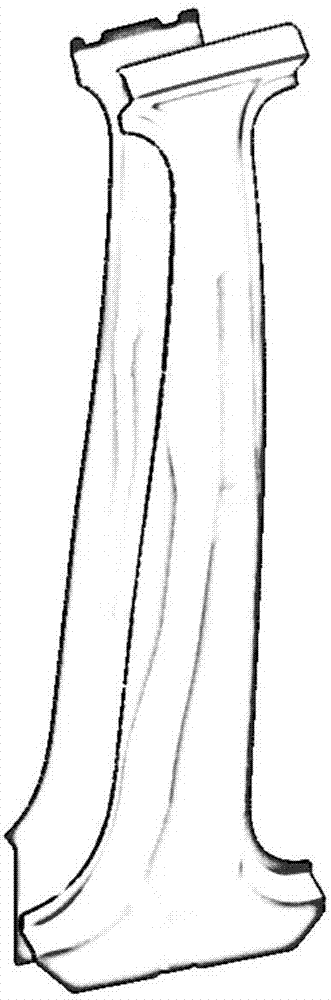
本发明涉及的是一种激光焊接领域的技术,具体是一种预测激光焊接变形量的实现方法。
背景技术:
:激光焊接过程逐渐开始广泛的应用于汽车车身板件的连接过程中,其具有自动化程度高、焊接速度快、焊接熔深深、接合强度高等优点,但也伴随着焊接变形、残余应力等问题。激光焊接引起的变形往往超出车身板件的装配公差,对装配精度有很大的影响。技术实现要素:本发明针对现有技术无法通过定义焊丝网格轮廓控制焊缝熔池区形貌、无法准确拟合焊缝处熔池区形貌,焊接变形仿真效果较差的缺陷,提出一种预测激光焊接变形量的实现方法,提高了温度场计算的准确性,提高了变形预测的准确性,大大减少了焊接变形预测的时间。本发明是通过以下技术方案实现的:本发明通过采集焊接后熔池区域的几何形貌并建立有限元模型以及由高斯面热源和高斯体热源组成的热源三维扫描模型,然后拟合热源参数并识别非完全耦合过程的耦合参数,再建立生产中的待连工件的有限元模型,并载入热源三维扫描模型和耦合参数,进行有限元仿真计算,最终获得待连工件的预测变形量。所述方法具体包括以下步骤:1)对试验工件进行激光焊接,并测量焊接后的工件变形量;2)对焊缝区域进行金相显微观察,获得熔池区域的几何形貌;3)建立试验工件的有限元模型;4)建立由高斯面热源和高斯体热源组成的热源三维扫描模型,拟合热源参数;5)识别非完全耦合过程的耦合参数;6)建立生产中的待连工件的有限元模型,并载入热源三维扫描模型和耦合参数,进行有限元仿真计算,获得待连工件的预测变形量。所述的步骤2)具体包括以下步骤:2.1)将焊缝区域切割为2×2cm方块;2.2)对方块进行镶嵌、打磨、抛光和腐蚀;2.3)对方块进行金相显微观察获得熔池区域的几何形貌。所述的步骤4)具体包括以下步骤:4.1)生成由高斯面热源和高斯体热源组成的热源三维扫描模型;4.2)设定一组热源参数,进行试验工件的仿真焊接;4.3)对比仿真结果中的熔池区域的几何形貌和金相中的熔池区域的几何形貌的关键特征(如熔池边界形貌、熔池面积),关键特征符合则将该组热源参数作为最终值,否则回到步骤4.2)。所述的热源参数包括:吸收率η,功率分配系数μ,面热源半径r0,体热源上面半径ru,体热源下面半径r1,体热源深度d。所述的高斯面热源的能量分布为所述的高斯体热源的能量分布为所述的步骤5)具体包括以下步骤:5.1)设定一组非完全耦合过程的耦合参数;5.2)进行试验工件的仿真焊接;5.3)仿真结果中的试验工件变形量与实际变形量之差小于阈值则该组耦合参数作为最终值,否则回到步骤5.1)。所述的耦合参数包括温度场计算步长ttemp和温度场个数n。所述的焊接为激光焊接。附图说明图1为本发明方法流程示意图;图2为试验工件结构图;图3为试验工件变形量示意图;图4为试验工件的有限元模型示意图;图5为几何形貌对比示意图;图中:(a)为金相结果的几何形貌图;(b)为仿真结果的几何形貌图;图6为热源三维扫描模型结构示意图;图7为实施例中待连工件的预测变形量有限元仿真示意图。具体实施方式如图1所示,本实施例包括以下步骤:1)对试验工件进行焊接,并测量焊接后的工件变形量。如图2所示,所述的试验工件为汽车车身中的b柱区域板件,即采用激光焊接方法来焊接b柱内板和b柱加强版。