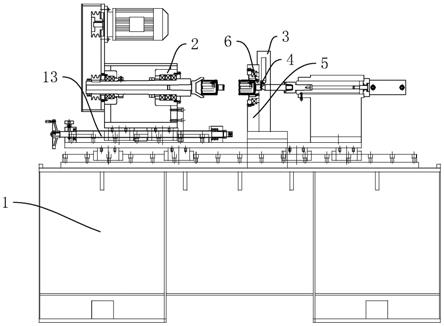
[0001]
本申请涉及万向节加工的领域,尤其是涉及一种机床及利用该机床加工万向节花键轴的方法。
背景技术:[0002]
万向节是汽车底盘传动系统中传递动力的重要部件,其驱动轴的作用是与变速箱、驱动桥一起将发动机的动力传递给车轮,使汽车产生驱动力。在驱动轴与万向节安装的端部通常设置有花键部,在驱动轴靠近花键部的位置开设有用于供扣环卡接的环槽。
[0003]
在加工驱动轴的环槽时,通常先对驱动轴夹持,之后通过车刀对驱动轴进行车削,但是针对上述中的相关技术,发明人发现在将驱动轴装车后,容易出现装配不合适的问题。
技术实现要素:[0004]
为了改善万向节装配时的装配精度,本申请提供一种机床及利用该机床加工万向节花键轴的方法。
[0005]
第一方面,本申请提供一种机床,采用如下的技术方案:一种机床,包括床身、设置于床身的主轴以及设置于床身的刀架,所述刀架连接有铣刀,所述床身固定有基准支架,所述基准支架与主轴同轴,所述基准支架转动嵌设有供万向节球笼抵接的抵靠部。
[0006]
通过采用上述技术方案,抵靠部用于供球笼抵接并对球笼实现定位,从而可以始终将球笼定位在相同的位置,提高定位精度,且通过基准支架,使得球笼杯体部分抵靠在抵靠部,从而扣环槽的基准可以以杯体到花键槽的长度来确定,使得加工基准与装配基准重合,降低由于热处理导致的形变误差,进而从源头提高装配精度。
[0007]
优选的,所述基准支架开设有安装槽,所述安装槽内壁设置有轴承,所述抵靠部过盈配合于轴承内壁。
[0008]
通过采用上述技术方案,通过在安装槽内设置轴承,使得抵接部在转动时更加顺畅,且对抵接部起到旋转支撑作用。
[0009]
优选的,所述抵靠部包括一与球笼端面抵接的抵接板,所述抵接板开设有供花键轴伸出的通孔,所述抵靠部还包括用于嵌设球笼的驱动部,所述驱动部开设有与球笼外壁形状适应的驱动腔。
[0010]
通过采用上述技术方案,工作时将球笼的花键轴伸出通孔,且球笼的侧壁抵接在抵接板上,当球笼转动时,由于驱动腔形状与球笼外壁相适应,通过球笼可带动抵接板同步转动。
[0011]
优选的,所述抵接板宽度与实际装车时同一位置处的轴承宽度相等。
[0012]
通过采用上述技术方案,通过抵接板可以模拟汽车实际安装结构,标定球笼位置,提高切割精度。
[0013]
优选的,所述主轴滑移连接于床身,所述床身设置有用于驱动主轴沿轴向移动的
丝杆。
[0014]
通过采用上述技术方案,通过丝杆可以驱动主轴移动,实现主轴的位置调节,从而适应不同尺寸的工件。
[0015]
第二方面,本申请提供一种加工万向节花键轴的方法,采用如下的技术方案:一种加工万向节花键轴的方法,包括如下步骤,步骤s1,安装基准,将基准支架固定于床身,且控制基准支架与主轴同心;步骤s2,确定对刀基准,将铣刀的基准线调整至抵靠部外侧壁,并记抵靠部外侧壁为0点;步骤s3,工件加装,在主轴加装碗型顶针,通过碗型顶针将球笼顶紧于抵靠部,使得球笼的花键轴穿过通孔,球笼的外壳嵌设于驱动腔;步骤s4,计算装车时轴承端面距离扣环槽的实际距离并记为l1,将铣刀从0点移动至l1点,并对花键轴进行铣削开槽。
[0016]
