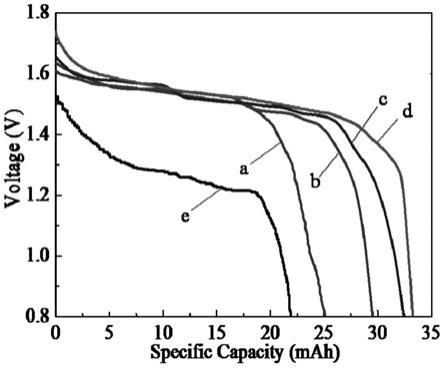
[0001]
本发明属于超铁电池技术领域,尤其涉及一种石墨烯修饰的高铁酸盐材料及其制备方法和应用。
背景技术:[0002]
随着对绿色化学能源和几乎枯竭的电极材料的需求不断增加,高铁酸盐化合物作为电池阴极材料具有广阔的发展前景。1999年,litch以高铁酸盐(mfeo4)作为阴极材料代替碱性锌锰电池中mno2阴极,并且将这种新电池命名为“超铁电池”,mfeo4/zn电池的放电产物是对环境不会产生污染的zno、水和fe2o3,与碱性mno2/zn和铅酸电池相比,mfeo4/zn电池是一种绿色无污染的可持续能源,被誉为新一代“绿色电池”。然而,尽管高铁酸盐具有潜在优势,但是高铁酸盐受化学性质不稳定的限制。高铁酸盐在水溶液或潮湿环境中非常不稳定,易分解;并且在酸性条件下氧气可以立即释放,在中性或弱碱性溶液中缓慢分解。因高铁酸盐的稳定性不佳,限制了超铁电池的广泛应用。因此提高高铁酸盐电池电化学性能的关键是保持稳定和持续放电。
[0003]
为提高高铁酸盐阴极的稳定性,现有技术中有人提出了以氯化锆(zrcl4)、二氧化锆(zro2)、三氧化二钇-二氧化锆(y2o
3-zro2)、酞菁(h2pc)等材料对高铁酸钾(k2feo4)进行包覆以提高高铁酸钾阴极的放电性能,但这些物质作为包覆材料时,mfeo4/zn电池的电容量仍存在增加不明显等问题。
[0004]
石墨烯是21世纪新兴的碳质材料,因其优异的电学、热学、力学、光学性能等,备受到人们的广泛关注,尤其是在电化学储能领域的应用。目前,氧化石墨烯(go)与化学还原石墨烯(crg)已经成功应用在锂离子电池、超级电容器、锂-空气电池中,且取得了不错的成果。然而,目前未见有使用化学还原石墨烯(crg)来包覆高铁酸盐作为阴极以提高超铁电池的稳定性以及放电性能的相关报道。
技术实现要素:[0005]
为了解决现有技术存在的技术问题,本发明提供了一种石墨烯修饰的高铁酸盐材料及其制备方法和应用。本发明方法以化学还原石墨烯(crg)作为包覆材料,通过共沉积法包覆于高铁酸盐表面,显著提高了高铁酸盐在潮湿环境和饱和koh溶液中的稳定性,以及与zn组成的碱性超铁电池在多种情况下的实际放电性能。
[0006]
为了实现上述目的,本发明在第一方面提供了一种石墨烯修饰的高铁酸盐材料的制备方法,所述方法包括如下步骤:
[0007]
(1)制备强酸性氧化石墨,用含有氮甲基吡咯烷酮和无水乙醇的混合液多次清洗所述强酸性氧化石墨,得到中性氧化石墨,然后用水将所述中性氧化石墨分散均匀,得到氧化石墨水分散液;
[0008]
(2)以抗坏血酸为还原剂,在超声辅助的水热条件下将所述氧化石墨水分散液中的氧化石墨还原成化学还原石墨烯,然后依次经过抽滤和干燥,得到化学还原石墨烯;
[0009]
(3)用步骤(2)得到的化学还原石墨烯配制化学还原石墨烯乙醇分散液,将高铁酸盐和所述化学还原石墨烯乙醇分散液通过共沉积法制得化学还原石墨烯包覆高铁酸盐的所述石墨烯修饰的高铁酸盐材料。
[0010]
优选地,所述高铁酸盐为高铁酸钾、高铁酸钠、高铁酸钡、高铁酸锂、高铁酸铯、高铁酸银、高铁酸锶中的一种或多种;优选的是,所述高铁酸盐为高铁酸钾。
[0011]
优选地,在步骤(1)中,所述强酸性氧化石墨与所述混合液中含有的氮甲基吡咯烷酮和无水乙醇的体积比为1:2:4。
[0012]
优选地,所述方法进一步还包括:将所述石墨烯修饰的高铁酸盐材料与所述化学还原石墨烯乙醇分散液进行多次共沉积得到具有不同化学还原石墨烯包覆量的石墨烯修饰的高铁酸盐材料的步骤。
