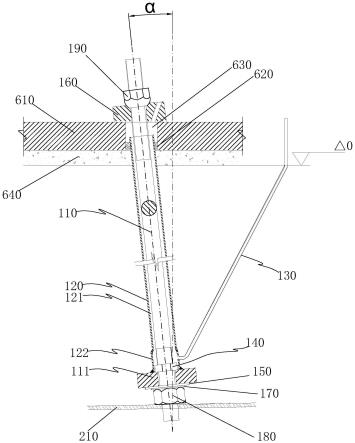
1.该发明涉及钢结构建筑施工技术领域,具体的来说是关于钢结构基础中的预应力长锚杆的施工安装方法。
背景技术:2.在房屋建筑领域,特别是钢结构建筑领域中,大量存在的钢立柱结构,钢立柱一般是竖向的设置的,其下端固定在钢混基础上,上端用于安装钢梁或者楼面结构,一般静态情况下,承受的为正向压力。所以,现有钢结构建筑中,钢立柱与钢混基础之间采用的为高强度预埋锚杆或者普通预埋锚杆进行机械连接的。
3.现有技术中的钢立柱和钢混基础之间的连接节点结构可以参考的结构如下:
4.cn217630845u公开一种钢立柱脚结构以及钢结构。钢立柱脚结构包括钢立柱、柱底板、多个加劲肋以及抗剪键,柱底板与钢立柱的底部固定连接,覆盖钢立柱的底部并向钢立柱的周侧超出钢立柱,以在钢立柱的周侧留有外挑边;加劲肋由外挑边的上表面向上延伸出,多个加劲肋沿钢立柱的周侧向外放射性分布,且各加劲肋与钢立柱固定连接;抗剪键由柱底板的下表面向下延伸出,用以伸入混凝土基础上开设的凹槽中;其中,柱底板用以与混凝土基础上下分隔设置,两者之间形成有间隙,间隙内填充有二次浇注的微膨胀细石混凝土层,外挑边开设有锚栓通孔,与预埋于混凝土基础中的锚栓配合,使柱底板与混凝土基础固定。该技术中,钢立柱就是出于90度竖直状态,属于常规钢立柱结构。
5.上述结构适用于钢立柱为竖直状态的常规情况。
6.在追求建筑个性化的今天,具有倾斜角度的钢立柱也产生了。本单位承接的某工程中,钢立柱具有竖向
±
5度的倾斜角度,且该钢立柱常规状态下承受正向压力。但是在地震等极端情况下要承受一定的拉应力,因此,钢立柱的受力要求较高。
7.不仅如此,通过力学有限元分析软件模拟可知,本结构设计中,钢立柱和钢混基础之间的锚杆或者锚杆连接存在失效的风险,这给本单位的施工带来了挑战。
技术实现要素:8.为了解决现有技术的不足,本发明提供一种建筑钢结构柱脚安装基础施工方法及节点,用于解决现有技术中对于带有倾斜角度的钢立柱柱脚施工存在的安装难、施工难,以及安装精度差的问题。
9.本发明解决其技术问题所采用的技术方案为:
10.建筑钢结构柱脚安装基础施工方法,其特征在于,
11.第一步,在计算机中放样出每根钢立柱安装节点中所有高强锚杆的精确位置和倾斜角度,并以每根钢立柱为单位模块利用计算机辅助设计绘制锚杆安装架和辅助支撑架图纸,根据图纸制作锚杆安装架和辅助支撑架;将锚杆安装架和辅助支撑架机械连接,并在锚杆安装架中按照设计要求装入高强锚杆组件,其中,所述高强锚杆组件由高强锚杆、六角螺母、球面螺母、保护导管、灌浆管、锁定螺母、石棉垫板和垫圈组成;
12.第二步,在筏板防水垫层施工阶段,根据外围轴线控制点及标高控制点测放出锚杆安装架每个预埋件的位置,安装预埋件后浇筑垫层混凝土,复测预埋件位置合格后混凝土养护至硬化;然后,将锚杆安装架及辅助支撑架整体吊装就位,待锚杆安装架定位校正完毕后,锚杆安装架与预埋件焊接,并对辅助支撑架与预埋件焊接,焊接完成后对高强锚杆的精确位置和倾斜角度复测;
13.第三步,筏板基础凹槽内绑扎钢筋笼,在钢筋绑扎过程中,使用全站仪对高强锚杆进行监测,且现场绑扎钢筋时避免将钢筋直接铺设在锚杆安装架上;在钢筋绑扎完后且混凝土浇注前,使用全站仪对高强锚杆进行复测,校正其位置精度及倾斜角度,合格后进入混凝土浇注工序;
14.第四步,混凝土浇注前将高强锚杆的上端螺纹处涂刷黄油、包上塑料纸并套上塑料管;灌浆管上端口伸出混凝土浇注顶面并用胶纸完全封闭,在混凝土浇注过程中,避免震动棒接触高强锚杆,同步使用全站仪对高强锚杆位置精度及倾斜角度进行监测;
