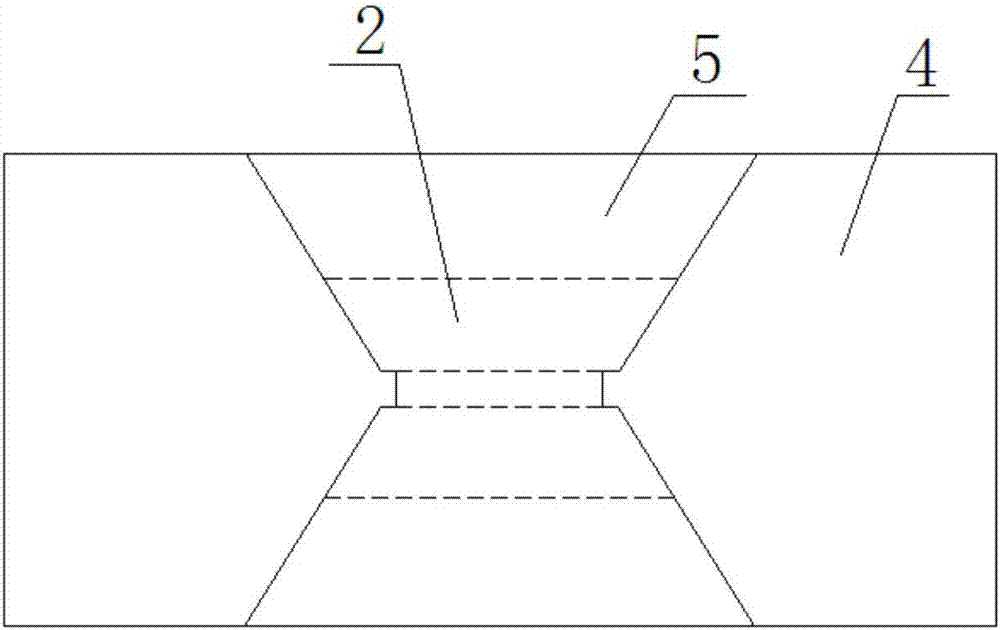
本发明属于电火工品技术领域,具体涉及一种片式合金箔点火电阻器及其制备方法。
背景技术:通常,桥丝式电火工品点火器是人们一直普遍使用的点火方式,是由一跟悬吊式电阻加热丝和两个电极相连组成,这种结构的点火器在较强的振动环境下,桥丝径向存在的拉伸作用容易导致桥丝发生变形,造成桥丝阻值改变从而影响点火器点火性能,并可能造成桥丝断裂及焊点破裂脱焊,造成点火器瞎火,极大的降低了桥丝式点火器的可靠性水平,且桥丝式点火器一般无法满足低发火能量和快速发火的要求。通常的金属薄膜桥点火器采用物理气相沉积方式直接沉积在基底上,基体采用聚酰亚胺基板,全套工艺采用溅射的方法进行制备。该方法能量低,一致性差,而且成本高。
技术实现要素:为解决上述技术问题,本发明提供了一种片式合金箔点火电阻器及其制备方法,该片式合金箔点火电阻器通过采用FR-4双面覆铜玻纤板做基体、镍铬合金箔做点火材料、聚酰亚胺做保护层,解决了桥丝式点火器可靠性低、无法满足低发火能量和快速发火的要求的问题。本发明通过以下技术方案得以实现。本发明提供的一种片式合金箔点火电阻器,包括基板、抗静电层、聚酰亚胺膜、电阻层、保护层、表背搭接层、铜层、镍层、锡层和焊盘;所述基板的上表面中部设置有抗静电层,下表面的两端分别设置有焊盘;所述聚酰亚胺膜设置在基板和抗静电层的上表面上,所述聚酰亚胺膜的上表面设置有电阻层,且所述电阻层的两端分别通过表背搭接层与焊盘连接,所述电阻层上还设置有保护层;所述铜层于保护层的两侧设置在电阻层上,且铜层将表背搭接层和焊盘的外表面覆盖,所述铜层的外表面上还依次设置有镍层和锡层。所述基板为FR-4双面覆铜玻纤板。所述基板的外形尺寸为50mm×60mm,厚度为0.35mm~0.6mm。所述抗静电层和焊盘的材料为Cu。所述抗静电层和焊盘的厚度为0.018mm~0.03mm。所述聚酰亚胺膜的厚度为0.025mm~0.04mm。所述电阻层的材料为NiCr合金或Ni-80.Cr-20合金。所述电阻层的厚度为0.0035mm~0.005mm。所述保护层的材料为光敏性聚酰亚胺。所述表背搭接层的材料为银浆。一种片式合金箔点火电阻器的制备方法,包括以下步骤:A、对基板进行清洗,去除表面的油污及杂质;B、通过光刻技术在基板的上表面的中部形成抗静电层,并在基板的下表面的两端形成焊盘;C、通过热压的方法将聚酰亚胺膜贴在基板和抗静电层的上表面;D、通过压合的方法将电阻层贴在聚酰亚胺膜的上表面;E、采用湿法刻蚀技术对电阻层进行刻蚀加工出桥丝,刻蚀的深度为电阻层的厚度;F、采用光刻技术在步骤E进行刻蚀处理的部位上形成保护层,且保护层还覆盖于电阻层的桥丝上;G、采用端面涂银的技术在基板的两端形成表背搭接层;H、根据产品尺寸要求,按常规方法对基片进行划片切割;I、通过电镀的方法依次形成铜层、镍层和锡层。所述步骤B中形成的抗静电层及焊盘的厚度为15~22μm。本发明的有益效果在于:采用成熟的半导体工艺技术和材料,在基板上制备出片式合金箔点火电阻器,通过选择散热系数更低的基板材料和热隔离材料,实现了片式合金箔点火电阻器焦耳热的更少散失,使得片式合金箔点火电阻器产生更多的用于加热药剂,从而提高了能量利用效率,有效降低了金箔点火电阻器的工作能量和点火时间。本发明的片式合金箔点火电阻器的点火电流1.5A,点火时间≤500μs,发火能量5毫焦,实现了小激发下快速发火;简单可靠,大大提高了点火电阻器工作的可靠性及一致性;生产工艺简单,具有靠性高、一致性好、质量轻、发火能量高、可量产等。附图说明图1是本发明的结构示意图;图2是图1去除铜层、镍层和锡层后的俯视图;图3是图1中电阻层的结构示意图;图中:1-基板,2-抗静电层,3-聚酰亚胺膜,4-电阻层,41-桥丝,5-保护层,6-表背搭接层,7-铜层,8-镍层,9-锡层,10-焊盘。