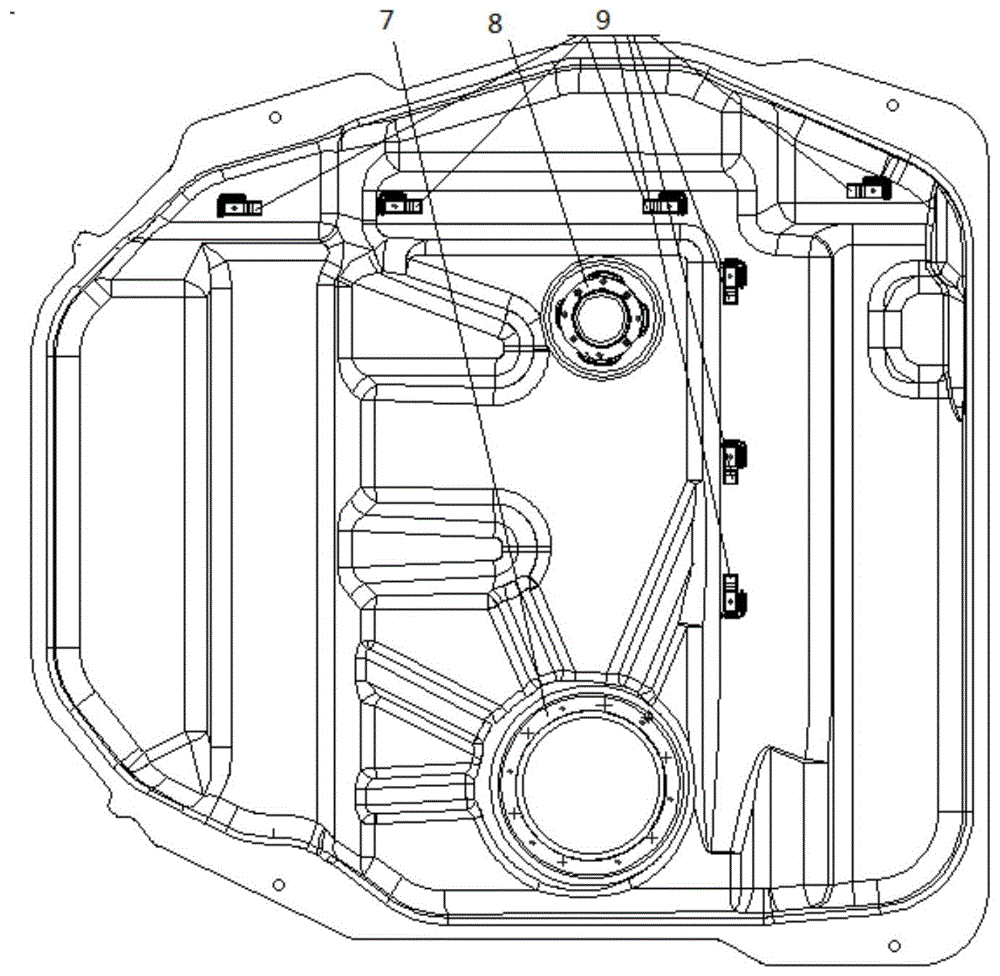
本申请涉及自动化领域,尤其涉及一种自动点焊系统。
背景技术:
:油箱上壳体有三种不同厚度的零件,例如管夹支架、小护圈和大护圈,如图1所示,需通过点焊将所述的不同厚度的零件固定连接到油箱壳体上,其中附图标记7指示大护圈、8指示小护圈、9指示管夹支架。点焊是焊接零件被压在两电极之间,当通过足够大的电流时,在零件接触处产生大量的电阻热,将中心加热成熔化状态,形成一个液态熔池,继续保持压力,断开电流,金属冷却后,形成一个焊点。点焊的原理就决定了不同零件厚度需要不同的焊接压力、焊接电流及焊接时间来保证焊接质量。目前所使用的普通中频点焊机虽然可以预存多套的焊接参数,但不能实现在焊接过程中各套焊接参数之间自动的切换,只能在停止焊接后手动选择焊接参数,其传统点焊的工艺是如图2所示将焊接工位A、B、C分别布置。传统点焊的工艺及布置存在如下的问题:①零件定位不准确:由于管夹支架9较小,只有通过人员放置在油箱壳体的焊接部位,其零件定位的准确度只有通过人来控制;②点焊质量波动较大:被点焊零件是否处于水平(即被点焊零件是否与点焊电极处于垂直状态)对点焊质量影响较大,而被点焊零件水平状态是通过人来保证,而人员拿持零件使之处于水平状态的难度较大,而且水平状态一致性也相差较大,故点焊质量波动较大;③效率低下:由于每个岗位都需要一个点焊人员、一个放置零件定位的辅助人员,需要两名人员的配合操作,而且需要三个工位才能完成壳体上的零件点焊,中间需要周转两次,造成效率的低下。技术实现要素:本申请的目的是提供一种自动点焊系统,以解决人工放置定位零件带来的零件一致性差、质量波动性大及效率低的问题。为实现上述目的,本申请提供了一种自动点焊系统,包括上电极、至少一个下电极和焊接机架;所述焊接机架包括能够在x方向上运动的x方向运动模组、能够在y方向上运动的y方向运动模组、能够在z方向上运动的z方向运动模组,所述上电极固定在所述z方向运动模组的底端,能够在所述x方向运动模组、y方向运动模组、z方向运动模组的带动下沿x、y、z方向移动;所述至少一个下电极为多点式固定电极,每个被点焊零件对应固定设置有一个所述下电极。优选地,还包括直线导轨,所述焊接机架能够在所述直线导轨上沿x、y方向移动。优选地,所述下电极中设置有磁铁,用于固定被点焊零件。优选地,还包括仿形夹具,所述仿形夹具根据被点焊壳体和被点焊零件设置。优选地,所述仿形夹具与所述下电极形成为一体。优选地,所述x方向运动模组和所述y方向运动模组与伺服电机连接,所述z方向运动模组与气缸连接。优选地,所述上电极和所述下电极均与焊接变压器连接,所述焊接变压器与焊接控制器连接。优选地,还包括PLC控制器,所述焊接控制器、所述伺服电机和所述气缸均与所述PLC控制器连接。由以上技术方案可知,本申请的自动点焊系统将传统的上、下电极固定、通过移动壳体来实现多零件、多焊点的点焊,改变为被点焊壳体及零件固定,通过固定多个所述下电极、移动所述上电极的方式来实现多零件、多焊点的点焊。附图说明图1为油箱壳体上的零件点焊示意图;图2为传统点焊工艺的布置图;图3为本申请一种实施例提供的自动点焊系统的俯视图。附图标记:1-焊接台、2-上电极、3-下电极、4-焊接机架、41-x方向运动模组、42-y方向运动模组、43-z方向运动模组、5-直线导轨、6-仿形夹具、7-大护圈、8-小护圈、9-管夹支架。具体实施方式为了使本领域的技术人员更好地理解本申请的技术方案,下面将结合附图对本申请作进一步的详细介绍。