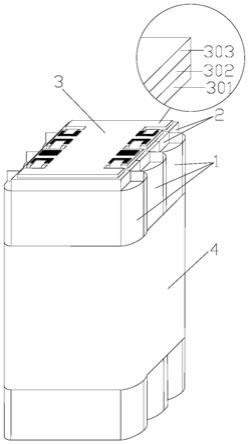
[0001]
本发明涉及一种锂离子电芯组装技术,具体涉及一种小型软包装锂离子电池储能系统。
背景技术:[0002]
目前,在储能市场领域存在一些小型储能单元市场,比如用于工商业、公共服务等的照明备用电源,应急灯备用电源,消防等的指示灯备用电源等。该类储能电源主要存在这样几个技术特征:
①
要求能量密度高。该类电源一般有较小的体积限制,同时又要求工作时间长,因而需求能量密度较高。
②
绝大部分要求能够便携。
③
放电倍率及放电电流较小。一般0.2c~0.5c就能满足要求。
④
容量较小,一般几十瓦时到一千瓦时之间。
⑤
电压要求较低,5v~24v的电压区间即可。
⑥
要求具有较低的成本。
[0003]
锂离子电池能够满足上述技术需求,同时由于清洁环保的要求,锂离子电池模组目前占据了该类产品的主要市场。由于能量密度及成本的限制,软包锂离子电池模组在市场份额中的比重越来越大。
[0004]
小型储能软包锂离子电池模组一般由电芯、保护板、外壳等构成。该模组在生产过程中一般采取的工艺技术及缺点包括:
①
保护板及电芯分别固定在壳体内部的不同位置,保护板与电池之间通过导线连接。此种结构中,保护板和电芯分别占据一定空间,间隙较大,降低了模组能量密度。导线连接方式会导致焊点增多,模组内阻增大。
②
模组由若干支单体电芯串并联而成,串并联时电芯极耳之间直接焊接在一起或者通过导线、镍带等焊接连接,焊接点很多,增大了模组内阻,电芯一致性变差。
③
在串联时,模组正负极耳反向放置,易出现接触短路现象,增大了安全隐患。
④
模组制备时导线种类(颜色、限流、长度)繁多,焊接时焊印种类多标准多,大大增加了工艺复杂性,容错性差,生产成本高。
技术实现要素:[0005]
本发明提供了一种小型软包装锂离子电池储能系统,通过自主开发具有串并联线槽及与电芯极耳一一对应的多焊接口设计的保护板,采用各部件紧凑装配的组装工艺,开发出了一种锂离子电芯组装成储能电源模组的技术。
[0006]
本发明是这样来实现的,一种小型软包装锂离子电池储能系统,主要由单体电芯、绝缘泡棉、模组保护板、热缩套管、双面胶、电芯顶边、正极耳和负极耳组成;其特征在于:若干支单体电芯成一排阵列排列,单体电芯之间通过双面胶连接,整个若干支单体电芯外面包裹热缩套管连接固定,单体电芯的电芯顶边之间的间隙位置填充绝缘泡棉,绝缘泡棉底部通过双面胶与单体电芯连接固定;模组保护板位于绝缘泡棉上方,模组保护板两侧有若干板脚卡在相邻两个电芯顶边之间;电芯顶部设有正极耳和负极耳,正极耳和负极耳通过焊接接口与模组保护板焊接连接成整体。
[0007]
进一步地,小型储能模组产品容量及电压较小,所需要的单体电芯数量较少,充放电的倍率一般不高于0.5c,说明电芯充放电时温升不大,再加上模组对于整体能量密度有
严苛的高要求,所以,本发明采取了组装最紧凑、空隙最小、模组保护板与若干单体电芯为不分离的结构。电芯单排阵列排列,周围不加装任何支架,模组保护板直接装配在电芯顶部,整个模组浑然一体,空隙最小,可以在保证模组热安全的前提下获得最高体积能量密度。
[0008]
进一步地,若干支单体电芯排列方式为同向排列,即所有单体电芯的相同极性极耳在同一侧。电芯同向排列在批量生产工程上具有纠错的优点。传统工艺上在电芯串联时,为节省导线,会把电芯正反错位排列,这样会有极耳触碰造成正负极短路的风险。电芯同向排列,操作简单,即使前后极耳触碰也不会造成短路。
[0009]
进一步地,所述若干支单体电芯之间的连接方式为:通过双面胶固定或者外面包裹热缩套管固定,两种方案中的一种或两种连接。
[0010]
进一步地,所述焊接接口,可与电芯极耳通过电阻焊、激光焊、锡焊中的一种或两种焊接方式连接。三种焊接方式均能满足模组的强度要求,电阻焊与激光焊不需要额外的辅助焊料,物料成本低,在批量生产时效率更高,但模组返修时焊点难以打开,售后成本更高;锡焊需要额外的焊料,物料成本较高,批量生产效率较低,但返修简单。综上,可根据不同的产品要求选择焊接方式。
[0011]
进一步地,所述绝缘泡棉的厚度比电芯顶边高度大0.5~1mm,即绝缘泡棉厚度=电芯顶边高度+0.5~1mm;绝缘泡棉的宽度为单体电芯厚度的一半,即绝缘泡棉宽度=单体电芯厚度*1/2;绝缘泡棉长度为单体电芯的宽度减去电芯厚度,即绝缘泡棉长度=单体电芯宽度-单体电芯厚度。电芯顶边的边缘是铝塑膜的切断断面,露出金属铝的风险很高,极耳在弯折的时候如果碰到露出的金属铝,会造成短路或者铝层腐蚀,引发安全风险。绝缘泡棉厚度高于电芯顶边可有效防止这种情况发生。
