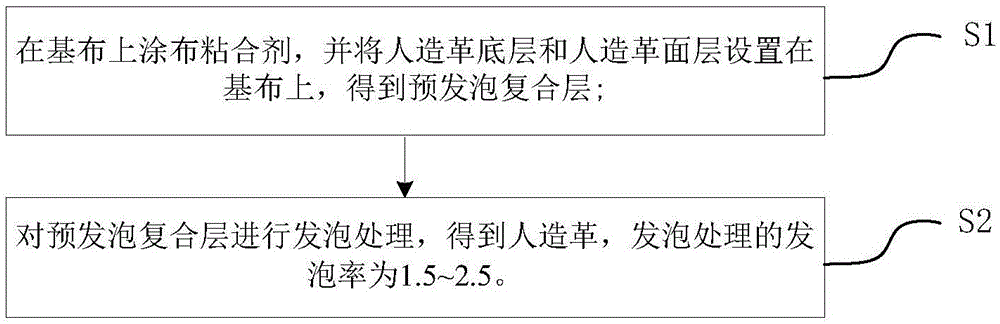
本发明涉及材料
技术领域:
,具体而言,涉及一种人造革及人造革的制备方法。
背景技术:
:皮革在包括汽车工业在内的多种领域中用作内部材料,皮革通常包括天然皮革和人造革,其中,人造革由于造价相比天然皮革便宜且容易批量生产,因此,目前广泛应用于汽车工业等领域中。人造革的制备工艺中通常先制备出面层和底层,然后在基布上涂布PVC等粘合剂浆料,然后先压延成型出底层,在底层薄膜从压延辊轮引取出来的同时趁热熔状态贴合到底布上,然后以同样的方法将压延成型的面层薄膜进行贴合,最后对底层和面层贴合后的产物进行发泡处理以得到人造革。然而,上述人造革在所需的厚度较小的情况下,在实际生产中容易使形成的人造革存在表面透浆的问题,表面透浆是指对人造革表面进行上色的油墨从人造革表面渗透至人造革最底层的基布中的情况,从而达不到客户的要求。技术实现要素:本发明的主要目的在于提供一种人造革及人造革的制备方法,以解决现有技术中人造革较薄时由于存在表面透浆,而影响人造革表面的美观的问题。为了实现上述目的,根据本发明的一个方面,提供了一种人造革的制备方法,制备方法包括以下步骤:S1,在基布上涂布粘合剂,并将人造革底层和人造革面层设置在基布上,得到预发泡复合层;S2,对预发泡复合层进行发泡处理,得到人造革,发泡处理的发泡率为1.5~2.5。进一步地,发泡处理的发泡率为1.6~2.1。进一步地,人造革底层的厚度为0.13~0.21mm。进一步地,在步骤S1的步骤之前,制备方法还包括以下步骤:利用包括聚氯乙烯树脂、增塑剂和发泡剂的第一原料制备得到人造革底层,优选第一原料还包括钙粉。进一步地,第一原料中聚氯乙烯树脂的重量份为100,增塑剂的重量份为40~120,发泡剂的重量份为3~7,优选增塑剂包括邻苯二甲酸二辛酯和大豆油,邻苯二甲酸二辛酯的重量份为30~80,大豆油的重量份为10~40。进一步地,第一原料还包括液体钡锌稳定剂、粉体钡锌稳定剂、发泡稳定剂、硬脂酸和丙烯酸酯中的任一种或多种,优选第一原料中液体钡锌稳定剂的重量份为0.6~3,优选粉体钡锌稳定剂的重量份为1.0~4,优选发泡稳定剂的重量份为0.2~2.5,优选硬脂酸的重量份为0.2~1.5,优选丙烯酸酯的重量份为0.3~1.5。进一步地,在步骤S1的步骤之前,制备方法还包括以下步骤:利用包括聚氯乙烯树脂和增塑剂的第二原料制备得到人造革面层,优选第二原料还包括钙粉。进一步地,第二原料中聚氯乙烯树脂的重量份为100,增塑剂的重量份为40~100,优选增塑剂包括邻苯二甲酸二辛酯和大豆油,邻苯二甲酸二辛酯的重量份为25~80,大豆油的重量份为2~20,优选第二原料还包括液体钡锌稳定剂,更优选第二原料中液体钡锌稳定剂的重量份为1.5-4.5。进一步地,人造革的厚度小于0.85mm。根据本发明的另一方面,提供了一种人造革,人造革采用上述的人造革的制备方法制备而成。应用本发明的技术方案,提供了一种人造革的制备方法,由于该方法的发泡处理的发泡率为1.5~2.5,与现有技术相比降低了约10~30%,通过降低发泡率,提高了人造革中PVC的体积比,从而在利用油墨对人造革表面进行上色时,位于表层的油墨在人造革中由上至下进行渗透,被更多地留在PVC中,进而降低了油墨渗透至人造革中底布上的概率,有效地改善了制备出的人造革较薄时表面透浆的问题。