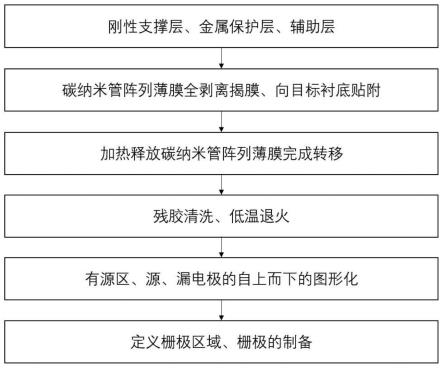
1.本发明属于半导体工艺技术领域。
背景技术:2.碳纳米管(cnt)作为准一维半导体材料,具有载流子弹道输运、高迁移率、高导热和机械性能好等特点,在射频器件、传感器和柔性电子等方面有着很大的应用前景。近几年来,碳纳米管的自组装合成技术有了一定的突破,北京大学团队在4英寸硅片基底上成功制备出达到集成电路应用需求的,高密度的碳纳米管单层阵列薄膜。然而在除了硅片以外的衬底上碳纳米管阵列无法进行沉积,这极大限制了基于碳纳米管的电子器件类型和应用场景,使得碳纳米管阵列的转移技术亟需发展。
3.在下一代物联网通信技术发展的牵引下,射频器件向更高频和柔性化迈进,对沟道材料和器件制备工艺都提出了更高的要求,碳纳米管被认为是射频场效应晶体管的理想材料,理论上具备高频段工作的物理性能优势,有接近太赫兹(thz)范围的本征截止频率以及可柔性化的特点。然而,受限于碳纳米管阵列的物理特性,需要开发有效的碳纳米管阵列薄膜的无损转移技术,以及射频晶体管的低温制备工艺等关键技术,才能制成碳纳米管柔性射频器件,发挥其性能优势。
4.现有的二维材料薄膜等纳米材料的转移方法,主要基于湿法转移或传统干法转移。众所周知,由于单根碳纳米管的高机械强度,其高取向性阵列具有各相异性的力学特征,不可避免地会导致碳纳米管阵列薄膜在转移过程中应力问题突出,湿法转移置于液体后阵列排布难以保持,传统干法转移时附着于聚二甲基硅氧烷(pdms)等薄膜难以成膜保形,因此通过现有方法无法进行碳纳米管阵列的转移,此外,带有硅衬底非全剥离的转移由于杨氏模量差异无法满足柔性弯曲的器件性能需求。
技术实现要素:5.发明目的:为了解决上述现有技术存在的问题,本发明提供了一种基于干法转移的碳纳米管阵列的柔性射频器件的制备方法。
6.技术方案:本发明提供了一种基于干法转移的碳纳米管阵列的柔性射频器件的制备方法,具体包括如下步骤:步骤1:刚性支撑层制备:在支撑层上涂覆光刻胶,通过辊将热释放胶带不带胶的一面平铺在光刻胶上,通过加热固化将热释放胶带贴附于支撑层上;步骤2:碳纳米管阵列保护层制备:在碳纳米管阵列的上表面蒸镀一层金属薄膜,所述碳纳米管阵列沉积在硅片衬底上;步骤3:辅助层制备:在步骤2中的金属薄膜上旋涂光刻胶;步骤4:将步骤1中的热释放胶带带胶的一面贴在步骤3中的光刻胶上;步骤5:针对步骤4得到的结构,固定住硅片衬底,对刚性支撑层施加外力,使得碳纳米管阵列与硅片衬底实现完全剥离;
步骤6:将步骤5中与硅片剥离的碳纳米管阵列贴附在柔性目标衬底上;步骤7:将步骤6得到的结构置于热板上加热,使得热释放胶带受热失去粘性,从而使得刚性支撑层与带有金属薄膜的碳纳米管阵列完全剥离;得到金属薄膜-碳纳米管阵列-柔性目标衬底结构;步骤8:使用有机溶剂对步骤7得到的结构上的残胶进行清洗;步骤9:将清洗后的金属薄膜-碳纳米管阵列-柔性目标衬底结构置入烘箱进行退火;步骤10:在金属薄膜上定义并制备源、漏电极区域以及碳纳米管阵列的沟道区域;步骤11:在碳纳米管阵列的沟道区域中定义栅极区域,并通过腐蚀的方式去除栅极区域的金属薄膜;步骤12:将栅介质沉积在碳纳米管阵列的沟道区域中,并在栅介质上覆盖栅金属,形成栅极结构。