如前所述,需通过点焊将不同厚度的零件固定连接到油箱壳体上,点焊的原理决定了不同零件厚度需要不同的焊接压力、焊接电流及焊接时间来保证焊接质量。例如某油箱壳体上零件焊接参数差异主要如表1所示。表1油箱壳体上零件焊接参数差异表油箱壳体传统点焊的工艺参数如表2所示。表2油箱壳体传统点焊的工艺参数表序号焊接工位一A焊接工位二B焊接工位三C焊接零件7件管夹支架1件小护圈1件大护圈焊接压力0.35MPa0.4MPa0.4MPa焊接电流6.5KA8.0KA8.4KA焊接时间10周12周14周焊接设备63KVA中频点焊机100KVA中频点焊机100KVA中频点焊机人员配置2人2人2人油箱壳体传统点焊的布置如图1所示,存在零件定位不准确、一致性差、点焊质量波动较大及效率低下等问题。为解决上述问题,本申请提供了一种自动点焊系统的实施例。图3为本申请一种实施例提供的自动点焊系统的结构示意图。如图3所示,一种自动点焊系统,包括焊接台1,还包括上电极2、至少一个下电极3,焊接机架4;所述焊接机架4包括能够在x方向上运动的x方向运动模组41、能够在y方向上运动的y方向运动模组42、能够在z方向上运动的z方向运动模组43,所述上电极2固定在所述z方向运动模组43的底端;所述x方向运动模组41和所述y方向运动模组42与伺服电机(未示出)连接,所述z方向运动模组43与气缸(未示出)连接;所述至少一个下电极3为多点式固定电极,每个被点焊零件对应固定设置有一个所述下电极3。本申请实施例的自动点焊系统,被点焊壳体及零件固定,通过固定多下电极、移动上电极式来实现多零件、多焊点的点焊。所述下电极3为多点固定式电极,一个被点焊零件对应一个固定的所述下电极3,所述焊接机架4为可移动龙门式结构,所述x方向运动模组41和所述y方向运动模组42通过伺服电机的驱动实现移动,所述z方向运动模组43通过气缸的驱动实现移动,从而实现上电极2在x、y、z三个相互垂直方向上的移动。本申请实施例的自动点焊系统可以将某油箱壳体上不同厚度零件的三个工艺过程集成到一个工位上,实现一次性自动点焊。本申请实施例的自动点焊系统还包括直线导轨5,所述焊接机架4在所述直线导轨5上可实现x或y方向的移动。本申请实施例的自动点焊系统还包括仿形夹具6,作为被点焊壳体的定位装置,所述仿形夹具6与气缸连接。所述仿形夹具6根据被点焊壳体的外形和被点焊零件的位置设置。既要保证被点焊壳体的定位一致性,同时也要保证被点焊零件的定位的准确性、可调节性及可靠性。点焊时,先将被点焊零件放置在所述仿形夹具6的指定位置,再放置被点焊壳体,例如油箱壳体,放置完成后启动控制按钮,通过气缸自动夹持来实现点焊过程中零件始终处于水平的位置,保持其一致性,降低了焊点质量的波动。为解决由于零件小造成定位困难的问题,可以将固定式的所述下电极3与所述仿形夹具6合二为一,形成为一体,既作为点焊的下电极3,也作为被点焊壳体的定位夹具,同时在所述下电极3中镶嵌强力磁铁,解决小零件装夹不可靠、易脱落及电机干涉的问题。仿形夹具6可以通过螺钉与焊接机架4联接,同时通过螺钉与焊接设备的下导电板联结。本申请实施例的自动点焊系统中,所述上电极2和所述下电极3均与焊接变压器连接,所述焊接变压器与焊接控制器连接。本申请实施例的自动点焊系统还可以包括PLC控制器,所述焊接控制器、所述伺服电机和所述气缸均与所述PLC控制器连接。本申请实施例中所述焊接变压器、焊接控制器及PLC控制器均未在附图中示出。