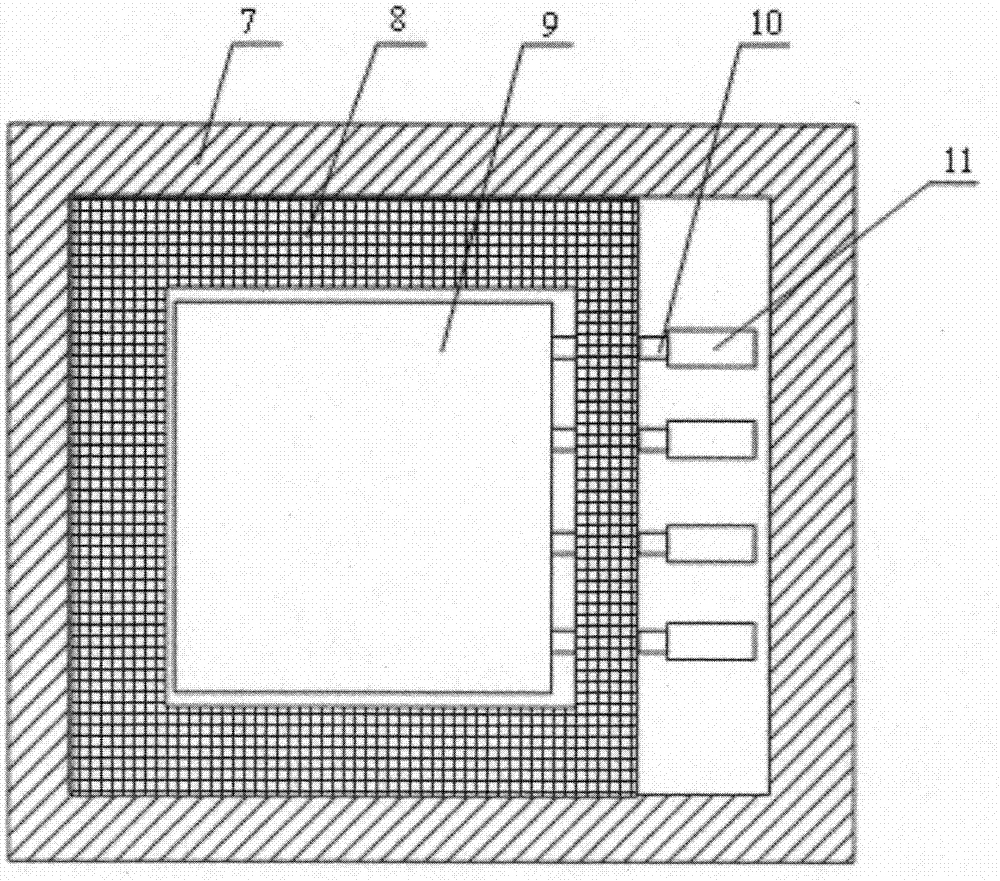
(一)
技术领域:
本发明属于半导体(mems)制造领域,涉及阳极键合方法,尤其涉及一种硅-玻璃键合面区域存在有高压敏感结构(如pn结)时,能使这些结构避开强电场破坏的阳极键合方法,以实现键合面区域带有高压敏感结构的mems器件在键合时的电学性能保护。(二)
背景技术:
:阳极键合在mems
技术领域:
中,主要应用于玻璃与硅的表面键合,硅-玻璃阳极键合的基本原理是:将300~1500v直流电源正极接硅片,负极接玻璃片,由于玻璃在一定高温下的性能类似于电解质,而硅片在温度升高到300~400℃时,电阻率将因本征激发而降至0.1ω·m,此时玻璃中的导电粒子(如na+)在外电场作用下漂移到负电极的玻璃表面,而在紧邻硅片的玻璃表面留下负电荷,由于na+的漂移使电路中产生电流流动,紧邻硅片的玻璃表面会形成一层极薄的宽度约为几微米的空间电荷区(或称耗尽层)。由于耗尽层带负电荷,硅片带正电荷,所以硅片与玻璃之间存在着较大的静电吸引力,使两者紧密接触,并在键合面发生物理化学反应,形成牢固结合的si-o共价键,将硅与玻璃界面牢固地连接在一起。根据这一基本原理,一般的阳极键合中,键合面区域n型硅上不适合存在p掺杂的电阻条,原因在于:p掺杂的电阻条与n型硅衬底构成一个pn结,在阳极键合过程中键合电流通过硅-玻璃键合面时,高达300~1500v的键合电压容易将键合面区域的pn结反向击穿,导致其漏电,破坏了mems器件上的电路,影响器件 的性能。因此,针对上述现有技术中存在的问题,有必要提供一种在硅-玻璃键合面区域存在有高压敏感结构(如pn结)时,能使这些结构避开强电场破坏的阳极键合方法,以实现键合面区域带有高压敏感结构的mems器件在键合时的电学性能保护。(三)技术实现要素:本发明的目的在于:提供一种硅基上多晶硅与玻璃的阳极键合方法,这种方法特别适用于当硅-玻璃键合面区域存在有高压敏感结构(如pn结)时,使键合电流在阳极键合过程中不通过这些结构,以实现mems器件的电学性能保护。为实现上述目的,本发明采用如下技术方案:一种硅基上多晶硅与玻璃的阳极键合方法,所述方法按如下步骤进行:(1)在硅衬底面上沉积一层绝缘层,所述绝缘层的材料选自sio2、si3n4或sic;(2)以光刻胶作掩膜,对绝缘层进行刻蚀,将硅衬底面与多晶硅将要连通的区域暴露出来形成开槽区;(3)在开设有开槽区的硅衬底面的绝缘层上沉积一层多晶硅,多晶硅在所述的开槽区与硅基导通;(4)所述的多晶硅与玻璃进行阳极键合。本发明硅基上多晶硅与玻璃的阳极键合方法,步骤(1)中绝缘层的沉积可采用下列方法之一:①采用等离子体增强型化学气相沉积法(pecvd)在硅衬底面 上沉积绝缘层;②采用低压化学气相沉积(lpcvd)工艺沉积薄膜的方法;所述绝缘层的厚度为0.5~1μm;所述绝缘层覆盖硅衬底以保证高压敏感区(如pn结区域)与键合区域之间的绝缘性。本发明步骤(2)中所述对绝缘层进行刻蚀可采用rie刻蚀(reactionionetching,反应离子刻蚀)或湿法腐蚀;所述绝缘层的开槽区域要尽量均匀分布,且面积要尽量大,还有需要注意的是,开槽的位置要尽量远离高压敏感区域,对于不同的器件可以按不同的结构和性能要求选择不同的开槽位置,本发明并没有对开槽的位置进行限制,只要利用沉积绝缘层并光刻腐蚀开槽,并沉积多晶硅将其与硅衬底导通来实现多晶硅与玻璃的阳极键合,则其就位于本发明的保护范围内。