7.进一步的,所述支撑层为表面平整的硬质刚性材料,包括硅片,玻璃片,石英片或者塑料板。
8.进一步的,所述金属薄膜采用的金属为能够被化学腐蚀的金属,金属薄膜的厚度范围在10~500nm。
9.进一步的,所述步骤3中的光刻胶为聚甲基丙烯酸甲酯光刻胶;旋涂聚甲基丙烯酸甲酯光刻胶时转速为5000 转/分钟,烘胶固化时间大于4分钟,厚度小于1μm。
10.进一步的,所述柔性衬底为柔性塑料衬底,采用的塑料为苯二甲酸乙二醇酯,聚萘二甲酸乙二醇酯或者聚酰亚胺。
11.进一步的,所述步骤10和步骤11中采用紫外曝光、深紫外曝光、电子束直写、纳米转印或者印刷电子技术划分出源极区域,漏极区域,沟道区域和栅极区域。
12.进一步的,所述步骤11中采用金属腐蚀液去除栅极区域的金属薄膜,所述金属腐蚀液为基于氰化物的金属腐蚀液、碘化钾和碘的金属腐蚀液、王水、氢氟酸、硼酸溶液、盐酸溶液、硝酸溶液或者上述任意两种液体的组合。
13.进一步的,所述步骤8中有机溶剂为丙酮、乙酸、氯仿、二氯甲烷或n-甲基-2-吡咯烷酮乙腈中的一种溶剂或多种溶剂的组合。
14.有益效果:本发明通过适用于碳纳米管阵列的干法转移工艺,实现对碳纳米管阵列薄膜向各类衬底的无损转移,使得晶圆级面积大小的碳纳米管阵列薄膜整体完全剥离原硅片衬底,并保持良好形貌,整体转移至目标衬底,本发明无需通过基于溶液的湿法剥离过程,减少了碳纳米管与各类溶液接触造成的污染,同时避免了薄膜受溶液表面张力对碳纳米管阵列结构造成的破坏。本发明定义的转移过程保证碳纳米管阵列的材料和电学特性,从而综合提升基于碳纳米管晶体管的器件性能、形态和应用。此外,本发明可实现柔性碳纳米管阵列射频器件,构造用于可穿戴、脑机接口等应用的高质量的柔性碳纳米管晶体管电路,从而在保证碳纳米管晶体管的性能的前提下,拓展碳纳米管器件异质异构下的各类功能设计和集成。
附图说明
15.图1为本发明的流程图;
图2为本发明热释放胶带贴附在光刻胶后的结构图;图3为将碳纳米管阵列整体与硅片完全剥离的示意图;图4为将碳纳米管阵列贴付在目标柔性衬底上的结构图;图5为金属薄膜-碳纳米管阵列-柔性目标衬底结构的结构示意图;图6为本发明最终的得到的射频晶体管器件结构示意图。
16.附图标记说明:1,硅片;2,碳纳米管阵列;3,金属薄膜;4,辅助层;5,热释放胶带;6,支撑层;7,目标柔性衬底;8,源、漏电极;9,栅介质;10,栅金属。
具体实施方式
17.构成本发明的一部分的附图用来提供对本发明的进一步理解,本发明的示意性实施例及其说明用于解释本发明,并不构成对本发明的不当限定。
18.如图1所示,本实施例提供了一种基于干法转移的碳纳米管阵列的柔性射频器件的制备方法,具体包括如下步骤:步骤1:刚性支撑层制备——支撑层6上涂覆光刻胶,将热释放胶带5不带胶面朝向支撑层,通过辊将其平铺并固定在硅片上,通过加热固化将热释放胶带贴附于支撑层上。
19.步骤2:碳纳米管阵列保护层制备——在硅片衬底1沉积的碳纳米管阵列2的上表面蒸镀一层金属薄膜3。
20.步骤3:辅助层制备——在金属薄膜的上面旋涂光刻胶4。
21.步骤4:全剥离揭膜——如图2所示将步骤1中得到的热释放胶带贴在在步骤3的光刻胶上;如图3所示固定住硅片衬底,对刚性支撑层施加外力,使得整片碳纳米管阵列作为整体与硅片衬底完全剥离。
