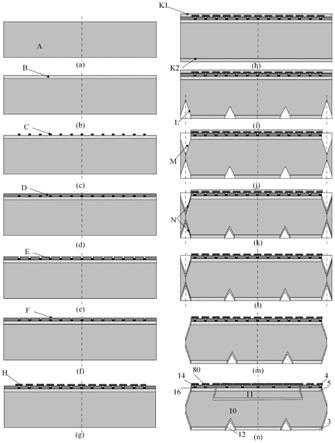
1.本发明属于特种加工技术领域,涉及一种电解加工用的可编程硅电极及其制备方法,尤其涉及一种用于变截面孔微细电解加工的可编程硅电极设计及制备方法。
背景技术:2.随着现代科学技术的发展,机械零件上的变截面孔的设计和应用越来越多。这些具有随着深度而直径变化的孔结构往往在流体喷射、气膜形成和散热冷却等方面具有特殊的性能,广泛应用于航空航天、汽车、工业打印、化纤化工和精密仪器等领域内,如航空发动机涡轮叶片上的竹节冷却孔,用于气膜冷却的异形扩散孔,高端柴油发动机喷油嘴上的燃油喷孔,工业喷墨打印头上的漏斗形喷孔和用于特殊形状化纤丝的喷丝孔等。这些零件不但在加工精度、表面光洁度和无表面损伤方面要求严苛,而且生产需求量巨大,发展一种高精度、高效率、无损伤加工方法的需求愈发迫切。
3.目前,传统的机械钻孔方法无法加工变截面孔,而针对金属合金材料的的特种加工工艺如电火花加工、电解加工、脉冲激光加工等在加工精度、效率方面有各自的特点。其中电火花加工用于锥形孔加工已经进入批量生产阶段,但是该方法很难加工形状更复杂的孔结构,而且无法避免的电极损耗也会降低加工精度。采用特殊设计的激光光路系统虽然可以加工变截面孔,但是加工高深宽比结构比较困难,而且存在表面热影响层。相比之下,在电解加工工艺中在线改变工艺参数可以加工各种具有复杂的变截面孔。研究证实了采用空心电极直接改变参数加工变截面孔的可行性,针对高深宽比的孔结构,目前已经形成了先加工通孔,再采用特制电极加工内部形状的基本工艺路线,但是,针对变截面孔的电解加工工艺还存在以下两个难题没有解决。
4.其一是预先制备针对不同内部结构变截面孔的电极困难。由于变截面孔的内部结构形状多变,针对不同的截面形状,需要预先设计并制备不同种类的电极,电极的特殊形状和局部侧壁绝缘使得电极制备非常困难,尚不存在面向多种不同形状的变截面孔通用的电极,而且对变截面孔的内部形状也难以控制。
5.其二是电极与已加工的直孔难以对中心。先加工直壁孔,再用特殊电极通过电解加工改变其内部结构构成变截面孔加工的基本工艺,但是由于直壁孔加工需要采用侧壁完全绝缘的工具电极,而变截面孔的内部形状的形成需要采用局部绝缘的工具电极,在两个工序间需要更换工具电极,而两个工序间电极与孔的中心难以完全对准,这样就会导致变截面孔的内部结构加工的不均匀,破坏加工精度,甚至导致变截面孔无法加工。
技术实现要素:6.本发明的目的是提出一种电解加工用的可编程硅电极及其制备方法,以解决目前变截面孔的加工难题,工序之间无需更换电极,即可实现直壁孔加工及孔侧壁复杂形状加工的复合功能。
7.本发明提出的电解加工用的可编程硅电极,由重掺杂硅基体、绝缘层、外部隔离
层、中间隔离层、导电单元阵列、连接线、导电引出阵列和电极供电端组成;重掺杂硅基体分为电极夹持部分和电极加工部分,电极夹持部分的正面设置有导电引出阵列和电极供电端,电极夹持部分的背面设置有定位槽;电极夹持部分的正面和电极加工部分的正面设置有中间隔离层,中间隔离层上布置有连接线,连接线上面覆盖有外部隔离层,连接线用于连接导电单元阵列和导电引出阵列,用于向导电单元阵列供电,中间隔离层用于隔离连接线、导电单元引出与重掺杂硅基体;导电单元阵列位于电极加工部分表面的外部隔离层上,外部隔离层用于隔离连接线与电解液,导电单元阵列靠近电极加工部分的末端,绝缘层覆盖在可编程硅电极侧壁面,绝缘层用于阻隔可编程硅电极的侧壁与待加工工件间的杂散电流。
8.本发明提出的电解加工用的可编程硅电极及其制备方法,其特点和优点是:
9.本发明的电解加工用的可编程硅电极,可以用于加工变截面的孔,工序之间无需更换电极,即可实现直壁孔加工及孔侧壁复杂形状加工。在采用本发明电极加工直壁孔后无需更换工具电极和二次对中,利用电极侧壁面分布的辅助电极单元作为电极使用,可以直接对孔的侧壁进行加工,而且通过改变辅助电极单元的通电控制,可以在线对加工的变截面孔的内部形状进行在线编程控制,使得该电极可以面向多种具有不同内部形状的变截面孔加工,拓宽工具电极的通用性。本发明的电解加工用可编程硅电极的制备方法,通过刻蚀、沉积工艺得到电极基体、检测单元和绝缘层,工艺较成熟,因此具有大批量制作的应用潜力。
附图说明
10.图1是本发明提出的可编程硅电极的结构示意图。图1中,(a)是可编程硅电极正面示意图,(b)可编程硅电极反面示意图。
11.图2是图1所示的去掉导电单元阵列和外部隔离层后的可编程硅电极的示意图,图2 中,(a)是电极加工部分局部放大图(去掉导电单元阵列和外部隔离层),(b)是可编程硅电极正面示意图(去掉导电单元阵列和外部隔离层)。
12.图3是图1所示的可编程硅电极的中导电单元阵列局部放大图,图3中,(a)是电极加工部分局部放大图(局部剖开),(b)是中间隔离层表面结构和导电柱示意图。
13.图4是图1所示的可编程硅电极的电极加工部分和电极夹持部分的截面图,图4中, (a)是图1的a-a截面示意图,(b)是图1的b-b的截面示意图。
14.图1-图4中,1是可编程硅电极,2是重掺杂硅基体,3是绝缘层;4是外部隔离层, 5是中间隔离层,6是导电单元阵列,7是连接线,8是导电引出阵列,9是电极供电端, 10是电极夹持部分,11是电极加工部分,12是定位槽,13是导电触点,14是导电柱,15 是引线,16是端子。
15.图5是图1所示的可编程硅电极中电极加工部分的制备过程示意图。
16.图5中,a是单晶硅材料基体,b是中间隔离层,c是金属层,d是外部隔离层,e是局部刻蚀窗口,f是金属填充物,g是导电单元60,k1是正面掩膜层,k2是反面掩膜层, l是刻蚀窗口,m是掩膜窗口,n是绝缘层,14是导电柱,16是端子,60是导电单元,4 是外部隔离层;5是内部隔离层;3是绝缘层;11是电极加工部分。
17.图6是图1所示的可编程硅电极中电极夹持部分的制备过程示意图。
18.图6中,a是重掺杂硅基体,b是中间隔离层,c是金属层,d是外部隔离层,e是刻蚀窗口,f是金属填充物,h是-导电引出端80,k1是正面掩膜层,k2是-反面掩膜层,l 是刻蚀窗口,m是掩膜窗口,n是绝缘层,12是定位槽,16是导电触点,14是导电柱,11 是电极加工部分,12是定位槽,10是电极夹持部分,3是绝缘层,4是外部隔离层,5是内部隔离层。
19.图7是本发明的可编程硅电极的使用状态示意图。
20.图7中,1是可编程硅硅电极,17是专用夹具,18是电机,19是精密主轴,20是导电滑环,21是电解液,22是工件。
21.图8是使用本发明的可编程硅电极加工的几种常见的变截面孔示意图。
具体实施方式
22.本发明提出的电解加工用的可编程硅电极及其制备方法,其特征在于可编程硅电极1 由重掺杂硅基体2、绝缘层3、外部隔离层4、中间隔离层5、导电单元阵列6、连接线7、导电引出阵列8和电极供电端9组成;重掺杂硅基体2分为电极夹持部分10和电极加工部分11,电极夹持部分10的正面设置有导电引出阵列8和电极供电端9,电极夹持部分 10的背面设置有定位槽12;电极夹持部分10的正面和电极加工部分11的正面设置有中间隔离层5,中间隔离层5上布置有连接线7,连接线7上面覆盖有外部隔离层4,连接线 7用于连接导电单元阵列6和导电引出阵列8,用于向导电单元阵列6供电,中间隔离层5 用于隔离连接线7、导电单元引出8与重掺杂硅基体2;导电单元阵列6位于电极加工部分表面11的外部隔离层4上,外部隔离层4用于隔离连接线7与电解液,导电单元阵列6 靠近电极加工部分11的末端,绝缘层3覆盖在可编程硅电极侧壁面,绝缘层3用于阻隔可编程硅电极1的侧壁与待加工工件间的杂散电流(导电引出阵列8、电极供电端9和导电单元阵列外6的侧壁面以及可编程硅电极的前端面无需覆盖绝缘层3)。
