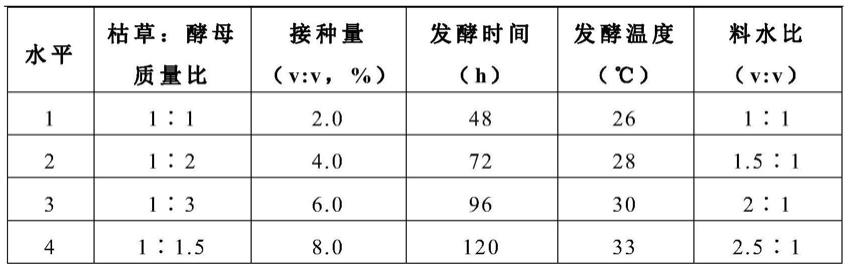
1.本发明涉及中药废渣处理技术领域,尤其是涉及一种中药药渣发酵复合物及其制备方法和应用。
背景技术:2.饲料的质量安全是保障畜产品安全和食品安全的第一道关口。随着社会的发展和对畜产品安全要求的不断提高,目前饲料质量安全的概念已有所延伸,不再单指违禁药物的添加、瘦肉精的使用等,而是纳入到整个社会发展的安全体系中,无抗养殖已成为我国畜牧养殖大趋势。因此,推行健康养殖理念刻不容缓,无抗健康的养殖模式必将进一步深入人心。开发健康绿色无公害的产品刻不容缓。
3.中药加工后产生药渣,其药渣中仍然含有粗蛋白,粗脂肪,粗纤维素和生理活性较强的、能增强机体免疫力的生物碱,皂苷等成分,这些物质具有一定的防病效果和饲用价值,是一种开发潜力很大的饲料资源。然而目前,我国多采用堆积、焚烧、填埋方法对中药药渣进行后处理,不仅污染环境,而且造成资源的严重浪费。如何根据中药药渣的用途进行开发利用,从而提高经济效益,成为当前迫切需要解决的问题。
技术实现要素:4.针对上述现有技术中存在的问题,本发明提供一种中药药渣发酵复合物及其制备方法和应用。
5.为了实现上述目的,第一方面,本发明提供一种中药药渣发酵复合物,其以中药药渣为原料,利用复合发酵菌经至少两次发酵制备而成;其中复合发酵菌包括桦褐孔菌、枯草芽孢杆菌和酵母菌中的至少两者。
6.优选地,复合发酵菌包括桦褐孔菌、枯草芽孢杆菌和/或酵母菌。
7.第二方面,本发明提供一种中药药渣发酵复合物的制备方法,其包括以下步骤:
8.步骤1、中药药渣用桦褐孔菌进行第一次发酵,得到中药药渣预处理液;
9.步骤2、中药药渣预处理液用枯草芽孢杆菌和/或酵母菌进行第二次发酵,得到中药药渣发酵复合物。
10.第三方面,本发明提供一种第一方面或第二方面制备的中药药渣发酵复合物的应用,优选用于饲料领域中。
11.本发明的中药药渣发酵复合物及其制备方法和应用所具有的有益效果包括:
12.(1)本发明的中药药渣经桦褐孔菌发酵后,能够产生低聚多糖和其他对机体有益的活性功能代谢产物,进一步加入枯草芽孢杆菌和酵母菌进行二次发酵,两者相互作用,得到中药药渣发酵复合物,其含有丰富的生物活性肽类和一定的酵母菌及其培养物;
13.(2)本发明的中药药渣发酵复合物加入到饲料中,能够有效降低仔猪的腹泻发病率,提高采食量和料肉比,其能够有效改善饲料适口性,提高饲料转化率,提高育肥猪出栏重,具有显著的经济性、环保性和高效性的特点;
14.(3)本发明的原料廉价易得,制备方法简单,中药药渣经二次发酵处理后即可利用,无需进行后处理,节省成本,符合当前绿色环保的发展趋势;
15.(4)本发明能够实现中药废渣的循环利用,提高中药生产企业的经济效益,极具推广应用前景。
附图说明
16.图1为本发明发酵前中药药渣和发酵后中药药渣发酵复合物的营养成分变化图;
17.图2为本发明不同发酵时间的中药药渣发酵复合物的碱性蛋白酶活力数据图。
具体实施方式
18.下面结合附图对本发明的较佳实施例进行详细阐述,以使本发明的优点和特征能更易于被本领域技术人员理解,从而对本发明的保护范围做出更为清楚明确的界定。
19.需要说明的是,在本文中,术语“包括”、“包含”或者其任何其他变体意在涵盖非排他性的包含,从而使得包括一系列要素的过程、方法、物品或者设备不仅包括那些要素,而且还包括没有明确列出的其他要素,或者是还包括为这种过程、方法、物品或者设备所固有的要素。在没有更多限制的情况下,由语句“包括
……”
限定的要素,并不排除在包括要素的过程、方法、物品或者设备中还存在另外的相同要素。
20.第一方面,本发明提供一种中药药渣发酵复合物,其以中药药渣为原料,利用复合发酵菌经至少两次发酵制备而成;其中复合发酵菌包括桦褐孔菌、枯草芽孢杆菌和酵母菌中的至少两者。
21.优选地,复合发酵菌包括桦褐孔菌、枯草芽孢杆菌和/或酵母菌。
22.其中,白腐真菌是唯一一类能充分降解木质纤维素的微生物,桦褐孔菌作为白腐真菌的一种,而目前对桦褐孔菌的研究只是如何通过改变发酵条件和发酵培养基组分而获得较高的产量,对其具有分解木质纤维素这一特点的关注明显不足。因此本发明利用桦褐孔菌分解中药药渣,使产生低聚多糖和其他对机体有益的活性功能代谢产物,为中药药渣的循环利用提供前提条件。
