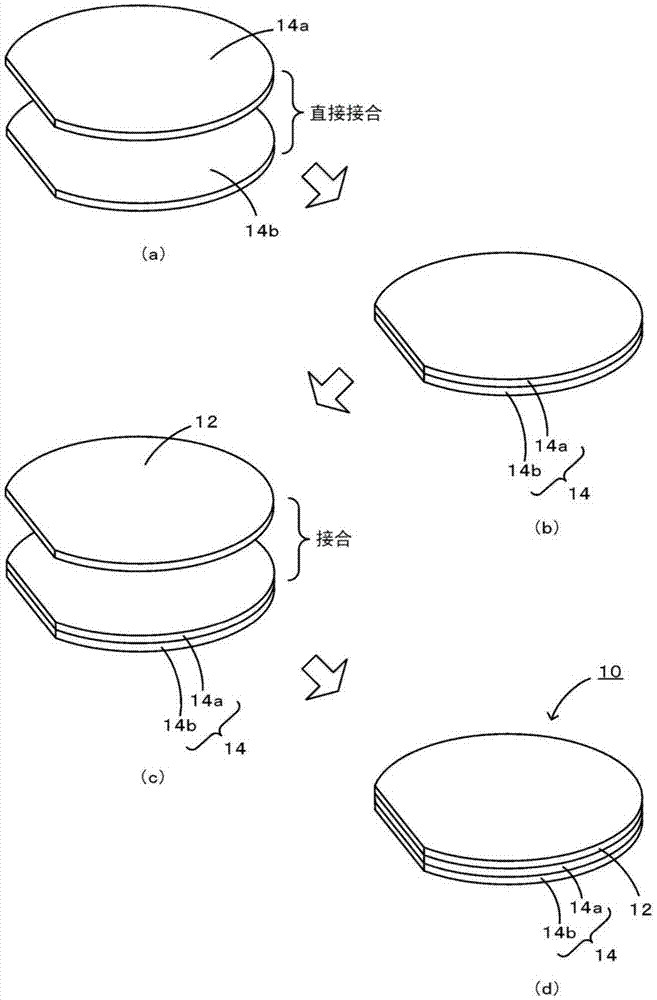
本发明涉及复合基板、弹性波装置以及弹性波装置的制造方法。
背景技术:
:近年来,为了改善弹性波装置的温度特性,使用在热膨胀系数小的支撑基板上粘合薄压电基板的复合基板。例如,专利文献1公开了一种复合基板,其具有通过由环氧粘着剂形成的粘着层将作为压电基板的LT基板(LT为钽酸锂的简称)与作为支撑基板的硅基板粘合在一起的结构。在使用这种复合基板制造弹性波装置时,存在如下问题。首先,由于复合基板随温度变化而产生较大的翘曲,故在经历各种工序温度的弹性波装置的制造过程中,存在图形的精度劣化,以及复合基板的自动操作变困难的问题。其次,存在复合基板的强度较低,以及在制造弹性波装置时的加热工序中产生基板开裂的问题。为了解决这些问题,例如,可以在专利文献1的复合基板中,增加支撑基板的厚度。通过简单地增加支撑基板的厚度,可提高刚性,抑制复合基板的翘曲。此外,也降低了因基板翘曲而导致的损坏。或者,专利文献2中提出,在支撑基板中的其与压电基板的接合面的相反一侧的表面上,设置补偿层,该补偿层实质上具有与压电基板相等的热膨胀系数,以及与压电基板具有相等的厚度。在这种复合基板中,由于压电基板和补偿层在温度变化时发生相同的伸展,故可抑制复合基板的翘曲。现有技术文献专利文献专利文献1:日本专利特开2007-150931号公报专利文献2:美国专利第7408286号说明书技术实现要素:本发明要解决的问题然而,在专利文献1的复合基板中,如果增加支撑基板的厚度例如约500μm,则虽然解决了上述问题,但由于使用该复合基板制造的弹性波装置的高度过高,故违背了薄型化的趋势,商业价值下降。因此,需要通过研磨来减薄制造的弹性波装置的支撑基板的背面。然而,研磨成本很高,导致弹性波装置的成本增加。另一方面,在专利文献2的复合基板中,由于在支撑基板的背面增加了补偿层,故存在使用其制造的弹性波装置的成本增加的问题。本发明的主要目的在于解决这些问题,同时实现复合基板的翘曲的降低以及强度的提高,抑制制造弹性波装置时的制造成本的增加。解决问题的方法本发明为了实现上述主要目的而采用了如下方法。本发明的复合基板是将压电基板与热膨胀系数比该压电基板低的支撑基板粘合在一起所形成的复合基板,所述支撑基板通过以刀片可剥离的强度将由相同材料制成的第1基板和第2基板以直接接合方式接合在一起来形成,并以所述第1基板中的其与所述第2基板的接合面的相反一侧的表面,与所述压电基板粘合在一起。本发明的弹性波装置的制造方法包括如下工序:(a)制造上述复合基板;(b)在所述复合基板中的所述压电基板的表面上形成用于弹性波装置的电极;(c)用刀片从所述第1基板上剥离除去所述第2基板;(d)将所述复合基板切成方块获得弹性波装置。本发明的弹性波装置通过上述本发明的弹性波装置的制造方法获得。发明效果在本发明的复合基板中,作为支撑基板,是通过以刀片可剥离的强度,将由相同材料制成的第1基板与第2基板以直接接合的方式接合在一起来形成的。于是,与仅使用第1基板作为支撑基板的情况相比,可增加支撑基板的厚度。因此,可将随温度变化而产生的复合基板的翘曲抑制得较小,以及还可提高复合基板的强度。此外,在制得弹性波装置之后,通过使用刀片从第1基板上剥离除去第2基板,可容易地降低支撑基板的厚度。于是,与通过研磨使厚支撑基板减薄的情况相比,其所需的成本较低。因此,可抑制制造弹性波装置时的制造成本增加。在制造本发明的复合基板时,可重复使用被除去的第2基板,这也可抑制成本。