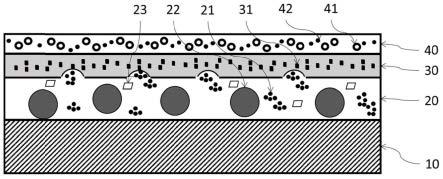
1.本发明涉及膜技术领域,具体涉及用于显示器的抗眩光减反射膜。
背景技术:2.在显示装置例如阴极射线管显示装置(crt)、等离子体显示器(pdp)、电致发光显示装置(eld)和液晶显示装置(lcd)上,减反射薄膜通常安装在显示装置的外表面以防止因外来光的反射降低对比度或者防止外来光经反射进入图像。
3.减反射膜,又称增透膜,它以光的波动性和干涉现象为基础,主要功能是减少或消除光学元器件表面的反射光,从而增加光在这些元器件上的透过率,减少或消除系统的杂散光。减反射薄膜在光学薄膜产业占有极其重要的位置。
4.一般来说,减反射薄膜是可通过化学蒸镀(cvd)法、物理蒸镀(pvd)法在透明薄膜基材形成多层结构的防反射层,如现有专利文件1。利用高折射率层和低折射率层搭配,可以实现宽谱带的减反射,这个技术虽然在干法镀膜已经实现。但由于干法镀膜必须在真空中成膜,因此存在生产设备结构复杂,设备投资高,生产率低等缺点。因此近年来,湿法涂膜技术,因为其低成本,可大面积涂布和连续化生产,越来越多的被人们所关注。但目前现有技术主要为用湿法涂布的单层减反膜,如专利文件2-3。
5.在湿法镀膜领域,存在膜层的雾度偏高而不能使用的问题。
6.液晶显示设备自身发出的光与环境中光源在显示屏幕上的反射光相互叠加会形成眩光,眩光长期作用与人眼,不但会造成视觉上的不适应感,而且强烈的眩光还会损害视觉。为此,市场上各类液晶显示设备表面均贴合具有防眩光膜(ag膜),此类硬化膜同时还要具备高耐磨作用,如电子黑板用防眩光硬化膜在这基础上还要解决良好的闪点和书写效果。
7.因此,现在的显示器不仅仅要求表面有能起到减反射作用的光学膜,还需要有能防眩光的光学膜,这样才能提供更优异的可视性。另外,应用于显示盖板上的涂层,需要有较高的硬度和较好的耐磨性能,但现在湿法涂布技术制备得到的低折射率层的硬度偏低,最高仅能达到500g/1h,耐磨性能也很差,仅能达到100g/10次。这也限制了减反射膜更广泛的应用。
8.现有专利技术文件:
9.1、中国发明专利,公开号:cn104614787a。
10.2、中国发明专利,公开号:cn1322338c。
11.3、中国台湾发明专利,公开号:twi515271b。
技术实现要素:12.为解决上述至少一个技术缺陷,本发明提供了如下技术方案:
13.本技术文件公开用于显示器的抗眩光减反射膜,自下至上依次包括基底、ag涂层、hr涂层、ar涂层;
14.ag涂层中包括粘合剂树脂、二氧化硅颗粒、有机粒子、无机耐磨颗粒;所述二氧化硅颗粒为100nm-3000nm的团聚体颗粒;所述有机粒子为聚甲基丙烯酸甲酯微粒子、聚苯乙烯微粒子,聚甲基丙烯酸甲酯聚苯乙烯共聚物微粒子,聚倍半硅氧烷微粒子中的一种或多种;所述无机耐磨颗粒为纳米氧化铝、纳米氧化锆、纳米金刚石、六方氮化硼纳米片中一种或多种形成,所述无机耐磨颗粒为50-200nm的团聚体颗粒;
15.hr涂层的折射率1.53-1.74;
16.ar涂层的折射率1.2-1.48。
17.本方案中将防眩光的ag涂层与高折射hr、低折射的ar涂层以限定层级结构复合,集防眩光、减反射为一体。
18.在ag涂层中限定形态的无机耐磨颗粒的成分及形态并通过其分散在粘合剂树脂中起到防眩光、提高耐磨性能等作用。优选限定粒径的二氧化硅形态,该团聚形态部分使固化后涂层表面形成凹凸起伏的形貌,部分存在于涂层内部,相配合提升防眩光效果。优选有机粒子,存在于涂层内部,具有提供内雾度、减少二氧化硅粒子团聚体彼此间再团聚的作用、填充树脂以及调节粒子与树脂之间的折射率差异的作用,实现内外雾度平衡,该涂膜液制备的膜在硬度、耐磨等性能取得提升,同时使膜层具有高清晰度、低闪点、泛白抑制性好等优点。