22.步骤5:目标衬底贴附——将步骤4所得的碳纳米管阵列贴附在目标衬底表面,如图4所示。
23.步骤6:热释放转移——将步骤5中得到的结构置于热板上加热,使得热释放胶受热失去粘性与碳纳米管阵列上的金属薄膜剥离,得到金属薄膜-碳纳米管阵列-柔性目标衬底结构,该结构如图5所示。
24.步骤7:残胶清洗——使用有机溶剂将步骤6中得到结构的金属薄膜表面的残胶进行清洗。
25.步骤8:低温退火——将步骤7所得的结构置入烘箱进行退火。
26.步骤9:自上而下的图形化——在金属薄膜上定义并制备源、漏电极区域8以及碳纳米管阵列的沟道区域;本实施例采用紫外曝光、深紫外曝光、电子束刻写、纳米转印或者印刷电子技术划分出源极区域,漏极区域,沟道区域和栅极区域。
27.步骤10:定义栅极区域——在步骤9得到的沟道区域上通过光刻或电子束直写等方式定义栅极区域,通过腐蚀的方式去除栅极区域的金属薄膜;本实施例采用的金属腐蚀液为基于氰化物的金属腐蚀液、碘化钾和碘的金属腐蚀液、王水、氢氟酸、硼酸溶液、盐酸溶液、硝酸溶液或者上述任意两种液体的组合。
28.步骤11:如图6所示,栅极的制备——通过原子层沉积(ald)的方式将栅介质9沉积在源漏电极之间的间隙内的碳纳米管阵列上,随后在栅介质上覆盖栅金属10,形成栅极结构。
29.步骤1中所述的支撑层可以为玻璃片、石英片、塑料板等表面平整的硬质刚性材料,从而起到支撑作用,避免在机械剥离操作过程中胶带的弯曲导致的薄膜开裂破损、连续性差等问题,以及热释放胶贴附不平整导致的释放不完全的问题。
30.步骤2中所述金属薄膜采用的材料为金、钯等一种或多种能够被化学腐蚀的金属;所述金属薄膜的厚度为10~500nm,优选的,厚度为50~100nm,旋涂后于180℃下烘烤5min;金属薄膜直接与碳纳米管接触,从而避免有机胶对表面态活跃的碳纳米管薄膜材料的污染,随后通过腐蚀的方法去除,从而提高碳纳米管阵列薄膜表面的洁净度。
31.步骤3中采用的光刻胶为涂聚甲基丙烯酸甲酯(pmma)光刻胶;在旋涂pmma时,转速为5000、转/分钟,烘胶固化时间》4分钟,厚度需小于1μm,本实施例的厚度为500nm;pmma作为辅助层隔开热释放胶和金属保护层,解决两者间的应力的不匹配问题,防止热释放过程中金属的破裂和热释放胶的渗透。
32.步骤5中所述柔性衬底为,柔性塑料衬底,所述塑料为聚对苯二甲酸乙二醇酯(pet),聚萘二甲酸乙二醇酯(pen)或者聚酰亚胺(pi)。
33.由于硬质支撑层的作用使得此步骤前热释放胶所载有结构无法拉伸弯曲,因此柔性衬底可通过辊向热释放胶贴附,以达到最佳的转移贴合效果。
34.所述步骤7中所述有机溶剂包括丙酮、乙酸、氯仿、二氯甲烷、n-甲基-2-吡咯烷酮乙腈及其组合,去胶处理时间的为30分钟至1个小时,可根据需要选择用于使用的的对应配方的热释放胶的去除的最优化的残胶清洗过程和组合;无需复杂的去胶工艺,避免残胶影响碳纳米管表面形貌和洁净度等从而影响与金属的欧姆接触等晶体管的界面态问题。
35.步骤8中退火温度为80~100℃,时间为8~12小时,本实施例中退火温度为90℃;步骤9采用氧气等离子体刻蚀技术去除碳纳米管薄膜。