在本发明的弹性波装置的制造方法中,通过如下工序获得弹性波装置:制造上述本发明的复合基板,在该复合基板中的压电基板的表面上形成用于弹性波装置的电极,使用刀片从第1基板上剥离除去第2基板,然后切成方块。在形成用于弹性波装置的电极之后,通过用刀片从第1基板上剥离除去第2基板,可容易地降低支撑基板的厚度。于是,与通过研磨使厚支撑基板减薄的情况相比,其所需的成本较低。因此,可抑制制造弹性波装置时的制造成本增加。附图说明[图1]示意地显示复合基板10的剖面图。[图2]示意地显示复合基板10的制造工序的剖面图。[图3]示意地显示弹性波装置30的制造工序的剖面图。符号说明10复合基板12压电基板14支撑基板14a第1基板14b第2基板30弹性波装置(弹性表面波装置)31电极32,34IDT电极36反射电极具体实施方式接下来,基于附图对本发明的实施方式进行说明。图1为示意地显示本发明实施方式的复合基板10的剖面图。该复合基板10具有压电基板12和支撑基板14。压电基板12是可传播弹性波的基板。作为该压电基板12的材料,可例举钽酸锂(LT)、铌酸锂(LN)、铌酸锂-钽酸锂固溶体单晶、水晶、硼酸锂、氧化锌、氮化铝、硅酸镓镧(LGS)、钽酸镓镧(LGT)等。在这些中,优选LT或LN。LT和LN因其弹性表面波的传播速度较快并且机电耦合系数较大而适合作为弹性波装置用于高频和宽带频率。压电基板12的尺寸没有特别限定,例如直径为50-150毫米,厚度为0.2-50μm。支撑基板14的热膨胀系数小于压电基板12的热膨胀系数,支撑基板14经由有机粘着层或者通过直接接合被接合在压电基板12的背面上。由于支撑基板的热膨胀系数小于压电基板12的热膨胀系数,故可抑制温度变化时的压电基板12的尺寸变化,并且可抑制将复合基板10作成弹性波装置使用时频率特性的温度变化。该支撑基板14是通过以刀片可剥离的强度将由相同材料制成的第1基板14a和第2基板14b以直接接合方式接合在一起来形成的。此外,支撑基板14以第1基板14a中的其与第2基板14b的接合面的相反一侧的表面与压电基板粘合在一起。作为支撑基板14的材料,可例举硅、蓝宝石、氮化铝、氧化铝、硼硅酸玻璃、石英玻璃等。优选硅。此外,支撑基板14的尺寸,例如,直径为50-150mm,厚度为200-1200μm。第1基板14a以及第2基板14b的尺寸分别为,例如,直径为50-150mm,厚度为100-600μm。此外,优选支撑基板14的杨氏模量大于压电基板12的杨氏模量。用于压电基板12和支撑基板14的典型材料的热膨胀系数如表1所示。表1接下来,使用图2对制造这种复合基板10的方法进行说明。图2为示意地显示复合基板10的制造工序的剖面图。首先,准备圆盘状的由相同材料制成的第1基板14a和第2基板14b(参见图2(a)),通过以直接接合方式接合这两个基板14a、14b来制造支撑基板14(参见图2(b))。作为直接接合这两个基板14a、14b的方法,如下方法被列举。也就是说,首先,清洗两个基板14a、14b的接合面,除去附着在该接合面上的污垢。接着,通过在两个基板14a、14b的接合面上照射氩气等非活性气体的离子束,除去残留杂质(氧化膜和吸附物等)并活化该接合面。然后,在真空中、常温下,将两个基板14a、14b接合在一起。两个基板14a、14b的接合强度是插入厚度为100微米的刀片时的剥离强度。为了形成这样的强度,通过实验来确定接合面的表面粗糙度、离子束的照射时间、接合时的压力等。