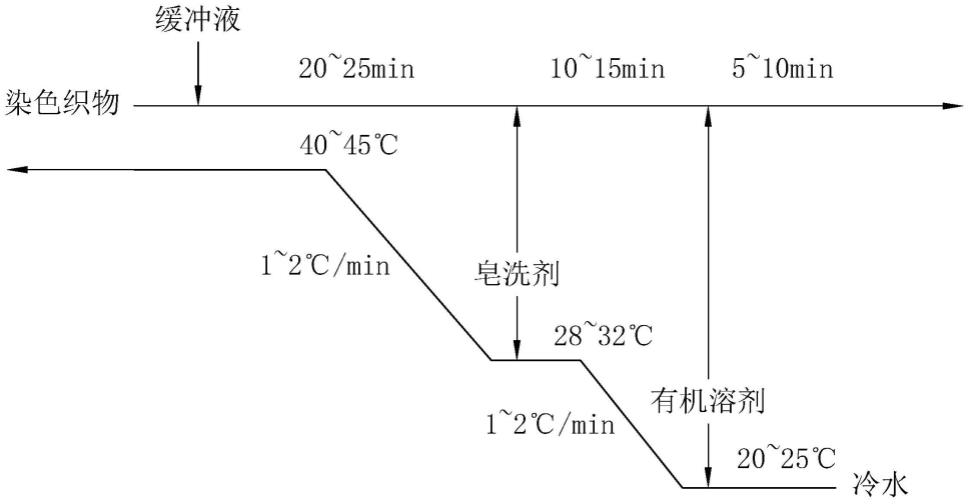
1.本发明涉及染整的技术领域,尤其是涉及一种活性染料防沾色低温洗涤方法。
背景技术:2.活性染料又称反应染料,其分子中含有能与纤维中的羟基和蛋白质纤维中氨基发生反应的活性基团,染色时与纤维生成共价键,生成“染料-纤维”化合物。又由于活性染料具有颜色鲜艳、均染性好、染色渐变、色谱齐全和成本较低的特点,因而广泛应用于含羟基、氨基或亚氨基的纤维(如纤维素纤维、蛋白质纤维、尼龙纤维等)、纱线或织物的染色或印花工艺中,以获得较好的染色牢度。
3.现有的活性染料在印染过程中,并不能完全和纤维反应,其利用率在70%左右。同时,纤维、纱线或者织物上会存在一些未参与反应的染料以及水解染料,这些未参与反应的染料需要通过洗涤去除,否则严重影响产品的水洗色牢度和摩擦色牢度。另外,这些未反应的染料还会继续与浅色或白底织物反应染色,造成沾色。因此,在经过活性染料染色后,通过洗涤来提高产品的色牢度、从织物上去除水解染料方面起着重要的作用。
4.目前,染色织物的洗涤工艺包括热水洗、冷水洗、皂洗剂皂洗、再经过冷水洗。其需要在95~105℃进行多次皂洗和热水洗,以去除染色织物表面的浮色,且洗涤过程需要耗用大量水和热能,并且导致排污量和污染符合增加,生产成本提高。此外,目前工业中所用皂洗剂主要是表面活性剂及其复配物组成的化学皂洗剂、从而进一步增加了废水处理的负担,直接影响染色的节能减排和环保性。
5.因此,现亟需对经过活性染料染色后的染色织物的洗涤方法进行改进,以在去除染色织物表面的浮色、提高水洗色牢度和摩擦色牢度的同时,能降低洗涤过程的水和热能等资源的耗用和处理负担,实现节能减排和环保的目的。
技术实现要素:6.本发明要解决的问题是针对现有技术中所存在的上述不足而提供一种活性染料防沾色低温洗涤方法,其保证染色织物色牢度、防沾色性能的同时,达到了节能减排的目的。
7.本发明的上述发明目的是通过以下技术方案得以实现的:一种活性染料防沾色低温洗涤方法,所述方法包括,沿着冷水的流动路径依次配置水洗区段、混合洗区段和皂洗区段的过程;在所述混合洗区段靠近水洗区段的一端连续投入有机溶剂的过程,并控制所述有机溶剂的体积浓度为20~30%;在所述皂洗区段靠近混合洗区段的一端连续投入皂洗剂的过程,并控制所述皂洗剂的浓度为0.10~1.00g/l;其中,所述皂洗剂由以下重量百分比的原料制成,枯草菌脂肽钠20~40%,葡糖氧化酶20~40%,氢化溶血卵磷脂20~40%,多功能助剂10~20%;以及,将染色织物依次经过皂洗区段、混合洗区段和水洗区段洗涤的过程。
8.通过采用上述技术方案,洗涤时,水流方向和染色织物的输送方向相反,并且在冷水的流动路径上依次补充有机溶剂和皂洗剂,能在实现染色织物皂洗、混合洗和水洗的同时,大大减少水和热能等资源的耗用和处理负担,实现节能减排和环保的目的;在染色织物经过皂洗区段时,枯草菌脂肽钠作为主要皂洗成分,是经过生物发酵而获得的,其在混合液中的浓度约为0.02~0.40g/l,枯草菌脂肽钠通过降低表面张力,渗透于浮色和植物纤维之间,即使在碱性环境下,也能有效去除染色织物表面肤色并提高湿摩擦牢度,同时,氢化溶血卵磷脂能与枯草菌脂肽钠形成复配体系,提高了在酸性条件下皂洗剂的乳化稳定性,实现对降低表面张力及其效率的增效,此外,葡糖氧化酶能与上述复配体系进一步复配,不仅能提高