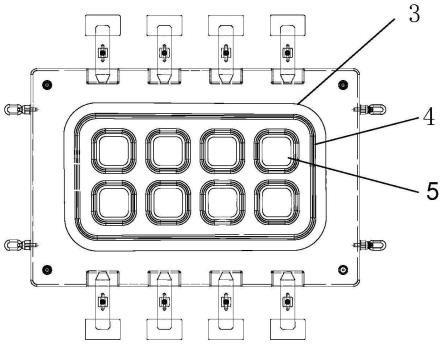
1.本发明属于航空航天领域,具体涉及一种航空钣金口盖类零件成型方法。
背景技术:2.目前,现有技术的成型方案的劣势:
3.1、现有技术中成型航空钣金口盖类零件所使用的设备为进口77000t胶囊压力机、盐浴炉,投资成本大;
4.2、设备使用频次高,占用设备资源时间长,且影响设备使用寿命;
5.3、成型(压形工序、热处理工序)工序繁杂,零件加工周期长,生产效率低;
6.4、压形过程中零件r角转接处易出现断裂现象,从而产生报废,生产成本高;
7.5、多次热处理影响零件机械性能,且热处理后零件变形大,校形、整形工作量大。
技术实现要素:8.本发明提供一种钣金口盖类零件成型方法,其目的是为了减少零件成型工序,降低生产成本、提高生产效率。
9.为了实现上述目的,本发明采取下述技术方案:
10.一种钣金口盖类零件成型方法,包括以下步骤:
11.步骤一、在压力机上安装与待成型的口盖类零件窝型腔匹配的上凸模和下凹模;
12.步骤二、将零件坯料设置在上凸模与下凹模之间,在零件坯料上表面的圆周处设置软质弹性压边圈ⅰ,完成第一次压型;
13.步骤三、将第一次压型后的零件坯料翻面,在其翻面后的上表面圆周处设置软质弹性压边圈ⅰ,完成第二次压型;
14.步骤四、将软质弹性压边圈ⅰ依次更换为软质弹性压边圈ⅱ、软质弹性压边圈
ⅲ……
软质弹性压边圈n,其中n≥2,每更换一次软质弹性压边圈,完成一次压型;其中,软质弹性压边圈ⅰ、软质弹性压边圈ⅱ、
……
软质弹性压边圈n的厚度依次递减;
15.步骤五、撤销软质弹性压边圈,完成最后一次压型;
16.步骤六、切割去余量,淬火校型。
17.进一步的,步骤一中,在待成型的口盖类零件上成型若干个窝型腔,所述若干个窝型腔呈对称结构。
18.进一步的,步骤二中,第一次压型后,对每个窝型腔,以其中心为圆心,开设止裂孔。
19.进一步的,步骤二中,对开设止裂孔的零件坯料进行完全退火,完全退火的条件为:在温度413
±
15℃下,保温至少2h,随炉冷却至260℃,然后空气环境下冷却。
20.进一步的,步骤三中,对于窝型腔呈左右对称分布的零件坯料,首先左右两边对换后,再翻面反压。
21.进一步的,步骤四中,对第三次压型后的零件坯料进行中间退火,中间退火的条件
为:在温度为340
±
10℃下,保温0.5h-1h,空气环境下冷却。
22.进一步的,步骤四中,当n=4时,将软质弹性压边圈ⅰ依次更换为软质弹性压边圈ⅱ、软质弹性压边圈ⅲ和软质弹性压边圈ⅳ,对应依次完成第三次压型、第四次压型和第五次压型。
23.进一步的,所述第一次压型的压力为800t-1000t,保压10s,第二次压型的压力为800t-1000t,保压10s,第三次压型的压力为1000t-1200t,保压10s,第四次压型的压力为1200t-1500t,保压10s,第五次压型的压力为1200t-1500t,保压10s。
24.进一步的,所述软质弹性压边圈ⅰ、软质弹性压边圈ⅱ、软质弹性压边圈ⅲ和软质弹性压边圈ⅳ的厚度依次为25mm、10mm、5mm和3mm,其硬度值均为70
°‑
80
°
。
25.进一步的,步骤五中,所述淬火的条件为494℃,保温30-40min,淬火水冷后冷冻保存。
26.采用本发明的技术方案成型航空钣金口盖类零件,具有以下优点:
27.1、使用现有的设备(国产2000t橡皮容框压力机、空气炉)加以简单改造,投资成本小;同时释放进口77000t胶囊压力机床的产能,提高零件生产效率;
28.2、设备使用频次低,占用设备资源时间短,设备使用寿命延长;
29.3、降低零件成形和热处理的次数,压形工序、热处理工序少,节约生产成本,显著提高生产效率;
30.4、有效解决压形过程中零件r角转接处断裂现象,降低生产成本,提高零件的成品率;
31.5、减少热处理次数,有效解决热处理变形问题,减少校形、整形工作量;
32.6、本发明的工艺方法简单,可批量生产。
附图说明
33.图1是压力机的轴测图;