23.其中,在饲料添加剂的微生物中,枯草芽孢杆菌具有改善动物肠道、促进动物生长和预防疾病等功能。枯草芽孢杆菌在制剂中以内生孢子形式存在,孢子进入动物肠道后,在肠道上部能迅速复活并分泌高活性的蛋白酶、脂肪酶、淀粉酶,有助于降解中药药渣中复杂的碳水化合物,产生具有拮抗肠道致病菌的多肽类物质等,起到抑菌和预防作用。酵母菌也可分泌多种淀粉酶、蛋白酶和纤维素酶等,因此可加强对中药药渣的消化利用,促进畜禽生长,增进其食欲,增强抵抗疾病和抗应激的能力。因此,本发明进一步利用枯草芽孢杆菌和酵母菌进行二次发酵,两者相互作用,得到中药药渣发酵复合物,其含有生物活性肽类,能够提高适口性,易于动物消化;并且含有一定的酵母菌及其培养物,能够提高饲料吸收利用率,从而有效降低仔猪的腹泻发病率。
24.第二方面,本发明提供一种中药药渣发酵复合物的制备方法,其包括以下步骤:
25.步骤1、中药药渣用桦褐孔菌进行第一次发酵中,得到中药药渣预处理液。
26.在本发明中,桦褐孔菌,优选桦褐孔菌bncc117822,其可以市购,例如购自北京北纳创联生物技术研究院。
27.在本发明的一个优选实施方式中,为了使中药药渣发酵均匀且完全,在该步骤1之前还包括对中药药渣进行预处理,预处理包括洗涤、干燥、研磨、过筛,收集40~140目的中药药渣。具体地,将中药药渣用蒸馏水至少洗涤三次,然后自然晾干、研磨过筛,收集40~140目的中药药渣,更优选收集60~120目的中药药渣后,装袋存放干燥处备用。
28.其中,中药药渣为补气益气类中药药渣,其成分包括大枣、人参、黄芪和蒲公英根中的至少一者。该中药药渣可以市购,示例性的,购于长春中药制药有限公司。
29.在本发明的一个优选实施方式中,步骤1可以进一步地包括以下子步骤:
30.步骤1
‑
1、将桦褐孔菌接种于琼脂培养基中,获得一级种子。
31.在本发明中,该琼脂培养基包括蛋白胨、琼脂和麦芽浸粉;其中蛋白胨、琼脂和麦芽浸粉的质量比为1:(3~8):(8~12)。
32.根据本发明,在步骤1
‑
1中,培养温度为20~30℃,培养时间为2~10天,且ph保持自然。例如,在22~28℃下培养5~7天。
33.具体过程可以为:准备一支含有5~10ml无菌水的试管和2个琼脂培养基、装有桦褐孔菌bncc117822冻干粉的冻干管;
34.吸取0.5ml的无菌水打入冻干管中,混匀;
35.分别吸取0.2ml菌悬液打入2个琼脂培养基中,涂布混匀;
36.将两个含有菌悬液的琼脂培养基放于22~28℃,培养5~7天。
37.步骤1
‑
2、将一级种子接种于液体培养基中,获得二级种子。
38.在本发明中,该液体培养基包括蛋白胨、葡萄糖、酵母浸出物和无机盐。其中蛋白胨、葡萄糖、酵母浸出物和无机盐的质量比为(1~5):(15~25):1:(1~4)。优选地,该无机盐主要包括氯化钙cacl2、磷酸二氢钾kh2po4和硫酸镁mgso4。其中cacl2、kh2po4和mgso4的质量比为(0.05~0.15):1:(1~3)。
39.该液体培养基的制备过程为将蛋白胨、葡萄糖、酵母浸出物和无机盐混合,用蒸馏水定容到100ml,且ph保持自然。
40.其中,桦褐孔菌生长慢、量产低,因此本发明采用液体培养基对其进行培养,以获得粗壮且活性较强的菌种。
41.在本发明的一个优选实施方式中,该步骤1
‑
2的培养温度为20~30℃,搅拌速度为100~180rpm/min。
42.在本发明的一个优选实施方式中,当液体培养基中的菌种状态呈现密集菌球,转入冰箱冷藏,用于菌种的保存。
43.在本发明的一个优选实施方式中,为了除菌,使液体培养基达到无菌。在步骤1
‑
2之前,还包括将液体培养基置于高温灭菌锅中灭菌,其中灭菌温度为110~140℃,灭菌时间为15~40min。优选,灭菌温度为120~130℃,灭菌时间为20~40min,例如121℃灭菌30min。
44.步骤1
‑
3、将二级种子接种于加中药药渣的发酵培养基中,进行第一次发酵,得到中药药渣预处理液。
