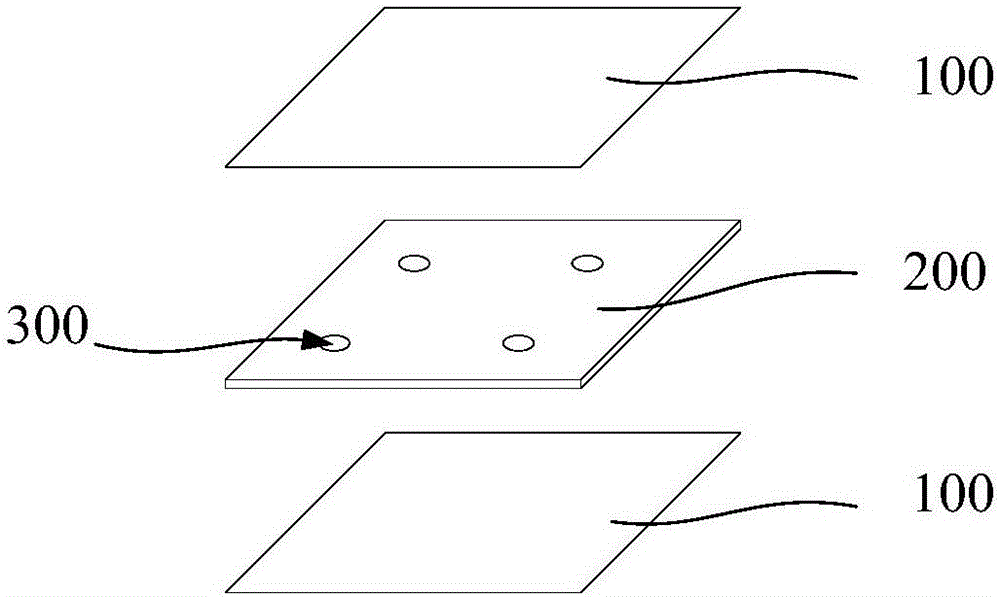
本发明涉及一种导电介质,特别是涉及导电浆料及其制备方法和用途。
背景技术:
:印制电路板(pcb线路板),是电子元器件电气连接的提供者。它的发展已有100多年的历史了,其主要优点是大大减少布线和装配的差错,提高了自动化水平和生产劳动率。贯穿孔(via)是多层pcb的重要组成部分之一,每一层板子在黏合前必须要先钻孔与镀铜。如果不经过这个步骤,那么就没办法实现互相连接。在根据钻孔需求由机器设备钻孔之后,孔璧里头必须经过电镀(镀通孔技术,plated-through-holetechnology,pth)。在孔璧内部作金属处理后,可以让内部的各层线路能够彼此连接。孔壁镀铜都会在化学制程中完成,需采用大量的水,因而有多种重金属废水和有机废水排出,成分复杂,处理难度较大。这些存在于废液、废水中的金属如不经处理就排放,既造成了浪费又污染了环境。近年来对于印制电路板孔填充用导电浆料的研究日益增多,在助焊剂和树脂中添加低熔点金属粉和高熔点金属粉,在一定条件下加热,低熔点金属粉首先熔化,溶解高熔点金属粉从而发生合金化,实现孔内的电导通。这种新工艺避免了以往化学镀铜带来的废水处理问题,是目前多层线路板领域研究的热点之一。目前常用的金属粉为锡粉和铜合金粉等。目前技术方案中使用至少两种金属粉,低熔点的金属先熔化,然后浸润溶解高熔点金属粉从而发生合金化,因此,高熔点金属粉表面的氧化层会影响低熔点金属对其表面的润湿性,从而影响两种金属粉合金化的进行。而使用银包覆的铜合金粉,虽然抗氧化性有提高,但是会带来成本增加的问题。因此寻找合适的方法提高金属粉末的抗氧化性,以及如何加快低温金属熔化后与高温金属形成合金化的速度,是这个领域面临的技术难题。技术实现要素:鉴于以上所述现有技术的缺点,本发明的目的在于提供一种导电浆料及其制备方法和用途,用于解决现有技术中印刷电路板中贯穿孔中填充材料的成本高,成型速度慢的问题。为实现上述目的及其他相关目的,本发明是通过以下技术方案获得的。本发明提供一种导电浆料,所述导电浆料包括以下原料组分及重量百分含量:助焊剂5~20wt%表面镀锡的铜粉和/或表面镀锡的铜合金粉80~95wt%。优选地,所述助焊剂为10~20wt%。助焊剂是在焊接工艺中能除去金属表面形成的氧化膜,帮助和促进焊接过程,同时具有保护作用、阻止氧化反应的化学物质。所述助焊剂,可以使用钎料膏中已经公知的助焊剂成分。在一个优选的实施例中,所述助焊剂包括溶剂、赋形剂和活性剂。本申请中的助焊剂为粘稠膏状,便于印刷使用。优选地,以所述溶剂、赋形剂和活性剂的总质量为基准计,所述助焊剂包括以下百分含量的原料组分:赋形剂30wt%-70wt%活性剂5wt%-20wt%余量为溶剂。优选地,所述赋形剂为35wt%~50wt%。更优选地,所述所述赋形剂为35wt%~45wt%。优选地,所述活性剂为5wt%~15wt%。本申请中溶剂为醇、酮、酯、醚、烷烃、芳香族系溶剂中的一种或多种。如,所述醇选自乙醇,乙二醇,异丙醇、松油醇、甘油等;所述酯选自乙酸乙酯等;所述醚选自乙二醇乙醚,乙二醇单丁醚、二乙二醇单丁醚,二丙二醇甲醚,二丙二醇乙醚,二丙二醇丙醚等。本申请中赋形剂为松香及其改性衍生物(如聚合松香,富马酸改性松香,马来酸改性松香,酚醛改性松香,乙醇酸改性松香,丙烯酸改性松香,松香改性苯酚)、环氧树脂、酚醛树脂、丙烯酸树脂、聚酯树脂、聚酰亚胺、聚酰胺、纤维素系树脂、萜烯树脂,聚乙烯醇,聚乙二醇或聚乙烯吡咯烷酮中一种或多种。