19.进一步,hr涂层中包括粘合剂树脂、折射率在2.0-2.8的无机金属氧化物粒子,无机金属氧化物粒子在涂层中团聚呈粒径10-80nm的颗粒状,无机金属氧化物粒子为纳米氧化锆或氧化钛;
20.ar涂层中包括粘合剂树脂、折射率1.15-1.40的空心二氧化硅粒子。
21.在hr涂层中加入限定形态的无机金属氧化物,降低雾度,有助提高膜层清晰度、力学性能等。在ar涂层中加入空心二氧化硅来调整折射率等,上述层级、组分下的膜层结合稳定且在硬度、耐磨等性能上取得突破。
22.进一步,以质量计,ag涂层中,相对于22-45份的粘合剂树脂,二氧化硅颗粒3-7份,有机粒子1-3份,无机耐磨颗粒1-3份;
23.以质量计,hr涂层中,相对于40-200份的粘合剂树脂,纳米氧化锆粒子20-75份;
24.以质量计,ar涂层中,相对于9-25份粘合剂树脂,空心二氧化硅粒子30-80份。
25.粘合剂树脂与量比下的功能粒子为组成涂层的基本成分,对于润滑剂、消泡剂、流平剂等助剂以及固化成型的固化剂等可根据需求自由添加。
26.进一步,固化成型ag涂层的涂液组分、固化成型hr涂层的涂液组分、固化成型ar涂层的凃液组分中的粘合剂树脂均包括六官能团以上的光固化低聚物树脂,三官能团以上的光固化稀释单体树脂;
27.光固化低聚物树脂为聚氨酯丙烯酸酯低聚物、环氧丙烯酸酯低聚物、聚酯丙烯酸酯和聚醚丙烯酸酯、聚丙烯酸树脂低聚物、环氧树脂聚合物、含氧丙烯酸酯、脲酸丙烯酸酯中一种或多种;
28.光固化稀释单体树脂为(甲基)丙烯酸乙酯、(甲基)丙烯酸乙基己酯、苯乙烯、甲基苯乙烯、n-乙烯基吡咯烷酮单官能度单体、聚羟甲基丙烷三(甲基)丙烯酸酯、二甘醇二(甲基)丙烯酸酯、三丙二醇二(甲基)丙烯酸酯、1,6-己二醇二(甲基)丙烯酸酯、己二醇(甲基)丙烯酸酯、季戊四醇三(甲基)丙烯酸酯、二季戊四醇六(甲基)丙烯酸酯、新戊二醇二(甲基)
丙烯酸酯中一种或多种。
29.优选限定结构的树脂组分,光固化成型方便,有助提高涂层的硬度、柔韧性等。
30.进一步,ar涂层中包括含氟聚合物2-8份、无机粒子5-30份、poss5-23份,无机粒子为氟化镁、氮化硼、二氧化硅、三氧化二铝中一种或多种,含氟聚合物为部分氟化的丙烯酸酯有机硅共聚物、部分或者完全氟化的丙烯酸类化合物、部分或者完全氟化的乙烯基醚的一种或多种,poss为苯基poss、氨基poss、乙烯基poss、丙烯酰基poss中一种或多种。含氟聚合物,其主要作用为增大水接触角以及改善涂膜的耐摩擦性能,poss为提高ar涂层的硬度,无机粒子为提高ar涂层的耐摩擦性。
31.进一步,以质量计,ag涂膜液包括六官能团以上的光固化低聚物树脂占比18-38%,三官能团以上的光固化稀释单体树脂4-7%;二氧化硅颗粒8-12%,有机粒子1-3%,无机耐磨颗粒1-3%,助剂1-5%,光引发剂1-3%;优选ag涂膜液中固含量在42-55%;
32.以质量计,hr涂膜液包括六官能团以上的光固化低聚物树脂占比1-3%,三官能团以上的光固化稀释单体树脂0.3-1%;纳米二氧化锆粒子1-3%,助剂0.05-0.2%,光引发剂0.1-0.5%;优选hr涂膜液中固含量在3-6%。