皂洗区段混合液的抗氧化性能,充分带走浮色,防止浮色与织物纤维再结合,还能降低洗涤后混合液的处理负担,最后通过多功能助剂促进这些组分分散、乳化和增溶,以获得较高的洗涤效率和洗涤效果;在染色织物经过皂洗区段和混合洗区段时,通过有机溶剂和水的组合,不仅能促进浮色溶出,降低水资源的好用,还能将洗涤温度从95~105℃降低至40~45℃,最后通过冷水洗涤1次即可,达到了节能减排和环保的目的;在此过程中,通过反向输送染色织物和冷水,并在冷水的流动路径上依次补充有机溶剂和皂洗剂,能充分去除浮色,在保证染色织物色牢度、防沾色性能的同时,大大减少水和热能等资源的耗用和处理负担,达到了节能减排的目的。
9.进一步地,所述有机溶剂为甲醇、乙醇、丙醇、异丙醇、丁醇、丙酮、丁酮、甲基异丁基酮、乙腈和n,n-二甲基甲酰胺中的一种或几种的组合物。
10.进一步地,所述多功能助剂为羧甲基玉米淀粉钠,所述枯草菌脂肽钠、葡糖氧化酶和氢化溶血卵磷脂的质量比为1.00:(0.05~1.50):(1.00~2.00)。
11.或者,所述多功能助剂为聚乙烯吡咯烷酮,所述枯草菌脂肽钠、葡糖氧化酶和氢化溶血卵磷脂的质量比为1.00:(1.00~2.00):(0.05~1.50)。
12.进一步地,在所述水洗区段中,控制进水温度为20~25℃,洗涤时间为5~10min,浴比为1:(40~60)。
13.进一步地,在所述混合洗区段中,在有机溶剂投入0~2min后,将有机溶剂和水的混合液按照1~2℃/min的速度升温,并控制出液温度为28~32℃,洗涤时间为10~15min,浴比为1:(10~20)。
14.更进一步地,在所述混合洗区段中,控制有机溶剂投料口与液面距离为5~50cm。
15.进一步地,在所述皂洗区段中,在皂洗剂投入0~2min后,将皂洗剂、有机溶剂和水的混合液按照1~2℃/min的速度升温,并控制出液温度为40~45℃,洗涤时间为20~25min,浴比为1:(10~20)。
16.更进一步地,在所述皂洗区段中,控制皂洗剂投料口与液面距离为5~50cm。
17.进一步地,所述方法还包括预先在染色织物两侧表面雾化喷淋缓冲液的过程,并控制所述缓冲液的雾化粒径为100~200μm,喷淋量为0.4~0.6l/
㎡
;其中,所述缓冲液包括0.30~0.50g/l的冰醋酸和0.10~0.25g/l的醋酸钠。
18.综上所述,本发明的有益技术效果为:通过反向输送染色织物和冷水,并在冷水的流动路径上依次补充有机溶剂和皂洗剂,能充分去除浮色,在保证染色织物色牢度、防沾色性能的同时,大大减少水和热能等资源的耗用和处理负担,达到了节能减排的目的。
附图说明
19.图1是本发明提供的方法的流程图;图2是实现本发明的方法的洗涤系统结构图;图中,1、雾化喷淋装置;2、皂洗槽;21、出液口;22、皂洗剂投料口;3、混合洗槽;31、有机溶剂投料口;4、水洗槽;41、进水口;5、辊筒组;6、加热元件。
具体实施方式
20.为了使本发明实现的技术手段、创作特征、达成目的与作用更加清楚及易于了解,下面结合附图和具体实施方式对本发明作进一步阐述。
21.实施例1:为本发明公开的一种活性染料防沾色低温洗涤方法,其包括,a)沿着冷水的流动路径依次配置水洗区段、混合洗区段和皂洗区段的过程;b)在混合洗区段靠近水洗区段的一端连续投入有机溶剂的过程;c)在皂洗区段靠近混合洗区段的一端连续投入皂洗剂的过程;d)预先在染色织物两侧表面雾化喷淋缓冲液的过程;e)将染色织物依次经过皂洗区段、混合洗区段和水洗区段洗涤的过程。
