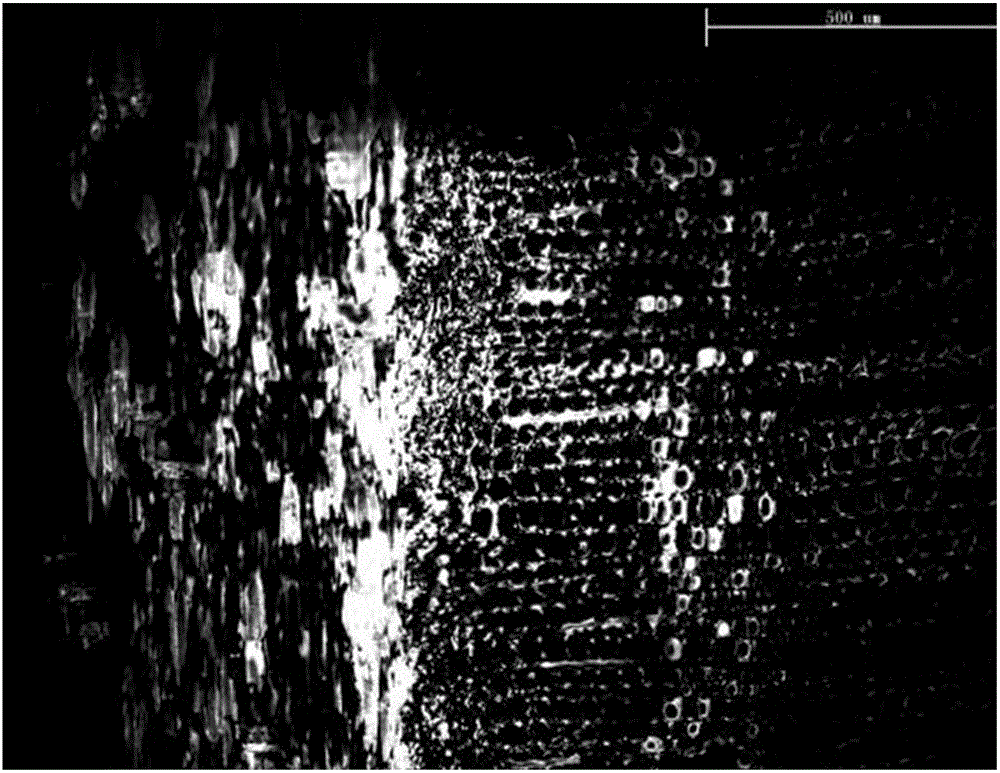
本发明涉及一种提高胶合强度的方法,特别涉及一种提高木质材料胶合强度的方法及胶合板制备方法。
背景技术:
:常规胶合板制造工艺包括原木截断、蒸煮、旋切或者刨切、干燥、施胶、铺装、热压、冷却、裁切和分选等工序。其中胶黏剂对胶合强度起着重要作用。在综合考虑生产成本和胶合强度的因素下,胶合板生产一般使用脲醛树脂胶黏剂。由于脲醛树脂本身性能的影响,如低摩尔比、低游离醛树脂和较低的固含量等因素都会导致胶合板的耐水性差和胶合强度(湿强度)的下降。同时,在常规制造工艺中,若采用胶黏剂的黏度不高,尤其不脱水胶粘剂,胶黏剂容易渗透到木质单板中,且木材是多孔性材料,从而导致在胶层处的胶黏剂量明显减少,不利于胶合。另一方面,热固性胶粘剂通常在热压过程中,起初随着温度提高,胶粘剂粘度降低,X.Lu和A.Pizzi指出:当胶层温度达到60-80℃时,粘度最小,分散性达到最大,之后胶粘剂粘度急剧增加。粘度降低加大胶粘剂通过木材中的木射线或裂隙渗透[参考:X.LuandA.Pizzi,SubstrateInfluenceonTTTandCHTCuringDiagramsofWoodAdhesives,HolzalsRoh-undWerkstoff.56(5)(1998):339-346],导致胶合性能显著降低。一些国内外研究表明,如[作者为钱俊等,文献名称为:《电场对杨木胶合效应之初探》,来自《浙江林学院学报》,1999,16(2):109-113;作者为钱俊等,文献名称为:《电场对杨木胶合效应之再探》,来自《浙江林学院学报》,1999,16(2):293-296],其研究使用低压条件制备胶合板,且胶黏剂是聚醋酸乙烯乳液,是非通用制备胶合板的胶黏剂,且胶合板的胶合强度提高效果不是很明显;同时也未完全解决现有技术中存在的胶黏剂的粘度低、摩尔比低、木材多孔性导致的渗胶量大,木质胶合材料的胶合强度不高,甲醛释放量高等问题;尤其对于国内采用的胶黏剂是未经过脱水的,上述问题更加严重。技术实现要素:1.发明要解决的技术问题针对现有技术中存在的胶黏剂的粘度低、摩尔比低、木材多孔性导致的渗胶量大、木质胶合材料的胶合强度低、甲醛释放量和工作环境是否安全等技术问题,本发明公开了一种提高木质材料胶合强度的方法及胶合板制备方法,通过在热压过程中利用高压静电场处理涂胶后的木质材料,使木质材料的两侧形成强大的静电电压,即使采用的胶黏剂是未经过脱水的(固含量为等于或小于50%),处理后木质胶合材料的胶合强度完全满足要求,与采用普通胶合方法制备的木质胶合材料相比胶合强度提高了一倍以上。2.技术方案发明原理:基于库伦定律、静电理论Vanutian规则和集聚原则,微小带电粒子上若混有反极性的大粒子时,会使凝聚速度加快。在木质材料胶合过程,进行冷压或热压,当其温度达到60℃~80℃时,胶黏剂的黏度达到最低,加高压静电,在高压静电场的作用下,甲醛与尿素反应进一步完善(见图3),由红外图谱得出:在低波数区段,1500-1575cm-1为酰胺ΙΙ带,其特征峰逐渐移向低波数,说明反应强度变大,反应更加完全;在985-1035cm-1内,波峰强度逐渐增强,说明了羟甲基含量增加,使固化后的胶黏剂交联密度上升。再之,在高压静电条件下,胶黏剂分子极性化和取向化,从而获得了更多的化学键,增加了尿素与甲醛的反应几率。最终,胶黏剂发生集聚现象,并于木质材料胶接面上凝聚,从而提高木质材料的胶合强度,降低了甲醛释放量;而低压静电无法促使胶黏剂取向化和集聚,且未完全解决现有技术中存在的胶黏剂的粘度低、摩尔比低、木材多孔性导致的渗胶量大、木质胶合材料的胶合强度不高和甲醛释放量等问题;尤其对于国内采用的胶黏剂是未经过脱水的,上述问题更加严重。