[0012]
进一步地,所述模组保护板为一种印刷电路板(pcb),其在厚度方向上为三层结构,包括绝缘层、上部配件附着层和下部配件附着层,三层结构在模组保护板制备时通过热压固定在一起,模组保护板在功能上由三个区块构成,包括功能区、串并联布线区、板脚焊接区。模组保护板底部的绝缘层将模组保护板与电芯顶部进行绝缘分离,防止由于碰撞、挤压等造成保护板配件与顶边接触,造成短路或者电芯外壳破损,引发安全风险。
[0013]
进一步地,所述功能区为模组保护板控制元件的集中区域,是模组保护板主要功能发生区,包括升压、限流、过充过放保护、均衡、过温保护等,模组的输入和输出模块也在此区域。
[0014]
进一步地,所述串并联布线区,通过把串并联导线集成在模组保护板上,并与焊接接口相连接,实现模组电芯串并联,同时导线接入功能区,实现保护板对电芯的保护控制功能。
[0015]
进一步地,所述板脚焊接区,每个板脚上分布有1~2个焊接接口,每个接口与电芯极耳一一对应。把每只电芯的极耳与一一对应的焊接接口连接,然后通过集成在板上的串并联导线进行串并联连接,同时导线接入监测、控制、输入输出等元器件,完成模组的整体功能。
[0016]
本发明的优点是:(1)采取了组装最紧凑、空隙最小、保护板与电芯不分离的结构,在保证模组热安全的前提下获得最高体积能量密度。(2)电芯同向排列,操作简单,防止极耳触碰短路,降低安全风险。(3)通过集成在板上的串并联导线进行串并联连接,减少了焊
点,节省了导线,降低了物料成本及模组内阻。(4)整个模组制备过程,焊点种类单一,无导线连接操作,工艺简单可靠,容错性高,生产效率高,生产成本低。
附图说明
[0017]
图1为本发明的模组整体示意图。
[0018]
图2为本发明的单体电芯示意图。
[0019]
图3为本发明的三串模组俯视示意图。
[0020]
图4为本发明的三并模组俯视示意图。
[0021]
图5为本发明的三并三串模组俯视示意图。
[0022]
图中,1单体电芯、2绝缘泡棉、3模组保护板、4热缩套管、5双面胶、101电芯顶边、102正极耳、103负极耳、301绝缘层、302上部配件附着层、303下部配件附着层、304功能区、305串并联布线区、306板脚焊接区、307焊接接口、308串并联导线。
具体实施方式
[0023]
以下结合附图说明对本发明的实施例作进一步详细描述,但实施例并不用于限制本发明,凡是采用本发明的相似结构及其相似变化,均应列入本发明的保护范围。
[0024]
实施例1
[0025]
如图1、图2、和图3所示,一种三只电芯串联的软包装锂离子电池模组,三支单体电芯(1)成一排阵列排列,电芯之间通过双面胶(5)或者外面包裹热缩套管(4)连接固定;电芯顶边(101)之间的间隙位置填充绝缘泡棉(2),绝缘泡棉(2)底部通过双面胶与单体电芯(1)连接固定;模组保护板(3)位于绝缘泡棉(2)上方,两侧有若干板脚卡在相邻两个电芯顶边之间;电芯正极耳(102)和负极耳(103)通过焊接接口(307)与模组保护板(3)焊接连接成整体。
[0026]
其中,所述三支单体电芯(1)排列方式为同向排列,即所有电芯的相同极性极耳在同一侧。
[0027]
其中,所述三支单体电芯(1)之间的连接方式为:通过双面胶(5)固定或者外面包裹热缩套管(4)固定,两种方案中的一种或两种连接。
[0028]
其中,所述焊接接口(307),可与电芯极耳通过电阻焊、激光焊、锡焊中的一种或两种焊接方式连接。
[0029]
其中,所述绝缘泡棉(2)厚度=电芯顶边高度+0.5~1mm。绝缘泡棉(2)的宽度=单体电芯厚度*1/2。绝缘泡棉(2)长度=单体电芯宽度-单体电芯厚度。
[0030]
其中,所述模组保护板(3)为一种印刷电路板(pcb),其在厚度方向上为三层结构,包括绝缘层(301),上部配件附着层(302)及下部配件附着层(303),三层在保护板制备时通过热压固定在一起。模组保护板(3)在功能上由三个区块构成,包括功能区(304),串并联布线区(305),板脚焊接区(306)。
[0031]
其中,所述功能区(304)为保护板控制元件的集中区域,是保护板主要功能发生区,包括升压、限流、过充过放保护、均衡、过温保护等,模组的输入和输出模块也在此区域。
[0032]
其中,所述板脚焊接区(306),每个板脚上分布有1~2个焊接接口(307),每个接口与电芯极耳一一对应。