22.参照图1和图2,本发明方法的具体实现方式为,s1配置洗涤系统洗涤系统包括沿染色织物输送路方向顺次连接的雾化喷淋装置1、用于形成皂洗区段的皂洗槽2、用于形成混合洗区段的混合洗槽3、用于形成水洗区段的水洗槽4、以及用于供染色织物绕设的辊筒组5;其中,雾化喷淋装置1(市购)按照喷淋口朝向染色织物两侧表面的方式安装在皂洗槽2上,皂洗槽2远离混合洗槽3的一端设置有出液口21,皂洗槽2靠近混合洗槽3的一端设置有皂洗剂投料口22,混合洗槽3靠近水洗槽4的一端设置有有机溶剂投料口31,水洗槽4远离混合洗槽3的一端设置有进水口41,辊筒组5布置于皂洗槽2、混合洗槽3和水洗槽4内;s2配置缓冲剂、皂洗剂和有机溶剂s21缓冲液由冰醋酸、醋酸钠和水混合而成,冰醋酸的浓度为0.40g/l,醋酸钠的浓度为0.20g/l;s22皂洗剂由以下重量份的原料混合而成,枯草菌脂肽钠30.00份,葡糖氧化酶30.00份,氢化溶血卵磷脂36.00份,多功能助剂4.00份;其中,多功能助剂为羧甲基玉米淀粉钠;s23有机溶剂为乙醇;s3配置洗涤液s31将22℃的冷水自进水口41连续投入至水洗区段内,且冷水依次流动经过水洗区段、混合洗区段和皂洗区段;s32将有机溶剂自有机溶剂投料口31连续投入至混合洗区段内,并控制有机溶剂的体积浓度为25%,有机溶剂投料口31与液面距离为5~50cm;在有机溶剂随水流输送并混合0~2min后,混合洗槽3内布置的加热元件6将有机溶剂和水的混合液按照1℃/min的速度升温,并控制出液温度为30℃;s33将皂洗剂自皂洗剂投料口22连续投入至皂洗区段内,并控制皂洗剂的浓度为
0.50g/l,皂洗剂投料口22与液面距离为5~50cm;在皂洗剂随水流输送并混合0~2min后,皂洗槽2内布置的加热元件6将皂洗剂、有机溶剂和水的混合液按照2℃/min的速度升温,并控制出液温度为42℃;s34皂洗剂、有机溶剂和水的混合液自出液口21输出;s4染色织物洗涤s41预先将染色织物绕设于辊筒组5上,布置在洗涤系统上和/或下游的牵引设备(图中未示出)可将染色织物依次输送经过雾化喷淋装置1、皂洗区段、混合洗区段和水洗区段;s42在染色织物经过雾化喷淋装置1时,雾化喷淋装置1在染色织物两侧表面雾化喷淋缓冲液,并控制缓冲液的雾化粒径为200μm,喷淋量为0.5l/
㎡
;s43在皂洗区段中,染色织物浸没于皂洗剂、有机溶剂和水的混合液中,控制染色织物的洗涤时间为22min,浴比为1:15;s44在混合洗区段中,染色织物浸没于有机溶剂和水的混合液中,控制染色织物的洗涤时间为12min,浴比为1:15;s45在水洗区段中,染色织物浸没于冷水中,控制染色织物的洗涤时间为7min,浴比为1:50;s46洗涤后的染色织物经过挤压脱水,出料。
23.测定洗涤后的皂洗剂、有机溶剂和水的混合液的吸光度,再根据活性染料的标准曲线,计算得混合液中染料的浓度为17mg/l。
24.测定洗涤后的染色织物的皂洗色牢度和摩擦色牢度,其中,原样褪色为5级,白布沾色为5级,干态摩擦为5级,湿态摩擦为5级。
