品选择性,降低干气和焦炭产率,提高fcc装置的经济性,降低目的产品硫含量,减少再生烟气中sox及nox含量等。催化裂化轻循环油(lco)中有一定含量的硫和氮,均以有机化合物的形式存在,而且芳烃含量高,尤其是两环以上芳烃的含量高,通常lco直接循环回催化裂化装置内继续转化,或者进入加氢处理装置加氢后再进入催化裂化装置,或者进入其他装置加工或者直接作为产品。cn106701189a、cn106701190a、cn106701191a和cn102732314a公开了一种渣油加氢处理工艺中掺炼lco和/或重循环油的工艺技术,主要目的是生产优质催化裂化原料,或者让lco在渣油加氢处理装置与催化裂化装置间循环的组合加工技术,实现催化裂化装置的清洁生产,但是由于渣油与lco混合后直接加氢,lco的加氢深度不能有效控制,只能以混合加氢产物(催化裂化原料)的硫含量或者氮含量作为控制目标,不利于以lco生产优质汽油的有效控制。综上所述,对比现有的lco加氢技术和渣油加氢处理技术,通常都是lco直接掺炼至渣油加氢处理装置中进行加氢,混合加氢后得到的加氢渣油和加氢lco共同作为催化裂化装置的原料,即lco加氢后再返回催化裂化装置,由于不刻意控制lco的加氢深度,催化裂化汽油的质量并没有达到最好,而且没有反应物料耦合的组合加工技术。技术实现要素:针对现有技术的不足,本发明提供一种渣油加氢处理与加氢精制组合工艺。通过从加氢处理反应区中部设置的气液分离器中抽出部分反应气相物流,将所述的渣油原料油和lco原料油通过加氢处理和加氢精制的组合工艺生产优质催化裂化原料。本发明的一种渣油加氢处理与加氢精制组合工艺,包括如下步骤:a、渣油原料油首先在加氢处理条件下通过加氢处理反应区的上游保护剂和级配加氢处理催化剂床层,得到第一加氢处理物流,这部分反应物流分成两部分,其中一部分通过气液分离器进行分离,得到气相物流抽出加氢处理反应区;b、步骤a中剩余部分加氢处理物流与补充氢混合后,继续在加氢处理条件下通过加氢处理反应区的下游级配加氢处理催化剂床层,得到加氢处理反应区生成物流经过分离、分馏(或汽提)后得到加氢处理气体产品、加氢处理石脑油产品、加氢处理柴油和加氢处理重馏分;c、步骤a所得抽出加氢处理反应区的气相物流与lco混合后,在加氢精制条件下通过加氢精制反应器的加氢精制催化剂床层,得到加氢精制反应区生成物流经过分离、分馏(或汽提)后得到加氢精制气体产品、加氢精制石脑油产品、加氢精制柴油。根据本发明的渣油加氢处理与加氢精制组合工艺,其中,步骤b得到的加氢处理反应区生成物流和步骤c得到的加氢精制反应区生成物流混合后进行分离、分馏(或汽提),得到加氢气体产品、加氢石脑油产品、加氢柴油。即,步骤b和步骤c中所述的分离和分馏共用一套分离和分馏系统。步骤b和步骤c所得到高压富氢气体循环使用。产品质量、环保要求、工艺条件操作等的要求都对催化裂化装置的原料油性质进行了限制,尤其是硫含量的限制,而且由于原料油组成的不同,催化裂化产品的分布和性质也有较大的差别;研究表明:lco的芳烃加氢饱和深度对催化裂化汽油产品质量的影响较大,尤其是汽油中单环芳烃是高辛烷值组分,增加加氢lco中单环芳烃的含量即可增加催化裂化汽油的辛烷值,而抽出的加氢处理气相物流中含有一定浓度的硫化氢和氨,其抑制作用相当于降低了加氢催化剂的活性,而通过体积空速和反应温度的调节,刚好可以控制lco的加氢深度,即在满足硫含量的前提下将lco中的两环芳烃和多环芳烃加氢至单环芳烃,而不是加氢深度过度生成环烷烃,或者加氢深度不足生成两环芳烃,这样加氢处理后的产物再次进入到催化裂化装置时可以提高催化裂化汽油中芳烃的含量,从而提高催化裂化汽油的辛烷值。与现有技术相比较,本发明渣油加氢处理与加氢精制组合工艺的优点在于:1、本发明中,加氢处理反应区中包括至少两个级配加氢处理催化剂床层。通过设置在加氢预处理反应区床层中间的气液分离器将其中一部分加氢处理气相物料抽取步骤,即可实现对加氢处理物料股的有效分配,再使所得到的物料经过加氢组合工艺,从而可以生产不同规格的目的产品。