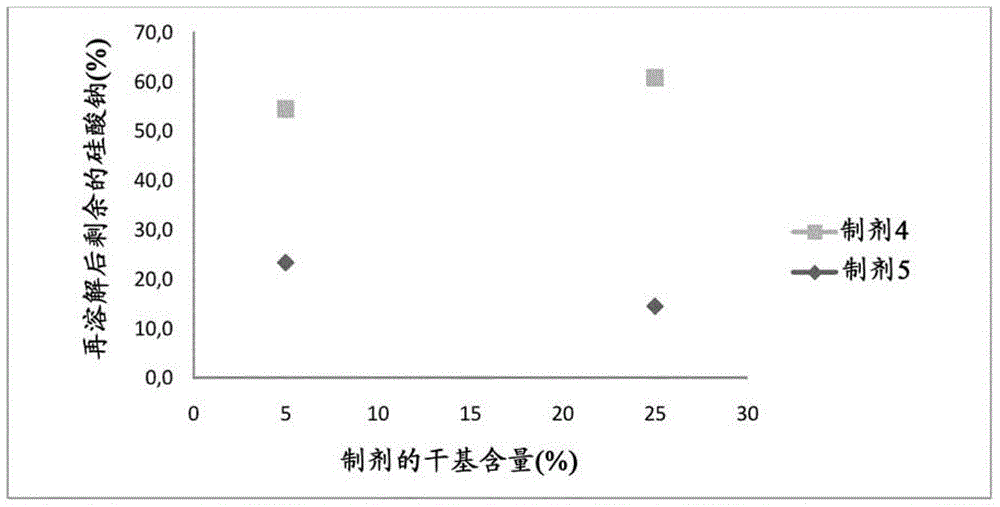
本发明涉及一种环境友好型的木材处理工艺。背景本发明背景和现有技术木质产品被广泛用在许多应用领域,包括建筑和家具。作为一种可再生资源,在建筑物建造和其它应用领域更广泛地利用木材是非常可取的。然而,当使用木质材料建造以及用于户外应用时,一个主要问题是其固有的生物降解性和较差的耐火性。为了防止腐烂、真菌和昆虫引起的木材退化和/或使其更耐火,木材行业用不同的化学物质处理木材。传统上,各种杀生物剂和杀虫剂,如铜基盐(如铜铬砷酸盐(CCA))、硼酸盐、煤焦杂酚油等被用作木材防腐剂。以相同的方式,如今普遍使用的各种阻燃剂是基于含溴化合物或磷酸盐的。然而,所有这些化合物,如果从木材中浸出的话,将对环境有负面影响。出于这个原因,在过去的几十年,保护木材的新手段吸引了研究者的关注。硅是自然界最常见的元素之一,且它作为固有的环境友好物质在许多应用领域已获得青睐。基于这个原因,使用碱金属硅酸盐处理木材被广泛地研究。自19世纪以来,已经知晓碱金属硅酸盐处理过的木材的阻燃性能(参见美国专利No.63,618)。在过去的二十年中,一些研究还考察了作为防止真菌侵蚀的木材防腐剂的碱金属硅酸盐的性质(综述参见MaiC.和H.Militz.(2004)Modificationofwoodwithsiliconcompounds,inorganicsiliconcompoundsandsolgelsystems:areview.WoodSciTechnol37:339-348)。然而,当使用碱金属硅酸盐作为木材防腐剂时,一个主要的问题是其水溶性。特别是硅酸钠(俗称水玻璃),其在水中极易溶解。当处于室外条件,例如雨水,或者被置于水中时,硅酸钠溶解并从处理过的木材中浸出。因此,该领域最近的研究重点是解决浸出问题。一种使硅酸钠不溶于水的方法是使硅酸钠单体聚合为长的聚合链。当酸化硅酸钠溶液时,这种反应很容易发生。已经开发了几种方法,其中木材首先用硅酸钠处理和其后进行酸性溶液处理(参见,例如FurunoT.和Y.Imamura.(1998).CombinationsofwoodandsilicatePart6.Biologicalresistanceofwood-mineralcompositesusingwaterglass-boroncompoundsystems.WoodSciTechnol23:161-170;美国专利1,900,212;美国专利4,612,050;美国专利5,205,874)。另一种方法是促进硅酸钠单体和多价离子之间形成复合物。特别地,已使用硼酸、铝、钙和镁的盐。已经开发了类似的使用酸性溶液的两步法,其中,木质材料首先用硅酸盐溶液处理,然后用包含复合物粘合剂的溶液处理(例如,参见美国专利3,974,318;US2005/0129861A1)。但是,即使硅酸钠作为木材防腐剂的性能已经广为人知,却并没有被该行业广泛地接受。一个主要的原因是成本高,涉及多步应用。在如真空-压力浸渍木材的大规模工业应用中,工艺成本必须保持在最低限度。由于在两步骤之间木材需要进行干燥,这是高成本的,因而上述的两步工艺是困难和不经济的方法。为了解决这个问题,已经进行了一些研究。例如:美国专利No7,297,411描述了如下方法,在该方法中,木质材料用硅酸钠处理,然后在升高的温度下干燥木材,以使硅酸钠不溶解。然而,当使用这种方法时,需要非常高的温度(>200°C),以使所有的硅酸钠不溶解,这使得该方法成本高昂并且能耗高。国际专利申请WO02/078865描述了如下方法,在该方法中,硼酸和硅酸钠在一个溶液中混合。根据该发明,调整加入到硅酸钠中的硼酸的量的水平使得该制剂保存期长(不胶凝或沉淀)但在对处理过的木材进行干燥时开始聚合。然而,硼酸是杀生物剂,因而对生态系统有害。因此,为使碱金属硅酸盐不溶解而使用无毒的有机酸(如柠檬酸、酒石酸等)会是更为环境友好的解决方案。根据美国专利No4,612,050,硅酸钠、柠檬酸和粘土混合在一起形成单一溶液。加入到硅酸钠的柠檬酸的量调整到使该制剂保持处于所谓的初始胶凝条件(incipientjellingcondition)的条件下。当该溶液应用在木材上时,部分硅酸钠聚合,从而变得不溶解。但是,即使处理过的木材中的一些硅酸钠在该溶液处理后成为不溶解的,很大一部分硅酸钠仍然是可溶的且在接触到水时可浸出。如本文所述,存在许多方式来解决碱金属硅酸盐在水中溶解的技术问题。然而,仍然缺乏一种工业上可行的、完全环境友好方法来使用硅酸钠作为木材防腐剂。仍然需要使用含有硅酸钠的木材防腐剂使得木质材料的耐水性好的工业方法,并且还是其中木材防腐剂不从经处理的木材中浸出的方法。