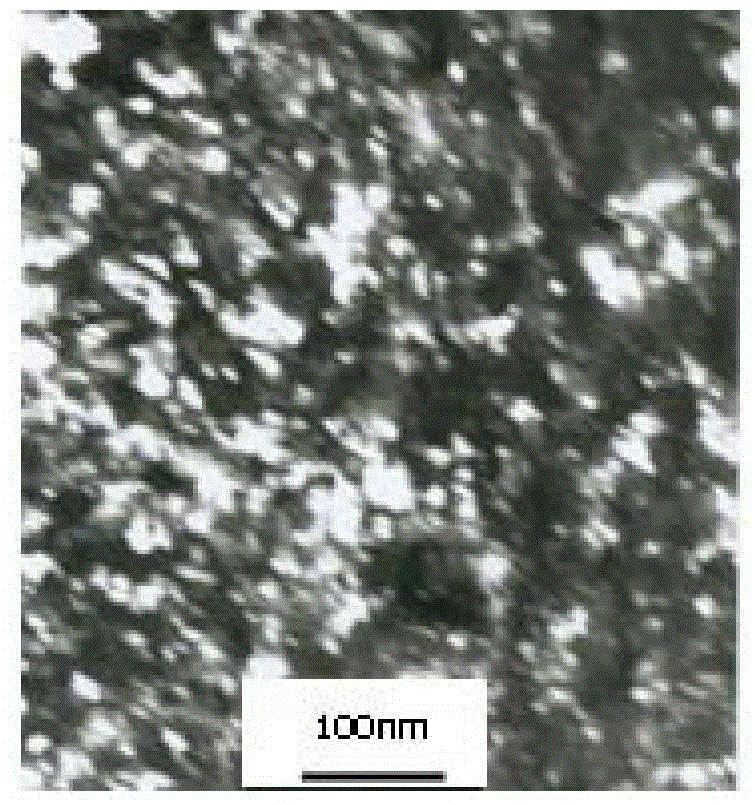
本发明涉及一种钨合金材料,特别涉及一种高比重钨合金材料及其制备方法。
背景技术:高比重钨合金是一类以钨元素为基体材料(含钨量为80%~97%),并适量添加有Ni、Cu、Fe、Co、Mo、Cr等元素组成的合金,由于其克服了钨的脆性,并保持了钨的高熔点、高密度、低膨胀系数等优良性能,因而在航空航天、军事、民用工业等行业中得到了广泛的应用。目前,高比重钨合金的制备主要通过烧结后进行旋转锻造。虽然旋转锻造能够提高钨合金强度,但塑性很差;另外,旋转锻造的一次变形量很小,需要经过多次加热和锻造才能获得较大的变形量,不仅工艺周期长、能耗大、成本高,而且表面质量较差、加工余量较大、材料利用率也较低。静液挤压技术是一种对难变形材料进行塑性加工的工艺,其主要分为冷静液挤压和热静液挤压。冷静液挤压一般采用高压或超高压液体作为压力传递的润滑介质,其使挤压材料置于密封的高压液体中,这样在变形时材料始终处于良好的润滑条件和有利的三向压应力状态下,因此可提高材料的塑性;然而,采用高压液体会带来模具密封和生产安全等问题,并且其变形抗力大、残余应力大,这些因素均限制了其在生产中的实际应用。热静液挤压能够克服冷静液挤压的上述缺陷,因此在生产上具有极大的应用潜力,目前也有少量相关研究。例如,公开号为CN101386947A的发明专利公开了一种高比重钨合金材料及其制备方法,首先将钨粉末、镍粉末、铁粉末和钴粉末混合均匀后制成坯料,然后进行烧结;同时,将石墨和玻璃粉混粉后成型,制成润滑介质;其次,将预热的坯料和润滑介质放入模具中进行挤压,即制得高比重钨合金材料。上述方法将各元素粉末混合后烧结至致密状态,然而由于原料钨粉末的 粒度通常较大(3~10um),在高温烧结后钨合金微观组织较为粗大(钨颗粒尺寸30~40um),材料容易出现成分偏析和严重的坍塌变形,即使通过后续的形变强化工艺也很难将其细化,并且在强度提高的同时会产生塑性降低。此外,现有的钨合金材料在变形量、抗拉强度和延伸率等方面还有待进一步提高。
技术实现要素:本发明提供一种高比重钨合金材料及其制备方法,用于解决现有技术的钨合金材料微观组织粗大,强度提高时塑性降低,合金材料变形量、抗拉强度和延伸率有限等技术缺陷。本发明提供一种高比重钨合金材料的制备方法,包括如下步骤:1)对钨粉进行球磨,制得平均尺寸为亚微米级的改性钨粉;2)将镍粉和铁粉按照质量配比为(6~8):(4~2)混合后进行球磨,制得纳米晶镍铁固溶体;3)将所述改性钨粉和所述纳米晶镍铁固溶体按照质量配比为93:7混粉后,压制成相对密度为70~85%的坯料;4)对所述坯料进行液相烧结,制成相对密度为93.9~99.8%的烧结坯料;5)将粒径为500nm~2.5μm的石墨粉和粒径为5~15nm的二氧化硅粉末按照质量配比为(60~90):(20~40)混粉后进行球磨,随后压制至相对密度为80~90%并制成润滑介质;6)将所述烧结坯料置于所述润滑介质中进行热静液挤压,并对热静液挤压后的烧结坯料进行热处理,制得高比重钨合金材料。在本发明中,所采用的钨粉为纯度达到99.9%以上、平均粒径为3μm左右的还原钨粉;镍粉为纯度达到99.5%以上、平均粒径为5μm左右的羰基镍粉;铁粉为纯度达到99.5%以上、平均粒径为5μm左右的羰基铁粉。