通过采用上述技术方案,通过改变传统基准,实现割槽基准与装车基准的统一,进而即使花键轴端部经过热处理,也可以在一定程度上减小扣环槽的装车误差,提高装配精度。
[0017]
优选的,步骤s3之后通过尾座顶紧至花键轴的端面,实现对工件夹紧固定。
[0018]
通过采用上述技术方案,尾座顶紧工件,从而实现对工件的固定,提高工件稳定性。
[0019]
优选的,步骤s2中,可根据不同型号的球笼选用适应尺寸的抵接部。
[0020]
通过采用上述技术方案,抵接部可根据不同型号的工件实现更换,进而提高适应性。
附图说明
[0021]
图1是本发明的整体结构示意图。
[0022]
图2是本发明的基准支架的结构示意图。
[0023]
附图标记说明:1、床身;2、主轴;3、刀架;4、铣刀;5、基准支架;6、抵靠部;7、安装槽;8、轴承;9、抵接板;10、通孔;11、驱动部;12、驱动腔;13、丝杆。
具体实施方式
[0024]
以下结合附图1-2对本申请作进一步详细说明。
[0025]
本申请实施例公开一种机床。参照图1和图2,该机床包括床身1以及设置在床身1的主轴2以及尾座,在床身1上还设置有可移动刀架3,在刀架3上安装有铣刀4。在床身1上设置有滑轨,主轴2滑移连接于滑轨,在床身1上转动连接有丝杆13,主轴2螺纹连接于丝杆13,从而当转动丝杆13时,可以驱动主轴2沿轴向移动。
[0026]
在床身1上且位于主轴2和尾座之间的位置通过螺栓固定连接有基准支架5,基准支架5开设有圆形的安装槽7,且安装槽7与主轴2同轴,在基准支架5的安装槽7里转动嵌设有抵靠部6,万向节的球笼可以抵接在抵靠部6上。
[0027]
为了实现抵靠部6的转动嵌设,在安装槽7内壁过盈配合连接有轴承8,抵靠部6的外壁过盈配合在轴承8内圈的内壁。通过设置轴承8使得抵靠部6能够转动嵌设在安装槽7
内,从而当球笼抵接在抵靠部6时,抵靠部6能够与球笼同步转动。
[0028]
抵靠部6包括与轴承8内圈连接的驱动部11,驱动部11的端面一体连接有抵接板9,抵接板9上开设有供花键轴伸出的通孔10,驱动部11开设有与球笼外壁形状适应的驱动腔12,从而当将球笼嵌设于驱动腔12内时,球笼的花键轴可穿设在通孔10内并伸出通孔10。
[0029]
其中抵接板9的宽度与实际装车时同一位置处的轴承8的宽度相等,从而模拟实际装车时的装配关系,便于后续铣削扣环槽时的基准标定。
[0030]
本实施例同时提供一种加工万向节花键轴的方法,包括如下步骤,步骤s1,安装基准,将基准支架5固定于床身1,且控制基准支架5与主轴2同心;步骤s2,确定对刀基准,将铣刀4的基准线调整至抵靠部6外侧壁,并记抵靠部6外侧壁为0点;步骤s3,工件加装,在主轴2加装碗型顶针,通过碗型顶针将球笼顶紧于抵靠部6,使得球笼的花键轴穿过通孔10,球笼的外壳嵌设于驱动腔12,并且尾座移动并通过尾座上的顶针顶紧于花键轴的端面顶针孔内;步骤s4,计算装车时轴承8端面距离扣环槽的实际距离并记为l1,将铣刀4从0点移动至l1点,并对花键轴进行铣削开槽。从而通过改变传统基准,实现割槽基准与装车基准的统一,进而即使花键轴端部经过热处理,也可以在一定程度上减小扣环槽的装车误差,提高装配精度。
[0031]
以上均为本申请的较佳实施例,并非依此限制本申请的保护范围,故:凡依本申请的结构、形状、原理所做的等效变化,均应涵盖于本申请的保护范围之内。