发明目的本发明涉及一种新型环境友好、工业上可行的处理木材(wood)的方法和利用该方法处理的木质材料(woodenmaterial)。特别地,本发明涉及木材处理方法,该方法是工业上可行的,并且完全环境友好,其中,木材防腐剂(woodpreservative)不从经处理的木材中浸出(leachout)。根据本发明的方法处理过的木材的特征还在于其具有对白蚁、真菌和火的耐性。发明概要本发明描述了一种处理木材以提高木质材料阻燃性能以及对腐烂、真菌、霉菌和昆虫的耐性的方法。本发明的木材处理方法,包括以下步骤:a)提供木质材料和提供水基制剂(waterbasedformulation),该制剂在室温下或在15~35°C的温度范围稳定;b)提供本发明的水基制剂,其基本上由碱金属硅酸盐、水和不溶解化试剂(insolubilizationagent)构成,该不溶解化试剂选自有机酸、无机酸或无机多价离子,其添加量低于使制剂达到胶凝点所需的不溶解化试剂的量;c)将水基制剂应用到木质材料上;d)在任何给定温度下干燥经所述水基制剂处理过的木质材料,以去除过量的水;以及e)在升高的温度下熟成(curing)已干燥的木质材料,以使碱金属硅酸盐不溶解。在另一个实施方式中,本发明描述了一种处理木材以提高木质材料的阻燃性能以及对腐烂、真菌、霉菌和昆虫的耐性的方法。本发明的木材处理方法包括以下步骤;处理木质材料以提高木质材料的阻燃性能以及对腐烂、真菌、霉菌和昆虫的耐性的压力浸渍法(pressureimpregnationmethod),其中,使用水基制剂处理木质材料,并包括以下步骤:a)提供木质材料,放置该木质材料到真空-压力浸渍容器内;b)提供水基制剂,该制剂在室温下或在15~35°C的温度范围稳定,并且主要由下述成分构成;-碱金属硅酸盐-水-不溶解化试剂,其选自有机酸、无机酸或无机多价离子,其添加量低于使制剂达到胶凝点所需的不溶解化试剂的量;c)通过将所述水基制剂添加到压力浸渍容器来将水基制剂应用到木质材料上;d)使所述浸渍容器和内容物(content)处于高于90%的真空10~40分钟;e)使所述浸渍容器和内容物处于6~16巴的压力20分钟~12小时;f)使所述浸渍容器和内容物处于高于90%的真空10~40分钟;g)在任何给定温度下干燥经所述水基制剂处理过的木质材料,以去除过量的水;以及h)在升高的温度下熟成已干燥的木质材料,以使碱金属硅酸盐不溶解。进一步的实施方式本发明的实施方式还包括下列的可选组合:木材处理方法,其中,相对水基制剂的总重量%,碱金属硅酸盐的重量%可以为1%w/w~50%w/w,更优选为5%w/w~30%w/w,和最优选为10%w/w~20%w/w。木材处理方法,其中,水基制剂中的碱金属,例如钠或钾,与硅酸根之间的摩尔比(M+:SiO44-)的范围为0.1:1~2:1,更优选为0.5:1~0.8:1,最优选的摩尔比为0.6:1(对应于SiO2和Na2O之间的重量比为3.22)。木材处理方法,其中,不溶解化试剂为有机酸,其分子量例如为40~500g/mol或40~300g/mol。木材处理方法,其中,不溶解化试剂为有机酸,其选自乙酸、扁桃酸、柠檬酸、酒石酸、天冬氨酸、谷氨酸、甲酸、丙酸、丁酸、戊酸、草酸、马来酸、琥珀酸或戊二酸、甲磺酸(或甲基磺酸,CH3SO3H)、乙磺酸(或乙基磺酸,CH3CH2SO3H)、苯磺酸(或苯基磺酸,C6H5SO3H)、对甲苯磺酸(或对甲基苯磺酸,CH3C6H4SO3H)或三氟甲磺酸(或三氟甲基磺酸,CF3SO3H)。木材处理方法,其中,不溶解化试剂为无机酸,例如矿物酸,其选自任意的卤化氢:盐酸(HCl)、氢溴酸(HBr)、氢碘酸(HI),或卤素的含氧酸:次氯酸、氯酸、高氯酸、高碘酸和溴和碘相应的化合物,或选自硫酸(H2SO4)、氟磺酸、硝酸(HNO3)、磷酸(H3PO4)、氟锑酸(fluoroantimonicacid)、氟硼酸、六氟磷酸、铬酸(H2CrO4)或硼酸(H3BO3)中的任意。木材处理方法,其中,不溶解化试剂为无机多价离子,其选自Al3+、Mg2+、Fe2+、Fe3+、Ca2+、Ba2+或具有抗衡离子的CaCl2、MgCl2、FeCl2或它们的组合。木材处理方法,其中,木质材料选自云杉(spruce)、松木(pine)、桦木(birch)、橡木(oak)、红杉(redwood)、雪松(cedar),或复合材料,如胶合板、纤维板、刨花板(particleboard),或基于纸浆的材料,如纸板、瓦楞纸板、石膏级纸板(gypsumgradepaperboard)、特种纸或纸浆模塑制品(mouldedpulpproduct)。