23.上述可编程硅电极中的连接线7,由导电触点13、导电柱14、引线15和端子16构成, (如图2、图3和图4所示),导电触点13位于电极夹持部分10表面的中间隔离层5上,端子16位于电极加工部分11表面的中间隔离层5上;引线15连接导电触点13和端子16;导电柱14位于外部隔离层4的内部,导电柱14用于连接导电单元6与端子16以及导电引出端80与导电触点13。
24.上述可编程硅电极中的导电单元阵列6,位于电极加工部分11表面的外部隔离层4上,如图1(a)所示,导电单元阵列6靠近可编程硅电极1的末端,导电单元阵列6由多个阵列排布的导电单元60构成,导电单元60的排数大于3,列数大于3,导电单元60通过导电柱14、端子16、引线15和导电触点13连接至导电引出端80上。如图3(a)中所示。
25.上述可编程硅电极中的的导电单元60和导电引出端80的形状为矩形、椭圆形或圆形。
26.上述可编程硅电极中的导电单元阵列6,其中的导电单元为阵列式排布,各个导电单元之间不连接,处于电学隔离状态。
27.上述可编程硅电极中的重掺杂硅基体2,由优良导体材料制作,优良导体材料的电导率范围为10-2
~10-3
ωcm,重掺杂硅基体2为高浓度掺杂的n型或p型单晶硅,优选地为 n型,掺杂浓度为10
19
~10
20
/cm3。
28.上述可编程硅电极中的绝缘层、外部隔离层和内部隔离层由氧化硅、氮化硅或碳
化硅制作。
29.上述可编程硅电极中的导电单元阵列、连接线和导电引出阵列由金属剥离工艺形成,导电单元阵列、连接线、导电引出阵列和电极供电端由金属薄膜制作,金属薄膜的厚度均为纳米级、宽度为微米级。
30.上述可编程硅电极中的金属薄膜,其材料可以为铂、银或金,优选为铂。
31.本发明提出的电解加工用的可编程硅电极的制备方法,其过程的两个不同的部位分别如图5和图6所示,图5是可编程硅电极中电极加工部分11的制备过程,图6是电极夹持部分10的制备过程。具体过程如下:
32.(1)在重掺杂硅基体a的正面沉积一层中间隔离层b,形成可编程硅电极的中间隔离层5;如图5(b)和图6(b)所示。
33.(2)在步骤(1)的中间隔离层5上沉积一层金属层c,形成图形化的金属层,得到可编程硅电极的引线15、端子16和导电触点13;如图5(c)和图6(c)所示。
34.(3)在步骤(2)的金属层上沉积一层外部隔离层d,形成可编程硅电极的外部隔离层4;如图5(d)和图6(d)所示。
35.(4)对步骤(3)的外部隔离层刻蚀,穿透至金属层,暴露引线15、端子16和导电触点13,形成局部刻蚀窗口e;如图5(e)和图6(e)所示。
36.(5)在步骤(4)的局部窗口内填充金属f,形成可编程硅电极的导电柱14;如图5 (f)和图6(f)所示。
37.(6)在步骤(5)的外部隔离层4上沉积一层金属层g,形成图形化的金属层,得到的可编程硅电极的导电单元阵列6和导电引出阵列8;如图5(g)和图6(g)所示。
38.(7)在步骤(6)的基体的正面和反面分别沉积一层掩膜层k1和k2;如图5(h)和图6(h)所示。
39.(8)在步骤(7)的电极加工部分基体下表面的掩膜层k2上刻蚀出梯形掩膜窗口l,对单晶硅基体进行湿法腐蚀,得到背面减薄窗口,如图5(i)所示,在步骤(7)的电极夹持部分基体下表面的掩膜层k2上刻蚀出定位槽12;如图6(i)所示。
40.(9)在步骤(8)的基体的上表面的掩膜层和隔离层上刻蚀出掩膜窗口m,对单晶硅基体进行湿法腐蚀得到电极的基本轮廓;如图5(j)所示和图6(j)所示。
41.(10)在步骤(9)的基体所有侧面和反面沉积一层绝缘层n;如图5(k)和图6(k) 所示。
42.(11)对步骤(10)的单晶硅基体的正面上的掩膜层k1进行刻蚀,暴露出导电单元阵列、导电引出阵列和局部重掺杂硅基体表面;如图5(l)和图6(l)所示。
43.(12)使步骤(10)的单晶硅基体按照电极的轮廓裂片,形成可编程硅电极。如图5 (l)和图6(m)所示。
