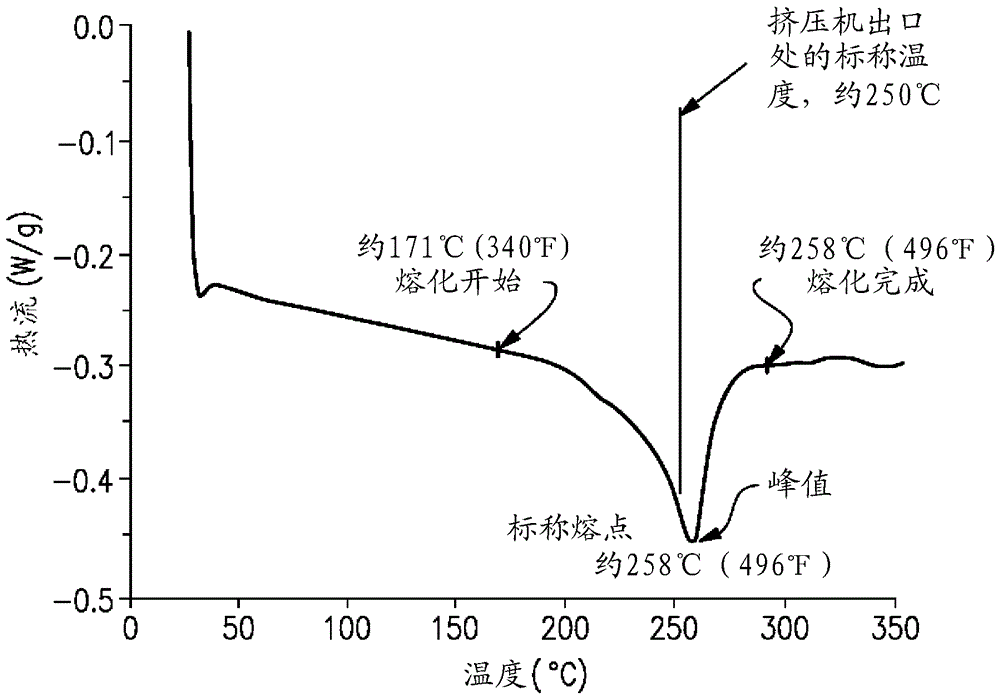
本公开涉及燃料电池分隔器板组件,以及在连续、自动化的过程中制造多个分隔器板组件及其流场板的方法。
背景技术:用于单个的燃料电池分隔器板组件的组合物以及生产单个的燃料电池分隔器板组件的制造过程已经被开发出来,例如在美国专利申请公开号2010/0307681中公开的内容,该文献通过引用的方式被并入。热纯化的片状石墨和具有15-20%氟化乙烯丙烯(FEP)的典型成分的FEP树脂材料已被用于制造分隔器板组件。其它疏水性树脂,例如全氟烷氧基共聚物(PFA)和聚四氟乙烯(PTFE),也是适合的。所述树脂能够从例如DuPont的制造商获得。分隔器板组件也已知为双极分隔器板,并且包含在分隔器板组件两侧上的流场,该流场在燃料电池内分配反应物。用于UTCPowerPC-50磷酸燃料电池(PAFC)中的一个示例性流场具有500mm×500mm的平台,并且包含约150个反应物流动通道,该反应物流动通道对于阴极流场而言约为1.4mm宽且0.7mm深,而对于阳极流场而言为1.4mm宽且1.0mm深。阳极流场和阴极流场的总厚度分别约为1.7mm和1.4mm。当前,通过将石墨-FEP的粉末状混合物放入到模具中,在分批过程中制造预成形件。相对于2.1-2.2g/mL的模制密度,这些粉末具有约0.6-0.7g/mL的体积密度。该干燥过程具有几个缺点。难以在整个部件上实现均匀的粉末分布。该变化转变成整个部件上的较差的厚度均匀性和密度均匀性。当人们试图将流场模制成净形状时,还存在额外的复杂因素,即流场腹板上粉末的压缩比与流场的肋上的不同。这导致肋具有比腹板低的密度,从而导致较低的热导率和电导率以及较高的酸吸收率和酸转移率,这些都是不合需要的。肋中石墨颗粒的取向更趋于沿着肋而非横穿肋,这也是不理想的。制造中所用的典型分批过程则是相当昂贵的。在其10-20年的使用寿命内,分隔器板组件必须具有非常低的电解质吸纳和非常低的穿过平面的酸转移率。这是分隔器板组件最需要的特性。由于石墨表面的电化学氧化(腐蚀),酸从板的阴极侧到该板的阳极侧,从而渗透分隔器板组件。氧化使石墨亲水,这导致它被酸性电解质浸湿。当前用于分隔器板组件中的热纯化的大片状石墨相对于先前所用的球状石墨具有两个好处。第一,大石墨片情况下边缘面相对于基面的低比率导致了相比于球状石墨非常低的腐蚀速率。第二,当前的制造过程也导致石墨片优先垂直于穿过平面的方向对齐。对于穿过平面的酸渗透而言,这产生了非常高的迂曲,其进一步阻碍酸渗透到板中。通过使用熔融挤压过程,热塑性塑料(例如FEP)被成形成管材、膜、片材以及电气布线上的绝缘涂层。这些材料通常是100%的FEP。在一些应用中,添加几个百分点的填料以对产品着色或影响它们的电气属性。挤压机通常具有多个加热区。根据DuPont,这些区的温度通常是330-370℃,该温度显著高于典型FEP的约260℃的熔点。FEP以熔融、完全液体的状态并在环境压力下离开挤压机。多种方法被用于冷却形成的制品,以凝固FEP并控制挤压制品的尺寸。例如,FEP管材被拉制在心轴上同时被浸没在水浴中,这样设定直径并凝固FEP。在一个示例性制造方法中,FEP膜利用激冷轧辊压延以设定其厚度并凝固FEP。