25.实施例2:为本发明公开的一种活性染料防沾色低温洗涤方法,与实施例的不同之处在于,s2和s3的具体实现方式如下,s2配置缓冲剂、皂洗剂和有机溶剂s21缓冲液由冰醋酸、醋酸钠和水混合而成,冰醋酸的浓度为0.35g/l,醋酸钠的浓度为0.15g/l;s22皂洗剂由以下重量份的原料混合而成,枯草菌脂肽钠25.00份,葡糖氧化酶37.50份,氢化溶血卵磷脂25.00份,多功能助剂12.50份;其中,多功能助剂为聚乙烯吡咯烷酮;s23有机溶剂为丙酮;s3配置洗涤液s31将20℃的冷水自进水口41连续投入至水洗区段内,且冷水依次流动经过水洗区段、混合洗区段和皂洗区段;s32将有机溶剂自有机溶剂投料口31连续投入至混合洗区段内,并控制有机溶剂的体积浓度为28%,有机溶剂投料口31与液面距离为5~50cm;在有机溶剂随水流输送并混合0~2min后,混合洗槽3内布置的加热元件6将有机溶剂和水的混合液按照2℃/min的速度升温,并控制出液温度为32℃;s33将皂洗剂自皂洗剂投料口22连续投入至皂洗区段内,并控制皂洗剂的浓度为0.10g/l,皂洗剂投料口22与液面距离为5~50cm;在皂洗剂随水流输送并混合0~2min后,皂
洗槽2内布置的加热元件6将皂洗剂、有机溶剂和水的混合液按照1℃/min的速度升温,并控制出液温度为40℃;s34皂洗剂、有机溶剂和水的混合液自出液口21输出;s4染色织物洗涤s41预先将染色织物绕设于辊筒组5上,布置在洗涤系统上和/或下游的牵引设备(图中未示出)可将染色织物依次输送经过雾化喷淋装置1、皂洗区段、混合洗区段和水洗区段;s42在染色织物经过雾化喷淋装置1时,雾化喷淋装置1在染色织物两侧表面雾化喷淋缓冲液,并控制缓冲液的雾化粒径为100μm,喷淋量为0.4~0.6l/
㎡
;s43在皂洗区段中,染色织物浸没于皂洗剂、有机溶剂和水的混合液中,控制染色织物的洗涤时间为25min,浴比为1:20;s44在混合洗区段中,染色织物浸没于有机溶剂和水的混合液中,控制染色织物的洗涤时间为15min,浴比为1:20;s45在水洗区段中,染色织物浸没于冷水中,控制染色织物的洗涤时间为8min,浴比为1:60;s46洗涤后的染色织物经过挤压脱水,出料。
26.测定洗涤后的皂洗剂、有机溶剂和水的混合液的吸光度,再根据活性染料的标准曲线,计算得混合液中染料的浓度为15mg/l。
27.测定洗涤后的染色织物的皂洗色牢度和摩擦色牢度,其中,原样褪色为5级,白布沾色为5级,干态摩擦为4~5级,湿态摩擦为4~5级。
28.实施例3:为本发明公开的一种活性染料防沾色低温洗涤方法,与实施例的不同之处在于,s2和s3的具体实现方式如下,s2配置缓冲剂、皂洗剂和有机溶剂s21缓冲液由冰醋酸、醋酸钠和水混合而成,冰醋酸的浓度为0.50g/l,醋酸钠的浓度为0.25g/l;s22皂洗剂由以下重量份的原料混合而成,枯草菌脂肽钠40.00份,葡糖氧化酶2.00份,氢化溶血卵磷脂40.00份,多功能助剂18.00份;其中,多功能助剂为羧甲基玉米淀粉钠;s23有机溶剂为n,n-二甲基甲酰胺;s3配置洗涤液s31将25℃的冷水自进水口41连续投入至水洗区段内,且冷水依次流动经过水洗区段、混合洗区段和皂洗区段;s32将有机溶剂自有机溶剂投料口31连续投入至混合洗区段内,并控制有机溶剂的体积浓度为20%,有机溶剂投料口31与液面距离为5~50cm;在有机溶剂随水流输送并混合0~2min后,混合洗槽3内布置的加热元件6将有机溶剂和水的混合液按照1℃/min的速度升温,并控制出液温度为28℃;s33将皂洗剂自皂洗剂投料口22连续投入至皂洗区段内,并控制皂洗剂的浓度为1.00g/l,皂洗剂投料口22与液面距离为5~50cm;在皂洗剂随水流输送并混合0~2min后,皂洗槽2内布置的加热元件6将皂洗剂、有机溶剂和水的混合液按照2℃/min的速度升温,并控