45.根据本发明,采用液体发酵,可以使底物与发酵物充分接触,从而进一步解决了桦褐孔菌生长慢、量产低的问题。
46.其中,发酵生产过程中的各种因素如发酵培养基成份、接种量、接种比例、ph值、温度等均对发酵结果有大的影响,本发明建立了一种适用于桦褐孔菌高密度发酵的培养基及
生产工艺,能够大大提高桦褐孔菌的活菌数。
47.在本发明的一个优选实施方式中,该步骤1
‑
3中,氮源为有机氮源和/或无机氮源,有机氮源包括蛋白胨、牛肉膏和酵母浸出物中的至少一者,无机氮源包括尿素和/或(nh4)2so4。
48.经研究发现,在氮源选择时,发酵相同时间的情况下,采用(nh4)2so4做氮源时,木质素和纤维素降解率均能够达到40%以上,采用尿素做氮源时,纤维素降解率能够达到40%以上,而木质素降解率明显较低,一般为20~30%左右,采用蛋白胨、牛肉膏或酵母浸出物为氮源时,木质素降解率明显较低,为20~30%左右,而纤维素降解率能够达到50%以上。
49.同时,对中药药渣的选择系数进行评价,选择系数=木质素降解率/纤维素降解率。当采用(nh4)2so4做氮源时,选择系数最高,为0.87左右,有机氮源的选择系数明显低于无机氮源。因此,本发明优选选择(nh4)2so4做氮源。无机氮源对选择系数的促进作用优于有机氮源;培养条件对选择系数的促进具有协同作用。
50.在本发明的一个优选实施方式中,该步骤1
‑
3中,中药药渣与发酵培养基的质量体积比为(1~20)g:100ml,更优选为(1~10)g:100ml。
51.经研究发现,中药药渣添加量的改变对选择系数和降解率的影响小于氮源种类的变化。随着中药药渣添加量的增加,选择性系数虽有变化,但是降解率差距并不明显。
52.在本发明的一个优选实施方式中,该步骤1
‑
3第一次发酵时,发酵温度为20~30℃,发酵时间为5~15天,搅拌速度为100~180rpm/min。
53.经研究发现,随着发酵时间的增加,中药药渣的木质素、纤维素和半纤维素的含量均出现减少,中药药渣的重量损失升高,这表明桦褐孔菌对中药药渣有高效降解作用。其中木质素的减少速率明显高于纤维素和半纤维素,体现出了桦褐孔菌在此培养条件下对木质素的选择性降解。但是发酵时间达到8天时,随着发酵时间的继续增加,木质素和纤维素的含量保持稳定,半纤维素的含量则继续减少。
54.其中,木质纤维素降解酶的活性均呈现先高后低、略有浮动的酶活。其中,降解木质素的lac(漆酶)、lip(木质素过氧化物酶)、mnp(锰过氧化物酶)三个酶的酶活明显高于纤维素降解酶fpa,cmc酶和β
‑
葡萄糖苷酶,体现了降解的选择性。在发酵第6天,mnp最大达到317.9iu/ml。
55.其中,发酵2天的中药药渣在酶解12h后总还原糖量达到最大265.82mg/g,产糖率也达到29.61%,显示出发酵较短时间即可达到较好效果的优势。
56.降低总还原糖产量是由纤维素和半纤维素的含量之和来决定,本发明需要选择性地降解木质素、保留纤维素和半纤维素,以提高糖化产糖量,因此本发明的发酵时间为5~15天,优选为6~7天。
57.在本发明中,该发酵培养基包括玉米粉(水解)、(nh4)2so4、cocl2·
6h2o、feso4·
7h2o、kh2po4、mgso4·
7h2o、znso4·
7h2o、mncl2·
4h2o、cacl2和tween80。
58.经研究发现,减少(nh4)2so4、kh2po4和tween80的量,降低发酵培养基的ph,均能够提高中药药渣的选择系数。因此本发明的上述原料玉米粉(水解)、(nh4)2so4、cocl2·
6h2o、feso4·
7h2o、kh2po4、mgso4·
7h2o、znso4·
7h2o、mncl2·
4h2o、cacl2和tween80的质量体积比为(2.5~3.5)g:(0.18~0.3)g:(0.001~0.005)g:(0.003~0.008)g:(0.002~0.007)g:
(0.015~0.025)g:(0.001~0.003)g:(0.006~0.012)g:(0.03~0.07)g:(0.35~0.50)ml。更优选为(2.8~3.2)g:(0.20~0.25)g:(0.001~0.003)g:(0.004~0.006)g:(0.003~0.006)g:(0.018~0.022)g:(0.001~0.002)g:(0.007~0.010)g:(0.04~0.06)g:(0.40~0.45)ml。
59.该发酵培养基的制备过程为将玉米粉(水解)、(nh4)2so4、cocl2·
6h2o、feso4·
7h2o、kh2po4、mgso4·
7h2o、znso4·
7h2o、mncl2·
4h2o、cacl2和tween80按照上述比例进行混合,用蒸馏水定容到100ml,ph调至4~7之间。
60.在本发明的一个优选实施方式中,为了除菌,使发酵培养基达到无菌。在步骤1
‑
3之前,还包括将发酵培养基置于高温灭菌锅中灭菌,其中灭菌温度为110~140℃,灭菌时间为15~40min。优选,灭菌温度为120~130℃,灭菌时间为20~40min,例如121℃灭菌30min。
61.根据本发明,采用上述培养条件,使得桦褐孔菌降解中药药渣的选择系数为1.23,比传统的选择系数增长了95.23%。
62.步骤2、中药药渣预处理液用枯草芽孢杆菌和/或酵母菌进行第二次发酵,得到中药药渣发酵复合物。
63.在本发明中,在步骤2之前还包括,在中药药渣预处理液中补加(nh4)2so4,补加量为8~12g/l。
64.优选地,使用枯草芽孢杆菌和酵母菌进行第二次发酵。
65.在本发明中,枯草芽孢杆菌和酵母菌为活化后的菌种,优选用马铃薯糖水液体培养基进行活化。其中,马铃薯糖水液体培养基可以自制也可以为市购,例如购于今品化学技术(上海)有限公司。
66.枯草芽孢杆菌,优选为枯草芽孢杆菌accc01185。酵母菌优选为酿酒酵母菌,更优选酿酒酵母菌accc20042。
67.枯草芽孢杆菌accc01185和酿酒酵母菌accc20042可以市购,例如购自中国农业微生物菌种保藏管理中心。
68.其中,枯草芽孢杆菌accc01185或酿酒酵母菌accc20042的活化过程相同,具体可以包括以下步骤:
69.准备一支含有5~10ml无菌水的试管和2个马铃薯糖水液体培养基、装有枯草芽孢杆菌accc01185或酿酒酵母菌accc20042冻干粉的冻干管;
70.吸取0.5ml的无菌水打入冻干管中,充分溶解后重新打回无菌水的试管中,混合均匀;
71.分别吸取0.2ml菌悬液打入2个马铃薯糖水液体培养基中,涂布混匀;
72.将含有菌悬液的试管和2个马铃薯糖水液体培养基全部放于35~39℃,好氧,20~60h培养,例如37℃培养24~48h。
73.在本发明的一个优选实施方式中,在该步骤2中,第二次发酵时,发酵温度为20~35℃,发酵时间为2~7天。优选发酵温度为26~33℃,发酵时间为2~5天。
74.经研究发现,发酵温度对菌种的发酵影响最大,当发酵温度为20~35℃,优选为26~33℃,例如30℃时,极大的促进了菌种的代谢活动,在该温度下,菌种之间相互协调发酵的能力加强,中药药渣发酵复合物的各项检测指标最为理想。
75.发酵时间对中药药渣发酵复合物的品质影响最大,由于菌种在发酵前期处于发酵
调整阶段,因此中药药渣发酵复合物中小肽和总蛋白的质量含量值在发酵过程中是一个增长的过程,但是当发酵时间4天时,继续增加发酵时间,小肽和总蛋白的质量含量增加的并不明显,因此,本发明的发酵时间为2~7天,优选2~5天,例如4天。
76.在本发明的一个优选实施方式中,在该步骤2中,枯草芽孢杆菌与酵母菌的接种量为2~10%。
77.同理,接种量是指移入种子液的体积和接种后培养基体积的比例,本发明的接种量为枯草芽孢杆菌与酵母菌两者的接种总体积与接种后培养基体积比。接种量对中药药渣发酵复合物的品质影响也较大,固体发酵相对液体发酵而言,接入菌种不能与营养物质和发酵料等快速接触进入生长对数期,菌种在固体发酵中只能自我增殖扩散汲取营养物,因此比液体发酵需要更长的发酵时间,接种量的大小在固态发酵过程中比较重要,直接影响发酵时间。因此,在本发明中接种量为2~10%,优选为2~6%,例如4%,中药药渣发酵复合物的各项检测指标最为理想。