并且,所述改性钨粉的颗粒尺寸为500nm~5μm,晶粒尺寸为14nm~117nm;所述纳米晶镍铁固溶体的颗粒尺寸为0.8~2μm,晶粒尺寸为6nm~10nm。由经球磨改性的超细化且均匀的改性钨粉和纳米晶镍铁固溶体经一段时间的混粉所形成的合金粉末,能够有效避免钨向镍铁固溶体中大量扩散并溶解,从而避免了合金材料的塑性降低;同时,其还能够有效地阻止钨颗粒在 后续液相烧结时长大,因此能够在相对较低的温度下达到较高的致密度,进而提高材料的力学性能。在一具体实施方式中,步骤1)和步骤2)所述的球磨在保护气氛中进行,并且控制所述球磨的转速为200~350转/分,球磨时间为5~35小时。所述保护气氛例如可以采用纯度达到99.99%以上的高纯氩气作为保护气体,从而防止粉末在球磨过程被氧化;镍粉和铁粉的质量配比例如可以为7:3,并且可以采用常规的球磨机进行(例如搅拌式高能球磨机)所述球磨,磨球材料可以为GCr15(直径例如为6mm),球料比(质量比)可以为5:1~15:1。进一步地,为了防止所述球磨过程中粉末的过度粘球,可以加入一定量(例如0.5~2wt%)的过程控制剂,例如无水乙醇、硬脂酸等。添加适当的过程控制剂能够明显提高机械球磨的出粉率,特别有利于工业生产。经上述球磨改性的在本发明一具体方案中,可以在球磨机中进行步骤3)所述的混粉。进一步地,控制步骤3)所述的混粉的时间为50~70小时,例如60小时,此外,所述混粉可以在转速为80~120转/分下进行;并且采用冷等静压进行步骤3)所述的压制,并且控制所述压制的压力为200~350MPa,例如230~270MPa。在该压力下可以获得密度较高、密度分布及孔隙度更加均匀的冷压坯,其在后续的液相烧结工艺中有利于液相均匀填充孔隙,从而不易造成成分偏析。进一步地,控制步骤4)所述的液相烧结的温度为1445~1530℃,例如1465℃左右,烧结时间为20~120分钟,例如30~60分钟。烧结温度过低或烧结时间过短时会使得γ相对钨相不浸润或浸润差,导致两相界面结合较弱,易成为裂纹源;而当烧结温度过高或烧结时间过长时,则会产生钨晶粒的聚集长大,合金中会出现钨颗粒大小不均且粘结相分布不均匀,其易使得合金的延伸性降低。在本发明中,采用纳米级的SiO2和超细的石墨粉为原料制作热静液挤压的润滑介质,其能够在更细的微观状态下形成充分混合,在以该润滑介质进行热静液挤压时,细化的熔融SiO2所形成微小且均匀的传力单元被吸附在石墨层中,由于传力单元与润滑单元均细化至纳米级,因而能形成更加稳定的静液传力层,不仅能够有效地改善挤压工艺(例如降低挤压力),还能够大幅 改善强化后的材料的性能(例如大幅提高材料强度时仍能保持良好的延伸率)以及尺寸精度。具体地,在步骤5)中,将所述石墨粉和二氧化硅粉末置于球磨装置中进行所述混粉和球磨;并且在进行所述混粉和球磨前,先对所述球磨装置抽真空并充入0.5~1.0MPa氩气;在进行所述混粉和球磨时,控制所述混粉的转速为80~120转/分,混粉时间为40~60小时,所述球磨的转速为300~450转/分,球磨时间为10~30小时。进一步地,所采用的石墨粉的纯度为99.8%以上,二氧化硅粉末的纯度为99.9%以上。进一步地,采用冷压进行步骤5)所述的压制,并且控制所述压制的压力为400~1000MPa。