[0033]
其中,所述串并联布线区(305),通过把串并联导线(308)集成在保护板上,并与焊接接口(307)相连接,实现模组电芯串并联,同时导线接入功能区(304),实现保护板对电芯的保护控制功能。
[0034]
实施例2
[0035]
如图1、图2、和图4所示,一种三只电芯并联的软包装锂离子电池模组,三支单体电芯(1)成一排阵列排列,电芯之间通过双面胶(5)或者外面包裹热缩套管(4)连接固定;电芯顶边(101)之间的间隙位置填充绝缘泡棉(2),泡棉底部通过双面胶与单体电芯(1)连接固定;模组保护板(3)位于绝缘泡棉(2)上方,两侧有若干板脚卡在相邻两个电芯顶边之间;电芯正极耳(102)和负极耳(103)通过焊接接口(307)与模组保护板(3)焊接连接成整体。
[0036]
其中,所述三支单体电芯(1)排列方式为同向排列,即所有电芯的相同极性极耳在同一侧。
[0037]
其中,所述三支单体电芯(1)之间的连接方式为:通过双面胶(5)固定或者外面包裹热缩套管(4)固定,两种方案中的一种或两种连接。
[0038]
其中,所述焊接接口(307),可与电芯极耳通过电阻焊、激光焊、锡焊中的一种或两种焊接方式连接。
[0039]
其中,所述绝缘泡棉(2)厚度=电芯顶边高度+0.5~1mm。绝缘泡棉(2)的宽度=单体电芯厚度*1/2。绝缘泡棉(2)长度=单体电芯宽度-单体电芯厚度。
[0040]
其中,所述模组保护板(3)为一种印刷电路板(pcb),其在厚度方向上为三层结构,包括绝缘层(301),上部配件附着层(302)及下部配件附着层(303),三层在保护板制备时通过热压固定在一起。模组保护板(3)在功能上由三个区块构成,包括功能区(304),串并联布线区(305),板脚焊接区(306)。
[0041]
其中,所述功能区(304)为保护板控制元件的集中区域,是保护板主要功能发生区,包括升压、限流、过充过放保护、均衡、过温保护等,模组的输入和输出模块也在此区域。
[0042]
其中,所述板脚焊接区(306),每个板脚上分布有1~2个焊接接口(307),每个接口与电芯极耳一一对应。
[0043]
其中,所述串并联布线区(305),通过把串并联导线(308)集成在保护板上,并与焊接接口(307)相连接,实现模组电芯串并联,同时导线接入功能区(304),实现保护板对电芯的保护控制功能。
[0044]
实施例3
[0045]
如图1、图2、和图5所示,一种九只电芯三并三串的软包装锂离子电池模组,九支单体电芯(1)成一排阵列排列,电芯之间通过双面胶(5)或者外面包裹(4)热缩套管连接固定;电芯顶边(101)之间的间隙位置填充绝缘泡棉(2),泡棉底部通过双面胶与单体电芯(1)连接固定;模组保护板(3)位于绝缘泡棉(2)上方,两侧有若干板脚卡在相邻两个电芯顶边之间;电芯正极耳(102)和负极耳(103)通过焊接接口(307)与模组保护板(3)焊接连接成整体。
[0046]
其中,所述九支单体电芯(1)排列方式为同向排列,即所有电芯的相同极性极耳在同一侧。
[0047]
其中,所述九支单体电芯(1)之间的连接方式为:通过双面胶(5)固定或者外面包裹(4)热缩套管固定,两种方案中的一种或两种连接。
[0048]
其中,所述焊接接口(307),可与电芯极耳通过电阻焊、激光焊、锡焊中的一种或两种焊接方式连接。
[0049]
其中,所述绝缘泡棉(2)厚度=电芯顶边高度+0.5~1mm。绝缘泡棉(2)的宽度=单体电芯厚度*1/2。绝缘泡棉(2)长度=单体电芯宽度-单体电芯厚度。
[0050]
其中,所述模组保护板(3)为一种印刷电路板(pcb),其在厚度方向上为三层结构,包括绝缘层(301),上部配件附着层(302)及下部配件附着层(303),三层在保护板制备时通过热压固定在一起。模组保护板(3)在功能上由三个区块构成,包括功能区(304),串并联布线区(305),板脚焊接区(306)。
[0051]
其中,所述功能区(304)为保护板控制元件的集中区域,是保护板主要功能发生区,包括升压、限流、过充过放保护、均衡、过温保护等,模组的输入和输出模块也在此区域。
[0052]
其中,所述板脚焊接区(306),每个板脚上分布有1~2个焊接接口(307),每个接口与电芯极耳一一对应。
[0053]
其中,所述串并联布线区(305),通过把串并联导线(308)集成在保护板上,并与焊接接口(307)相连接,实现模组电芯串并联,同时导线接入功能区(304),实现保护板对电芯的保护控制功能。