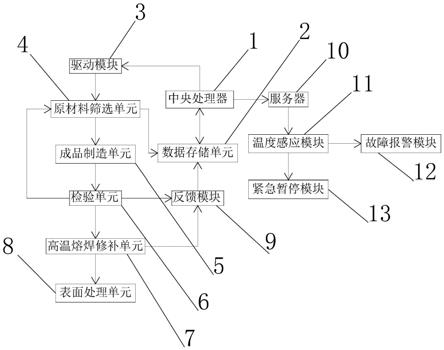
[0001]
本发明涉及汽车车轮钢圈制造技术领域,具体为一种汽车车轮钢圈的制造系统及工艺。
背景技术:[0002]
近年来,汽车数量快速发展,车轮的需求量也逐年增加,而车轮最重要的组成部分就是钢圈,钢圈也叫做轮毂,可以说是汽车的“鞋”。中国有句俗话,脚下没好鞋,为人穷半截。这话放到汽车上同样适用。如今一辆好车的轮毂肯定不会小,改装的时候轮毂也是很多人的第一个切入点。因为不但当爱车一下子漂亮很多,而且直接提升汽车某个方面的性能,汽车长时间的使用,钢圈的好坏决定这汽车的命运,为此我们需要解决钢圈的承载能力与其强度,且现有技术生产出来的车轮钢圈的质量残次品较多,需要通过反厂进行维修,费时费力,且制造成本较高,质量较平庸。
技术实现要素:[0003]
本发明的目的在于提供一种汽车车轮钢圈的制造系统及工艺,以解决上述背景技术中提出的问题。
[0004]
为实现上述目的,本发明提供如下技术方案:一种汽车车轮钢圈的制造系统,包括中央处理器、数据储存单元、驱动模块、原材料筛选单元、成品制造单元、检验单元、高温熔焊修补单元、表面处理单元、反馈模块、服务器、温度感应模块、故障报警模块和紧急暂停模块,所述数据储存单元与中央处理器双向信号连接,所述中央处理器发射端与驱动模块接收端信号连接,所述驱动模块发射端与原材料筛选单元接收端信号连接,所述原材料筛选单元发射端与成品制造单元接收端信号连接,所述成品制造单元发射端与检验单元接收端信号连接,所述检验单元发射端与高温熔焊修补单元接收端信号连接,所述高温熔焊修补单元发射端与表面处理单元接收端信号连接,所述高温熔焊修补单元发射端与反馈模块接收端信号连接,所述反馈模块发射端与数据储存单元接收端信号连接,所述中央处理器发射端与服务器接收端信号连接,所述服务器发射端与温度感应模块接收端信号连接,所述温度感应模块发射端与故障报警模块接收端信号连接,所述温度感应模块发射端与紧急暂停模块接收端信号连接。
[0005]
优选的,所述检验单元发射端与原材料筛选单元接收端信号连接,所述检验单元发射端与反馈模块接收端信号连接。
[0006]
优选的,所述原材料筛选单元发射端与数据储存单元接收端信号连接。
[0007]
优选的,所述检验单元包括超声波探伤检测模块、高温无尘检测模块和低温无尘检测模块。
[0008]
优选的,所述成品制造单元包括切割熔融模块、压铸成型模块、卷圆模块、对焊模块、刮渣模块、扩口模块、滚型模块和扩张模块。
[0009]
优选的,所述数据储存单元包括数据删除模块和数据更新模块,所述数据更新模
块接收端与原材料筛选单元发射端信号连接。
[0010]
优选的,所述故障报警模块包括蜂鸣器和闪光灯,所述紧急暂停模块包括空气断电开关。
[0011]
一种汽车车轮钢圈的制造工艺,包括以下步骤:
[0012]
s1、通过设置有原材料筛选单元对钢块进行表面规格筛选,并通过采用检验单元对选取好的钢块进行内部探伤,进一步优质筛选;
[0013]
s2、通过将经过s1步骤挑选好的优质原材料通过切割熔融模块、压铸成型模块、卷圆模块、对焊模块、刮渣模块、扩口模块、滚型模块和扩张模块制成汽车车轮钢圈成品,在切割熔融模块中熔炼温度为1680-1980℃,在压铸成型模块中模具预热至400-450℃即可,开始进行压铸工作,整体压铸时间在15-25s内完成,同时通过采用温度感应模块对其进行监测;
[0014]
s3、对经过s2步骤中制好的成品件通过检验单元中超声波探伤检测模块、高温无尘检测模块和低温无尘检测模块进行多层次质量检测,其中高温无尘检测模块中温度为700-800℃,持续时间为10-15min,其中低温无尘检测模块中温度为-5℃以下;
[0015]
s4、对s3步骤中出现的不合格品通过高温熔焊修补单元7进行修补,修补后再次通过检验单元进行二次复检;
[0016]
s5、通过表面处理单元对s4步骤中复检后的成品和s3中首检的成品进行表面打磨、抛光,去毛刺;
[0017]
s6、常温放置1-2天后,对成品表面喷涂隔离漆,并进行包装,封箱处理。
[0018]