[0013]
优选地,所述石墨烯修饰的高铁酸盐材料中含有的高铁酸盐与还原石墨烯的质量比为100:(0.8~5.2)。
[0014]
优选地,所述氧化石墨水分散液中含有的氧化石墨的浓度为0.05~0.2mg/l。
[0015]
优选地,所述化学还原石墨烯乙醇分散液中含有的化学还原石墨烯的浓度为0.05~0.12mg/ml。
[0016]
优选地,所述水热温度为24~60℃。
[0017]
本发明在第二方面提供了由本发明在第一方面所述的制备方法制得的石墨烯修饰的高铁酸盐材料。
[0018]
本发明在第三方面提供了由本发明在第一方面所述的制备方法制得的石墨烯修饰的高铁酸盐材料作为阴极材料在超铁电池中的应用。
[0019]
本发明与现有技术相比至少具有如下有益效果:
[0020]
(1)本发明方法创新性地利用氮甲基吡咯烷酮(nmp)和无水乙醇的混合液清洗强酸性氧化石墨,经过6-7次清洗就可以将ph不大于1的氧化石墨转化成中性,有效地提高了制备中性氧化石墨的效率。
[0021]
(2)本发明方法以化学还原石墨烯(crg)作为包覆材料,通过共沉积法包覆于高铁酸盐表面,显著提高了高铁酸盐在潮湿环境和饱和koh溶液中的稳定性,以及与zn组成的碱性超铁电池在多种情况下的实际放电性能。
[0022]
(3)本发明制得的石墨烯修饰的高铁酸盐材料在60天后,潮湿环境中crg包覆型k2feo4(5次)的纯度为46.7%,比未包覆k2feo4高出33.9%;饱和koh溶液中crg包覆型k2feo4(5次)的纯度为75.9%,比未包覆k2feo4高出25.6%;本发明制得的石墨烯修饰的高铁酸盐材料作为超铁电池阴极材料应用时,crg包覆型k2feo4(5次)与zn组成的碱性高铁电池在1775ω下的实际电容量和活性成分利用率比k2feo4分别高出比率为22.9%和22.8%,较mno2分别高出比率为33.4%和15.9%。
附图说明
[0023]
图1是本发明实施例1中的中性氧化石墨(go)和化学还原石墨烯(crg)的红外谱图(ftir谱图)。图中a为crg的ftir谱图,图中b为go的ftir谱图。
[0024]
图2是本发明实施例1中的中性氧化石墨(go)和化学还原石墨烯(crg)的x射线光电子能谱图(xps谱图)。图中a为go的xps谱图,图中b为crg的xps谱图。
[0025]
图3是本发明实施例1中的石墨粉、中性氧化石墨(go)和化学还原石墨烯(crg)的x射线衍射谱图(xrd谱图)。图中a为crg的xrd谱图,图中b为go的xrd谱图,图中c为石墨粉的xrd谱图。
[0026]
图4是本发明实施例1中的k2feo4和crg包覆型k2feo4(3次)的照片和sem图。图中a和c分别表示k2feo4的照片和sem图,图中b和d分别表示crg包覆型k2feo4(3次)的照片和sem图。
[0027]
图5是本发明实施例2中的k2feo4和crg包覆型k2feo4(3次)在不同环境中的纯度随时间的变化曲线图。图中a表示k2feo4+干燥空气,b表示crg包覆型k2feo4(3次)+饱和koh溶液,c表示k2feo4+饱和koh溶液,d表示crg包覆型k2feo4(3次)+潮湿空气,e表示k2feo4+潮湿空气下的纯度随时间的变化曲线。图中,横坐标time表示时间,单位为天(day),纵坐标purity(%)表示纯度,单位为%。
[0028]
