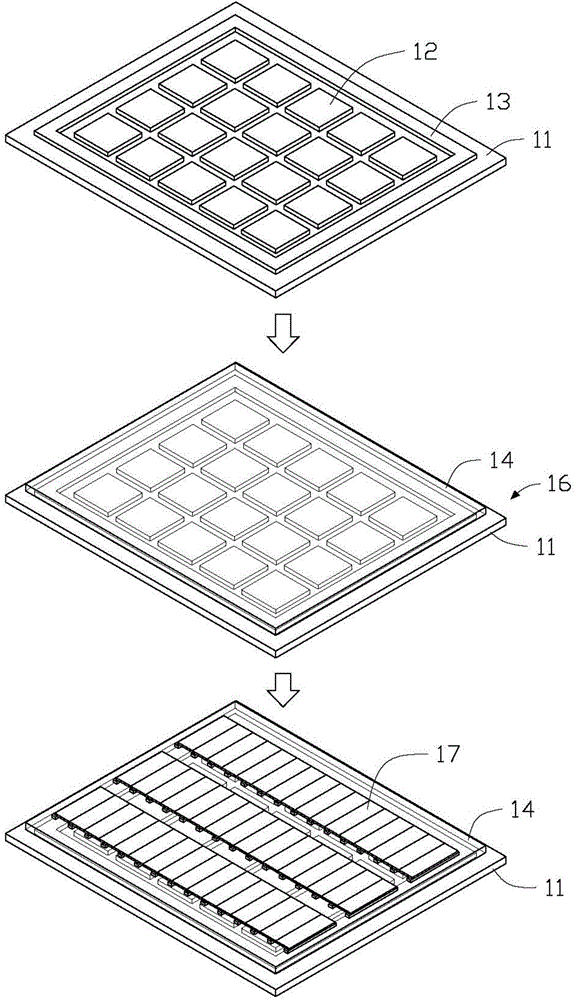
本发明涉及一种液晶显示面板制造方法。
背景技术:
:现有液晶显示面板的制造过程中,将形成TFT阵列的玻璃基板上和具有彩色滤光层的玻璃基板之间灌入液晶分子以形成液晶显示面板。然而,为了满足用户对产品更轻薄化的需求,如何使得液晶显示设备更轻薄化仍然是目前业界研究的重要课题之一。现有技术中,利用氢氟酸(HF)与玻璃产生化学反应以降低玻璃基板的厚度,以实现玻璃基板薄化。由于氢氟酸为有刺激性液体,容易对环境造成影响。同时,在处理过程中无法保证玻璃基板表面的平整性,降低了产品的良率并且成本较高。技术实现要素:有鉴于此,有必要提供一种降低制程复杂程度且有利于轻薄化的液晶显示面板制造方法。一种液晶显示面板制造方法,其包括步骤:a)第一转载板的表面形成多个第一间隔物和一个第一框体,并在第二转载板的表面形成多个第二间隔物和一个第二框体;b)在真空腔体内将第一转载板和第一基板相互吸附为一体以形成第一基板组,在真空腔体内将第二转载板和第二基板相互吸附为一体以形成第二基板组;c)在第一基板远离第一转载板的一侧形成薄膜晶体管阵列,在第二基板远离第二转载板的一侧形成彩色滤光层;d)将形成TFT阵列的第一基板组反转使得TFT阵列与彩色滤光层相对放置,并在第一基板组和第二基板组之间设置框胶及填充液晶并将二者贴合为一体;e)利用激光切割第一框体以使得第一转载板与第一基板相脱离,利用激光切割第二框体以使得第一转载板与第二基板相脱离,移除第一转载板和第二转载板以形成液晶显示面板。与先前技术相比较,本申请直接采用厚度为0.2mm的第一基板和第二基板制造液晶显示面板,通过在第一转载板承载第一基板并第二转载板承载第二基板以增强第一基板和第二基板的强度,避免第一基板和第二基板在制造过程中破损,保证了第一基板和第二基板的表面平整性并降低了制造流程的复杂程度。附图说明图1为第一实施方式之液晶显示面板制作方法之流程图。图2至图4为图1中各步骤对应结构之示意图。图5为图4中第一基板组和第二基板组沿V-V方向的剖示图。图6为图2中第二实施方式之间隔物结构之示意图。图7为图2中第三实施方式之间隔物结构之示意图。图8为第二实施方式之液晶显示面板制作方法之流程图。图9至图11为图8中各步骤对应结构之示意图。图12为图11中第一基板组和第二基板组沿XI-XI方向的剖示图。主要元件符号说明液晶显示面板制造方法S11~S15,S81-S87液晶显示面板10,70第一转载板11,71第一间隔物12,52,62,72第一框体13,73第二转载板21,81第二间隔物22,82第二框体23,83第一基板14,74第二基板24,84第一基板组16,76第二基板组26,86薄膜晶体管阵列17,77彩色滤光层27,87第一粘接框78第二粘接框88如下具体实施方式将结合上述附图进一步说明本发明。具体实施方式请一并参阅图1至图5,其为一种较佳实施方式的液晶显示面板10制造方法之流程图。图2-图4为图1所示各流程步骤相应之结构示意图,图5为图4中第一基板组16和第二基板组26沿V-V方向的剖示图。在本实施方式中,液晶显示面板10为薄膜晶体管(TFT-LCD)面板。在其他可替代实施方式中,液晶显示面板10也可为主动矩阵有机发光二极管(AMOLED)面板。步骤S11,在第一转载板11的表面形成多个第一间隔物12和一个第一框体13,并在第二转载板21的表面形成多个第二间隔物22和一个第二框体23。多个第一间隔物12位于第一框体13内,且呈矩阵排列;多个第二间隔物22位于第二框体23内,且呈矩阵排列。其中,第一间隔物12和第一框体13利用掩膜进行光刻(photolithography)而一体成型;第二间隔物22和第二框体23利用掩膜进行光刻(photolithography)而一体成型。第一框体13远离第一转载板11的表面为光滑且平坦的表面,第二框体23远离第二转载板21的表面为光滑且平坦的表面。第一间隔物12和第二间隔物22均大致呈长方体状实心结构。