78.在本发明的一个优选实施方式中,在该步骤2中,枯草芽孢杆菌与酵母菌的接种质量比1:(1~5)。
79.经研究发现,2种菌种的接种质量比,也影响着中药药渣发酵复合物的品质。当2种菌种的接种质量比为1:(1~5),优选1:(1~3),例如1:2时,中药药渣发酵复合物的各项检测指标最为理想。
80.在本发明中,通过测定吸光度(od)值及2种菌种的个数,然后统一个数例如为105/ml,这样2种菌种的接种质量比就转化为接种体积比。
81.在本发明的一个优选实施方式中,在该步骤2中,第二次发酵的料水比为(1~3.5):1。
82.经研究发现,料水比是指发酵料与水的体积比,其也影响着中药药渣发酵复合物的品质。这是由于菌种代谢离不开水,而固体发酵时一种无游离水分的发酵工艺,要使发酵过程中要使发酵过程中菌种拥有正常的代谢能力,保持发酵基质的水活度就显得尤为重要,因此在发酵的过程中发酵料需要含有一定的水分,也就是半固态发酵。当料水比为(1~3.5):1,优选为(1~2.5):1,例如1:1时,中药药渣发酵复合物的各项检测指标最为理想。
83.根据本发明,本发明首先利用桦褐孔菌分解中药药渣,使产生低聚多糖和其他对机体有益的活性功能代谢产物,为中药药渣的循环利用提供前提条件。同时优化发酵培养基的氮源种类和中药药渣的添加量,使得中药药渣的选择系数达到最佳。
84.其次,进一步利用枯草芽孢杆菌和酵母菌进行二次发酵,两者相互作用,得到中药药渣发酵复合物,其含有生物活性肽类,能够提高适口性和提高饲料吸收利用率。同时优化发酵工艺,建立了一种发酵时间短、操作性简便和经济性好的制备中药药渣发酵复合物的方法。
85.第三方面,本发明提供一种第一方面或第二方面制备的中药药渣发酵复合物的应用,优选用于饲料领域中。
86.在本发明的一个优选实施方式中,中药药渣发酵复合物作为饲料添加剂使用时,中药药渣发酵复合物的添加量为饲料含量的5
‰
~15
‰
。
87.为了进一步理解本发明,下面结合实施例对本发明提供的中药药渣发酵复合物进行描述,本发明的保护范围不受以下实施例的限制。
88.实施例
89.实施例1
90.(1)中药药渣的预处理:
91.将主要成分为大枣,人参,黄芪及蒲公英根的益气补气类中药药渣,用蒸馏水清洗3遍,自然条件下晾干、磨碎过筛,收集60
‑
120目的药渣颗粒,装袋后存放干燥处备用。
92.(2)培养基的制备:
93.琼脂培养基(w/v):蛋白胨0.3g,琼脂1.5g,麦芽浸粉3g,ph保持自然;
94.液体培养基(w/v):cacl20.01g,葡萄糖2g,酵母浸出物0.1g,kh2po40.1g,蛋白胨0.3g,mgso40.15g,用蒸馏水定容到100ml,ph保持自然;
95.发酵培养基(w/v):玉米粉(水解)3.0g,(nh4)2so40.222g,cocl2·
6h2o 0.002g,feso4·
7h2o 0.005g,kh2po40.004g,mgso4·
7h2o 0.02g,znso4·
7h2o 0.001g,mncl2·
4h2o 0.009g,cacl20.05g,tween 800.43ml,用蒸馏水定容至100ml,ph值调至4.3。
96.(3)中药药渣发酵复合物的制备过程
97.将桦褐孔菌bncc117822接种到琼脂培养基上,于26℃条件下培养7天,得到一级种子,然后将一级种子用10ml蒸馏水洗脱,制成一级种子母液,
98.将液体培养基在高压灭菌锅中121℃高压灭菌30min后接种3ml一级种子母液,摇床培养,转速150rpm/min、温度28℃。当液体培养基中的菌种状态呈现密集菌球,转入4℃冰箱冷藏,作为二级种子;
99.将发酵培养基在高压灭菌锅中121℃高压灭菌30min后,加入中药药渣4g,接种3ml二级种子,摇床,第一次发酵6天,转速150rpm/min、温度28℃,得到中药药渣预处理液;
100.在中药药渣预处理液中补加(nh4)2so4,补加量为10g/l,料水比为1:1,其中料水比为中药药渣预处理液中发酵料与水的体积比;