点焊过程中需要自动切换不同的点焊参数,本申请实施例先在焊接控制器内设置适合不同零件厚度的多套点焊参数,以不同的代号表示不同的整套点焊参数,再通过增加PLC控制器对每一点的点焊参数直接调用相应的点焊参数代号,实现在点焊过程中每一点的焊接参数自动的切换,从而解决点焊过程中由于被点焊零件厚度不同需要不同的点焊参数问题。所述焊接变压器可以提供不同等级的焊接电压。具体实施时,根据工艺方案,考虑到产能的均衡及人员效率的问题,将工艺布置成并排的两台同样的设备,配置一名操作员工,操作员工装夹好被点焊零件的情况下,按下启动按钮,就可以取下另一工位点焊好的壳体零件,继续装夹新的零件,从而提升人员效率。以油箱壳体的点焊为例,具体实施时的操作过程如下:第一步:操作者先将管夹支架8等小零件放置在仿形夹具6上,再将壳体放置在仿形夹具6处,PLC控制器控制气缸自动夹持仿形夹具6,来实现点焊过程中零件始终处于水平的位置,保持其一致性;PLC控制器将点焊参数发送焊接控制器,焊接控制器控制焊接变压器提供适合电压给所述上电极2和所述下电极3,所述上电极2通过焊接机架4移动到对应的管夹支架8的位置,焊接压力为0.35MPa,焊接电流为6.5KA;管夹支架8被压在所述上电极2和所述下电极3之间,在焊接压力为0.35MPa、焊接电流为6.5KA情况下,在管夹支架8与壳体接触处产生大量的电阻热,将中心加热成熔化状态,形成一个液态熔池,继续保持压力,断开电流,金属冷却后,形成一个焊点;第二步:点焊大护圈7和小护圈8,调整焊接压力为0.4MPa,焊接电流为8.0KA,所述上电极2通过焊接机架4先后移动至大护圈7和小护圈8位置进行点焊;第三步:自动焊接完成后,气缸驱动仿形夹具6自动打开,操作者取下焊接好的零件,进入下一个循环。通过本申请实施例的自动点焊系统,油箱壳体的点焊工艺具有以下效果:(1)节省5个操作人员的配置,将会节省50万/年的用工成本5*10万/年·人=50万/年;(2)传统点焊工艺需要三台设备,预计一年消耗78690度电:(63KVA/h+100KVA/h+100KVA/h)*0.2(设备耗电系数)*8h(工作时间)*0.85(设备利用率系数)*220天/年(工作天数)=78690度;新点焊工艺需要两台设备,预计一年消耗59840度电:(100KVA/h+100KVA/h)*0.2(设备耗电系数)*8h(工作时间)*0.85(设备利用率系数)*220天/年(工作天数)=59840度,节省能耗15080元:(78690度-59840度)*0.8元/度=15080元;每年将节约费用约52万。本申请实施例将壳体上多零件、多焊点、不同厚度、不同焊接参数的点焊方式从传统的上、下电极固定、通过移动壳体来实现多零件、多焊点的点焊,改变为被点焊壳体及零件固定,通过固定多个下电极、移动上电极来实现多零件、多焊点的点焊。本申请实施例将传统多工位集成为一个工位,减少人员的配置,提升生产效率。通过增加PLC控制器、伺服电机等来实现多焊点的一次性自动焊接,通过PLC控制器,实现每个焊点可以调用独立的焊接系统参数,通过仿形夹具实现焊点位置一致性及被点焊零件的水平状态,降低了焊点质量的波动。解决了传统手工焊接的焊接零件位置一致性差、焊接质量波动大的问题,同时减少了操作员工的定员,每年节省约52万元的成本。以上只通过说明的方式描述了本申请的某些示范性实施例,毋庸置疑,对于本领域的普通技术人员,在不偏离本申请的精神和范围的情况下,可以用各种不同的方式对所描述的实施例进行修正。因此,上述附图和描述在本质上是说明性的,不应理解为对本申请权利要求保护范围的限制。当前第1页1 2 3