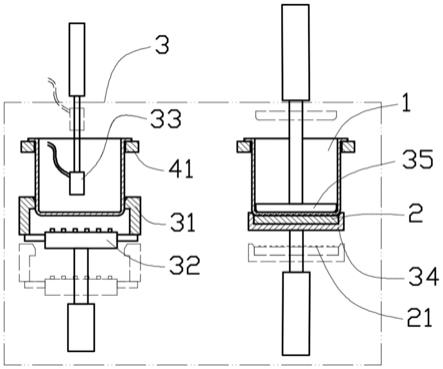
[0001]
本发明涉及锅具加工技术领域,具体涉及一种熔融态多点式锅底贴合工艺及其生产装置。
背景技术:[0002]
锅具通常用来烹煮食物,因此为了使用安全多使用铁质或者不锈钢材质的作为内层,同时为了保证锅体的导热性,需要在锅体内部包裹铝层,使得锅体整体的导热性能良好。传统的加工工艺通常直接将铝层附着贴合在锅体底部,贴合时使用片层材料进行贴合,这样使得锅体内部钢铁层与铝制层之间贴合面积较小,容易产生分离隔层现象,造成锅体的导热性能变差。在传统的钢铁层和铝制层贴合工艺中,需要同时对贴合位置进行加热,但是由于钢铁熔点和铝的熔点差距较大,比较难以控制温度,使得贴合过程更加困难。另外在锅具加工过程中,锅体通常采用拉伸工艺制造而成,使得锅体中具有应力,这种应力容易对锅体底部造成破坏。
技术实现要素:[0003]
针对以上问题,本发明提供一种只对锅体钢铁层进行加热,然后通过热传导的方式使得钢铁层与铝制层之间具有更好贴合的熔融态多点式锅底贴合工艺。
[0004]
本发明解决其技术问题所采用的技术方案是:一种熔融态多点式锅底贴合工艺,它包括以下加工步骤:
[0005]
一、将钢铁类金属板材拉伸成型锅体;
[0006]
二、将成型后锅体开口朝上从上部夹取送入贴合烤箱中;
[0007]
三、在贴合烤箱中,将所述锅体从中间靠下位置通过加热罩卡住,形成下部敞开的加温腔;
[0008]
四、在上步的加工腔中通过高温加热,将锅体下部表面加热到1400-1600℃,使得锅体下部形成熔融状态,锅体上部通入氮气,使得锅体上步保持固体状态,停止加热,将上部带有凸点的铝板放入到锅体下部,然后通过模具将铝板向上压与锅体底部贴合;
[0009]
五、将锅体冷却从壳体中取出。
[0010]
作为优选,所述锅体内部的钢铁板材为不锈钢材料。
[0011]
作为优选,步骤四中使用的加热方式为火焰加热,步骤四中所述锅体下部加热时间小于60秒。
[0012]
作为优选,步骤四中停止加热后到铝板与锅体底部贴合时间小于30秒。
[0013]
一种步骤三中所述的用于熔融态多点式锅底贴合工艺的贴合烤箱,所述贴合烤箱包括壳体,所述壳体设计有水平的腔体,所述壳体内装配有水平的夹钳,所述夹钳夹住所述锅体的上部,所述夹钳装配在运动线上,所述运动线控制夹钳在所述壳体内从左到右移动两个工位,当锅体在第一个工位时,锅体的下部装配有环形的加热罩,所述加热罩的下部中间位置固定装配有水平放置的喷火盘,所述加热罩与喷火盘下部装配有可以控制二者上下
运动的升降模块,当所述加热罩与喷火盘被升降模块升到上部位置时,所述加热罩的环形内边贴紧在所述锅体侧边靠下位置,所述加热罩与锅底形成向下开口的加温腔,所述喷火盘上喷射有向上的火焰对锅底进行加热,将锅底加热到熔融状态;所述锅体正上方设计有向下的喷气管,所述喷气管上部装配有可以控制其上下运动的升降模块,当升降模块控制喷气管运动到下部位置,喷气管深入锅体内部正对锅底,所述喷气管喷射氮气;在所述锅体运动到所述壳体内部第二工位时,所述锅体的下部设计有上部敞开的模具,所述模具内水平放置有圆形的铝板,所述铝板上部设计有三个以上的凸点,所述模具下部设计有控制模具上下运动的升降模块,在第二工位所述锅体的上部装配有水平的压板,所述压板上部设计有控制所述压板上下运动的升降模块,当压板被升降模块运动到下部位置时,对所述锅体向上进行限位,所述模具被升降模块控制向上运动,使得铝板贴附在所述锅底下部。锅体下部通过第一工位的喷火盘加热到熔融状态,这时所述铝板贴合时铝板凸点将锅体下部顶压变形,使得铝板贴附在锅体下部,同时铝板吸热到达熔点与锅体下部进行进一步熔合,这时锅体由于铝板吸热,使得锅体底部降温固化,使得两种金属交融。
[0014]
作为优选,所述升降模块为气缸。
[0015]