因此,对于胶合强度没有明显的作用。为解决上述技术问题,本发明通过下述实施方案来实现:一种提高木质材料胶合强度的方法,其步骤包括:涂胶后的木质材料在其加压过程中,对涂胶后的木质材料两侧加高压静电,形成最终木质胶合材料。优选的在加压过程中,在热压过程中对涂胶后的木质材料沿热压方向的两侧加高压静电。优选的高压静电,即接电后,涂胶后的木质材料两侧的电压差至少为1kV。如,通过高压静电发生器接负极板于涂胶后的木质材料上侧,负压为至少1kV(千伏)以上;接地极板为0kV于涂胶后的木质材料下侧。优选的对涂胶后的木质材料两侧加高压静电,其处理时间至少为200s以上;且通过高压静电发生器接负极板于涂胶后的木质材料上侧,接地极板于涂胶后的木质材料下侧。优选的木质材料的含水率为8±3%;高压静电处理时间为300s至500s。优选的所述涂胶后的木质材料,其采用的胶黏剂是未经脱水的,固含量等于或小于50%。一种胶合板制备方法,包括以下步骤:(1)将木材旋切或者刨切成木质单板;(2)对步骤(1)中处理后的木质单板进行干燥;(3)对步骤(2)中处理后的木质单板进行涂饰胶黏剂,且在胶黏剂中加入固化剂氯化铵;(4)对步骤(3)中处理后的木质单板进行组坯;(5)对步骤(4)中处理后的板坯进行热压,沿热压方向对板坯两侧加高压静电,将高压静电发生器接负极板于板坯上侧,负压为1-15kV以上;接地极板为0kV于板坯下侧;(6)对步骤(5)中处理的板坯,达到静电处理时间后立即关静电;(7)对步骤(6)中处理后的板坯,达到热压时间后,卸压、冷却、裁边和砂光处理,制得胶合板。优选的,所述的步骤(1)中木质单板的厚度为2.6-2.8mm;所述步骤(2)的干燥,在干燥箱中进行的,干燥温度为50℃,时间为12h,终含水率为8±3%。优选的,所述的步骤(3)处所述的胶黏剂为脲醛树脂,不经过脱水处理,固含量为小于等于50%,甲醛与尿素的摩尔比为1.5,氯化铵是脲醛树脂的重量的0.5-1.5%,双面施胶量为200-300g/m2。优选的,步骤(4)中所述板坯为纵-横-纵三层或奇数层组坯方式,其热压条件为95℃-110℃,单位压力为1MPa,热压时间20-60s/mm;步骤(6)高压静电处理时间为300s-500s。3.有益效果通过利用高压静电场处理木质材料胶合,影响胶黏剂的分布、定向和运动,从而使木质材料两侧的胶黏剂产生集聚现象,解决了低摩尔比胶黏剂对于木质材料胶合性能差和耐水性差的问题,以及减少了木材自身多孔性缺陷的影响,获得了木质胶合材料胶合强度倍增的效果,大大减少了胶黏剂和木材本身对木质胶合材料的不利影响,显著地提高了胶合强度,得到了高性能的木质胶合材料。同时利用高压静电条件处理热压过程中的木质材料,不仅提高木质胶合材料的胶合强度,而且高压静电法消耗功率小,从而实现了低成本、高性能木质胶合材料的制备。附图说明:图1(a)为未加静电处理制备的胶合板纵向和横向单板(无裂隙度)胶接层处微观构造图,其中,1—纵向单板,2—胶接层,3—横向单板;图1(b)为未加静电处理制备的胶合板纵向和横向单板(无裂隙度)胶接层处的胶黏剂在两单板中分布状态的微观构造图(不含木材部分),其中白色部分为胶黏剂的分布形态,图片背景为黑色;图2(a)为静电处理500s后所制备的胶合板纵向和横向单板(无裂隙度)胶接层处微观构造图,其中,1—纵向单板,2—胶接层,3—横向单板;图2(b)为静电处理500s后所制备的胶合板纵向