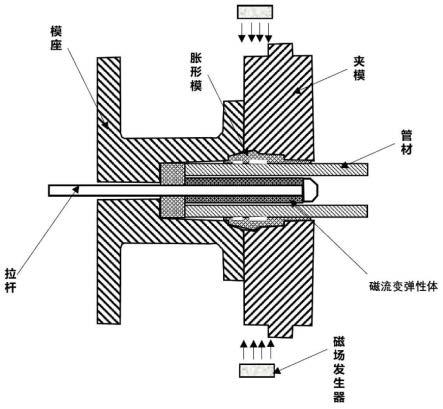
1.本发明属于金属形状加工与复杂构件先进制造技术领域,具体是一种无扩口管路连接的磁流变弹性体胀形装置及方法。
背景技术:2.飞机系统的导管零件担负着为各系统输送压力的重要功能。飞机在作战训练过程中,由于受到振动、摩擦和外来物撞击的作用,致使导管容易产生裂纹、断裂和破损等损伤中。导管一旦损伤,轻则造成漏油、漏气,重则造成飞机系统功能丧失,严重危及飞行安全。飞机战伤仿真的结果表明,飞机导管的战伤概率约为4.3%。目前,飞机导管常用的材料有铝合金、钛合金、不锈钢和铜合金等,其连接件结构型式主要有扩口和无扩口两种,其中扩口式连接结构简单,为目前应用最主要的连接形式,但由于它的密封面积大,制造过程中所产生的形状误差、表面粗糙度误差难以消除,因此密封性不好、自锁性差,通常保险丝锁紧,极大的增大了飞机整体重量。为了解决上述问题,国内外逐步采用无扩口导管连接形式,不仅满足密封性、自锁性要求,而且减轻了飞机重量。无扩口导管连接件制造技术国内目前仍处于研发和试制阶段。无扩口导管预装成形原理,就是借助预装机在一定时间内,利用胶套压缩产生的膨胀力挤压导管内壁,将导管紧紧压在管套环形槽内,实现导管和管套密封的目的。
3.而磁流变弹性体(mre)是当前几年广泛使用的mr材料之一。将微米级磁性颗粒添加到聚合物基体中,以在磁场环境下混合并固化。因此,基质中的磁性颗粒形成链状或柱状有序结构。mre可以解决mr流体中的磁性颗粒问题,例如易泄漏,易沉降,环境污染和整体稳定性差的问题。此外,它不需要特殊的容器来存储。磁致伸缩模量,抗拉强度,硬度,滞后发热等参数可用于测量磁致伸缩性能。关键参数是磁致伸缩性能的磁致伸缩模量部分,它反映了磁场对材料性能的影响,并表现为在力和磁耦合场下的材料特性。
4.导管膨胀后的槽深质量控制,是导管预装成形工艺的一个难点。因此,运用一种用于无扩口管路连接的磁流变弹性体胀形方法,并在磁场环境下加工导管,使磁流变胶套对应管套呈现合适的力学性能,从而减少因普通橡胶力学性能单一造成的管壁破裂和导管与管套贴合不好等问题。
技术实现要素:5.本发明的目的在于提供一种无扩口管路连接的磁流变弹性体胀形装置及方法,以解决上述背景技术中提出的问题。
6.为实现上述目的,本发明提供如下技术方案:
7.一种无扩口管路连接的磁流变弹性体胀形装置,包括底座和设置在其上端用于传输待胀形金属管材的传输组件,所述传输组件包括两个平行设置的传输辊,两个传输辊之间绕设有用于传输的传输带,所述传输带表面分布有防滑层,所述传输辊的固定轴端通过支腿与底座连接固定,其中一个所述传输辊的固定轴端部连接用于带动其转动的传输电
机,所述传输带表面分布有若干个等间距设置的缓存固定槽,所述缓存固定槽用于放置固定金属管材,所述传输带的两侧分别设有一个用于对金属管材端部进行胀形的胀形机构。
8.作为本发明进一步的方案:所述胀形机构包括便于金属管材端部插入的胀形模具和用于插入金属管材内部的拉杆,所述拉杆外端连接用于牵引其的牵引器,所述胀形模具包括一个上模座和一个下模座,所述下模座和上模座端部分别与下夹模和上夹模连接固定,所述下模座、上模座和下夹模以及上夹模之间围合成用于成型的成型腔,所述成型腔中设有与金属管材外侧壁相配合用于胀形的胀形模,胀形模内壁设有便于金属管材向外侧成型的胀形槽,所述胀形模包括上下两个模具块,上下两个模具块分别与下模座和上模座连接固定,所述下模座连接用于带动其上下运动的第二伸缩杆,所述上模座连接用于带动其上下运动的第一伸缩杆,所述第一伸缩杆设置在固定支架上,所述固定支架下端与底座连接固定,在第一伸缩杆和第二伸缩杆的作用下下模座和上模座实现合并或者分开,以便对金属管材端部进行夹持和后期的卸料;