图6是本发明实施例2中的k2feo4、crg包覆型k2feo4(1次、3次和5次)在潮湿空气下的纯度随时间的变化曲线图。图中a、b、c、d分别表示k2feo4、crg包覆型k2feo4(1次)、crg包覆型k2feo4(3次)、crg包覆型k2feo4(5次)在潮湿空气中的纯度随时间的变化曲线。
[0029]
图7本发明实施例3中的crg包覆型k2feo4在1775ω下的放电性能曲线图。图中a表示k2feo4的放电性能曲线,b表示crg包覆型k2feo4(1次)的放电性能曲线,c表示crg包覆型k2feo4(3次)的放电性能曲线,d表示crg包覆型k2feo4(5次)的放电性能曲线,e表示mno2的放电性能曲线。图中,横坐标sepcific capacity表示实际放电量,单位为mah,纵坐标voltage表示电压,单位为v。
[0030]
图8是本发明实施例3中的crg包覆型k2feo4在200ω和20ω下的放电性能曲线图。图中a表示crg包覆型k2feo4(5次)在200ω下的放电性能曲线,b表示crg包覆型k2feo4(5次)在20ω下的放电性能曲线。
具体实施方式
[0031]
为使本发明的目的、技术方案和优点更加清楚,下面将结合本发明实施例,对本发明的技术方案进行清楚、完整地描述。显然,所描述的实施例是本发明的一部分实施例,而不是全部的实施例。基于本发明中的实施例,本领域普通技术人员在没有做出创造性劳动的前提下所获得的所有其他实施例,都属于本发明保护的范围。
[0032]
本发明在第一方面提供了一种石墨烯修饰的高铁酸盐材料的制备方法,所述方法包括如下步骤:
[0033]
(1)制备强酸性氧化石墨(ph不大于1的氧化石墨),用含有氮甲基吡咯烷酮(nmp)和无水乙醇的混合液多次清洗所述强酸性氧化石墨,得到中性氧化石墨,然后用水将所述中性氧化石墨分散均匀,得到氧化石墨水分散液(go分散液);在本发明中,氧化石墨即氧化石墨烯,所述氧化石墨水分散液指的是以中性氧化石墨为分散质,以水为分散介质的分散液;在本发明中,例如可以以石墨粉为原料,通过hummers法制备所述强酸性氧化石墨;在本发明中,所述中性氧化石墨为清洗后未经过干燥的含水的中性氧化石墨(含水氧化石墨),这是因为,本发明人经过大量的实验后发现,在氧化石墨表面的大量稳定性差的含氧官能团在干燥过程中会发生快速分解,引起固体氧化石墨难以全部分散在水中,而以含水氧化石墨作为分散质后分散液的质量浓度能得到明显的提高。在本发明中,用含有氮甲基吡咯
烷酮和无水乙醇的混合液进行清洗的具体步骤例如可以为:往所述强酸性氧化石墨中按照一定的体积比加入nmp和无水乙醇的两体系混合液,并且搅拌5分钟后,再静止放置20分钟,再将放置20min的混合溶液真空抽滤,将得到的滤饼搅拌分散于100ml蒸馏水中,通过离心(8000r/min,15min)分离出酸性减弱的氧化石墨;最后重复使用nmp、无水乙醇和去离子水处理酸性减弱的氧化石墨,直到其ph=7左右,得到所述中性氧化石墨。
[0034]
(2)以抗坏血酸(还原型抗坏血酸,l-aa)为还原剂,在超声辅助的水热条件下将步骤(1)得到的所述氧化石墨水分散液(go分散液)中的氧化石墨(go)还原成化学还原石墨烯(crg),然后依次经过抽滤和干燥,得到化学还原石墨烯(crg);在本发明中,具体地,例如可以将所述氧化石墨水分散液置于水浴锅中,加入l-aa,在超声辅助下反应直到获得纯黑色crg水分散液,然后通过真空抽滤所述crg水分散液得到黑色滤饼,最后将黑色滤饼置于50℃真空干燥箱中干燥12h,即可得到黑色薄膜状固体crg。
[0035]