技术实现要素:一种制造流场板的方法,包括混合石墨和树脂材料以提供混合物。例如,通过柱塞挤压或双带压力机,该混合物被成形成连续的流场板。该连续的流场板被分割成离散的流场板。在连续的流场板和离散的流场板之一中提供流场通道。在一个示例中,公开了一种柱塞挤压过程,用于将PAFC所用的片状石墨-FEP流场成形成净形状。该过程包括:在FEP树脂包括两相(即,液相和固相)的温度下,从模中排出流场板。流场通道可以在连续的流场板成形过程期间或其后形成。公开了一种分隔器板组件的构造,其包括与含氟弹性体结合在一起的两个片状石墨-FEP流场。在另一个示例中,公开了一种双带压力机成形过程,用于通过将片状石墨-FEP糊料挤到连续钢带上来将片状石墨-FEP流场成形成净形状,所述连续钢带包含作为流场板的镜像的通道构造。还公开了一种形成片状石墨-FEP流场板坯件的双带压制过程。附图说明通过参照以下详细描述并且结合附图一起考虑,可以进一步理解本公开,在附图中:图1是示例性燃料电池分隔器板的一部分的示意图。图2是描绘了使用柱塞挤压将流场板连续成形成净形状的示例性过程的流程图。图3是描绘了使用柱塞挤压来连续形成双极板坯件的示例性过程的流程图。图4是一个示例性氟化乙烯丙烯的差示扫描热量计曲线图。图5A是根据图2中所述的柱塞挤压过程制造的连续的流场板的立面图。图5B是图示了彼此结合的两个流场板的截面图。图6A是柱塞挤压机的示意图。图6B是用于图6A的柱塞挤压机的模的示意图。图7是描绘了图2和图3中所述的柱塞挤压过程的温度曲线的图形。图8是描绘了使用双带压力机将流场板连续成形成净形状的示例性过程的流程图。图9是描绘了使用双带压力机连续形成双极板坯件的示例性过程的流程图。图10是描绘了使用图8和图9的双带压制过程的糊料挤压序列和流场板成形的流程图。图11是具有糊料分配和干燥器区的双带压力机的示意图。图12A是用于图11中所示机器的带的俯视图。图12B是图12A中所示带的侧视图。具体实施方式图1中示意性地图示了燃料电池分隔器板10。板10具有第一和第二侧12、14,二者分别提供了对应于阴极和阳极流场的第一和第二流场16、18。第一和第二流场16、18分别包括延伸到板10的周界24的第一和第二流场通道20、22。每个流场可以包括大约150个通道。由周界24限定的一个典型的板10的平台(在X-Y方向)为500mm×500mm(19.7英寸×19.7英寸)。在一个示例中,流场板的宽度相对于其厚度的纵横比约为300-350:1。这些流场板中的一个为1.7mm厚,所以其纵横比为500/1.7=294。其它流场板为1.4mm厚,所以其纵横比为500/1.4=357。在图示的示例中,每一侧上的流场通道是相互平行的,并且一侧上的流场通道垂直于相对侧上的通道。在一个示例中,板10具有厚度26,其约为3.1mm。在一个示例中,第一流场通道20具有约1.4mm(0.06英寸)的宽度28和约0.7mm(0.03英寸)的深度30。第二流场通道具有1.4mm(0.06英寸)的宽度128和1.0mm(0.04英寸)的深度130。阳极流场和阴极流场的总厚度分别约为1.7mm和1.4mm。在此示例中,图1中双极板的总体厚度约为3.1mm。所述总体厚度包括:燃料通道的深度(1.0mm)+空气通道的深度(0.7mm)+腹板厚度(1.4mm)。腹板是燃料通道底部到空气通道底部之间的厚度。图5B中的板包括阳极流场和阴极流场。对于1.7mm的总体厚度来说,阳极流场具有1.0mm的燃料通道深度和0.7mm的腹板厚度。对于1.4mm的总体厚度来说,阴极流场具有0.7mm的空气通道深度和0.7mm的腹板厚度。图1和图5B中的总体厚度为大致相同的3.1mm。图2和图3是描绘了使用柱塞挤压机(图6A和图6B)来生产分隔器板组件(图5A和图5B)的示例性制造方法32、132的过程流程图。描述了两种示例性制造方法32、132。图2涉及将流场板挤压成具有在挤压过程期间所形成的流场通道的净形状。可替代地,可期望的是,挤压流场坯件,并且将通道机加工到所述坯件的任一侧中,如图3中所述。参照图2和图3,FEP粉末34和石墨粉末36(例如,片状石墨),被计量和称重38以提供混合物。可以使用除FEP之外的树脂。将混合物彻底混合40。