而在现有技术中,加氢精制技术和加氢处理技术通常只能根据本技术来生产一种加氢工艺的目的产品。2、本发明通过在加氢处理反应区的催化剂床层中间设置气液分离器,将渣油原料经过加氢处理的加氢预处理气相物流抽取出加氢处理反应区,并将其与lco混合送入单独设置的加氢精制反应器进行加氢反应,由于抽出的气相物流中含有硫化氢和氨,不利于lco的加氢脱硫反应,但是可以通过调节体积空速和反应温度等反应条件来控制lco的加氢深度,即控制lco中两环芳烃和多环芳烃加氢饱和的深度,控制在尽量将两环芳烃好多环芳烃加氢至单环芳烃,这样将加氢后lco再次进行催化裂化时降低裂化反应难度或者提高催化裂化汽油中的芳烃含量,从而提高了催化裂化汽油的辛烷值;而对于加氢处理部分来说,因为抽出了气相部分含有加氢处理催化剂床层催化剂加氢脱硫和加氢脱氮反应生产的硫化氢和氨,抽出气相后的剩余物流与补充氢混合后相当于减少了下部加氢处理催化剂床层范围内的硫化氢分压和氨分压,也就是降低了对后续加氢处理催化剂活性中心的抑制,或者说提高了加氢处理催化剂的活性,降低了加氢处理操作的苛刻度。3、本发明中,加氢处理反应区加氢处理催化剂床层中间得到的抽出气相物流本身具有很高的温度和压力,其与换热后的lco混合后可以直接进入新设置的加氢精制反应器中进行反应,从而充分利用这股部分加氢处理气相物料所携带的热量,实现加氢处理反应器与加氢精制反应器的耦合操作。4、本发明中,加氢处理反应系统和加氢精制反应系统的操作压力相同,因此两个系统中的高压富氢气体可以使用一套氢气脱硫系统和一套氢气循环系统,若进一步两个系统共用一套分离、分馏(或汽提)系统,则可以大幅度节省设备投资和操作费用。附图说明图1为本发明的原则流程示意图。图2为本发明的另一原则流程示意图。其中:1-渣油原料油,2-加氢处理反应器,3-加氢处理抽出气相物流,4-lco原料油,5-加氢处理反应器循环氢,6-加氢处理反应器生成物流,7-加氢精制反应器,8-加氢精制反应器生成物流,9-加氢精制高压分离器,10-加氢精制分馏塔,11-加氢精制气体,12-加氢精制石脑油,13-加氢精制柴油,14-加氢精制高压分离器富氢气体,15-补充氢,16-加氢处理高压分离器,17-加氢处理分馏塔,18-加氢处理石脑油,19-加氢处理柴油,20-加氢处理重馏分油,21-加氢处理高压分离器富氢气体,22-混合高压分离器,23-混合分馏塔,24-混合加氢石脑油,25-混合加氢柴油,26-加氢处理重馏分油,27-混合高压分离器富氢气体,28-气液分离器。具体实施方式步骤a所述渣油原料的初馏点为200~450℃,终馏点为550~750℃。所述的渣油原料油可以是石油加工得到的常压渣油、减压渣油、焦化重油、脱沥青油、回炼油等中的一种,从煤得到的煤焦油、煤直接液化油、煤间接液化油、合成渣油、页岩油等中的一种,也可以是它们其中几种的混合油。步骤a和步骤b所述的保护剂、加氢处理催化剂均为常规的渣油加氢系列催化剂,主要包括加氢保护剂、加氢脱金属剂、加氢脱硫催化剂、加氢脱残炭催化剂等。加氢催化剂中加氢活性组分为co、mo、w、ni中的一种或几种,以氧化物计的重量含量为5%~70%,加氢催化剂的载体一般为氧化铝、无定型硅铝、氧化硅、氧化钛等,同时可以含有其它助剂,如p、si、b、ti、zr等。可以采用市售催化剂,也可以按本领域现有方法制备。加氢活性组分为氧化态的催化剂,在使用之前进行常规的硫化处理,使加氢活性组分转化为硫化态。商业加氢催化剂主要有,如抚顺石油化工研究院(fripp)研制开发的fzc-1系列保护剂、fzc-2系列脱金属催化剂、fzc-3系列脱硫催化剂、fzc-4系列脱残炭催化剂等加氢催化剂,ifp公司的hmc945、hmc841等加氢催化剂,uop公司开发的rf系列催化剂和r系列催化剂,akzo公司的kfr系列参加,axen公司开发的ht系列催化剂和haldortopsoe公司开发的tk系列催化剂等加氢催化剂步骤。以原料油和氢气混合物流动方向计,催化剂级配装填的原则为,粒度由大到小,催化剂活性由低到高。