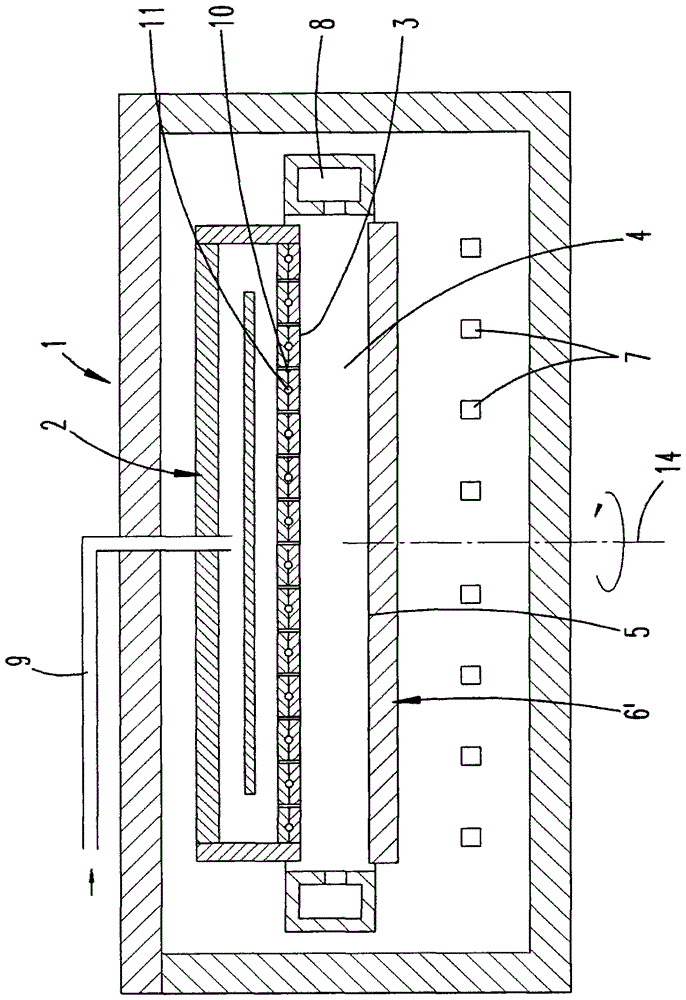
该发明涉及一种清洁CVD(化学气相沉积)-反应器过程室的方法,该过程室具有一个可由加热装置进行加热的基座作为过程室底座和一个与过程室底座对置的过程室盖罩,在CVD过程中在过程室底座和过程室盖罩上形成的寄生覆层通过借助加热装置加热底座和输入腐蚀气体在两个相继的清洁过程中加以去除。
背景技术:DE10102745C2说明了一种CVD-反应器和一种用于清洁CVD-反应器的方法,含氟气体被输送至反应室内,在反应室内该气体借助等离子体进行电离。DE19832566C2说明了一种用于清洁CVD-反应器过程室的方法,在清洁过程中重复变化过程室的压力和温度。使用氯氟化合物作为腐蚀气体。DE102006018515A1说明了一种方法,对于该方法而言,CVD-反应器的过程室通过输入腐蚀气体进行清洁。由于在腐蚀时过程室盖板会下降,过程室的高度降低,从而使得过程室的底座和盖板可以同时通过腐蚀加以清洁。DE3888736T2=EP0296804B1说明了一种CVD-反应器过程室清洁方法。在基座放电后,将含氯化氢的腐蚀气体的强气流输送至过程室中,以便对基座进行清洁。在基座清洁后,气体成分发生变化,整个反应器室上聚集的沉积物被清除。US6,242,347B1说明了一种用于清洁过程室,尤其是基座的两阶段腐蚀方法,对此在清洁过程中将“PlaceboWafer(安慰晶片)”置于基座上,以便在清洁过程中保护基座的表面。建议使用石英片作为安慰晶片。US2005/0242061A1说明了一种CVD-反应器清洁方法,对此将清洁气体输入过程室中,并在过程室中形成等离子体。US5,812,403说明了一种CVD-反应器和一种通过腐蚀去除在涂敷过程中附着在过程室表面的涂层。使用和涂层反应的反应气体。US6,042,654说明了一种通过输入氯气对CVD-反应器的过程室进行清洁的过程,氯气在热分解过程中分解为自由基。EP0855453A1或者US5,348,587说明了一种方法,对于该方法而言,使用通过等离子体进行分解的含氯气体作为腐蚀气体,以便对CVD-反应器过程室的覆层和内壁加以清洁。US6,242,347B1说明了一种两阶段清洁方法,可以对CVD-反应器过程室在涂敷过程中形成的覆层加以清洁。此处使用氯化合物作为腐蚀气体。对于该清洁步骤而言,过程室必须加热至比涂敷过程的过程温度更高的温度。DE3888736T2说明了一种硅外延附生物分离方法,在分离过程后过程室通过输入腐蚀气体进行清洁。过程室包含一个过程室盖板和一个用于支承待涂敷基材的基座,该基座可以由下方进行加热,DE102006018515A1,DE102006013801A1和DE10217806A1对这一特征作了说明。在该装置中,基材被放置在基座上,通过输送过程气体涂覆半导体涂层或者类似涂层。过程气体不仅会在基材的表面进行热分解,而且也会对裸露的、未被基材覆盖的基座表面区域以及过程室盖罩的表面进行热分解。在实施一次或者多次涂覆过程后必须清除寄生覆层。对此使用诸如氯化氢或者氯气。此外,清洁过程的效率还取决于待清洁表面的表面温度。通过在下方进行加热,将基座表面温度提高至进行腐蚀过程的600至650摄氏度。过程室盖罩由基座的辐射热量进行加热,因此温度稍低。为了更有效地实施腐蚀过程,上述现有技术建议减小过程室盖罩和过程室底部之间的垂直距离,以便可以在辐射热量传递的过程中过程室盖罩可以获得更高的温度。此外,由于基座的特征,尤其是基座表面的涂层,基座无法被加热超过特定的极限温度,因此基座的可加热性受限。