本申请中常用活性剂为有机酸、有机胺或胺的氢卤酸盐等,也可以选择其中多种的混合。如,有机酸选自苹果酸、柠檬酸,月桂酸、硬脂酸,油酸,棕榈酸、戊二酸,己二酸,辛二酸,壬二酸,癸二酸,枞酸,马来酸,富马酸,抗坏血酸的一种或多种。有机胺选自单乙醇胺、二乙醇胺,三乙醇胺和苯胺中的一种或多种。胺的氢卤酸盐选自乙胺盐酸盐,二乙胺盐酸盐,二甲胺盐酸盐,环己胺盐酸盐,三乙醇胺盐酸盐,谷氨酸盐酸盐和乙胺氢溴酸盐中的一种或多种。另外,实际使用中,可以添加常规触变剂(石蜡,聚酰胺类有机物,蓖麻油及其衍生物,如聚酰胺蜡,氢化蓖麻油,聚酰胺改性氢化蓖麻油等),缓蚀剂(苯并三氮唑,咪唑类),表面活性剂(op-10),防腐剂,抗氧化剂等,提高浆料的印刷性以及稳定性,添加量一般不超过所述溶剂、赋形剂和活性剂的总质量的10wt%。本申请中所述表面镀锡的铜粉是指具有核壳结构的锡包覆铜粉。所述表面镀锡铜粉具有核壳结构,即具有铜核及包覆在同核外的锡壳,核壳结构的表面镀锡铜粉的粒径不超过12μm,优选为1μm~12μm,如可以为1~8μm、2~8μm、2~10μm、3~10μm、2~11μm、1μm~11μm、9μm~12μm等;优选地,表面镀锡铜粉的粒径为3μm~8μm,如可以为3μm~5μm、5μm~7μm、4μm~8μm等等。其中,核壳结构的表面镀锡铜粉的铜核直径与核壳结构总直径的比值为0.60~0.90,如可以为0.60、0.65、0.70、0.75、0.80、0.85和0.90等,优选为0.67~0.88之间。本申请中所述表面镀锡的铜合金粉是指具有核壳结构的锡包覆铜合金粉。所述表面镀锡的铜合金粉具有核壳结构,即具有铜合金核及包覆铜合金核外的锡壳结构,核壳结构的总粒径不超过12μm,优选为1μm~12μm,如可以为1~8μm、2~8μm、2~10μm、3~10μm、2~11μm、1μm~11μm、9μm~12μm等;优地,表面镀锡的铜合金的粒径3μm~8μm,如可以为3μm~5μm、5μm~7μm、4μm~8μm等等。其中核壳结构的表面镀锡铜合金粉的铜合金核直径与核壳结构总直径的比值为0.60~0.90,如可以为0.60、0.65、0.70、0.75、0.80、0.85和0.90等,优选为0.67~0.88。本申请中所述铜合金可以是铜镍合金。优选地,合金中镍为10wt%~15wt%。本申请中所述铜合金也可以是铜锰合金。优选地,合金中锰为10wt%~15wt%。本申请中所述铜合金优选为铜镍合金。本申请中还公开如上述所述导电浆料的制备方法,所述制备方法为将各原料组分混合均匀制备获得。优选地,混合后还包括研磨处理,可以避免浆料中金属粒子的团聚现象,达到更好的分散效果。本申请还公开了如上述所述导电浆料在印刷电路板中的用途。优选地,所述用途为采用上述所述导电浆料填充印刷电路板中的贯穿孔,再经过升温熔化并在加压作用下形成具有电连接作用的过孔导体。优选地,首先在一定压力下,升温至150℃~230℃之间,使得浆料中助焊剂成分起作用,去除金属锡表面氧化物;然后升温到230℃以上,保持压保持一段时间。在此期间,金属锡首先熔化成为熔融态,熔解铜/铜合金生成金属间化合物,形成过孔导体,此过孔导体可以连接绝缘层树脂两侧的铜箔,同时在压力条件下,也实现了树脂绝缘层与铜箔粘合。