制出液温度为45℃;s34皂洗剂、有机溶剂和水的混合液自出液口21输出;s4染色织物洗涤s41预先将染色织物绕设于辊筒组5上,布置在洗涤系统上和/或下游的牵引设备(图中未示出)可将染色织物依次输送经过雾化喷淋装置1、皂洗区段、混合洗区段和水洗区段;s42在染色织物经过雾化喷淋装置1时,雾化喷淋装置1在染色织物两侧表面雾化喷淋缓冲液,并控制缓冲液的雾化粒径为200μm,喷淋量为0.6l/
㎡
;s43在皂洗区段中,染色织物浸没于皂洗剂、有机溶剂和水的混合液中,控制染色织物的洗涤时间为20min,浴比为1:18;s44在混合洗区段中,染色织物浸没于有机溶剂和水的混合液中,控制染色织物的洗涤时间为13min,浴比为1:18;s45在水洗区段中,染色织物浸没于冷水中,控制染色织物的洗涤时间为5min,浴比为1:55;s46洗涤后的染色织物经过挤压脱水,出料。
29.测定洗涤后的皂洗剂、有机溶剂和水的混合液的吸光度,再根据活性染料的标准曲线,计算得混合液中染料的浓度为20mg/l。
30.测定洗涤后的染色织物的皂洗色牢度和摩擦色牢度,其中,原样褪色为5级,白布沾色为5级,干态摩擦为5级,湿态摩擦为5级。
31.实施例4:为本发明公开的一种活性染料防沾色低温洗涤方法,与实施例的不同之处在于,s2和s3的具体实现方式如下,s2配置缓冲剂、皂洗剂和有机溶剂s21缓冲液由冰醋酸、醋酸钠和水混合而成,冰醋酸的浓度为0.30g/l,醋酸钠的浓度为0.10g/l;s22皂洗剂由以下重量份的原料混合而成,枯草菌脂肽钠35.00份,葡糖氧化酶42.00份,氢化溶血卵磷脂3.15份,多功能助剂19.85份;其中,多功能助剂为聚乙烯吡咯烷酮;s23有机溶剂为乙醇;s3配置洗涤液s31将25℃的冷水自进水口41连续投入至水洗区段内,且冷水依次流动经过水洗区段、混合洗区段和皂洗区段;s32将有机溶剂自有机溶剂投料口31连续投入至混合洗区段内,并控制有机溶剂的体积浓度为22%,有机溶剂投料口31与液面距离为5~50cm;在有机溶剂随水流输送并混合0~2min后,混合洗槽3内布置的加热元件6将有机溶剂和水的混合液按照2℃/min的速度升温,并控制出液温度为29℃;s33将皂洗剂自皂洗剂投料口22连续投入至皂洗区段内,并控制皂洗剂的浓度为0.80g/l,皂洗剂投料口22与液面距离为5~50cm;在皂洗剂随水流输送并混合0~2min后,皂洗槽2内布置的加热元件6将皂洗剂、有机溶剂和水的混合液按照1℃/min的速度升温,并控制出液温度为41℃;
s34皂洗剂、有机溶剂和水的混合液自出液口21输出;s4染色织物洗涤s41预先将染色织物绕设于辊筒组5上,布置在洗涤系统上和/或下游的牵引设备(图中未示出)可将染色织物依次输送经过雾化喷淋装置1、皂洗区段、混合洗区段和水洗区段;s42在染色织物经过雾化喷淋装置1时,雾化喷淋装置1在染色织物两侧表面雾化喷淋缓冲液,并控制缓冲液的雾化粒径为100μm,喷淋量为0.5l/
㎡