33.以质量计,ar涂膜液包括六官能团以上的光固化低聚物树脂0.25-0.5%,三官能团以上的光固化稀释单体树脂0.05-0.1%,空心二氧化硅粒子0.3-1.5%,实心二氧化硅粒子0.1-1%, poss0.1-1%,光引发剂0.1-0.5%。优选ar涂膜液中固含量在2.0-5.0%。
34.优选组分比例的涂膜液,光固化成型机理,使用时,可将各涂液经狭缝涂布、微凹涂布、刮刀涂布、辊涂等已知的涂布技术实现涂覆,之后经紫外光固化、电子辐射固化、热固化等一种或者两种组合方式固化而成,因紫外光固化具有可选择的原料种类更多的优势,优选紫外光固化方式。
35.对于助剂而言,如湿流平剂、消泡剂、阻聚抑制剂、表面控制剂等,光引发剂如苯乙酮类、二苯甲酮类、噻吨酮类、苯偶姻、苯偶姻甲醚,用芳香族重氮鎓盐、芳香族锍盐、芳香族碘鎓盐、茂金属化合物、苯偶姻磺酸酯,也可配合选用具有活性的有机胺,如三乙胺、正丁胺等作为辅助引发剂。
36.对于溶剂,如极性溶剂、非极性溶剂,具体可选择丙酮、甲基乙基酮、甲基异丁基酮、环己酮、乙酸甲酯、乙酸乙酯、乙酸丙酯、乙酸丁酯、甲酸甲酯、甲酸乙酯、甲酸丙酯、甲酸丁酯、甲醇、乙醇、丙醇、异丙醇、异丁醇、丙二醇甲醚、正丁醇,优选甲基异丁基酮、丙二醇甲醚、异丁醇、乙酸乙酯、乙酸丁酯,可以为单一种溶剂,优选三种及三种以上的混合溶剂。
37.进一步,ag涂液组中:所述二氧化硅颗粒通过分散液的形式加入,以10nm-50nm的原始粒径与溶剂混合处理得到二次粒径为100nm-2000nm的二氧化硅颗粒分散液;
38.所述无机耐磨颗粒通过分散液的形式加入,以10-50nm原生粒径与溶剂混合得到二次粒径为50-200nm的分散液;
39.所述有机粒子的粒径为1μm-10μm。
40.限定形态及加入形式,经检测有助进一步提升膜层性能。
41.进一步,纳米氧化锆粒子的平均粒径为hr涂层厚度的5%-80%;空心二氧化硅粒径 50-80nm,实心二氧化硅平均粒径为ar膜层厚度的30%-100%,有助提升膜层性能。
42.进一步,所述无机耐磨颗粒为六方氮化硼纳米片形成,预处理步骤:将原始粒径的六方氮化硼纳米片与溶剂搅拌混合并超声分散处理得到胶液,将胶液离心处理得一次底部
固体;
43.将一次底部固体重复进行上述预处理步骤得到二次底部固体;
44.将二次底部固体重复上述预处理步骤并收集所得的离心液,该离心液即无机耐磨颗粒的分散液。针对性设计分散液制备工艺,有助分布均匀,进而提升膜层性能。
45.六方氮化硼纳米片可以经公知的制备方法得到,如电弧放电法、溶剂热法、气相沉积法、液相法。因为纳米粒子具有高表面能容易团聚,还需要对其表面进行处理,如聚合物分散剂、偶联剂处理,优选为可与树脂参与反应得具有反应性官能得硅烷偶联剂作为表面处理剂。
46.进一步,纳米氧化锆粒子为四方相、立方相型中一种或二者混合。限定相型有助提高膜层性能。
47.进一步,纳米氧化锆粒子以分散液的形式加入固化成型hr涂层的涂膜液中,纳米氧化锆粒子的分散液制备如下:
48.第一,将含锆化合物与溶剂、有机酸的混合物按比例混合,升温至250-320℃,恒温反应3-18h;
49.第二,将反应得到过滤物经多次洗涤后,得到四方或立方相纳米氧化锆粒子;
50.第三,将得到的纳米氧化锆粒子、分散助剂加入到溶剂中,处理得到透明的纳米氧化锆分散液,分散液中纳米氧化锆粒子形成二次分散粒径为10-50nm的团聚态。
51.结晶纳米氧化锆,是采用溶剂热一步合成法制备得到。原材料为含锆的化合物和有机溶剂,或者有机溶剂和有机酸的混合物,含锆化合物可以是有机锆化合物,包括正丙醇高,正丁醇锆,四叔丁醇锆等,也可以是无机锆化合物,包括硝酸锆,氯化锆,碱式碳酸锆等,优选有机锆化合物,更优选正丙醇锆。有机溶剂包括甲醇,乙醇,丁基醚,苯甲醇等,优选甲醇,乙醇,苯甲醇,有机酸包括甲酸,葵酸,硬脂酸,油酸等,优选甲酸,油酸。