b柱加强版和b柱内板为试验工件。对试验工件进行光学扫描,获得试验工件的几何外形,用于建立有试验工件的限元模型。如图3所示,所述的试验工件完成焊接后,进行三维光学扫描,获得焊接后的试验工件的变形量。2)对焊缝区域进行金相显微观察,获得熔池区域的几何形貌。2.1)将焊缝区域切割为2×2cm方块。2.2)对方块进行镶嵌、打磨、抛光和腐蚀。2.3)对方块进行金相显微观察获得熔池区域的几何形貌。3)建立试验工件的有限元模型。如图4所示,采用simufactwelding软件建立的试验工件的有限元模型,包括三维体网格生成的板件网格模型、焊缝路径设置以及夹具位置设置。4)建立由高斯面热源和高斯体热源组成的热源三维扫描模型,拟合热源参数。4.1)生成由高斯面热源和高斯体热源组成的热源三维扫描模型。4.2)设定一组热源参数,进行试验工件的仿真焊接。4.3)如图5所示,对比仿真结果中的熔池区域的几何形貌和金相中的熔池区域的几何形貌的关键特征(熔池边界形貌、熔池面积),关键特征符合则将该组热源参数作为最终值,否则回到步骤4.2)。热源参数最终值如表1所示。表1热源参数数值如图6所示,所述的热源三维扫描模型包括高斯面热源和高斯体热源。热源参数包括:吸收率η,功率分配系数μ,面热源半径r0,ru体热源上面半径,r1体热源下面半径,d体热源深度。对于输入功率为q,吸收率η的激光热源,高斯面热源能量分布为高斯体热源能量分布为其中:qvol=μηq,qsurf=(1-μ)ηq,r坐标点的径向坐标,r0为深度d以下的体热源半径,α为激光入射的倾斜角度。5)识别非完全耦合过程的耦合参数。5.1)设定非完全耦合过程的耦合参数,耦合参数包括温度场计算步长ttemp和温度场个数n。5.2)进行试验工件的仿真焊接。5.3)仿真结果中的试验工件变形量与实际变形量之差小于阈值则该组耦合参数作为最终值,否则回到步骤5.1)。得到温度场计算步长ttemp和温度场个数n的最终值为0.02s和5。6)建立生产中的待连工件的有限元模型,并载入热源三维扫描模型和耦合参数,进行有限元仿真计算,获得待连工件的预测变形量,如图7所示。仿真结果与扫描结果对比如表2所示,最大误差不超过实测误差的10%。表2仿真结果与扫描结果对比变形量123456扫描(mm)1.011.151.251.230.890.21仿真(mm)0.941.121.191.130.850.20误差(%)-6.9-2.6-4.8-8.1-4.5-4.8与现有技术相比,本发明通过焊接试验及相应焊接件的金相试验与光学扫描,即可得到预测程度较高的仿真模型,无需进行焊接过程的温度曲线测量与残余应力测量。仿真过程采用非完全耦合的过程,相比相同热分析步长的完全耦合过程,仿真精度将近,仿真时长缩短为36%,如表3所示。表3非完全耦合方法与完全耦合方法结果对比实例非完全耦合完全耦合扫描结果热分析步长(s)0.02s0.02s\耦合分析步长(s)0.1s0.02s\计算时间0.36tt\测点最大变形量(mm)1.191.211.25相对误差(%)-4.8-3.20上述具体实施可由本领域技术人员在不背离本发明原理和宗旨的前提下以不同的方式对其进行局部调整,本发明的保护范围以权利要求书为准且不由上述具体实施所限,在其范围内的各个实现方案均受本发明之约束。当前第1页12