除了上面所描述的目的、特征和优点之外,本发明还有其它的目的、特征和优点。下面将参照图,对本发明作进一步详细的说明。附图说明构成本发明的一部分的说明书附图用来提供对本发明的进一步理解,本发明的示意性实施例及其说明用于解释本发明,并不构成对本发明的不当限定。在附图中:图1示出了本发明实施方式所提供的人造革的制备方法的流程示意图。具体实施方式需要说明的是,在不冲突的情况下,本发明中的实施例及实施例中的特征可以相互组合。下面将参考附图并结合实施例来详细说明本发明。为了使本
技术领域:
的人员更好地理解本发明方案,下面将结合本发明实施例中的附图,对本发明实施例中的技术方案进行清楚、完整地描述,显然,所描述的实施例仅仅是本发明一部分的实施例,而不是全部的实施例。基于本发明中的实施例,本领域普通技术人员在没有做出创造性劳动前提下所获得的所有其他实施例,都应当属于本发明保护的范围。需要说明的是,本发明的说明书和权利要求书及上述附图中的术语“第一”、“第二”等是用于区别类似的对象,而不必用于描述特定的顺序或先后次序。应该理解这样使用的数据在适当情况下可以互换,以便这里描述的本发明的实施例。此外,术语“包括”和“具有”以及他们的任何变形,意图在于覆盖不排他的包含,例如,包含了一系列步骤或单元的过程、方法、系统、产品或设备不必限于清楚地列出的那些步骤或单元,而是可包括没有清楚地列出的或对于这些过程、方法、产品或设备固有的其它步骤或单元。正如
背景技术:
中所介绍的,现有技术中所需厚度较小的人造革在实际生产中容易使形成的人造革存在表面透浆的问题,从而达不到客户的要求。本申请的发明人针对上述问题进行研究,提出了一种人造革的制备方法,如图1所示,制备方法包括以下步骤:在基布上涂布粘合剂,并将人造革底层和人造革面层设置在基布上,得到预发泡复合层;对预发泡复合层进行发泡处理,得到人造革,发泡处理的发泡率为1.5~2.5。本发明的上述人造革的制备方法中由于发泡处理的发泡率为1.5~2.5,与现有技术相比降低了约10~30%,通过降低发泡率,提高了人造革中PVC的体积比,从而在利用油墨对人造革表面进行上色时,位于表层的油墨在人造革中由上至下进行渗透,被更多地留在PVC中,进而降低了油墨渗透至人造革中底布上的概率,有效地改善了制备出的人造革较薄时表面透浆的问题。下面将更详细地描述根据本发明提供的人造革的制备方法的示例性实施方式。然而,这些示例性实施方式可以由多种不同的形式来实施,并且不应当被解释为只限于这里所阐述的实施方式。应当理解的是,提供这些实施方式是为了使得本申请的公开彻底且完整,并且将这些示例性实施方式的构思充分传达给本领域普通技术人员。首先,执行步骤S1:在基布上涂布粘合剂,并将人造革底层和人造革面层设置在基布上,得到预发泡复合层。在上述步骤S1中,可以通过将人造革底层和人造革面层依次置于基布上并进行压延成型,以得到预发泡复合层。本领域技术人员可以根据现有技术对压延成型的工艺条件进行设定。