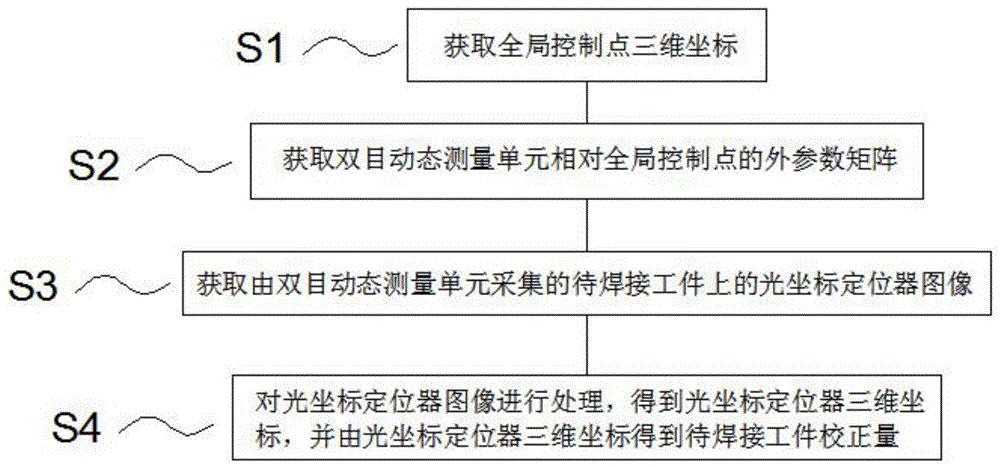
本发明涉及焊接定位方法领域,具体是一种大型钢筋骨架焊接的自动校准方法和系统。
背景技术:
:焊接技术是船舶建造工程的关键工艺技术。目前,世界各主要造船企业在20世纪90年代中期已普遍完成了一轮现代化改造。同时,在此基础上又陆续启动了新一轮现代化改造计划。投资目标大多集中于高新技术,投资力度进一步加大,大量采用全新的造船焊接工艺流程,高度柔性的自动化焊接生产系统和先进的焊接机器人技术,以保证这些造船强国在国际竞争中具有独特的技术优势。当前在船舶建造过程中的大型钢筋骨架焊接已经普遍采用焊接机器人、用于待焊接件调节的自动调整平台等自动化设备,以提高生产效率。但是,焊接过程的监控、反馈、校准调整等一系列对甲板焊接拼装精度影响至关重要的环节自动化程度较低,这是制约焊接精度提示的关键所在。技术实现要素:本发明的目的是提供一种大型钢筋骨架焊接的自动校准方法和系统,以解决现有技术船舶建造过程中大型钢筋骨架焊接时监控、反馈、校准调整自动化程度低的问题。为了达到上述目的,本发明所采用的技术方案为:一种大型钢筋骨架焊接的自动校准方法,包括以下步骤:s1、获取每个全局控制点在世界坐标系下的三维坐标;s2、接收多个双目动态测量单元分别采集的至少三个全局控制点的图像,结合所采集的全局控制点在世界坐标系下的三维坐标,得到每个双目动态测量单元相对全局控制点的外参数矩阵;s3、接收多个双目动态测量单元分别实时采集的各自测量区域中待焊接工件上所有光坐标定位器的图像;s4、结合每个双目动态测量单元的内参数和步骤s2得到的相对全局控制点的外参数矩阵,对每个双目动态测量单元采集的图像进行处理,得到每个光坐标定位器在世界坐标系下的三维坐标;然后基于预设的每个待焊接工件在世界坐标系下的三维坐标以及计算得到的每个待焊接工件上光坐标定位器的三维坐标,得到每个待焊接工件的校正量,以便基于所述校正量对待焊接工件进行调整完成焊接作业。本发明所述的一种大型钢筋骨架焊接的自动校准方法步骤s1中,使用全站仪配合摄影测量系统测量得到每个全局控制点在世界坐标系下的三维坐标,其过程如下:通过全站仪采集一条对角线的距离,得到作为摄影测量的比例尺;通过摄影测量系统采集每个全局控制点上编码点的多个图像,并对图像进行处理得到编码点中心在世界坐标系下的三维坐标。本发明步骤s1中,对每个标志点编码点和非编码点中心的图像坐标进行定向和三维重建,再加入所述比例尺约束,得到每个全局控制点在世界坐标系下的三维坐标。本发明所述的一种大型钢筋骨架焊接的自动校准方法,在使双目动态测量单元按步骤s2采集全局控制点的图像前,首先对双目动态测量单元进行标定,得到双目动态测量单元的内参数和相对外参数,然后再设置该双目动态测量单元采集全局控制点的图像。本发明所述的一种大型钢筋骨架焊接的自动校准方法步骤s3中,多个双目动态测量单元呈阵列分布布局,每个双目动态测量单元的测量范围覆盖至少一个光坐标定位器,并且各个双目动态测量单元的总测量区域完全覆盖所有光坐标定位器。本发明步骤s3执行前,通过双目动态测量单元采集每个待焊接工件两对称侧边的光坐标定位器图像,并比较两对称侧图像,确定两对称侧边光坐标定位器的偏移值,由此得到单个焊接工件的弯曲变形量;通过双目动态测量单元采集对正的任意两个待焊接工件中每个待焊接工件两对称侧边的光坐标定位器图像,确定对正的两个待焊接工件中同侧的光坐标定位器的偏移值,由此得到对正的任意两个待焊接工件的找平误差。