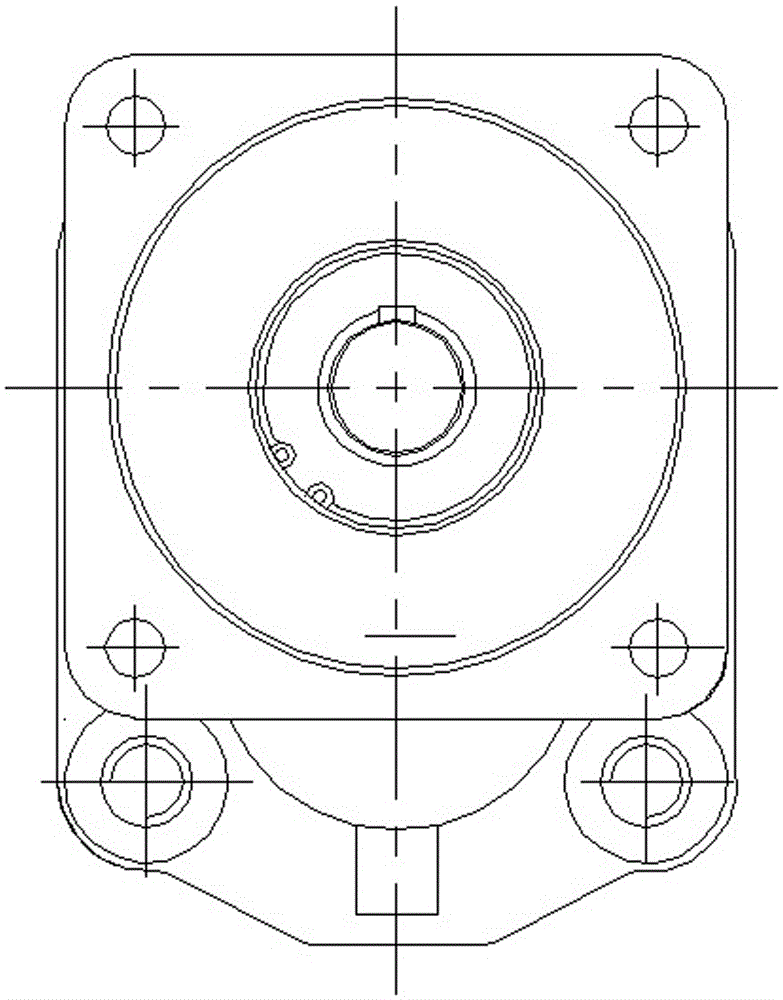
本发明涉及一种齿轮泵,具体是一种采用抗冲击型浮动侧板的齿轮泵。
背景技术:
:目前我公司生产的高压齿轮泵其浮动侧板均采用封闭式环形密封方式,以减小齿轮端面及径向泄漏,提高容积效率,在后续的使用中,发现此种结构的齿轮泵在使用冲击频率高的工况下故障率较高,当液压回路的压力由高压25MPa瞬间下降至0MPa时,浮动侧板与齿轮端面配合面的压力可瞬间下降至0MPa,但浮动侧板背面由小孔d引入的压力,由于通道较窄且长,所以在响应时间上较正面滞后,瞬间对浮动侧板的压紧力要大于推开力,齿轮对浮动侧板摩擦力增加,摩擦产生的热量增加,在高频率冲击下热量不断增加,由于高温,浮动侧板首先会在钢性相对薄弱区产生变形,即两端翘起,齿轮与浮动侧板之间产生异常磨损,烧伤,密封失效,至齿轮泵建立不起压力。技术实现要素:为了克服上述现有技术的不足之处,本发明提供了一种采用抗冲击型浮动侧板的齿轮泵。本发明是通过如下技术方案实现的:一种采用抗冲击型浮动侧板的齿轮泵,包括泵体、通过定位销连接在泵体上的前盖以及安装在泵体内且相互啮合的主动齿轮和从动齿轮,所述的主动齿轮和从动齿轮的两侧端面均安装有浮动侧板,浮动侧板与主动齿轮和从动齿轮的端面相接触的配合面设有泄荷槽,浮动侧板的背齿面设有外形呈“W”型的W密封槽,浮动侧板中部开有贯穿泄荷槽至背齿面W密封槽的槽内的通孔Ⅰ,W密封槽的槽内在靠近“W”形的两侧盲端处均设有贯穿浮动侧板的通孔Ⅱ,主动齿轮和从动齿轮两侧的浮动侧板在背齿面依次安装有W密封圈、压板和固定侧板,所述的W密封圈镶嵌在W密封槽内。进一步地,所述的浮动侧板为“8”字型,浮动侧板上的泄荷槽形状呈与W密封槽相对的“W”型。进一步地,所述的主动齿轮的转轴与前盖之间装有深沟球轴承,深沟球轴承在远离主动齿轮一端安装有防止深沟球轴承轴向移动的挡圈Ⅰ。进一步地,所述的主动齿轮的转轴与前盖之间还装有耐压油封,耐压油封位于深沟球轴承与主动齿轮之间,耐压油封在远离深沟球轴承一端安装有油封挡圈,耐压油封另一端设有防止耐压油封轴向移动的挡圈Ⅱ。进一步地,所述的主动齿轮的转轴与从动齿轮的转轴上在两侧的固定侧板外侧均安装有滚针轴承。进一步地,所述的泵体与前盖之间装有用于密封的矩形密封圈。本发明的有益效果是:本发明的浮动侧板在原有基础之上,在次高压区增加了通孔Ⅱ,在压力突变时,浮动侧板的正反两面的压力能瞬间达成一致,又因通孔Ⅱ开在W密封圈补偿力较大的区域,同时也改善了浮动侧板的整体压力平衡问题,经对比测试,齿轮泵在超高压区间内容积效率变化较之前相对稳定,具体测试数据见下表:压力(MPa)05101520253025未改进前流量值(L/min)126.3126.3126.3126.3124.1121.8123120改进后流量值(L/min)126.3126.3126.3126.3124.1122120122由上组测试数据可看出,当压力增高到30MPa时,未改进前容积效率反而增加,说明在此区间补偿力已经大大超出齿轮的反推力,导致浮动侧板贴紧齿轮端面,在此之间不能形成油膜,侧板有磨损加据,所以当压力再调到25MPa时,流量较之前有所下降,长时间运行会造成侧板磨损发热,最终侧板烧坏,齿轮泵失效。这两组泵经拆检,其侧板的磨损情况与测试数据相吻合,改进后的侧板磨损量及变型量相对未改进侧板要小很多。经主机厂试用,改进侧板后的齿轮泵在冲击频率高的工况下使用,故障率明显降低。