第一框体13和第二框体23结构相同,第一间隔物12和第二间隔物22结构相同。在本实施方式中,第一转载板11和第二转载板21为透明玻璃板。在其他可替代的实施方式中,第一间隔物12和第二间隔物22的形状可不同;第一间隔物12和第二间隔物22可呈非矩阵式排列。步骤S12,在真空腔体内将第一转载板11和第一基板14相互吸附为一体以形成第一基板组16,在真空腔体内将第二转载板21和第二基板24相互吸附为一体以形成第二基板组26。优选地,第一基板14和第二基板24的厚度为0.1~0.3mm。在本实施方式中,第一基板14和第二基板24的厚度均为0.2mm。具体地,在腔体内将第一转载板11和第一基板14对位,将腔体抽成真空以使第一转载板11和第一基板14相互吸附为一体以形成第一基板组16,并在腔体内将第二转载板21和第二基板24对位,将腔体抽成真空以使第二转载板21和第二基板24相互吸附为一体以形成第二基板组26。其中,第一框体13用于与第一转载板11及第一基板14配合在第一基板组16内形成真空;第一间隔物12用于在第一转载板11与第一基板14吸附为一体时给第一基板14提供均匀支撑力。第二框体23用于与第二转载板21及第二基板24配合在第二基板组26内形成真空。第二间隔物22用于在第二转载板21与第二基板24吸附为一体时给第二基板24提供均匀支撑力。第一基板组16外的气压大于第一基板组16内部的气压,以使得第一转载板11和第一基板14吸附为一体;第二基板组26外的气压大于第二基板组26内部的大气压,以使得第二转载板21和第二基板24吸附为一体。在本实施方式中,第一基板组16和第二基板组26分别在两个不同的腔体内完成对位结合。在其他可替代的实施方式中,第一基板组16和第二基板组26可在相同的腔体内完成对位结合。步骤S13,在第一基板14远离第一转载板11的一侧形成薄膜晶体管(thinfilmtransistor,TFT)阵列17,在第二基板24远离第二转载板21的一侧形成彩色滤光(colorfilter,CF)层27。步骤S14,将形成TFT阵列17的第一基板14组反转使得TFT阵列17与第二基板24上的彩色滤光层27相对放置,并在第一基板组16和第二基板组26之间设置框胶及填充液晶并将二者贴合为一体,从而得到位于该第一转载板11与第二转载板21之间的液晶显示面板10。步骤S15,利用激光切割第一框体13使得空气进入第一基板组16内以使得第一转载板11与第一基板14相脱离,利用激光切割第二框体23使得空气进入第二基板组26内以使得第一转载板11与第二基板24相脱离,移除第一转载板11和第二转载板21以获得该液晶显示面板10。在本实施方式中,利用激光切割第一框体13与任意相邻两个第一间隔物12之间空隙相对的位置;利用激光切割第二框体23与任意相邻两个第二间隔物22之间空隙相对的位置。如图6所示,其为第二实施方式之第一间隔物52结构。其中,第一间隔物52为圆形实心结构。如图7所示,其为第三实施方式之第一间隔物62结构。其中,第一间隔物62为中空的圆环结构。请一并参阅图8至图12,其为第二实施方式之液晶显示面板70的制造方法之流程图。图9-图11为图8所示各流程步骤相应之结构示意图,图12为图11中第一基板组76和第二基板组86沿XI-XI方向的剖示图。在本实施方式中,液晶显示面板70为薄膜晶体管(TFT-LCD)面板。在其他可替代实施方式中,液晶显示面板70也可为主动矩阵有机发光二极管(AMOLED)面板。步骤S81,在第一转载板71的表面形成多个第一间隔物72和一个第一框体73,并在第二转载板81的表面形成多个第二间隔物82和一个第二框体83。多个第一间隔物72位于第一框体73内,且呈矩阵排列;多个第二间隔物82位于第二框体83内,且呈矩阵排列。其中,第一间隔物72和第一框体73利用掩膜进行光刻(photolithography)而一体成型;第二间隔物82和第二框体83利用掩膜进行光刻(photolithography)而一体成型。第一框体73远离第一转载板71的表面为光滑且平坦的表面,第二框体83远离第二转载板81的表面为光滑且平坦的表面。