压制后形成的坯料可经机加工形成包套形式的润滑介质,其外径例如可以为52mm,壁厚例如可以为3~6mm。在本发明一具体方案中,步骤6)中的所述热静液挤压包括:将所述烧结坯料置于所述润滑介质后,以10~20℃/分钟的升温速度升温至600~1250℃,保温30~60分钟后,置于挤压模具中进行热静液挤压;其中,控制所述烧结坯料与所述润滑介质的质量配比为2.5~3.5:1,所述热静液挤压的挤压比6~40,挤压力600~800MPa。挤压模具的预热温度不能太高,例如可以为200℃~350℃。经上述热静液挤压的材料变形量达到85%以上,钨颗粒变形程度加大,不仅细化组织的效果更加明显,而且能够使材料的组织在纵向形成纤维状分布,不仅有利于提高钨合金材料的强度,使利用该材料制成的弹芯穿甲威力增强;同时能够减少或者消除烧结体中的残留孔隙,提高材料的致密度。此外,由于采用上述制备的润滑介质,热静液挤压形变强化润滑条件得到改善,处于三向压应力状态下的材料的变形强化效果优异,并且材料的性价比高,特别适合批量生产。进一步地,步骤6)中的所述热处理包括:将热静液挤压后的烧结坯料置于热处理装置后,对所述热处理装置进行抽真空,随后以10~30℃/分钟的升温速度将所述烧结坯料升温至600~800℃,保温2~4小时后冷却至室温。适宜的热处理能够控制晶粒或亚晶的大小和分布以及析出相的形貌、大小、分布,改善位错分布及组态,并消除或部分消除残余应力,其对于提高 弹芯尺寸的稳定性具有重要作用,进而提高产品的力学性能;然而,过高的热处理温度会导致大量的钨颗粒粘连在一起而降低材料的延伸率。本发明还提供一种高比重钨合金材料,按照上述任一所述的制备方法制得。该高比重钨合金材料的形变量达到80%以上,抗拉强度达到1600MP以上,延伸率达到15%以上。本发明的实施,至少具有以下优势:1、本发明通过对原料进行球磨改性,从而有效避免钨向镍铁固溶体中大量扩散并溶解,避免了合金材料的塑性降低;同时,其还能够有效地阻止钨颗粒在后续液相烧结时长大,因此能够在相对较低的温度下达到较高的致密度,进而有利于降低生产成本、简化工艺、减少烧结时的污染和成分变化。2、本发明采用纳米级SiO2和超细石墨粉为原料制作热静液挤压的润滑介质,在以该润滑介质进行热静液挤压时能够形成更加稳定的静液传力层,不仅有利于改善挤压工艺(例如降低挤压力),还能够大幅改善强化后的材料的性能和尺寸精度。3、本发明的高比重钨合金材料的形变量达到80%以上,抗拉强度达到1600MP以上,延伸率达到15%以上,该材料具有优异的综合性能,可用作穿甲武器的弹芯,并具有良好的穿甲威力。附图说明图1为本发明实施例1的改性钨粉的扫描电镜图;图2为本发明实施例1的纳米晶镍铁固溶体的透射电镜图;图3为本发明实施例1的高比重钨合金棒材纵向的扫描电镜图。具体实施方式为使本发明的目的、技术方案和优点更加清楚,下面将结合本发明的附图和实施例,对本发明实施例中的技术方案进行清楚、完整地描述,显然,所描述的实施例是本发明一部分实施例,而不是全部的实施例。基于本发明中的实施例,本领域普通技术人员在没有做出创造性劳动前提下所获得的所有其他实施例,都属于本发明保护的范围。本发明实施例采用的原料如下:还原钨粉:纯度为99.9%,平均粒径为3μm;羰基镍粉:纯度为99.5%,平均粒径为5μm;羰基铁粉:纯度为99.5%,平均粒径为5μm;石墨粉:纯度为99.8%,粒径为500nm~2.5μm;二氧化硅粉末:纯度为99.9%,粒径约为10nm。