(3)用步骤(2)得到的化学还原石墨烯配制化学还原石墨烯乙醇分散液(crg乙醇分散液),将高铁酸盐和所述化学还原石墨烯乙醇分散液通过共沉积法制得化学还原石墨烯包覆高铁酸盐的所述石墨烯修饰的高铁酸盐材料;在本发明中,具体地,例如可以将高铁酸盐粉末例如高铁酸钾粉末(k2feo4)加入crg乙醇分散液中,并快速搅拌使得高铁酸钾悬浮于分散液中,20min后停止搅拌,再静止10min;然后将固液混合物通过真空抽滤除去剩余的乙醇,再将滤渣置于50℃下真空干燥箱内2h除去残留的乙醇,即可得到表面被crg包覆的k2feo4,并轻轻吹拂去除过量的crg。在本发明中,所述化学还原石墨烯乙醇分散液指的是以化学还原石墨烯为分散质,以乙醇(例如无水乙醇)为分散介质的分散液;在本发明中,当所述高铁酸盐为k2feo4时,也将石墨烯修饰的高铁酸盐材料记作crg包覆型k2feo4。
[0036]
众所周知,制备氧化石墨比较成熟的制备工艺包括brodie法、standenmaier法和hummers法,其中相对较安全和简单的hummers法被广泛使用,但通过hummers法制得是强酸性氧化石墨,而强酸性氧化石墨无法直接使用,所以需要除去其中吸附的酸性物质。现有技术中的除酸方法主要有离心水洗、抽滤水洗或渗透,但是离心水洗和渗透都会浪费大量的水和时间,并且无法进行大批量处理。另外在不断地抽滤洗水洗过程中,呈薄片状的氧化石墨会因吸附水分而发生体积膨胀,而体积膨胀的氧化石墨可以堵死滤膜上的微孔,所以通过真空抽滤彻底除去酸性物质也是十分困难的。本发明方法创新性地利用氮甲基吡咯烷酮(n-甲基吡咯烷酮)和无水乙醇的混合液清洗强酸性氧化石墨,相比于传统的过滤水洗、渗透和离心水洗,利用nmp溶液和乙醇溶液的两体系混合液清洗酸性氧化石墨6-7次,就可以将酸性氧化石墨的ph值从不大于1提高到6.5-7,本发明清洗酸性氧化石墨的方法更加高效、便捷和环保,有效地提高了制备中性氧化石墨的效率。
[0037]
此外,本发明方法以化学还原石墨烯(crg)作为包覆材料,通过共沉积法包覆于高铁酸盐表面,显著提高了高铁酸盐在潮湿环境和饱和koh溶液中的稳定性,以及与zn组成的碱性超铁电池在多种情况下的实际放电性能。
[0038]
根据一些优选的实施方式,所述高铁酸盐为高铁酸钾(k2feo4)、高铁酸钠(na2feo4)、高铁酸钡(bafeo4)、高铁酸锂(li2feo4)、高铁酸铯(cs2feo4)、高铁酸银(ag2feo4)、高铁酸锶(srfeo4)中的一种或多种;优选的是,所述高铁酸盐为高铁酸钾;在本发明中,所述高铁酸钾例如可以通过次氯酸盐氧化法(一步法)制备得到。
[0039]
根据一些优选的实施方式,在步骤(1)中,所述强酸性氧化石墨与所述混合液中含
有的氮甲基吡咯烷酮和无水乙醇的体积比为1:2:4。
[0040]
根据一些优选的实施方式,所述方法进一步还包括:将所述石墨烯修饰的高铁酸盐材料与所述化学还原石墨烯乙醇分散液进行多次共沉积得到具有不同化学还原石墨烯包覆量的石墨烯修饰的高铁酸盐材料的步骤。在本发明中,具体地,例如将所述石墨烯修饰的高铁酸盐材料粉末加入新配制的crg乙醇分散液中,并快速搅拌使得所述石墨烯修饰的高铁酸盐材料悬浮于分散液中,20min后停止搅拌,再静止10min;然后将固液混合物通过真空抽滤除去剩余的乙醇,再将滤渣置于50℃下真空干燥箱内2h除去残留的乙醇,即可得到被化学还原石墨烯二次包覆的所述石墨烯修饰的高铁酸盐材料;重复该步骤进行多次共沉积,即可得到被化学还原石墨烯多次包覆的所述石墨烯修饰的高铁酸盐材料,即得到多种具有不同化学还原石墨烯包覆量的石墨烯修饰的高铁酸盐材料。