第一间隔物72和第二间隔物82均大致呈长方体状实心结构。在本实施方式中,第一转载板71和第二转载板81为透明玻璃板。在其他可替代的实施方式中,第一间隔物12和第二间隔物22的形状可不同;第一间隔物12和第二间隔物22可呈非矩阵式排列。步骤S82,围绕第一框体73形成第一粘接框78,围绕第二框体83形成第二粘接框88。在本实施方式中,第一粘接框78和第二粘接框88为耐高温粘胶,其可在高温或紫外光下固化。步骤S83,在真空腔体内将第一转载板71和第一基板74相互吸附为一体以形成第一基板组76,在真空腔体内将第二转载板81和第二基板84相互吸附为一体以形成第二基板组86。优选地,第一基板14和第二基板24的厚度为0.1~0.3mm。在本实施方式中,第一基板74和第二基板84的厚度为0.2mm。具体地,在腔体内将第一转载板71和第一基板74对位结合,将腔体抽成真空以使第一转载板71和第一基板74相互吸附为一体以形成第一基板组76,并在腔体内将第二转载板81和第二基板84对位结合,将腔体抽成真空以使第二转载板81和第二基板84相互吸附为一体以形成第二基板组86。其中,第一框体73用于与第一转载板71及第一基板74配合在第一基板组76内形成真空。第一间隔物72用于在第一转载板71与第一基板74吸附为一体时给第一基板74提供均匀支撑力。第二框体83用于与第二转载板81及第二基板84配合在第二基板组86内形成真空。第二间隔物82用于在第二转载板81与第二基板84吸附为一体时给第二基板84提供均匀支撑力。当对腔体进行抽真空后,第一基板组76外的气压大于第一基板组76内部的大气压,以使得第一转载板71和第一基板74吸附为一体,同时第二基板组86外的气压大于第二基板组86内部的气压,以使得第二转载板81和第二基板84吸附为一体。然后,通过高温或紫外光照射第一基板组76和第二基板组86,使得第一粘接框78固化以提高第一转载板71和第一基板74之间的贴附紧密度;第二粘接框88固化以提高第二转载板81和第二基板84之间的贴附紧密度。本实施方式中,第一基板组76和第二基板组86分别在两个不同的腔体内完成对位结合。在其他可替代的实施方式中,第一基板组76和第二基板组86可在相同的腔体内完成对位结合。步骤S84,在第一基板74远离第一转载板71的一侧形成薄膜晶体管(thinfilmtransistor,TFT)阵列77,在第二基板84远离第二转载板81的一侧形成彩色滤光(colorfilter,CF)层87。步骤S85,将形成TFT阵列77的第一基板组76反转使得TFT阵列77与第二基板组86上的彩色滤光层87相对放置,在第一基板组76和第二基板组86之间设置框胶及填充液晶并将二者贴合为一体。步骤S86,利用激光切割第一框体73使得空气进入第一基板组76内以使得第一转载板71与第一基板74相脱离,利用激光切割第二框体83使得空气进入第二基板组86内以使得第二转载板81与第二基板84相脱离。在本实施方式中,利用激光切割第一框体73任意相邻两个第一间隔物72之间空隙相对的位置;利用激光切割第二框体83与任意相邻两个第二间隔物82之间空隙相对的位置。步骤S87,利用激光切割第一粘接框78和第二粘接框88,移除第一转载板71和第二转载板81以形成液晶显示面板70。在其他可替代实施方式中,可利用激光清除整个第一粘接框78和第二粘接框88。利用本发明提供的液晶面板制造方法直接采用厚度为0.2mm的第一基板14,74和第二基板24,84,并藉由第一转载板11,71承载第一基板14,74及第二转载板21,81承载第二基板24,84以增强第一基板14,74和第二基板24,84承载力,避免了第一基板14,74和第二基板24,84的表面平整性并降低了制造流程的复杂程度。本
技术领域:
的普通技术人员应当认识到,以上的实施方式仅是用来说明本发明,而并非用作为对本发明的限定,只要在本发明的实质精神范围之内,对以上实施例所作的适当改变和变化都落在本发明要求保护的范围之内。当前第1页1 2 3