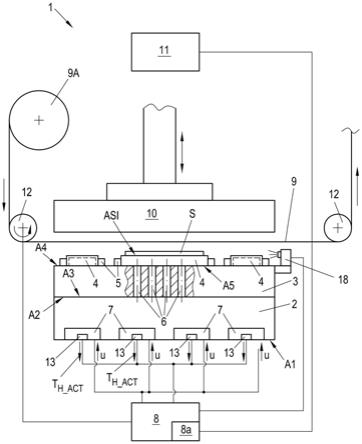
1.本发明涉及一种用于将金属箔压印至基板上的热箔压印机器,所述压印机器包括具有第一表面和相对的第二表面的加热板、用于加热所述加热板的至少一个区域的至少一个加热装置、用于至少在所述加热板的区域中测量所述加热板的温度的至少一个温度传感器以及具有第五表面和相对的压印界面表面的至少一个压印板,其中所述压印板的第五表面附接至所述加热板的第二表面,其中所述压印板界面表面被构造成用于布置所述基板,所述金属箔要借助于所述压印机器的压印元件压印至所述基板上。本发明进一步涉及一种用于确定构件的第二表面的不可测量的温度的方法。
背景技术:2.热箔压印机器通常被用来在相对高的温度和适当的压力下将箔(优选地由金属制成)印刷至基板上。热箔压印机器基本上由加热板、附接至其的安装板以及可以安装至所述安装板上的一个或多个热压印板组成。可以调节所述一个或多个热压印板的数量、尺寸和安装位置,以便执行不同的特定的箔压印操作。在每个压印板上,提供用于布置所述基板的压印界面表面,金属箔要通过压印头压印至所述基板上。在所述热箔压印机器的操作期间,所述加热板通过加热装置(例如电阻加热器)加热。因此,通过从所述加热板经由所述安装板和所述压印板的热传导使每个压印界面表面的温度升高至某一操作温度。
3.可以在所述安装板的外边缘处额外地固定一组吹气喷嘴,以便避免在每次压印过程结束时所述基板粘附于所述压印界面上。为了获得令人满意的压印质量,至关重要的是,无论环境温度、吹气喷嘴的吹气强度、操作速度以及热压印的面积如何,将所述压印界面温度维持于优选的恒定值。否则,由于基板上的成品金属箔的不希望的劣化,可能导致较差的压印质量。然而,由于带有在压印过程期间覆盖所述压印界面表面的所述基板和所述压印单元的压印过程的性质,不可获得对所述压印界面表面的直接温度测量,这使得难以实现用于将所述界面温度控制至期望温度的闭环控制系统。
4.为了克服这个缺点,已知对于所述压印界面表面的给定的期望温度将所述加热板加热至预设的升高温度,其中所述升高温度的值从查找表获得,在所述查找表中对于不同的条件(例如,各种压印界面表面温度、各种区域、各种处理速度、各种环境温度、等等)存储所述加热板与所述压印界面表面之间的稳态温度差。
5.然而,传统的查找表方法具有许多限制,例如,没有可用的动态温度差,而可用的动态温度差是实现适当的温度控制性能所需要的。因此,在稳态条件之前的瞬态加热过程期间,可能导致低效率的加热和大的温度确定误差。进一步,为了获得均匀的温度分布(在所述温度分布下获得查找表),完全地激发所述加热板的所有可用的加热区,而与安装于所述安装板上的压印板的数量无关。因此,很大一部分输入能量将被浪费,特别是当多个压印板聚集在一个或两个加热区的区域中时。此外,环境温度、操作速度、所安装的压印板的数量以及此外由来自吹气喷嘴的气流所引起的强制对流可能在相对较宽的范围内变化。为了确保查找表方法尽可能准确,需要付出巨大的努力,并且因此需要大量的时间来在不同的
操作条件下进行多次测试,以创建合适的数据库。
技术实现要素:6.因此,本发明的第一个目的是提供一种热箔压印机器,所述热箔压印机器容许在变化的条件下也提高压印质量。第二个目的是提供一种用于确定构件的表面的不可测量的温度的方法。
7.根据本发明,利用一种热箔压印机器实现第一个目的,所述热箔压印机器包括用于将所述压印界面表面的温度控制至预定的期望温度的控制单元,其中所述控制单元被构造成从所述加热板的至少一个温度传感器接收所述加热板的至少一个实际温度并且向所述至少一个加热装置提供操纵变量,其中所述压印机器进一步包括状态观测器,用于基于所述加热板与所述压印板之间的热传递的至少一个基于物理学的分析模型估计所述至少一个压印板的压印界面表面的实际温度,并且其中所述控制单元进一步包括反馈控制器,用于基于所述预定的期望温度以及所述压印界面表面的、由所述状态观测器提供的估计的实际温度来计算所述至少一个加热装置的操纵变量。