本发明步骤(3)中多晶硅的沉积过程可采用等离子体增强型化学气相沉积法进行;硅衬底面的绝缘层上沉积的多晶硅的非开槽区厚度为2~4μm,优选为3μm。本发明所述硅基上多晶硅与玻璃的阳极键合方法,当硅基上与玻璃键合面区域存在高压敏感结构,如pn结时,优选使用本发明方法,用本方法进行硅基上多晶硅与玻璃的阳极键合,使键合电流在阳极键合过程中不通过这些结构,以实现mems器件的电学性能保护。本发明所述的硅基可以是n或p型硅衬底。本发明步骤(4)中,阳极键合的工艺参数为:电压300~1000v,电流15~25ma,温度300~400℃,压力2000~3000n,时间5~20min;优选阳极键合的工艺参数为:电压450~1000v,电流20~25ma,温度350~380℃,压力2500~3000n,时间10~20min。本发明硅基绝缘层上多晶硅与玻璃的阳极键合方法可应用于圆片级封装、芯片级封装或系统级封装;需要注意的是,绝缘层腐蚀的区域需要尽量满足下述条件:(a)尽量远离电路的高压敏感区域,避免大电压(电流)破坏器件的电学性能;(b)尽量均匀分布以保证键合电压均匀分布;(c)面积要尽量大,以保证电流能顺利从硅基通向多晶硅;(d)在保证满足器件结构与性能要求的前提下,尽量不增大器件的体积,尽量减少版图的数量。在应用于圆片级封装中时,优选绝缘层的开槽区域在分片槽位置,这样做很好地满足了以上四个条件,任何其它能满足上述四点要求的硅基-多晶硅的连通区域分布都可采用,本领域的技术人员也可按实际情况对上述条件进行取舍。与现有技术相比,本发明阳极键合方法具备以下优势:一般的硅-玻璃键合过程中的高键合电压容易将键合面区域的高压敏感结构(如pn结)击穿,导致键合以后器件的电学性能遭到破坏。本方法巧妙地利用绝缘层将高压敏感区域与键合面隔离,通过腐蚀开槽并沉积多晶硅与硅基导通,使键合时电流直接从硅基通到多晶硅,避开了硅基上的高压敏感结构(如pn结),最终实现多晶硅与玻璃的阳极键合。并且,通过键合电流图以及显微镜下观察可知这种多晶硅-玻璃阳极键合仍然能保证接近硅-玻璃的键合强度。另一方面,利用绝缘层将键合玻璃与电路隔开可以保证电路在工艺过程中不受玻璃中na+等金属离子污染。(四)附图说明图1是本发明硅基上多晶硅与玻璃阳极键合的剖面示意图;图2是实施例1、实施例2或对比例中的器件结构俯视图;图3(a)~3(f)是实施例1或实施例2中阳极键合的工艺流程剖面示意图;图3(a)是沉积绝缘层的示意图;图3(b)是刻蚀绝缘层的示意图;图3(c)是沉积多晶硅的示意图;图3(d)是刻蚀管脚区域的示意图;图3(e)是多晶硅与玻璃阳极键合的示意图;图3(f)是划片的示意图;图4是实施例1键合电流图;图5是实施例1键合面显微照片;图6是实施例2键合面显微照片;图7是对比例硅-玻璃阳极键合的剖面示意图;附图中各数字标记的含义为:1-键合玻璃,2-多晶硅,3-绝缘层,4-高压敏感结构,5-硅衬底,6-电流方向,7-分片槽,8-键合区,9-工作区,10-浓硼区(实施例1或对比例)/浓磷区(实施例2),11-管脚,12-pn结。