和横向单板(无裂隙度)胶接层处的胶黏剂在两单板中分布状态的微观构造图(不含木材部分),其中白色部分为胶黏剂的分布形态,图片背景为黑色;图3(a)为未加静电处理制备的胶合板纵向和横向单板(裂隙度38%)胶接层处微观构造图,其中,1—纵向单板,2—胶接层,3—横向单板;图3(b)为未加静电处理制备的胶合板纵向和横向单板(裂隙度38%)胶接层处的胶黏剂在两单板中分布状态的微观构造图(不含木材部分),其中白色部分为胶黏剂的分布形态,图片背景为黑色;图4(a)为静电处理500s后所制备的胶合板纵向和横向单板(裂隙度38%)胶接层处微观构造图,其中,1—纵向单板,2—胶接层,3—横向单板;图4(b)为静电处理500s后所制备的胶合板纵向和横向单板(裂隙度38%)胶接层处的胶黏剂在两单板中分布状态的微观构造图(不含木材部分),其中白色部分为胶黏剂的分布形态,图片背景为黑色;图5为未加静电处理和静电处理500s后制备的胶合板(裂隙度38%)中的脲醛树脂的傅里叶变换红外光谱图。具体实施方式:实施例1:一种利用高压静电高效提高木质胶合材料胶合强度的制造方法,包括如下步骤:1)刨切:刨切好的南方松单板(无裂隙度),其厚度为2.6-2.8mm的木质单板,在干燥箱中进行的,干燥温度为50℃,时间为12h,终含水率为7%。2)涂胶:将干燥后的木质单板进行涂饰胶黏剂,且在胶黏剂中加入固化剂氯化铵,胶黏剂为脲醛树脂,甲醛与尿素摩尔比为F/U=1.5,氯化铵是脲醛树脂重量的1%,双面施胶量为300g/m2,固含量为50%。3)组坯:按照胶合板的纵-横-纵三层组坯方式,制备三层结构胶合板的板坯。4)热压并加高压静电:将板坯放入压机后,将高压静电发生器接负极板于板坯上侧,负压为10kV;接地极板为0kV于板坯下侧,立即打开高压静电发生器,静电处理时间分别为0s(未处理)、200s、300s和500s。热压条件为110℃,板坯压力为1.0MPa,热压时间60s/mm(秒每毫米)。5)关闭静电发生器:达到高压静电处理时间后关闭静电发生器。6)卸压:达到热压时间后,热压结束,卸压取出板坯,然后冷却、裁边、和砂光处理,制的胶合板。按照实施例1的工序得到的木质材料的胶合板检测数据(GB/T17657-2013),如表1和表2所示;图1(a)为未加静电处理制备的胶合板纵向和横向单板胶接层处微观构造图,其中,纵向单板1,胶接层2,横向单板3;以及图1(b)为未加静电处理制备的胶合板纵向和横向单板胶接层处的胶黏剂在两单板中分布状态的微观构造图(不含木材部分),其中白色部分为胶黏剂的分布形态,图片背景为黑色。而图2(a)为静电处理500s后所制备的胶合板纵向和横向单板胶接层处微观构造图,其中,纵向单板1,胶接层2,横向单板3;图2(b)为静电处理500s后所制备的胶合板纵向和横向单板胶接层处的胶黏剂在两单板中分布状态的微观构造图(不含木材部分),其中白色部分为胶黏剂的分布形态,图片背景为黑色。从上述图中反映出通过利用高压静电场处理木质材料胶合,影响胶黏剂的分布、定向和运动,从而使木质材料两侧的胶黏剂产生集聚现象,解决了低摩尔比胶黏剂对于木质材料胶合性能差和耐水性差的问题,以及减少了木材自身多孔性缺陷的影响,获得了木质胶合材料胶合强度倍增的效果,大大减少了胶黏剂和木材本身对木质胶合材料的不利影响,显著地提高了胶合强度。表1木质材料胶合板的胶合强度检测数据表2木质材料的胶合板甲醛释放量检测数据静电处理时间(s)甲醛释放量(mg/L)035002.7实施例2:一种利用高压静电高效提高木质胶合材料胶合强度的制造方法,包括如下步骤:实施步骤同实施例1,不同在于,1)旋切:旋切好的木质单板(裂隙度38%),其厚度为2.6-2.8mm的单板,含水率为7%。