在上述步骤S1中,本领域技术人员可以根据现有技术对基布的种类进行选取;并且,通过在基布上涂布粘合剂能够增加基布与人造革底层之间的粘附力,进而使所制备的人造革产品具有较高的底层剥离强度,本领域技术人员也可以根据现有技术对上述粘合剂的种类进行合理选择,优选地,粘合剂为PVC糊树脂。上述优选种类的粘合剂由于具有优秀的粘合性能,从而能够有效地增强底层与基布之间的粘合力。本领域技术人员可以根据现有技术对上述人造革面层的厚度进行合理选取,人造革面层的厚度可以为0.08~0.1mm;而为了更为有效地解决所需人造革厚度较小时表面透浆的问题,优选地,人造革底层的厚度为0.13~0.21mm。此时,本申请中的人造革面层仍可以具有与现有技术中的人造革面层相同的厚度,与现有技术中的人造革底层的厚度相比,本申请中的人造革底层的厚度范围加厚了10~20%,由于发泡率的降低会影响人造革的厚度,从而通过仅增加了人造革底层的厚度,有效地保持了人造革整体厚度的要求;并且,采用上述制备方法通过合理选取面层的厚度,从而在发泡工艺后仍可以得到厚度小于0.85mm的人造革,从而满足客户对人造革厚度的要求。在一种优选的实施方式中,在步骤S1的步骤之前,制备方法还包括以下步骤:利用包括聚氯乙烯树脂(PVC树脂)、增塑剂和发泡剂的第一原料制备得到人造革底层。可以采用现有技术中常规的制备工艺制备得到上述人造革底层,在上述制备工艺中通过将PVC树脂、发泡剂与增塑剂等原料混合均匀,以使增塑剂发挥应有的效果。本申请的上述第一原料中,发泡剂可以采用现有人造革制品中常用的材料,本申请中并未做特殊限定。为了实现更好的发泡效果,优选地,上述发泡剂选自偶氮二甲酰胺(即AC发泡剂)和/或偶氮甲酰胺甲酸钾。上述优选种类的发泡剂不仅能够满足不同发泡倍率的需求,而且具有较低的成本,从而适合工艺批量生产的需求。上述第一原料中各组分的含量可以根据实际需求进行选取,为了提高人造革底层的性能,优选地,第一原料中聚氯乙烯树脂的重量份为100,增塑剂的重量份为40~120,发泡剂的重量份为3~7;更为优选地,上述增塑剂包括邻苯二甲酸二辛酯和大豆油,邻苯二甲酸二辛酯的重量份为30~80,大豆油的重量份为10~40。第一原料还可以包括钙粉,由于钙粉价格低廉,从而有效地降低了人造革底层的制备成本;优选地,第一原料中钙粉的重量份为40~130。在上述包括聚氯乙烯树脂、增塑剂、发泡剂和钙粉的第一原料中,第一原料还可以包括液体钡锌稳定剂、粉体钡锌稳定剂、发泡稳定剂(即气泡调整剂)、硬脂酸和丙烯酸酯中的任一种或多种,其中,硬脂酸和丙烯酸酯均为润滑剂。上述第一原料中各助剂的含量可以根据实际需求进行选取,为了进一步提高人造革底层的性能,优选地,第一原料中液体钡锌稳定剂的重量份为0.6~3,粉体钡锌稳定剂的重量份为1.0~4,发泡稳定剂的重量份为0.2~2.5,硬脂酸的重量份为0.2~1.5,且丙烯酸酯的重量份为0.3~1.5。在一种优选的实施方式中,在步骤S1的步骤之前,制备方法还包括以下步骤:利用包括聚氯乙烯树脂(PVC树脂)和增塑剂的第二原料制备得到人造革面层。本领域技术人员可以采用现有技术中常规的制备工艺制备得到上述人造革面层,在上述制备工艺中通过将PVC树脂与增塑剂等原料混合均匀,以使增塑剂发挥应有的效果;并且,本领域技术人员可以根据实际需求对上述第二原料中各组分的含量进行合理选取,并且,根据各种不同人造革产品的需求。