34.图2是压力机的主视图;
35.图3是双排八孔类口盖零件成型示意图;
36.图4是单排三孔口盖零件成型示意图;
37.图5是软质弹性压边圈的安装位置示意图;
38.图6是成型后的口盖类零件结构示意图;
39.图中,1、上台面,2、下台面,3、零件坯料,4、软质弹性压边圈,5、窝型腔,6、止裂孔。
具体实施方式
40.下面将结合实施例和附图,对本发明的技术方案进行清楚、完整地描述,显然,所描述的实施例仅是发明的一部分实施例,而不是全部的实施例,基于本发明中的实施例,本领域普通技术人员在没有做出创造性劳动的前提下所获得的所有其他实施例,都属于本发明保护的范围。
41.具体实施方式一
42.一种钣金口盖类零件成型方法,包括以下步骤:
43.步骤一、压力机选取国产2000t胶囊容框压力机床,加装带t型槽的上台面1和下台
面2,在带t型槽的上台面1和下台面2上分别安装与待成型的口盖类零件窝型腔5匹配的上凸模和下凹模,成型飞机口盖类零件,工装结构见图1和图2;选取国产2000t胶囊容框压力机代替进口的77000t胶囊压力机上单面模的航空钣金成型方式,释放贵重设备机床产能;
44.步骤二、将零件坯料3设置在上凸模与下凹模之间,在零件坯料3上表面的圆周处设置软质弹性压边圈ⅰ,完成第一次压型;对每个窝型腔5,以其中心为圆心,开设止裂孔6;对开设止裂孔6的零件坯料3进行完全退火,完全退火的条件为:在温度413
±
15℃下,保温至少2h,随炉冷却至260℃,然后空气环境下冷却。此时选择完全退火的原因:零件第一次压型后材料变形量大,应力过于集中,其目的是释放零件应力;
45.步骤三、将第一次压型后的零件坯料翻面,在其翻面后的上表面圆周处设置软质弹性压边圈ⅰ,完成第二次压型;
46.步骤四、将软质弹性压边圈ⅰ依次更换为软质弹性压边圈ⅱ、软质弹性压边圈
ⅲ……
软质弹性压边圈n,其中n≥2,每更换一次软质弹性压边圈,完成一次压型;其中,软质弹性压边圈ⅰ、软质弹性压边圈ⅱ、
……
软质弹性压边圈n的厚度依次递减;
47.步骤五、撤销软质弹性压边圈4,完成最后一次压型;
48.步骤六、切割去余量,淬火校型。
49.进一步的,步骤一中,在待成型的口盖类零件上成型若干个窝型腔5,所述若干个窝型腔5呈对称结构。
50.进一步的,步骤三中,对于窝型腔5呈左右对称分布的零件坯料3,首先左右两边对换后,再翻面反压,不仅实现了聚料的目的,而且还有效解决过度r处的开裂问题,大幅度降低报废率。
51.进一步的,步骤四中,对第三次压型后的零件坯料3进行中间退火,中间退火的条件为:在温度为340
±
10℃下,保温0.5h-1h,空气环境下冷却。
52.进一步的,步骤四中,当n=4时,将软质弹性压边圈ⅰ依次更换为软质弹性压边圈ⅱ、软质弹性压边圈ⅲ和软质弹性压边圈ⅳ,对应依次完成第三次压型、第四次压型和第五次压型。
53.进一步的,所述软质弹性压边圈ⅰ、软质弹性压边圈ⅱ、软质弹性压边圈ⅲ和软质弹性压边圈ⅳ的材质优选聚氨酯材料;
54.进一步的,步骤五中,所述淬火的条件为494℃,保温30-40min,淬火水冷,校型前低温保存,优选温度≤-18℃,校型后常温保存。
55.由于零件加强窝型腔5深度过大,本发明的方案中上、下压模结构直接成型零件,为防止零件走料不均匀而导致零件窝型腔及其周边边缘出现皱褶现象,软质弹性压边圈代替工装压边圈,见图3和图4,通过设置软质弹性压边圈4厚度逐层递减的方式成型零件。
56.结合不同形状的产品特点及不同厚度的软质弹性压边圈垫板厚度,压力也不尽相同,详见下表。
[0057][0058]
软质弹性压边圈垫板的合理选择在零件成型时起到最关键的作用,此方案解决了工装无压边力的情况,同时与汽车行业冲压件的金属压边圈相比,简化模具结构,大幅度降低了工装的生产成本,一套带压边圈的口盖类引申模具的价格在50-70万之间,此方案模具制造配合聚氨酯垫板模具的费用是上述的15-20%。
[0059]
根据实际成型的产品,选择不同厚度的软质弹性压边圈,压型的次数也可根据实际情况确定。