2)涂胶:胶黏剂为脲醛树脂,甲醛与尿素摩尔比为F/U=1.5,氯化铵是脲醛树脂重量的1.5%,双面施胶量为300g/m2,固含量为47%。3)组坯:按照胶合板的组坯方式,制备三层结构胶合板。4)热压并加高压静电:将高压静电发生器接负极板于板坯上侧,负压为10kV;接地极板为0kV于板坯下侧。将板坯放入压机后,立即打开静电发生器,静电处理时间分别为0s、300s和500s。热压条件为110℃,板坯压力为1.0MPa,热压时间60s/mm。5)关闭静电发生器:达到高压静电处理时间后关闭静电发生器6)卸压:热压结束后,卸压取出板坯,然后冷却、裁边、砂光处理,制的胶合板。按照实施例2的工序得到的木质材料胶合板的检测数据(GB/T17657-2013),如表3所示;图3(a)为未加静电处理制备的胶合板纵向和横向单板胶接层处微观构造图,其中,纵向单板1,胶接层2,横向单板3;图3(b)为未加静电处理制备的胶合板纵向和横向单板胶接层处的胶黏剂在两单板中分布状态的微观构造图(不含木材部分),其中白色部分为胶黏剂的分布形态,图片背景为黑色。图4(a)为静电处理500s后所制备的胶合板纵向和横向单板胶接层处微观构造图,其中,纵向单板1,胶接层2,横向单板3;图4(b)为静电处理500s后所制备的胶合板纵向和横向单板胶接层处的胶黏剂在两单板中分布状态的微观构造图(不含木材部分),其中白色部分为胶黏剂的分布形态,图片背景为黑色;图5为未加静电处理和静电处理500s后制备的胶合板中的脲醛树脂的傅里叶变换红外光谱图。从上述图中反映出,在高压静电条件下,胶黏剂分子极性化和取向化,从而获得了更多的化学键,增加了尿素与甲醛的反应几率。最终,胶黏剂发生集聚现象,并于木质材料胶接面上凝聚,从而提高木质材料的胶合强度。由红外图谱得出:在高压静电场的作用下,甲醛与尿素反应进一步完善,在低波数区段,1500-1575cm-1为酰胺ΙΙ带,其特征峰逐渐移向低波数,说明反应强度变大,反应更加完全;在985-1035cm-1内,波峰强度逐渐增强,说明了羟甲基含量增加,使固化后的胶黏剂交联密度上升。表3木质材料胶合板的胶合强度检测数据由于实施例1的表1中的单板选用的是南方松单板,即无裂隙度;而实施例2中的板坯材料选用的是旋切单板,有裂隙度,裂隙度为38%。一部分胶黏剂会遗留在裂隙中,因此胶合强度提高率会降低,但都高于现有的试验数据。实施例3:步骤同实施例2,在干燥箱中进行的,干燥温度为50℃,时间为12h,终含水率为8%。区别在于胶黏剂的固含量50%,甲醛与尿素摩尔比为F/U=1.5,氯化铵是脲醛树脂重量的0.5%,双面施胶量为200g/m2。按照实施例3的工序得到的木质材料的检测数据(GB/T17657-2013),如表4所示:表4木质材料胶合板的胶合强度检测数据实施例4:步骤同实施例2,区别在于胶黏剂的固含量50%,甲醛与尿素摩尔比为F/U=1.5,氯化铵是脲醛树脂重量的1%,热压温度为95℃。按照实施例4的工序得到的木质材料的检测数据(GB/T17657-2013),如表5所示:表5木质材料胶合板的胶合强度检测数据实施例5:步骤同实施例2,在干燥箱中进行的,干燥温度为50℃,时间为12h,终含水率为5%。区别在于胶黏剂的固含量50%,甲醛与尿素摩尔比为F/U=1.5,氯化铵是脲醛树脂重量的1%,奇数层组坯方式为五层结构胶合板,热压温度为100℃。