例如,在两个基板14a、14b均为硅基板的情况中,由于通常硅材料本身的强度为2-2.5J/m2,故使两个基板14a、14b中的Si与Si的结合能为小于该硅材料本身的强度的值,例如0.05-0.6J/m2。如果其低于0.05J/m2,那么在弹性波装置的制造中存在剥离的风险,如果其高于0.6J/m2,那么可能不能顺利地插入刀片。接着,将支撑基板14与压电基板12接合在一起(参见图2(c))。具体地说,将支撑基板14中的第1基板14a的表面与压电基板12的背面接合在一起。接合方法可以为直接接合,也可以经由有机粘着层进行接合。因为已对直接接合进行了说明,故在此省略说明。只是,确定接合面的表面粗糙度、离子束照射时间,以及粘合时的压力等,以使接合强度等于或大于硅材料本身的强度2-2.5J/m2。在经由有机粘着层接合的情况中,首先,在支撑基板14的表面和压电基板12的背面的一个面或两个面上均匀地涂布有机粘着剂,在支撑基板和压电基板这两者重叠的状态下,通过固化有机粘着剂进行接合。如上所述,获得复合基板10(参见图2(d))。直接接合方法没有特别限定,除了在此所示的方法以外,还可以为使用等离子体的方法,使用中性原子束的方法等。其次,关于使用该复合基板10制造弹性波装置30的方法,使用图3进行如下说明。图3为示意地显示弹性波装置30的制造工序的剖面图。首先,制备复合基板10(参见图3(a))。由于已使用图2对此进行了说明,故在此省略说明。然后,在复合基板10中的压电基板12的表面上形成用于弹性波装置的电极31(参见图3(b))。压电基板12的表面被分区以形成多个弹性波装置,在对应于各个弹性波装置的位置处,利用光刻技术形成用于弹性波装置的电极31。此外,如图3(d)所示,电极31由IDT电极32、34和反射电极36构成。接着,使用厚度为100μm的刀片从第1基板14a上剥离除去第2基板14b(参见图3(c))。剥离掉第2基板14b后的第1基板14a的表面(剥离面)因其表面粗糙度Ra足够小而不需要特别的研磨,但可以视需要进行研磨。此外,第1基板14a的剥离面上除了包含来自第1基板14a的材料的元素之外,还包含来自在直接接合时使用的真空室的材料的元素。例如,在真空室的材料为不锈钢的情况中,包含来自其的Fe元素和Cr元素。从第1基板14a上剥离的第2基板14b可在下次制造复合基板10时被重复使用。最后,通过沿着分区切成方块,获得多个弹性波装置30(参见图3(d))。当向输入端的IDT电极32施加高频率信号时,获得的弹性波装置30在电极之间产生电场,从而激发弹性表面波并传播到压电基板12上。然后,可以从沿着传播方向设置的输出端的IDT电极34中获得传播的弹性表面波作为电信号。换句话说,弹性波装置30为弹性表面波装置。根据如上所述的本发明的实施方式,因为使用通过接合由相同材料制成的第1基板14a与第2基板14b而形成的支撑基板作为支撑基板14,故与仅使用第1基板14a作为支撑基板14的情况相比,可增加支撑基板14的厚度。因此,可将因温度变化而产生的复合基板10的翘曲抑制得较小,以及还可提高复合基板10的强度。此外,在制造用于弹性波装置的电极31之后,通过使用刀片从第1基板14a上剥离除去第2基板14b,可容易地减小支撑基板14的厚度。因此,与通过研磨减薄厚度与支撑基板14相同的一体的支撑基板(bulksupportingsubstrate)的情况相比,实现了低成本。因此,可抑制弹性波装置30的制造成本增加。因为可在下次制造复合基板10时重复使用被除去的第2基板14b,故就该点来说,可抑制成本。此外,本发明不限于上述实施方式,显然能够以属于本发明的技术范围的各种方式进行实施。