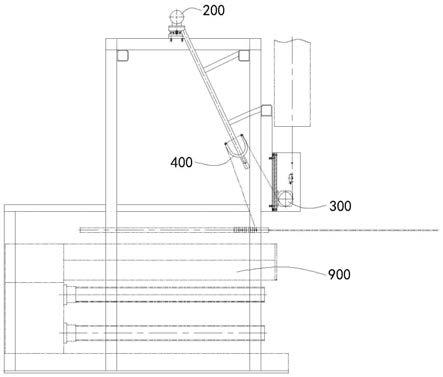
1.本发明涉及纺丝卷绕技术领域,尤其涉及一种新型纺丝卷绕装置及纺丝卷绕方法。
背景技术:2.纺丝卷绕装置是将由纺丝装置出来的丝束卷绕到卷绕机的卡头纸管形成规则丝饼。目前,纺丝机架加工难度大,不便于安装调试,加工成本高。比如,专利cn206736414u公开了一种纺丝卷绕装置,需要有两个分丝位,只有到分丝二位配合上方挂丝装置才能得到足够的包角,包覆上导盘,两个分丝位增加挂丝时间,产生的废丝相应增加。
技术实现要素:3.本技术提供一种新型纺丝卷绕装置及纺丝卷绕方法,解决了相关技术中由于多个分丝位导致挂丝时间长、废丝量大的技术问题。
4.本技术提供一种新型纺丝卷绕装置,包括框架、上导盘、下导盘以及叉式支架,上导盘可移动地固定于框架,下导盘固定于框架,叉式支架可移动地安装于框架,叉式支架被配置为丝束绕经叉式支架的叉头且与叉式支架围合形成穿孔区域,以在丝束随叉式支架上移后上导盘移入穿孔区域将丝束挂载在上导盘上。
5.可选地,新型纺丝卷绕装置设有用于驱动叉式支架作直线往复运动的驱动机构,驱动机构安装于框架。
6.可选地,驱动机构包括作直线伸缩运动的伸缩杆,以驱动叉式支架作直线往复运动,叉式支架与伸缩杆一端防转动连接。
7.可选地,叉式支架的叉头设有带轴承导丝器,丝束通过带轴承导丝器绕经叉式支架设置。
8.可选地,新型纺丝卷绕装置包括上导盘安装机构和下导盘安装机构;
9.上导盘安装机构包括:
10.上导盘支撑横梁,固定于框架;
11.上导盘过渡板,安装于上导盘支撑横梁上;
12.直线导轨,固定于上导盘过渡板上;
13.推出气缸,固定于上导盘过渡板上;
14.上导盘座板,滑设于直线导轨,且与推出气缸的活塞杆连接;
15.其中,上导盘安装于上导盘电机的电机轴,上导盘电机安装于上导盘座板,以在丝束随叉式支架上移后驱动上导盘移入穿孔区域将丝束挂载在上导盘上;
16.下导盘安装机构包括下导盘过渡板,下导盘过渡板固定于框架,下导盘安装于下导盘电机的电机轴,下导盘电机安装于下导盘过渡板。
17.可选地,新型纺丝卷绕装置包括平行度调节机构,平行度调节机构包括上导盘调节组和/或下导盘调节组;
18.上导盘调节组包括:
19.第一上导盘托架,沿水平设置且与上导盘的盘面垂直,固定于上导盘支撑横梁上;
20.第一上导盘安装板,沿水平设置且与上导盘的盘面垂直,设于第一上导盘托架远离上导盘支撑横梁的一侧,与直线导轨和推出气缸固定连接;上导盘过渡板包括第一上导盘托架和第一上导盘安装板;
21.多个第一调节件,包括固定于第一上导盘托架下侧面的第一螺帽以及与第一螺帽配合的第一调节螺钉,第一调节螺钉与第一上导盘托架螺纹连接且一端与第一上导盘安装板相接;以及
22.至少一个第一固定螺钉,与第一上导盘托架和第一上导盘安装板螺纹连接;
23.下导盘调节组包括:
24.第二下导盘托架,沿竖向设置且与下导盘的盘面垂直,固定于框架;
25.第二下导盘安装板,沿竖向设置且与下导盘的盘面垂直,设于第二下导盘托架远离框架的一侧,与下导盘电机固定连接;下导盘过渡板包括第二下导盘托架和第二下导盘安装板;
26.多个第二调节件,包括固定于第二下导盘托架一竖侧的第二螺帽以及与第二螺帽配合的第二调节螺钉,第二调节螺钉与第二下导盘托架螺钉连接且一端与第二下导盘安装板相接;以及
27.至少一个第二固定螺钉,与第二下导盘托架和第二下导盘安装板螺纹连接。
28.可选地,新型纺丝卷绕装置包括平行度调节机构,平行度调节机构包括上导盘调节组和/或下导盘调节组;
29.上导盘调节组包括:
30.第三上导盘托架,沿竖向布置且与上导盘的盘面平行,底端与上导盘座板固定连接,与上导盘电机间隔设置;
31.第三上导盘安装板,沿竖向布置且与上导盘的盘面平行,设于第三上导盘托架一侧,与上导盘电机固定连接;
