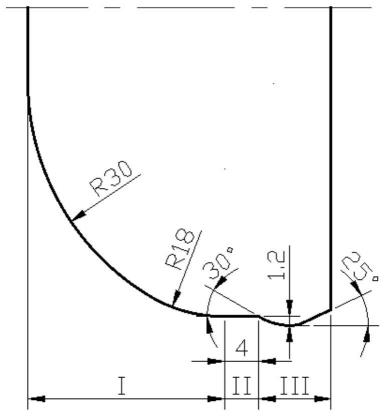
1.本发明涉及薄壁深杯形件的旋压工艺,尤其涉及一种多型面旋轮及其双重组合复合旋压成形方法。
背景技术:2.用于薄壁深杯形件旋压成形的毛坯又可以分为车削毛坯和板料毛坯,前者仍然需要采用棒料进行车削,首先得到厚壁浅杯形车削毛坯,再采用多个台阶旋轮进行流动旋压成形,最终得到薄壁深杯形零件,同样会在车削毛坯时产生材料浪费,并且破坏材料内部纤维结构、降低材料机械性能。而后者采用板料作为旋压毛坯,则一般先用一个或多个弧形型面旋轮进行拉深旋压,获得厚壁浅杯形件,再更换旋压机床或更换工装,采用多个台阶旋轮进行流动旋压成形,最终获得薄壁深杯形零件。
3.也有采用至少三个将拉深旋压面与流动旋压面组合的旋轮,在电流辅助条件下将板料毛坯旋压成为杯形件的,但由于需要电流辅助,增加了工装的复杂程度和加工成本,而且多个旋轮的型面与工件的接触情况较难协调,增加了工艺调整的难度。同时由于拉深旋压后的回弹作用难免会导致工件与芯模之间存在大小不一致的间隙,给后续流动旋压成形带来一定的不利影响。
技术实现要素:4.本发明的目的在于克服上述现有技术的缺点和不足,提供一种多型面旋轮及其双重组合复合旋压成形方法。
5.本发明通过下述技术方案实现:
6.一种多型面旋轮,所述多型面旋轮的型面依次包括弧形型面i、圆柱形型面ii和锥形型面iii;其中,
7.所述弧形型面i,用于拉深旋压;
8.所述圆柱形型面ii,用于贴模整形;
9.所述锥形型面iii,用于流动旋压。
10.所述弧形型面i的外径<圆柱形型面ii的外径,圆柱形型面ii的外径<锥形型面iii的外径。
11.所述圆柱形型面ii的外径与锥形型面iii的外径之差,为坯料最终减薄量的0.8~1.2倍。
12.所述圆柱形型面ii的轴向长度,为坯料初始厚度的1~2倍。
13.一种双重组合旋轮复合旋压成形方法;在成形过程中,将所述多型面旋轮,作为第一层次组合旋轮;将第一层次组合旋轮与多个流动旋轮,共同作为第二层次组合旋轮;
14.具体包括如下步骤:
15.步骤一,第一层次组合旋轮对坯料进行拉深旋压成形、贴模整形和流动旋压成形,以完成第一层次复合旋压成形;
16.步骤二,将第一层次组合旋轮与多个流动旋轮进行组合,共同作为第二层次组合旋轮,并共同完成第二层次复合旋压成形;进而完成双重组合旋轮复合旋压成形。
17.所述第二层次复合旋压成形过程中,第一层次组合旋轮的数量为一个,流动旋轮的数量为两个;
18.其中,一个第一层次组合旋轮和两个流动旋轮,围绕旋压机芯模中心线呈120
°
均匀分布。
19.所述第一层次复合旋压成形和第二层次复合旋压成形过程中,包括单道次拉深旋压、单道次流动旋压、单道次拉深旋压、多道次流动旋压。
20.所述第一层次复合旋压成形和第二层次复合旋压成形过程中,包括多旋轮错距旋压和多旋轮等距旋压。
21.本发明相对于现有技术,具有如下的优点及效果:
22.在对薄壁深杯形件的旋压成形过程中,本发明将多型面旋轮,作为第一层次组合旋轮;将第一层次组合旋轮与多个流动旋轮,共同作为第二层次组合旋轮;具体步骤是:步骤一,第一层次组合旋轮对坯料进行拉深旋压成形、贴模整形和流动旋压成形,以完成第一层次复合旋压成形;步骤二,将第一层次组合旋轮与多个流动旋轮进行组合,共同作为第二层次组合旋轮,并共同完成第二层次复合旋压成形;进而完成双重组合旋轮复合旋压成形。
23.由上述技术特征可知,本发明(1).可以采用板料毛坯直接旋压成薄壁深杯形零件,提高了零件的机械性能,降低了零件的加工成本。(2).提高了旋压工艺设计的灵活性,既可以完成单旋轮单道次或多道次拉深旋压,又可以完成多旋轮单道次或多道次流动旋压,还可以完成拉深旋压和流动旋压道次数的不同组合。并且既可以用于等距旋压,还可以用于错距旋压,同时在调整旋轮错距量的时候,不用特别顾虑第一个旋轮组合型面的影响。(3).有利于提高旋压件的成形质量,得到高精度的旋压件。