101.将质量比1:2,接种量为4.0%的枯草芽孢杆菌accc01185和酿酒酵母菌accc20042,一次性接种到中药药渣预处理液中,其中,在30℃下进行第二次发酵4天,得到中药药渣发酵复合物,其中接种量为枯草芽孢杆菌accc01185和酿酒酵母菌accc20042两者的接种总体积与接种后中药药渣预处理液体积比。
102.实施例2~5
103.与实施例1相似的过程,区别仅在于,发酵培养基中氮源不同,氮源依次为牛肉膏、蛋白胨、酵母提取物或尿素。
104.实施例6~10
105.与实施例1相似的过程,区别仅在于,中药药渣的添加量不同,分别为3g、5g、10g、15g和20g。
106.实施例11
107.与实施例1相似的过程,区别仅在于,第二次发酵时枯草芽孢杆菌accc01185和酿酒酵母菌accc20042接入质量比(a)、接种量(b)、发酵时间(c)、发酵温度(d)和料水比(e)不同,具体数据见表1。
108.表1不同发酵参数数据
[0109][0110]
实验例
[0111]
实验例1木质纤维素的成分含量测定
[0112]
(1)对实施例1和实施例2~5的中药药渣预处理液进行木质纤维素的成分含量测定。
[0113]
实验结果表明,当第一次发酵时间为8天时,实施例1的木质素降解率为42.58%,纤维素降解率45.17%;实施例5的纤维素降解率46.23%,木质素降解率为28.30%,低于实施例1。实施例2~4的木质素降解率(28.85%、25.76%、23.07%)明显低于实施例1和实施例5,纤维素降解率(51.89%、52.34%、55.84%)则高于实施例1和实施例5。
[0114]
实施例1的选择系数最高0.87(选择系数是木质素降解率与纤维素降解率的比值)。实施例2~4的选择系数低于实施例1和实施例5。
[0115]
(2)对实施例1和实施例6~10的中药药渣预处理液进行木质纤维素的成分含量测定。
[0116]
实验结果表明,实施例6的选择系数为0.89,实施例8的选择系数为1.1,实施例7的选择系数为0.8,实施例1和实施例9~10的选择系数均在0.95以上。因此中药药渣添加量的改变对选择系数和降解率的影响小于氮源种类的变化。
[0117]
实验例2中药药渣进行动态降解测试
[0118]
对60
‑
120目未处理的中药药渣进行成分含量的测定,得到表2中数据:
[0119]
表2未处理中药药渣中木质纤维素组成
[0120][0121]
实验结果表明,随着发酵天数的延长,木质素、纤维素和半纤维素的含量都出现减少,中药药渣的重量损失升高。发酵第2天,相较于空白对照组,重量损失增加16.21%,木质素减少25.65%,纤维素减少15.3%,半纤维素减少9.1%,其他成分减少39.14%,表明桦褐孔菌对中药药渣的高效降解作用。发酵至第6天时,中药药渣整体损失率达到26.13%,木质素、纤维素和半纤维素的含量明显减少,较对照组分别重量减少了29.4%、24.2%和19.7%。其中,木质素的减少速率明显高于纤维素和半纤维素,体现出了桦褐孔菌在此培养条件下对木质素的选择性降解。发酵第8天为转折点,之后木质素和纤维素的含量保持稳定,半纤维素的含量则继续减少。发酵第14天,半纤维素较对照组重量减少35.3%。推测,在此培养条件下,木质素和纤维素降解酶的高酶活在0
‑
8天,8
‑
14天半纤维素降解酶成为优势
酶,半纤维素降解量增加。
[0122]
实验例3木质素降解酶活性的测定
[0123]
在实施例1的第一次发酵过程中,间隔2天随机取出发酵组,抽滤后获得发酵液和残渣,并立即测定发酵液的酶活,发酵液即为粗酶液。结果如表3所示:
[0124]
表3不同发酵时间的发酵液的酶活数据
[0125][0126]
从表3中可以看出,木质纤维素降解酶的活性均呈现先高后低、略有浮动的酶活。其中,降解木质素的lac、lip、mnp三个酶的酶活明显高于纤维素降解酶fpa,cmc酶和β
‑
葡萄糖苷酶,体现了降解的选择性。在发酵第6天,mnp最大达到317.9iu/ml。
[0127]
实验例4糖化实验
[0128]
在实施例1的第一次发酵过程中,间隔2天随机取出发酵组,抽滤后获得发酵液和残渣,残渣经40目分选筛与菌丝体分离后,用400目分选筛全部收集并抽滤,60℃烘干至恒重。各组精确称量1g残渣样品放入100ml锥形瓶中,按20fpu/g的量添加cmc纯酶,加入1.0ml(ph=5,0.50mm)醋酸