32.多个第三调节件,包括固定于第三上导盘安装板远离第三上导盘托架的一侧的第三螺帽,以及与第三螺帽配合的第三调节螺钉,第三调节螺钉与第三上导盘安装板螺纹连接且一端与第三上导盘托架相接;以及
33.至少一个第三固定螺钉,与第三上导盘托架和第三上导盘安装板螺纹连接;
34.下导盘调节组包括:
35.第四下导盘托架,沿竖向布置且与下导盘的盘面平行设置,与框架固定连接,与下导盘电机间隔设置;
36.第四下导盘安装板,沿竖向布置且与下导盘的盘面平行设置,设于第四下导盘托架一侧,与下导盘电机固定连接;
37.多个第四调节件,包括固定于第四下导盘安装板远离第四下导盘托架的一侧的第四螺帽,以及与第四螺帽配合的第四调节螺钉,第四调节螺钉与第四下导盘安装板螺纹连接且一端与第四下导盘托架相接;以及
38.至少一个第四固定螺钉,与第四下导盘托架和第四下导盘安装板螺纹连接。
39.可选地,上导盘安装机构还设有限位组,限位组包括:
40.中空的定位柱,底端固定于上导盘过渡板,顶端与上导盘底板相接;
41.弹性件,呈压缩状态设置,沿竖向布置,内设于定位柱;
42.顶珠,内设于定位柱,与弹性件的顶部相接,与上导盘底板的底侧的凹槽配合,以在推出气缸动作时限位上导盘底板;以及
43.限位块,固定于直线导轨一端,以在推出气缸动作时限位上导盘底板。
44.可选地,下导盘安装机构还包括罩壳,罩壳固定安装于下导盘过渡板,罩壳罩设于下导盘电机,下导盘电机的电机轴穿设于罩壳,下导盘外设于罩壳,罩壳还安装有预网络器和切吸丝器,丝束依次绕经切吸丝器、预网络器、下导盘、叉式支架以及卷绕机的移动导丝器。
45.一种纺丝卷绕方法,采用上述的新型纺丝卷绕装置,包括:
46.采用吸枪吸住丝束绕过下导盘经叉式支架到卷绕机的移动导丝器;
47.叉式支架上行至上导盘位置处;
48.上导盘移动至叉式支架与丝束形成的穿孔区域中;
49.叉式支架下行,丝束挂载在上导盘;
50.卷绕机的移动导丝器推至正常纺丝位置,进行生头。
51.本技术有益效果如下:本技术提供一种新型纺丝卷绕装置,利用叉式支架带动丝束移动,配合上导盘的可移动式固定,保障足够包角完成挂丝以及减少分丝位从而改善技术问题,具体地,丝束绕经叉式支架的叉头且与叉式支架围合形成穿孔区域,开始时,将丝束绕过下导盘、叉式支架至卷绕机,然后通过叉式支架的移动带动丝束上移,至上导盘区域,后驱动上导盘移动至穿孔区域,再将叉式支架下移,即可将丝束挂载在上导盘上,通过叉式支架与丝束形成的穿孔区域,保障足够包角,保证能在卷绕机的最外侧挂丝,无需先将移动导丝器推到最里面,丝束到上导盘后再将移动导丝器拉出来挂丝,大大减少生头时间,减少废丝量;而且驱动叉式支架上行不存在大负载,可采用简易式驱动机构,有利于降低成本;通过本装置,挂丝操作更简单,效率更高。
附图说明
52.为了更清楚地说明本发明实施例或现有技术中的技术方案,下面将对实施例描述中所需要使用的附图作简单地介绍,显而易见地,下面描述中的附图仅仅是本发明的一些实施例。
53.图1为本技术提供的一种新型纺丝卷绕装置的侧视图;
54.图2为图1所示装置的正视图;
55.图3为图1中上导盘安装机构与上导盘调节组的具体结构示意图;
56.图4为图2中下导盘安装机构与下导盘调节组的具体结构示意图;
57.图5为图2中叉式支架与丝束形成穿孔区域的示意图;
58.图6为图2中限位组的部分结构示意图;
59.图7为图1所示装置的开始挂丝状态图;
60.图8为图1所示装置的挂丝中间状态图;
61.图9为图1所示装置的挂丝完成状态图;
62.图10为本技术提供的另一种新型纺丝卷绕装置的侧视图;
63.图11为图10所示装置的正视图;
64.图12为图10中上导盘调节组的结构示意图;
65.图13为图11中上导盘安装机构与限位组部分结构的示意图;
66.图14为图10中下导盘调节组的结构示意图;
67.图15为图11中下导盘安装机构的结构示意图;
68.图16为本技术提供的纺丝卷绕方法的流程示意图。
