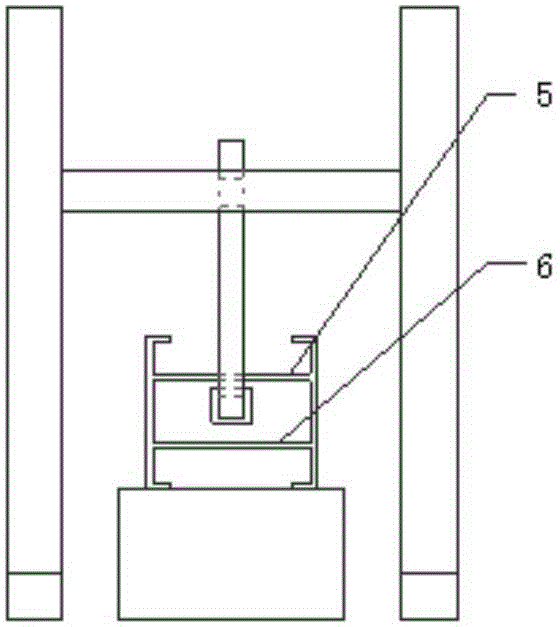
本发明涉及一种在刮板输送机中部槽中制备熔覆层的方法及其应用。
背景技术:
:刮板输送机是采煤工作面中输煤的主要设备,其主要由机头部、机尾部和中间部3大部分组成。刮板输送机的中间部是刮板输送机最长的部分,由机头部、中间部和机尾部三部分组成。以SGZ764/400刮板输送机为例,总长度为150m,而中间部约为142m,其成本占整机成本的70-90%,所以中部槽的使用寿命直接决定着刮板输送机的寿命。刮板输送机的中间部中最重要的就是中部槽,中部槽主要用于连接煤矿井下刮板输送机和转载机。另外,中部槽是刮板输送机的机身,由中板和槽帮钢等组成,刮板输送机中部槽的上槽面用于运输煤,而下槽面供刮板链返程用。而刮板输送机作为采煤工作面中输煤的主要设备,其中部槽的两链道及槽帮经受严重的三体磨料磨损,尤其是中部槽磨损严重,严重制约着煤炭输送和高效生产。目前,现有技术主要采用激光熔覆和电弧堆焊等方法来制备熔覆层,对中部槽新品进行强化以及对旧品进行再制造(修复)。然而,采用上述现有技术的方法制备熔覆层时必须要对中部槽的下槽面进行切割才能方便地处理中部槽的下槽面,而且,由于受到激光器体积以及熔覆焦距的影响,采用激光熔覆技术制备熔覆层时在实际的处理中往往受限较多,例如:1)材料消耗与浪费较大;2)激光熔覆时间长;3)加工余量大;4)成本昂贵。因此,目前亟需找到一种能够克服上述现有技术的缺陷,在不切割中部槽的下槽面的基础上就能够快速、简便、高效地在刮板输送机中部槽的上槽面和/或下槽面的上表面制备熔覆层的方法。技术实现要素:本发明的目的是克服现有技术的缺陷,在不切割中部槽的下槽面的前提下提供一种能够快速、简便、高效地在刮板输送机中部槽中制备熔覆层的方法,而且通过该方法制备的刮板输送机中部槽中的熔覆层具有耐磨性强、成本低以及使用寿命超过新品的优点。为了实现上述目的,一方面,本发明提供一种在刮板输送机中部槽中制备熔覆层的方法,该方法包括:采用等离子熔覆设备对所述刮板输送机中部槽的上槽面和/或下槽面的上表面进行等离子熔覆,制备熔覆层;其中,所述等离子熔覆设备由龙门式操作机控制。另一方面,本发明还提供一种本发明的所述方法在刮板输送机中部槽中再制造熔覆层中的应用。本发明的上述方法能够克服现有技术的缺陷,在不切割中部槽的下槽面的前提下,能够快速、简便、高效地在刮板输送机中部槽中制备熔覆层,而且通过该方法制备的熔覆层具有较强的耐磨性,使得得到的刮板输送机中部槽具有更长的使用寿命,而且通过本发明的该方法得到的刮板输送机中部槽中的熔覆层还具有成本低、效率高的优点。特别地,通过本发明所述的方法制备得到的熔覆层使得再制造得到的产品的性能达到甚至超过新品的性能。而且,本发明的方法可以一次性实现对所述刮板输送机中部槽的上槽面和/或下槽面的上表面进行等离子熔覆,克服了传统工艺方法所必须的对于下槽面的切割以及熔覆完成后进行组焊的操作步骤。具体地,相对于现有技术的工艺,本发明的方法还具有以下优点:1)节约材料:采用等离子熔覆设备形成的熔覆层均匀致密,与现有技术的激光熔覆相比节省了材料;2)熔覆时间短:采用等离子熔覆设备制备熔覆层时可以缩短喷涂时间,使得工件热影响小,变形小;3)加工余量小;4)喷涂材料价格低廉。