与现有技术相比,本发明的有益效果是:该汽车车轮钢圈的制造系统及工艺,能够使得车轮钢圈的质量得到保障,且其表面光滑,使得生产效率大幅度提高并减少了维护成本,能够提高钢圈的抗压性与其自身的强度,从而提高了车轮钢圈的使用寿命,其提高而了生产效率;通过采用温度感应模块对整个系统中温度进行监测,保证事故的及时处理和预防措施。
附图说明
[0019]
图1为本发明系统整体流程图;
[0020]
图2为本发明检验单元结构示意图;
[0021]
图3为本发明成品制造单元结构示意图;
[0022]
图4为本发明数据存储单元结构示意图。
[0023]
图中:1中央处理器、2数据储存单元、3驱动模块、4原材料筛选单元、5成品制造单元、6检验单元、7高温熔焊修补单元、8表面处理单元、9反馈模块、10服务器、11温度感应模块、12故障报警模块、13紧急暂停模块、14超声波探伤检测模块、15高温无尘检测模块、16低温无尘检测模块、17切割熔融模块、18压铸成型模块、19卷圆模块、20对焊模块、21刮渣模块、22扩口模块、23滚型模块、24扩张模块、25数据删除模块、26数据更新模块。
具体实施方式
[0024]
下面将结合本发明实施例中的附图,对本发明实施例中的技术方案进行清楚、完整地描述,显然,所描述的实施例仅仅是本发明一部分实施例,而不是全部的实施例。基于
本发明中的实施例,本领域普通技术人员在没有做出创造性劳动前提下所获得的所有其他实施例,都属于本发明保护的范围。
[0025]
请参阅图1-4,本发明提供一种技术方案:一种汽车车轮钢圈的制造系统,包括中央处理器1、数据储存单元2、驱动模块3、原材料筛选单元4、成品制造单元5、检验单元6、高温熔焊修补单元7、表面处理单元8、反馈模块9、服务器10、温度感应模块11、故障报警模块12和紧急暂停模块13,数据储存单元2与中央处理器1双向信号连接,中央处理器1发射端与驱动模块3接收端信号连接,驱动模块3发射端与原材料筛选单元4接收端信号连接,原材料筛选单元4发射端与成品制造单元5接收端信号连接,成品制造单元5包括切割熔融模块17、压铸成型模块18、卷圆模块19、对焊模块20、刮渣模块21、扩口模块22、滚型模块23和扩张模块24,原材料筛选单元4发射端与数据储存单元2接收端信号连接,数据储存单元2包括数据删除模块25和数据更新模块26,数据更新模块26接收端与原材料筛选单元4发射端信号连接,成品制造单元5发射端与检验单元6接收端信号连接,检验单元6包括超声波探伤检测模块14、高温无尘检测模块15和低温无尘检测模块16,检验单元6发射端与原材料筛选单元4接收端信号连接,检验单元6发射端与反馈模块9接收端信号连接,检验单元6发射端与高温熔焊修补单元7接收端信号连接,高温熔焊修补单元7发射端与表面处理单元8接收端信号连接,高温熔焊修补单元7发射端与反馈模块9接收端信号连接,反馈模块9发射端与数据储存单元2接收端信号连接,中央处理器1发射端与服务器10接收端信号连接,服务器10发射端与温度感应模块11接收端信号连接,温度感应模块11发射端与故障报警模块12接收端信号连接,温度感应模块11发射端与紧急暂停模块13接收端信号连接,故障报警模块12包括蜂鸣器和闪光灯,紧急暂停模块13包括空气断电开关,该汽车车轮钢圈的制造系统及工艺,能够使得车轮钢圈的质量得到保障,且其表面光滑,使得生产效率大幅度提高并减少了维护成本,能够提高钢圈的抗压性与其自身的强度,从而提高了车轮钢圈的使用寿命,其提高而了生产效率;通过采用温度感应模块11对整个系统中温度进行监测,保证事故的及时处理和预防措施。
[0026]
为解决某项该发明解决的问题,提出以下实施例:
[0027]
实施例一
[0028]
一种汽车车轮钢圈的制造工艺,包括以下步骤:
[0029]
s1、通过设置有原材料筛选单元4对钢块进行表面规格筛选,并通过采用检验单元6对选取好的钢块进行内部探伤,进一步优质筛选;
[0030]
s2、通过将经过s1步骤挑选好的优质原材料通过切割熔融模块17、压铸成型模块18、卷圆模块19、对焊模块20、刮渣模块21、扩口模块22、滚型模块23和扩张模块24制成汽车车轮钢圈成品,在切割熔融模块17中熔炼温度为1980℃,在压铸成型模块18中模具预热至450℃即可,开始进行压铸工作,整体压铸时间在25s内完成,同时通过采用温度感应模块对其进行监测;