69.附图标注:100
‑
框架,110
‑
立柱,121
‑
第一横梁,122
‑
第二横梁,123
‑
第三横梁,131
‑
第一托脚,132
‑
第二托脚,140
‑
竖杆,200
‑
上导盘,210
‑
上导盘电机,300
‑
下导盘,310
‑
下导盘电机,400
‑
叉式支架,410
‑
穿孔区域,420
‑
驱动机构,421
‑
方孔,430
‑
带轴承导丝器,500
‑
上导盘安装机构,510
‑
上导盘支撑横梁,520
‑
上导盘过渡板,530
‑
直线导轨,540
‑
推出气缸,550
‑
上导盘座板,560
‑
万向接头,600
‑
下导盘安装机构,610
‑
下导盘过渡板,620
‑
罩壳,621
‑
预网络器,622
‑
切吸丝器,700
‑
平行度调节机构,710
‑
上导盘调节组,711
‑
第一上导盘托架,712
‑
第一上导盘安装板,713
‑
第一调节件,713a
‑
第一螺帽,713b
‑
第一调节螺钉,714
‑
第一固定螺钉,721
‑
第三上导盘托架,722
‑
第三上导盘安装板,723
‑
第三调节件,723a
‑
第三螺帽,723b
‑
第三调节螺钉,724
‑
第三固定螺钉,730
‑
下导盘调节组,731
‑
第二下导盘托架,732
‑
第二下导盘安装板,733
‑
第二调节件,733a
‑
第二螺帽,733b
‑
第二调节螺钉,734
‑
第二固定螺钉,741
‑
第四下导盘托架,742
‑
第四下导盘安装板,743
‑
第四调节件,743a
‑
第四螺帽,743b
‑
第四调节螺钉,744
‑
第四固定螺钉,800
‑
限位组,811
‑
定位柱,812
‑
弹性件,813
‑
顶珠,820
‑
限位块,900
‑
卷绕机。
具体实施方式
70.本技术实施例通过提供一种新型纺丝卷绕装置及纺丝卷绕方法,解决了相关技术中由于多个分丝位导致挂丝时间长、废丝量大的技术问题。
71.本技术实施例中的技术方案为解决上述技术问题,总体思路如下:
72.一种新型纺丝卷绕装置,包括框架、上导盘、下导盘以及叉式支架,上导盘可移动地固定于框架,下导盘固定于框架,叉式支架可移动地安装于框架,叉式支架被配置为丝束绕经叉式支架的叉头且与叉式支架围合形成穿孔区域,以在丝束随叉式支架上移后上导盘移入穿孔区域将丝束挂载在上导盘上。
73.为了更好的理解上述技术方案,下面将结合说明书附图以及具体的实施方式对上述技术方案进行详细的说明。
74.实施例1
75.请参照图1至图9,其中图1至图6公开了本实施例提供的新型纺丝卷绕装置具体结构,图7至图9公开了本实施例提供的新型纺丝卷绕装置的工作状态变化示意。
76.具体地,新型纺丝卷绕装置包括框架100、上导盘200、下导盘300以及叉式支架400,上导盘200可移动地固定于框架100,下导盘300固定于框架100,叉式支架400可移动地安装于框架100,叉式支架400被配置为丝束绕经叉式支架400的叉头且与叉式支架400围合形成穿孔区域410,以在丝束随叉式支架400上移后上导盘200移入穿孔区域410将丝束挂载在上导盘200上。
77.需要指出的是,上导盘200可移动地固定于框架100,具体指的是上导盘200在装置
中的固定位置可以驱动下改变,且可以维持一个点位不变,且固定于框架100指的是上导盘200的空间位置,还包括上导盘200本身可旋转的设置,以配合丝束卷绕。具体地,该固定设置指的是上导盘电机210的固定设置,上导盘200安装于上导盘电机210的电机轴,可自由旋转。
78.类似的,实施例中的下导盘300固定于框架100,值得是下导盘300在装置中的空间位置不变,且可转动设置,以配合丝束卷绕。