木材处理方法,其中,不溶解化试剂为有机酸,以及碱金属硅酸盐为硅酸钠。木材处理方法,其中,不溶解化试剂为有机酸,且其中有机酸和硅酸钠之间合适的摩尔比可以为1:18~1:100。木材处理方法,其中,不溶解化试剂为有机酸,其中有机酸和硅酸钠之间合适的摩尔比可以为1:18~1:100,其中硅酸钠的Na+比SiO44-的摩尔比为0.6:1,且其中所述制剂具有大于11的pH值。木材处理方法,其中,不溶解化试剂的使用量比使水基制剂达到胶凝点所需的不溶解化试剂的量低至少10重量%。木材处理方法,其中,根据待处理的木质材料的酸度来选择或调整水基制剂中不溶解化试剂的量;木质材料酸度越高则制剂中需要的不溶解化试剂量越少。木材处理方法,其中,在干燥步骤之后进入木材处理工艺的熟成步骤之前,木质材料的干燥度为70%或更多。木材处理方法,其中,稳定的制剂为在室温或更低或在15~35°C的温度范围的保存期长于一个月。木材处理方法,其中,干燥步骤在室温或更低温度下进行,或在稍微升高的温度,例如15~70°C,尤其是20~50°C下进行。木材处理方法,其中,熟成步骤在40°C或更高的温度下进行,或在50°C~250°C或在70°C~120°C的范围或在75°C~100°C的范围进行。木材处理方法,其中,熟成步骤进行10~60分钟。木材处理方法,其中,通过在制剂中浸渍或浸泡木质材料,用制剂喷涂、涂覆或刷涂木质表面,或者根据通常的真空-压力浸渍程序通过使用真空和/或压力用制剂浸渍木质材料而将水基制剂应用到木质材料上。木材处理方法,其中,水基制剂还包括浓度为0.05%~5%(w/w)的润湿剂和/或浓度为0.05%~5%(w/w)的流变改性剂。本发明的方法处理的木质材料,其具有提高的阻燃性能,和具有提高的对腐烂、真菌、霉菌和昆虫的耐性。根据本发明的方法,其中,水基制剂具有比水的粘度高的粘度。根据本发明的方法,其中,使所述浸渍容器和内容物处于小于0.1atm的压力。附图说明图1示出熟成温度和各种无机或多价离子不溶解化试剂的再溶解后剩余的产品的图。图2示出浓度和再溶解后剩余的产品的图。图3示出熟成对于浸出的影响的图。图4示出熟成温度和再溶解后剩余的产品的图。图5示出熟成温度和浸出的图。图6示出不同制剂的熟成温度和浸出的图。图7示出根据本发明的不同的熟成温度的硅酸钾制剂对再溶解后剩余的产品的影响的图。发明详述介绍本发明涉及新型环境友好的木质材料处理方法,和用该方法处理的木质材料。特别是本发明涉及木材处理方法,在该方法中,使用了含有碱金属硅酸盐和不溶解化试剂的水基制剂以实现通过单罐制剂(one-potformulation)处理木质材料。木材处理方法用于处理木质材料,其中用水基制剂处理木质材料以提高木质材料的阻燃性能,以及木质材料对腐烂、真菌、霉菌和昆虫的耐性,该方法包括以下步骤:提供木质材料,然后提供水基制剂,该水基制剂保存期(shelflife)长,其基本上由碱金属硅酸盐、水和不溶解化试剂(选自有机酸、无机酸或无机多价离子)构成。为了确保水基制剂保存期长,并且使水基制剂在输运过程中、工厂内的储存和操作过程中保持稳定(不胶凝或沉淀),不溶解化试剂的添加量低于引起该水基制剂中的碱金属硅酸盐胶凝所需的不溶解化试剂的量。该点被称为胶凝点。任选地,本发明的水基制剂可包括润湿剂和/或流变改性剂。本发明的水基制剂通过下述方式应用到木质材料上:通过在制剂中浸渍(soaking)或浸泡(dipping)木质材料;或用制剂喷涂、涂覆或刷涂木质表面;或根据通常的真空-压力浸渍法通过使用真空和/或压力用制剂浸渍木质材料,然后在任何给定的温度下干燥经处理的木质材料以去除过量的水,接着进行最后步骤,包括在升高的温度下熟成经处理的木质材料,以使在经处理的木质材料内部或表面的碱金属硅酸盐不溶解。根据本发明的方法处理的木质材料,其特征在于具有对白蚁、真菌、霉菌的耐性以及耐火性能。木材处理组合物中的碱金属硅酸盐在使用本发明的木材处理方法应用到木质材料上以后,会高度不溶于水,并因此不容易从木材中浸出。经处理的木质材料即使在室外或潮湿的环境中使用,本发明的木材处理方法也能赋予木材对白蚁、真菌的耐性和耐火特性。根据本发明的方法应用到木质材料上的碱金属硅酸盐具有足够高的耐水性,换句话说,从木质材料中浸出的碱金属硅酸盐是足够低的,因此,即使经处理的木质材料处于水中或在室外使用,木质材料也能保持其对白蚁、真菌的耐性和耐火性能。使用本发明的方法处理的木质材料将能抵抗由腐烂真菌和白蚁破坏导致的腐败。木质材料也将具有耐火性,且有防霉性能。碱金属硅酸盐从经处理的木质材料中浸出通过测量当木材经历水时移出的碱金属硅酸盐的量来计算。这可通过实验,称重木质材料处理前,处理后以及经处理的木质材料在水浴中保存后的重量来完成。