本发明还公开了一种印刷电路板,所述印刷电路板包括若干个金属箔层和夹设在所述金属箔层之间的树脂绝缘层,所述树脂绝缘层上设有若干贯穿的贯穿孔;所述树脂绝缘层中的贯穿孔上填充有采用如上述所述导电浆料形成的过孔导体;树脂绝缘层两侧的金属箔层通过所述过孔导体实现电连接。优选地,所述金属箔层为铜箔,其作为导电层。本申请中金属箔的厚度及树脂绝缘层的厚度均可以按照产品需要进行定制。本发明还公开了一种如上述所述的印刷电路板基板的制备方法,包括如下步骤:a)在树脂绝缘层上形成贯穿孔;b)在贯穿孔内填充导电浆料;c)然后采用金属箔配置在所述树脂绝缘层的两侧;d)经加温压合形成印刷线路板基板。步骤a)中,可以采用现有技术中对树脂层进行打孔的技术手段在树脂绝缘层上形成贯穿孔。优选地,步骤a)中,形成贯穿孔的方式可以为机械钻孔或者二氧化碳气体激光钻孔。所述贯穿孔的直径可以根据具体需要进行设定。优选地,步骤b)中,采用网版印刷方法在贯穿孔内填充导电浆料。步骤d)中加热升温是指在一定压力下升温。优选地,步骤d)中,加温至温度为150℃~400℃。更优选地,步骤d)中,加温至150℃~300℃。更优选地,在一定压力下,先加温至150℃~230℃,使得浆料中助焊剂成分起作用,去除金属锡表面氧化物;然后保持压力升温到230℃以上,优选接近但是不超过所述树脂绝缘层的熔点温度。优选地,步骤d)中,压力为0.5~5mpa。步骤c)中,所述加温压合过程可以在真空热压机中进行。在此期间,金属锡首先熔化成为熔融态,熔解铜/铜合金生成金属间化合物,形成过孔导体,此过孔导体可以连接绝缘层树脂两侧的铜箔,同时在压力条件下,也实现了树脂绝缘层与铜箔粘合。优选地,将所述导电浆料填充到贯穿孔中,在一定压力下,升温至150℃~230℃之间,使得浆料中助焊剂成分起作用,去除金属锡表面氧化物;然后升温到230℃以上加压保持一段时间形成过孔导体。优选地,升温至230℃以上时,温度接近但是不超过所述树脂绝缘层的熔点温度。优选地,所述树脂绝缘层为熔点在250℃以上的热塑性树脂。如选自聚酰亚胺(简写为pi),液晶聚合物(简写为lcp),聚醚酮树脂(简写为peek),聚苯硫醚(简写为pps),聚苯醚(简写为ppo),聚四氟乙烯(简写为ptfe)中的一种或多种。优选为液晶聚合物(简写为lcp)。本发明还公开了一种印刷电路板的制备方法,包括如下步骤:1)利用化学刻蚀对单面贴覆有铜箔的树脂绝缘层板均进行表面铜箔图形化处理;2)对单面贴覆有铜箔的树脂绝缘层板的树脂层钻孔形成盲孔或通孔;3)在盲孔或通孔内填充上述导电浆料;4)将若干个经上述处理后的单面贴覆有铜箔的树脂绝缘板进行对位层叠,并固定;5)经加温压合形成印刷线路板。在一种印刷电路板的制备方法中,步骤2)中钻孔通过通过激光或机械方法在指定位置进行钻孔形成盲孔或通孔。步骤4)中,固定采用铆钉固定。步骤5)中,加温压合部分如上述所述,即加温压合时,包括如下特征中的一种或多种:在一定压力下先升温至150℃~230℃,再保持压力升温至230℃以上;压力为0.5~5mpa。本发明的有益效果:本申请采用表面镀锡的铜粉和/或表面镀锡的铜合金粉,避免了铜粉/铜合金粉表面的氧化层产生,另外,锡镀层直接与铜/铜合金表面接触,在加热过程中,首先熔化的锡使得铜/铜合金的熔解及合金化变得更容易进行,不仅加快了合金化的速度,也使合金化反应更完全,提高了孔连接的可靠性。附图说明图1显示为本发明实施例1中的印刷电路板未形成过孔导体时的结构示意图。图2显示为本申请实施例1中的印刷电路板形成过孔导体时的结构示意图。