本发明的其他特征和优点将在随后的具体实施方式部分予以详细说明。附图说明附图是用来提供对本发明的进一步理解,并且构成说明书的一部分,与下面的具体实施方式一起用于解释本发明,但并不构成对本发明的限制。在附图中:图1是用于本发明的方法的操作设备的主视图;图2是图1中的操作设备的左视图;图3是图1中的操作设备的俯视图;图4是本发明所述的八字型熔覆路径;图5是本发明所述的叉字型熔覆路径;图6是本发明所述的网格型熔覆路径。附图标记说明1龙门式操作机2内孔等离子熔覆枪3中部槽4工作台5上槽面6下槽面具体实施方式以下对本发明的具体实施方式进行详细说明。应当理解的是,此处所 描述的具体实施方式仅用于说明和解释本发明,并不用于限制本发明。本发明提供了一种在刮板输送机中部槽中制备熔覆层的方法,该方法包括:采用等离子熔覆设备对所述刮板输送机中部槽的上槽面和/或下槽面的上表面进行等离子熔覆,制备熔覆层;其中,所述等离子熔覆设备由龙门式操作机控制。在本发明中,需要特别说明的是,本领域技术人员对所述龙门式操作机的操作方法均已知悉,本发明在此不再赘述。通过本发明的上述方法在刮板输送机中部槽中制备熔覆层时,能够避免现有技术的手段中必须对刮板输送机中部槽下槽面进行的切割的步骤,采用等离子熔覆设备配合龙门式操作机的方法,降低了操作复杂度和工艺成本,适合在工业大生产中的应用。根据本发明所述的方法,本发明的发明人发现,优选情况下,当所述熔覆层的厚度为1-6mm时,通过本发明的方法形成的熔覆层能够与所述刮板输送机中部槽的上槽面和/或下槽面的上表面紧密结合,从而能够延长刮板输送机中部槽的使用寿命;更加优选地,当所述熔覆层的厚度为2-4mm时,通过本发明的方法形成的熔覆层与所述刮板输送机中部槽的上槽面和/或下槽面的上表面的结合强度更大,能够更加显著地延长刮板输送机中部槽的使用寿命,节省材料,而且,刮板输送机中部槽的使用性能也能够达到最优。在本发明中,需要特别说明的是,所述熔覆层的厚度是指所述熔覆层相对于所述刮板输送机中部槽的上槽面和/或下槽面的上表面凸起的高度。在本发明中,所述熔覆层的路径可以包括叉字型、八字型和网格型中的至少一种,所述路径可以采用CAD制图程序在龙门式操作机上进行控制,例如,本发明的实施例中均示例性地采用叉字形路径。其中,所述八字型熔覆路径如图4中所示;所述叉字型熔覆路径如图5中所示;所述网格型熔覆路径如图6中所示。根据本发明所述的在刮板输送机中部槽中制备熔覆层的方法,本发明所述的方法对熔覆层的种类和化学成分没有特别的限定,本发明的方法可以用于具有各种化学成分的熔覆层,然而,本发明的发明人发现,当所述熔覆层为铁基合金粉、WC-12Co和镍基合金粉中的至少一种时,形成的熔覆层的耐磨性更强。进一步地,当所述铁基合金粉中含有12-15重量%的Cr、0.3-0.7重量%的Mn、0.5-1.1重量%的B、1-1.5重量%的Si、1.5-1.9重量%的Mo、3.5-4重量%的Ni、0.1-0.15重量%的C以及余量的Fe时,能够使得形成的刮板输送机中部槽上槽面和下槽面的上表面中的熔覆层的使用寿命更长。