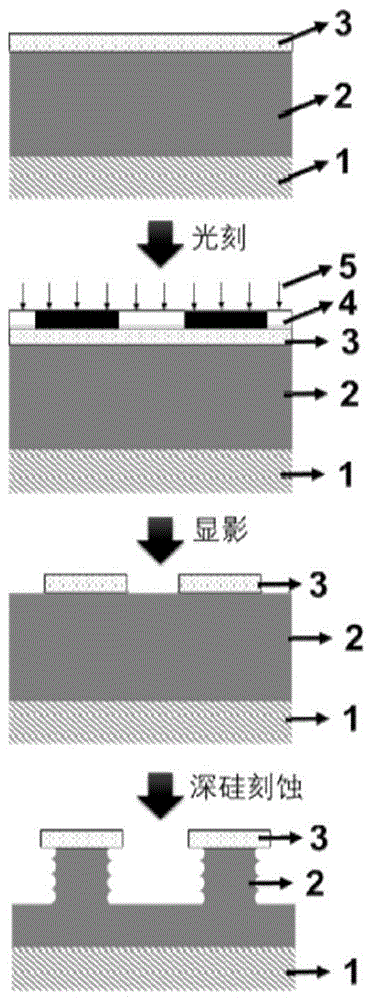
本发明属于微纳米加工领域,具体而言,涉及一种具有超双疏性的复合凹角微米结构的制备方法。
背景技术:
:超双疏表面由于其特殊的表面浸润特性,在抗结冰、水油分离、生物医药器件及自清洁表面等方面有着巨大的应用前景。相较于较高表面能的水,低表面能液体颇易于表面发生浸润。于是,超疏油特性的实现是获得超双疏表面的主要难点。据现有研究表明,表面构建特定的微纳米凹角结构,利用向上的拉普拉斯力将液滴稳定在具有空气层的cassie态,令低表面能液体也可在其表面不浸润,是获得超双疏表面的重要途径。如专利cn105220185a和cn105216295a等通过制备t型凹角结构获得了超双疏表面,而专利cn102180016a制备多层沟槽凹角结构制得了超双疏表面,然而这两种单独的凹角结构将低表面能液滴稳定于cassie态的能力有限,所提供的超疏油性能仍有待提升。因此,为获得更加优化的稳定的超疏油性能,一种复合凹角结构及其制备方法亟待发展。如专利cn108466015a通过制备微纳米复合凹角结构获得了性能优良的超双疏表面,但该纳米结构的凹角结构特征不明显,且纳米级结构的耐磨性较差,影响其实际应用潜力。综上所述,简单高效地制备具有优异超双疏性且耐磨性良好的表面仍是一个重要课题。技术实现要素:针对现有技术不足,本发明的目的是提供一种具有超双疏性的复合凹角微米结构的制备方法;即利用光刻与深硅刻蚀技术,结合选择性刻蚀,在表面形成t型多层沟槽复合凹角纯微米结构,提供优化的超双疏性能与耐磨性能。为实现该目的,本发明的具体技术方案是:一种具有超双疏性的复合凹角微米结构的制备方法,其特征在于,具体制备步骤如下:a)在衬底表面蒸镀硅层;b)在硅层表面旋涂光刻胶层,进行预烘固化;c)以紫外光透过图案化掩模板的镂空部分至光刻胶,曝光后将掩模板图案转移至光刻胶上;d)置于显影液中,曝光的光刻胶被溶解,形成光刻胶的微柱阵列;e)以光刻胶微柱阵列为刻蚀掩模,利用深硅刻蚀工艺将结构传递至硅层,获得周期性的沟槽结构,最终获得t型多层沟槽复合微米结构;f)在t型多层沟槽复合微米结构外部包裹sio2层,对t型多层沟槽复合微米结构表面进行防粘处理,获得具备超双疏性能的表面。优选步骤a)中所述衬底为玻璃或金属;其中优选金属为铁、镍或铜;优选所述硅层厚度为3-5微米。衬底可以是但不限于玻璃或金属,也可以直接用硅。优选步骤b)中所述光刻胶为az5214光刻胶或s1813光刻胶;光刻掩模版为方形阵列图案。优选步骤b)中所述光刻胶层厚度为0.5-1.5微米;旋涂的转速为3000-6000转/分钟,旋涂时间为40-60s;预烘固化的温度为90-120℃,预烘固化的时间为1-3min。优选步骤c)中所述紫外光的光强为20-50mj/cm2,曝光时间为2-10s。优选步骤d)中所述显影液为az300mif显影液,显影时间为20-50s。优选步骤e)中所述深硅刻蚀工艺的参数为:每个循环的钝化(优选每个循环c4f8气体钝化)时间为1-2s,刻蚀时间为2-4s;每个循环刻蚀高度为0.5-1微米;刻蚀循环周期为3-15圈。优选步骤e)中所述t型多层凹槽复合微米结构的t型顶部“帽子”厚度为0.5-1.5微米;顶部“帽子”直径为3-50微米;顶部直径与下层柱子直径差为0.5-1.5微米;下层柱子高度为3-30微米。优选步骤f)中包裹sio2层的方法为等离子体增强化学气相沉积技术;包裹的sio2层厚度为20-40nm。优选步骤f)中所述的防粘处理为:在真空系统中,以全氟烷基氯硅烷蒸汽处理,在85-100℃氛围中静置2-4小时使其挥发至样品表面从而完成表面改性。