图3显示为本申请实施例中的印刷电路板形成过孔导体后的爆炸结构示意图。图1和图2中元件标号说明100金属箔层200树脂绝缘层300贯穿孔400由导电浆料形成的过孔导体具体实施方式以下由特定的具体实施例说明本发明的实施方式,熟悉此技术的人士可由本说明书所揭露的内容轻易地了解本发明的其他优点及功效。在进一步描述本发明具体实施方式之前,应理解,本发明的保护范围不局限于下述特定的具体实施方案;还应当理解,本发明实施例中使用的术语是为了描述特定的具体实施方案,而不是为了限制本发明的保护范围。下列实施例中未注明具体条件的试验方法,通常按照常规条件,或者按照各制造商所建议的条件。当实施例给出数值范围时,应理解,除非本发明另有说明,每个数值范围的两个端点以及两个端点之间任何一个数值均可选用。除非另外定义,本发明中使用的所有技术和科学术语与本
技术领域:
技术人员通常理解的意义相同。除实施例中使用的具体方法、设备、材料外,根据本
技术领域:
的技术人员对现有技术的掌握及本发明的记载,还可以使用与本发明实施例中所述的方法、设备、材料相似或等同的现有技术的任何方法、设备和材料来实现本发明。实施例1如图1和图2所示,本实施例中,印刷电路板包括lcp树脂绝缘层200及分别压覆于其两侧的金属箔层100,金属箔层100具体为铜箔,以作为导电层。本申请中铜箔的厚度及lcp树脂绝缘层的厚度均可以按照产品需要进行定制。本申请本实施例中,金属箔层100的厚度为18μm。lcp树脂绝缘层200的厚度为50μm。孔内填充由导电浆料合金化形成的过孔导体。具体实现方式为:首先准备厚度为50μm的lcp树脂片,利用机械钻孔或者二氧化碳气体激光在指定位置钻孔,形成直径100μm的通孔,然后用高锰酸钾溶液去除孔内树脂残胶。利用网版印刷方法在孔内填充导电浆料,在70℃烘箱内干燥30分钟,然后在lcp树脂片两面配置厚度18μm的单面粗糙化铜箔,粗糙面朝向lcp树脂一侧,并利用真空热压机进行高温压合,压合过程为:在4mpa压力下,先升温至220℃并保温10分钟,然后压力降低至1mpa,升温至290℃,保温保压20分钟,然后再降温至60℃以下,开模取出即得到一体化的印制线路板基板。然后可以根据需要在铜箔表面进行图案化,得到印制线路板产品。所述导电浆料按如下方法制备:取表面镀锡的铜粉90重量份,与10重量份的助焊剂搅拌混合均匀,然后利用三辊机研磨,得到所述的导电浆料。所述表面镀锡的铜粉为具有核壳结构的锡包覆铜粉,平均粒径3μm,其中铜核直径与核壳结构总直径的比值在0.80左右。本实施中所述助焊剂含聚乙二醇10份,松香35份,己二酸10份,乙二醇25份,乙二醇乙醚20份。导电性测试:测量单个贯穿孔内的过孔导体的电阻,均小于40mω。热循环测试:将样品-55℃/+125℃下30min进行1000个循环,测试单个通孔内的电阻。电阻值变化率小于25%;本申请中将样品在-55℃下放置30min,再在125℃下放置30min为一个循环;回流耐焊性:n2气氛条件下,加热到260℃,保持1min,降温到常温,测试电阻变化小于20%。对比例1对比例1中导电浆料按以下方法制备:取铜粉45重量份,纯锡粉45重量份,与10重量份的助焊剂搅拌混合均匀,然后利用三辊机研磨,得到所述的导电浆料。所述铜粉与锡粉平均粒径3μm,所述助焊剂采用实施例1中助焊剂。印制线路板基板制作过程与实施例1相同。测试:测量单个过孔内的过孔导体的电阻,大部分未导通(大于1000mω)。