更优选情况下,在本发明中,所述熔覆层包括铁基合金粉和WC-12Co,其中,WC-12Co的含量为10-30重量%,铁基合金粉的含量为70-90重量%。含有WC-12Co和铁基合金粉的熔覆层能够使形成的熔覆层硬度更高,更耐磨,并且具有更长的使用寿命。更优选情况下,在本发明中,所述熔覆层包括铁基合金粉和Ni45,所述Ni45的含量为20-75重量%,所述铁基合金粉的含量为25-80重量%。含有Ni45和铁基合金粉的熔覆层能够使形成的熔覆层硬度更高,更耐磨,并且具有更长的使用寿命。在本发明中,所述等离子熔覆设备是指能够实施等离子熔覆技术的设备。根据本发明所述的在刮板输送机中部槽中制备熔覆层的方法,所述等离子熔覆设备为内孔等离子熔覆焊枪。在本发明中,需要特别说明的是,本领域技术人员对内孔等离子熔覆焊枪的操作方法均已知悉,本发明在此不再赘述。本发明的发明人发现,采用内孔等离子熔覆设备修复中部槽的方法能够实现降低操作复杂度和工艺成本的目的,并且能够避免现有技术手段中所必须的对刮板输送机中部槽的下槽面进行切割的步骤,以及熔覆完成后进行组 焊的步骤,能够大幅度延长刮板输送机中部槽的使用寿命,适合工业生产中应用。在本发明所述的在刮板输送机中部槽中制备熔覆层的方法中,所述等离子熔覆设备的喷枪的行走线速度为0.6-1.2m/min;优选地,所述等离子熔覆设备的喷枪的行走线速度为0.8-1.0m/min。根据本发明的一种优选的具体实施方式,所述在刮板输送机中部槽中制备熔覆层的方法包括:先在所述龙门式操作机中设置所述等离子熔覆设备的操作条件,然后通过所述龙门式操作机控制等离子熔覆设备进行等离子熔覆。在本发明所述的在刮板输送机中部槽中制备熔覆层的方法中,所述等离子熔覆设备的操作条件包括:氩气流量为15-80L/min;优选为30-50L/min。在本发明所述的在刮板输送机中部槽中制备熔覆层的方法中,所述等离子熔覆设备的操作条件包括:电压为20-60V;优选为29-49V。在本发明所述的在刮板输送机中部槽中制备熔覆层的方法中,所述等离子熔覆设备的操作条件包括:电流为250-450A;优选为300-400A。在本发明所述的在刮板输送机中部槽中制备熔覆层的方法中,所述等离子熔覆设备的操作条件包括:熔覆距离为5-15mm;优选为8-12mm。在本发明所述的在刮板输送机中部槽中制备熔覆层的方法中,所述等离子熔覆设备的操作条件包括:送粉率为20-80g/min;优选为40-60g/min。根据本发明所述的在刮板输送机中部槽中制备熔覆层的方法,其中,所述刮板输送机中部槽可以为磨损后待修复的刮板输送机中部槽。根据本发明的一种优选的具体实施方式,当所述刮板输送机中部槽为磨损后待修复的刮板输送机中部槽时,该方法还可以包括:先将所述磨损后待修复的刮板输送机中部槽的上槽面和/或下槽面的上表面依次进行预加工处理、清洗处理,然后再形成所述熔覆层。在本发明中,所述预加工处理的目的是除去待修复的刮板输送机上的疲 劳层和磨损层等。在本发明中,所述磨损后待修复的刮板输送机中部槽仅是为了区分刮板输送机中部槽在进行修复前和修复后的不同状态,实际上均是指同一个刮板输送机中部槽。在本发明中,需要进行修复的刮板输送机中部槽在利用本发明的方法完成修复后,也即形成新的熔覆层之后即为修复后的刮板输送机中部槽。