在本发明中,crg会包覆于k2feo4表面的原因可能是,在极性很低的乙醇溶液中,表面带有负电荷的k2feo4会与表面带有正电荷的crg相互吸引,使crg包覆在k2feo4表面,发生共沉积现象;当crg包覆型k2feo4被再次投入到新的crg分散液中后,分散液的平衡会被破坏,引起原本分散的crg会在再次与crg包覆型k2feo4发生团聚,因此使用crg乙醇分散液重复处理k2feo4可以得到不同crg包覆量的k2feo4。
[0041]
根据一些优选的实施方式,所述石墨烯修饰的高铁酸盐材料中含有的高铁酸盐与化学还原石墨烯的质量比为100:(0.8~5.2)。
[0042]
根据一些优选的实施方式,所述氧化石墨水分散液中含有的氧化石墨的浓度为0.05~0.2mg/l(例如0.05、0.1、0.15或0.2mg/l),优选为0.15mg/l。
[0043]
根据一些优选的实施方式,所述化学还原石墨烯乙醇分散液中含有的化学还原石墨烯的浓度为0.05~0.12mg/ml(例如0.05、0.1或0.12mg/ml),优选为0.1mg/ml。
[0044]
根据一些优选的实施方式,所述水热温度(水热条件下的反应温度)为24~60℃(例如24℃、36℃、48℃或60℃),优选为36℃。本发明人发现,提高水热温度可以明显提高还原型抗坏血酸(l-aa)对氧化石墨(go)的还原速度,36℃、48℃和60℃时的化学反应速率约为24℃时的2倍、3倍和3倍。但是当反应温度超过36℃后,含氧量逐渐减低的go会在水中团聚形成的无定型碳,并且反应温度越高,团聚现象越明显。而本发明人发现在超声辅助的水热条件下还原可以有效防止在36℃下制备的化学还原石墨烯(crg)水分散液中出现无定型碳,并且也会非常明显地提升还原速度,约为24℃时的15倍以上。但是当反应温度超过48℃后,超声辅助对阻止无定型碳形成的能力已经不足。因此,本发明人发现,在本发明中,制备crg的最佳反应条件是,将go水分散液置于36℃超声辅助下还原2h。
[0045]
本发明在第二方面提供了由本发明在第一方面所述的制备方法制得的石墨烯修饰的高铁酸盐材料。
[0046]
本发明在第三方面提供了由本发明在第一方面所述的制备方法制得的石墨烯修饰的高铁酸盐材料作为阴极材料在超铁电池中的应用。
[0047]
下面结合实施例对本发明作进一步说明。这些实施例只是就本发明的优选实施方式进行举例说明,本发明的保护范围不应解释为仅限于这些实施例。
[0048]
实施例1:石墨烯修饰的高铁酸盐材料的制备
[0049]
①
往强酸性氧化石墨中按照体积比为强酸性氧化石墨:nmp:乙醇=1:2:4的体积比加入nmp和无水乙醇的两体系混合液,并且搅拌5分钟后,再静止放置20分钟;再将放置
20min的混合溶液真空抽滤,把得到的滤饼搅拌分散于100ml蒸馏水中,通过离心(8000r/min,15min)分离出酸性减弱的氧化石墨;最后重复使用nmp、无水乙醇和去离子水处理酸性减弱的氧化石墨(每次酸性氧化石墨:nmp:乙醇的体积比为1:2:4),直到其ph=7左右,得到所述中性氧化石墨;最后用水将所述中性氧化石墨分散均匀,得到氧化石墨的质量浓度为0.15mg/ml的氧化石墨水分散液(go分散液);其中,所述强酸性氧化石墨以石墨粉为原料,通过hummers法制得。
[0050]
②