作为优选,所述贴合烤箱的前部设计有送料线,所述送料线与贴合烤箱之间装配有所述运动线,所述运动线带动所述夹钳循环运动,所述夹钳在送料线上运动时,具有进料和出料两个工位,所述夹钳设计有可以开合和夹紧的结构,所述锅体在步骤一拉伸成型后通过送料线运送到所述进料工位,夹钳将锅体夹紧送入贴合烤箱的壳体内,当锅体贴合铝板后,运动线将锅体从壳体内送入到送料线的出料工位,通过送料线运出。
[0016]
作为优选,所述夹钳的前端为左右开合的两个半圆环,所述夹钳的内侧装配有弹性层,所述夹钳通过弹性层将锅体弹性加紧。
[0017]
本发明的有益效果在于:本熔融态多点式锅底贴合工艺主要用来对蒸煮的圆柱形锅体底部进行铝板复合加工,该工艺将锅体底部加工成熔融状态,然后通将铝板的凸点面进行贴合,这时铝板的凸点可以将锅体底部挤压变形使得锅体底部产生凹陷,然后铝板在贴合过程中吸热,由于铝材的熔化温度远远低于钢铁类材料,这时铝材表面会吸热变成熔化状态,与锅体底部原来熔融状态的钢铁材料进行熔合,同时原来的锅体的钢铁材料开始凝固,随着热量的散失,锅体底部的钢铁层和铝层完全交融,由于原来凸点结构的设计,使得二者材料的熔合面积和深度大大高于传统的加工方式,使得锅体底部交融状态更好。这样导热性能更好,同时锅体底部更加的牢固,不易损坏,锅体使用寿命更长。在锅体贴合前氮气的通入,可以带走部分热量,使得锅体内部底边不会熔化,保证了锅底的形状。同时这种贴合加工工艺通过高温加热可以有效的去除锅底的应力,防止锅体在以后的加热中产生变形。
附图说明
[0018]
图1是用于熔融态多点式锅底贴合工艺的贴合烤箱正向剖面的结构示意图。
[0019]
图2是用于熔融态多点式锅底贴合工艺的贴合烤箱俯视方向的结构示意图。
[0020]
图3是锅体与铝板贴合前的剖面结构示意图。。
具体实施方式
[0021]
下面结合实施例对本发明进一步说明:
[0022]
如图1、图2和图3的实施例中,该一种熔融态多点式锅底贴合工艺,它包括以下加工步骤:
[0023]
一、将钢铁类金属板材拉伸成型锅体;在本实施例中,使用食品级的不锈钢为锅体1的主要原料,采用传统的拉伸工艺进行加工成型;
[0024]
二、将成型后锅体1开口朝上从上部夹取送入贴合烤箱中;所述贴合烤箱主要用来将铝板2与锅体1底部进行加热贴合;
[0025]
三、在贴合烤箱中,将所述锅体从中间靠下位置通过加热罩31卡住,形成下部敞开的加温腔;
[0026]
四、在上步的加工腔中通过高温加热,将锅体下部表面加热到1400-1600℃,这个温度可以覆盖多数钢铁金属的熔点,保证锅体1下部形成熔融状态,锅体1上部通入氮气,使得锅体1上步保持固体状态,停止加热,将上部带有凸点21的铝板放入到锅体1下部,然后通过模具21将铝板2向上压与锅体1底部贴合;
[0027]
五、将锅体冷却从壳体中取出。
[0028]
本熔融态多点式锅底贴合工艺主要用来对蒸煮的圆柱形锅体底部进行铝板复合加工,该工艺将锅体1底部加工成熔融状态,然后通将铝板2的凸点21面进行贴合,这时铝板2的凸点21可以将锅体1底部挤压变形使得锅体1底部产生凹陷,然后铝板2在贴合过程中吸热,由于铝材的熔化温度远远低于钢铁类材料,这时铝材表面会吸热变成熔化状态,与锅体1底部原来熔融状态的钢铁材料进行熔合,同时原来的锅体1的钢铁材料开始凝固,随着热量的散失,锅体底部的钢铁层和铝层完全交融,由于原来凸点21结构的设计,使得二者材料的熔合面积和深度大大高于传统的加工方式,使得锅体底部交融状态更好。在锅体1贴合前氮气的通入,可以带走部分热量,使得锅体1内部底边不会熔化,保证了锅底的形状。同时这种贴合加工工艺通过高温加热可以有效的去除锅底的应力,防止锅体1在以后的加热中产生变形。
[0029]
在具体实施时,步骤四中使用的加热方式为火焰加热,火焰加热方式简单,成本较低,容易高温加热,便于控制,安全性更好。步骤四中所述锅体1下部加热时间小于60秒。即在步骤四中,采用快速加热,这样不仅更加的节能,同时可以避免锅体整体温度升高变形。步骤四中停止加热后到铝板与锅体底部贴合时间小于30秒。快速贴合有助于所述锅体1温度的快速下降,防止积聚在锅体1底部的热量扩散到整个锅体,使得贴合效果更好,也可以有效防止锅体加工中变形。