15.第五步,混凝土硬化后,切除锚杆安装架露出混凝土表面以上的部分,并复测各高强锚杆位置精度及倾斜角度;
16.第六步,钢立柱安装:拆高强锚杆上端的球面螺栓,并在外露的保护导管外侧涂抹密封胶,将钢立柱柱脚底板中的安装圆孔对准高强锚杆并安装在筏板基础上,将钢立柱柱脚底板调平并达到设计标高,在钢立柱柱脚底板下方空间内灌浆并养护至硬化,在高强锚杆上依次套入楔形垫板和球面螺母,其中球面螺母与楔形垫板中的球面定位孔进行球面配合,初步预紧球面螺母,初步预紧过程中通过调整球面螺母的角度消除高强锚杆的安装角度偏差;待钢立柱四周的高强锚杆都初步预紧后,在高强锚杆上端使用液压张拉工具进行预应力张拉,并紧固球面螺母,张拉顺序采用对边紧固原则逐一张拉,最后通过灌浆设备自灌浆管向保护导管内部进行灌浆,直至锚固垫板上溢流孔有连续的浆液溢出,逐一完成所有灌浆并养护至合格。
17.进一步地,在步骤一中,所述高强锚杆组件在锚杆安装架中的装配具体步骤如下:
18.子步骤1,锚杆安装架内安装保护导管,保护导管上端刚好伸出套架上表面,且保护导管与锚杆安装架成α角度倾斜设置并焊接固定,所述保护导管的上下两端分别与锚杆安装架的上钢板和下钢板中的锚杆穿孔对应;吊装并自上向下将高强锚杆插入保护导管内,吊装点设置方式为在杆体上端安装临时螺母并在临时螺母上焊接吊耳,高强锚杆的上下两端是分别插入在上钢板和下钢板的锚杆穿孔内,高强锚杆安装到位后在下端螺纹段自下向上按顺序装入锁定螺母、锚固端板、石棉垫板、垫圈和六角螺母,并使用六角螺母将锚固端板固定,然后起吊松钩,拆除临时螺母,并安装球面螺母,通过球面螺母与上钢板之间的锁紧实现锚杆上端的初步定位,完成高强锚杆组件的安装;
19.子步骤2,安装灌浆管,将灌浆管与保护导管焊接连接并形成灌浆通道,且灌浆管斜向上延伸并出筏板基础标高高点;
20.子步骤3,重复子步骤1和子步骤2,完成所有高强锚杆组件的安装;
21.子步骤4,锚杆安装架上钢板上标出钢立柱控制点,并校正每根高强锚杆的定位尺寸和倾斜角度,然后分别再次紧固球面螺母和六角螺母,然后保护导管与锚固端板围焊连接;最后将锚固端板与套架下钢板焊接连接;
22.子步骤5,并在辅助支撑架与锚杆安装架之间使用几字形连接板机械连接。
23.进一步地,所述筏板防水垫层中的预埋件安装位置加深设计。
24.建筑钢结构柱脚安装节点,包括筏板基础、锚杆安装架、高强锚杆组件、楔形垫板和钢立柱,其中,所述锚杆安装架中固定有多个高强锚栓组件,且锚杆安装架和高强锚栓组件安装在筏板基础中,其特征在于,
25.所述高强锚杆组件由高强锚杆、六角螺母、球面螺母、保护导管、灌浆管、锁定螺母、石棉垫板和垫圈组成;其中,高强锚杆的下端螺纹段自下向上按顺序装入锁定螺母、锚固端板、石棉垫板、垫圈和六角螺母,且锚固端板和保护导管焊接,保护导管下端与灌浆管焊接,保护导管上端与钢立柱柱脚底板中的安装孔连接;高强螺杆的上端自上向下按顺序安装楔形垫板和球面螺母,且球面螺母与楔形垫板中的球面定位孔进行球面配合;所述高强锚杆处于预应力拉紧状态,并在该高强锚杆和保护导管之间设有灌浆填充物;所述保护导管和锚固端板分别与所述锚杆安装架焊接连接,且高强锚杆与竖向具有α夹角;所述筏板基础为钢混结构,且内部的钢筋笼与锚杆安装架彼此不接触。
26.进一步地,还包括辅助支撑架,所述辅助支撑架位于锚杆安装架的外围,并于锚杆安装架一并在筏板基础中形成防拔结构。
27.本发明的有益效果是:
28.1、安装措施简单、设备投入少、部分措施可回收节约成本。以每根钢立柱为单位设计一个锚杆安装架,锚杆安装架将多个高强锚杆预固定(非焊接连接)在套架内,并作为一个装配模块进行整体吊装和安装,并且套架与埋件焊接连接,可实现高强锚杆的粗略定位;同时由于锚杆安装架的保护,使得高强锚杆在工地现场交叉施工时不易被撞击而损坏,为高强锚杆的验收合格提供技术支撑。