将浓度为0.15mg/ml的所述氧化石墨水分散液置于36℃水浴锅中,加入抗坏血酸l-aa,使得分散液中l-aa的浓度为30mg/l,在超声辅助下反应2h直到获得纯黑色crg水分散液,然后通过真空抽滤所述crg水分散液得到黑色滤饼,最后将黑色滤饼置于50℃真空干燥箱中干燥12h,即可得到黑色薄膜状固体crg,并研磨成粉末。
[0051]
③
配制crg的质量浓度为0.1mg/ml化学还原石墨烯乙醇分散液(crg乙醇分散液)20ml;将100mg研磨均匀的高铁酸钾(k2feo4)粉末加入到所述crg乙醇分散液中,并快速搅拌使k2feo4悬浮于分散液中,20min后停止搅拌,再静止10min;然后将固液混合物通过真空抽滤除去剩余的乙醇,再将滤渣置于50℃下真空干燥箱内2h除去残留的乙醇,即可得到表面被crg包覆的k2feo4,并轻轻吹拂去除过量的crg。将已经被go包覆1次的k2feo4重复以上包覆步骤即可以得到不同crg包覆量的k2feo4(具有不同化学还原石墨烯包覆量的石墨烯修饰的高铁酸盐材料)。包覆型crg的质量数据如表1所示。其中,k2feo4为通过次氯酸盐氧化法制备得到的纯度为94.7%的k2feo4晶体。
[0052]
表1:k2feo4和crg包覆型k2feo4的质量数据
[0053]
包覆次数k2feo4(mg)crg包覆型k2feo4(mg)包覆百分比1100100.80.8%3100102.72.7%5100105.25.2%
[0054]
在本实施例中,通过红外光谱(ftir)、x射线光电子能谱分析(xps)和x射线衍射(xrd)对得到的crg的化学结构和晶体结构进行了表征:与氧化石墨相比,crg的ftir图谱中部分含氧峰明显消失,例如,如图1所示,crg在1730cm-1
(o-c=o或c=o的伸缩振动)、1224cm-1
(o-c-o的伸缩振动)、1051cm-1
(c-o的伸缩振动)和3391cm-1
(-oh键的伸缩振动)处吸收峰的消失和减弱可以证明l-aa可以有效的将氧化石墨还原成crg,但是在1388cm-1
处新出现的c-oh吸收峰则说明仍有少量的含氧官能团残留在crg中;与氧化石墨相比,xps图谱中含氧峰的强度和面积明显变小,例如,如图2所示,这证明l-aa可以有效地引起go中的c-o/c-o-c发生开环反应,进而将go还原成crg;与氧化石墨相比,xrd图谱中层间距变小和导电性明显增强,例如,如图3所示,氧化石墨的特征衍射峰出现在2θ=11.4
°
,层间距为0.794nm,在经过l-aa还原后,氧化石墨的特征衍射峰已经消失,并在2θ=24.5
°
(间距为0.37nm)处出现了新的衍射峰,其位置与石墨的特征(002)衍射峰(2θ=26.1
°
,间距为0.34nm)位置相近,但是峰型扁平,crg的层间距小于氧化石墨,但大于石墨烯的理论层间距值(0.335nm),说明l-aa去除了crg中大部分含氧官能团,但仍有少量的含氧官能团残留在crg的层隙之间,并使crg的平面电子共轭体系得到了一定程度的重建。
[0055]
在本实施例中,对k2feo4和crg包覆型k2feo4(3次)进行了扫描电子显微镜表征
(sem表征),如图4所示:相比k2feo4,crg包覆型k2feo4(3次),在crg乙醇分散液中,通过共沉积法可以在k2feo4表面形成一定厚度的crg包覆层,并且外观上表现为由带有金属光泽的晶体颗粒(图4a)转变成体积更大的暗黑色颗粒(图4b),在sem下的形貌为堆积在一起的不规则团块(团球状)。
[0056]
实施例2:crg包覆对k2feo4稳定性的影响实验
[0057]
