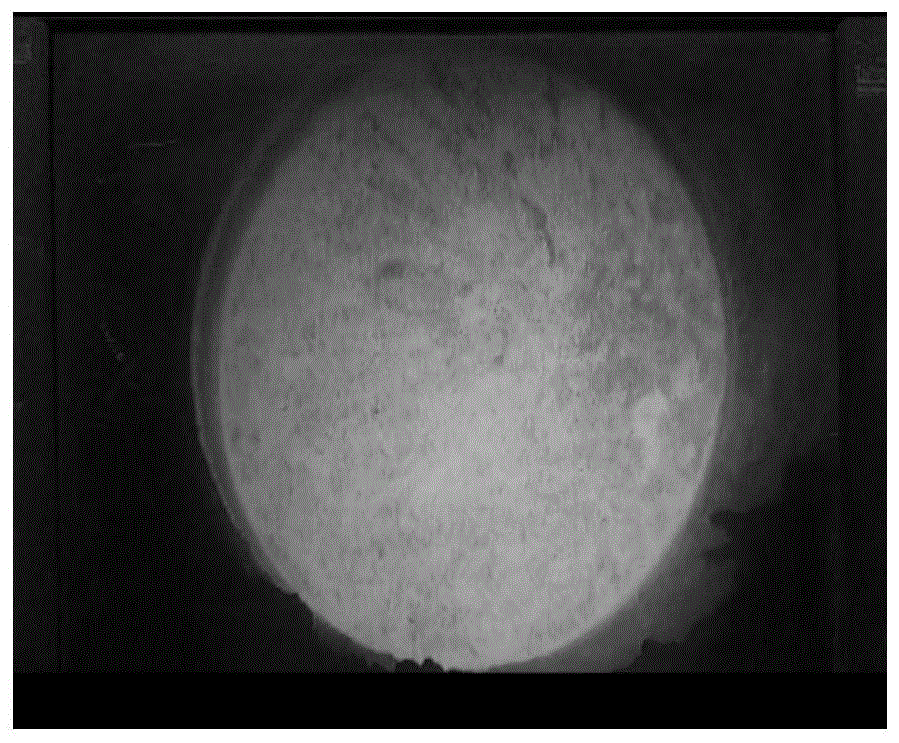
本发明属于钢铁
技术领域:
,涉及rh精炼炉性能评估方法。
背景技术:
:rh真空炉从50年代开始运用于钢水脱氢处理,已成为世界范围内应用最广泛的炉外精炼设备;它在降低钢水氢含量,提高钢水质量上取得显著效果,适合大量生产超纯净钢。当钢中w[h]高时,会形成白点,这对一些应用条件苛刻的钢材来说是致命的,如管线钢、高强度的结构钢等。钢中w[h]超过白点临界值时,会导致钢材性能恶化乃至报废,因此现代钢材生产中,必须把氢去除到规定的数值之下。目前,钢厂为控制钢水最终氢含量,设定的rh炉真空脱气工艺时间多为定性评估,工艺设计时间与钢水氢含量缺乏系统定量评估;主要以延长rh炉真空脱气工艺设计时间,保证钢水氢含量要求,使rh工艺设计时间与生产匹配矛盾突出。目前,钢厂为控制钢水最终氢含量,设定的rh精炼炉真空脱气工艺时间多为定性评估,工艺设计时间与钢水氢含量缺乏系统定量评估;主要以延长rh炉真空脱气工艺设计时间,保证钢水氢含量要求,使rh工艺设计时间与生产匹配矛盾突出。技术实现要素:本发明解决的技术问题:通过研究提升气体流量、浸渍管插入深度等影响rh脱氢效果的工艺因素,定量评估钢水氢含量与rh工艺时间的关系,实现rh工艺过程高效化、钢水洁净化的生产,对于现代钢铁企业生产质量改善具有很好的推广价值。本发明具体采用如下技术方案:一种评估rh精炼炉真空脱氢能力的方法,其特征在于包括如下步骤:(一)通过试验研究提升气体流量对真空处理阶段rh脱氢影响情况及程度;试验过程中,只改变提升气体流量,保持其他参数不变;(二)通过试验研究浸渍管插入深度对真空处理阶段rh脱氢影响情况及程度;试验过程中,只改变浸渍管插入深度,保持其他参数不变;(三)试验定氢及取样方案:定氢时选取相同位置进行定氢,定氢取样保证一用一备,保证成功率定氢与取气体样分析同时进行,记录实际取样定氢时间,其中定氢时间记录为定氢仪显示示数后的时间;(四)根据步骤(一)、(二)、(三)进行rh精炼炉真空脱氢能力评估。优选地,步骤(一)中,提升气体流量以20nm3/h为梯度进行试验,试验过程中保持其他参数不变,只改变提升气体流量。优选地,步骤(二)中,浸渍管插入深度以100mm为梯度,在不改变其他参数及工艺条件下研究浸渍管插入深度对rh脱氢影响情况及程度;所述浸渍管插入深度为稳定工作时浸渍管底部距结渣表面距离。优选地,步骤(三)真空处理过程中,定氢取样间隔时间为4min。本发明通过研究提升气体流量、浸渍管插入深度等影响rh精炼炉脱氢效果的工艺因素,实现定量评估钢水氢含量与rh工艺时间的关系,达到rh工艺过程高效化、钢水洁净化的生产。附图说明图1:气体流量为100nm3/h的液面波动示意图;图2:气体流量为120nm3/h的液面波动示意图;图3:气体流量为140nm3/h的液面波动示意图;图4:气体流量为140nm3/h的液面波动喷溅示意图(喷溅);图5:浸渍管插入深度500mm;图6:浸渍管插入深度400mm。图7:不同方案条件下氢含量随真空处理时间变化图;图8:不同方案条件下脱氢速率随时间变化图。具体实施方式下面对本发明技术方案做进一步详细说明。实施例1一种评估rh精炼炉真空脱氢能力的方法,包括如下步骤:1、研究提升气流量对真空处理阶段rh脱氢影响情况及程度研究rh提升气体流量对钢液h含量变化的影响,提升气体流量以20nm3/h为梯度进行试验,具体方案如表1所示。表1提升气体流量试验方案表试验方案流量nm3/h插入深度mm其他工艺参数1100500保持不变2120500保持不变3140500保持不变提升气体流量试验情况:按提升气体流量100、120、140nm3/h进行试验,试验过程中除提升气体流量外,不对其他条件进行改变。