实施例1一、原料的球磨改性将还原钨粉置入高能搅拌式球磨机中进行球磨,在球磨时采用纯度为99.99%的高纯氩气作为保护气体,并添加1wt%的硬脂酸作为球磨过程控制剂,磨球材料选用GCr15,其直径约为6mm,球料比(质量比)为15:1左右,并且控制球磨机转速为350rpm左右,球磨时间为35h左右,制得平均尺寸为亚微米级的改性钨粉(出粉率94.3%左右),其扫描电镜结果如图1所示。由图1可知,经球磨改性的钨颗粒得到明显细化,颗粒形状趋于“等轴”状,平均尺寸已达到亚微米级,约为500nm左右,粉末粒度已在超细颗粒的粒度范围,晶粒尺寸达到14nm左右。将羰基镍粉和羰基铁粉按照质量配比约为7:3配制成混合粉末后,置于混粉机中混合均匀,然后置入高能搅拌式球磨机中进行球磨,在球磨时采用纯度为99.99%的高纯氩气作为保护气体,磨球材料选用GCr15,其直径约为6mm,球料比为15:1左右,并且控制球磨机转速为350rpm左右,球磨时间为25h左右,制得纳米晶镍铁固溶体,其透射电镜结果如图2所示。由图2可知,经球磨改性的粉末微观组织不仅得到了细化,而且已全部形成了纳米晶镍基固溶体,其颗粒尺寸约为2μm,晶粒尺寸约为6nm。二、冷等静压和液相烧结将上述制备的改性钨粉和纳米晶镍铁固溶体按照质量配比为93:7制成复合粉末后,置于混粉机混粉60h左右;然后将混合均匀的复合粉末放入壁厚约为2mm的胶套中,然后置于270MPa超高压室内进行冷等静压,得到相对密度为77%左右的冷压坯料;随后,将上述冷压坯料放入真空热处理炉中,在1460℃下进行液相烧结,烧结时间为40min,制得密度达17.69g/cm3、相对密度约为99.8%的烧结坯料,该烧结坯料中钨颗粒的平均尺寸小于20μm, 并且其呈球形分布于γ相中,γ相的分布也较为均匀。经检测,该烧结坯料的抗拉强度达1024MP左右,屈服强度达827MP左右,延伸率达23.4%左右,韧性达155J/cm2左右。三、热静液挤压将石墨粉和二氧化硅粉末按照质量配比约为6:4配制成复合粉末后,按球料比为40:1左右放入球磨罐中,对球磨罐抽真空至约10-2Pa后,向球磨罐中充入1.0MPa左右的氩气,先在约100rpm的转速下低速混粉50h左右,混粉结束后在约400rpm的转速下机械球磨20h左右;将经球磨的复合粉末置入钢模中,在400MPa左右的压力下进行冷压,得到相对密度为85%左右的块状坯料,经机加工,制成外径约为52mm、壁厚约为6mm的包套(即润滑介质)。将上述制备的烧结坯料装入上述制备的包套后,以15℃/min的升温速率升温至约1200℃,保温40min左右后,置于挤压模具中进行热静液挤压,其中烧结坯料与包套的质量配比约为3.5:1,模具的预热温度约为300℃,挤压比约为27,挤压力约为800MPa,经挤压得到直径为10mm的棒材。四、热处理将上述棒材置于真空炉后,对真空炉抽真空至10-2Pa以下,随后以10℃/min的速度将棒材升温至600℃,保温4h后随炉冷却至室温,即得到直径为10mm的高比重钨合金棒材,其纵向扫描电镜结果如图3所示。由图3可知,该棒材的钨颗粒沿变形方向被极大地拉长,γ相因变形被挤压成长条状,其显微组织呈明显的纤维状结构,γ相均匀地分布在绝大多数的钨颗粒之间。