技术实现要素:该发明的所要解决的技术问题在于更高效地实施清洁过程。首先,建议在第一个清洁步骤中在第一个清洁温度下主要对过程室底部进行清洁。该清洁步骤可以在一个低于基座最大可负载温度的温度下进行。在该请解步骤下,过程室盖罩的表面温度低于过程室底部的表面温度,因此在第一清洁步骤中主要、必要时仅对过程室底部进行清洁。在实施第一清洁步骤后,过程室冷却至较低的温度。将基座从过程室中移除。然后在第二清洁温度下在第二清洁步骤中对过程室盖罩进行清洁。在第二清洁步骤中主要对过程室盖罩,或者说仅对过程室盖罩进行清洁。在第二个清洁步骤中可以将在第一个清洁步骤中清洁过的基座替换为具有这样性能的辅助基座,即能够使得过程室盖罩的表面温度加热至高于在第一清洁步骤中达到的过程室盖罩温度,且该温度足够确保对盖罩实施高效的清洁。第二清洁温度可以高于第一清洁温度。过程室盖罩在第二清洁过程中至少拥有比第一清洁步骤更高的清洁温度。辅助基座可以是一种适用第二清洁步骤而生产的、并且其结构与此相关地进行过优化的固体。但也可以使用之前多次进行过涂覆过程的废旧基座。优选使用卤素化合物,例如氯化氢和氯气作为腐蚀气体。但在相应的高温下也可以仅使用氢气作为腐蚀气体。在第一个清洁步骤中,基座优选加热至600至650摄氏度的温度。辅助基座在第二清洁过程中加热至明显更高的温度,例如800至1000摄氏度。也可以超过1000摄氏度,例如如果使用氢气作为腐蚀气体,加热至超过1200摄氏度的温度。第一和/或第二清洁步骤可以包含多个子周期,对此多个周期通过所使用的腐蚀气体和/或清洁温度加以区分。涂覆步骤在清洁步骤之前。该涂覆步骤是一种MOCVD(金属有机化合物化学气相淀积)-方法,在该方法中,将第III或者第II主族金属有机化合物和同时或者与之交替地将第V或者第VI主族元素的氢化物以及必要时与惰性气体一起输送至过程室中。过程气体在过程室中发生热分解,并在基座上的一个或者多个基材上离析出单晶半导体涂层。使用TMAI、TMGa和/或者TMIn作为过程气体。为形成InGaAs、AlN、AlGaN,金属有机成分和AsH3、PH3或者NH3一起或者与AsH3、PH3或者NH3交替地输送至过程室中。输送过程借助气体输入装置进行,通过该装置也可以在该清洁步骤中将腐蚀气体输送至过程室中。过程气体或者清洁气体通过气体排出装置从过程室中重新排出。在涂覆过程或者清洁过程中,过程气体或者清洁气体在过程室内流动。不管是涂覆过程还是清洁过程,均优选使用额外的载气,该气体可以是氢气、氮气,也可以是惰性气体。涂覆过程或者腐蚀过程也可以在不同的总压力下进行。在涂覆过程或者清洁过程中,过程室中的气体总压力介于100至900mbar之间。在一种特别优先使用的腐蚀方法中,在沉积过程和从过程室中取出晶片后,首先在600至800摄氏度的温度下进行低温腐蚀步骤,在该步骤中使用氯气作为腐蚀气体。在一个或者多个借助氮气或者氯气从过程室去除腐蚀物的冲洗步骤后,将底座或者过程室加热至1100摄氏度以上。然后在该温度下通过输入氢气进行第二个清洁步骤。在过程室冷却后可以重新放入待涂覆的基材。如果使用辅助底座,则需要更换为可放置基材或者已经放置有待涂覆基材的基座。附图说明该发明的实施例在下文中结合附图加以说明。