下面的公式用于计算(其中W=重量):未浸出的碱金属硅酸盐(%)=[(W浸出后的木材-W处理前的木材)/(W处理后的木材-W处理前的木材)]·100W处理后=用本发明方法处理的木质材料的干重W浸出后=用本发明方法的处理的木质材料进行了上述浸出步骤后的干重W处理前=用本发明方法处理前的木质材料的干重未浸出的碱金属硅酸盐(%)=进行了浸出步骤后,经处理的木质材料中剩余的碱金属硅酸盐的量(%)。未浸出的碱金属硅酸盐的百分含量总是期望尽可能地高。高的未浸出碱金属硅酸盐百分比值表示碱金属硅酸盐保留在经处理的木质材料中。理想的是,在经历水后,有高于70%的碱金属硅酸盐留在木质材料中(未浸出的碱金属硅酸盐的百分比高于70%)。本发明的方法中使用的水基制剂通常是由碱金属硅酸盐和不溶解化试剂形成,该不溶解化试剂一旦施加在木质材料上,即促进碱金属硅酸盐的聚合或以其他方式使其不溶解。该不溶解化试剂有助于使碱金属硅酸盐不溶解和耐水。合适的碱金属硅酸盐的例子是硅酸钠和硅酸钾。不溶解化试剂的例子是有机酸、无机酸和无机多价离子。下面的本发明的详细描述和相应的实施例将说明本发明的方法及其相应的材料。工艺详细描述提供木质材料合适的木质材料是,但不仅限于,实木(solidwood),如云杉、松木、桦木、橡木、红杉、雪松和其他;或复合材料,如胶合板、纤维板、刨花板或其他复合材料。根据本发明,源自木材的材料如纸浆基材料,例如纸板、瓦楞纸板、石膏等级纸板、特种纸,例如滤纸或打印纸、纸浆模塑制品,或其他以纸浆为基础的材料也被定义为木质材料,并也可以用该制剂处理。水基制剂根据本发明的木材处理方法包括混合碱金属硅酸盐、水和不溶解化试剂形成均匀水性溶液而制成的组合物或预制的水基制剂(premadewaterbasedformulation)。所述水基制剂也可任选地含有润湿剂和流变改性剂。组合物中不溶解化试剂与碱金属硅酸盐的比例仅可在较狭窄的特定范围内,并且加入到溶液中的不溶解化试剂的量须低于引发碱金属硅酸盐胶凝化所需要的量。不溶解化试剂的量必须在木质材料经过溶液处理后足以增强碱金属硅酸盐的胶凝形成,但并未达到在水基制剂应用到木质材料上以前启动胶凝形成的过程。通过仔细地选择不溶解化试剂和碱金属硅酸盐之间的比例,可以得到保存期长的制剂,其在处理木质材料然后干燥和熟成所述木材后变得不溶解。碱金属硅酸盐碱金属硅酸盐在水基制剂的总重量%中的重量百分比可以从1%w/w到50%w/w,更优选为10%w/w到40%w/w,最优选10%w/w到25%w/w。合适的碱金属硅酸盐的例子是硅酸钾和硅酸钠。由于经济方面的考虑,在制剂中硅酸钠是优选的。根据本发明的碱金属硅酸盐优选具有通式XNa+SiO44-的硅酸钠。硅酸钠是由Na2O和SiO2以反应形成XNa+SiO44-而制备的。钠和硅酸根(silicate)之间的摩尔比(Na+:SiO44-)可以在任意给定的摩尔比范围变化,但优选摩尔比为0.1:1至2:1的范围,更优选为0.5:1至0.8:1,最优选的摩尔比为0.6:1(对应于SiO2和Na2O之间的重量比为3.22)。本文所提及的所有的摩尔比均具有高的水溶性,这对保持制剂的低粘度以有效地浸渍木材是重要的。如上文所述的相同的摩尔比可适用到硅酸钾。钾和硅酸根的摩尔比(XK+:SiO44-)可以在任意给定的摩尔比范围变化,但优选在0.1:1至2:1的范围,或更优选为0.5:1至0.8:1。总体而言,根据本发明的水基制剂中碱金属(XM+)和硅酸根(SiO44-)之间的摩尔比可以在任何给定的摩尔比范围变化,但优选在0.1:1至2:1的范围。不溶解化试剂不溶解化试剂是可以提高碱金属硅酸盐聚合反应或复合物形成的物质。适用于本发明的不溶解化试剂是能够提高碱金属硅酸盐聚合或胶凝的,或以任何其他方式使之不溶于水的(例如通过促进碱金属硅酸盐单体物质形成复合物)的任何物质。通过向包含碱金属硅酸盐的水基制剂中添加酸或酸性化合物,或者添加能够促进碱金属硅酸盐单体形成复合物的无机多价离子,当pH值减小到一定水平时会发生碱金属硅酸盐的聚合或胶凝。不溶解化试剂的例子是有机酸、无机酸或无机多价离子。根据本发明,用作不溶解化试剂的有机酸例如是,低分子量或者分子量例如为40~500克/摩尔或40~300克/摩尔的有机酸。有机酸,例如选自任意羧酸;乙酸、扁桃酸、柠檬酸、天冬氨酸、谷氨酸、酒石酸、甲酸、丙酸、丁酸、戊酸、草酸、马来酸、琥珀酸或戊二酸或它们的组合。有机酸也可以选自任何低分子量磺酸,例如选自甲磺酸(CH3SO3H)、乙磺酸(或乙基磺酸,CH3CH2SO3H)、苯磺酸(或苯基磺酸,C6H5SO3H)、对甲苯磺酸(或对甲基苯磺酸,CH3C6H4SO3H)或三氟甲磺酸(或三氟甲基磺酸,CF3SO3H)。