52.纳米氧化锆分散液所用的溶剂,可以是极性溶剂,也可以是非极性溶剂,如正己烷,甲苯,乙醇,乙酸丁酯,乙酸乙酯,异丙醇,异丁醇,丙酮,丁酮,甲基异丁酮,丙二醇甲醚等,优选甲苯,乙酸丁酯,异丙醇,异丁醇,甲基异丁酮,丙二醇甲醚等。
53.在制备该纳米氧化锆分散液时,需要加入适量的分散助剂,分散助剂可以是硅烷偶联剂,钛酸酯偶联剂,具有表面亲和作用的高分子聚合物,丙烯酸酯单体和丙烯酸酯低聚物,优选具有表面亲和作用的高分子聚合物和丙烯酸酯单体,对氧化锆粉体进行分散。
54.该工艺下限定工序流程及反应温度,有助得到所需形态的纳米氧化锆。
55.进一步,所述ag涂层厚度在2-50μm且ag涂层的表面水接触角低于80
°
,所述hr涂层的光学厚度为1/2λ0,所述ar涂层的光学厚度为1/4λ0。
56.限定涂层的光学厚度关系,可得到反射率曲线为w型的宽谱带减反射膜。
57.对于基底而言,可以为三醋酸纤维素膜(tac)、聚对苯二甲酸乙二醇酯膜(pet)、聚降冰片烯膜(cop)、聚甲基丙烯酸甲酯膜(pmma)、聚碳酸酯膜(pc)、透明聚酰亚胺膜(cpi) 等基材种的一种,从透明性及光学延迟性考虑,优选三醋酸纤维素膜(tac)。所述的透明基体的厚度,优选为25μm-300μm,当作为偏光片表面保护膜的情况下,出于薄型化考虑,优选25μm-80μm。
58.与现有技术相比,本发明的有益效果:
59.1、本发明膜层集合防眩光、减反射为一体,且膜层具有高清晰度、低闪点、泛白抑
制性好、硬度高、耐磨等优点。
附图说明
60.为了更清楚地说明本发明实施例中的技术方案,下面将对实施例描述中所需要使用的附图作简单地介绍,显而易见地,下面描述中的附图仅仅是本发明的一些实施例,对于本领域普通技术人员来讲,在不付出创造性劳动的前提下,还可以根据这些附图获得其他的附图。
61.图1为ag-hr-ar膜的膜层结构说明;
62.图2为实施例1的ag1-hr1-ar1膜透射率及反射率谱图;
63.图3为实施例2的ag2-hr1-ar1膜透射率及反射率谱图;
64.图4为对比例1的ag1-hr1-ar2膜透射率及反射率谱图;
65.图5为对比例2的ag1-ar1膜透射率及反射率谱图;
66.图6为实施例1的ag1-hr1-ar1膜扫描电镜ag层截面图;
67.图7为实施例1的ag1-hr1-ar1膜扫描电镜ag层截面放大图;
68.图8为实施例1的ag1-hr1-ar1膜扫描电镜ar层截面图;
69.图9为实施例7结晶纳米氧化锆的电镜照片;
70.图10为实施例7结晶纳米氧化锆的xrd图谱;
71.图11为实施例7氧化锆分散液的粒度分布图。
72.其中,附图标记为:
73.10、基底;20、ag涂层;21、有机微粒子;22、二氧化硅粒子团聚体;23、无机耐磨粒子团聚体;30、hr涂层;31、纳米氧化锆粒子团聚体;40、ar涂层;41、空心二氧化硅粒子; 42、实心二氧化硅粒子。
具体实施方式
74.下面结合附图和具体实施例对本发明作进一步说明。
75.第一、结晶纳米氧化锆分散液的制备
76.案例1、结晶纳米氧化锆分散液的制备方法:将正丙醇锆和苯甲醇按质量比0.6:1的比例加入釜中(反应物总体积不超过釜体积的60%),设定转速为450转/min,釜体最高温度为 225℃。反应完成后将得到的粉体先后使用乙醇和丙二醇甲醚多次洗涤,后用丙二醇甲醚作为溶剂,高分子聚合物为分散助剂,对氧化锆粉体进行超声分散得到纳米氧化锆分散液,分散液的固含量为20%。纳米氧化锆的分散粒径为52nm,纳米氧化锆的原生粒径为5-10nm,通过xrd测试可知,纳米氧化锆的晶型为四方相和立方相氧化锆的混合型。