8.优选地,所述压印机器进一步包括布置于所述加热板与所述压印板之间的安装板,所述安装板具有附接至所述加热板的第二表面的第三表面,以及相对的第四表面,所述压印板的第五表面附接至所述相对的第四表面上。因此,例如可以使用呈蜂窝板或等等的形式的安装板,这有助于例如使用合适的安装支架安装所述一个或多个压印板。
9.在有利的实施例中,所述控制单元进一步包括前馈控制器,用于基于所述至少一个基于物理学的分析模型从所述压印界面表面的预定的期望温度计算前馈控制值。这样,所述反馈控制器仅仅需要调节较小的误差,这提高控制性能。
10.可能进一步有益的是,所述状态观测器包括优选地呈pid控制器的形式的观测器补偿器,用于基于可用的温度测量值校正所述至少一个压印板的压印界面表面的估计的实际温度,其中所述可用的温度测量值至少包含所述加热板的、用所述至少一个温度传感器测量的实际温度和/或环境温度。
11.优选地,所述基于物理学的分析模型为包括分布参数模型和集总参数模型的混合模型,其中在优选实施例中,所述分布参数模型为本征函数展开模型并且所述集总参数模型为热阻抗电路模型。由此,为所述加热板的加热装置(一个或多个)的局部控制输入与受到各种热通量干扰的压印界面表面温度之间的关系提供实时的有能力的并且因此在计算上高效的模型,这使得能够实现在线温度估计并且因此实现所述压印界面表面的良好的温度控制性能。
12.有利的是,在所述混合模型中,所述至少一个加热板、优选地设置的至少一个安装板和所述至少一个压印板各自沿着主轴线分成多个层,所述主轴线优选地垂直于所述第一表面、第二表面、第三表面、第四表面、第五表面或界面表面中的一个,其中所述分布参数模型计算所述多个层中的每一个层中的温度分布,并且其中所述集总参数模型计算所述多个层之间的、沿所述主轴线的方向的热通量。因此,作为压印界面表面的瞬态温度的主要影响因素的平面热扩散和沿着所述主轴线的热传导首先可以被单独地公式化,然后可以组合起来形成所述混合模型。
13.进一步优选的是,所述混合模型为包括前向路径和反馈路径的闭环模型,其中所
述分布参数模型在所述前向路径中实现并且所述集总参数模型在所述反馈路径中实现。因此,提供一种模型,所述模型在物理上是直观的并且代表热传递的固有结构。
14.根据本发明,利用一种方法实现第二目的,所述方法包括测量所述构件的第一表面的实际温度,所述第一表面与所述第二表面相间隔、优选地与所述第二表面相对,以及使用所述第一表面与所述第二表面之间的热传递的至少一个基于物理学的分析模型基于所述第一表面的测量的实际温度估计所述第二表面的实际温度,其中包括分布参数模型和集总参数模型的混合模型被用作所述基于物理学的分析模型。
15.优选地,所述方法进一步包括通过以下步骤将所述构件的第二表面的温度控制至预定的期望温度:利用反馈控制器基于所述第二表面的估计的实际温度和所述第二表面的预定的期望温度计算加热装置的操纵变量,以及使用计算的操纵变量利用所述加热装置加热所述构件的第一表面。这样,所述估计的实际温度可有利地被用作为反馈控制中的实际值。
16.根据本发明所述的方法可以有利地被用于确定和/或控制构件的表面的不可测量的温度,所述构件的表面优选地为热箔压印机器的压印板的压印界面表面、热密封机器的加热单元的加热表面、半导体生产中的晶片的表面或电子装置的电子构件的热临界表面。
附图说明