(五)具体实施方式下面通过具体实施例对本发明作进一步说明,但本发明的保护范围并不仅限于此。实施例1一种基于n型硅衬底,用浓硼作导线连接管脚并且阳极键合区域覆盖了 浓硼区域情况下的器件,如图2所示。由于键合区域存在着多个pn结,若直接采用硅-玻璃的阳极键合,很可能导致pn结被击穿,影响器件的电学性能。采用本发明方法则能保护键合区域的pn结,保护器件的电学性能。图3(a)~3(f)示出了上述情况下为了避免pn结区域存在大电压(电流)所使用的阳极键合方法,具体过程如下:(1)如图3(a)所示,在硅衬底5上pecvd生长一层绝缘层3;所述硅衬底为n型硅衬底;所述绝缘层为si3n4绝缘层,厚度为1μm;pecvd工艺参数:温度365℃,气体流量sih4∶n2∶nh3=10/100/500,压力2torr,高频300w,速率时间36min。(2)如图3(b)所示,旋转涂抹8μm厚4620光刻胶作掩膜光刻分片槽区域,rie刻蚀si3n4绝缘层至硅衬底;rie工艺参数:气体流量cf4/rf=40/200,压力3pa,速率时间14min。本实施例中,选择分片槽区域来作为绝缘层的腐蚀区域(硅基-多晶硅的连通区域),有以下几个优点:(a)分片槽位置与器件pn结距离较远,能避免键合时的大电压(电流)破坏这些pn结,影响器件电学性能;(b)分片槽位置在圆片中均匀分布,保证键合电压均匀分布;(c)分片槽位置面积足够大,以保证电流能顺利从硅基通向多晶硅;(d)选用分片槽位置作为硅基-多晶硅的连通区域,能在保证满足器件结构与性能要求的前提下,尽量不增大器件的体积,尽量减少版图的数量。(3)如图3(c)所示,pecvd生长一层多晶硅2,所述多晶硅的厚度为3μm;pecvd工艺参数:温度365℃,气体流量sih4∶n2=30/1000,压力 2.4torr,高频350w,速率时间30min。(4)如图3(d)所示,旋转涂抹8μm的az4620光刻胶作掩膜光刻管脚11区域,依次刻蚀多晶硅和si3n4绝缘层;所述的刻蚀工艺采用rie;rie工艺参数:气体流量cf4/rf=60/200,压力3pa,时间28min。(5)如图3(e)所示,多晶硅与玻璃阳极键合。阳极键合工艺采用如下工艺参数:电压(v)电流(ma)温度(℃)压力(n)时间(min)45020360240020从图4,图5可以观察到:一方面,多晶硅与玻璃阳极键合已经完全成功,且具有较好的键合强度,另一方面,从图4中电流曲线可以看出,电流是通过硅-多晶硅-玻璃导通,而并非通过硅-中间层(绝缘层)-玻璃导通。(6)如图3(f)所示,划片以实现单个芯片的封装。划片分两次完成,第一次划片,去除管脚上方玻璃;第二次划片,划去分片槽中结构,分离单个芯片并完成封装。实施例2一种基于p型硅衬底,用浓磷作导线连接管脚并且阳极键合区域覆盖了浓磷区域情况下的器件,如图2所示。与实施例1相同,键合区域同样存在着多个pn结,若直接采用硅-玻璃的阳极键合,很可能导致pn结被击穿,影响器件的电学性能。采用本发明方法则能保护键合区域的pn结,保护器件的电学性能。