9.所述拉杆端部设有与金属管材内壁相配合的活动封堵块,所述拉杆上滑动设有一个固定封堵块,所述固定封堵块与成型腔左端相配合,所述固定封堵块和活动封堵块之间的拉杆上套设有一个磁流变弹性体,磁流变弹性体构成的胶套相比于用聚氨酯或橡胶作为胀形胶套,具有性能可控、无污染、能耗低的优势,所述胀形模具外侧分布有用于调整磁流变弹性体所在位置磁场分布的磁场发生器。
10.作为本发明再进一步的方案:所述供料组件包括一个设置在传输带上方的载料框,所述载料框内部设有便于若干个金属管材连续堆积的存储腔,所述存储腔的宽度和长度分别与金属管材的直径和长度相对应,所述载料框外侧通过连接架与底座连接固定,所述存储腔下端口与传输带之间的距离相当于金属管材的半径,所述缓存固定槽的深度与金属管材的半径相对应。
11.一种用于无扩口管路连接的磁流变弹性体胀形方法,包括以下步骤:
12.步骤1)以金属管材为复杂曲面胀形材料,选取合适壁厚和合适管径的金属材料备用;
13.步骤2)采用合适的合金材料作为胀形模具,即作为管套,采用金相砂纸打磨基体材料表面,并进行抛光处理,最后采用去离子水、丙酮、无水乙醇以及去离子水依次进行超声清洗并晾干待用;
14.步骤3)采用easy公司的as40加成型橡胶作为橡胶基体材料,选用粒径均值为4.5μm的羰基铁粉作为磁性粒子,其压实密度为7.86g/cm3;除此之外,还需采用能提高磁流变弹性体固化工程中羰基铁粉在基体材料中运动能力的二甲基硅油作为添加剂。利用这些材料制作出磁流变弹性体作为胶套;
15.步骤4)将制作好的胀形模具和磁流变弹性胶套装入无扩口连接工艺装置,随后将拉杆的运动功率参数输入到动力控制系统中,进行无扩口导管端头连接过程;在整个成形过程中,是在可调节磁场环境下对复杂曲面导管进行胀形的,利用磁流变弹性胶套在不同磁场加载强度下性能不同,对磁流变弹性胶套压缩性精确控制,实现不同的胀形效果;也可通过改变磁流变弹性胶套的磁性粒子浓度来实现。
16.作为本发明进一步的方案:所述步骤2)中的表面预处理过程为:依次采用1~6号金相砂纸打磨导管和管套表面,随后进行机械抛光处理,直至在显微镜下观察无明显划痕
为止,并依次在去离子水、丙酮以及无水乙醇中超声清洗10min,晾干备用。
17.作为本发明进一步的方案:所述步骤3)中的胶套预处理为:首先,分别以100:10的质量比加入硅和催化剂并均匀搅拌。之后,加入质量分数为25%的二甲基硅油。搅拌均匀后,加入质量分数为50%的羰基铁粉充分搅拌。完成上述步骤后,将液态mr混合物倒入模具中,置于预热至70℃的传热段进行固化。
18.作为本发明进一步的方案:所述步骤3)中的胶套结构形式为:空心圆柱体,中间插入拉杆来进行压缩变形。
19.作为本发明进一步的方案:所述步骤3)中为了提高mre固化过程中羰基铁粉在基体材料中的运动能力,向橡胶中添加了二甲基硅油。该油的主要功能是覆盖羰基铁颗粒的表面,使其能够在外磁力的作用下沿磁感应线的方向移动,从而形成规则的链结构。
20.所述步骤3)中加成固化硅橡胶是最关键的硅产品之一。它的组成通常包括乙烯基聚合物,增强材料,氢交联剂,催化剂,抑制剂等。硫化可以通过混合所有原料并在一定条件下固化来实现。硅橡胶是一种以si-o-si无机结构为主链,有机基团为侧链的半无机和半有机聚合物。它具有有机和无机化合物的特性,并且具有出色的性能。
21.作为本发明进一步的方案:所述步骤4)中的磁场发生器由电磁铁和高精度直流励磁源两部分组成。在实验条件下,通过调节外部电流和气隙,磁场发生器可以提供700mt以下的磁场强度。