步骤a所述的操作条件可采用常规的操作条件,一般为反应压力5.0mpa~19.0mpa,反应温度为300℃~450℃,液时体积空速0.05h-1~5.0h-1,氢油体积比为100:1~2000:1。步骤a中所述第一加氢处理反应区可以设置一台反应器,也可以设置多台反应器,如2~8台。步骤a中所述抽出的部分反应物流时对应催化剂位置为加氢脱金属催化剂和加氢脱残炭催化剂床层之间的任意位置,即可以为加氢脱金属催化剂和加氢脱硫催化剂相连部位,可以是加氢脱硫催化剂床层内部,也可以是加氢脱硫催化剂和加氢脱残炭催化剂相连部位。步骤a中所述抽出的气相物流占加氢处理反应区入口氢气量的体积百分比为5~90wt%,优选为10~50wt%。步骤b所述的操作条件可采用常规的操作条件,一般为反应压力5.0mpa~19.0mpa,反应温度为300℃~450℃,液时体积空速0.05h-1~5.0h-1,氢油体积比为100:1~2000:1。步骤b中所述的分离通常包括为加氢处理高压分离器和低压分离器分离两部分。其中高压分离器分离得到加氢处理高压富氢气体和液体,高压分离器分离得到的液体进入低压分离器。低压分离器将高压液体产物分离得到富烃气体和低压液体产物。富烃气体经分离得到需要的加氢处理气体产物。步骤b中所述的分馏(或汽提)在加氢处理分馏塔(或汽提塔)系统中进行。低压液体产物在分馏塔中分馏得到加氢处理石脑油产品、加氢处理柴油和加氢处理重馏分。步骤c所述lco原料为催化裂化装置的轻循环油,其初馏点为100~200℃,终馏点为320~400℃。所述的lco原料油中也可以掺混一些焦化柴油、乙烯裂解焦油、煤焦油等芳烃含量高的柴油馏分中的一种或几种。步骤c所述的加氢精制催化剂均为常规的加氢精制催化剂。一般以ⅵb族和/或第ⅷ族金属为活性组分,以氧化铝或含硅氧化铝为载体,第ⅵb族金属一般为mo和/或w,第ⅷ族金属一般为co和/或ni。以催化剂的重量计,第ⅵb族金属含量以氧化物计为10wt%~35wt%,第ⅷ族金属含量以氧化物计为3wt%~15wt%,其性质如下:比表面为100~650m2/g,孔容为0.15~0.6ml/g。主要的催化剂有抚顺石油化工研究院研制开发的3936、ff-14、ff-16、ff-24、ff-26、ff-36、ff-56、fhuds-5、fhuds-7等加氢精制催化剂,也可以是国内外催化剂公司开发的功能类似催化剂,如uop公司的hc-k、hc-p,topsoe公司的tk-555、tk-565催化剂,和akzo公司的kf-847、kf-848等。操作条件可采用常规的操作条件,一般为反应压力3.0mpa~19.0mpa,反应温度为260℃~450℃,优选为280℃~410℃,液时体积空速0.2h-1~6.0h-1,氢油体积比为100:1~2000:1。步骤c中所述的分离加氢精制高压分离器和低压分离器内进行。其中加氢精制高压分离器分离得到加氢精制高压富氢气体和液体,高压分离器分离得到的液体进入低压分离器。低压分离器将高压液体产物分离得到富烃气体和低压液体产物。富烃气体经分离得到需要的加氢精制气体产物。步骤c中所述的分馏(或汽提)在加氢精制分馏塔(或汽提塔)系统中进行。低压液体产物在分馏塔中分馏得到加氢精制石脑油产品、加氢精制柴油。步骤b和步骤c中所述的加氢处理气体产品和加氢精制气体产品可以单独作为产品,也可以混合为混合气体产品。步骤b和步骤c中中所述的加氢处理石脑油产品和加氢精制石脑油产品可以单独作为产品,也可以混合为混合石脑油产品。步骤b所述的加氢处理柴油可以单独作为产品,也可以和步骤c中的加氢精制柴油混合作为催化裂化装置的原料油。步骤b所述的加氢处理重馏分作为催化裂化装置的原料油。步骤b和步骤c中所述的分离也可以在混合高压分离器和混合低压分离器内进行,即两个反应器的生成物流混合进入同一个高压分离器和同一个低压分离器。其中混合高压分离器分离得到混合高压富氢气体和混合液体,混合高压分离器分离得到的混合液体进入混合低压分离器。混合低压分离器将高压液体产物分离得到混合富烃气体和混合低压液体产物。