17.下面参考图1至图4更详细地解释说明本发明,图1至图4示出本发明的示例性的、示意性的且非限制性的有利实施例,其中:
18.图1示出热箔压印机器的基本构件,
19.图2示出用于温度控制的控制方案,
20.图3示出用于温度估计的混合模型,
21.图4示出用于描述分析热传递模型的加热板。
具体实施方式
22.图1示出热箔压印机器1的示意性示例。由于热箔压印机器的结构和操作在本领域中为众所周知的,因此仅仅示出与本发明相关的那些构件。热箔压印机器1包括加热板2,所述加热板2例如可以布置于基座结构上,为了简单起见,所述基座结构未示出。加热板2可以例如由刚性材料制成,例如具有合适的导热系数的金属或等等,例如钢合金。加热板2可以为正方形、矩形或任何其它形状,并且可以包括第一表面a1和相对的第二表面a2。优选地,加热板2在相对的第一表面a1、第二表面a2之间具有均匀的厚度。加热板2包括例如呈一个或多个电阻加热器的形式的至少一个加热装置7,所述加热装置7可以以网格图案布置于加热板2的第一表面a1上。通过加热装置7(一个或多个),加热板2可以被加热至一定的温度。进一步,一个或多个温度传感器13布置于加热板2上,用于测量加热板2的温度。例如,一个温度传感器13可以设置于每个加热装置7的区域中,用于测量加热板2的第一表面a1的温度,如图1中所示。
23.在加热板2的第二表面a2的顶部上,可以布置可选的安装板3,所述安装板3也可以由具有合适的导热系数的合适的刚性材料制成,例如钢合金。同样,安装板3可以具有正方形、矩形、圆形或任何其它形状。安装板3包括第三表面a3和相对的第四表面a4,其中第三表
面a3与加热板2的第二表面a2接触。安装板3的第四表面a4和加热板2的第一表面a1彼此相背。安装板3继而在第三表面a3和第四表面a4之间具有优选的均匀的厚度,并且可以基本上通过比如螺钉或支架(未示出)的任何合适的安装装置固定于加热板2上。安装板3被构造成用于安装至少一个压印板4,但是当然也可以同时在安装板3上安装多个压印板4,如图1中以虚线示出的。然而,安装板3仅仅为可选的,并且至少一个压印板4也可以直接地附接至加热板2。在这种情况下,用于安装压印板4的合适的紧固元件设置于加热板2上。因此,加热板2既用作用于加热的加热板,又用作用于安装一个或多个压印板4的安装板。在下文中,将仅仅参考一个压印板4来描述本发明。
24.至少一个压印板4也可以由具有合适的导热系数的刚性材料制成,例如钢合金。同样,压印板4可以具有正方形、矩形、圆形或任何其它形状。压印板4包括第五表面a5和相对的压印界面表面asi。假设根据图1中所示的示例,将单独的安装板3布置于加热板2与压印板4之间,则第五表面a5与安装板3的第四表面a4接触。然而,在没有在压印机器1中设置单独的安装板3的情况下,压印板4的第五表面a5附接至加热板2的第二表面a2。压印板4继而在第五表面a5与压印界面表面asi之间具有优选的均匀的厚度。压印板4可以例如通过合适的安装支架5固定于安装板3上,如图1中所示。为了能够快速且简单地将一个或多个压印板4也安装于安装板3上的不同位置处,安装板3可以例如具有带有多个凹槽的蜂窝构造。图1中所示的示例性安装板3包括多个孔6,所述孔6连接相对的表面a3、a4并且优选地均匀地分布于安装板3上以便实现蜂窝状构造。
25.在压印板4的顶部,可以布置基板s,将通过借助于压印机器1执行压印过程将箔9压印至所述基板s上。多种材料组合可以被用于基板s和箔9。比如纸、纸板、塑料、皮革、木材等等的材料可以被用于基板s。基本上所有适合于与所使用的基板s的材料结合的金属和塑料都可以被用作箔9的材料。然而,主要使用金属箔,例如金、银、青铜、铜或不同的金属合金。基板s可以例如松散地布置于压印板4的压印界面表面asi上,或者可以通过任何合适的固定元件(一个或多个)固定,然而这些固定元件需要具有比基板s稍小的厚度。