如图2中所示,例如,使用柱塞挤压过程,连续地挤压出具有提供通道的带肋轮廓的流场板。如42处所指示的,产生连续的流场板挤压,并且其被示意性地描绘在图5A中,包括流场通道120。如图2的46中所描绘的,在修整之后,连续的挤压提供了离散的流场板162(通过虚线示出)。可替代地,如图3的142处所示,坯件(即,没有肋和通道)可以被连续挤压。如44处所指示,流场板或坯件被冷却。返回到图2并且参照图5B,通过联接来自两条挤压生产线的修整过的流场板来生产分隔器板110,但是也可以使用单条挤压生产线。如图5B中所示,修整过的流场板62(在图2中46处指示,来自一条挤压生产线)被涂以含氟弹性体66(如图2中50处所指示),以联接流场板62、162的侧面64、164(如图2中的52所指示)。在一个示例中,通过已知的技术(例如喷涂或丝网印刷),含氟弹性体66像窗框一样在组件的周界附近被施加到这些流场板中的一个的平坦侧面。含氟弹性体66在两个流场板62、162之间创建气体和液体的密封,结果得到了分隔器板组件116。例如,含氟弹性体可以是LaurenManufacturing出售的Fluorolast®WB-200,其中氟含量的重量百分比至少为68%。板62的第一侧112提供第一流场116,第一流场116包括阴极的第一通道120。板162的第二侧114提供第二流场118,第二流场118包括阳极的第二通道122。例如,(图2)在150-200℃(317-415°F)下,两个板62、162在低压平板层压机54中被结合,或通过其它已知的层压装置被结合,例如印压机。可替代地,流场可以在其初始加热循环期间就在PAFC内被结合就位。可湿性涂层被静电施加到阳极侧114,如块56处所指示地。可替代地,众所周知,可湿性涂层可以通过将炭黑的水性悬浮液喷涂到流场上并进行干燥来施加。机加工废弃物被收集起来,并且以后可以被用于生产冷却器组件,例如,如48处所指示的那样。参照图3,在修整之后,将通道机加工在相同坯件的阴极侧上和阳极侧上,如58和60处分别指示的那样。例如,如148处所指示的,机加工废弃物被收集起来,并且以后可以被用于生产冷却器组件。可湿性涂层被静电施加到阳极侧,如56处所指示的。图6A示出了水平柱塞挤压机68的示意图。石墨和FEP粉末从存储箱70、72被供给到漏斗74中,当柱塞80被取出时,漏斗74将粉末供给到桶86中。柱塞装置76包括液压活塞78,液压活塞78具有能够滑动地接收在缸82中的柱塞80。所述柱塞挤压机及过程实现了通过非连续材料供给的连续流场板的连续化生产。当柱塞80被插入到桶86中时,混合的粉末被压紧。冷却部段87被设置在桶86的入口附近,以防止进入桶86的材料比期望的更早熔化。桶86包括模89,模89具有图6B中所示提供板的宽度和厚度的轮廓91。如果要在挤压期间形成流场通道,则轮廓91也包括通道和肋。当混合物利用柱塞80的每个冲程沿桶86前进时,该混合物通过附接到桶86的电加热元件88、90、92进行加热,直至混合物达到FEP熔点以上的温度。模89占据了介于1/3和1/4之间的挤压机长度,并且位于挤压机的出口处。熔融混合物进入模89,其中当熔融混合物通过冷却部段94时它被冷却。如下文所讨论的,受挤压混合物是FEP和固体石墨的两相液体-固体混合物。作为石墨片上的粘性力作用的结果,随着混合物通过模89的初始部分,熔融石墨-FEP混合物中的石墨片变为垂直于流场平面来取向。挤压成的部件在高于FEP开始熔化的温度并低于FEP完全熔化的温度的温度下从模89排出。图4是用于FEP的差示扫描热量计(DSC)曲线图,其示出了热塑性聚合物(例如FEP)具有相对宽的熔点。在DSC图中的峰值处,树脂以两相状态存在,其中一半的FEP树脂处于液体状态,一半处于固体状态。