混合富烃气体经分离得到需要的混合气体产物。混合高压富氢气体可以直接作为循环氢使用,也可以选择通过循环氢脱硫系统脱除硫化氢后再循环使用。步骤b和步骤c中所述的分馏(或汽提)在混合分馏塔(或混合汽提塔)系统中进行。混合低压液体产物在混合分馏塔中分馏得到混合加氢石脑油产品、混合加氢柴油和加氢重馏分油。本发明中,所述加氢精制反应器内的加氢精制过程包括依次进行的两个反应阶段,第一反应阶段在含有加氢精制催化剂的催化剂床层a内进行,第二反应阶段在含有加氢精制催化剂的催化剂床层b内进行。优选地,本发明中还可以包括将lco原料油切割为轻馏分和重馏分的过程,所述切割的温度为245~300℃。则所述加氢精制的具体过程为,所述重馏分与步骤a中抽出的第一加氢处理气相物流混合后通过催化剂床层a,催化剂床层a所得加氢精制物流与所述lco轻馏分混合后通过催化剂床层b。进一步地,加氢精制反应器中第二反应阶段的反应温度y2低于第一反应阶段的反应温度y1,优选地y2比y1低5-20℃。lco原料油切割所得lco重馏分中以多环芳烃为主,其经过更多的加氢精制催化剂反应,可以达到控制芳烃加氢深度的目的,而lco轻馏分中双环芳烃经过较少的加氢精制催化剂反应,可以与lco重馏分同时达到控制芳烃加氢深度的目的,即加氢精制后的lco满足硫含量要求的同时双环芳烃和多环芳烃均适度加氢至单环芳烃,其进一步催化裂化后可以满足硫含量要求的催化裂化汽油,而且可以提高汽油的辛烷值。此外,加氢精制反应器内催化剂床层b在低于催化剂床层a的温度下进行操作,也有利于双环芳烃加氢饱和转化为单环芳烃反应的进行。本发明中,所述的催化剂床层a和催化剂床层b可以设置在一个加氢精制反应器内,也可以分别设置在两个以上的加氢精制反应器内。本发明中优选采用第一种方式。本发明中,在加氢处理反应区中,所述“上游”与“下游”是指按照反应物料的接触顺序来划分的,先与反应物料接触的催化剂床层为“上游”,之后再与反应物料接触的催化剂床层则位于“下游”。结合图1,本发明的方法具体如下:渣油原料油1首先与循环氢5混合进入加氢处理反应器2,经过第一加氢处理催化剂床层的反应物流中抽出加氢处理抽出物流3,抽出物流3后的物流与补充氢混合后继续进入下部的加氢处理催化剂床层,抽出的加氢处理抽出物流3与lco原料油4混合后进入加氢精制反应器7,通过加氢精制催化剂床层的生成物流8进入加氢精制高压分离器9中进行气液分离,分离得到的液体进入加氢精制分馏塔10中分馏得到加氢精制气体11、加氢精制石脑油12和加氢精制柴油13、加氢处理反应器生成物流6进入加氢处理高压分离器16中进行气液分离,分离得到的液体进入加氢处理分馏塔17中分馏得到加氢处理石脑油18、加氢处理柴油19、加氢处理重馏分20、加氢精制高压分离器9分离得到的加氢精制富氢气体14与加氢处理高压分离器16分离得到的加氢处理富氢气体21混合后经循环氢压缩机增压后进一步与补充氢15混合作为循环氢。下面通过实施例说明本发明方案和效果。实施例1-4使用fripp研制开发和生产的保护剂、脱金属催化剂、脱硫催化剂、脱残炭催化剂组合的fzc系列催化剂体系进行了加氢处理试验研究;使用fripp研制开发和生产的fhuds-5加氢精制催化剂进行了加氢精制试验研究。表1渣油原料油的主要性质渣油1渣油2lco密度,g/cm30.9250.9480.932馏分范围,℃320~650450~750156~370硫含量,wt%3.53.01.3氮含量,wt%0.270.210.09残炭,wt%12.010.1—ni+v含量,µg/g10588—芳烃含量,wt%——91.2表2工艺条件续表2工艺条件表3试验结果其中lco轻馏分与重馏分的切割温度为270℃。由实施例可以看出,采用本发明的渣油加氢处理与加氢精制组合工艺,通过从加氢处理反应器内抽出一部分气相反应物流,抽出气相物流与lco混合加氢精制生产优质催化裂化原料,抽出气相物流后的剩余加氢理物流继续加氢处理生产优质石脑油、加氢柴油和加氢重馏分的目的,提供优质催化裂化原料,生产方式灵活。当前第1页12