44.下面将结合具体实施方式及附图,对本发明的可编程电极及其制备方法作进一步的详细说明。
45.本发明的可编程电极1的重掺杂硅基体2,由电极夹持部分10和电极加工部分11组成,电极夹持部分10用于可编程硅电极1的精确装夹和定位,电极加工部分11作为电解加工用的工具阴极。电极夹持部分10正面设置有导电引出阵列8和电极供电端9,电极夹持部分10背面设置有定位槽12。导电引出阵列位于电极夹持部分表面的外部隔离层上,并靠近电
极夹持部分的另一端,除导电引出阵列8和电极供电端9表面外,电极夹持部分 10表面覆盖有绝缘层3,如图1(b)。电极供电端9与重掺杂硅基体2直接连接,二者界面间无绝缘层。电极加工部分11是伸出电极夹持部分10的悬臂结构。电极夹持部分10 和电极加工部分11的正面设置有中间隔离层5。中间隔离层5上布置有连接线7,连接线 7位于中间隔离层5和外部隔离层4之间,连接导电单元阵列6和导电引出阵列8。连接线7上面覆盖有外部隔离层4。导电单元阵列6位于电极加工部分11表面的外部隔离层4 上,并靠近电极加工部分11的末端,其表面无绝缘层3,电极加工部分11的其余表面均覆盖有绝缘层3,如图1(a)。可编程电极中的连接线7由导电触点13、导电柱14、引线 15和端子16构成,导电触点13位于电极夹持部分10表面的中间隔离层5上。端子16位于电极加工部分11表面的中间隔离层5上。引线15连接导电触点13和端子16,导电柱 14位于外部隔离层4内部,分别连接着导电单元60和端子16、导电引出端80和导电触点13,如图2。可编程电极中的导电单元阵列6位于电极加工部分11表面的外部隔离层4 上,并位于靠近电极的末端,导电单元阵列6由多个阵列排布的导电单元60构成,导电单元60的排数大于3,导电单元60的列数大于3,图中所示为5
×
5的排布的导电单元60 构成导电单元阵列6;导电单元60通过导电柱14、端子16、引线15、导电触点13和导电柱14,最终连接至导电引出端80上。导电引出阵列8由多个导电引出端80组成,其数量与导电单元60的数量相同。导电单元60和导电引出端80的形状可选为矩形、椭圆形或圆形等。
46.本发明的制备方法的实施例中,采用沉积工艺在单晶硅材料基体a上沉积一层隔离层 b作为中间隔离层5,材料选用二氧化硅(sio2),厚度为10-500nm,优选为200nm,电极加工部分截面如图5(b)和电极夹持部分截面如图6(b)。
47.制备方法的步骤(2)中,对隔离层b表面进行单面光刻,以光刻胶作为掩膜,在其表面上沉积一层金属薄膜,材料可选用铂、银等,优选为银,其沉积厚度为10-200nm,优选地为100nm。利用lift-off工艺,去掉光刻胶,得到图形化的金属层c(形成导电触点13、引线15和端子16),电极加工部分截面如图5(c)和电极夹持部分截面如图6(c);
48.制备方法的步骤(3)中,采用沉积工艺在上述中间隔离层b和金属层c上沉积一层隔离层d,作为外部隔离层4,材料选用二氧化硅(sio2),厚度为10-500nm,优选为200nm,电极加工部分截面如图5(d)和电极夹持部分截面如图6(d)。
49.制备方法的步骤(4)中,对隔离层d表面进行单面光刻,以光刻胶作为掩膜,对其表面进行局部刻蚀,将外部隔离层d刻穿,至金属层c暴露,形成局部窗口得到图形化的刻蚀窗口e,电极加工部分截面如图5(e)和电极夹持部分截面如图6(e);
50.制备方法的步骤(5)中,在上述图形化的刻蚀窗口e填充金属f,可选材料为铜或铝,优选为铜,作为导电柱14,填充方法可选用电铸方法,修整其表面,电极加工部分截面如图5(f)和电极夹持部分截面如图6(f);