在模89的出口处,所期望的树脂熔固比在40:60和60:40之间(当树脂是FEP时,大致在250℃(482℉)),但是也可以使用其它比率。液体状态提供了允许通过模89在期望压力下挤压出流场板的润滑,而固体状态将结构结合在一起,从而获得可接受的物理属性。柱塞挤压通过模具外部的加热器而非通过摩擦来提供熔化的FEP树脂,例如,像在螺旋挤压过程的情况中那样。因此,平移柱塞80而不是围绕其轴线旋转该柱塞的柱塞挤压产生了少得多的石墨片磨损,并且最终得到具有与通过分批过程制造的现有期望的分隔器板组件的属性相类似的属性的流场。在柱塞挤压过程中能够比在螺旋挤压过程中采用高得多的压力。这在将极端粘稠的两相FEP-石墨组合物挤压通过模89时是非常有用的。参照图7,沿挤压机的第一个四分之一长度的一个示例性温度曲线提供了从150℃(302℉)到350℃(662℉)的上升温度,挤压机的接下来的一半长度保持350℃(662℉)的流场温度,并且挤压机的最后四分之一长度将温度从350℃(662℉)降低至250℃(482℉)。同样,在该示例中模89占据了1/3至1/4的挤压机长度。在一个示例中,当其离开所述模时,挤压成的流场板的温度约为260℃。该温度对应于FEP约50%为液体、50%为固体的情况。挤压成的流场板被传送通过淬火台,其被示意性地示出为冷却部段94,在其中流场板的温度从250℃(482℉)下降至接近环境温度。淬火台可包含一系列辊来保持挤压成的流场板和淬火台之间的接触,以增加冷却速率。如先前所讨论的,单个流场板62、162被形成为分隔器板组件110。如图6A中所示,挤压机68、168可以被用于使用低压连续平板层压机96来生产流场板62、162。如所讨论的,阳极流场涂有可湿性处理物。使用双带压力机来制造流场板的方法示于图8和图9中。图8中所示的实施例使用双带压制过程将流场板生产成净形状。可能期望替代地形成流场板坯件,并将流场通道机加工到该坯件中。图9中所示的实施例生产坯件,随后在该坯件的两侧上进行机加工,以生产完成的分隔器板组件。参照图8,其示出了流场成形过程200,其中流场通道被一体地形成。用于在钢带中填充通道的糊料挤压过程可以被用于将石墨-FEP流场成形成净形状。用于制造这些流场的石墨片具有每100g约10g的非常低的DBP(例如,邻苯二甲酸二丁酯)油吸收值。与油吸收值有关的标准和测试其的方法阐述于ASTMD2414中。这意味着仅需要非常少量的溶剂(vehicle)来浸透石墨片以及生产粘性糊料。在一个示例中,糊料能够用约20%的水和80%的石墨-FEP制成。能够在低于200-250℃的情况下汽化的烃类液体也可以被用作溶剂以生产糊料。这样的糊料的比重约为1.7g/mL。图10概述了用于制备这样的糊料的过程240。该糊料的压缩比约为1.26(2.15/1.70),相对于干燥过程3.3(2.15/0.65)的压缩比而言。压缩比是模制板的密度相对于干燥糊料密度或用于制造板的粉末混合物的体积密度的比率。较低的压缩比将使模制板中腹板和肋之间的密度差最小化。参照图8,FEP202、片状石墨粉末204以及按体积高达约20%的水206的混合物被准备,以形成糊料。片状石墨粉末与树脂的比率约为4:1。在挤压到传送带上之前(如212处所指示的),糊料被称重208和混合210。在一个示例中,如图12A和图12B中所示,带278通过具有凸脊284的连续钢带282提供,凸脊284提供了流场板中对应的流场通道。在通过双带装置进行压制(在如216处所指示的)之前,水从糊料中蒸发(如214处所指示的)。混合物在压力下加热,并且随后在压力下冷却,如218处所指示。连续流场被分开并且切割成离散的流场板,如220处所指示。