77.案例2、结晶纳米氧化锆分散液的制备方法:将正丁醇锆和二丙酮醇按质量比0.56:1 的比例加入釜中(反应物总体积不超过釜体积的60%),设定转速为450转/min,釜体最高温度为225℃。反应完成后将得到的粉体先后使用乙醇和mibk多次洗涤,后用mibk作为溶剂,高分子聚合物为分散助剂,对氧化锆粉体进行超声分散得到纳米氧化锆分散液,分散液的固含量为20%。纳米氧化锆的分散粒径为42nm,纳米氧化锆的原生粒径为8-12nm,通过xrd 测试可知,纳米氧化锆的晶型为四方相和立方相氧化锆的混合型。
78.案例3、结晶纳米氧化锆分散液的制备方法:将碱式碳酸锆和正己醇按质量比
0.62:1 的比例加入釜中(反应物总体积不超过釜体积的60%),设定转速为450转/min,釜体最高温度为225℃。反应完成后将得到的粉体先后使用乙醇和mibk多次洗涤,后用mibk作为溶剂,高分子聚合物为分散助剂,对氧化锆粉体进行超声分散得到氧化锆分散液,分散液的固含量为20%。纳米氧化锆的分散粒径为45nm,纳米氧化锆的原生粒径为8-12nm,通过xrd测试可知,纳米氧化锆的晶型为四方相和立方相氧化锆的混合型。
79.案例4、结晶纳米氧化锆分散液的制备方法:将正丁醇锆和苯甲醇按质量比0.48:1的比例加入釜中(反应物总体积不超过釜体积的60%),设定转速为450转/min,釜体最高温度为 225℃。反应完成后将得到的粉体先后使用乙醇和mibk多次洗涤,后用mibk作为溶剂,高分子聚合物为分散助剂,对氧化锆粉体进行超声分散得到氧化锆分散液,分散液的固含量为 20%。纳米氧化锆的分散粒径为45nm,纳米氧化锆的原生粒径为8-12nm,通过xrd测试可知,纳米氧化锆的晶型为四方相和立方相氧化锆的混合型。
80.案例5、结晶纳米氧化锆分散液的制备方法:将硝酸锆和尿素和水的混合物按质量比0.48: 1的比例加入釜中(反应物总体积不超过釜体积的60%),设定转速为450转/min,釜体最高温度为220℃。反应完成后将得到的粉体先后使用乙醇和mibk多次洗涤,后用mibk作为溶剂,高分子聚合物为分散助剂,对氧化锆粉体进行超声分散得到氧化锆分散液,分散液的固含量为20%。纳米氧化锆的原生粒径为20-25nm,通过xrd测试可知,纳米氧化锆的晶型为单斜相和四方相的混合型。由于反应是在水溶液中进行的,后续处理很难完全将水除去,故所得到的分散液二次粒径偏大,大于100nm,并且分散液稍显浑浊,不是透明的。
81.案例6、结晶纳米氧化锆分散液的制备方法:将四叔丁醇锆和苯甲醇按质量比0.6:1的比例加入釜中(反应物总体积不超过釜体积的60%),设定转速为450转/min,釜体最高温度为300℃。反应完成后将得到的粉体先后使用乙醇和丙二醇甲醚多次洗涤,后用丙二醇甲醚作为溶剂,高分子聚合物为分散助剂,对氧化锆粉体进行超声分散得到氧化锆分散液,分散液的固含量为20%。纳米氧化锆的原生粒径为15-25nm,通过xrd测试可知,纳米氧化锆的晶型为主要为立方相。过高的反应温度制备得到的纳米氧化锆的原生粒径较大,并且更难分散,该条件下制备得到的纳米氧化锆的分散液二次粒径大于100nm,并且分散液稍显浑浊,不是透明的。