22.作为本发明进一步的方案:所述步骤4)中不同磁场加载强度影响胶套的磁流变效应与弹性模量表现为:磁场强度分别在0mt,160mt,321mt,485mt,650mt。其中0mt下磁流变效应为0.076,弹性模量为1.28mpa;160mt下磁流变效应为0.162,弹性模量为1.40mpa;321mt下磁流变效应为0.168,弹性模量为1.48mpa;485mt下磁流变效应为0.156,弹性模量为1.32mpa;650mt下磁流变效应为0.152,弹性模量为1.30mpa。
23.作为本发明进一步的方案:所述步骤4)中不同磁性粒子浓度影响胶套的体积模量表现为:在固定磁场加载强度为0mt,加载速度为5mm/min时,磁性粒子浓度为11.9%,26.4%,44.7%时,体积模量分别为338.9mpa,354.8mpa,389.9mpa;在固定磁场加载强度为200mt,加载速度为20mm/min时,磁性粒子浓度为11.9%,26.4%,44.7%时,体积模量分别为365.2mpa,400.2mpa,452.4mpa。
24.与现有技术相比,本发明的有益效果是:1)本发明在常温环境下加工导管,无需改变导管的温度,属于冷成形,从而可以在微观尺度上保持管件原有的组织,保证构件表面的综合机械性能。
25.2)本发明采用磁流变弹性体作为胶套,相比于用聚氨酯或橡胶作为胀形胶套,本发明具有性能可控、无污染、能耗低的优势,可以在很大范围内解决在使用一般橡胶胶套的情况下出现的管壁过薄、成形槽深不足等技术问题
26.3)本发明可以通过磁场发生器加载不同的磁场强度,来实现对磁流变弹性胶套的控制。利用磁场加载强度的不同使磁流变弹性体达到不同的弹性模量和体积模量,对于调控无扩口管路连接的成形质量具有重要的意义。
附图说明
27.图1为本发明中无扩口管路连接磁流变弹性体胀形技术装置图。
28.图2为本发明中无扩口管路连接磁流变弹性体胀形技术加工示意图。
29.图3为本发明中磁流变弹性胶套内部磁性粒子分布示意图。
30.图4为本发明的原理框图。
31.图5为本发明中胀形装置的结构示意图。
32.图6为本发明中胀形装置另一侧的结构示意图。
33.图7为本发明中胀形模具的结构示意图。
34.其中:底座11、传输电机12、传输辊13、载料框14、存储腔15、第一伸缩杆16、固定支架17、磁场发生器18、缓存固定槽19、防滑层20、胀形机构100、传输带21、牵引器22、拉杆23、第二伸缩杆24、胀形模具25、金属管材26;
35.下模座2501、上模座2502、胀形槽2503、上夹模2504、胀形模2505、活动封堵块2508、磁流变弹性体2509、固定封堵块2510。
具体实施方式
36.实施例1
37.请参阅图5-图7,本发明实施例中,一种无扩口管路连接的磁流变弹性体胀形装置,包括底座11和设置在其上端用于传输待胀形金属管材26的传输组件,所述传输组件包括两个平行设置的传输辊13,两个传输辊13之间绕设有用于传输的传输带21,所述传输带21表面分布有防滑层20,所述传输辊13的固定轴端通过支腿与底座11连接固定,其中一个所述传输辊13的固定轴端部连接用于带动其转动的传输电机12,所述传输带21表面分布有若干个等间距设置的缓存固定槽19,所述缓存固定槽19用于放置固定金属管材26,所述传输带21的两侧分别设有一个用于对金属管材26端部进行胀形的胀形机构100,这样在运输金属管材26的过程中就可以完成对金属管材26的两端处理,并且两个处理工艺工序重合,有助于提高加工效率;