本发明所述的一种大型钢筋骨架焊接的自动校准方法步骤s4中,利用三角测量原理对每个双目动态测量单元采集的图像进行处理,得到每个光坐标定位器在世界坐标系下的三维坐标。本发明步骤s4中对待焊接工件进行调整后,依据步骤s3再次得到调整后待焊接工件上光坐标定位器的图像,并将每个双目动态测量单元采集的图像依据步骤s4再次进行处理,判断是否存在校正量。本发明所述的一种大型钢筋骨架焊接的自动校准方法,每次焊接作业后,依据步骤s3再次得到调整后待焊接工件上光坐标定位器的图像,并将每个双目动态测量单元采集的图像依据步骤s4再次进行处理,判断是否存在校正量,若存在校正量则判定此次焊接不合格,若不存在校正量则判定此次焊接合格。本发明一种大型钢筋骨架焊接的自动校准系统,包括计算机、反馈调节单元、多个全局控制点、多个光坐标定位器、多个双目动态测量单元,其中:所述计算机存储有计算机程序,所述计算机程序可被执行以实现如权利要求1-9任一项所述的方法。所述全局控制点固定于焊接区域的地面并呈阵列分布;所述光坐标定位器固定于焊接区域的待焊接工件上,每个待焊接工件至少一侧固定至少一个光坐标定位器;所述双目动态测量单元布置于各个待焊接工件上方并呈阵列分布,每个双目动态测量单元的测量范围覆盖若干光坐标定位器,且各个双目动态测量单元的总测量范围完全覆盖所有光坐标定位器;所述双目动态测量单元、反馈调节单元分别与计算机电连接,其中反馈调节单元用于基于计算机计算得到的校正量通过驱动调整平台调节待焊接工件。本发明所述的一种大型钢筋骨架焊接的自动校准系统,每个全局控制点包括底座、控制点,底座底部固定于焊接区域地面,控制点设置于底座顶面。本发明中,每个全局控制点还包括电机、转动座、保护盖,转动座固定于底座一侧地面,转动座中转动安装有转轴,电机固定于转动座,电机的输出轴与转轴轴向一端连接,保护盖盖罩于底座,保护盖对应于转动座的一侧固定于转动座中转轴,由电机驱动转轴转动进而使保护盖打开。本发明所述的一种大型钢筋骨架焊接的自动校准系统,每个光坐标定位器包括固定座、拆装手柄、标记点、磁吸限位器,固定座底部固定于拆装手柄上部,标记点设置于固定座顶部,磁吸限位器固定于拆装手柄下部,拆装手柄通过磁吸限位器吸附固定于待焊接工件。本发明需要在整个焊接工作区域的地面上阵列铺设全局控制点,使用全站仪、摄影测量获取全局控制点坐标。对应在距离地面一定高度上阵列铺设双目动态测量单元。焊接进行前在多个不同的焊接部件安放光坐标定位器。双目动态测量单元实时动态捕获不同焊接零件上光坐标定位器三维位置,通过算法计算出面、法向量、圆心等数据,进一步计算拼装偏差超差程度。超差位置给出数据并反馈至反馈调节单元实时调整位置直至达到合格范围内后,给出焊接信号由机器人完成焊接。本发明提供了一套能够实时动态监测待焊接工件位置并进行自动校准的方法和系统,能够联动各调整平台,可实现焊接实施过程中同步调整,一次完成高质量高精度的焊接拼装。本发明与现有技术对比的有益效果包括:本发明中通过双目动态测量单元采集全局控制点的图像,得到每个双目动态测量单元相对至少三个全局控制点的参数矩阵,并通过参数矩阵确定的双目动态测量单元采集待焊接工件上分别设置光坐标定位器图像,由双目动态测量单元采集的图像送入计算机中自动处理,由此可得到每个待焊接工件的三维坐标,并基于每个待焊接工件上光坐标定位器的三维坐标得到每个待焊接工件的校正量;得到的校正量可作为现有焊接用自动调整平台的工作参数,由自动调整平台完成自动校正。因此通过本发明可实现在焊接全过程中校正量的全程监测和自动采集,并为自动调整平台工作调整提供校正量数据支持,使自动调整平台能够基于采集的校正量实现自动校准,全程无须人工干预,并且采集的校正量具有较高的准确性,故采用本发明进行大型钢筋框架焊接作业时能够有效提高焊接的精度水平。