根据本发明,用作不溶解化试剂的无机酸例如是,矿物酸(mineralacids),这样的矿物酸选自任何的卤化氢和它们的溶液,例如:盐酸(HCl)、氢溴酸(HBr)、氢碘酸(HI)或卤素含氧酸,例如,次氯酸、氯酸、高氯酸、高碘酸和溴和碘相应的化合物,或选自硫酸(H2SO4)、氟磺酸、硝酸(HNO3)、磷酸(H3PO4)、氟锑酸、氟硼酸、六氟磷酸、铬酸(H2CrO4)或硼酸(H3BO3)中的任意,或它们的组合。通过利用复合物形成来使碱金属硅酸盐不溶解,也可以采用无机多价离子,如Cl2+、Mg2+、Fe2+、Fe3+、Ca2+、Ba2+或具有抗衡离子的CaCl2、MgCl2、FeCl2。制剂中的催化剂的浓度随碱金属硅酸盐的浓度和不溶解化试剂的效率而变化。如果使用酸作为不溶解化试剂,酸的pKa值对所需要的量是至关重要的。当采用酸时,木质材料本身的酸度也需要考虑,这是由于当应用到木材上时,木材内的酸也增加制剂中的总酸性物质含量。由于环境的原因,根据本发明的最优选的不溶解化试剂是无毒的有机酸,当用于工业规模时,它们是经济的替代方案。水溶液中的碱金属硅酸盐在某一点上开始胶凝。水基制剂的胶凝点或非胶凝范围可以通过控制该制剂的pH值或者通过控制不溶解化试剂与碱金属硅酸盐的摩尔比来测量或控制。重要的是,控制不溶解化试剂与碱金属硅酸盐的摩尔比或pH值的正确区间,以使得在将制剂应用到木质材料上之前,保持制剂不胶凝。例如,如果使用Na+与SiO44-的摩尔比为0.6:1的硅酸钠时,如期望该制剂的保存期长,则该制剂的pH值应不低于11。有机酸和硅酸钠之间合适的摩尔比可以是例如1:18~1:100,取决于经处理的木质基体的酸度和有机酸的pKa值。为了使水基制剂保持长的保存期,pH值必须不降低至目标点下,否则该制剂在保存较长一段时间后,将形成胶凝或沉淀。如果碱金属硅酸盐在应用到木材上之前开始胶凝,它将不能渗透固体木质材料。不溶解化试剂和碱金属硅酸盐之间的摩尔比也需要在特定的范围内,从而当水基制剂在高温下被干燥和熟成时,使碱金属硅酸盐不溶解。如果不溶解化试剂的量过低时,则在将碱金属硅酸盐制剂应用到木材上并熟成后,碱金属硅酸盐制剂将不会变得不溶解。根据所使用的不溶解化试剂及其作用模式(酸或多价离子),也需要考虑处理的木质材料。由于松香酸及其他木材产生的提取(extractive)物质,某些木材种类比其他的具有更高程度的固有酸度。其他具有更多的离子如Ca2+或Mg2+。当决定适当的不溶解化试剂和碱金属硅酸盐之间的摩尔比时,需要考虑各种固有物质的不同水平。例如,相比具有较低酸度的木质材料,如果采用相同程度的酸处理具有更高的固有酸度的木质材料时,碱金属硅酸盐可能就由于表面的局部pH太低而在木质材料的表面胶凝。这将限制可以渗入木质材料的碱金属硅酸盐的量,并因此限制该制剂在木质材料的阻燃和耐真菌性能方面的效率。可以通过进行一些简单的实验来确定不溶解化试剂和碱金属硅酸盐之间的适当的摩尔比。可以通过例如向碱金属硅酸盐水基制剂中加入不溶解化试剂,直到碱金属硅酸盐开始胶凝来确定加入到碱金属硅酸盐中的不溶解化试剂的最高浓度。通过加入比胶凝浓度低约10%的不溶解化试剂,会产生保存期长并且在经干燥和熟成变为不溶解的制剂。相比在木材外部干燥包含碱金属硅酸盐和不溶解化试剂的溶液,当木质材料用该制剂处理并熟成时,通常更高水平的碱金属硅酸盐变得不溶解。不受理论的约束,原因可能是,固有的酸度和/或木质材料中的多价离子浓度通过增加不溶解化试剂相对于碱金属硅酸盐的总浓度,有助于不溶解化过程,从而增加了不溶解化的碱金属硅酸盐的量。不溶解化试剂的优选的选择是无毒的有机酸,但也可以采用其它的酸。根据本发明的一个实施方式,保存期长的水基制剂是含有Na+:SiO44-的摩尔比为0.6:1的硅酸钠且pH大于11的制剂。含有相同的碱金属硅酸盐的制剂,如果pH值低于11则开始胶凝。保存期长的水基制剂是可以在室温或更低的温度或15~35°C温度范围存储一定的时间的试剂。在本发明的一个实施方式中,保存期长的水基制剂是可以在室温或更低的温度或15~35°C温度范围存储至少一个月或更长时间的制剂。在其它实施方式中,保存期长的制剂是可以存储至少2个月或更长的制剂。根据本发明的水基制剂具有长的保存期且是可存储是重要的,因为根据本发明的过程或方法,其目的是用在现代工业过程中。润湿剂和/或流变改性剂根据本发明,水基制剂中润湿剂(或表面活性剂)和/或流变改性剂的加入是可选的。润湿剂或表面活性剂可以加入到本发明的水基制剂中以降低表面张力。这对于使制剂更容易地渗入木质材料从而提高处理效果可能是重要的。