29.2、多次复测和监测实现高强锚杆的精确定位。在钢筋绑扎和混凝土浇注期间,采用全站仪对每根锚杆进行监测和复测,以实现对锚杆进行精确校正和定位;保证后期钢立柱的抗拔效果。
30.3、在高强锚杆张拉端设计球面螺母,该球面配合能调节和消除部分锚杆的安装角度微小偏差,提高了钢立柱的抗拔效果,同时可使所有不同角度配件做到标准化。
31.以下通过具体实施例,对本技术的创新性和有益效果做进一步地阐述和理解。
附图说明
32.图1为本发明中钢立柱固定后的结构示意图。
33.图2为本发明中球面螺母调节原理图。
34.图3为锚杆安装架正立面图。
35.图4为锚杆安装架侧立面图。
36.图5为锚杆安装架中上钢板的平面图。
37.图6为锚杆安装架中下钢板的平面图。
38.图7为高强锚杆在锚杆安装架中的安装图(正立面、单根)。
39.图8为高强锚杆在锚杆安装架中的安装图(侧立面、单根)。
40.图9为锚杆安装架上部分切割后的示意图(正立面)。
41.图10为锚杆安装架上部分切割后的示意图(侧立面)。
42.图11为施工过程中锚杆安装架、高强锚杆组件和辅助安装架在筏板基础凹槽中的
安装视图。
43.图12为锚杆安装架和辅助安装架之间的连接示意图。
44.图13为本发明钢立柱的安装节点图。
45.图中:
46.100高强锚杆组件,110锚杆杆体,111锚固端板,120保护导管,121环形空间,122扩大部,130灌浆管,140锁定螺母,150石棉垫板,160楔形垫板,161溢浆孔,170垫圈,180六角螺母,190球面螺母,191球面配合,
47.200锚杆安装架,210上钢板,220下钢板,230锚杆穿孔,
48.300辅助支撑架,310几字形连接件,
49.400预埋件,400’预埋件,
50.500钢筋笼,510筏板基础,
51.600钢立柱,610底板,620密封胶,630溢流空间,640找平填充层。
具体实施方式
52.本单位承建的某工程中,主楼工程由于塔楼倾斜和大悬臂结构的外形设计,结构在风荷载或地震等侧向力作用下外框钢立柱可能产生较大的拔力,及钢立柱存在拉应力的可能性,经测算,每根单根钢立柱最大拔力为15524kn。
53.高强锚杆安装角度与倾斜钢立柱安装角度一致,参考图1,安装倾角α的范围为4
°
~6
°
,本实施例中选择α=5
°
。经计算高强度锚杆在筏板基础中的埋设深度在1.0米至3.0米之间,高强度锚杆外露尺寸在0.5米,用于连接钢立柱,实现钢立柱柱脚的稳固、可靠安装。
54.本实施例中,采用了m50规格的高强预应力锚杆群对钢立柱柱脚与筏板基础之间进行机械连接以抵抗拔力,本实施中选择最佳布置,及锚杆群中的锚杆与上述的钢立柱的倾角是一致的设计。设计锚杆最长长度为3500mm,且锚杆双向倾斜5度布设,数量为10根。单根锚杆抗拉极限强度为830n/mm2、屈服强度为535n/mm2,图1为本实施例中高强锚杆装配简图。
55.施工中,高强锚杆与筏板基础紧密连接,最下端埋深至筏板底部受力钢筋表面处,将上部结构与筏板基础浇注并连成一个整体,承受钢立柱柱脚的拔力,参考图13。该高强锚杆大部被浇注在筏板基础中,并在筏板基础中绑扎钢筋笼。
56.传统的高强锚杆组件是由锚杆和两端的垫片、螺母等组成的。本实施例采用预应力安装方法安装,其中锚杆杆体的上下两端设置有螺纹段,用于安装螺母,螺母分为球面螺母和常规六角螺母。
57.锚杆杆体采用碳—铬合金材料热轧制成型制造,锚杆杆体相关参数如下表:
[0058][0059]