附图说明图1为本发明的内部结构示意图;图2为本发明的左视图;图3为本发明浮动侧板配合面视图;图4为本发明A-A剖视图;图5为本发明浮动侧板背齿面视图;图中,1、主动齿轮,2、挡圈Ⅰ,3、深沟球轴承,4、挡圈Ⅱ,5、耐压油封,6、油封挡圈,7、前盖,8、滚针轴承,9、定位销,10、矩形密封圈,11、浮动侧板,12、W密封圈,13、压板,14、固定侧板,15、泵体,16、从动齿轮,17、通孔Ⅰ,18、通孔Ⅱ。具体实施方式下面根据附图和实施例对本发明进一步说明。如图1、图3、图4和图5所示,一种采用抗冲击型浮动侧板的齿轮泵,包括泵体15、通过定位销9连接在泵体15上的前盖7以及安装在泵体15内且相互啮合的主动齿轮1和从动齿轮16,所述的主动齿轮1和从动齿轮16的两侧端面均安装有浮动侧板11,浮动侧板11与主动齿轮1和从动齿轮16的端面相接触的配合面设有泄荷槽,浮动侧板11的背齿面设有外形呈“W”型的W密封槽,浮动侧板11中部开有贯穿泄荷槽至背齿面W密封槽的槽内的通孔Ⅰ17,W密封槽的槽内在靠近“W”形的两侧盲端处均设有贯穿浮动侧板11的通孔Ⅱ18,主动齿轮1和从动齿轮16两侧的浮动侧板11在背齿面依次安装有W密封圈12、压板13和固定侧板14,所述的W密封圈12镶嵌在W密封槽内。本发明的主动齿轮1和从动齿轮16相啮合,在主机发动机的带动下旋转,将液压油转换成高压油输送到液压系统中;浮动侧板11、固定侧板14、W密封圈12和压板13起端面密封作用,另外压板13还能保护W密封圈12不受冲击;W密封圈12弹性变形产生的力使齿轮和浮动侧板11之间保持仅有一层油膜厚度的间隙,齿轮泵工作时出油口的液压油通过浮动侧板11上的通孔Ⅰ17引入浮动侧板11的背齿面,同时次高压区的液压油通过浮动侧板上的通孔Ⅱ18引入浮动侧板的背齿面,这样浮动侧板前后的压差为0,浮动侧板11对齿轮端面的压紧力完全由矩形密封圈10的压缩量来提供,浮动侧板11的推开力与压紧力之差为一定值,与齿轮泵的压力大小无关,由此齿轮泵容积效率能得到较好的保证,且液压油引入W环形区域内,推动W密封圈12紧贴四周金属表面,形成全密封空间,减少浮动侧板11的外圆与泵体15内腔形成的间隙泄漏,提高齿轮泵的容积效率。如图3所示,所述的浮动侧板11为“8”字型,浮动侧板11上的泄荷槽形状呈与W密封槽相对的“W”型。如图1所示,所述的主动齿轮1的转轴与前盖7之间装有深沟球轴承3,深沟球轴承3在远离主动齿轮1一端安装有防止深沟球轴承3轴向移动的挡圈Ⅰ2。深沟球轴承3是在主动齿轮1受到外部径向力作用时,对泵起保护作用。如图1所示,所述的主动齿轮1的转轴与前盖7之间还装有耐压油封5,耐压油封5位于深沟球轴承3与主动齿轮1之间,耐压油封5在远离深沟球轴承3一端安装有油封挡圈6,耐压油封5另一端设有防止耐压油封5轴向移动的挡圈Ⅱ4。耐压油封5和油封挡圈6防止液压油沿主动齿轮1的转轴的向泵外渗漏。滚针轴承8对主动齿轮1和从动齿轮16起支承作用。如图1所示,所述的主动齿轮1的转轴与从动齿轮16的转轴上在两侧的固定侧板14外侧均安装有滚针轴承8。因为本发明结构紧凑,径向安装尺寸受限制,而滚针轴承具有较小的截面,因此径向结构紧凑,且滚针轴承内径尺寸和载荷能力与其它类型轴承相同时,外径最小,所以这里使用滚针轴承为支承结构。如图1所示,所述的泵体15与前盖7之间装有用于密封的矩形密封圈10。如图2所示,组合好的泵体和前盖通过四根螺栓和弹簧垫圈紧固成为一台单联齿轮泵。当前第1页1 2 3