有益效果:与现有技术相比,本发明的复合双重凹角结构对低表面能液体可提供更稳定的cassie态,从而提供优异的超双疏性能,相较于纳米结构与微纳米复合结构,纯微米结构可提供更好的耐磨性能。另外,制备工艺简单,适合批量生产,在国防、工业生产以及日常生活等领域的自清洁表面具有广泛的应用前景。附图说明图1是本发明中一种t型多层沟槽复合凹角微米结构的制备流程示意图;其中1-衬底,2-硅层,3-光刻胶层,4-光刻掩模板,5-紫外光;图2是实施例1-3中所制备t型多层沟槽复合凹角微米结构的sem平面图;其中(a)代表的是实施例1,(b)代表实施例2,(c)代表实施例3;(d)代表实施例4;图3是本发明实施例1中所制备t型多层沟槽复合凹角微米结构的sem截面图。具体实施方式以下结合附图说明对本发明的具体实施方式进行阐述,显然,所描述的实施例是本发明一部分的实施例,而非全部的实施例。以下实施例1-4的t型纳米结构超双疏表面的基本制备流程如图1所示,具体制备方法包括以下步骤:制备光刻胶层:在衬底表面旋涂光刻胶,光刻胶为正胶,进行预烘固化;光刻曝光:以紫外光透过图案化掩模板的镂空部分至光刻胶上,曝光后将掩模板图案转移至光刻胶;显影:置于显影液中,显影时间为20-50s,曝光部分的光刻胶被溶解,形成光刻胶的微柱阵列;深硅刻蚀:以光刻胶微柱阵列为刻蚀掩模,使用hse深硅刻蚀设备将结构传递至硅层,通过周期交替的侧壁钝化(c4f8气体)与刻蚀工艺过程,获得周期性的沟槽结构,由于硅相较光刻胶更严重的横向刻蚀,最终获得t型多层沟槽复合微米结构;防粘处理:在t型多层沟槽复合微米结构外部以等离子体增强化学气相沉积包裹一定厚度的sio2,进一步增强整体机械性能,在真空体系中,利用1h,1h,2h,2h-全氟癸基三氯硅烷蒸汽对t型多层沟槽复合微米结构表面进行防粘处理,获得具备超双疏性能的表面。实施例1选用光刻掩模版图案为边长50微米,间距50微米非平行排列的方块阵列,具体实施过程如下:选用玻璃作为衬底材料,在表面利用物理气相沉积5微米厚的硅层。制备光刻胶层:在硅表面旋涂光刻胶az5214,旋涂转速为4000转/分钟,旋涂时间为40s,光刻胶厚度为1微米,以90℃烘烤1min对光刻胶进行预固化;光刻曝光:以光强为23mj/cm2的紫外光曝光5s;显影:置于显影液az300mif中,显影时间为20s,曝光的光刻胶被溶解,形成光刻胶的微柱阵列;深硅刻蚀:以光刻胶微柱阵列为刻蚀掩模,使用深硅刻蚀技术将结构传递至硅层,每个循环的钝化时间为1s,刻蚀时间为2s,每个循环刻蚀高度为0.5微米,经过7个刻蚀周期,如图2(a)所示,最终得到顶部边长50微米,间距50微米非平行排列的t型方块阵列,t型顶部“帽子”厚度为1微米,如图3所示,顶部直径与下层柱子边长差为0.635微米,下层柱子高度为5微米的t型多层沟槽复合微米结构。防粘处理:先使用等离子体增强化学气相沉积技术在t型多层沟槽复合微米结构外部镀30nm的sio2,然后将样品放入真空烘箱中,以全氟烷基氯硅烷蒸汽处理,在95℃氛围中静置4小时使其挥发至样品表面从而完成表面改性。实施例2选用光刻掩模版图案为边长为50微米,间距50微米平行排列的方块阵列,具体实施过程如下:选用金属镍作为衬底材料,在镍片表面利用物理气相沉积3微米厚的硅层;制备光刻胶层:在硅表面旋涂光刻胶s1813,旋涂转速为3000转/分钟,旋涂时间为40s,光刻胶厚度为1.5微米,以110℃烘烤1.5min对光刻胶进行预固化;光刻曝光:以光强为38mj/cm2的紫外光曝光2.5s;显影:置于显影液az300mif中,显影时间为40s,曝光的光刻胶被溶解,形成光刻胶的微柱阵列;深硅刻蚀:以光刻胶微柱阵列为刻蚀掩模,使用深硅刻蚀设备将结构传递至硅层,所述深硅刻蚀工艺中每个循环的钝化时间为1.5s,刻蚀时间为3s,每个循环刻蚀高度为0.8微米,经过3个刻蚀周期,如图2(b)所示,最终获得顶部边长50微米,间距50微米平行排列的t型方块阵列,t型顶部“帽子”厚度为1.5微米,顶部直径与下层柱子边长差为0.5微米,下层柱子高度为3微米的t型多层沟槽复合微米结构。