附图说明
24.图1是薄壁深杯形件示意图;
25.图2是本发明多型面旋轮示意图;
26.图3是本发明图2所示多型面旋轮,应用于双重组合旋轮复合旋压过程示意图;其中编号1-3为三个错距布置的多型面旋轮;
27.图4是本发明工艺应用举例,图中为柔轮制齿的薄壁杯形旋压坯示意图。
具体实施方式
28.下面结合具体实施例对本发明作进一步具体详细描述。
29.实施例1
30.图1所示为本发明工艺中,所涉及的深杯形薄壁件工艺举例;
31.材料为08钢,零件外径d=80mm,壁厚t1=0.6mm,高度h=110mm,底部厚度t0=3.0mm,用于打孔固定零件。按本发明旋压工艺进行设计和成形:
32.(1).查手册可知修边余量:δ=5mm,于是材料体积:v≈π(h+δ-t0)dt1+0.25πd2t0=31953mm3;板料毛坯初始直径:d0=2[v/(πt0)]
1/2
≈116mm。拉深系数:80/116≈0.69,大于一次拉深成形的极限拉深系数0.46~0.6,可以一次拉深成形,判定也可以通过一次拉深旋
压成形。
[0033]
(2).图2为1#(即第一层次组合旋轮的多型面旋轮)旋轮设计,其型面结构为:其中弧形型面i,用于拉深旋压成形;圆柱形型面ii,用于贴模整形;锥形型面iii,用于流动旋压成形。圆柱形型面ii的圆柱部分的长度为毛坯初始厚度的1.0~2.0倍,根据毛坯初始厚度3.0mm,08钢强度较低的情况,在3.0~6.0mm中取4.0mm,再根据圆柱形型面ii的圆柱部分的外径与锥形型面iii外径的差值为坯料总减薄量0.8~1.2倍,毛坯总减薄量为2.4mm,08钢强度较低的情况,在1.9mm~2.9mm中取2.4mm(即半径差1.2mm)。
[0034]
(3)旋压成形:采用三旋轮错距旋压成形,除1#旋轮以外,另外两个旋轮为普通的锥面流动成形旋轮。三个旋轮间隔120
°
围绕在芯模轴线周围,第一道次通过复合旋压成形得到壁厚为1.3mm的杯形件(复合旋压过程示意图如图3所示),在此复合旋压过程中,1#旋轮的弧形部分首先接触坯料进行拉深旋压成形,随后三个旋轮相继开始流动旋压成形。第二道次三个旋轮再通过单一的流动旋压成形将壁厚由1.3mm减薄至0.6mm。最后再将口部余量切除即得图1所示零件。
[0035]
实施例2
[0036]
图4所示为本发明所涉及的另一种用于柔轮加工的旋压制坯工艺举例;
[0037]
材料为30crmnsia钢,零件内径d=55mm,底部厚度2.8mm,壁厚分别为0.4mm和0.7mm,两段壁部高度均为10mm。
[0038]
采用本发明工艺旋压成形的步骤如下:
[0039]
采用厚度2.8mm,直径90mm的板料作为旋压毛坯,采用与实施例1相同的三个旋轮,但由于零件中部有一个台阶,不能进行错距旋压,因此采取等距旋压成形,即三个旋轮的锥形型面部分在芯模半径方向和轴线方向均处于同一位置,第一道次先用复合旋压工序成形为等壁厚1.1mm的杯形件,第二道次再采用单一的流动旋压成形壁部不同厚度,即从底部开始,将壁厚由1.1mm减薄至0.4mm,当满足0.4mm部分的10mm长度时,通过伺服电机将三个旋轮同时向外移动0.3mm,将剩余部分的壁厚由1.1mm减薄至0.7mm,从而完成两段壁厚的一次性旋压成形。
[0040]
如上所述,便可较好地实现本发明。
[0041]
本发明的实施方式并不受上述实施例的限制,其他任何未背离本发明的精神实质与原理下所作的改变、修饰、替代、组合、简化,均应为等效的置换方式,都包含在本发明的保护范围之内。