26.可以例如以一个或多个匝圈9a的形式提供箔9,箔9被缠绕于所述匝圈9a上。箔9可以例如跨一个或多个固定的或可调节的辊12而从线圈9a被供应至压印机器的处理区域中的基板s。在一个简单的实施例中,可以例如通过手动地展开和移动箔9而手动地供应箔9。然而,为了实现更高的生产率,例如通过合适的驱动装置将箔9自动地进给至处理区域可能是有利的。例如,可以通过电动马达(未示出)驱动匝圈9a和/或辊12。
27.热箔压印机器1可以进一步包括至少一个压印头10,所述压印头10通常可运动地布置于压印板4上方,如图1中用双箭头所示出的。压印头10可以由合适的材料制成,例如类似于压印板4、安装板3或加热板2的金属。为了执行压印过程,压印头10可以朝向基板s运动以便将箔9压制至基板s上,由此将特定的压印力施加至箔9和基板s上。在压印过程期间,基板s通过加热板2所生成的并且从加热板2经由安装板3传导至压印板4的热量被加热至一定的期望的压印温度。在压制力和加热板2所提供的热量的作用下,箔9被镀覆至基板s上。
28.在一定的处理时间之后,压印头10回撤,并且包含附着的箔9的成品基板s可以被移除。基板s的所需的处理温度当然取决于箔9的材料和基板s本身的材料,并且通常在100℃与300℃之间的范围内。对于给定的条件(基板s的材料和形状以及箔9的材料),压印界面表面asi的所需的温度被假定为已知的,并且在下文中被指定为压印板4的界面表面asi的
期望温度t
si_d
。为了便于从压印板4移除其上压印有箔9的成品基板s,可以可选地在压印机器1中、例如在安装板3的外边缘上设置吹气喷嘴18。借助于吹气喷嘴18,可以将加压空气供应至基板s,例如优选地供应于基板s与压印界面表面asi之间。
29.为了获得压印于基板s上的箔9的特定图案,如标志、文本、等等,压印头10的表面(面对基板s)也可以以相应的方式成形。为了灵活地改变图案,可以提供具有不同图案的可互换的插入件。在简单的实施方式中,压印头10例如可以为可手动操作的,例如借助于操作杆(未示出)。然而,为了实现更高的生产率和更好的压印质量,可能有利的是,压印头由合适的驱动装置11自动地操作,例如(电动)机械地或(电动)液压地操作。因此,可以达到一致的处理速度(其基本上对应于压制动作的持续时间)和一致的压印力,这产生恒定的压印质量。
30.为了控制热箔压印机器1,在热箔压印机器1中提供例如呈合适的基于微处理器的硬件和/或软件的形式的至少一个控制单元8。控制单元8例如还可以包括可编程逻辑控制器(plc)、现场可编程门阵列(fpga)、专用集成电路(asic)、模拟计算机、或模拟电路。利用控制单元8,可以控制至少加热板2、特别地一个或多个加热装置7。如果压印头10例如由驱动装置11自动地驱动和/或箔9例如由辊12的驱动装置自动地供应,则控制单元8也可以被用于控制驱动装置11和/或辊12的驱动装置,如图1中的连接线所示。控制单元8可以例如控制箔9的进给速度、和/或压印速度、和/或压印头10的压印力。当在压印机器1中提供吹气喷嘴18时,控制单元8还可以控制吹气喷嘴18,例如由吹气喷嘴18所供应的空气的量,例如以体积流量或压力的形式来控制。为了调节压印过程的不同参数(例如,处理速度、压印界面表面asi的期望温度、压印压力、等等),用户界面8a可以设置于压印机器1中,例如设置于控制单元8中。