采用实施例1中的k2feo4和crg包覆型k2feo4(3次)进行实验:将三份k2feo4分别置于常温干燥空气中、潮湿空气环境(潮湿环境)中和饱和koh溶液环境中,并将两份crg包覆型k2feo4(3次)分别置于潮湿空气环境中和饱和koh溶液环境中,研究k2feo4、crg包覆型k2feo4(3次)在不同环境中纯度随时间的变化情况,结果如图5所示。
[0058]
由图5可知:在常温干燥空气中,k2feo4的纯度在60d内仅下降了1.1%,说明k2feo4在干燥空气中十分稳定。然而将k2feo4和crg包覆型k2feo4(3次)在潮湿环境中放置60d后,纯度都发生了大幅度下降,分别下降到12.8%和40.8%,分别下降了81.9%和53.9%。另外,为模拟超铁电池环境,向k2feo4中滴加饱和koh溶液,k2feo4的纯度在60天内由最初的94.7%下降到了50.3%,下降了44.4%,而crg包覆型k2feo4(3次)的纯度则小幅度下降到了75.9%,下降了18.8%。在潮湿环境和饱和koh环境中crg包覆型k2feo4(3次)的纯度变化曲线一直位于k2feo4之上,说明crg包覆可以明显地提升k2feo4的稳定性,这可能的原因是包覆在k2feo4表面的大量crg具有优秀的疏水性能,可以将大部分的水分隔离在外,进而防止k2feo4发生快速地大规模水解反应。
[0059]
本实施例进一步研究了crg包覆次数对k2feo4在潮湿环境下稳定性的影响,如图6所示:在放置60d后crg包覆型k2feo4(5次)的纯度约为46.7%,比k2feo4高出33.9%(差值),但是与crg包覆型k2feo4(3次)的纯度相近;这说明包覆的次数越多,crg包覆型k2feo4的稳定性越好,但过多的包覆会变得没有明显效果。虽然经过crg包覆后,k2feo4的纯度在潮湿环境下仍有明显的下降,这说明crg在k2feo4表面形成的包覆层只能在一定时间内防止电解液中水分的大量浸入,但这相比现有其它材料包覆的k2feo4,已经明显提高了k2feo4在潮湿环境下的稳定性。
[0060]
在本发明中,通过亚铬酸盐法分析高铁酸钾固体样品的纯度,高铁酸钾纯度的计算公式为:
[0061][0062]
式中:p-高铁酸钾的纯度;v-所消耗的硫酸亚铁铵溶液fe(nh4)2(so4)2体积(ml);n-fe(nh4)2(so4)2当量浓度;m
w-k2feo4分子量=198.04;m-k2feo4样品质量或crg包覆型k2feo4样品质量。
[0063]
实施例3:crg包覆型k2feo4在常温恒电阻下的放电性能测试实验
[0064]
将k2feo4或crg包覆型k2feo4与乙炔黑混轧成薄片后作为阴极,以zn箔为阳极,以饱和氢氧化钾为电解液,以玻璃纤维隔膜为电池隔膜,组成cr2032型纽扣电池,具体的原料配比为:k2feo4或crg包覆型k2feo4:乙炔黑:zn=100mg:10mg:200mg。
[0065]
测试cr2032型纽扣电池在恒定电阻1775ω负载下的放电性能曲线和活性成分利用率,测试方法为:电池在恒定电阻下放电,通过电池测试系统采集时间、电压和电流数据,并使用origin软件将时间和电流曲线进行分段拟合,拟合模型为2次多项式;再通过定积分
计算时间-电流曲线与横坐标围成图形的面积,即实际放电量(实际电容量),再绘制成实际电容量-电压曲线,即放电性能曲线,且k2feo4活性成分有效利用率的计算公式如下:
[0066][0067]
式中:a:活性成分的有效利用率;c:100mg k2feo4或crg包覆型k2feo4实际放电量;40.6:100mg纯度为100%的k2feo4的理论电容量;94.7%:所用k2feo4的纯度。