36.步骤11中所述栅介质为氧化铝(al2o3)或氧化铪(hfo2)中的任意一种,沉积温度小于90℃,保证碳纳米管在介质生长过程中的稳定,沉积介质厚度大于10nm,满足沟道区域完全被栅介质覆盖。
37.本发明的一个实施例:准备支撑层(本实施例中支撑层采用硅片)和热释放胶带,硅片上旋涂az7908胶,将热释放胶带不带胶面朝向硅片,通过辊将其平铺并固定在硅片上,通过110℃,2分钟加热固化将热释放胶带贴附于硅片上,并揭离热释放胶带的离型保护膜,将热释放胶带有胶的一面的四条边中的任意一条边上贴上pi薄膜,使pi薄膜所覆盖的部分区域失去粘性;方便后续剥离;pi薄膜为离型塑料膜,厚度<10μm。
38.在带有氧化硅的硅片衬底沉积的碳纳米管阵列的上表面先蒸镀一层50nm厚度的金属薄膜,用来防止光刻胶或热释放胶等极大降低射频性能的有机污染,提高洁净度;随后在金保护层的上面涂覆pmma a6光刻胶。pmma辅助层的构筑起到隔离应力和防止形变的作用,更好辅助碳纳米管阵列成膜全剥离及释放过程中形貌的保持。
39.将步骤(1)中热释放胶带有胶的面贴附在pmma a6光刻胶上,通过静电吸附排出空气形成贴合,排出剩余气泡后,对支撑层施加外力,该外力沿着步骤(1)中带pi薄膜的边,通过脱/吸附力的范德华力竞争,将碳纳米管阵列与硅片衬底完全分离(本实施例在热释放胶带的一边贴pi薄膜,能够使得碳纳米管阵列与硅片衬底剥离更加顺利)。
40.准备柔性目标衬底,通过丙酮、酒精清洗后,将与硅片衬底剥离的碳纳米管阵列贴
附在柔性目标衬底上。
41.将上述得到的结构的热释放胶带置于130℃以上的热板上加热。热释放胶受热失去粘性,碳纳米管阵列薄膜与热释放胶带脱离,并自主附着在目标衬底上,形成金属薄膜在最上层,碳纳米管阵列在中间层,目标衬底在最下层的金属薄膜-碳纳米管阵列-柔性目标衬底结构。
42.清洗金属薄膜-碳纳米管阵列-柔性目标衬底结构表面的残胶,使用有机溶剂清洗来减少金属薄膜表面的pmma和以丙烯酸等为主的热释放胶残留有机化合物,浸入丙酮30分钟,过乙醇浸泡10分钟,浸入nmp中60℃水浴加热30分钟,过乙醇浸泡10分钟。
43.将金属薄膜-碳纳米管阵列-柔性目标衬底结构置于90℃烘箱中退火8小时,从而释放转移过程中造成的微区应力,优化碳纳米管阵列在新衬底上的电学性能。
44.在金属薄膜上通过光刻定义源、漏电极区域以及碳纳米管阵列的沟道区域,电极图形处蒸镀ti/au(钛/金,本实施例中ti的厚度为20nm,au的厚度为180nm),然后通过腐蚀和氧等离子体刻蚀去掉有源区以外的金属薄膜,用氧等离子体刻蚀除去有源区以外的碳纳米管薄阵列。
45.在沟道区域上通过光刻或电子束直写等方式定义栅极区域,通过腐蚀的方式去除栅极区域的金属薄膜,使得碳纳米管阵列暴露并以此形成源漏电极之间的间隙。
46.通过原子层沉积ald的方式将al2o3(氧化铝)沉积在源漏电极之间的间隙内的碳纳米管阵列上,沉积温度90℃,厚度10nm。随后在栅介质上覆盖ti/au,形成栅极结构。从而完成基于碳纳米管阵列转移的柔性射频器件的制备。