31.如开始所述,由于不可能对压印板4的压印界面表面asi的温度进行直接温度测量,所以控制输入迄今为止基于查找表,在所述查找表中存储加热板2的温度、特别地加热板2的第一表面a1的温度与压印板4的压印界面表面asi的温度之间的稳态相关性。然而,由于处理条件(所安装的压印板的数量、环境温度、处理速度、由吹气喷嘴18所供应的空气的温度和体积流量、等等)的变化,利用查找表方法不能充分满足高质量标准。因此,根据本发明,提供一种具有更好的性能的改进的压印机器1,如将在下面参考图2和图3所描述的。
32.根据本发明,压印机器1包括控制单元8,用于将压印界面表面asi的温度t
si
控制至预定的期望温度t
si_d
,其中控制单元8被构造成从加热板2的至少一个温度传感器13接收加热板2的至少一个实际温度t
h_act
并且向至少一个加热装置7提供操纵变量u。压印机器1进一步包括状态观测器14,用于基于加热板2与压印板4之间的热传递的至少一个基于物理学的分析模型17估计至少一个压印板4的压印界面表面asi的实际温度
33.状态观测器14可以例如以单独的构件(例如,一件硬件或软件)的形式提供,或者可以在控制单元8中实现(例如,作为软件),如图2中所示。控制单元8进一步包括反馈控制器15,用于基于预定的期望温度t
si_d
以及压印界面表面asi的、由状态观测器14提供的估计的实际温度计算至少一个加热装置7的操纵变量u,通常基于期望温度t
si_d
与估计的实际温度之间的误差。反馈控制器15可以例如包括本领域中已知的合适的控制器,
例如pid控制器或pi控制器。为了清楚起见,在图2中以简化的方式示出压印机器1,并且加热装置7和温度传感器13被显示为网格的节点,其中它们布置于加热板2的第一表面a1上。当然,加热装置7不一定需要精确地在如图所示的节点上加热加热板2,而是可以在一定区域上加热加热板2。
34.优选地,控制单元8进一步包括前馈控制器16,用于基于至少一个基于物理学的分析模型17从压印界面表面asi的预定的期望温度t
si_d
计算前馈控制值。特别地,考虑到安装于压印机器1中的多个压印板4的压印板区域(一个或多个)和安装位置(一个或多个),为压印界面表面asi上的期望的温度分布计算前馈控制值。前馈控制值是根据基于物理学的分析模型17的逆解计算的。例如,为了减少热能,期望的温度分布可以包括一个或多个压印板4的压印界面表面asi(一个或多个)的区域(一个或多个)的特定的期望温度t
si_d
,并且可以进一步包括一个或多个压印板4的压印界面表面asi(一个或多个)的区域(一个或多个)外部的区域(一个或多个)的期望温度。
35.尽管反馈控制器15、状态观测器14和前馈控制器16在图2中所示的控制结构中被表示为单独的构件,但是对于本领域中的技术人员而言显而易见的是,它们当然也可以以软件的形式在控制单元8中实现。进一步,应当理解的是,基于物理学的分析模型17不是图2的控制回路的物理构件(用虚线表示),而是代表对压印机器1的热行为的数学描述,其充当设计状态观测器14和可选的前馈控制器16的基础。基于物理学的分析模型17例如可以以合适的形式在状态观测器14和可选的前馈控制器16二者中实现。因此,图2中所示的代表基于物理学的分析模型17的方框仅仅为了清楚起见而被示出。
36.由于存在压印机器1的基于物理学的分析模型17,现在可以实现对压印界面温度t
si
的反馈控制,因为可以相对精确地估计压印板4的压印界面表面a
si
的实际温度尽管没有直接测量可用。
37.为了校正压印板4的压印界面表面asi的估计的实际温度可以可选地在压印机器1中提供观测器补偿器19,所述观测器补偿器19特别地在状态观测器14中优选地以pid控制器或任何其它合适的控制器的形式实现。所述校正基于可用的温度测量值t
i_act