‑
醋酸钠缓冲液,0.003%四环素作为抑菌剂。糖化酶解的参数:摇床150r/min,60℃。糖化实验周期内的动态测定时间点:3h,6h,9h,12h,24h,36h,48h,随机取出3组,迅速冷却并测定还原糖量,测定方法同上。
[0129]
其中,糖化率%=还原糖总量
×
0.9/(底物半纤维素和纤维素总量)
×
100%。
[0130]
实验结果表明,发酵2天的残渣在酶解12h后,总还原糖量达到最大265.82mg/g,产糖率达到29.61%,高于发酵大于2天的残渣,说明短时间的发酵即可达到较高的糖化率。
[0131]
实验例5小肽含量的测定方法
[0132]
对实施例11第二次发酵得到的中药药渣发酵复合物进行小肽含量的测定。具体结果见表4。
[0133]
表4实施例11中不同发酵参数对应的小肽含量
[0134][0135][0136]
从表4中可以看出,枯草芽孢杆菌accc01185和酿酒酵母菌accc20042接入质量比、接种量、发酵时间、发酵温度和料水比均影响着中药药渣发酵复合物的品质。利用实施例1中m(枯草芽孢杆菌):m(酿酒酵母菌)=1:2,接种量(v/v)为4.0/100,料水比(v/v)为1:1,发酵温度为30℃,发酵时间为96时,能够获得较高品质的中药药渣发酵复合物。
[0137]
实验例6中药药渣发酵复合物的品质分析
[0138]
对实施例1的中药药渣发酵复合物进行总蛋白含量、有机酸含量、碱性蛋白酶活力进行测定,实验结果如图1和图2所示。
[0139]
从图1中可以看出,发酵后的中药药渣发酵复合物中总蛋白含量在原料的基础上
提高了10.5%,达到33.8%;发酵后小肽的含量是发酵前的7.02倍,达到23.6%;有机酸含量达到3.27%,从而可以提高动物消化道的酸度,抑制消化道有害微生物的活动,促进营养物质的消化吸收。
[0140]
大豆胰蛋白酶抑制因子从25.4mg/100g降解到饲料标准规定含量以下的0.25mg/100g,由于中药药渣发酵复合物中的大豆胰蛋白酶抑制因子的有效降解,从而提高动物对蛋白质和各营养物质的消化吸收率。
[0141]
从图2中可以看出,在发酵前36h碱性蛋白酶的产量不断增高,酶活也呈不断上升趋势,但发酵至36h时酶活达到最高值为2340.72u/g,之后酶活呈缓慢下降趋势。
[0142]
实验例7动物实验
[0143]
(1)中药药渣发酵复合物对断奶仔猪采食量、生长性能和腹泻率的影响。
[0144]
选用体重均匀一致的健康杜长大断奶仔猪(7.44
±
0.29kg),分为4个处理,每个处理6个重复,每个重复7头。实验组1
‑
3将实施例1得到的中药药渣发酵复合物作为饲料添加剂用于仔猪的饲养中。
[0145]
对照组为饲喂普通乳猪饲料;普通乳猪饲料配方参照nrc(1998)仔猪的营养需要设计和配制,日粮组成及营养水平见表6,饲料制成颗粒饲料。
[0146]
表5仔猪实验设计
[0147][0148]
表6日粮组成及营养成分含量(%)
[0149][0150][0151]
注:1.粗蛋白、赖氨酸、蛋氨酸、胱氨酸、苏氨酸、钙和磷为计算值(根据《中国饲料
成分及营养价值表(2009年版)》)。
[0152]
注:2.每公斤日粮提供:维生素a,11 000iu;维生素d3,2 305iu;维生素e,34.1iu;维生素k,2.3mg;硫胺素,5.77mg;核黄素,6.22mg;维生素b6,9.45mg;泛酸,20.0mg;烟酸,37.0mg;叶酸,0.70mg;维生素b12,0.21mg;胆碱,350mg;锰,55.0mg;铁,120.0mg;锌,90.0mg;铜,116.5mg;碘,0.40mg;硒,0.30mg;钴,0.70mg。
[0153]
(1
‑
1)中药药渣发酵复合物对猪仔生长性能的影响
[0154]
各组猪自由采食,实验时间为42天。每周测定一次,包括:平均日增重、平均日采食量、料肉比,具体测试结果见表7。
[0155]