来自另一条生产线的流场板被切割,如226处所指示,并且通过含氟弹性体被连接到另一个流场板,如224处所指示,并且运行通过层压机,如228处所指示。来自切割的任何废弃物都可以被回收和再利用,如222处所指示。可湿性涂层被静电施加到阳极侧,如230处所指示。图10和图11分别描绘了可以被用在过程200中的糊料挤压过程240和双带压力机266。石墨被添加到混合器268(图11),如242处所指示(图10)。对填充有石墨的混合器抽真空,如244处所指示,这有助于浸透石墨以及去除气泡。混合器被配置成使所述石墨片不破损。一个示例性片状石墨是SuperiorSGC-2901G。在进行混合时,并且在释放真空之前,含氟聚合物乳胶(例如PTFE)被添加到混合器,如246处所指示的。也可使用FEP乳胶,例如DyneonFEP6300GZ分散物。在混合期间,乳胶可以被冷却至约7℃(45℉),以确保混合物自由流动。在高速混合期间形成均匀混合以生产糊料,如248处所指示。该糊料被供应给挤压机(268,图11),如250处所指示。螺旋挤压机252将糊料分配到带(278,图11)上,如254处所指示。包含糊料的带278穿过干燥器部段270,如图11中所示。干燥器部段270在高于100℃(212℉)的情况下去除水,在高于250℃(482℉)的情况下去除表面活性剂,如图10中的256、258处所指示。加热的混合物进入具有下带和上带278、280的双带压力机272。所述带中的一个或多个,例如,下带,可以包括压制期间形成流场通道的肋。返回到图10,混合物在热区274(图11)中在3.5-7.0MPa(500-1000psi)下被加热至高于300℃(572℉),如260处所指示。在冷区276(图11)中,混合物保持在该压力下并被冷却至低于200℃,如262处所指示。连续的流场板被成形为具有净形状的厚度和宽度,如264处所指示,并且可以通过切割器286(图11)被分割成离散的流场板。在约200℃(415℉)的温度下,所形成的流场从双带排出,该温度低于大部分FEP已经凝固的温度,这导致了期望的物理属性,例如2.1-2.2g/mL的密度是期望的范围。另一个机器266可以将流场板供给到层压机288,其中该流场板以先前所述的方式与另一个板联接。参照图9,其示出了流场成形过程300,其中生产出流场坯件。FEP302和片状石墨粉末304和水的混合物被混合。如312处所指示的,在放置到带上之前,混合物被称重308和混合310。所述带可以被设置为双带压制系统的一部分。双带压制系统与图12A和图12B中所示的类似,但没有用于成形流场通道的凸脊。在该示例中,水不与FEP和石墨混合来制造糊料。然而,如果糊料被用于过程300中,则在通过双带压制装置进行压制(如316处指示的)之前,水从该糊料中蒸发(如314处指示的)。混合物在压力下加热并且随后被冷却,如318处所指示的。连续流场被分开并且切割成离散的流场板,如320处所指示。在修整之后,将通道机加工在相同坯件的阴极侧上和阳极侧上,如332和334处分别所指示的。来自切割的任何废弃物都可以被回收和再利用,如322处所指示。可湿性涂层被静电施加到阳极侧,如330处所指示。示例性双带压力机266可以被用于根据相对于图9所述的过程将石墨-FEP流场坯件成形成净形状。单独的流场板62、162被形成为如图5B中所示和上文中所述的分隔器板组件。如图11中所示,挤压机266、266可以被用于生产流场板62、162。阳极流场和阴极流场使用低压连续平板层压机288被结合在一起。如已知的,阳极流场涂有可湿性处理物。尽管已经公开了示例性实施例,但本领域普通技术人员可意识到在权利要求的范围内可以产生某些修改。因此,所附权利要求应当被研究以确定它们的真实范围和内容。