38.所述胀形机构100包括便于金属管材26端部插入的胀形模具25和用于插入金属管材26内部的拉杆23,所述拉杆23外端连接用于牵引其的牵引器22,所述胀形模具25包括一个上模座2502和一个下模座2501,所述下模座2501和上模座2502端部分别与下夹模和上夹模2504连接固定,所述下模座2501、上模座2502和下夹模以及上夹模2504之间围合成用于成型的成型腔,所述成型腔中设有与金属管材26外侧壁相配合用于胀形的胀形模2505,胀形模2505内壁设有便于金属管材26向外侧成型的胀形槽2503,所述胀形模2505包括上下两个模具块,上下两个模具块分别与下模座2501和上模座2502连接固定,所述下模座2501连接用于带动其上下运动的第二伸缩杆24,所述上模座2502连接用于带动其上下运动的第一伸缩杆16,所述第一伸缩杆16设置在固定支架17上,所述固定支架17下端与底座11连接固定,在第一伸缩杆16和第二伸缩杆24的作用下下模座2501和上模座2502实现合并或者分开,以便对金属管材26端部进行夹持和后期的卸料;
39.所述拉杆23端部设有与金属管材26内壁相配合的活动封堵块2508,所述拉杆23上滑动设有一个固定封堵块2510,所述固定封堵块2510与成型腔左端相配合,所述固定封堵块2510和活动封堵块2508之间的拉杆23上套设有一个磁流变弹性体2509,磁流变弹性体2509构成的胶套相比于用聚氨酯或橡胶作为胀形胶套,具有性能可控、无污染、能耗低的优势,所述胀形模具25外侧分布有用于调整磁流变弹性体2509所在位置磁场分布的磁场发生
器18,这样在实际使用时,通过磁场发生器18调整磁流变弹性体2509的磁场分布,使得胀形槽2503两侧的磁流变弹性体2509弹性变小,使得胀形槽2503所在位置的磁流变弹性体2509弹性增大,然后通过牵引器22拉动拉杆23,此时活动封堵块2508会紧压磁流变弹性体2509,从而迫使弹性较小的位置挤压金属管材26表面嵌入胀形槽2503中,从而完成胀形操作,这里通过磁场的分布的调节使得位于胀形槽2503所在位置的形变更加容易,与传统普通的弹性材料相比,本技术可以连续的对胀形槽2503自左向右进行成型操作,而现有的成型方式必须同时对胀形槽2503所在位置的管材进行成型操作;
40.所述供料组件包括一个设置在传输带21上方的载料框14,所述载料框14内部设有便于若干个金属管材26连续堆积的存储腔15,所述存储腔15的宽度和长度分别与金属管材26的直径和长度相对应,所述载料框14外侧通过连接架与底座11连接固定,所述存储腔15下端口与传输带21之间的距离相当于金属管材26的半径,所述缓存固定槽19的深度与金属管材26的半径相对应,这样就使得每次缓存固定槽19经过载料框14下方时,都有一个金属管材26会落入缓存固定槽19中,从而实现连续给料。
41.本发明的工作原理是:在实际使用时,供料组件会不断的将金属管材26送入缓存固定槽19中,随着传输带21转动,金属管材26一端转动到第一个胀形机构100位置,此时在第一伸缩杆16和第二伸缩杆24的作用下下模座2501和上模座2502实现合并,以便对金属管材26端部进行夹持定位,此时先通过牵引器22带动拉杆23和套设在其外侧磁流变弹性体2509插入金属管材26中,随后活动封堵块2508插入金属管材26中后,随着拉杆23继续插入,此时活动封堵块2508和固定封堵块2510将磁流变弹性体2509封堵在填充腔位置,通过磁场发生器18调整磁流变弹性体2509的磁场分布,使得胀形槽2503两侧的磁流变弹性体2509弹性变小,使得胀形槽2503所在位置的磁流变弹性体2509弹性增大,然后通过牵引器22拉动拉杆23,此时活动封堵块2508会紧压磁流变弹性体2509,从而迫使弹性较小的位置挤压金属管材26表面嵌入胀形槽2503中,从而完成胀形操作,然后第一伸缩杆16和第二伸缩杆24的作用下下模座2501和上模座2502实现分开,通过牵引器22牵引拉杆23抽离金属管材26,上述操作完成了金属管材26一端的胀形处理,随着传输带21继续传动,金属管材26另一端也会传输到另一个胀形机构100位置,此时完成对金属管材26另一端胀形操作,从而完成对金属管材26两端胀形操作;