在附图中:图1示出CVD-反应器横截面,其基本原理由DE102006013801A1已知,图2示出根据图1所示的CVD-反应器,其中基座6替换为辅助底座6′,图3示出本发明的第二个实施例,CVD-反应器基本原理由DE102006018515A1已知,图4示出根据图3所示的CVD-反应器,其中基座6更换为辅助基座6′。具体实施方式图1和2所述的反应器的结构和作用原理引用DE102006013801A1,其公开的内容已经全部在该申请中作了说明。在一个相对于外部气密地密封的反应器外壳1中存在过程室4。过程室4的盖罩3由气体输入装置2的下端组成,该气体输入装置为喷头状。通过输送管9将过程气体或者清洁气体输送至气体输送装置2的内部。过程气体或者清洁气体通过气体输送装置2的下端离开其内部,在该下端处具有大量的气体排出开口10。在该结构示例中,如果在涂覆过程中应对过程室盖罩3进行冷却,气体输入装置的下端具有流淌有冷却液体的冷却管道11。过程室4的底部5由和气体输入装置2对置的基座6上端构成。基座6可以是由石墨、钼或者其他合适的材料制成的固体。基本上呈圆盘状的过程室被环状的气体排出装置8所包围。在基座6的下方是以附图标记7表示的加热装置,该加热装置配备有红外辐射器或者RF-加热器。借助该加热装置,基座6可以加热至过程温度或者清洁温度。在涂覆过程中,在基座6上放置一个或者多个基材(参见DE102006013801A1)。在按规定使用CVD-反应器时,通过气体输送管9或者多个为了简化此处未作说明的其他气体输送管将一种或者多种过程气体输送至气体输入装置2中,并经由气体排出开口10进入过程室4内。过程气体可以使用AsH3、PH3、NH3、或者TMAl、TMGa或者TMIn。过程气体随同载气,例如氢气或者氮气输送至过程室4中。基座6在涂覆时加热至过程温度,在该温度下,过程气体进行热分解,从而使得基材上离析出InGaAs、AlN和/或者AlGaN涂层。在一个或者多个这一类的涂层离析步骤(在这些步骤中一种或者多种涂层在基材上在不同的过程参数下进行离析)后,将已涂覆的基材从过程室取出。在涂覆过程中,在过程室盖罩3或者在过程室底部5上未被基材覆盖到的区域形成覆层。该覆层在根据该发明的清洁步骤(腐蚀步骤)中加以去除。在第一个清洁步骤中,在第一清洁温度下主要对过程室底部5进行清洁。对此,通过气体输送管9将腐蚀气体,例如氯化氢或者氯气输送至气体输入装置2中。该输入过程和载气,例如氢气或者氮气一起进行。气体混合物经由气体排出开口10进入过程室4中。在第一个清洁步骤中,底座6,也就是过程室底部5,被加热至大约600至650摄氏度。在该温度下,腐蚀气体和覆层发生反应。该反应过程为干式腐蚀过程,在化学反应的过程中,覆层转变为气态。气状的覆层反应产物由载气输送至气体排出装置8中,并通过该排出装置离开过程室4。在第一个清洁步骤中,过程室盖罩3被辐射加热至较低的温度。该温度不足以让过程室盖罩3通过干式腐蚀进行有效的清洁。在结束第一个清洁步骤后,过程室通过惰性气体,例如氮气或者氢气进行冲洗和冷却,直至基座6达到允许将其从反应器外壳1中移除的温度。在该实施例中,基座6被替换为辅助基座6′。辅助基座6′可以是一个单独针对第二清洁步骤生产的物体。例如与基座6相比,该辅助基座可以具有更小的横截面,且具有更高的耐热性。在一种优选的变型中,基座6仅更换为不再用于涂覆过程的废旧基座,尽管其表面可能在温度负载下出现损伤,但由于该基座不再用于涂覆过程,因此可以接受该情况。在安装辅助基座6′(参见附图2)或者在更换基座(参见附图1)后,过程室通过更大的加热功率借助加热装置7加热至与第一清洁过程相比更高的温度。