不同类型的润湿剂是例如具有疏水尾部以及在其头部具有形式上带电的基团(formallychargedgroups)的极性物质,不同的表面活性剂的例子,请参见表面活性剂和界面现象,第三版(SurfactantsandInterfacialPhenomena,3rdEdition)。非离子表面活性剂的头部没有带电基团。本发明的水基制剂中的润湿剂的合适的浓度可以是,例如0.05%至5%(w/w)。流变改性剂可以加入到根据本发明的水基制剂中以增加制剂的粘度,从而,例如更容易通过使用不同的(例如)刷涂或涂敷技术将根据本发明的水基制剂应用到木质材料上。不同类型的流变改性剂是,例如,淀粉及其衍生物,或纤维素衍生物如羧甲基纤维素。本发明的水基制剂中的流变改性剂的合适的浓度,例如可以在0.5%至5%(w/w)。水基制剂在木质材料上的应用方法可以通过任何目前使用的工业工艺将水基制剂应用到木质材料上,例如通过在制剂中浸渍或浸泡木质材料,用制剂喷涂、涂覆(painting)或刷涂木质表面,或根据通常真空-压力浸渍程序通过使用真空和/或压力用制剂浸渍木质材料。干燥步骤当木质材料已被任何上面提到的应用方法处理后,需要将其干燥以从木质材料中除去多余的水。干燥过程可以发生在任何给定的温度下,但优选稍微升高的温度。在干燥木质材料时,确保进入在木材处理工艺的下一个步骤(熟成步骤)之前实现了足够的干燥是重要的。通过确保在进入熟成步骤前木质材料是干燥的(70~90%干燥度),我们发现木材仅需熟成很短的时间(短至1分钟)则仍然可以在低浸出方面得到提高的性能。因此,相比任何已知的木材处理方法,根据本发明的方法是对环境更友好的,这是由于木材处理过程中加热的使用可以被减少到最低限度,并且碱金属硅酸盐仍然无法容易地从经处理的木质材料中浸出。本发明的一个实施方式中的干燥步骤在室温或稍高的温度下进行,如在15~70°C或15~60°C或15~50°C或尤其是20~50°C进行。用标准化的设备检测木材干燥度来容易地监控木材的干燥。在熟成步骤之前,木材的干燥度为至少70%或更高,优选为80%或更高,或最优选85%或更高。如果在进入熟成步骤之前完成干燥,则在升高的温度下的熟成的时间会更短。根据本发明方法,在熟成木质材料前,木质材料的干燥度应为70%干燥度或更高,例如70~100%的干燥度,或例如80~100%的干燥度。干燥步骤的温度优选为10°C至100°C,或甚至可以更优选为25°C至70°C或尤其是40°C至60°C。可以使用普通的木质材料干燥设备,以促进木质材料的干燥。熟成步骤当在干燥步骤期间,一定量的水从木材中蒸发后,根据本发明的经处理的木质材料需要在升高的温度下熟成一定的时间,以便让碱金属硅酸盐反应形成聚合物或复合物,这使得碱金属硅酸盐不溶解于水。在本发明的一个实施方式中,在40°C或更高的温度下熟成经处理的木质材料,优选在60°C或更高。在本发明更优选的实施方式中,木材在60°C至150°C的温度范围熟成,在更优选的实施方案中,木材在70°C至120°C的温度范围熟成。在本发明最优选的实施方式中,木材在75°C至100°C的温度范围熟成。该区间的选择是由于其工业适用性和由于使用该温度区间碱金属硅酸盐得到其所需的浸出性能的事实。根据熟成温度,足以使碱金属硅酸盐不溶解的时间会有所不同。熟成温度越高需要的熟成时间越短,熟成温度越低则需要的熟成时间越长。如果使用高于150°C的熟成温度,必须警惕不要产生由于纤维的热解导致的木材变色。取决于制剂中不溶解化试剂的碱金属盐的摩尔比,熟成时间也可以有所不同。约接近胶凝点的摩尔比需要的熟成时间越短,而越高的摩尔比相应将需要越长的熟成时间。在最优选的实施方案中,根据木质材料的厚度,木质材料应在70-90°C熟成10-60分钟。然而,根据木材的品种和使用的制剂,需要不同的熟成时间。最佳熟成时间,可以很容易地由本领域技术人员通过一些简单的实验来确定。使用根据本发明的方法处理的木质材料根据本发明,还提供经所述方法处理的木质材料。木质材料可以是任何类型,包括实木如杉木、松木、桦木、橡木、红杉、雪松和其他;或复合材料,如胶合板、纤维板、刨花板或其他复合材料。根据本发明,木质材料也可以是基于木纸浆的材料,如纸板、瓦楞纸板、石膏级纸板、特种纸、纸浆模塑制品,或其他基于纸浆的材料。木质材料的特征在于,具有阻燃性能和/或耐真菌性能,如对腐烂真菌(rotfungus)和/或霉菌的耐性。此外,木质材料具有更好的抵抗噬木昆虫如白蚁、蚂蚁和钻蛀虫(borer)的性能。通过本方法,木质材料的表面还可以硬化,这在某些应用中是非常有用的。根据本发明的优选方法的实例:本发明方法的一种优选的应用例是真空-压力-真空浸渍法。在该方法中,木质材料被放置在真空-压力-浸渍容器中。之后该容器填充水基制剂,其后在处于高于90%的真空10~40分钟时间,然后在6~16巴的压力20分钟至12小时,然后在高于90%的真空下10~40分钟。