79.该方式中利用叉式支架400带动丝束移动,配合上导盘200的可移动式固定,保障足够包角完成挂丝以及减少分丝位从而改善技术问题。其中,丝束绕经叉式支架400的叉头且与叉式支架400围合形成穿孔区域410,开始时,如图7所示将丝束绕过下导盘300、叉式支架400至卷绕机900,然后如图8所示通过叉式支架400的移动带动丝束上移,至上导盘200区域,后驱动上导盘200移动至穿孔区域410,如图9所示再将叉式支架400下移,即可将丝束挂载在上导盘200上。
80.通过叉式支架400与丝束形成的穿孔区域410,主要通过如图5和图6所示的叉式支架400的两个叉头将丝束撑开,配合上导盘200移入、移出穿孔区域410,保障足够包角,保证能在卷绕机900的最外侧挂丝,从而无需先将移动导丝器推到最里面,可入图7至图9所示丝束到上导盘200后再将移动导丝器拉出来挂丝,大大减少生头时间,减少废丝量。
81.而且在本实施例提供的新型纺丝卷绕装置中,关于叉式支架400上移,驱动装置仅需要驱动叉式支架400上下移动,相较于一般技术中驱动上导盘200与上导盘电机210上下移动的方式,本方式减小了驱动负载,可采用简易式驱动机构420,有利于降低成本。此外如图7至图9所示方式,通过本装置,挂丝操作更简单,工作效率更高。
82.可选地,新型纺丝卷绕装置设有用于驱动叉式支架400作直线往复运动的驱动机构420,驱动机构420安装于框架100。如图2、图7至图9所示,驱动机构420可采用气缸、电液推杆等形式,驱动叉式支架400上移与下行。
83.可选地,驱动机构420包括作直线伸缩运动的伸缩杆,例如气缸的活塞杆以驱动叉式支架400作直线往复运动。叉式支架400与伸缩杆一端防转动连接,如图5所示,通过叉式支架400上的方孔421与气缸活塞杆一端连接,保证气缸上行时叉式支架400稳定不偏转。
84.为了实现叉式支架400可移动地安装于框架100,具体为叉式支架400上行和下移,除了上述作直线往复运动,还可以将叉式支架400设置为弧形运动、旋转运动等,具体可利用导轨、摆臂等。
85.可选地,如图5所示,叉式支架400的叉头设有带轴承导丝器430,丝束通过带轴承导丝器430绕经叉式支架400设置。在丝束绕经叉式支架400、叉式支架400上行的过程中,在卷绕机900至下导盘300之间的丝束长度随着上行而递增,通过带轴承导丝器430有利于丝束与叉式支架400间的相对移动。
86.为了丝束绕经叉式支架400的叉头且与叉式支架400围合形成穿孔区域410,叉式支架400处于图5和图6所示的较简洁形式,还可以设置成树杈形、十字形、y形等。
87.如图6所示,叉式支架400的部分杆件呈弧形设置,与上导盘200的圆形匹配。
88.可选地,如图1和图3所示,新型纺丝卷绕装置包括上导盘安装机构500,上导盘安装机构500包括上导盘支撑横梁510、上导盘过渡板520、直线导轨530、推出气缸540以及上导盘座板550,上导盘支撑横梁510固定于框架100,上导盘过渡板520安装于上导盘支撑横
梁510上,直线导轨530固定于上导盘过渡板520上,推出气缸540固定于上导盘过渡板520上,上导盘座板550滑设于直线导轨530,上导盘座板550且与推出气缸540的活塞杆连接。其中,上导盘200安装于上导盘电机210的电机轴,上导盘电机210安装于上导盘座板550,以在丝束随叉式支架400上移后驱动上导盘200移入穿孔区域410将丝束挂载在上导盘200上。
89.上述通过控制推出气缸540的动作,驱动上导盘座板550在直线导轨530上作直线运动,进而控制上导盘座板550上的上导盘电机210、上导盘200作直线运动,以实现上导盘200可移动地固定于框架100,具体为驱动上导盘200移动至穿孔区域410,将叉式支架400下移,即可将丝束挂载在上导盘200上。
90.可选地,如图3所示,推出气缸540通过万向接头560与上导盘座板550连接,保证上导盘200推出顺畅、不卡顿。