基座6或者辅助基座6′达到最高1000摄氏度或者超过1000摄氏度的温度。在该温度下,过程室盖罩3被加热至超过600摄氏度的温度,因此可以通过输送腐蚀气体对过程室盖罩3上的覆层进行有效的清除。取代卤素气体,尤其是含氯腐蚀气体,也可以使用在高温下具有腐蚀作用的纯氢气,尤其用于去除过程室盖罩3上的镓或者铝。在该清洁步骤中,冷却管道内无冷却剂。插图3和4所示的结构示例是一种在DE102006018515A1中描述过的MOCVD-反应器。因此可以完全引用该文档公开的内容。同附图1和2所示的反应器,附图3和4所示的反应器拥有一个对称轴14,基座6围绕该轴进行旋转驱动。在附图3和4所示的实施例中,气体输入装置2位于过程室4的中心位置。基座6环状包围气体输入装置。过程室4拥有一个过程室盖罩3,在涂覆过程中,过程室盖罩借助安装在过程室盖罩3上方的冷却装置进行冷却。过程室4的底部5由基座6构成,该基座可以是带涂层的石墨、钼或者其他合适材料制成的固体。待涂层基材放置在旋转驱动的基材支架12上,该支架位于基座6的卡槽中。平放在支架13上的基座在下方使用加热装置7进行加热。该加热过程也可以以IR或者RF的方式进行。在涂覆过程结束并将一个或者多个基材从基材支架12上取下后,第一个清洁步骤中的氯气或者氯化氢通过气体输入装置2和载气一起输送至加热到第一清洁温度的过程室4中。在第一清洁步骤中,过程室底部5,也就是基座6的表面或者基材支架12的表面拥有一个清洁温度,在该温度下覆层和腐蚀气体发生反应,进而形成可离开过程室4的挥发性反应产物。对于该实施例而言,尚未冷却的过程室盖罩3仅受到辐射加热且仅可达到在第一清洁步骤中的表面温度,在该表面温度下腐蚀过程完全无法进行或者仅可低效率进行。在结束第一个清洁步骤且基座6冷却后,将基座6移除,并更换为旧的、不再用于涂覆过程的基座6(附图3)或者更换为单独针对第二清洁过程生产的辅助基座6′(见附图4)。这一类装配有辅助基座6,6′的过程室4同样使用加热装置7进行加热。但辅助基座6,6′加热至比第一清洁步骤更高的温度。在第二清洁步骤中,辅助基座6,6′的表面温度应足够高,从而使得尚未冷却的过程室盖罩3加热至可以有效进行腐蚀过程的温度。在第二清洁步骤中同样使用氯化氢、氯气或者其他合适的气体作为腐蚀气体。也可以通过氢气腐蚀表面。如果过程室盖罩是使用冷却剂冷却的过程室盖罩,可以在第二清洁步骤中关闭冷却装置,从而停止冷却。在腐蚀后,辅助基座6′重新更换为实施涂覆过程的过程基座6。在使用氯气或者氯化氢作为清洁气体时,金属覆层转化为挥发性的氯化物。在第一清洁步骤中,基座6得到清洁,在第二清洁步骤中,过程室盖罩3或者其他远离基座6的表面得到清洁。在接下来的第三个清洁过程中,使用氢气作为腐蚀气体,以便将反应器壁上吸附的氯化物,尤其是吸附的氯通过转化为氯化氢加以去除。所有已经公开的特征(个体)都是本发明的实质内容。在该申请的公开内容中,相关/附带的优先性资料(在先申请副本)的公开内容被完全引用,,对于这些资料的目的、特征也被包含在本发明的权利要求中。从属权利要求能够在其任选的并列的技术方案中独立地刻画现有技术的有创造性的扩展设计,尤其可以基于这些权利要求进行分案申请。附图标记清单:1反应器外壳2气体输入装置3过程室盖罩4过程室5过程室底部6基座7加热装置8气体输出装置9气体输送管10气体输出开口11冷却管道12基材支架13支架14轴线