试验发现提升气流量对终点h含量影响明显,真空室钢液波动变化也较为明显,如图1-4所示,当流量为120nm3/h较100nm3/h时液面波动更为明显,且无明显喷溅现象,真空室形状保持较好的形状,而流量为140nm3/h时产生了明显的喷溅现象,真空室底部形状变化明显,已造成结瘤如图4所示。当进行改变提升气体流量试验时,保持抽真空及循环处理阶段流量为试验流量不变,考察记录不同流量达到要求真空度所需时间。2、研究浸渍管插入深度对真空处理阶段rh脱氢影响情况及程度插入深度以100mm为梯度,在不改变其他参数及工艺条件下研究插入深度对rh脱氢影响情况及程度,具体方案如表2所示。表2浸渍管插入深度试验方案表试验方案流量nm3/h插入深度mm其他工艺参数1100500保持不变4100400保持不变此处浸渍管插入深度为稳定工作时浸渍管底部距渣表面距离。如图5所示,结渣处为插入深度500mm,现场目测结合顶升高度分析液面约降低100mm。图6为减少插入深度后渣液面图,即插入深度400mm。结合浸渍管安全插入深度要求及现场条件的限制,浸渍管插入深度最浅约400mm。3、试验定氢及取样方案定氢时选取相同位置进行定氢,定氢取样保证一用一备,保证成功率定氢与取气体样分析同时进行,记录实际取样定氢时间,其中定氢时间记录为定氢仪显示示数后的时间。表3取样定氢时间表深真空时间/min0min4min8min12min16min20min定氢及取样①②③④⑤⑥4、氢含量分析4.1脱氢机理建模研究表明钢液中脱氢过程由钢液边界层中的传质控制,对物质i,传质速率式中:a——气-钢液反应的界面面积、c[i]——物质i在钢液内部浓度、——物质i在气液界面处浓度。ni——物质i的物质的量由物质平衡可得(传质速率等于脱气速率),v表示钢液体积联立两式可得kd——传质系数假设为常数,在0~t内对上式积分得式中c[i]——物质i在钢液中的原始浓度及真空处理t时该元素的浓度。在表面浓度及初始浓度为常数时,上式可表达为[h]=a·e-bt+c式中a、b、c均为正常数。4.2数据拟合处理由以上推导,拟合试验所得到的定h数据,得到不同提升气流量、插入深度条件下氢含量随时间变化情况,如表4所示。表4各方案拟合计算结果方案拟合结果斜率表达式1y=4.1*exp(-x/5.537)+1.8y′=-0.74*exp(-x/5.537)2y=4.438*exp(-x/3.57)+1.59y′=-1.243*exp(-x/3.57)3y=4.286*exp(-x/4.215)+1.61y′=-1.017*exp(-x/4.215)4y=3.445*exp(-x/6.325)+1.57y′=-0.545*exp(-x/6.325)拟合曲线中y轴限度受原始数据中时间最大值及氢含量最小值影响、第一项系数受原始数据中钢液初始氢含量影响,故拟合结果与实际存在一定误差,但整体趋势基本一致,如图7所示。从图7中各拟合曲线可以看出,要想h含量达到2.0以下,方案1需16.71min,方案2、3和4分别需要8.5min、10.07min和13.14min,方案2为最优方案。设y=f(x),则-f′(x)为各个方案拟合结果在时刻为x时的脱氢速率,在0~t内对-y′=-f′(x)积分得为钢液氢含量变化量,即[h]脱除量,各个方案拟合结果-y′=-f′(x)随时间变化情况如图8所示。从图8中可知,当提升气流量为120nm3/h时,前6min脱氢速率最高,在脱氢相同时间内脱氢率也最高(即积分面积最大),方案2依然为最优方案;4种方案在25min后脱氢速率基本相同,从1到4分别为0.008、0.001、0.003和0.005ppm/min,可见在试验条件下基本达到脱氢极限,延长处理时间对脱氢来说已影响不大,时间因素已不是脱氢限制性条件。当前第1页12