实施例[实施例1]准备两个直径为100毫米、厚度为250微米的硅基板作为第1基板和第2基板。各个硅基板的两个表面均精加工成镜面。在清洗各个硅基板的表面并除去表面污垢之后,将它们放入由不锈钢制造的真空室中。将真空室内调节成1×10-6Pa以上、不足1×10-7Pa的真空气氛,以及向其内的各个硅基板的表面上照射Ar离子束180秒。接着,在重叠各个硅基板的离子束照射面以使它们彼此接触之后,通过施加500kgf负载来接合这两个硅基板,获得总厚度为500微米的支撑基板。除了该支撑基板之外,还制造两个表面被精加工成镜面的直径为100毫米、厚度为230微米的LT基板作为压电基板。然后,再次清洗LT基板和支撑基板,并放入真空室中。将真空室内调节成1×10-6Pa以上、不足1×10-7Pa的真空气氛,并向其内的LT基板的表面和支撑基板的表面(第1基板的表面)照射Ar离子束300秒。然后,在重叠LT基板的离子束照射面和支撑基板的离子束照射面以使它们彼此接触后,通过施加2000kgf负载来接合这两个基板,获得具有三层结构的复合基板。将作为该复合基板中的压电基板的LT基板研磨至约20微米。测得研磨前后的复合基板的翘曲量为约25微米。此外,测得研磨后的基板在100℃下加热前后的翘曲量为约250微米。[比较例1]除了使用一个直径为100毫米、厚度为250微米的硅基板作为支撑基板之外,使用与实施例1相同的方式制造复合基板。测得研磨前后的复合基板的翘曲量为约60微米。此外,测得其在100℃下加热前后的翘曲量为约1500微米。[翘曲量概要]表2概括了实施例1和比较例1的翘曲量的结果。由表1清楚可见,与比较例1相比,实施例1因支撑基板较厚而具有大幅降低翘曲的效果。[表2]LT基板研磨前后的翘曲量100℃下加热前后的翘曲量实施例1约25微米约250微米比较例1约60微米约1500微米[实施例2]在实施例1的研磨后的复合基板上进行用于弹性波装置(弹性表面波装置)的电极的图案化之后,在Si与Si的接合部中插入刀片,进行接合基板的剥离。于是,获得接合LT基板和Si基板(第1基板)的两层结构的复合基板,以及单层的Si基板(第2基板)。通过AFM(原子力显微镜)观察两层结构的复合基板的剥离面以及单层Si基板的剥离面,晶片的表面粗糙度Ra为约0.4纳米,即使不研磨也具有充分的表面状态。此外,通过使用能量分散性X射线谱(EDS),对先前的剥离面进行元素分析,除Si元素外,还检测出Fe元素以及Cr元素。Fe元素和Cr元素是来自真空室的元素。这些元素在直接接合第1基板与第2基板时被混入。使用裂纹开口(CrackOpening)法测量每单位面积的结合能。LT基板与Si基板(第1基板)之间的结合能为约2.5J/m2,Si基板(第1基板)与Si基板(第2基板)之间的结合能为约0.2J/m2。通常认为硅材料本身的强度为2-2.5J/m2,在LT基板与Si基板(第1基板)之间具有该硅材料本身的强度以上的结合能,而Si基板(第1基板)与硅基板(第2基板)之间的结合能小于该硅材料本身的强度,这表明可通过刀片进行剥离。此外,裂纹开口法是在粘合界面中插入刀片并根据刀片进入距离测定接合界面的表面能的方法。使用的刀片是羽安全剃刀株式会社制造的商品号99077(刀刃的长度:约37毫米,厚度:0.1毫米,材料:不锈钢)。本申请要求2013年2月19日申请的日本专利申请第2013-30161号的优先权,在此通过引用将其全部内容结合到本说明书中。工业应用性本发明的复合基板可用于SAW滤波器等的弹性波装置。当前第1页1 2 3