91.可选地,如图2和图4所示,新型纺丝卷绕装置包括下导盘安装机构600,下导盘安装机构600包括下导盘过渡板610,下导盘过渡板610固定于框架100,下导盘300安装于下导盘电机310的电机轴,下导盘电机310安装于下导盘过渡板610,以实现下导盘300固定于框架100。
92.可选地,如图3和图6所示,上导盘安装机构500还设有限位组800,限位组800包括固定于直线导轨530一端的限位块820,以及中空的定位柱811、弹性件812与顶珠813的组合。
93.其中限位块820设置于直线导轨530一端,具体为叉式支架400上移到位时直线导轨530靠捡叉式支架400的一端。可以理解的是不限制于非要设置于端点。通过限位块820在推出气缸540动作时对上导盘200底板的移动起到限位作用。
94.在定位柱811、弹性件812与顶珠813的组合中,定位柱811底端固定于上导盘过渡板520,定位柱811顶端与上导盘200底板相接。弹性件812呈压缩状态设置,弹性件812沿竖向布置,弹性件812内设于定位柱811。顶珠813内设于定位柱811,顶珠813与弹性件812的顶部相接,顶珠813与上导盘200底板的底侧的凹槽配合,以在推出气缸540动作时限位上导盘200底板。通过定位柱811、弹性件812与顶珠813的配合,在上导盘200移动到位时,顶珠813在弹性件812的弹力下顶入上导盘200底板的底侧凹槽中,对上导盘200移动起到辅助限位作用。
95.上述限位块820,以及中空的定位柱811、弹性件812与顶珠813的组合,共同实现对上导盘200移动的限位。
96.可选地,如图1和图2所示,框架100包括主要的竖向布置的立柱110,以及横向布置的均与立柱110固定连接的第一横梁121、第二横梁122与第三横梁123,横梁将多个立柱110固定。第一横梁121还连接有竖向的竖杆140,竖杆140用以提供下导盘300的安装位置,具体为下导盘安装机构600中下导盘过渡板610的固定位置。
97.其中,框架100还包括第一托脚131和第二托架,第一托脚131一端与第一横梁121固定、另一端与驱动叉式支架400移动的驱动机构420固定连接,第二托脚132一端与第二横梁122固定,另一端与驱动叉式支架400移动的驱动机构420固定连接,通过第一托脚131和第二托脚132实现驱动机构420的固定。
98.第二横梁122、第三横梁123优选设置于框架100的顶部。请参照图1至图3,上导盘安装机构500中的上导盘支撑横梁510固定于第二横梁122和第三横梁123。
99.可选地,如图1、图2和图4所示,下导盘安装机构600还包括罩壳620,罩壳620固定安装于下导盘过渡板610,罩壳620罩设于下导盘电机310,下导盘电机310的电机轴穿设于罩壳620,下导盘300外设于罩壳620,罩壳620还安装有预网络器621和切吸丝器622,丝束依次绕经切吸丝器622、预网络器621、下导盘300、叉式支架400以及卷绕机900的移动导丝器。通过罩壳620安装切吸丝器622于预网络器621,以及防护下导盘电机310,合理利用空间。
100.在本实施例中,上丝沿着正常纺丝丝道上行,不和丝道产生交叉。
101.实施例2
102.请参照图1至图4,基于实施例1的新型纺丝卷绕装置,本实施例提供一种新型纺丝卷绕装置包括平行度调节机构700,平行度调节机构700包括上导盘调节组710和下导盘调节组730。
103.具体地,请参照图1至图3,上导盘调节组710包括第一上导盘托架711、第一上导盘安装板712、多个第一调节件713以及至少一个第一固定螺钉714。
104.第一上导盘托架711沿水平设置且与上导盘200的盘面垂直,第一上导盘托架711固定于上导盘支撑横梁510上。第一上导盘安装板712沿水平设置且与上导盘200的盘面垂直,第一上导盘安装板712设于第一上导盘托架711远离上导盘支撑横梁510的一侧,与直线导轨530和推出气缸540固定连接。如图3所示,上导盘过渡板520包括第一上导盘托架711和第一上导盘安装板712。第一调节件713包括固定于第一上导盘托架711下侧面的第一螺帽713a以及与第一螺帽713a配合的第一调节螺钉713b,第一调节螺钉713b与第一上导盘托架711螺纹连接且一端与第一上导盘安装板712相接。第一固定螺钉714与第一上导盘托架711和第一上导盘安装板712螺纹连接。