时间和压力的变化取决于所使用的木质材料,以及多少水基制剂应当渗入木质材料。渗入木质材料的水基制剂的量对于其能达到的效果是重要的。渗透越多将给予越好的阻燃性和真菌保护性能。本发明的制剂具有高于水的粘度,这使得相比于使用具有低于水的粘度或类似于水的粘度的浸渍液而言,木质材料的渗透更加困难。为了获得阻燃性和防腐烂方面的最高程度的效果,需要高渗透的木质材料浸渍。为了获得根据本发明的制剂在木质材料中的有效渗透的最有效的生产方法是真空-压力-真空浸渍法。所述浸渍容器可以处于低于0.1个大气压,例如0.1-0个大气压。根据本发明的水基制剂优选具有比水的粘度高的粘度。通过相应的实施例,本发明的更多的实施方式将是显而易见的。实验部分生产根据本发明的水基制剂的实施例生产1000g硼酸/硅酸钠溶液的实施例。在588.14克冷水中,边混合边添加19.76克硼酸。该溶液混合10分钟,以确保所有的硼酸溶解。向容器中添加392.10克的硅酸钠。在混合过程中,硼酸溶液以约200克/分钟的速率加入。完成的制剂另外搅拌10分钟,以确保该制剂是均匀的。经测定pH值为11.1。成品倒入塑料容器中存储。生产根据本发明的水基制剂时的其他考虑以类似上文的方式制备具有有机酸或无机酸作为不溶解化试剂的硅酸钠制剂。调整不溶解化试剂的量以获得保存期长的水基制剂,其在储存过程中是稳定的,并因此是不靠近它的胶凝化点的,对于含摩尔比为0.6:1的硅酸钠的制剂,其胶凝化点在pH值10.6左右。本发明的水基制剂中使用的不溶解化试剂所需的量,可通过下述方法测定,首先通过添加不溶解化试剂到硅酸盐溶液中,直到达到它的胶凝化点来制备溶液。为了制备根据本发明的新的可存储的、保存期长的稳定水基制剂,不溶解化试剂的添加量应充分低于达到的胶凝点所需的不溶解化试剂的量。例如根据本发明的不溶解化试剂使用的量比达到胶凝点水基制剂所需的不溶解化试剂的量少10重量%或少更多。这种不溶解化试剂的量的计算方法可用于根据本发明使用的所有可能的不溶解化试剂。当使用酸作为不溶解化试剂时,另一种测量所需的不溶解化试剂的量的方法是,水基制剂的pH值充分高于胶凝点的pH值。本发明的不同制剂的胶凝点的pH值会有所不同,这取决于使用何种碱金属硅酸盐,例如,根据本发明的保存期长的,并因此在储存过程中稳定的制剂的pH值可以是11或更高,使用相同的碱金属硅酸盐(含更多量的不溶解化试剂)时胶凝点的pH值在10.6左右。确定浸出的再溶解试验的通用方法在实施例1-2,实施例4和9中,使用根据以下原则的再溶解试验,通过模拟浸出来研究浸出性能:在塑料容器中制备根据本发明的制剂。此后该制剂(仍然在塑料容器)在不同温度下于烘箱中干燥和熟成。对干燥和熟成的制剂称重,并加入到烧杯中,用磁力搅拌器搅拌。200毫升沸腾的热水加入到烧杯中,在连续搅拌下,制剂再溶解3分钟。3分钟后,用滤纸和布氏漏斗真空过滤烧杯中的内容物。未溶解的碱金属硅酸盐的量依下式计算:再溶解后剩余的产品(%)=100-[(W熟成后-W再溶解后)/W熟成后]·100确定浸出的通用方法在实施例3和实施例5-6中,根据以下原则进行测试研究了浸出性能:制备根据本发明的制剂。此后,将该制剂应用到木质材料上。在不同温度和时间下,于烘箱中干燥和熟成处理木质材料。称重经干燥和熟成处理的木质材料,并加入烧杯中。经处理的木质材料在单独的容器中用蒸馏水(每天更换)浸出。1周后,对浸出的样品进行称重,并再调节(reconditioned)直至达到恒重为止。浸出期间的失重可以依据下式计算:浸出后在树样品中剩余的制剂(%)=100-[(W熟成后的制剂-W浸出后的制剂)/W熟成后的制剂]·100其中W熟成后的制剂=W熟成后的干样品-W处理前的干样品W浸出后的制剂=W浸出后的干样品-W处理前的干样品实施例下列实施例的目的是为了证明已经过本发明的方法处理的硅酸钠的溶解度,已经过本发明的方法处理的木质材料的已浸渍入木质材料中硅酸钠的浸出,阻燃和耐腐烂性。实施例1-提供改进的浸出性能的各种不溶解化试剂。使用含有各种不溶解化试剂的本发明的制剂对硅酸钠的溶解度的影响,在实施例中示出了无机酸:硼酸,无机多价离子:氯化钙。通过首先混合不溶解化试剂和水,然后在连续搅拌下缓慢向硅酸钠中加入溶解的不溶解化试剂混合物来制备制剂。将20.0克的制剂1、2和3加入到具有大表面积的一次性使用的容器中,在50°C下干燥过夜。当干燥了,所述制剂在20°C和190°C熟成30分钟。其结果示于图1。实施例2-制剂的浓度的影响使用具有不同的制剂干基含量(drycontent)的本发明的制剂对硅酸钠的溶解度的影响。通过首先混合不溶解化试剂和水,然后在连续搅拌下缓慢向硅酸钠中加入溶解的不溶解化试剂混合物来制备制剂。