图3(a)~3(f)示出了上述情况下为了避免pn结区域存在大电压(电 流)所使用的阳极键合方法,具体过程如下:(1)如图3(a)所示,在硅衬底上pecvd生长一层绝缘层;所述硅衬底为p型硅衬底;所述绝缘层为sio2绝缘层,厚度为1μm;pecvd工艺参数:温度365℃,气体流量sih4∶n2∶no2=9/900/900,压力2torr,高频300w,速率时间29min。(2)如图3(b)所示,旋转涂抹8μm厚4620光刻胶作掩膜光刻分片槽区域,rie刻蚀sio2至硅衬底;rie工艺参数:气体流量cf4/rf=40/300,压力3pa,速率时间18min。本实施例中,选择分片槽区域来作为绝缘层的腐蚀区域(硅基-多晶硅的连通区域),有以下几个优点:(a)分片槽位置与器件pn结距离较远,能避免键合时的大电压(电流)破坏这些pn结,影响器件电学性能;(b)分片槽位置在圆片中均匀分布,保证键合电压均匀分布;(c)分片槽位置面积足够大,以保证电流能顺利从硅基通向多晶硅;(d)选用分片槽位置作为硅基-多晶硅的连通区域,能在保证满足器件结构与性能要求的前提下,尽量不增大器件的体积,尽量减少版图的数量。(3)如图3(c)所示,pecvd生长一层多晶硅;所述多晶硅的厚度为2μm;pecvd工艺参数:温度365℃,气体流量sih4∶n2=30/1000,压力2.4torr,高频350w,速率时间20min。(4)如图3(d)所示,旋转涂抹8μm的az4620光刻胶作掩膜光刻管脚区域,依次刻蚀多晶硅和sio2绝缘层;所述的刻蚀工艺采用rie;rie工艺参数:气体流量cf4/rf=60/200,压力3pa,时间25nin。(5)如图3(e)所示,多晶硅与玻璃阳极键合。阳极键合工艺采用如下工艺参数:电压(v)电流(ma)温度(℃)压力(n)时间(min)45020360240020从图6可以观察到:多晶硅与玻璃阳极键合已经完全成功,且具有较好的键合强度。(6)如图3(f)所示,划片以实现单个芯片的封装。划片分两次完成,第一次划片,去除管脚上方玻璃;第二次划片,划去分片槽中结构,分离单个芯片并完成封装。对比例:一种基于n型硅衬底,用浓硼作导线连接管脚并且阳极键合区域覆盖了浓硼区域情况下的器件,如图2所示。键合区域存在着多个pn结,这里直接采用硅-玻璃的阳极键合。图7中示出了直接采用硅-玻璃阳极键合方案在键合时的电流方向,电流方向沿n型硅(n)-浓硼(p)-玻璃,键合过程中硅和玻璃的电阻很小,可以看成一个等势体,阳极键合过程中的大电压直接加在键合面上,将图中pn结方向击穿,导致封装以后加载到管脚上的电流直接通过浓硼流向硅衬底,使器件产生漏电现象。现有的阳极键合技术比较成熟,是相关领域技术人员熟知的一门技术,但它的一个缺点是键合时需要很大的电压,而且主要集中在键合区域表面,因此设计时键合区域一般不宜存在高电压敏感结构(比方说pn结),即使不得不存在高电压敏感结构的话一般会采取其他封装方式。然而本专利通过多晶硅作为中间导通层,直接将加在硅衬底上的电流 “引”到多晶硅上,通过利用硅-多晶硅-玻璃的电流方向来避免键合区域的高电压敏感结构遭到破坏,保护了整个电路的电学性能,这种阳极键合封装方法可以用于圆片级封装,也可以用于芯片级封装。当前第1页12