42.实施例2
43.请参阅图1-图4,一种用于无扩口管路连接的磁流变弹性体胀形方法如下:
44.第一步,采用gh4169镍基高温合金作为金属管材,选取壁厚为0.8mm、管径为φ16mm的gh4169镍基高温合金备用;
45.第二步,分别以100:10的质量比加入硅和催化剂并均匀搅拌。之后,加入质量分数为25%的二甲基硅油。搅拌均匀后,加入质量分数为50%的羰基铁粉充分搅拌。完成上述步骤后,将液态mr混合物倒入模具中,置于预热至70℃的传热段进行固化,制成磁流变弹性胶套,形式为空心圆柱体。
46.第三步,采用aisi 316不锈钢作为胀形模,即作为管套。依次采用1~6号金相砂纸打磨导管和管套表面,然后将其机械抛光直至在金相显微镜下没有明显的划痕,并在去离子水、丙酮、无水乙醇及去离子水中超声清洗10min,晾干待用;
47.第四步,将制作好的磁流变弹性胶套装入如附图1无扩口管路连接磁流变弹性体
胀形方法装置,随后将拉杆的运动功率参数输入到动力控制系统中,进行无扩口导管端头连接过程。在整个成形过程中,是在可调节磁场环境下对复杂曲面导管进行胀形的,利用磁流变弹性胶套在不同磁场加载强度下性能不同,对磁流变弹性胶套压缩性精确控制,实现不同的胀形效果。在管套的环形槽口处,所需要的成形力要大一些,因此需要此处的磁流变弹性胶套的弹性模量更高一些,因此可以采用650mt的磁场强度。其余部位的可不加载磁场。
48.依照上述实施步骤实现gh4169镍基高温合金的无扩口管路连接,磁场加载强度为650mt,磁场加载角度为90
°
,磁流变弹性胶套在管套的环形槽口处弹性模量为1.54mpa,可以满足对管径为φ16mm的gh4169镍基高温合金管件成形需求;
49.实施例3
50.请参阅图1-图4,本发明的一种用于无扩口管路连接的磁流变弹性体胀形方法如下:
51.第一步,采用6061铝合金作为金属管材,选取壁厚为1mm、管径为φ15mm的6061铝合金备用;
52.第二步,分别以100:10的质量比加入硅和催化剂并均匀搅拌。之后,加入质量分数为25%的二甲基硅油。搅拌均匀后,加入质量分数为50%的羰基铁粉充分搅拌。完成上述步骤后,将液态mr混合物倒入模具中,置于预热至70℃的传热段进行固化,制成磁流变弹性胶套,形式为空心圆柱体。
53.第三步,采用yg8钨钢合金作为胀形模,即作为管套。依次采用1~6号金相砂纸打磨导管和管套表面,然后将其机械抛光直至在金相显微镜下没有明显的划痕,并在去离子水、丙酮、无水乙醇及去离子水中超声清洗10min,晾干待用;
54.第四步,将制作好的磁流变弹性胶套装入如附图1无扩口管路连接磁流变弹性体胀形方法装置,随后将拉杆的运动功率参数输入到动力控制系统中,进行无扩口导管端头连接过程。在整个成形过程中,是在可调节磁场环境下对复杂曲面导管进行胀形的,利用磁流变弹性胶套在不同磁场加载强度下性能不同,对磁流变弹性胶套压缩性精确控制,实现不同的胀形效果。在管套的环形槽口处,所需要的成形力要大一些,因此需要此处的磁流变弹性胶套的弹性模量更高一些,因此可以采用321mt的磁场强度。其余部位的可不加载磁场。
55.依照上述实施步骤实现铝合金的无扩口管路连接,外加磁场强度为650mt,磁场加载角度为90
°
,磁流变弹性胶套在管套的环形槽口处弹性模量为1.54mpa,可以满足对管径为φ15mm的铝合金导管对于特定管套成形需求。