,优选地基于加热板2的、用至少一个温度传感器13测量的实际温度t
h_act
。
38.优选地,基于物理学的分析模型17为包括分布参数模型dpm和集总参数模型lpm的混合模型,将参考图3对其进一步描述。在混合模型中,加热板2、(可选的)安装板3以及压印板4各自沿着主轴线分成多个层lai。所述主轴线优选地垂直于第一、第二、第三、第四、第五表面a1-a5或界面表面asi中的至少一个,例如为图1中的竖直轴线。借助于分布参数模型dpm,可以基于输入至输入层la
ip
的热通量输入hfi计算多个层lai中的每一个层中的温度分布。借助于集总参数模型lpm,可以计算多个层lai之间的沿着主轴线的热通量。根据图3中所示的示例,压印机器1被分成输入层la
ip
、两个中间层lam以及输出层la
op
,但是当然可以选择具有更多或更少层的另一种细分,然而,需要至少两个层(输入层la
ip
和输出层la
op
)。输入层la
ip
对应于加热板2的第一表面a1,加热装置7布置于所述第一表面a1上,加热装置7提供热通量输入hfi。输出层la
op
对应于压印板4的压印界面表面asi,要估计所述压印界面表面asi的实际温度由于加热装置7(一个或多个)的分段的加热区,热通量输入hfi被
局部地施加于输入层la
ip
上,并且由于压印板4(一个或多个)的有限的操作区域(一个或多个),干扰会不均匀地分布于输出层la
op
上。为了解决局部边界条件以及加热区之间的热耦合对所产生的高度不均匀的温度分布的影响,如果仅仅集总参数模型将被用作用于对压印机器1的热传递的数学描述的单一模型,则将需要大量的模型元素(比如电阻r、电容c等等-参见下文)。然而,这将导致大量的计算时间,就优选的实时温度估计/控制而言,这是不希望的。另一方面,仅仅使用分布参数模型解析地求解瞬态三维温度场也将非常困难,同时数值计算技术(比如,有限元方法)也将需要巨大的计算量。因此,为了分别实现足够低的计算量、快速的计算时间以及同时实现足够的计算精度,在本发明中以混合模型的形式使用集总参数模型和分布参数模型的组合。
39.在优选实施例中,分布参数模型dpm为本征函数展开模型并且集总参数模型lpm为热阻抗电路模型。利用热阻抗电路模型,对各个层之间的动态关系进行建模,其中每一层lai被公式化为电路节点(满足基尔霍夫(kirchhoff)节点定律),并且相邻层lai之间的热动态被描述为热电阻r和热电容c,如图3中所示。对应于压印板4的压印界面表面asi的输出层la
op
上的局部热通量干扰也被建模为局部热电阻r。混合模型优选地被建模为包括前向路径和反馈路径的闭环模型,其中前向路径基于输入至输入层la
ip
的给定的热通量输入hfi描述每一层lai中的层温度分布,而反馈路径考虑给定的温度分布的传导的热通量(层lai之间)。分布参数模型dpm在前向路径中实现并且集总参数模型lpm在反馈路径中实现,如图3中所示。
40.当混合模型被公式化时,可以使用识别算法进行识别实验,以确定作为工作条件(例如处理速度、环境温度、吹气喷嘴的使用、等等)的函数的热通量干扰。这样的识别算法在本领域中为已知的,例如,从书籍“反向热传递:基础与应用(奥齐西克等著,2000年,书号:isbn 978-1560328384)(ozisik,m.necati et al.,2000.inverse heat transfer:fundamentals and applications,isbn 978-1560328384)”获知。利用在根据图2的控制方案中实施的混合模型,加热所述加热板2(基于提供至加热装置7的所计算的操纵变量u),以使得由于温度差产生朝向压印板4的热通量,这抵消压印界面表面asi处的变化的热通量干扰(由不同的工作条件下的压印引起),并且因此将压印界面温度t