本领域技术人员不应理解为对本发明的限制。在本发明所述的在刮板输送机中部槽中制备熔覆层的方法中,所述预加工处理步骤可以包括:去除所述磨损后待修复的刮板输送机中部槽的上槽面和/或下槽面的上表面的磨损后残留的熔覆层。在本发明中,需要特别说明的是,去除所述磨损后待修复的刮板输送机中部槽的上槽面和/或下槽面的上表面的磨损后残留的熔覆层的方法可以为本领域内常规使用的各种方法,本发明在此不再赘述。在本发明中,所述清洗的方法为本领域技术人员所公知,例如可以使用酒精和/或丙酮对待处理表面进行清洗,去除待修复的刮板输送机中部槽的上槽面和/或下槽面的上表面的残留污渍。根据本发明的一种优选的具体实施方式,本发明的方法包括:1)去除磨损后待修复的刮板输送机中部槽的上槽面和/或下槽面的上表面的磨损后残留的熔覆层;2)对经过步骤1)后得到的待修复的刮板输送机中部槽的上槽面和/或下槽面的上表面进行清洗,去除残留污渍;3)在所述龙门式操作机中设置等离子熔覆设备的操作条件;4)通过所述龙门式操作机控制所述等离子熔覆设备在经过步骤3)后的所述刮板输送机中部槽的上槽面和/或下槽面的上表面进行等离子熔覆,制备熔覆层;5)待经过步骤4)后得到的所述刮板输送机中部槽的上槽面和/或下槽面的上表面降至室温后,对其表面熔渣进行清理。另一方面,本发明还提供一种本发明的所述方法在刮板输送机中部槽中再制造熔覆层中的应用。特别地,将本发明的上述方法用于在刮板输送机中部槽中再制造熔覆层时,能够使得再制造得到的产品的性能(例如使用寿命等)达到甚至超过新品的性能。根据本发明的一种优选的具体实施方式,本发明所述的方法采用图1所示的操作设备进行,具体地,所述操作设备包括龙门式操作机1、内孔等离子熔覆枪2和工作台4,刮板输送机的中部槽3位于工作台上。并且,本发明的图2具体示出了刮板输送机的中部槽3的上槽面5和下槽面6,且图3为图1中的操作设备的俯视图。本发明的上述方法能够克服现有技术的缺陷,在不切割中部槽的下槽面的前提下,能够快速、简便、高效地在刮板输送机中部槽中制备熔覆层,而且通过该方法进一步提高了熔覆层的耐磨性,使得得到的刮板输送机中部槽具有更长的使用寿命。具体地,本发明的上述方法具有以下优点:1)节约时间,没有切割和熔覆后再焊接槽面的工艺过程;2)通过改变材料,提高了硬度和使用寿命。以下将通过实施例对本发明进行详细描述。在以下实施例中,所使用的各种材料和仪器均来自商购。以下实施例中使用的刮板输送机均为购自山东能源机械公司的SGB-630/150C(W)型号的刮板输送机,且各个实施例中的待修复的刮板输送机中下槽面的磨损程度相当。以下实施例中使用的等离子熔覆设备为内孔等离子熔覆焊枪,其中内孔焊枪购自武汉高力热喷涂工程有限责任公司,为PG-150/D35-NK100/1000型1M长内孔焊枪。