按照实施例5的工序得到的木质材料的检测数据(GB/T17657-2013),如表6所示:表6木质材料胶合板的胶合强度检测数据实施例6:步骤同实施例2,区别在于胶黏剂的固含量50%,高压静电发生器接负极板于板坯上侧,负压为1kV;接地极板为0kV于板坯下侧。得到的板坯均按照GB/T17657-2013进行检测。高压静电处理后的胶合板的胶合强度高于未加静电的板坯强度,且高压静电处理后的胶合板胶合强度均符合标准要求。实施例7:步骤同实施例2,区别在于,在干燥箱中进行的,干燥温度为50℃,时间为12h,终含水率为11%。胶黏剂的固含量50%,高压静电发生器接负极板于板坯上侧,负压为15kV;接地极板为0kV于板坯下侧。得到的板坯均按照GB/T17657-2013进行检测。高压静电处理后的胶合板的胶合强度高于未加静电的板坯强度,且高压静电处理后的胶合板胶合强度均符合标准要求。实施例8:步骤同实施例2,区别在于,胶黏剂的固含量为50%,对板坯左侧、右侧加压,高压静电发生器接负极板于板坯左侧,接负极板与板坯右侧。得到的板坯均按照GB/T17657-2013进行检测。高压静电处理后的胶合板的胶合强度高于未加静电的板坯强度,且高压静电处理后的胶合板胶合强度均符合标准要求。实施例9:步骤同实施例2,区别在于,胶黏剂的固含量为30%,得到的板坯均按照GB/T17657-2013进行检测。高压静电处理后的胶合板的胶合强度高于未加静电的板坯强度,且高压静电处理后的胶合板胶合强度均符合标准要求。实施例10:步骤同实施例2,区别在于,胶黏剂的固含量为40%,得到的板坯均按照GB/T17657-2013进行检测。高压静电处理后的胶合板的胶合强度高于未加静电的板坯强度,且高压静电处理后的胶合板胶合强度均符合标准要求。实施例11:一种利用高压静电高效提高木质材料胶合强度的制造方法,包括如下步骤:1)旋切:旋切好的木质单板(裂隙度38%),其厚度为2.6-2.8mm的单板,含水率为7%。2)涂胶:胶黏剂为酚醛树脂,固含量50%,双面施胶量为250g/m2。3)组坯:按照单板层积材的组坯方式,制备九层结构单板层积材。4)热压并加高压静电:将高压静电发生器接负极板于板坯上侧,负压为10kV;接地极板为0kV于板坯下侧。将板坯放入压机后,立即打开静电发生器。热压条件为145℃,板坯单位压力为1.0MPa,热压时间60s/mm。5)关闭静电发生器:达到高压静电处理时间后关闭静电发生器6)卸压:热压结束后,卸压取出板坯,然后冷却、裁边、分选。按照实施例11的工序得到的木质材料的检测数据(GB/T20241-2006),如表7所示:表7木质材料的浸渍剥离率检测数据实施例12:提高木质材料胶合木胶合强度的制造方法,包括如下步骤:1)制材:锯制好的南方松锯材,其厚度和宽度分别为16mm和140mm,含水率为10%。2)涂胶:胶黏剂为间苯二酚-苯酚-甲醛共聚树脂,固含量50%,双面施胶量为250g/m2。3)组坯:按照胶合木的组坯方式,制备三层结构胶合木的板坯。4)热压并加高压静电:将高压静电发生器接负极板于板坯上侧,负压为10kV;接地极板为0kV于板坯下侧。将板坯放入压机后,立即打开静电发生器。热压条件为145℃,板坯单位压力为1.0MPa,热压时间60s/mm。5)关闭静电发生器:达到高压静电处理时间后关闭静电发生器6)卸压:热压结束后,卸压取出材料,然后冷却、裁边和分选,制备三层结构胶合木。按照实施例12的工序得到的木质材料的检测数据(GB/T26899-2011)。高压静电处理后的木质材料胶合木的胶合强度高于未加静电的胶合木强度,且高压静电处理后的胶合强度均符合标准要求。当前第1页1 2 3