[0068]
本实施例得到的k2feo4、crg包覆型k2feo4(n次包覆)(n=1、3和5)和mno2/zn纽扣电池在1775ω负载下的放电性能曲线如图7所示,放电性能曲线和活性成分利用率数据如表2所示。
[0069]
表2:crg包覆型k2feo4在1775ω下放电的放电效率和活性成分利用率。
[0070]
阴极材料实际放电量(mah)活性成分利用率(%)k2feo425.666.5crg包覆型k2feo4(1次)29.576.6crg包覆型k2feo4(3次)32.383.9crg包覆型k2feo4(5次)33.286.2mno222.172.5
[0071]
注:表2中的crg包覆型k2feo4采用的是实施例1中制得的crg包覆型k2feo4(1次)、crg包覆型k2feo4(3次)和crg包覆型k2feo4(5次)材料。
[0072]
由图7和表2可知:当截止电压为0.8v时,100mg k2feo4的实际放电量约为25.6mah,起止电压为1.61v,放电平台电压为1.56
±
0.05v和活性成分利用率约为66.5%。而当经过crg包覆之后,k2feo4的实际放电量随着crg包覆量的增加而明显增加。当n=5时,crg包覆的k2feo4的实际放电量可以达到33.2mah,起止电压上升为1.73v,放电平台为1.57
±
0.05v,活性成分利用率更是达到了86.2%。为了与碱性锌锰电池形成对比,将纽扣电池的阴极材料替换为mno2,实验结果表明100mg mno2的实际放电量约为22.1mah,起止电压为1.52v,放电平台为1.28
±
0.05v和活性物质利用率为72.5%。与crg包覆型k2feo4(5次)相比,mno2的电容量比其低的比率为33.4%,放电平台电压低的比率为18.9%和活性成分利用率低的比率为15.9%,说明crg包覆型k2feo4(5次)比mno2电化学性能更加优异。
[0073]
本实施例进一步研究了负载对crg包覆型k2feo4的放电性能影响,测试了crg包覆型k2feo4(5次)在200ω和20ω下的放电性能曲线和活性成分利用率,结果如图8和表3所示。
[0074]
表3:crg包覆型k2feo4(5次)在200ω和20ω下放电的放电效率和活性成分利用率。
[0075][0076]
由图8和表3可知,在200ω和20ω的负载下crg包覆型k2feo4(5次)和mno2的实际放
电量都发生了明显的减小,且放电平台发生了明显的降低。当负载为200ω时,crg包覆型k2feo4(5次)的实际放电容量比负载为1775ω时降低的比率为12.3%,放电平台电压降低的比率为8.2%,活性成分利用率降低的比率为12.4%。当负载为20ω时,crg包覆型k2feo4(5次)的实际放电容量、放电平台电压和活性成分利用率又发生了进一步的减小。同时作为对比的mno2,在200ω和20ω下的实际放电容量、放电平台电压和活性成分利用率则比crg包覆型k2feo4(5次)更低。可见即使在重负荷放电下,crg包覆型k2feo4(5次)的放电性能也高于mno2。
[0077]
最后说明的是:以上实施例仅用以说明本发明的技术方案,而非对其限制;尽管参照前述实施例对本发明进行了详细说明,本领域普通技术人员应当理解:其依然可以对各实施例所记载的技术方案进行修改,或者对其中部分技术特征进行等同替换;而这些修改或者替换,并不使技术方案的本质脱离本发明各实施例技术方案的精神和范围。