实施例2如图1和图2所示,本实施例中,印刷电路板包括lcp树脂绝缘层200及分别压覆于其两侧的金属箔层100,金属箔层100具体为铜箔,以作为导电层。本申请中铜箔的厚度及lcp树脂绝缘层的厚度均可以按照产品需要进行定制。本申请本实施例中,金属箔层100的厚度为18μm。lcp树脂绝缘层200的厚度为50μm。孔内填充由导电浆料合金化形成的过孔导体。具体实现方式为:首先准备厚度为50μm的lcp树脂片,利用机械钻孔或者二氧化碳气体激光在指定位置钻孔,形成直径100μm的通孔,然后用高锰酸钾溶液去除孔内树脂残胶。利用网版印刷方法在孔内填充导电浆料,在80℃烘箱内干燥30分钟,然后在lcp树脂片两面配置厚度18μm的单面粗糙化铜箔,粗糙面朝向lcp树脂一侧,并利用真空热压机进行高温压合,压合过程为:在4mpa压力下,先升温至220℃并保温10分钟,然后压力降低至1mpa,升温至290℃,保温保压20分钟,然后再降温至60℃以下,开模取出即得到一体化的印制线路板基板。也可以根据需要在铜箔表面进行图案化,得到印制线路板产品。所述导电浆料按如下方法制备:取表面镀锡的铜粉90重量份,与10重量份的助焊剂搅拌混合均匀,然后利用三辊机研磨,得到所述的导电浆料。所述表面镀锡的铜粉为具有核壳结构的锡包覆铜粉,平均粒径3μm,其中铜核直径与核壳结构总直径的比值在0.80左右。本实施中所述助焊剂含聚乙二醇5份,松香30份,苹果酸5份,己二酸10份,乙二醇35份,乙二醇乙醚15份。导电性测试:测量单个贯穿孔内的过孔导体的电阻,均小于40mω。热循环测试:将样品-55℃/+125℃下30min进行1000个循环,测试单个通孔内的电阻。电阻值变化率小于25%;本申请中将样品在-55℃下放置30min,再在125℃下放置30min为一个循环;回流耐焊性:n2气氛条件下,加热到260℃,保持1min,降温到常温,测试电阻变化小于20%。实施例3本实施例中,印刷电路板包括ppo材料的树脂绝缘层200及金属箔层100,金属箔层100具体为铜箔。本申请中铜箔的厚度及ppo树脂绝缘层的厚度均可以按照产品需要进行定制。本申请本实施例中,金属箔层100的厚度18μm。ppo材料的树脂绝缘层200的厚度为50μm。孔内填充由导电浆料合金化形成的导体。具体实现方式为:如图3所示,首先准备两张单面贴覆有铜箔的ppo树脂绝缘层板;ppo树脂绝缘层的厚度为50μm,金属箔层厚度18μm。分别利用化学蚀刻进行表面铜箔图形化,将树脂面朝上,利用二氧化碳气体激光在指定位置钻孔,形成直径100μm的盲孔,然后用等离子工艺去除贯穿孔内树脂残胶。得到树脂片a和b。再准备一张单面贴覆有铜箔的ppo树脂绝缘板,ppo材料的树脂绝缘板的厚度为50μm,金属箔层厚度18μm。分别利用化学蚀刻进行表面铜箔图形化,机械钻孔机在树脂绝缘层指定位置钻孔,形成直径100μm的通孔,然后用等离子工艺去除孔内树脂残胶。得到树脂片c。利用网版印刷方法在贯穿孔内填充导电浆料,在60℃烘箱内干燥30分钟,然后将这几层填孔完毕的树脂片精密对位层叠,铆钉固定后,利用真空热压机进行加温压合,压合过程为:在5mpa压力下,先升温至200℃并保温10分钟,然后压力降低至1.5mpa,升温至260℃,保温保压50分钟,然后再降温至60℃以下,开模取出即得到多层印制线路板产品。具体如图3爆炸效果所示。所述导电浆料按如下方法制备:取表面镀锡的铜镍合金粉90重量份,与10重量份的助焊剂搅拌混合均匀,然后利用三辊机研磨,得到所述的导电浆料。