82.通过上述实施例及对比例结果说明,不同原料跟溶剂的选择会影响的纳米氧化锆的原生粒径跟晶型,且所得纳米氧化锆分散粒径更大。当选择此纳米氧化锆分散液加入到hr涂层中会导致涂层的透过率偏低,雾度偏高,并且影响涂层的折射率,参见下述对比例3。
83.第二、分散液的制备
84.二氧化硅颗粒分散液:分散液是将市购的10-50nm原始粒径的实心二氧化硅粒子(未经过表面处理)在乙醇溶剂中经球磨法研磨后得到二次分散粒径在预定范围的二氧化硅粒子分散液。可通过调整溶剂比例、研磨参数等调整二次分散粒径,此不在赘述。
85.无机耐磨颗粒分散液:首先,预处理步骤:将去离子水与乙醇按体积比1:1混合,将市购的原生粒径为10-50nm的六方氮化硼纳米片(无表面处理)在搅拌的情况下加入,搅拌 6-24hr,超声分散10min左右。再将分散液进行离心分离,离心机转速为6000-10000rpm,离心5-10min,弃上层清液,留下层沉淀物(一次底部固体)。
86.然后,用一次底部固体重复,重复上述预处理步骤(与溶剂混合、搅拌、超声、离心),得到二次底部固体待用。
87.最后,将溶剂与上述二次底部固体进行上述预处理步骤,得到离心胶体溶液即为纳米六方氮化硼分散液。
88.上述底部沉淀继续进行上述预处理步骤,收集离心胶体溶液,再将离心出的底部固体沉淀进行上述预处理步骤,直至底部没有沉淀为止,收集到的离心胶体溶液即为纳米六方氮化硼分散液。
89.颗粒粒径的大小可通过调整搅拌、超声、离心等参数获取,此不在赘述。
90.第三、凃液的制备
91.涂液ag1的制备:按质量百分数配置10kg涂液,其中十官能团的聚氨酯丙烯酸酯低聚物占28%,六官能团聚氨酯丙烯酸酯低聚物占3%,三官能团的丙烯酸酯单体占3%,六官能团丙烯酸酯单体占3%,硫醇类阻聚剂占2%,分散粒径为240nm的二氧化硅占8%,聚倍半硅氧烷微粒子占0.5%,分散粒径为80nm的六方氮化硼纳米片占2%,光引发剂占2%,将以上原料加入到乙酸丁酯和异丁醇的混合溶剂中,搅拌至以上组分完全溶解,得到固含量为51.5%的涂液ag1。
92.涂液ag2的制备:按质量百分数配置10kg涂液,其中九官能团聚氨酯丙烯酸酯低聚物占 21.5%,三十官能团超支化丙烯酸酯低聚物占2.8%,三官能团丙烯酸酯单体占1.0%,六官能团丙烯酸酯单体占2.4%,硫醇类阻聚剂占2%,聚乙二醇600da占1.9%,分散粒径为350nm 二氧化硅占8%,交联聚苯乙烯微粒占1%,分散粒径为100nm的纳米金刚石粒子2%,光引发剂占2.1%,将以上原料加入到乙酸丁酯和丙二醇甲醚的混合溶剂中,搅拌至以上组分完全溶解,得到固含量为44.7%的涂液ag2。
93.涂液ag3的制备:按质量百分数配置10kg涂液,其中九官能团聚氨酯丙烯酸酯低聚物占 21.7%,三十官能团超支化丙烯酸酯低聚物占3.1%,三官能团丙烯酸酯单体占1.2%,六官能团丙烯酸酯单体占2.4%,硫醇类阻聚剂占1.9%,聚乙二醇600da占2%,分散液的二次粒径为600nm二氧化硅占10%,聚甲基丙烯酸甲酯微粒占1.5%,分散粒径为80nm的纳米氧化铝粒子占2%,光引发剂占2.1%,将以上原料加入到乙酸丁酯和丙二醇甲醚的混合溶剂中,搅拌至以上组分完全溶解,得到固含量为47.9%的涂液ag3。
94.涂液ag4的制备:按涂液3的制备方法,区别在于不加聚甲基丙烯酸甲酯微粒。
95.涂液ag5的制备:按涂液3的制备方法,区别在于不加纳米氧化铝粒子。