[0031]
s3、对经过s2步骤中制好的成品件通过检验单元6中超声波探伤检测模块14、高温无尘检测模块15和低温无尘检测模块16进行多层次质量检测,其中高温无尘检测模块15中温度为800℃,持续时间为15min,其中低温无尘检测模块16中温度为-3℃;
[0032]
s4、对s3步骤中出现的不合格品通过高温熔焊修补单元7进行修补,修补后再次通过检验单元6进行二次复检;
[0033]
s5、通过表面处理单元8对s4步骤中复检后的成品和s3中首检的成品进行表面打磨、抛光,去毛刺;
[0034]
s6、常温放置2天后,对成品表面喷涂隔离漆,并进行包装,封箱处理。
[0035]
实施例二
[0036]
一种汽车车轮钢圈的制造工艺,包括以下步骤:
[0037]
s1、通过设置有原材料筛选单元4对钢块进行表面规格筛选,并通过采用检验单元6对选取好的钢块进行内部探伤,进一步优质筛选;
[0038]
s2、通过将经过s1步骤挑选好的优质原材料通过切割熔融模块17、压铸成型模块18、卷圆模块19、对焊模块20、刮渣模块21、扩口模块22、滚型模块23和扩张模块24制成汽车车轮钢圈成品,在切割熔融模块17中熔炼温度为1680℃,在压铸成型模块18中模具预热至400℃即可,开始进行压铸工作,整体压铸时间在15s内完成,同时通过采用温度感应模块对其进行监测;
[0039]
s3、对经过s2步骤中制好的成品件通过检验单元6中超声波探伤检测模块14、高温无尘检测模块15和低温无尘检测模块16进行多层次质量检测,其中高温无尘检测模块15中温度为700℃,持续时间为10min,其中低温无尘检测模块16中温度为-5℃;
[0040]
s4、对s3步骤中出现的不合格品通过高温熔焊修补单元7进行修补,修补后再次通过检验单元6进行二次复检;
[0041]
s5、通过表面处理单元8对s4步骤中复检后的成品和s3中首检的成品进行表面打磨、抛光,去毛刺;
[0042]
s6、常温放置1天后,对成品表面喷涂隔离漆,并进行包装,封箱处理。
[0043]
实施例三
[0044]
一种汽车车轮钢圈的制造工艺,包括以下步骤:
[0045]
s1、通过设置有原材料筛选单元4对钢块进行表面规格筛选,并通过采用检验单元6对选取好的钢块进行内部探伤,进一步优质筛选;
[0046]
s2、通过将经过s1步骤挑选好的优质原材料通过切割熔融模块17、压铸成型模块18、卷圆模块19、对焊模块20、刮渣模块21、扩口模块22、滚型模块23和扩张模块24制成汽车车轮钢圈成品,在切割熔融模块17中熔炼温度为1880℃,在压铸成型模块18中模具预热至430℃即可,开始进行压铸工作,整体压铸时间在20s内完成,同时通过采用温度感应模块对其进行监测;
[0047]
s3、对经过s2步骤中制好的成品件通过检验单元6中超声波探伤检测模块14、高温无尘检测模块15和低温无尘检测模块16进行多层次质量检测,其中高温无尘检测模块15中温度为750℃,持续时间为13min,其中低温无尘检测模块16中温度为-10℃;
[0048]
s4、对s3步骤中出现的不合格品通过高温熔焊修补单元7进行修补,修补后再次通过检验单元6进行二次复检;
[0049]
s5、通过表面处理单元8对s4步骤中复检后的成品和s3中首检的成品进行表面打磨、抛光,去毛刺;
[0050]
s6、常温放置1.5天后,对成品表面喷涂隔离漆,并进行包装,封箱处理。
[0051]
综上可得:该汽车车轮钢圈的制造系统及工艺,能够使得车轮钢圈的质量得到保障,且其表面光滑,使得生产效率大幅度提高并减少了维护成本,能够提高钢圈的抗压性与
其自身的强度,从而提高了车轮钢圈的使用寿命,其提高而了生产效率;通过采用温度感应模块11对整个系统中温度进行监测,保证事故的及时处理和预防措施。
[0052]
尽管已经示出和描述了本发明的实施例,对于本领域的普通技术人员而言,可以理解在不脱离本发明的原理和精神的情况下可以对这些实施例进行多种变化、修改、替换和变型,本发明的范围由所附权利要求及其等同物限定。