105.在本方案中,第一上导盘托架711、第一上导盘安装板712均沿水平布置,且与上导盘200的盘面垂直,如图3所示,通过固定的第一螺帽713a以及与第一螺帽713a配合的第一调节螺钉713b,在第一上导盘托架711固定的情形下可以调整第一上导盘安装板712的姿态,以调整处于一上一下的上导盘200、下导盘300的平行度。并于调整后通过第一固定螺钉714实现相对固定。
106.请参照图1、图2和图4,下导盘调节组730包括第二下导盘托架731、第二下导盘安装板732、多个第二调节件733以及至少一个第二固定螺钉734。
107.第二下导盘托架731沿竖向设置且与下导盘300的盘面垂直,第二下导盘托架731固定于框架100。第二下导盘安装板732沿竖向设置且与下导盘300的盘面垂直,第二下导盘安装板732设于第二下导盘托架731远离框架100的一侧,第二下导盘安装板732与下导盘电机310固定连接。如图4所示,下导盘过渡板610包括第二下导盘托架731和第二下导盘安装板732。
108.第二调节件733包括固定于第二下导盘托架731一竖侧的第二螺帽733a以及与第二螺帽733a配合的第二调节螺钉733b,第二调节螺钉733b与第二下导盘托架731螺钉连接且一端与第二下导盘安装板732相接。第二固定螺钉734与第二下导盘托架731和第二下导盘安装板732螺纹连接。
109.在第二下导盘托架731固定的情形下,通过固定的第二螺帽733a以及与第二螺帽733a配合的第二调节螺钉733b,调整第二下导盘安装板732的空间姿态,以调整图1中前后方向的平行度,调整下导盘300、上导盘200处于同一竖向面中。并于调整后通过第二固定螺
钉734实现固定。
110.通过上述上导盘调节组710和下导盘调节组730实现上导盘200、下导盘300于图1中前后、上下方向的平行度调整。
111.更多地,本实施例还公开上导盘调节组710、下导盘调节组730分别单独设置在装置中的方案。
112.通过本实施例的平行度调节,大大降低零件加工难度,提高材料利用率。
113.实施例3
114.请参照图10至图15,基于实施例1的新型纺丝卷绕装置,以及与实施例2的新型纺丝卷绕装置相比,本实施例提供一种新型纺丝卷绕装置包括平行度调节机构700,平行度调节机构700包括上导盘调节组710和下导盘调节组730。
115.如图10和图12所示,上导盘调节组710包括第三上导盘托架721、第三上导盘安装板722、多个第三调节件723以及至少一个第三固定螺钉724。
116.第三上导盘托架721沿竖向布置且与上导盘200的盘面平行,第三上导盘托架721底端与上导盘座板550固定连接,第三上导盘托架721与上导盘电机210间隔设置。第三上导盘安装板722沿竖向布置且与上导盘200的盘面平行,第三上导盘安装板722设于第三上导盘托架721一侧,第三上导盘安装板722与上导盘电机210固定连接。
117.第三调节件723包括固定于第三上导盘安装板722远离第三上导盘托架721的一侧的第三螺帽723a,以及与第三螺帽723a配合的第三调节螺钉723b,第三调节螺钉723b与第三上导盘安装板722螺纹连接且一端与第三上导盘托架721相接。第三固定螺钉724与第三上导盘托架721和第三上导盘安装板722螺纹连接。