所述表面镀锡的铜镍合金粉为具有核壳结构的锡包覆铜镍合金粉(铜镍合金中铜镍重量比9:1)平均粒径8μm,其中铜镍合金核直径与核壳结构总直径的比值在0.88左右。本实施中所述助焊剂为所述助焊剂含聚乙二醇10份,松香30份,苹果酸5份,己二酸5份,乙二醇35份,乙二醇乙醚15份。导电性测试:测量单个贯穿孔内的过孔导体的电阻,均小于40mω。热循环测试:将样品-55℃/+125℃下30min进行1000个循环,测试单个通孔内的电阻。电阻值变化率小于25%;本申请中将样品在-55℃下放置30min,再在125℃下放置30min为一个循环;回流耐焊性:n2气氛条件下,加热到260℃,保持1min,降温到常温,测试电阻变化小于20%。实施例4如图1和图2所示,本实施例中,印刷电路板包括lcp树脂绝缘层200及分别压覆于其两侧的金属箔层100,金属箔层100具体为铜箔,以作为导电层。本申请中铜箔的厚度及lcp树脂绝缘层的厚度均可以按照产品需要进行定制。本申请本实施例中,金属箔层100的厚度为18μm。lcp树脂绝缘层200的厚度为50μm。孔内填充由导电浆料合金化形成的过孔导体。具体实现方式为:首先准备厚度为50μm的lcp树脂片,利用机械钻孔或者二氧化碳气体激光在指定位置钻孔,形成直径100μm的通孔,然后用高锰酸钾溶液去除孔内树脂残胶。利用网版印刷方法在孔内填充导电浆料,在70℃烘箱内干燥30分钟,然后在lcp树脂片两面配置厚度18μm的单面粗糙化铜箔,粗糙面朝向lcp树脂一侧,并利用真空热压机进行加温压合,加温压合过程为:在4mpa压力下,先升温至190℃并保温10分钟,然后压力降低至1mpa,升温至280℃,保温保压20分钟,然后再降温至60℃以下,开模取出即得到一体化的印制线路板基板。然后可以根据需要在铜箔表面进行图案化,得到印制线路板产品。所述导电浆料按如下方法制备:取表面镀锡的铜粉85重量份,与15重量份的助焊剂搅拌混合均匀,然后利用三辊机研磨,得到所述的导电浆料。所述表面镀锡的铜粉为具有核壳结构的锡包覆铜粉,平均粒径3μm,其中铜核直径与核壳结构总直径的比值在0.80左右。所述助焊剂含聚乙二醇10份,松香35份,苹果酸5份;乙二醇35份,乙二醇乙醚15份。导电性测试:测量单个贯穿孔内的过孔导体的电阻,均小于40mω。热循环测试:将样品-55℃/+125℃下30min进行1000个循环,测试单个通孔内的电阻。电阻值变化率小于25%;本申请中将样品在-55℃下放置30min,再在125℃下放置30min为一个循环;回流耐焊性:n2气氛条件下,加热到260℃,保持1min,降温到常温,测试电阻变化小于20%。实施例5如图1和图2所示,本实施例中,印刷电路板包括lcp树脂绝缘层200及分别压覆于其两侧的金属箔层100,金属箔层100具体为铜箔,以作为导电层。本申请中铜箔的厚度及lcp树脂绝缘层的厚度均可以按照产品需要进行定制。本申请本实施例中,金属箔层100的厚度为18μm。lcp树脂绝缘层200的厚度为50μm。孔内填充由导电浆料合金化形成的过孔导体。具体实现方式为:首先准备厚度为50μm的lcp树脂片,利用机械钻孔或者二氧化碳气体激光在指定位置钻孔,形成直径100μm的通孔,然后用高锰酸钾溶液去除孔内树脂残胶。