防粘处理:先使用等离子体增强化学气相沉积技术在t型多层沟槽复合微米结构外部镀20nm的sio2,然后将样品放入真空烘箱中,以全氟烷基氯硅烷蒸汽处理,在100℃氛围中静置2小时使其挥发至样品表面从而完成表面改性。实施例3选用光刻掩模版图案为边长50微米,间距25微米平行排列的方块阵列,具体实施过程如下:选用玻璃作为衬底材料,在镍片表面利用物理气相沉积4微米厚的硅层;制备光刻胶层:在硅表面旋涂光刻胶az5214,旋涂转速为6000转/分钟,旋涂时间为60s,光刻胶厚度为0.8微米,以120℃烘烤1min对光刻胶进行预固化;光刻曝光:以光强为45mj/cm2的紫外光曝光2s;显影:置于显影液az300mif中,显影时间为45s,曝光的光刻胶被溶解,形成光刻胶的微柱阵列;深硅刻蚀:以光刻胶微柱阵列为刻蚀掩模,使用深硅刻蚀设备将结构传递至硅层,所述深硅刻蚀工艺中每个循环的钝化时间为1.8s,刻蚀时间为3.5s,每个循环刻蚀高度为1微米,经过5个刻蚀周期,如图2(c)所示,最终获得顶部边长50微米,间距25微米平行排列的t型方块阵列,t型顶部“帽子”厚度为0.8微米,顶部直径与下层柱子边长差为1微米,下层柱子高度为4微米的t型多层沟槽复合微米结构。防粘处理:先使用等离子体增强化学气相沉积技术在t型多层沟槽复合微米结构外部镀28nm的sio2,然后将样品放入真空烘箱中,以全氟烷基氯硅烷蒸汽处理,在85℃氛围中静置4小时使其挥发至样品表面从而完成表面改性。实施例4选用光刻掩模版图案为直径3微米,间距3微米平行排列的圆形阵列,具体实施过程如下:选用玻璃作为衬底材料,在镍片表面利用物理气相沉积4微米厚的硅层;制备光刻胶层:在硅表面旋涂光刻胶az5214,旋涂转速为6000转/分钟,旋涂时间为60s,光刻胶厚度为0.8微米,以120℃烘烤1min对光刻胶进行预固化;光刻曝光:以光强为35mj/cm2的紫外光曝光1.2s;显影:置于显影液az300mif中,显影时间为40s,曝光的光刻胶被溶解,形成光刻胶的微柱阵列;深硅刻蚀:以光刻胶微柱阵列为刻蚀掩模,使用深硅刻蚀设备将结构传递至硅层,所述深硅刻蚀工艺中每个循环的钝化时间为1.8s,刻蚀时间为3.5s,每个循环刻蚀高度为1微米,经过5个刻蚀周期,如图2(d)所示,最终获得顶部直径为3微米,间距3微米平行排列的t型圆形阵列,t型顶部“帽子”厚度为0.8微米,顶部直径与下层柱子直径差为1微米,下层柱子高度为4微米的t型多层沟槽复合微米结构。防粘处理:先使用等离子体增强化学气相沉积技术在t型多层沟槽复合微米结构外部镀28nm的sio2,然后将样品放入真空烘箱中,以全氟烷基氯硅烷蒸汽处理,在85℃氛围中静置4小时使其挥发至样品表面从而完成表面改性。上述实施例1-4得到的性能检测如下表所示:实施例1实施例2实施例3实施例4水接触角159°162.5°158°147°油接触角156.5°158°156°132°从上表可知,实施例1-3中不同大小、分布的t型多层沟槽复合微米结构均可获得高性能的超双疏表面,其中平行排列的方块性能优于非平行排列的方块,而实施例4中的圆形t型多层沟槽复合微米结构的疏水疏油效果都逊于方块。以上揭露的仅为结合具体实施方式对本发明所作的进一步详细说明,不能以此限定本发明之权利范围。因此,凡依本发明技术所作的均等变化,仍属本发明。当前第1页12