si
维持于期望温度t
si_d
。
41.下面参考图4呈现示例性的基于物理学的分析模型17。为了简单起见,仅仅针对加热板2示出基于物理学的分析模型17。在左侧,加热板2被以用于数学描述的坐标系示出,所述坐标系的原点o在左上角。由x-轴和y-轴跨越的xy-平面对应于加热板2的第一表面a1。作为主轴线的z-轴垂直于第一表面a1,并且沿朝向加热板2的相对的第二表面a2的方向延伸。如上所述,多个加热装置7(未示出)以网格图案布置于加热板2上,每个加热装置7在图4中被表示为节点。每个加热装置7作为热源向加热板2的第一表面a1的相应的节点提供热通量输入hfi,如图4中的箭头所示。
42.加热板2在它的第二(底部)表面a2处经受热传递系数为hz的时变对流。当加热板2暴露至具有环境温度的环境时,瞬态温度分布不仅仅由具有给定的控制输入的xy-平面热扩散决定,而且还受沿z-轴的方向朝向第二表面a2流动的热通量影响。热通量输入hfi提高xy-平面中的温度,以便为沿z-轴的方向的热传导提供温度差,热通量借助于所述温度差从第一表面a1朝向第二表面a2流动,以抵消时变对流边界条件以便将第二表面a2的温度维持于一定水平(=期望温度,例如对应于整个压印机器1中的压印界面表面asi的期望温度
t
si_d
,请参见图1和图2)。
43.z-轴热传导和xy-平面热扩散对温度分布的瞬态行为的上述影响可以由优选地呈闭环模型的形式的混合模型完全表征,如上面参考图3所描述的那样。同样,前向路径描述由具有已知的热通量输入hfi的xy-平面热扩散决定的温度分布,而对于给定的温度分布和对流边界条件,负反馈解决通过z-轴热传导耗散的热通量。xy-平面热扩散优选地被描述为分布参数模型dpm,并且沿z-轴的方向的热传导优选地被描述为集总参数模型lpm、特别地被描述为阻抗电路(参见图3)。如先前在上面参考图3所描述的,在混合模型中,加热板2被分成多个层lai,其中在图4中所示的示例中仅仅使用两个层lai。第一层为对应于加热板2的第一表面a1的输入层la
ip
,并且第二层为对应于加热板2的与第一表面a1相对的第二表面a2的输出层la
op
,如图4的右侧所示。
44.在下面的示例中,首先利用本征函数展开法解析求解输入层la
ip
(xy-平面,z=0)中的温度分布。此后,将沿z-轴的方向的热传导的分析模型公式描述为热阻抗电路(参见图3),最后示出呈闭环模型的形式的组合。
45.加热板2内的温度场t
he
(t,x,y,z)的控制方程可以由方程(1a)导出,其中t
he
=t-ta并且ta为环境温度。
[0046][0047]
方程(1b)示出x-轴、y-轴和z-轴的边界条件bc。
[0048][0049]
在方程(1c,1d)中示出时间t=0的初始条件。
[0050]
t
he
(0,x,y,z)=0其中α2=κ/ρc
p
ꢀꢀ
(1c,1d)
[0051]
在方程(1c,1d)中,α为热扩散系数,hn和hz分别为xy-平面和z-轴上的热传递系数,κ为导热系数,ρ为密度,并且c
p
为加热板2的比热容。x、y、z为加热板2的长度、宽度和高度(参见图4)。方程(1b)中的边界输入g(t,x,y,0)被表示为方程(2a),其中控制输入向量u(t)的元素ui被应用至第i个加热区(例如,对于根据图4的示例中所示的、对应于加热装置7的十二个节点,i=1,2,
…
12),其中它的加热区域gi(x,y)由长度li、宽度wi和在xy-平面上的安装位置li+li/2、wi+wi/2表征:
[0052]
其中u(t)=[... ui(t) ...]