利用网版印刷方法在孔内填充导电浆料,在70℃烘箱内干燥30分钟,然后在lcp树脂片两面配置厚度18μm的单面粗糙化铜箔,粗糙面朝向lcp树脂一侧,并利用真空热压机进行加温压合,加温压合过程为:在4mpa压力下,先升温至220℃并保温10分钟,然后压力降低至1mpa,升温至290℃,保温保压20分钟,然后再降温至60℃以下,开模取出即得到一体化的印制线路板基板。也可以根据需要在铜箔表面进行图案化,得到印制线路板产品。所述导电浆料按如下方法制备:取表面镀锡的铜粉80重量份,与20重量份的助焊剂搅拌混合均匀,然后利用三辊机研磨,得到所述的导电浆料。所述表面镀锡的铜粉为具有核壳结构的锡包覆铜粉,平均粒径3μm,其中铜核直径与核壳结构总直径的比值在0.80左右。所述助焊剂含聚乙二醇5份,松香35份,二乙醇胺5份;乙二醇35份,乙二醇乙醚20份。导电性测试:测量单个贯穿孔内的过孔导体的电阻,均小于40mω。热循环测试:将样品-55℃/+125℃下30min进行1000个循环,测试单个通孔内的电阻。电阻值变化率小于25%;本申请中将样品在-55℃下放置30min,再在125℃下放置30min为一个循环;回流耐焊性:n2气氛条件下,加热到260℃,保持1min,降温到常温,测试电阻变化小于20%。实施例6如图1和图2所示,本实施例中,印刷电路板包括lcp树脂绝缘层200及分别压覆于其两侧的金属箔层100,金属箔层100具体为铜箔,以作为导电层。本申请中铜箔的厚度及lcp树脂绝缘层的厚度均可以按照产品需要进行定制。本申请本实施例中,金属箔层100的厚度为18μm。lcp树脂绝缘层200的厚度为50μm。孔内填充由导电浆料合金化形成的过孔导体。具体实现方式为:首先准备厚度为50μm的lcp树脂片,利用机械钻孔或者二氧化碳气体激光在指定位置钻孔,形成直径100μm的通孔,然后用高锰酸钾溶液去除孔内树脂残胶。利用网版印刷方法在孔内填充导电浆料,在70℃烘箱内干燥30分钟,然后在lcp树脂片两面配置厚度18μm的单面粗糙化铜箔,粗糙面朝向lcp树脂一侧,并利用真空热压机进行高温压合,压合过程为:在4mpa压力下,先升温至220℃并保温10分钟,然后压力降低至1mpa,升温至290℃,保温保压20分钟,然后再降温至60℃以下,开模取出即得到一体化的印制线路板基板。然后可以根据需要在铜箔表面进行图案化,得到印制线路板产品。所述导电浆料按如下方法制备:取表面镀锡的铜粉85重量份,与15重量份的助焊剂搅拌混合均匀,然后利用三辊机研磨,得到所述的导电浆料。所述表面镀锡的铜粉为具有核壳结构的锡包覆铜粉,平均粒径3μm,其中铜核直径与核壳结构总直径的比值在0.80左右。所述助焊剂含聚乙二醇5份,松香30份,苹果酸5份,己二酸10份,乙二醇35份,乙二醇乙醚15份。导电性测试:测量单个贯穿孔内的过孔导体的电阻,均小于40mω。热循环测试:将样品-55℃/+125℃下30min进行1000个循环,测试单个通孔内的电阻。电阻值变化率小于25%;本申请中将样品在-55℃下放置30min,再在125℃下放置30min为一个循环;回流耐焊性:n2气氛条件下,加热到260℃,保持1min,降温到常温,测试电阻变化小于20%。上述实施例仅例示性说明本发明的原理及其功效,而非用于限制本发明。任何熟悉此技术的人士皆可在不违背本发明的精神及范畴下,对上述实施例进行修饰或改变。因此,举凡所属
技术领域:
中具有通常知识者在未脱离本发明所揭示的精神与技术思想下所完成的一切等效修饰或改变,仍应由本发明的权利要求所涵盖。当前第1页12