上述第二原料中各组分的含量可以根据实际需求进行选取,为了提高人造革面层的性能,优选地,第二原料中聚氯乙烯树脂的重量份为100,增塑剂的重量份为40~100;更为优选地,上述增塑剂包括邻苯二甲酸二辛酯和大豆油,邻苯二甲酸二辛酯的重量份为25~80,大豆油的重量份为2~20。第二原料也可以包括钙粉。由于钙粉价格低廉,从而有效地降低了人造革面层的制备成本;优选地,第二原料中钙粉的重量份为5~40。在上述包括聚氯乙烯树脂、增塑剂和钙粉的第二原料中,第二原料还可以包括液体钡锌稳定剂,上述第二原料中助剂的含量可以根据实际需求进行选取,为了进一步提高人造革面层的性能,优选地,第二原料中液体钡锌稳定剂的重量份为1.5-4.5。在完成上述步骤S1之后,执行步骤S2对预发泡复合层进行发泡处理,得到人造革,发泡处理的发泡率为1.5~2.5。通过上述发泡处理得到的人造革不仅具有柔顺性高及手感好的效果,而且有效地解决了人造革表面透浆的问题,能够具有较高的美观度。为了在有效解决人造革表面透浆问题的基础上降低人造革的制备成本,优选地,上述发泡处理的发泡率为1.6~2.1。本领域技术人员也可以根据现有技术对上述发泡处理的工艺条件进行合理选取。根据本申请的另一个方面,还提供了一种由人造革的制备方法制备而成的人造革。该人造革的制备方法中由于发泡处理的发泡率为1.5~2.5,与现有技术相比降低了约20~30%,从而通过降低发泡率使制备出的人造革表面不易透浆。下面将结合实施例进一步说明本发明提供的人造革及其制备方法。实施例1本实施例提供的人造革的制备方法包括以下步骤:利用100重量份的聚氯乙烯树脂、35重量份的增塑剂、和10重量份的发泡剂制备得到厚度为0.2mm的人造革底层,其中,增塑剂包括邻苯二甲酸二辛酯和大豆油,邻苯二甲酸二辛酯的重量份为25,大豆油的重量份为10,发泡剂为偶氮二甲酰胺;利用100重量份的聚氯乙烯树脂和35重量份的增塑剂制备人造革面层,其中,增塑剂包括邻苯二甲酸二辛酯和大豆油,邻苯二甲酸二辛酯的重量份为25,大豆油的重量份为10;在基布上涂布PVC浆作为粘合剂,并将上述人造革底层和上述人造革面层设置在基布上,得到预发泡复合层;对预发泡复合层进行发泡处理,得到人造革,发泡处理的发泡率为1.5。实施例2本实施例提供的人造革与实施例1的区别在于:利用100重量份的聚氯乙烯树脂、30重量份的邻苯二甲酸二辛酯、10重量份的大豆油和3重量份的发泡剂制备得到厚度为0.13mm的人造革底层,利用100重量份的聚氯乙烯树脂、38重量份的邻苯二甲酸二辛酯和2重量份的大豆油制备人造革面层,且发泡处理的发泡率为2.5。实施例3本实施例提供的人造革与实施例1的区别在于:利用100重量份的聚氯乙烯树脂、80重量份的邻苯二甲酸二辛酯、40重量份的大豆油和7重量份的发泡剂制备得到厚度为0.21mm的人造革底层,利用100重量份的聚氯乙烯树脂、25重量份的邻苯二甲酸二辛酯和5重量份的大豆油制备人造革面层,且发泡处理的发泡率为1.6。实施例4本实施例提供的人造革与实施例3的区别在于:利用100重量份的聚氯乙烯树脂、50重量份的邻苯二甲酸二辛酯、20重量份的大豆油、5重量份的发泡剂、0.5重量份的液体钡锌稳定剂(型号为BZ-105P)、重量份为0.1的发泡稳定剂(型号为BF-539A)和重量份为0.2的硬脂酸制备得到厚度为0.178mm的人造革底层,且发泡处理的发泡率为2.1。