56.实施例4
57.请参阅图1-图4,本发明的一种用于无扩口管路连接的磁流变弹性体胀形方法如下:
58.第一步,采用gh4169镍基高温合金作为金属管材,选取壁厚为0.8mm、管径为φ16mm的gh4169镍基高温合金备用;
59.第二步,采用aisi 316不锈钢合金作为胀形模,即作为管套。依次采用1~6号金相砂纸打磨导管和管套表面,然后将其机械抛光直至在金相显微镜下没有明显的划痕,并在去离子水、丙酮、无水乙醇及去离子水中超声清洗10min,晾干待用;
60.第三步,首先,硅橡胶、磁性颗粒和硅油的混合物均匀混合。之后,放入真空容器中,吸尘后,倒入
±
29*13mm的圆柱形模具中进行固化,磁纤维带方向与圆柱形形样品的轴向平行。在500mt磁场强度和70℃条件下,将样品放置在磁纤维和固体纤维中0.5小时,形成内部磁性粒子的链向。此后,在去除磁性纤维后,样品在70℃下为固体纤维,为0.5小时,以得到mre样品。其中一部分mre的磁性粒子浓度为26.4%%,另一部分为11.9%。之后制作成胶套。
61.第四步,将制作好的磁流变弹性胶套装入如附图1所示无扩口连接工艺装置,随后将拉杆的运动功率参数输入到动力控制系统中,进行无扩口导管端头连接过程。在整个成形过程中,固定磁场环境,对复杂曲面导管进行胀形通过磁流变弹性胶套磁性粒子浓度的不同来实现。在管套的环形槽口处,所需要的成形力要大一些,因此需要此处的磁流变弹性胶套的磁性粒子浓度更高一些,因此在环形槽口处采用磁性粒子浓度为26.4%的磁流变弹性胶套。
62.依照上述实施步骤实现gh4169镍基高温合金的无扩口管路连接,外加磁场强度为650mt,磁场加载角度为90
°
,磁流变弹性胶套在管套的环形槽口处体积模量为354.8mpa,可以满足对管径为φ16mm的gh4169镍基高温合金对于特定管套成形需求。
63.实施例5
64.请参阅图1-图4,本发明的一种用于无扩口管路连接的磁流变弹性体胀形方法如下:
65.第一步,采用6061铝合金作为金属管材,选取壁厚为1mm、管径为φ15mm的6061铝合金备用;
66.第二步,采用yg8钨钢合金作为胀形模,即作为管套。依次采用1~6号金相砂纸打磨导管和管套表面,然后将其机械抛光直至在金相显微镜下没有明显的划痕,并在去离子水、丙酮、无水乙醇及去离子水中超声清洗10min,晾干待用;
67.第三步,首先,硅橡胶、磁性颗粒和硅油的混合物均匀混合。之后,放入真空容器中,吸尘后,倒入
±
29*13mm的圆柱形模具中进行固化,磁纤维带方向与圆柱形形样品的轴向平行。在500mt磁场强度和70℃条件下,将样品放置在磁纤维和固体纤维中0.5小时,形成内部磁性粒子的链向。此后,在去除磁性纤维后,样品在70℃下为固体纤维,为0.5小时,以得到mre样品。其中一部分mre的磁性粒子浓度为44.7%,另一部分为11.9%。之后制作成胶套。
68.第四步,将制作好的磁流变弹性胶套装入如附图1所示无扩口连接工艺装置,随后将拉杆的运动功率参数输入到动力控制系统中,进行无扩口导管端头连接过程。在整个成形过程中,固定磁场环境,对复杂曲面导管进行胀形通过磁流变弹性胶套磁性粒子浓度的不同来实现。在管套的环形槽口处,所需要的成形力要大一些,因此需要此处的磁流变弹性胶套的磁性粒子浓度更高一些,因此在环形槽口处采用磁性粒子浓度为44.7%的磁流变弹性胶套。
69.依照上述实施步骤实现铝合金的无扩口管路连接,外加磁场强度为650mt,磁场加载角度为90
°
,磁流变弹性胶套在管套的环形槽口处体积模量为389.9mpa,可以满足对管径为φ15mm的铝合金导管对于特定管套成形需求。