[0060]
①
本发明采用翻面反压的聚料方式(反挤压成型)。
[0061]
金属挤压成型是对放在模具模腔内的金属坯料施加强大的压力,迫使金属坯料产生定向的塑性变形,从挤压模的模孔中挤出而获得所需断面形状、尺寸并具有一定力学性能的零件或半成品的塑性加工方法。
[0062]
反挤压:通过正挤压初成型对金属零件本身塑性得到提高,再进行反挤压,金属流动方向与凸模运动方向相同,在挤压过程中,被挤压金属在变形区能获得强烈和均匀的三向压缩应力状态,这就充分发挥了被加工金属本身的塑性。
[0063]
根据航空口盖类产品的形状特点:呈轴向对称的单排窝型腔,第一步用25mm厚的聚氨酯垫圈800-1000t压力成形后,完全去应力退火,第二步再翻面反压;如果是成型左右对称分布的双数排窝型腔,第一步用25mm厚的聚氨酯垫圈800-1000t压力成形后,完全去应力退火,第二步左右边对换后,再翻面反压,这样即实现了聚料的目的,从而有效解决过度r处的开裂问题,大幅度降低报废率。
[0064]
2航空钣金件一步法成型的合理应用
[0065]
航空铝合金钣金零件一步法是将淬火后的铝合金板材采用低温贮存(≤-18℃)的办法来保持铝合金薄板在新淬火状态下的良好塑性,并以机械化手段一次完成新淬火状态板料的成形和校型工作。
[0066]
现有技术中最终热处理(淬火)后的工件,变形量极大,工人校形难度大、周期长,一般单件在6-8小时左右。
[0067]
优选的,本发明方案的步骤中,在零件最后一步成形前,选择保留3mm的欠压量,先进行中间退火消除应力,之后按照最终使用状态淬火,淬火后直接上压模成形至最终状态,如此成形后基本消除热处理后的变形量,这样能有效解决热处理变形量而带来的校形、整形工作量增大的问题,工人校型时间一般在1-2h之内。工人校型效率大幅度提高。
[0068]
实施例1
[0069]
采用双排八孔类口盖零件成型为例,详细介绍本发明的具体步骤。
[0070]
此零件成型分以下九步成型,较比原有成型方案减少3-4次热处理(中间退火)工序,大幅度提升零件生产效率。
[0071]
第一步:在零件坯料的上表面圆周处放置25mm厚度的聚氨酯压边圈垫板ⅰ,压力800t,保压10秒,完成第一次压型,具体现场照片见图1;
[0072]
第二步:以加强窝型腔中心为圆心,开直径为80mm的止裂孔,零件坯料进行完全退火。此时选择完全退火的原因:零件第一步压型后材料变形量大,应力过于集中,退火的目的是为了释放零件应力。完全退火具体的要求是:温度为413
±
15℃,保温至少2h,随炉冷却至260℃,然后空气中冷却;
[0073]
第三步:将退火后的零件坯料翻面,在翻面后零件坯料上表面的圆周处放置25mm厚度的聚氨酯压边圈垫板ⅰ,反挤压成形,压力800t,保压10秒,完成第二次压型;
[0074]
第四步:将25mm厚度的聚氨酯压边圈垫板ⅰ更换为10mm厚度的聚氨酯压边圈垫板ⅱ,压力1000t,保压10秒,完成第三次压型;
[0075]
第五步:中间退火,中间退火具体要求是:温度为340
±
10℃,保温0.5h-1h,空气中冷却;
[0076]
第六步:将10mm厚度的聚氨酯压边圈垫板ⅱ更换为5mm厚度的聚氨酯压边圈垫板ⅲ,压力1200t,保压10秒,完成第四次压型;
[0077]
第七步:将5mm厚度的聚氨酯压边圈垫板ⅲ更换为3mm厚度的聚氨酯压边圈垫板ⅳ,压力1400t,保压10秒,完成第五次压型;
[0078]
第八步:撤消聚氨酯压边圈垫板ⅳ,压力1200t,保压10秒;
[0079]
第九步:按切割线去余量,淬火校型。淬火具体要求:494℃保温30-40min淬火水冷。
[0080]
成型后的口盖类零件结构示意图如图6所示。
[0081]
此外,应当理解,虽然本说明书按照实施方式加以描述,但并非每个实施方式仅包含一个独立的技术方案,说明书的这种叙述方式仅仅是为清楚起见,本领域技术人员应当将说明书作为一个整体,各实施例中的技术方案也可以经适当组合,形成本领域技术人员可以理解的其他实施方式。