[0030]
如图1、图2所示,本熔融态多点式锅底贴合工艺的主要贴合过程通过贴合烤箱来完成,所述贴合烤箱包括壳体3,所述壳体3设计有水平的腔体,所述壳体3内装配有水平的夹钳41,所述夹钳41夹住所述锅体1的上部,所述夹钳41装配在运动线4上,所述运动线4控制夹钳41在所述壳体3内从左到右移动两个工位,当锅体1在第一个工位时,锅体1的下部装配有环形的加热罩31,所述加热罩31的下部中间位置固定装配有水平放置的喷火盘32,所述加热罩31与喷火盘32下部装配有可以控制二者上下运动的升降模块。在本实施例中所述加热罩31和所述喷火盘32一体连接,这样便于整体控制。当所述加热罩31与喷火盘32被升降模块升到上部位置时,所述加热罩31的环形内边贴紧在所述锅体1侧边靠下位置,所述加
热罩31与锅底形成向下开口的加温腔,所述喷火盘32上喷射有向上的火焰对锅底进行加热。该加温腔上部封闭,这样当喷火盘对所述锅体1底部进行加热时,热量容易积聚,加工效果更好,可以快速的将锅底加热到熔融状态。所述锅体1正上方设计有向下的喷气管33所述喷气管33上部装配有可以控制其上下运动的升降模块,当升降模块控制喷气管33运动到下部位置。当喷火盘32在下部对锅体1底部加热时,所述喷气管33深入锅体1内部正对锅底,所述喷气管33喷射氮气。这样可以保证在锅体1下部熔融时,而锅体1内部锅体仍然保持固体状态,便于下部的加工。
[0031]
将锅体底部在第一工位加热成熔融状态时,快速通过所述运动线4的夹钳41将所述锅体33运动到所述壳体1内部第二工位,这时所述锅体1的下部设计有上部敞开的模具34,所述模具34内水平放置有圆形的铝板2,所述铝板2上部设计有三个以上的凸点21,所述模具4下部设计有控制模具34上下运动的升降模块,在第二工位所述锅体1的上部装配有水平的压板35,所述压板35上部设计有控制所述压板上下运动的升降模块,当压板35被升降模块运动到下部位置时,对所述锅体1向上进行限位,所述模具34被升降模块控制向上运动,使得铝板2贴附在所述锅底下部。这时锅体1下部仍保持通过第一工位的喷火盘32加热到熔融状态,这时所述铝板2贴合时铝板2凸点21将锅体1下部顶压变形,使得铝板2贴附在锅体1下部,同时铝板2吸热到达熔点与锅体1下部进行进一步熔合,这时锅体1由于铝板吸热,使得锅体1底部降温固化,使得两种金属交融。
[0032]
在具体设计时,如图1和图2所示,所述升降模块为气缸。所述贴合烤箱的前部设计有送料线5,所述送料线5与贴合烤箱4之间装配有所述运动线,所述运动线4带动所述夹钳41循环运动,所述夹钳41在送料线5上运动时,具有进料51和出料52两个工位,所述夹钳41设计有可以开合和夹紧的结构,所述锅体1在步骤一拉伸成型后通过送料线5运送到所述进料51工位,夹钳41将锅体1夹紧送入贴合烤箱的壳体3内,当锅体1贴合铝板2后,运动线4将锅体1从壳体3内送入到送料线5的出料52工位,通过送料线5运出。这种设计使得,运动线4上的夹钳不停循环运动,整个加工过程,所述送料线5在进料51位置通过夹钳41向贴合烤箱内送入刚拉伸完成的锅体1,在贴合烤箱内完成锅底与铝板2的贴合后,通过运动线4的夹钳41重新从贴合烤箱内将贴合铝板2后的锅体重新送回所述送料线5的出料52位置。这种产线布局,没有回复运动,更加节能,同时整条生产线生产效率大大提高。
[0033]
在具体设计时时,如图1所示,所述夹钳41的前端为左右开合的两个半圆环,所述夹钳的内侧装配有弹性层42,所述夹钳41通过弹性层42将锅体1弹性加紧。
[0034]
以上所述仅为本发明的较佳方式,并不用以限制本发明,凡在本发明的精神和原则之内,所作的任何修改、等同替换、改进等,均应包含在本发明的保护范围之内。