本实施例中,以高强锚杆组件100为配置单元并进行详细介绍,该组件的核心零件为锚杆杆体110,为便于描述,该锚杆杆体简称锚杆或者杆体,根据操作规范,锚杆杆体110热轧成型,不可焊接,避免杆体产生破坏。作为锚杆的配套零部件,还包括保护导管120、灌浆管130、锁定螺母140、石棉垫板150、楔形垫板160、垫圈170、六角螺母180、球面螺母190等
零部件,还包括一个力学部件——锚固端板111。其中,保护导管120为无缝薄壁钢管,直管,该保护导管120上端敞口,下端焊接锚固端板,且保护导管在锚杆安装架中倾斜设置。所谓的锚固端板111是指圆形的或者方形的钢板。保护导管120为钢管,具有便于焊接的优势,通过将保护导管与锚杆安装架的焊接固定来间接实现锚杆杆体与锚杆安装架的直接焊接,解决了锚杆杆体不能直接焊接的弊端。该保护导管120内径为φ80mm,远大于锚杆直径,安装后,锚杆与保护导管之间形成一个环形空间121,该环形空间作用有二,其一,作为锚杆拉应力施加时锚杆的变形空间,其二为拉应力施加完毕后进行的灌浆操作的空腔,通过灌浆操作实现对锚杆的状态保护,赶出空气并实现灌浆料的封装。上述的保护导管下端具有一个扩大部122,该扩大部的内径为φ100mm,扩大部有效长度为100mm,该扩大部扩大的内腔用于满足锁定螺母140的安装要求。锁定螺母140通过螺纹配合安装在锚杆杆体下端的螺纹段上,自上侧对锚固端板进行定位,在锚固端板下侧通过石棉垫板150和六角螺母固定,在上下两侧锁紧螺母140和六角螺母180的共同夹持和夹紧作用下,将锚固端板111固定在杆体的下端。
[0060]
本实施例中,锚固端板111中必然具有与,锚杆杆体配合的穿孔。该锚固端板111与上述的保护导管120下端的扩大部管口之间是焊接固定,两者之间形成完全的密封焊接,也就是说,保护导管与锚杆杆体之间是通过锚固端板保持相对固定位置的。
[0061]
在保证连接强度的情况下,该处的锚固端板111和保护导管之间也可以采用其他的机械连接方式,例如螺纹连接,皆在本技术的保护范围之内。
[0062]
锚杆杆体的最下端,即,下端螺纹段插入到锚杆安装架200的下钢板的穿孔中,并在重力的作用下搭放即可,实现锚杆轴向上的定位。
[0063]
有上述可知,灌浆管130下端焊接在保护导管的扩大部122上的,并在连接点做局部折弯,并实现两者之间的贯通,也是在对锚杆施加预应力后施加灌浆填充的路径。上述灌浆管130的上端口应当延伸至待浇注的筏板基础之上至少50厘米处,并做保护,避免堵塞,以便于灌浆操作的顺利进行。
[0064]
在钢立柱安装施工阶段,参考图1和图2,该螺杆杆体的上端通过球面螺母190自下而上旋紧的方式,将实现锚杆杆体110与钢立柱柱脚底板610的直接机械连接。
[0065]
在浇筑混凝土施工阶段,亦可以通过球面螺母的上表面与锚杆安装架的上钢板之间反向顶紧,施加向上的反向力,对螺杆杆件在上端形成轴向锁紧,配合螺杆杆件下端的锁紧,可以进一步地防止锚杆杆件的晃动。本结构中,球面螺母位于上钢板的下侧,自下而上顶紧。这样,上钢板对锚杆杆体自上端锁紧,锚固垫板自锚杆杆体下端锁紧,实现单根高强锚杆的初步定位和锁紧,该过程是在工厂车间完成的,装配精度高,装配效果好。
[0066]
楔形垫板用于后工序中的钢立柱的安装,在具体施工工法中做详细介绍。
[0067]
本工程中采用的高强锚杆,要求高强锚杆埋设精度高并且与主体钢结构连接可靠。
[0068]
施工中,应充分保证高强锚杆的精确定位和安装精度。若采用直接将高强度锚杆与钢筋笼绑扎的方式固定,不能满足精度要求,且在浇注混凝土的过程中,锚杆的位置会发生变化。所以直接安装高强锚杆存在难题,安装精度和效率不能满足技术要求。
[0069]