附图说明图1是本发明方法流程框图。图2是本发明系统结构原理图。图3是本发明系统中全局控制点结构示意图。图4是本发明系统中光坐标定位器结构示意图。图5是本发明方法全局控制点布局示意图。图6是本发明方法摄影测量原理示意图。图7是本发明方法双目动态测量单元布置示意图。图8是本发明方法光坐标定位器检验被测件弯曲的原理图。图9是本发明方法光坐标定位器在焊接拼接时的原理图。图10是本发明方法三维重建原理图。图11是本发明系统中计算机与双目动态测量单元连接示意图。具体实施方式下面结合附图和实施例对本发明进一步说明。如图1所示,本发明一种大型钢筋骨架焊接的自动校准方法包括以下步骤:s1、获取每个全局控制点在世界坐标系下的三维坐标;s2、接收多个双目动态测量单元分别采集的3-5个全局控制点的图像,结合所采集的全局控制点在世界坐标系下的三维坐标,得到每个双目动态测量单元相对全局控制点的外参数矩阵;s3、接收多个双目动态测量单元分别实时动态采集的各自测量区域中待焊接工件上所有光坐标定位器的图像;s4、结合每个双目动态测量单元的内参数和步骤s2得到的相对全局控制点的外参数矩阵,对每个双目动态测量单元采集的图像进行处理,得到每个光坐标定位器在世界坐标系下的三维坐标;然后基于预设的每个待焊接工件在世界坐标系下的三维坐标以及计算得到的每个待焊接工件上光坐标定位器的三维坐标,得到每个待焊接工件的校正量,以便基于所述校正量对待焊接工件进行调整完成焊接作业。如图2所示,本发明一种大型钢筋骨架焊接的自动校准系统包括计算机、反馈调节单元、多个全局控制点、多个光坐标定位器、多个双目动态测量单元,其中:全局控制点固定于焊接区域的地面并呈阵列分布;光坐标定位器固定于焊接区域的待焊接工件上,每个待焊接工件至少一侧固定至少一个光坐标定位器;双目动态测量单元布置于各个待焊接工件上方并呈阵列分布,每个双目动态测量单元的测量范围覆盖若干光坐标定位器,且各个双目动态测量单元的总测量范围完全覆盖所有光坐标定位器;双目动态测量单元、反馈调节单元分别与计算机电连接,其中反馈调节单元用于基于计算机计算得到的校正量通过驱动调整平台调节待焊接工件。如图3所示,每个全局控制点包括底座101、控制点102,底座101底部固定于焊接区域地面,控制点102设置于底座101顶面。每个全局控制点还包括电机103、转动座104、保护盖105,转动座104固定于底座101一侧地面,转动座104中转动安装有转轴,电机103固定于转动座104,电机103的输出轴与转轴轴向一端连接,保护盖105盖罩于底座101,保护盖105对应于转动座104的一侧固定于转动座104中转轴,由电机103驱动转轴转动进而使保护盖105打开。如图4所示,每个光坐标定位器包括固定座201、拆装手柄202、标记点203、磁吸限位器204,固定座201底部固定于拆装手柄202上部,标记点203设置于固定座201顶部,磁吸限位器204固定于拆装手柄202下部,拆装手柄202通过磁吸限位器204吸附固定于待焊接工件205。本发明自动校正的详细说明如下:本发明需要在整个焊接工作区域的地面上阵列铺设全局控制点,使用全站仪、摄影测量获取全局控制点坐标。对应在距离地面一定高度上阵列架设多个点位的双目动态测量单元。焊接进行前在多个不同的焊接部件安放磁吸光坐标定位器。双目动态测量单元实时动态捕获不同焊接零件上光坐标定位器三维位置,通过算法计算出面、法向量、圆心等数据,进一步计算拼装偏差超差程度。