51.制备方法的步骤(6)中,对隔离层d和填充金属f表面进行单面光刻,以光刻胶作为掩膜,在其表面上沉积一层金属薄膜,材料可选用铂、银等,优选为银,其沉积厚度为 10-500nm,优选地为200nm。利用金属剥离工艺,去掉光刻胶,得到图形化的金属层,作为导电单元阵7和导电引出阵列8,电极加工部分截面如图5(g)和电极夹持部分截面如图6(g);
52.制备方法的步骤(7)中,采用沉积工艺在单晶硅材料基体a正面上沉积一层sio2,再沉积一层氮化硅(si3n4),最后形成正面掩膜层k1;然后,采用沉积工艺在单晶硅材料基体
a反面上沉积一层sio2,再沉积一层si3n4,最后形成反面掩膜层k2,为后续的刻蚀加工图形化做准备。sio2的沉积厚度为50-400nm,优选为300nm,si3n4的沉积厚度为50
‑ꢀ
400nm,优选为200nm,电极加工部分截面如图5(h)和电极夹持部分截面如图6(h);
53.制备方法的步骤(8)中,对上述背面的掩膜层k2进行一次光刻。采用刻蚀工艺去除暴露的掩膜层,直到露出单晶硅材料基体a为止。除胶后在单晶硅材料基体a上形成工减薄窗口和定位槽掩膜轮廓,将上述单晶硅材料基体a放入腐蚀液中进行刻蚀加工,并严格控制刻蚀的时间,使刻蚀得到背面减薄窗口l,电极加工部分截面如图5(i)和电极夹持部分截面如图6(i)。
54.制备方法的步骤(9)中,对上述正面掩膜层k1进行一次光刻。采用刻蚀工艺去除暴露的掩膜层和隔离层,直到露出单晶硅材料基体a为止。除胶后在单晶硅材料基体a上形成硅电极的轮廓形状,将上述单晶硅材料基体a放入腐蚀液中进行刻蚀加工,并严格控制刻蚀的时间,刻蚀加工至上、下表面相交为止,电极加工部分截面如图5(j)和电极夹持部分截面如图6(j);
55.在制备步骤(9)和步骤(10)中,所采用的腐蚀液成分为koh,其浓度为20%~50%,优选地为20%。腐蚀温度为50~100℃,优选地为80℃。也可以适量添加少许异丙醇(ipa),其浓度小于0.1~5%,优选为1.5%。腐蚀液成分也可以为tmah,其浓度为10%~40%,优选地为25%。腐蚀温度为50~100℃,优选地为80℃。
56.在步骤10)中利用化学气相沉积在硅材料基体的两个侧面和反面上沉积一层sio2,再沉积一层si3n4,作为绝缘层n,即硅电极的绝缘层3,sio2的沉积厚度为50-400nm,优选为300nm,si3n4的沉积厚度为50-400nm,优选为200nm,电极加工部分截面如图5(k)和电极夹持部分截面如图6(k);
57.在步骤s11)中利用氢氟酸或者反应离子刻蚀局部处理所述的掩膜层k1,暴露导电单元阵列6、导电引出阵列8和局部重掺杂硅基体2表面,电极加工部分截面如图5(l)和电极夹持部分截面如图6(l);
58.将制备好的微细硅电极从单晶硅材料基体a上脱离下来,裂片方式可以采用手工裂片和高频脉冲激光切割裂片两种方式,最终得到的加工检测一体化硅电极如图5电极加工部分截面如图5(m)和电极夹持部分截面的示意图如图6(n)
59.本发明方法制备的电解加工用的可编程硅电极,在电解加工中应用的示意图如图7所示,其中可编程硅电极1装夹在专用夹具17上进行高速旋转形成柱状包络面,达到与柱状电极相同的加工效果。硅电极旋转由电机18带动精密主轴19和导电滑环20旋转实现。另外21是电解液,22是工件。
60.在变截面孔加工工艺中,首先以重掺杂硅基体2为工具阴极,各个导电单元60不通电,加工直壁结构孔,然后,将重掺杂硅基体2电极断电,以导电单元阵列6中的部分导电单元60为阴极,对孔侧壁进行材料加工,得到不同形状的变截面孔。
61.针对不同内部结构形状的变截面孔,改变导电单元阵列6中的通电的导电单元60可以对孔的内部结构在线控制,通过改变不同位置的导电单元通电/断电情况编辑加工的变截面孔的内部结构。如图所示列出了几种常见的变截面孔加工示意图8,图8(a)是鼓形孔的加工过程示意图;图8(b)是竹节形孔的加工过程示意图;图8(c)是葫芦形孔的加工过程示意图;图8(d)是漏斗形孔的加工过程示意图;图8(e)是倒锥形孔的加工过程示意图。