本实施例基于该问题,提出以下解决施工方案:
[0070]
技术措施包括锚杆安装架的制作、埋设定位、球面螺母的应用并提供全套施工工
艺。
[0071]
锚杆安装架的制作:采用cad技术在计算机中放样出每根钢立柱安装节点中所有高强锚杆的精确位置、倾斜角度等参数,并且以每根钢立柱为单位利用计算机辅助设计技术设计锚杆安装架、辅助支撑架的全套图纸,并根据图纸制造。具体来说,该锚杆安装架200主体采用角钢为原材料,通过竖向、横向、纵向和斜向的焊接形成立体结构,参考图3和图4中所示的长方体框架结构,由于跨度较大,设置上中下三层,并在该锚杆安装架中设上、下两层钢板,图5为上钢板210的平面图,图6为下钢板220的平面图。其中两个钢板中激光切割锚杆穿孔230作为锚杆的固定点,钢板采用q235或q345,厚度以20或者30
㎜
的厚钢板为宜。由图5和图6可知,上下两层钢板中的激光切割并形成锚杆穿孔230,彼此错位布置,通过将每根锚杆两端分别穿入两钢板中对应的锚杆穿孔,以保证高强锚杆具有5度设计角度。
[0072]
也就是说,钢板上的两个锚杆穿孔230形成的固定点之间的连线为锚杆的空间角度位形,图7和图8为高强预应力锚杆安装架简图。
[0073]
还包括辅助支撑架300,同锚杆安装架类似,该辅助支撑架采用同规格的角钢焊接支座,该辅助支撑架用于对锚杆安装架进行辅助的支撑。该辅助支撑架300是由是由四个向外倾斜的斜撑和两个方形框组成的台形结构,断面为上小下大的梯形轮廓。该辅助支撑架套在锚杆安装架的外围,并在两者之间设置几字形连接件310进行连接,几字形连接件优选钢板折弯成几字形钣金结构,钢条形成半刚性连接,阻断震动传递路线。
[0074]
上述的辅助支撑架300底部通过焊接的形成与预埋件400固定连接,其中的预埋件为位于筏板基础底部基础中的预埋金属件。
[0075]
上述的锚杆安装架200底部也通过焊接的形成与预埋件400’固定连接,其中的预埋件为位于筏板基础底部基础中的预埋金属件。
[0076]
上述实施中,锚杆安装架和辅助支撑架的结构较为简单,材料方便采购,现场加工以便运输,且可立即进行装配式施工,以节省工期。锚杆安装架和辅助支撑架加工全部采用焊接连接,以降低实施的成本。
[0077]
锚杆安装架200、辅助支撑架300和高强锚杆组件100在生产车间内完成组装,经运输至施工现场进行装配式施工(标高由锚杆顶点控制),施工现场用塔吊或者吊车将锚杆安装架、辅助支撑架和高强锚杆组件组成的共同体一并吊装至安装点,经测量定位后,锚杆安装架、辅助支撑架的安装脚分别与筏板垫层中的预埋件进行有效的焊接连接,锚杆安装架固定的同时实现了高强锚杆的粗略定位,参考图12。
[0078]
在锚杆安装架200周围所在的筏板垫层中进行钢筋的绑扎以便形成钢筋笼500,如图12中所示,该绑扎过程中,钢筋笼与锚杆安装架之间无直接的、刚性的连接,彼此不干扰。并采用全站仪对每根高强锚杆进行定位监测,并且在混凝土浇注前对每根锚杆定位复测,通过铜锤敲击锚杆顶部的方式,微调,以实现锚杆的精确定位,图7和图8为吊装前高强预应力锚杆安装架和锚杆组装简图。
[0079]
在对筏板基础坑槽进行混凝土浇注时,采用全站仪对每根高强锚杆进行定位监测,以观测锚杆位置是否变化,如有变化及时调整。
[0080]
筏板基础坑槽内的混凝土浇注完成并养护硬化后,形成钢筋混凝土结构的筏板基础510,使用切割机切割高强锚杆安装架混凝土表面以上的部分(或者切割到钢立柱底标高
△
0处),并将切除部分摘除,摘除后复测各高强锚杆位置,由于10根高强锚杆的布置、间距
和精度与设计完全一致,最后进行钢立柱的安装,图9和图10为钢结构吊装前高强预应力高强锚杆安装架切割后的简图。