实施例1本实施例用于说明本发明的在刮板输送机中部槽中制备熔覆层的方法,具体地,本实施例的步骤如下:1)去除磨损后待修复的刮板输送机中部槽的下槽面的上表面的磨损后残留的熔覆层;2)对经过步骤1)后得到的待修复的刮板输送机中部槽的下槽面的上表面进行清洗,去除残留污渍;3)在所述龙门式操作机中设置等离子熔覆设备的操作条件,所述操作条件如表1中所示;4)通过所述龙门式操作机控制所述等离子熔覆设备在经过步骤2)后的所述刮板输送机中部槽的下槽面的上表面进行等离子熔覆,制备熔覆层,其中,所述等离子熔覆设备的喷枪的行走线速度和熔覆层的厚度如表1所示,所述熔覆层为铁基合金粉熔覆层,且所述铁基合金粉的化学组成如表2所示;5)待经过步骤4)后得到的所述刮板输送机中部槽的下槽面的上表面降至室温后,对其表面熔渣进行清理。其中,在上述方法中,制备熔覆层的时间为30min。表1表2种类CrMnBSiMoNiCFe含量(重量%)130.50.81.21.73.50.15余量将上述经过修复后得到的刮板输送机中部槽用于煤矿井中,结果发现,上述经过再制造工艺修复所制备的熔覆层的硬度为54HRC,与原激光熔覆工艺的48HRC相当,其耐磨性也大致相当,但由于未分解中部槽,中部槽 整体再制造修复时间大幅缩短。实施例2本实施例用于说明本发明的在刮板输送机中部槽中制备熔覆层的方法,具体地,本实施例的方法与实施例1的方法相似,本实施例中的操作条件如表3中所示;等离子熔覆设备的喷枪的行走线速度和熔覆层的厚度如表3所示,所述熔覆层材料含有25重量%的WC-12Co和75重量%的铁基合金粉。WC-12Co的成分如表4所示,铁基合金粉的成分与实施例1中相同。其中,在本实施例的方法中,制备熔覆层的时间为31min。表3表4种类WCCo含量(重量%)0.880.12将上述经过修复后得到的刮板输送机中部槽用于煤矿井中,结果发现,上述经过再制造工艺修复所制备的熔覆层硬度为58HRC,大于原激光熔覆工艺的48HRC,其耐磨性更优,使用寿命超过新品,由于未分解中部槽,中部槽整体再制造修复时间大幅缩短。实施例3本实施例用于说明本发明的在刮板输送机中部槽中制备熔覆层的方法,具体地,本实施例的方法与实施例1的方法相似,本实施例中的操作条件如表5中所示;等离子熔覆设备的喷枪的行走线速度和熔覆层的厚度如表5所示,所述熔覆层材料含有25重量%的铁基合金粉和75重量%的Ni45,铁基合金粉的化学组成与实施例1中相同,Ni45的成分如表6所示。其中,在上述方法中,制备熔覆层的时间为28min。表5表6种类CBSiCrFeNi含量(重量%)0.93.54.1154余量将上述经过修复后得到的刮板输送机中部槽用于煤矿井中,结果发现,上述经过再制造工艺修复所制备的熔覆层的硬度为62HRC,大于原激光熔覆工艺的48HRC,其耐磨性更优,使用寿命超过新品,由于未分解中部槽,中部槽整体再制造修复时间大幅缩短。实施例4本实施例用于说明本发明的在刮板输送机中部槽中制备熔覆层的方法,具体地,本实施例的方法与实施例1的方法相似,不同的是,本实施例形成的熔覆层的厚度为6mm。其中,在上述方法中,制备熔覆层的时间为42min。将上述经过修复后得到的刮板输送机中部槽用于煤矿井中,结果发现,上述经过再制造工艺修复所制备的熔覆层的硬度为50HRC,大于原激光熔覆工艺的48HRC,其耐磨性和使用寿命与新品相当,由于未分解中部槽,中部槽整体再制造修复时间大幅缩短。实施例5本实施例用于说明本发明的在刮板输送机中部槽中制备熔覆层的方法,具体地,本实施例的方法与实施例1的方法相似,不同的是,本实施例形成的熔覆层的厚度为1mm。