将20.0克的制剂4和5以及制剂的水稀释物加入到具有大表面积的一次性使用的容器中,在50°C下干燥过夜。当干燥了,所述制剂在100°C熟成30分钟。然后,所有的样品都根据上述的通用方法进行再溶解测试。其结果示于图2。在图2中的稀释的制剂的干基含量对应于水溶液中的硅酸盐和不溶解化试剂的重量百分数。实施例3-经浸渍的纸材料的硅酸钠的浸出使用本发明的不同制剂浸渍的纸样品对硅酸钠浸出的影响。通过浸泡10秒来浸渍直径185毫米的滤纸样品。在室温下干燥经浸渍的样品过夜。在100°C熟成10分钟。在单独的容器中,用300毫升90°C的水,通过使纸材料在水中保持10分钟使样品进行浸出。干燥后,计算纸在浸出过程中的重量损失:浸出后剩余的制剂(%)=100-[(W浸出后的纸–W未处理的纸)/(W浸出前的纸–W未处理的纸)]·100浸出过程的结果显示当在制剂中添加不溶解化试剂(柠檬酸)时,抗浸出性提高。其结果示于图3。实施例4-熟成温度当使用具有不同的熟成温度的本发明的制剂时对硅酸钠溶解度的影响。通过首先混合不溶解化试剂(柠檬酸)和水,然后在连续搅拌下缓慢向硅酸钠中加入溶解的不溶解化试剂混合物来制备制剂。将20.0克的制剂3和6加入到具有大表面积的一次性使用的容器中,在室温下干燥到干燥。当干燥了,具有所述制剂的容器在20°C、70°C和190°C下熟成30分钟。然后,所有的样品都根据上述的通用方法进行再溶解测试。结果示于图4中。实施例5-硅酸钠浸渍的松木样品的浸出使用本发明的不同制剂浸渍的松木样品以及不同的熟成温度对硅酸钠浸出的影响。使用制剂3、6和7,在真空下浸渍尺寸为0.8厘米×1.5厘米×7厘米的松木边材样品20分钟,接着在大气压力下进行20分钟的浸泡。经浸渍的样品在50°C下干燥过夜,在20°C、70°C、110°C、150°C和190°C熟成30分钟。样品在单独的容器中用75毫升蒸馏水浸出,每天换水。在整个浸出过程中测定pH值。1周后,对该经浸出的样品进行称重,并在50°C下再调节直到达到恒重。然后可以根据下式计算浸出过程中的重量损失:浸出后松木样品中剩余的制剂(%)=100-[(W熟成后的制剂-W浸出后的制剂)/W熟成后的制剂]·100其中W熟成后的制剂=W熟成后的干样品-W处理前的干样品W浸出后的制剂=W浸出后的干样品-W处理前的干样品浸出过程的结果显示当在制剂中加入不溶解化试剂(柠檬酸)时抗浸出性增加。结果示于图5中。实施例6-经硅酸钠浸渍的松木样品的浸出使用制剂3、6和7,在真空条件下浸渍尺寸为0.8厘米×1.5厘米×7厘米的松木边材(sapwood)样品20分钟,接着在大气压力下进行20分钟的浸泡。经浸渍的样品在50°C下干燥过夜,并在70°C熟成30分钟。样品在单独的容器中用75毫升蒸馏水浸出,每天换水。在整个浸出过程中测定pH值。1周后,对该经浸出的样品进行称重,并在50°C下再调节直到达到恒重。然后可以根据下式计算浸出过程中的重量损失:浸出后松木样品中剩余的制剂(%)=100-[(W熟成后的制剂-W浸出后的制剂)/W熟成后的制剂]·100其中W熟成后的制剂=W熟成后的干样品-W处理前的干样品W浸出后的制剂=W浸出后的干样品-W处理前的干样品浸出过程的结果显示当制剂中加入不溶解化试剂(柠檬酸)时抗浸出性增加。越高的不溶解化试剂含量产生越好的抗浸出性。结果示于图6中。实施例7–对火的反应使用本发明的方法处理过的木材对阻燃性的影响通过使用标准化的ISO试验(ISO5660)进行评价。在试验中,对所述处理过的木质材料与火反应(reaction-to-fire)、释放热、产烟量和重量损失率进行了测量。在实验中,使用以下制剂处理木料。按照下面的过程浸渍纤维板,95%的真空度下40分钟和在8巴的压力下40分钟。然后在23°C,相对湿度50%的条件下干燥纤维板,直到达到平衡。结果表明,使用制剂3、6、8浸渍的纤维板时,指示等级从D类改善为C类,且使用制剂9浸渍的纤维板时,指示等级从D类改善为B类。实施例8–抗腐烂性根据下述过程评价本发明的制剂的抗腐烂性能力的效果,“EN113-用于确定抵抗木材破坏性担子菌类的防护效果的试验方法”。制剂10处理的松木边材通过了该标准。实施例-9硅酸钾制剂的浸出具有不同熟成温度的使用硅酸钾的本发明的制剂对溶解度的影响。通过首先混合不溶解化试剂和水,然后在连续搅拌下缓慢向硅酸钾中加入溶解的不溶解化试剂混合物来制备制剂。将20.0克的制剂11和12加入到具有大表面积的一次性使用的容器中,在50°C下干燥过夜。当干燥了,所述制剂的容器在20和190°C下熟成30分钟。然后,所有的样品都根据上述的通常方法进行再溶解测试。结果示于图7中。