t
ꢀꢀ
(2a,2b)
[0053]
[0054]
为了说明分段的边界控制输入对xy-平面温度分布和z-轴热传导的影响,假设控制方程(1a-1c)的解采用方程(3a)的形式,其中t
hei
为输入层la
ip
在z=0处由第i个加热区贡献的瞬态温度分布并且t
he
(t,z)表征z-轴热传导动态:
[0055][0056][0057][0058]
其中初始条件t
hei
(0,x,y)=0
ꢀꢀ
(3d)
[0059]
利用本征函数展开模型,层温度场控制方程(3b-3d)的解可以根据方程(4a)被导出为时空分离形式:
[0060]
其中θ(t,x,y)=t
hei
(t,x,y,0)
[0061]
(4a)
[0062]
其中
[0063]
以及
[0064]
在方程(4a-4c)中,φ
mn
(x,y)为具有时间相关系数的层温度分布的空间谐波核函数。类似地,分段控制输入也可以根据方程(5a-5e)被公式化为一系列空间谐波核函数:
[0065][0066]
其中其中m,n≠0
ꢀꢀ
(5b,5c)
[0067]
其中n≠0
[0068]
(5d,5e)
[0069]
当方程(4a)和(5a)被代入方程(3b)中时,t
hei
可以被表示为:
[0070]
其中
[0071][0072]
在方程(6b)中,τ
mn
为第(m,n)个空间谐波的热扩散时间常数。它随着增大的热扩散系数α、谐波次数(m,n)以及减小的轮廓尺寸(x,y)而减小。当方程(6c)与方程(3a)组合时,根据方程(7a,7b)描述由所有加热区贡献的温度分布,其中u
mn
表征边界控制输入的瞬态空间分布:
[0073][0074][0075][0076]
利用输入层la
ip
中的分别由u
mn
(t)和表征的局部热通量输入hfi和所得到的温度分布,描述xy-平面热扩散的动态的前向路径传递函数(参见图3)可以从方程(7a)被导出,如方程(7c)中所示,其中s为拉普拉斯算子。
[0077]
使用图3中所示的热阻抗电路,具有已知的温度分布的耗散热通量的传递函数可以从方程(8a,8b)获得。计算控制输入的温度分布的闭环传递函数u
mn
(s)可以根据方程(8c,8d)定义。
[0078]
其中τ
he
=c
he
(r
he
+1/hz)
ꢀꢀ
(8a,8b)
[0079]
其中
[0080]
在方程(8a-8d)中,c
he
为加热板2的z-轴热电容,并且r
he
为加热板2的z-轴热电阻。τ
he_mn
为综合时间常数,其说明xy-平面热扩散时间常数τ
mn
以及z-轴热传导时间常数τ
he
。对于不同的时间常数比τ
he
/τ
mn
,方程(8c,8d)提供输入层la
ip
在z=0处的温度分布的动态特征。基本上可以考虑以下两种情况。在情况1(τ
mn
》》τ
he
或τ
he_mn
≈2τ
he
)中,z-轴热传导的动态与xy-平面中的热扩散的动态相比相对较快,并且因此控制输入能量主要转移至具有时间常数2τ
he
的层z=z中。在情况2(τ
mn
《《τ
he
或τ
he_mn
≈2τ
mn
)中,z-轴热传导的动态与xy-平面中的热扩散的动态相比相对较慢,并且控制输入能量主要被用于具有时间常数2τ
mn
的xy-平面热扩散。
[0081]
输入层la
ip
在z=0处的瞬态(或时域)温度分布t
he
(t,x,y,0)可以根据方程(9)导出:
[0082][0083]
可以看出,方程(9)具有与方程(7a,7b)相同的形式,但是具有不同的时间常数和
更小的稳态幅度,这是因为负反馈回路消耗一些控制输入能量。如果输出层la
op
处的温度令人感兴趣,则方程(8c)可以被用来获得相对应的传递函数并且因此获得输出层la
op
处的瞬态温度分布。利用先前所示的(多层)混合模型,根据方程(9)将z-轴热传导和xy-平面热扩散的动态结合至顶层温度分布中,并且根据方程(1a,1b)-(2a,2b)将瞬态三维温度场的分析模型与局部边界条件bc公式化。
[0084]
虽然上面的分析模型是使用矩形加热板2的示例来示例说明的,但是所述原理当然也可以应用于更复杂的应用,比如具有堆叠板的三维场,就像在具有加热板2、安装板3和一个或多个压印板4的热箔压印机器1中一样(参见图1)。当然,分析模型也可以应用于非矩形构件,比如具有圆柱形或球形形状的构件,比如辊。根据本发明的用于使用分析模型、特别地所描述的闭环混合模型来估计(并且可选地控制)表面的不可测量的温度的方法的用途当然可以在各种其它技术应用中实现,在这些技术应用中,不能直接地测量感兴趣的表面温度。示例性应用为确定和/或控制热密封机器的加热单元的加热表面的表面温度,确定和/或控制半导体生产中的晶片的表面温度,或者确定(例如监控)和/或控制电子装置的电子构件的热临界表面的表面温度。