由于钨颗粒与γ相接触面积增加,因此钨颗粒与γ相的界面结合强度也显著增加,这使得具有纤维状组织的钨合金材料具有良好的强度和塑性。经检测,上述制备的高比重钨合金棒材的形变量达到85%左右,抗拉强度达到1650MP左右,延伸率达到15%左右。实施例2一、原料的球磨改性将还原钨粉置入高能搅拌式球磨机中进行球磨,在球磨时采用高纯氩气 作为保护气体,磨球材料选用GCr15,其直径约为6mm,球料比为10:1左右,并且控制球磨机转速为300rpm左右,球磨时间为25h左右,制得改性钨粉(出粉率96.3%左右),其晶粒尺寸达到34nm左右。将羰基镍粉和羰基铁粉按照质量配比约为6:4配制成混合粉末后,置于混粉机中混合均匀,然后置入高能搅拌式球磨机中进行球磨,在球磨时采用高纯氩气作为保护气体,磨球材料选用GCr15,其直径约为6mm,球料比为10:1左右,并且控制球磨机转速为300rpm左右,球磨时间为25h左右,制得纳米晶镍铁固溶体,其颗粒尺寸约为2μm,晶粒尺寸约为10nm。二、冷等静压和液相烧结将上述制备的改性钨粉和纳米晶镍铁固溶体按照质量配比为93:7制成复合粉末后,置于球磨机中在100rpm的速度下混粉70h左右;然后将混合均匀的复合粉末放入壁厚约为2mm的胶套中,然后置于230MPa超高压室内进行冷等静压,得到相对密度为71%左右的冷压坯料;随后,将上述冷压坯料放入真空热处理炉中,在1530℃下进行液相烧结,烧结时间为70min,制得相对密度约为98%的烧结坯料。三、热静液挤压将石墨粉和二氧化硅粉末按照质量配比约为7:3配制成复合粉末后,按球料比为40:1左右放入球磨罐中,对球磨罐抽真空至约10-2Pa后,向球磨罐中充入0.5MPa左右的氩气,先在约80rpm的转速下低速混粉60h左右,混粉结束后在约450rpm的转速下机械球磨10h左右;将经球磨的复合粉末置入钢模中,在800MPa左右的压力下进行冷压,得到相对密度为90%左右的块状坯料,经机加工,制成外径约为52mm、壁厚约为6mm的包套(即润滑介质)。将上述制备的烧结坯料装入上述制备的包套后,以20℃/min的升温速率升温至约1000℃,保温60min左右后,置于挤压模具中进行热静液挤压,其中烧结坯料与包套的质量配比约为3:1,模具的预热温度约为350℃,挤压比约为20,挤压力约为700MPa,经挤压得到棒材。四、热处理将上述棒材置于真空炉后,对真空炉抽真空至10-2Pa以下,随后以10℃/min的速度将棒材升温至700℃,保温3h后随炉冷却至室温,即得到高 比重钨合金棒材。经检测,上述制备的高比重钨合金棒材的形变量达到80%左右,抗拉强度达到1620MP左右,延伸率达到16%左右。实施例3一、原料的球磨改性将还原钨粉置入高能搅拌式球磨机中进行球磨,在球磨时采用高纯氩气作为保护气体,磨球材料选用GCr15,其直径约为6mm,球料比为15:1左右,并且控制球磨机转速为250rpm左右,球磨时间为20h左右,制得改性钨粉,其晶粒尺寸达到117nm左右。将羰基镍粉和羰基铁粉按照质量配比约为8:2配制成混合粉末后,置于混粉机中混合均匀,然后置入高能搅拌式球磨机中进行球磨,在球磨时采用高纯氩气作为保护气体,磨球材料选用GCr15,其直径约为6mm,球料比为15:1左右,并且控制球磨机转速为250rpm左右,球磨时间为20h左右,制得纳米晶镍铁固溶体,其颗粒尺寸约为2μm,晶粒尺寸约为10nm。