其中,在上述方法中,制备熔覆层的时间为28min。将上述经过修复后得到的刮板输送机中部槽用于煤矿井中,结果发现,上述经过再制造工艺修复所制备的熔覆层的硬度为51HRC,大于原激光熔覆工艺的48HRC,其耐磨性和使用寿命与新品相当,由于未分解中部槽,中部槽整体再制造修复时间大幅缩短。实施例6本实施例用于说明本发明的在刮板输送机中部槽中制备熔覆层的方法,具体地,本实施例的方法与实施例2的方法相似,不同的是,本实施例中铁基合金粉的化学成分如表7中所示。表7种类CrMnBSiMoNiCFe含量(重量%)110.20.81.52.13.90.1余量其中,在上述方法中,制备熔覆层的时间为35min。将上述经过修复后得到的刮板输送机中部槽用于煤矿井中,结果发现,上述经过再制造工艺修复所制备的熔覆层硬度为54HRC,大于原激光熔覆工艺的48HRC,其耐磨性优,使用寿命超过新品,由于未分解中部槽,中部槽整体再制造修复时间大幅缩短。实施例7本实施例用于说明本发明的在刮板输送机中部槽中制备熔覆层的方法,具体地,本实施例的方法与实施例3的方法相似,不同的是,本实施例中等离子熔覆设备的喷枪的行走线速度为1.4m/min。其中,在上述方法中,制备熔覆层的时间为34min。将上述经过修复后得到的刮板输送机中部槽用于煤矿井中,结果发现,上述经过再制造工艺修复所制备的熔覆层的硬度为54HRC,大于原激光熔覆工艺的48HRC,其耐磨性优,使用寿命超过新品,由于未分解中部槽,中部槽整体再制造修复时间大幅缩短。实施例8本实施例用于说明本发明的在刮板输送机中部槽中制备熔覆层的方法,具体地,本实施例的方法与实施例1的方法相似,不同的是,本实施例中等离子熔覆设备的操作条件中的送粉率为80g/min。其中,在上述方法中,制备熔覆层的时间为35min。将上述经过修复后得到的刮板输送机中部槽用于煤矿井中,结果发现,上述经过再制造工艺修复所制备的熔覆层的硬度为50HRC,与原激光熔覆工艺的48HRC相当,其耐磨性也大致相当,但由于未分解中部槽,中部槽整体再制造修复时间大幅缩短。实施例9本实施例用于说明本发明的在刮板输送机中部槽中制备熔覆层的方法,具体地,本实施例的方法与实施例2的方法相似,不同的是,本实施例中等离子熔覆设备的操作条件中的熔覆距离为15mm。其中,在上述方法中,制备熔覆层的时间为38min。将上述经过修复后得到的刮板输送机中部槽用于煤矿井中,结果发现,上述经过再制造工艺修复所制备的熔覆层硬度为52HRC,大于原激光熔覆工艺的48HRC,其耐磨性优,使用寿命超过新品,由于未分解中部槽,中部槽整体再制造修复时间大幅缩短。以上详细描述了本发明的优选实施方式,但是,本发明并不限于上述实施方式中的具体细节,在本发明的技术构思范围内,可以对本发明的技 术方案进行多种简单变型,这些简单变型均属于本发明的保护范围。另外需要说明的是,在上述具体实施方式中所描述的各个具体技术特征,在不矛盾的情况下,可以通过任何合适的方式进行组合,为了避免不必要的重复,本发明对各种可能的组合方式不再另行说明。此外,本发明的各种不同的实施方式之间也可以进行任意组合,只要其不违背本发明的思想,其同样应当视为本发明所公开的内容。当前第1页1 2 3