实施例5本实施例提供的人造革与实施例4的区别在于:液体钡锌稳定剂的重量份为0.6、发泡稳定剂的重量份为0.2,硬脂酸的重量份为0.3。实施例6本实施例提供的人造革与实施例4的区别在于:液体钡锌稳定剂的重量份为3、发泡稳定剂的重量份为2.5,硬脂酸的重量份为1.5。实施例7本实施例提供的人造革与实施例3的区别在于:利用100重量份的聚氯乙烯树脂、80重量份的邻苯二甲酸二辛酯、20重量份的大豆油和1重量份的液体钡锌稳定剂(型号为BZ-105P)制备人造革面层。实施例8本实施例提供的人造革与实施例7的区别在于:液体钡锌稳定剂的重量份为1.5。实施例9本实施例提供的人造革与实施例7的区别在于:液体钡锌稳定剂的重量份为4.5。实施例10本实施例提供的人造革与实施例3的区别在于:利用100重量份的聚氯乙烯树脂、60重量份的邻苯二甲酸二辛酯、40重量份的大豆油、5重量份的发泡剂、2重量份的液体钡锌稳定剂(型号为BZ-105P)、重量份为1.5的发泡稳定剂(型号为BF-539A)和重量份为1的硬脂酸制备得到厚度为0.19mm的人造革底层,且发泡处理的发泡率为1.8;利用100重量份的聚氯乙烯树脂、60重量份的邻苯二甲酸二辛酯、10重量份的大豆油和3重量份的液体钡锌稳定剂(型号为BZ-105P)制备人造革面层。对比例1本对比例提供的人造革与实施例1的区别在于:发泡处理的发泡率为2.55。在上述实施例1至10和对比例中人造革的表面上涂布深色油墨,并观察人造革的底部表面,以判断人造革是否透浆,从测试结果可以看出,实施例1至10中的人造革没有透浆现象发生,而对比例1中的人造革出现透浆现象。并且,对上述各实施例和对比例所制备的人造革的力学性能(拉伸负荷、撕裂负荷、涨破强度、剥离负荷)、耐老化性能和色牢度进行检测,测试结果如下表所示:性能拉伸负荷撕裂负荷涨破强度剥离负荷色牢度单位NNMPaN级实施例1354161.1214-5实施例2588301.8254-5实施例3503201.3224-5实施例4536221.5234-5实施例5534241.5234-5实施例6541271.6234-5实施例7359171.2214-5实施例8355161.1214-5实施例9361171.2214-5实施例10608321.9254-5从上述测试结果可以看出,本申请实施例1至10中的人造革均能够具有优异的抗拉伸强度等力学性能和色牢度较高;并且,相比于实施例1中的人造革,实施例2至10中的人造革能够具有更好的力学性能。从以上的描述中,可以看出,本发明上述的实施例实现了如下技术效果:1、通过降低发泡率有效地解决了制备出的人造革表面透浆的问题,进而提高了人造革表面的美观度;2、通过增加了人造革底层的厚度,更为有效地解决了制备出的人造革表面透浆的问题,进而进一步提高了人造革表面的美观度。以上所述仅为本发明的优选实施例而已,并不用于限制本发明,对于本领域的技术人员来说,本发明可以有各种更改和变化。凡在本发明的精神和原则之内,所作的任何修改、等同替换、改进等,均应包含在本发明的保护范围之内。当前第1页1 2 3