二、冷等静压和液相烧结将上述制备的改性钨粉和纳米晶镍铁固溶体按照质量配比为93:7制成复合粉末后,置于混粉机混粉50h左右;然后将混合均匀的复合粉末放入壁厚约为2mm的胶套中,然后置于350MPa超高压室内进行冷等静压,得到相对密度为85%左右的冷压坯料;随后,将上述冷压坯料放入真空热处理炉中,在1500℃下进行液相烧结,烧结时间为100min,制得相对密度约为99%的烧结坯料,该烧结坯料中钨颗粒的平均尺寸小于20μm,并且呈球形均匀地分布于γ相中。三、热静液挤压将石墨粉和二氧化硅粉末按照质量配比约为8:2配制成复合粉末后,按球料比为40:1左右放入球磨罐中,对球磨罐抽真空至约10-2Pa后,向球磨罐中充入1.0MPa左右的氩气,先在约120rpm的转速下低速混粉40h左右,混粉结束后在约300rpm的转速下机械球磨30h左右;将经球磨的复合粉末置入钢模中,在600MPa左右的压力下进行冷压,得到相对密度为80%左右的块状坯料,经机加工,制成外径约为52mm、壁厚约为6mm的包套(即润滑介 质)。将上述制备的烧结坯料装入上述制备的包套后,以20℃/min的升温速率升温至约600℃,保温30min左右后,置于挤压模具中进行热静液挤压,其中烧结坯料与包套的质量配比约为3:1,模具的预热温度约为200℃,挤压比约为25,挤压力约为600MPa,经挤压得到棒材。四、热处理将上述棒材置于真空炉后,对真空炉抽真空至10-2Pa以下,随后以20℃/min的速度将棒材升温至800℃,保温2h后随炉冷却至室温,即得到高比重钨合金棒材。经检测,上述制备的高比重钨合金棒材的形变量达到80%左右,抗拉强度达到1600MP左右,延伸率达到17%左右。对照例1采用实施例1的方法制备高比重钨合金材料,不同的是,对照例1不对还原钨粉进行球磨改性,而是直接将平均粒径为3μm的还原钨粉与实施例1制备的纳米晶镍铁固溶体按照质量配比为93:7制成复合粉末后进行冷等静压和液相烧结,制得的烧结坯料,该烧结坯料中钨颗粒的平均尺寸达到40μm左右,颗粒大小的不均匀性及γ相分布的不均匀性明显增加,材料容易出现成分偏析和严重的坍塌变形。经检测,该烧结坯料的抗拉强度达935MP左右,屈服强度达762MP左右,延伸率达20.0%左右,韧性达120J/cm2左右,其各方面的性能均不如采用球磨改性的钨粉所制备的烧结坯料。对照例2采用实施例1的方法制备高比重钨合金材料,不同的是,对照例2在制作包套(润滑介质)时采用平均粒径为25μm左右的石墨粉和平均粒径为2.5μm左右的玻璃粉,并且在进行热静液挤压时烧结坯料与包套的质量配比约为2:1。经检测,最终制得的高比重钨合金棒材的形变量为75%左右,抗拉强度为1450MP左右,延伸率为14%左右,其抗拉强度和延伸率均不如本发明实 施例所制备的高比重钨合金棒材。最后应说明的是:以上各实施例仅用以说明本发明的技术方案,而非对其限制;尽管参照前述各实施例对本发明进行了详细的说明,本领域的普通技术人员应当理解:其依然可以对前述各实施例所记载的技术方案进行修改,或者对其中部分或者全部技术特征进行等同替换;而这些修改或者替换,并不使相应技术方案的本质脱离本发明各实施例技术方案的范围。