超差位置给出数据并反馈焊件调整平台实时调整位置直至和合格范围内后给出焊接信号由机器人完成焊接。(1)全局控制点坐标获取第一步:全局控制点施工。介于单个双目动态测量单元的基距、立体角、以及合适镜头的选择范围。设置一定间隔距离的地面编码点坐标作为全局控制点使用。此部分需要保证一定的框架整体刚性。使得全局控制点整体可视为刚体进行分析。全局控制点布局见图5。图5中示例了一个35m*20m的测量范围。以2m*2m为间隔。当然可以按此布局扩大测量范围。全局控制点保护装置:全局控制点是整个测量的参考基准。保证其干净整洁是长期稳定工作的关键。如图3所示,使用大理石板制作的圆形的控制点102,螺栓固定于现场的钢结构地桩构成的底座101之上。另外综合施工现场环境,设计控制点自动防护用的保护罩105,使用一个转动座104和转轴构成的转动机构,配同电机103控制实现在使用时控制打开,非工作时间自动关闭保护标记点。保护罩105上盖的帽沿可起到防止喷淋水的影响,保护罩105内部设计防尘海绵保证光学控制点的清洁。第二步:使用全站仪测量全局控制点布局中一组对角线的距离。并以此作为摄影测量的比例尺使用。如图5中编码点10和编码点18之间的距离。第三步:如图6所示,使用摄影测量技术,通过在物体表面及周围放置标志点,包括编码点和非编码点,然后从不同的角度和位置对物体进行拍摄,得到一定数量的照片,经过图像处理和标志点识别,获得编码点和非编码点中心的图像坐标,然后经过相对定向、绝对定向、三维重建、以及捆绑调整计算,最后加入全站仪获取的比例尺约束即可获得全局控制点准确的三维坐标。全局控制点布局较大,受到环境温度等变化产生形变。可配合校正(重新测量获取全局控制点)解决此问题。(2)双目动态测量头标定在双目动态测量单元组装完毕,未吊装至最终位置前。首先进行每个测量头的标定工作。使用传统相机标定方法,通过标定板已知的三维坐标与对应的图像坐标的关系确定相机的内参数和相对外参数。然后安装在实际位置之后,采用获取的全局控制点作为已知量。通过采集双目动态测量单元一幅图像,即可计算出测量头相对全局控制点的外参数r,t矩阵。(3)测量单元布局、放置光坐标定位器首先:测量单元布局使用钢筋骨架在距离测量平台一定高度的上方安装多台双目动态测量单元,覆盖全场进行实时动态测量,布置如图7所示。以图7布置为例,多个双目动态测量单元的布置参数如下:5米高度,6mm镜头;单个相机5米处测量视场:7*5.2m;视场长度:2448*3.45um/(6mm*1000)*5m=7.038m;视场宽度:7.038m*3/4=5.2785m。为满足20*35m的测量视·场:阵列为3排7列双目动态测量单元布局数量:3排*7m=21m>20m7列*5.2m=36.4m>35m考虑成本问题,可使用5m工业相机,匹配6mm工业短焦镜头实现提升单个测头测量幅面大至7*5.2m。工业相机的参数如表1所示:表1工业相机参数表序号相机项目相机参数备注1分辨率5m2靶面2/33像元3.45um序号镜头项目镜头参数备注1焦距6mm2靶面2/3匹配相机每套双目动态测量单元配置如表2所示:表2双目动态测量单元配置表其次:光标光坐标定位器安装如图4所示,采用磁吸方式固定50mm光坐标定位器。以工件边沿作为限位装置,本发明的动态监测对安装位置无特殊要求。以边沿限位,放下吸合安装,下压手把拆卸,使用快捷方便。最后:光坐标定位器检测和对齐双目动态测量单元可拍摄识别多个标记点,计算出每个标记点所在的面、圆心位置、法向量。