具体实施方式下面进一步描述本发明的技术方案,但要求保护的范围并不局限于所述。如图1和图2所示的一种片式合金箔点火电阻器,包括基板1、抗静电层2、聚酰亚胺膜3、电阻层4、保护层5、表背搭接层6、铜层7、镍层8、锡层9和焊盘10;所述基板1的上表面中部设置有抗静电层2,下表面的两端分别设置有焊盘10;所述聚酰亚胺膜3设置在基板1和抗静电层2的上表面上,所述聚酰亚胺膜3的上表面设置有电阻层4,且所述电阻层4的两端分别通过表背搭接层6与焊盘10连接,所述电阻层4上还设置有保护层5;所述铜层7于保护层5的两侧设置在电阻层4上,且铜层7将表背搭接层6和焊盘10的外表面覆盖,所述铜层7的外表面上还依次设置有镍层8和锡层9。所述基板1为FR-4双面覆铜玻纤板,FR-4双面覆铜玻纤板具有较高的机械性能和介电性能,较好的耐热性和耐潮性并有良好的机械加工性,可作为片式合金箔点火电阻器的基体材料,能有效降低热量通过基板的散失,基板2外形尺寸为50mm×60mm,厚度为0.35mm~0.6mm。所述抗静电层2和焊盘10的材料为Cu;所述抗静电层2和焊盘10的厚度为0.018mm~0.03mm。所述抗静电层2及焊盘10的材料为Cu,表面铜层目的是为了在电阻器遇到静电情况时,静电产生的瞬间电流可通过,基板1上的铜层实际上就相当于一个静电释放通道,背面铜层为焊盘10,作为焊接用的一个背电极,其厚度为0.018mm~0.03mm。所述聚酰亚胺膜3的厚度为0.025mm~0.04mm。设置聚酰亚胺膜3目的是将电阻层4紧密的贴合在抗静电层2的表面上,并和抗静电层2绝缘。所述电阻层4的材料为NiCr合金或Ni-80.Cr-20合金;所述电阻层4的厚度为0.0035mm~0.005mm。所述保护层5的材料为光敏性聚酰亚胺,保护层5的厚度为0.004mm~0.006mm。所述铜层8材料为硫酸铜,其厚度为4~12μm;所述镍层9材料为镍扣,其厚度为2~8μm;所述锡层10材料为纯锡球,其厚度为3~14μm。所述表背搭接层6的材料为银浆,厚度为0.2mm~0.4mm。一种如图1和图2所示的片式合金箔点火电阻器的制备方法,包括以下步骤:A、对基板1进行清洗,去除表面的油污及杂质;B、通过光刻技术在基板1的上表面的中部形成抗静电层2,并在基板1的下表面的两端形成焊盘10;C、通过热压的方法将聚酰亚胺膜3贴在基板1和抗静电层2的上表面;D、通过压合的方法将电阻层4贴在聚酰亚胺膜3的上表面;E、采用湿法刻蚀技术对电阻层4进行刻蚀加工出桥丝41,刻蚀后的电阻层4如图3所示,刻蚀的深度为电阻层4的厚度;F、采用光刻技术在步骤E进行刻蚀处理的部位上形成保护层5,且保护层5还覆盖于电阻层4的桥丝41上,该保护层主要目的是保护桥丝(41);G、采用端面涂银的技术在基板1的两端形成表背搭接层6;H、根据产品尺寸要求,按常规方法对基片进行划片切割;I、通过电镀的方法依次形成铜层8、镍层9和锡层10。所述步骤B中形成的抗静电层2及焊盘10的厚度为15~22μm。制备好的片式合金箔点火电阻器可直接用回流焊的方式焊接在点火头上完成安装。本发明采用成熟的半导体工艺技术和材料,在基板上制备出片式合金箔点火电阻器,通过选择散热系数更低的基板材料和热隔离材料,实现了片式合金箔点火电阻器焦耳热的更少散失,使得片式合金箔点火电阻器产生更多的用于加热药剂,从而提高了能量利用效率,有效降低了金箔点火电阻器的工作能量和点火时间。本发明的式合金箔点火电阻器的点火电流1.5A,点火时间≤500μs,发火能量5毫焦,实现了小激发下快速发火;本发明的点火电阻器能量高、重量轻、可靠性高。本发明采用贴片式的制备方法,方便了安装而且可以适应回流焊,加工技术简单可靠,大大提高了点火电阻器工作的可靠性及一致性。