96.涂液hr1的制备:按质量百分数配置10kg涂液,其中脂肪族六丙烯酸酯占1.24%,十五官能团聚氨酯丙烯酸酯预聚物占0.165%,四官能团丙烯酸酯单体占0.245%,三官能团丙烯酸酯单体占0.31%,分散粒径为20nm的纳米氧化锆(案例1)占1.4%,流平剂占0.11%,光引发剂占0.27%,将以上原料加入到丙二醇甲醚溶剂中。搅拌至以上组分完全溶解,得到固含量为3.7%的涂液hr1。
97.涂液hr2的制备:按涂液hr1的制备方法,选用案例5制备的分散粒径大于100nm氧化锆分散液。
98.涂液ar1的制备:按质量百分数配置10kg涂液,其中九官能团脂肪族聚氨酯丙烯酸酯占 0.314%,三官能团环氧丙烯酸酯占0.078%,粒径70nm空心二氧化硅占1.26%,实心二氧化硅占0.27%,poss占0.5%,光引发剂占0.24%,将以上原料添加到甲基异丁基酮和甲基异丁基酮、丙二醇甲醚、异丁醇、乙酸乙酯、乙酸丁酯的混合溶剂中,搅拌至以上组分完全溶解,得到固含为2.7%的涂液ar1。
99.涂液ar2的制备:用涂液ar1的配制方法,区别在于选用20nm的空心二氧化硅。
100.涂液ar3的制备:用涂液ar1的配制方法,区别在于不加实心二氧化硅。
101.涂液ar4的制备:用涂液ar1的配制方法,不加poss。
102.第四、涂层的制备
103.以下各实施例中膜层结构如表1所示。
104.实施例1
105.首先,用微凹辊涂布机,将涂液ag1涂布在80μm厚度的三醋酸纤维素膜上并在80℃下干燥。之后,在氮气氛围中,用高压汞灯在600mj/cm2固化能量下使涂层固化,涂层厚度为 4μm,得到膜ag1。ag涂层的表面水接触角低于80
°
。
106.然后,用狭缝涂布涂布机,将涂液hr1涂布在ag1膜上,并在80℃下干燥。之后,在氮气氛围中,用高压汞灯在600mj/cm2固化能量下使涂层固化,hr的涂层厚度为(1/2)λ0,得到膜ag1-hr1。
107.最后,用狭缝涂布涂布机,将涂液ar1涂布在上述ag1-hr1膜上,并在80℃下干燥。之后,在氮气氛围中,用高压汞灯在600mj/cm2固化能量下使涂层固化,ar的涂层厚度为(1/4) λ0,得到膜ag1-hr1-ar1。
108.实施例2
109.按实施例1的方法,将hr的涂层厚度减半为1/4λ0,得到膜ag1-hr1(1/4λ0)-ar1。
110.实施例3
111.按实施例1的方法,将涂液ag1替换为ag2(表面水接触角低于80
°
),得到膜ag2-hr1-ar1。
112.实施例4
113.按实施例1的方法,将涂液ag1替换为ag3(表面水接触角低于80
°
),得到膜ag3-hr1-ar1。
114.实施例5
115.按实施例1的方法,将涂液ag1替换为ag4(表面水接触角低于80
°
),得到膜ag4-hr1-ar1。
116.实施例6
117.按实施例1的方法,将涂液ag1替换为ag5(表面水接触角低于80
°
),得到膜ag5-hr1-ar1。
118.对比例1
119.按实施例1的方法,将涂液ar1替换为ar2,得到膜ag1-hr1-ar2。
120.对比例2
121.按实施例1的方法,不涂布hr层,得到膜ag1-ar1。
122.对比例3
123.按实施例1的方法,将涂液hr1替换为hr2,得到膜ag1-hr2-ar1。
124.对比例4
125.按实施例1的方法,将涂液ag1替换为ag2,将涂液ar1替换为ar3,得到膜ag2-hr1-ar3。
126.对比例5
127.按实施例1的方法,将涂液ag1替换为ag3,将涂液ar1替换为ar4,得到膜ag3-hr1-ar4。
128.第五、测试