如图8所示,单个待焊接工件205(工字钢)的上边沿固定标记点装置,两边各限位固定一个。通过双目动态测量单元采集每个待焊接工件205两对称侧边的光坐标定位器206图像,并比较两对称侧图像,确定两对称侧边光坐标定位器206的偏移值,由此系统可检测单个待焊接工件205本身表面是否弯曲变形。如图9所示,两根待焊接工件205对正过程中,通过双目动态测量单元采集对正的任意两个待焊接工件205中每个待焊接工件两对称侧边的光坐标定位器206图像,确定对正的两个待焊接工件205中同侧的光坐标定位器的偏移值,由此可实时检测两个待焊接工件205的三维偏差,反馈自动调整系统直至达到找平对正的误差要求。(4)实时采集光坐标定位器图像采用usb或者gige工业相机可实现十几到几十毫秒的采集速度。配置环形频闪灯光源通过同步控制触发,可实时采集光坐标定位图像至计算机以备三维重建和相应计算。(5)计算机中三维重建光坐标定位器坐标、计算校正量如图10所示,双目立体视觉的几何模型,oxyz-为世界坐标系,o1和o2分别为两相机的光心,o1-x1y1z1为左相机坐标系,o2-x2y2z2-为右相机坐标系。物方点p在左右相机中对应的像点分别为p1和p2,直线o1p1和直线o2p2在空间相交于点p。如果已知p1和p2的图像坐标和相机的内、外参数(内参数包括摄相机的焦距,主点坐标以及各种畸变参数,外参数是指左右两个相机坐标系之间的旋转矩阵r和平移矩阵t),就可以利用三角测量原理计算得到物方点p在世界坐标系下的三维坐标。构造两相机投影矩阵ml与mr:ml=al[rl|tl]mr=ar[rr|tr]通过两个相机图像点坐标(ul,vl),(ur,vr)和两相机投影矩阵,计算出三维物体点坐标w:w=(aat*aa)-1*aat*bb通过安装在不同被测件上光坐标定位器的三维坐标,软件计算三轴校正量。(6)反馈调节单元通过通信总线对适配的调整平台进行驱动控制。进行实时调节、采集、计算、反馈的闭环流程操作。直至调节工作完成。(7)机器人焊接调节至合适位置后,通过总线驱动适配的机器人进行不同单元的焊接。每焊接一个点位可立即采集、计算、反馈一次。进行最终的焊接是否合格的判定。以避免多段焊接后因总体变形等引起的超差返工。(8)环境光本发明采用光源采用蓝光450±10nm,匹配窄带镜头滤镜。同时,使用同步频闪光源瞬间实现超高亮度的照明,配合特殊反光材质的光坐标定位器。实现大视场准确可靠的识别。很好的解决了现场复杂环境对光学测量的干扰。(9)计算机本发明优选品牌高性能台式工作站计算双目动态测量单元。完成标定、测量、偏差计算显示、控制、输出报告等工作。pc端采用光口pcie采集卡,配以品牌多光口万兆交换机。传输线采用光线远距离传输保证数据传输带宽。可实现整体采集一次1s以内。如图11所示,计算机301连接有多个交换机302,每个交换机302分别各自与多个双目动态测量单元303连接。举例计算:12m千兆网口相机,帧率8fps。计算机配置3张pcie双光纤接口交换机,每个交换机采用24个口千兆接口和2个光纤接口,所有相机同时工作最高可以达到6帧采集速度,24口*6/8帧*1000mbps=18000mbps<20000mbps,三个交换机独立,最终全部运行可在6帧167ms内完成。本发明所述的实施例仅仅是对本发明的优选实施方式进行的描述,并非对本发明构思和范围进行限定,在不脱离本发明设计思想的前提下,本领域中工程技术人员对本发明的技术方案作出的各种变型和改进,均应落入本发明的保护范围,本发明请求保护的技术内容,已经全部记载在权利要求书中。当前第1页12