从表7可见,实验前3周,仔猪日增重、日采食量提高,差异极显著(p<0.01),而料肉比没有显著差异(p>0.05)。第4周三个实验组的日增重、日采食量、料肉比均显著高于对照组(p<0.05)。第5周三个实验组的日增重、日采食量显著高于对照组(p<0.05),实验组1料肉比显著低于对照组和实验组2。实验全期中,实验组平均日增重、平均日采食量极显著地高于对照组(p<0.01),料肉比无显著差异(p>0.05)。以上说明,添加中药药渣发酵复合物能提高断奶仔猪的采食量,进而提高其日增重。
[0156]
中药药渣发酵复合物中富含核苷酸、游离氨基酸(20种)、有机酸等风味物质,这些物质具有良好的诱食效果,能改善饲料适口性,提高仔猪的采食量。同时含有一定的酵母菌及其培养物,富含菌体蛋白、b族维生素、有机微量元素,是胃肠道内有益菌优良的培养基,能使胃肠道内的有益菌迅速生长,产生大量有助于消化吸收的酶,提高饲料吸收利用率,降低料肉比。
[0157]
表7中药药渣发酵复合物对断奶仔猪生长性能的影响
[0158][0159]
注:数字肩标大写字母表示差异极显著(p<0.01),数字肩标小写字母表示差异显著(p<0.05)。
[0160]
(1
‑
2)中药药渣发酵复合物对断奶仔猪腹泻的影响
[0161]
腹泻指数是腹泻头次乘以相应的腹泻得分,腹泻得分标准参考表8。腹泻率为试验期间腹泻的仔猪总头次除以每天的仔猪总头数乘以试验天数。
[0162]
表8腹泻评分标准
[0163][0164]
从表9可见,实验组1的腹泻率显著低于对照组(p<0.05),实验组2、3的腹泻率极显著地低于对照组(p<0.01),显著低于实验组1(p<0.05)。
[0165]
因此,从实验第3周开始添加中药药渣发酵复合物对仔猪的生长性能产生影响,能有效降低仔猪的腹泻发病率,提高采食量和料肉比。综合考虑仔猪的生长性能、腹泻和饲料成本,在仔猪日粮中此中药药渣发酵复合物的添加量最佳为8.0
‰
,即8.0kg/t。
[0166]
表9中药药渣发酵复合物对断奶仔猪腹泻的影响
[0167]
组别对照组实验组1实验组2实验组3腹泻率(%)12.3
±
2.5
a
6.2
±
0.6
a
2.7
±
0.42.6
±
0.3腹泻指数33.2
±
3.5
a
20.2
±
4.2
a
13.2
±
2.89.6
±
1.9
[0168]
注:数字肩标大写字母表示差异极显著(p<0.01),数字肩标小写字母表示差异显著(p<0.05)
[0169]
(2)中药药渣发酵复合物对育肥猪增重效果的影响
[0170]
选择体重110斤左右,日龄相近的杜
×
长
×
大三元商品健康的育肥猪40头,随机分成4组,每组10头。组间供试猪初始体重差异不显著。试验时间为60天。试验饲粮分为2个处理,对照组和试验组,见表10,对照组添加基础日粮,试验组在对照组的基础上添加适量的中药药渣发酵复合物。基础日粮组成及营养成分如表11所示,基础日粮营养水平参照中国猪饲养标准(2004)。通过60天的试验期,测定使用中药药渣发酵复合物后,育肥猪增重效果,具体数据见表12。
[0171]
表10育肥猪试验设计
[0172]
组别试验组1对照组1试验组2对照组2添加量(kg/t)5.005.00
[0173]
表11日粮组成及营养成分含量(%)
[0174][0175]
从表12中可以看出,在育肥猪日常饲粮中添加中药药渣发酵复合物,通过60天的实验期,实验组与对照组相比,增重较明显,实验组比对照组平均多增重6.5
±
2.1kg。这是因为在中药药渣发酵复合物中含有丰富的小肽、有机酸、必需氨基酸等小分子物质,机体更易于吸收,且中药药渣发酵复合物中含有易于肠道有益菌增殖的有益物质(如菌多糖、核苷酸等),促进肠道对营养物质的消化吸收,有效提高动物机体对饲料的利用率,提高料肉比,增加养殖户的经济效益。
[0176]
表12育肥猪增重效果
[0177][0178]
以上结合具体实施方式和范例性实例对本发明进行了详细说明,不过这些说明并不能理解为对本发明的限制。本领域技术人员理解,在不偏离本发明精神和范围的情况下,可以对本发明技术方案及其实施方式进行多种等价替换、修饰或改进,这些均落入本发明的范围内。