[0081]
参考图1和图13安装钢立柱600的底板610,钢立柱底板采用135
㎜
厚钢板,该钢立柱600的底板610上具有容高强度高强锚杆穿过的穿孔,也是安装孔。穿孔为多个,每根高强度高强锚杆对应一个,本实施例节点中,每根钢立柱600对应十个安装孔。具体来说,高强锚杆的上端采用球面螺母进行锚固,为解决球面螺母与钢立柱底板之间存在安装偏差的难题,在两者之间设置一个楔形垫块,具体来说,该楔形垫块上下端面之间具有5度夹角,该楔形垫块与钢立柱底板之间保持粗糙面配合,例如表面压花措施,防止两者之间的相对滑动。该楔形垫块与球面螺母之间为球面配合面,能够同时适应一定范围倾斜角度锚杆的安装,使所有配件标准化,降低实施成本,图5为球面螺母安装端部大样图。
[0082]
同时,在该楔形垫块160上具有一个溢浆孔161,该溢浆孔上下方向贯穿该楔形垫块,使得保护导管中的灌浆砂浆可以自下向上溢流,并最终灌浆砂浆将套筒内部空间填充满。
[0083]
上述结构中,如果高强锚杆存在倾斜角度上的安装偏差,在灌浆步骤之前,可以调整球面螺母,通过与楔形垫块之间的转动来消化此安装偏差;这是可以轻松实现的。
[0084]
高强锚杆的可调节角度大小可根据锚杆直径、楔形垫板中间球面孔、钢立柱底板安装圆孔直径以及各配件的厚度等因素确定,例如楔形垫板中间的球面孔直径明显大于高强锚杆的直径,以便具有充分的调整空间,如下图6所示,以球面螺母球面中心为转动点,调节角度θ范围为:-0.5《θ《+0.5(设顺时钟转动时为负,即a为负值),图2为球面螺母可调整锚杆角度倾斜偏差图。
[0085]
参考图1,保护导管上端插入到钢立柱底板610的安装圆孔内,插入深度为钢立柱底板的三分之一厚度,也就是安装圆孔孔深的三分之一处,并在保护导管的管口部位与安装圆孔内壁之间之间填充密封胶620,实现保护导管上端的固定。上述安装圆孔中形成一个灌浆浆料的溢流空间630。
[0086]
灌浆浆料的流动路线为:灌浆管(自上而下)、保护导管(自下而上)、安装圆孔(底板)、溢流孔(楔形垫板)、套管内腔。
[0087]
高强预应力锚杆在钢结构基础中的施工方法,
[0088]
第一步,采用cad技术在计算机中放样出每根钢立柱安装节点中所有高强锚杆的精确位置,并且以每根钢立柱为单位利用计算机辅助设计技术设计锚杆安装架和辅助支撑架全套图纸,该锚杆安装架主体采用角钢通过竖向、横向、纵向和斜向的焊接形成立体结构,并在该锚杆安装架中设上、下两层钢板,钢板中激光切割锚杆孔作为锚杆的固定点,钢板采用q235或q345,厚度以20或者30
㎜
的厚钢板为宜。且上下两层钢板中的激光切割锚杆孔彼此错位布置,通过将每根锚杆两端分别穿入两钢板中对应的锚杆孔。
[0089]
在钢结构制作车间制作锚杆安装架和辅助支撑架,并在加工车间内,就将高强锚杆组件预装配到锚杆安装架内,以减少施工现场作业和与其它工程的交叉作业,降低安全风险,且作业速度快能够降低成本。
[0090]
车间内,高强锚杆组件在锚杆安装架中的装配具体步骤如下:
[0091]
子步骤1、锚杆安装架内安装φ88*2锚杆保护导管(保护导管下端设放大头,尺寸为φ102*2),保护导管上端略伸出套架上表面,保护导管与锚杆安装架成角度α(本实施例α
为5
°
)设置并焊接固定,且保护导管的上下两端分别与上钢板和下钢板上的锚杆穿孔对应,倾斜5度设置;采用桁吊安装锚杆,将其插入保护导管内,吊装点设置方式为在锚杆一端安装一个临时螺母并在临时螺母上焊接吊耳(需要说明:锚杆为高强钢不得在上面焊接任何零件,本实施例中将焊点设置在临时螺母上,没有违反这一原则);同时在锚杆的下端螺纹段中自下向上按顺序装入锁定螺母、锚固端板、石棉垫板、垫圈和六角螺母,并使用六角螺母将锚固端板固定在杆体的下段,参考图7和图8,然后起吊松钩;最后去除临时吊装螺母,并安装球面螺母,并通过球面螺母与上钢板之间的锁紧实现锚杆上端的初步定位,完成一根锚杆的安装。锚杆安装架内的所有锚杆按上述顺序逐根完成。