;s43在皂洗区段中,染色织物浸没于皂洗剂、有机溶剂和水的混合液中,控制染色织物的洗涤时间为21min,浴比为1:10;s44在混合洗区段中,染色织物浸没于有机溶剂和水的混合液中,控制染色织物的洗涤时间为10min,浴比为1:10;s45在水洗区段中,染色织物浸没于冷水中,控制染色织物的洗涤时间为10min,浴比为1:40;s46洗涤后的染色织物经过挤压脱水,出料。
32.测定洗涤后的皂洗剂、有机溶剂和水的混合液的吸光度,再根据活性染料的标准曲线,计算得混合液中染料的浓度为18mg/l。
33.测定洗涤后的染色织物的皂洗色牢度和摩擦色牢度,其中,原样褪色为5级,白布沾色为4~5级,干态摩擦为5级,湿态摩擦为5级。
34.实施例5:为本发明公开的一种活性染料防沾色低温洗涤方法,与实施例的不同之处在于,s2和s3的具体实现方式如下,s2配置缓冲剂、皂洗剂和有机溶剂s21缓冲液由冰醋酸、醋酸钠和水混合而成,冰醋酸的浓度为0.45g/l,醋酸钠的浓度为0.20g/l;s22皂洗剂由以下重量份的原料混合而成,枯草菌脂肽钠20.00份,葡糖氧化酶30.00份,氢化溶血卵磷脂40.00份,多功能助剂10.00份;其中,多功能助剂为羧甲基玉米淀粉钠;s23有机溶剂为丙酮;s3配置洗涤液s31将23℃的冷水自进水口41连续投入至水洗区段内,且冷水依次流动经过水洗区段、混合洗区段和皂洗区段;s32将有机溶剂自有机溶剂投料口31连续投入至混合洗区段内,并控制有机溶剂的体积浓度为30%,有机溶剂投料口31与液面距离为5~50cm;在有机溶剂随水流输送并混合0~2min后,混合洗槽3内布置的加热元件6将有机溶剂和水的混合液按照1℃/min的速度升温,并控制出液温度为31℃;s33将皂洗剂自皂洗剂投料口22连续投入至皂洗区段内,并控制皂洗剂的浓度为0.30g/l,皂洗剂投料口22与液面距离为5~50cm;在皂洗剂随水流输送并混合0~2min后,皂洗槽2内布置的加热元件6将皂洗剂、有机溶剂和水的混合液按照2℃/min的速度升温,并控制出液温度为43℃;s34皂洗剂、有机溶剂和水的混合液自出液口21输出;
s4染色织物洗涤s41预先将染色织物绕设于辊筒组5上,布置在洗涤系统上和/或下游的牵引设备(图中未示出)可将染色织物依次输送经过雾化喷淋装置1、皂洗区段、混合洗区段和水洗区段;s42在染色织物经过雾化喷淋装置1时,雾化喷淋装置1在染色织物两侧表面雾化喷淋缓冲液,并控制缓冲液的雾化粒径为200μm,喷淋量为0.5l/
㎡
;s43在皂洗区段中,染色织物浸没于皂洗剂、有机溶剂和水的混合液中,控制染色织物的洗涤时间为23min,浴比为1:12;s44在混合洗区段中,染色织物浸没于有机溶剂和水的混合液中,控制染色织物的洗涤时间为14min,浴比为1:12;s45在水洗区段中,染色织物浸没于冷水中,控制染色织物的洗涤时间为9min,浴比为1:45;s46洗涤后的染色织物经过挤压脱水,出料。
35.测定洗涤后的皂洗剂、有机溶剂和水的混合液的吸光度,再根据活性染料的标准曲线,计算得混合液中染料的浓度为16mg/l。
36.测定洗涤后的染色织物的皂洗色牢度和摩擦色牢度,其中,原样褪色为4~5级,白布沾色为5级,干态摩擦为5级,湿态摩擦为5级。
37.最后说明的是,以上实施例仅用以说明本发明的技术方案而非限制,尽管参照较佳实施例对本发明进行了详细说明,本领域的普通技术人员应当理解,可以对本发明的技术方案进行修改或者等同替换,而不脱离本发明技术方案的宗旨和范围,其均应涵盖在本发明的权利要求范围当中。