118.第三上导盘托架721和第三上导盘安装板722均沿竖向布置,且与上导盘200的盘面平行。在第三上导盘托架721固定于上导盘座板550的情形下,通过第三螺帽723a以及与第三螺帽723a配合的第三调节螺钉723b,调整第三上导盘安装板722的空间位置及姿态,从而调整上导盘200的空间位置及姿态,并在调整后通过第三固定螺钉724进行固定。本方案中通过多个第三调节件723,可以实现上导盘200与下导盘300在两个方向的平行度调整,以图10举例,分别为一上一下的上下方向的平行度,以及一左一右的左右方向的平行度。
119.可选地,如图13所示,上导盘调节组710采用四个第三调节件723,并且四个第三调节件723沿矩形的四角布置,该矩形的上下两边沿水平设置。本处举例说明,结合图12和图13,当调整上方的两个第三调节件723、使对应第三调节螺钉723b顶出上导盘200安装板,而下方两个第三调节件723不变,即可实现图12中上导盘200安装板的微偏转。
120.请参照图10、图11、图14和图15,下导盘调节组730包括第四下导盘托架741、第四下导盘安装板742、多个第四调节件743以及至少一个第四固定螺钉744。
121.第四下导盘托架741沿竖向布置且与下导盘300的盘面平行设置,第四下导盘托架741与框架100固定连接,第四下导盘托架741与下导盘电机310间隔设置。第四下导盘安装板742沿竖向布置且与下导盘300的盘面平行设置,第四下导盘安装板742设于第四下导盘托架741一侧,第四下导盘安装板742与下导盘电机310固定连接。
122.第四调节件743包括固定于第四下导盘安装板742远离第四下导盘托架741的一侧的第四螺帽743a,以及与第四螺帽743a配合的第四调节螺钉743b,第四调节螺钉743b与第四下导盘安装板742螺纹连接且一端与第四下导盘托架741相接。第四固定螺钉744与第四
下导盘托架741和第四下导盘安装板742螺纹连接。
123.在第四下导盘托架741与框架100固定的情形下,通过第四螺帽743a以及与第四螺帽743a配合的第四调节螺钉743b,调整第四下导盘安装板742的空间位置及姿态,并在调整后通过第四固定螺钉744实现固定。如图14和图15所示,可选地,下导盘调节组730也可选沿矩形四角布置的四个第四调节件743的方案。与上述上导盘调节组710的调节一致,通过下导盘调节组730可以对下导盘300的空间位置及姿态进行调整,进而调整上导盘200与下导盘300的平行度。
124.更多地,本实施例还公开上导盘调节组710、下导盘调节组730分别单独设置在装置中的方案。
125.通过本实施例的平行度调节,大大降低零件加工难度,提高材料利用率。
126.实施例4
127.请参照图7至图9以及图16,基于实施例1、实施例2或实施例3的新型纺丝卷绕装置,本实施例提供一种纺丝卷绕方法,包括:
128.采用吸枪吸住丝束绕过下导盘300经叉式支架400到卷绕机900的移动导丝器;
129.叉式支架400上行至上导盘200位置处;
130.上导盘200移动至叉式支架400与丝束形成的穿孔区域410中;
131.叉式支架400下行,丝束挂载在上导盘200;
132.卷绕机900的移动导丝器推至正常纺丝位置,进行生头。
133.通过纺丝卷绕方法,保障足够包角,保证能在卷绕机900的最外侧挂丝,从而如图7和图8所示,在对上导盘200挂丝时无需先将移动导丝器推到最里面,待丝束到上导盘200后再将移动导丝器拉出来挂丝,大大减少生头时间,减少废丝量。而且驱动叉式支架400上行不存在大负载,可采用简易式驱动机构420,有利于降低成本。通过本方法使得挂丝操作更简单,效率更高。
134.尽管已描述了本发明的优选实施例,但本领域内的技术人员一旦得知了基本创造性概念,则可对这些实施例作出另外的变更和修改。所以,所附权利要求意欲解释为包括优选实施例以及落入本发明范围的所有变更和修改。
135.显然,本领域的技术人员可以对本发明进行各种改动和变型而不脱离本发明的精神和范围。这样,倘若本发明的这些修改和变型属于本发明权利要求及其等同技术的范围之内,则本发明也意图包含这些改动和变型在内。