[0092]
子步骤2、安装灌浆管φ20*2,将其与保护导管焊接连接,其中,在对应的焊接点位置的保护导管上设置有灌浆孔,该灌浆孔与灌浆管贯穿对应。该灌浆管斜向上延伸并出筏板基础标高高点。为便于灌浆,该灌浆管与保护导管之间具有夹角。
[0093]
子步骤3、重复子步骤1和子步骤2,完成所有高强锚杆组件100的安装。
[0094]
子步骤4、套架上表面标出钢立柱控制点(即钢立柱定位轴线控制点),校正每根锚杆的定位尺寸和倾斜角度,然后紧固球面螺母和六角螺母,使得高强锚杆、锚固端板和保护导管灌浆管形成一个整体,本实施例中,上述的高强锚杆的上下两端是分别插入在上钢板和下钢板的锚杆穿孔内的;复测锚杆并通过敲击的方式调整锚杆的夹角数值为设计角度,然后保护导管与锚固端板围焊连接;最后将锚固端板与套架下钢板再次进行焊接连接,完成精准定位,并通过多个焊点保证螺杆杆体的安装强度。
[0095]
第二步,锚杆安装架的吊装及安装:
[0096]
1、预埋件安装:在筏板防水垫层施工阶段,根据外围轴线控制点及标高控制点测放出套架每个预埋件的准确位置,安装预埋件;对较高和较重的高强锚杆安装架,应增加辅助支撑架预埋件,以保证锚杆安装架的预固定强度,不晃动,牢靠。垫层混凝土完成后,对预埋件定位进行复测,以保证精度。
[0097]
2、高强锚杆系统埋设:筏板底筋绑扎前,开始预应力高强锚杆支撑套架埋设工作。采用土建塔吊将高强锚杆安装架吊装就位,待锚杆安装架定位校正完毕后,将该锚杆安装架的角钢支腿与垫层中的预埋件焊接;为了防止筏板混凝土浇注和钢筋绑扎对锚杆产生位移和变形,在锚杆安装架外围加设辅助支撑安装架,以增强锚杆安装架的刚度,同时在两个安装架之间的中部增设几字形连接板,形成横向支撑,且几字形连接板具有半刚性的特点,具有减震和隔振的良好效果,参考图11和图12。
[0098]
第三步,绑扎钢筋笼,混凝土浇注前的精确定位复测,在钢筋绑扎过程中,采用全站仪对锚杆安装架进行定位监测,且现场绑扎钢筋时避免将钢筋直接铺设在套架上以免锚杆安装架整体倒塌或者形变;并且在钢筋绑扎完后和筏板混凝土浇注前,使用全站仪对预应力锚杆进行最后复测,校正其位置及标高,进入下道混凝土浇注工序;高强锚杆具有直径大、尺寸长、单根较重、每根钢立柱数量不等、且倾斜一定角度的安装特点,要满足锚杆准确高精度定位,必须保证安装架和支撑架的稳固,筏板钢筋绑扎和混凝土浇注时必须防止变形和移动。
[0099]
第四步,混凝土浇注时的保护措施和定位监测:混凝土浇注前需将锚杆的上端螺纹处涂刷黄油、包上塑料纸并套上塑料管;并将灌浆管上端口用胶纸完全封闭,并且伸出混凝土浇注顶面400mm。在混凝土浇注过程中,派专人对其进行监控,并且避免震动棒接触锚
杆或离锚杆太近,以免影响定位精度;同时在混凝土浇注时,在基坑四周采用全站仪对锚杆位置进行监测,全过程控制混凝土浇注对高强锚杆定位的影响。
[0100]
第五步,锚杆安装架的处理:在混凝土浇注完成后,切割锚杆安装架混凝土表面以上的部分(或者切割到钢立柱底标高处),参考图9和图10,保留筏板基础中的部分,并复测各高强锚杆位置,最后进行主体钢立柱安装。
[0101]
高强预应力锚杆不得在施工现场进行任何焊接,并且在交叉作业时和锚杆安装架切割时保护好锚杆螺纹。
[0102]