47.与本发明形成对比的实施例和分析:1.无pmma辅助层——金属薄膜剥落,阵列应力,无法转移,具体步骤如下:准备硅片和热释放胶带,硅片上旋涂az7908胶,将热释放胶带平铺并固定在硅片上。在硅片衬底沉积的碳纳米管阵列的上表面蒸镀100nm的金。将热释放胶带贴在带金属薄膜的碳纳米管阵列上表面,随后揭开热释放胶带,此时金属薄膜的表面可见裂纹,这是由于热释放胶带接触热板的同时胶受热膨胀以及碳纳米管阵列在剥离过程中的应力不均匀,加载在金属薄膜表面的负荷无法向面外传递,而金属的低韧性阻碍其断裂前吸收变形能量。在加热释放的过程中,由于金属结构的破坏,热释放胶渗透穿插进入金/碳纳米管的分层结构中,造成薄膜结构的变形和微区机械应力的形成,从而表现出热释放后金/碳纳米管薄膜的破裂,通过表征分析得出碳纳米管阵列形貌得到了永久性的破坏,薄膜的电学性能损失,无法用于射频晶体管的制备。
48.2.无金属薄膜——pmma和丙烯酸胶的污染降低电学性能,填充膨胀破坏阵列形貌,具体步骤如下:准备石英片和热释放胶带,硅片上旋涂az7908胶,将热释放胶带平铺并固定在硅片上。在硅片衬底沉积的碳纳米管阵列的上表面旋涂pmma a6光刻胶,厚度为500nm。将热释放胶带贴在带pmma辅助层的碳纳米管阵列上表面,随后揭开热释放胶带,将带有碳纳米管的面贴附在pi衬底上,随后加热130℃进行释放,清洗去胶和退火后得到直接暴露的碳纳米管阵列/柔性衬底。随后蒸镀一层50nm的金,通过光刻进行源漏栅极的图案化制备,利用电子束直写进行栅极定义,随后腐蚀金属薄膜后通过ald生长10nm的hfo2作为栅介质、蒸镀栅
金属后形成射频晶体管器件。经过测试发现沟道内电流小于100μa/mm,相比于本实施例有两个数量级的衰减。经过表征发现沟道内的碳纳米管上有大量有机物残留,且阵列的形态造成破坏,形成大量无序的方向杂乱的区域。这是由于金属薄膜的缺失,造成了大量热释放胶(丙烯酸胶)和pmma胶的渗透,在热释放过程中胶呈半液半固态,流动性极大增强后渗透进入碳纳米管阵列,挤压破坏形貌,并渗入碳纳米管下表面从而在后续的去胶清洗过程中难以被去除。大量有机胶的包覆形成缺陷和声子散射,削弱了碳纳米管阵列的电学性能。
49.3.无刚性支撑层——褶皱裂纹,机械形变,大面积的脱落剥离,无法保持阵列形貌,具体步骤如下:在硅片衬底沉积的碳纳米管阵列的上表面蒸镀50nm的金,随后在其上表面旋涂pmma a6光刻胶,厚度为500nm作为辅助层。将热释放胶带贴在带pmma辅助层和金保护层的碳纳米管阵列上表面,随后揭开热释放胶带,将带有碳纳米管的面贴附在pi衬底上,随后加热130℃进行释放,清洗去胶和退火后发现碳纳米管和金属薄膜大面积褶皱和从目标衬底上脱离。硬质支撑层的缺失是造成这一现象的主要原因,由于热释放胶带在剥离碳纳米管过程中需要加载一定的负荷弯曲揭离,造成碳纳米管阵列上的金保护层在微区延展形成滑移,而在恢复平直后延展部分会形成交叠并转移压平在目标衬底上,从而形成大量微区的碳纳米管阵列的交叠,丧失单层阵列形貌。在去胶清洗过有机溶剂过程中,褶皱重叠的金属薄膜导致有机溶剂的渗入和区域应力的突变,碳纳米管与目标衬底的部分接触也较少此区域的范德华力吸附,从而导致部分区域的薄膜脱离。由于碳纳米管阵列本身的内在大应力,微区的剥落连带整体大面积的脱落剥离,造成转移的失败。
50.另外需要说明的是,在上述具体实施方式中所描述的各个具体技术特征,在不矛盾的情况下,可以通过任何合适的方式进行组合。为了避免不必要的重复,本发明对各种可能的组合方式不再另行说明。