129.本发明膜层的结构图1所示,底部为透明的基底10,基底上依次为ag涂层20、hr涂层 30、ar涂层40,ag涂层20内为有机微粒子21、二氧化硅粒子团聚体22、无机耐磨粒子团聚体23以及位于表面处的二氧化硅粒子团聚体22,hr涂层30中的纳米氧化锆粒子团聚体 31,ar涂层40内的空心二氧化硅粒子41、实心二氧化硅粒子42。
130.测试评价方法说明:
131.1、减反射膜的光学性能
132.检测仪器:紫外分光光度计
133.检测方法:将涂布后的柔性薄膜进行光学性能测试,测试薄膜的透射率、反射率,测试范围为300-1100nm。
134.2、减反射膜的疏水功能
135.检测仪器:接触角测试仪
136.检测方法:将涂布后的柔性薄膜进行水接触角测试,水滴体积2微升。
137.3、减反射膜的耐磨性能
138.检测仪器:耐摩擦试验机
139.检测方法:将涂布后的柔性薄膜进行耐摩擦性能测试,按照不同的要求放置砝码,更改滑动次数和速度。
140.4、减反射膜的硬度
141.检测仪器:电动铅笔硬度计
142.检测方法:将涂布后的柔性薄膜进行硬度测试,测试要求为:500g,速度40。
143.5、涂层折射率的测定:
144.检验仪器:椭偏仪semilab se-2000
145.测试方法:采用提拉涂布的方法将涂液镀在硅片上,将硅片放入椭偏仪中进行测试。
146.6、涂层厚度:
147.检验仪器:厚度仪
148.测试方法:将涂布后的柔性薄膜放置在厚度仪上进行测试。
149.7、涂层雾度:
150.检验仪器:光电雾度仪wgw
151.测试方法:将涂布后的柔性薄膜放置在雾度仪中进行测试。
152.8、防眩光膜的清晰度及泛白抑制性测试
153.清晰度性:通过防眩膜观察荧光灯的灯管轮廓,对膜的透射扩散性进行评价。
154.清晰看到灯管,轮廓清晰,无扩散效应
155.○
:可以看到灯管,轮廓轻微模糊
156.×
:无法看清灯管,扩散效应明显
157.泛白抑制性:将防眩膜贴于黑色亚克力板上,观察涂膜泛白情况:
158.泛白抑制性极佳
159.○
:泛白抑制性良好
160.×
:泛白抑制性差。
161.测试结果如表1、图2-图11所示:
[0162][0163]
从实施例1跟对比例1的结果可以看出,当ar涂层选20nm的空心二氧化硅粒子,耐磨性会提高,但会影响光学性能,所以需要选择粒径合适的空心二氧化硅粒子。
[0164]
从实施例1跟对比例2的结果可以看出,当增加hr层后,涂膜的硬度和耐磨性都会提高,透射率增加,反射率降低,所以需要选择粒径合适的空心二氧化硅粒子。
[0165]
从实施例1跟对比例3的结果可以看出,当hr涂层中添加分散粒径大于100nm的纳米氧化锆粒子会影响涂膜的光学透过性能,所以优选比hr。
[0166]
从实施例3跟对比例4的结果可以看出,当ar涂层中不添加实心二氧化硅粒子,涂膜的耐磨性下降。
[0167]
从实施例4跟对比例5的结果可以看出,当ar涂层中不添加poss,涂膜的硬度跟耐磨性都下降。
[0168]
从实施例5的结果可以看出,当ag层中不加有机粒子,由于不能通过增加内部散射得到内雾都,所以涂膜的总雾度明显下降。
[0169]
从实施例6的结果可以看出,当ag层中不加无机耐磨粒子,涂膜的钢丝绒耐磨性明显下降。
[0170]
以上仅是本发明的优选实施方式,本发明的保护范围并不仅局限于上述实施例,凡属于本发明思路下的技术方案均属于本发明的保护范围。应当指出,对于本技术领域的普通技术人员来说,在不脱离本发明原理前提下的若干改进和润饰,这些改进和润饰也应视为本发明的保护范围。