第六步,钢立柱安装:拆高强锚杆上端的球面螺栓,并在外露的保护导管外侧涂抹密封胶,将钢立柱柱脚底板中的安装圆孔对准高强锚杆并安装在筏板基础上,将钢立柱柱脚底板调平并达到设计标高,在钢立柱柱脚底板下方空间内灌浆并养护至硬化,形成找平填充层640。该找平填充层为混凝土砂浆,填充在筏板基础和钢立柱柱脚底板之间的空间中,这对于底板的安装精度具有积极意义。在高强锚杆上依次套入楔形垫板和球面螺母,其中球面螺母与楔形垫板中的球面定位孔进行球面配合191,初步预紧球面螺母,初步预紧过程中通过调整球面螺母的角度消除高强锚杆的安装角度偏差;待钢立柱四周的高强锚杆都初步预紧后,在高强锚杆上端使用液压张拉工具进行预应力张拉,并紧固球面螺母,张拉顺序采用对边紧固原则逐一张拉,最后通过灌浆设备自灌浆管向保护导管内部进行灌浆,直至锚固垫板上溢流孔有连续的浆液溢出,逐一完成所有灌浆并养护至合格。
[0103]
步骤六中,球面螺母误差调整的调整方法,参考图2,钢立柱安装完成后,安装球面螺母并消化高强锚杆安装角度偏差,高强锚杆进行预应力张拉后紧固螺母,最后进行高强锚杆灌浆。
[0104]
本实施例的施工优势至少包括以下几点:
[0105]
1、一般来说普通锚杆一般为定位锚杆非受力锚杆且材料等级不高,现场安装时可以进行焊接固定。本实施例中,使用的是高强锚杆,高强锚杆的特性是强度高且有脆性,按照高强螺杆的使用说明,不得进行现场焊接,本实施例中要求高强锚杆与锚杆安装架之间通过保护导管和锚固端板进行间接固定,且保护导管和锚固端板与锚固安装架之间存在多处焊接,安装牢靠性有保证。
[0106]
2、按传统方法,在锚杆焊接后,锚杆位置要进行调整较为困难,而本施工安装方法中,锚杆杆体上端采用的连接为非焊接连接,且该锚杆杆体尽在下端与锚固端板进行固定,且在锚杆杆体和保护导管之间具有一定的调节空间,通过球面螺栓的作用可以对安装误差进行微调,可以调节锚杆上端的安装精度。
[0107]
3、锚杆张拉端采用球面螺母,可以适应不同倾斜角度锚杆的安装,可使配件标准化,节约成本,同时可以消化锚杆安装误差,技术较为先进。
[0108]
4、传统锚杆全部埋设,出现安装误差不方便调整,只能拆除重建,成本高。
[0109]
5、本技术,大部分预装配工作在车间内完成,可以采用装配式施工提高了施工效率。
[0110]
本技术实施后,可以一次性实现多根预应力高强锚杆在一个钢立柱安装点中的预设难题,通过分布在钢立柱处。例如,传统中,每一个钢立柱需要配置8至12根锚杆,涉及面积和数量较大。本施工中采用锚杆安装架和锚杆同时安装的做法,将一个钢立柱所需要的锚杆全部预装配于一体,车间预装配,施工现场仅需采用一台小型汽车吊就能满足吊装要
求,避免了现场采用塔吊逐根锚杆安装,以减少了塔吊起重设备的投入,大大节约了安装成本。
[0111]
锚杆张拉端采用球面螺母可以适应倾斜锚杆的角度,使所有不同角度锚杆的配件全部按倾斜5度加工,做到标准化,大大节约了配件加工成本,经济效益非常可观。
[0112]
锚杆安装架车间内焊接加工,且锚杆在加工完成时同步安装,然后运输至指定地点进行吊装,整个工作可以与其它工序同时进行,又减少了现场交叉作业,施工周期最短。
[0113]
锚杆张拉端采用球面螺母可以适应一定范围的倾斜锚杆角度,并且可以消化部分安装角度误差。从完成工程安装结果来看,100%的钢立柱锚杆预埋定位准确,无一底板扩孔现象,无一返工现象,在国内钢结构安装行业中也少有。
[0114]
安装时采用了锚杆安装架一次定位,并于筏板基础预埋件焊接固定,锚杆二次精确定位,提高了安装精度,能够满足预埋精度要求。
[0115]
本实施例仅仅是基于本工程的一次有效尝试的描述,不应对本技术的保护范围造成自我限制,具有类似的施工,也应落入本发明的保护范围。